J. Cent. South Univ. (2017) 24: 2813-2818
DOI: https://doi.org/10.1007/s11771-017-3696-1

Improvement to anti-rust property of hot rolled rebar by compact oxide scale
CHEN Qing-an(陈庆安)1, 2, LIU Li-zhong(刘立忠)3, LIU Xin(刘鑫)1, LIU Xiang-hua(刘相华)1, 4
1. State Key Laboratory of Rolling and Automation, Northeastern University, Shenyang 110819, China;
2. College of Mechanical and Equipment Engineering, Hebei University of Engineering, Handan 056038, China;
3. School of Material and Metallurgy, Northeastern University, Shenyang 110819, China;
4. Research Academy, Northeastern University, Shenyang 110819, China
Central South University Press and Springer-Verlag GmbH Germany,part of Springer Nature 2017
Abstract: A method was proposed to improve the anti-rust property of hot rolled rebar, which uses oil–water emulsion cooling instead of water cooling after hot rolling. The experiments were carried out by two cooling methods, one cooled by water, the other cooled by oil–water emulsion. The results of wet/dry cyclic accelerated corrosion test showed that the anti-rust property of rebar cooled by oil–water emulsion was better than that by water obviously. The results of OM, SEM and EPMA analysis indicated that these two scales contained three layers: an outer Fe3O4 layer, an intermediate FeO layer with island-shaped pro-eutectoid Fe3O4, an inner eutectoid Fe3O4 layer. For the water cooled rebar, all three layers of oxide scale were relatively thin. Moreover, the scale had plenty of defects such as porosity, and crack. However, for the oil–water emulsion cooled rebar, all three layers of oxide scale were relatively thick and compact, which played an important role in protecting the rebar from atmospheric rust.
Key words: hot rolled rebar; anti-rust property; compact oxide scale; oil–water emulsion cooling
1 Introduction
Hot rolled rebar is widely used as the skeleton of reinforced concrete in construction industry, and its consumption has been occupying a larger proportion of steel production. In order to improve the mechanical performance of rebar and maintain a low cost of production, water cooling instead of air cooling has been employed after hot rolling before coming into cooling bed. The grain size of rebar can be refined by water cooling, which improves the strength of rebar. However, the rebar produced by water cooling tends to rust during storage and transportation, which would destroy the appearance of the rebar severely [1]. This will bring significant economic losses to the production enterprises. Thus, it is important to improve the anti-rust property of the water cooled rebar.
It is well known that the surface of hot rolled rebar will be covered with oxide scale. It is exactly this oxide scale can prevent the corrosive media from entering into the matrix, thereby protecting the matrix against rust. Obviously, the thicker and more compact the oxide scale is, the better the anti-rust property it will be. The compactness of oxide scale is closely related to its structure. Many studies show that the oxide scale formed on mild steel during hot rolling comprises of three layers, namely, a thin outermost layer of hematite (Fe2O3), an intermediate magnetite (Fe3O4) layer, and a thick inner Wüstite (FeO) layer [2–4]. As mentioned above, hematite (Fe2O3) tends to absorb water and transform to rust if the environment is moist. Moreover, due to the fact that this layer is very thin, its protection effect is negligible. Fe3O4 is a chemical stable oxide in the atmospheric environment. Moreover, Fe3O4 has a compact inverse spinal structure [5]. Therefore, Fe3O4 layer can protect the matrix against rust effectively. FeO layer usually cannot protect the matrix against rust due to its loose and porous structural characteristic and unstable chemical characteristics [6]. In conclusion, how to obtain a thick and compact Fe3O4 layer is the key to improve the anti-rust property of water cooled rebar.
To solve the problem of water cooled rebar tending to rust, oil–water emulsion was used as the quenching medium during cooling of the hot rolled rebar, and a thick and compact Fe3O4 layer formed in the scale. This process does not need to change the conditions of manufacture. It has the feature of preferable anti-rust property, low cost and no pollution. In this work, the anti-rust property of hot rolled rebar cooled by oil–water emulsion was compared with water-cooled rebar. The thickness, morphology and structure of the oxide scale obtained using two cooling processes (water cooling, oil–water emulsion cooling) were investigated. The influence of the different scale on the anti-rust property was discussed.
2 Experimental
2.1 Material and experiment procedures
The steel samples used in the experiment were a commercial 20MnSiV hot rolled rebar with its chemical composition shown in Table 1. The rebar was machined into cylinders (φ16 mm×80 mm) and the surfaces were cleaned with acetone. Then the samples were pickled using 10% HCl solution to remove the original scale. After all the preparations, they were heated to 1000 °C for 15 min under an anti-oxidizing flux protection. Then the samples were respectively cooled by water and oil–water emulsion (volume ratio of oil and water was 1:10, and they were mixed by mechanical stirring), and the quenching time was 1 s for both the two cooling methods. Afterwards the samples were cooled in air to room temperature. In this process, the temperature of sample surface was measured by a thermocouple, and recorded by GRAPHTEC GL220 data recorder.
Table 1 Chemical composition of 20MnSiV hot rolled rebar (mass fraction, %)

2.2 Dry/wet cyclic accelerated corrosion test
In order to simulate the corrosion of rebar in humid environment, 12 cycles of dry/wet cyclic accelerated corrosion tests were carried out. The cyclic condition of each cycle was immersing in water for 2 h and then laying in atmosphere for 22 h.
2.3 OM analysis
In order to study the influence of two cooling processes on the thickness of scale, a ZEISS Axio Imager M2m optical microscope (OM) was used to measure the thickness of the scale. The preparing process of the samples for OM analysis was as follows. First, the samples were machined into cylinders (φ16 mm×10 mm) and mounted using epoxy resin to fix the scale. Then, they were ground and polished. Finally, they were rinsed with absolute alcohol and dried by hair drier.
2.4 SEM and EPMA analysis
The surface morphology of scale was studied using a ZEISS Ultra Plus scanning electron microscope (SEM). The preparing process of the samples for SEM analysis was as follows. First, the samples were machined into semi-cylinder (φ16 mm×10 mm). Then, they were cleaned ultrasonically in acetone for 30 min. Finally, they were rinsed with absolute alcohol and dried by hair drier.
The cross-section morphology of the scale was observed using a JEOL JXA-8530F electron probe micro-analyzer (EPMA). In order to determine the phase composition of the scale, the percentage contents of Fe and O were simultaneously analyzed in typical position of the cross-section. The EPMA analysis was carried out using the samples of OM analysis.
3 Results
3.1 Measurement of temperature
Figure 1 shows the temperature of sample surface in the two cooling processes. In water cooling process, the temperature of sample surface sharply reduced to about 320 °C after quenching for about 1 s. Then it self- tempered to about 610 °C after about 9 s. As for oil–water emulsion cooling process, the temperature of sample surface sharply reduced to about 410 °C after quenching for about 1 s. Then it self-tempered to about 700 °C after about 8 s.

Fig. 1 Temperature of sample surface
3.2 Result of dry/wet cyclic accelerated corrosion test
Figure 2 shows the appearance morphology of two kinds of rebars after 12 cycles of dry/wet cyclic accelerated corrosion tests. The surface of water cooled rebar appears rough and is covered by plenty of yellow rust. Furthermore, the rusting is prone to occurring in the rib region of the rebar. That is because the rib region tends to stress concentration, and the plasticity of the oxide scale is worse than that of the matrix. Hence the scale in the rib region tends to cracking or peeling off, thereby causing the rust of rebar. However, the surface of oil–water emulsion cooled rebar appears smooth and lustrous, which indicates that the rebar is almost with no rust.
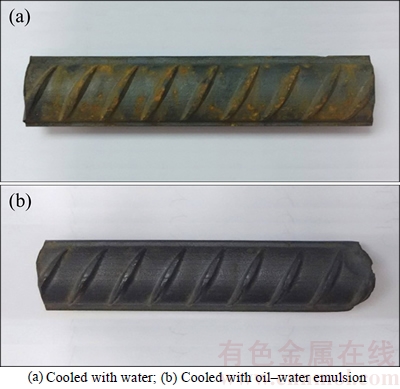
Fig. 2 Appearance morphology of rebar after corrosion test:
3.3 Thickness of scale
In order to grantee the accuracy of measurement, the thickness of the scale was obtained at representative position and measured by rule tools of OM system. Figure 3 shows the metallograph of the cross-section for the surface of the rebar. For water cooled rebar, the thickness of scale is about 7 μm. As for oil–water emulsion cooled rebar, the thickness of scale is about 12 μm.
3.4 Morphology and composition of scale
Figure 4 shows the surface morphology of the two scales. From Fig. 4(a), it can be clearly seen that the surface of water cooled scale appears rough and cracks, squamae and other defects occur. Figure 4(b) shows the partly-enlarged figure of Fig. 4(a). It can be seen that the surface is loose, and the grains are coarse. From Fig. 4(c), it can be seen that the surface of oil–water emulsion cooled scale appears relatively smooth and has almost no defect. And as seen in the partial enlarged Fig. 4(d),the surface is compact and the grain is relatively fine. The defects of oxide scale have important influence on its anti-rust performance. Due to the existence of defects, the corrosive medium in the environment is easy to contact with the matrix through defects, which lead to the rust of the matrix. Evidently, the oil–water emulsion cooled scale is favorable to blocking off the transportation of the corrosive medium to the matrix.

Fig. 3 Metallographs of cross-section for surface of rebar:

Fig. 4 Surface morphology of scales obtained by two different cooling processes:
To identify the structure of the scale, an etchant containing 1% HCl in ethanol was used to reveal the scale morphology. Figure 5 shows the cross-section morphologies of the two scales, and points 1–8 in Fig. 5 are the measuring positions for the percentage content of Fe and O. It can be seen that the two scales are both divided into three layers, and the intermediate layer contains some island-shaped structures. However, the water cooled scale (Fig. 5(a)) appears loose and porous. Compared with water cooled scale, the oil–water emulsion cooled scale (Fig. 5(b)) is more compact and almost no pores in it. In addition, it can be seen that there is a discontinuous gap between the water cooled scale and the matrix, which causes the scale peeling off easily. But the oil–water emulsion cooled scale is closely combined with the matrix, which is beneficial to protecting the matrix from rusting.
The percentage contents of Fe and O in typical position of the cross-section are shown in Table 2. As can be seen in Table 2, the atomic ratios of Fe to O at test points 1, 3, 4, 5, 7, 8 are quite close to Fe3O4, and those at test points 2, 6 are quite close to FeO. Therefore, it can be concluded that these two scales contains three layers: an outer Fe3O4 layer, an intermediate FeO layer with island-shaped Fe3O4, and an inner Fe3O4 layer. For water cooled scale, the thickness ratio of the three layers is 2:4:1, and that of oil–water emulsion cooled scale is 2:3:1.

Fig. 5 Cross-section morphology of scales obtained by two different cooling processes:
Table 2 Contents of Fe and O

4 Discussions
4.1 Influence of cooling processes on scale
Different structures of oxide scale may develop depending on the cooling conditions of the steel [7]. According to the results of SEM and EPMA analysis, there is no evident Fe2O3 layer in these two scales, which is different from the classical three–layer structure: FeO layer, Fe3O4 layer and Fe2O3 layer. The mechanism of the formation of oxide scale in these cooling processes can be illustrated in Fig. 6.
The whole cooling process can be divided into three stages: quenching, self-tempering, air cooling. In quenching stage, the rebar at high temperature will react with water according to reactions (1) and (2):
(1)
(2)
After quenching, it will form two layers with three interfaces, namely, I-Fe/FeO, II-FeO/Fe3O4 and III-Fe3O4/O2. The reactions in self-tempering stage are as follows:
I-Fe/ FeO interface:
y>x (3)
II-FeO / Fe3O4 interface:
, y>x (4)
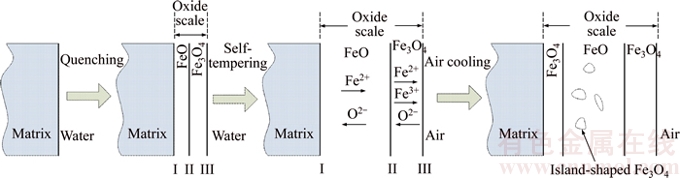
Fig. 6 Schematic diagram of formation process of oxide scale
III-Fe3O4/O2 interface:
(5)
(6)
According to PAIDASSI [8], it is difficult to prevent the precipitation of Fe3O4 inside FeO in cooling process. In air cooling stage, the pro-eutectoid reaction will take place in the FeO layer according to reaction (7) above 570 °C:
y>x (7)
The pro-eutectoid Fe3O4 will form at the interface of Fe3O4/FeO or inside the FeO layer. When the temperature is below 570 °C, the eutectoid reaction (8) will take place and the eutectoid Fe3O4 will form at the interface of Fe/FeO [9, 10].
(8)
Therefore, it can be identified that the island-shaped Fe3O4 is production of the pro-eutectoid reaction, and the inner Fe3O4 layer is production of the eutectoid reaction.
According to the results of OM and SEM analysis, the oil–water emulsion cooled scale is thicker and more compact than water cooled scale. There are two factors influencing the characteristic of the scale. Firstly, the oxidation rate can be considered to be primarily controlled by temperature. This can be expressed by the Arrhenius equation [11–14]:
(9)
where K is the oxidation rate; A is model constant; Q is the activation energy of steel; R is gas constant; T is temperature. It can be obviously seen that, high temperature enhances the oxidation process. According to Fig. 1, the self-tempered temperature of the oil–water emulsion cooled rebar is higher than that of water cooled rebar by about 90 °C due to the fact that the coefficient of heat transfer of oil–water emulsion is relatively low. Therefore, the oil–water emulsion cooled scale is thicker than water cooled scale.
Secondly, it will generate thermal stress in the scale during cooling process, due to the difference of thermal expansion coefficient between the matrix and the scale. When the thermal stress is accumulated to a certain degree, it will bound to be released by the deformation or cracking of the scale. According to SUN et al [15], the oil–water emulsion reduces the thermal stress in the formation of the scale due to the fact that its evaporation is relatively slow. Thus, it reduces the property of generating pores and cracks in the scale.
4.2 Influence of scale on anti-rust property
The rust of rebar in atmospheric environment is a complex electrochemical process. The main product of this process is FeOOH [16]. Generally, there are two processes that lead to the rust of the rebar. One is the rust of the rebar matrix according to reactions (10)–(12) and the other is the rust of the FeO according to reaction (13) [17]. Thus, FeO usually cannot protect the matrix against rust due to its loose and porous structural characteristics and unstable chemical characteristics. However, Fe3O4 has a compact structure and stable chemical characteristics. It can protect the matrix against rust effectively.
(10)
(11)
(12)
(13)
According to the discussion above, the outer Fe3O4 layer of the scale is the leading factor that affects the anti-rust property of the rebar. Furthermore, the outer Fe3O4 layer is thicker and more compact, and its anti-rust performance is better. By comparing the two kinds of scales, the outer Fe3O4 layer of the oil–water emulsion cooled scale is relatively thick and compact, so it can effectively prevent the corrosive media entering into the FeO layer and matrix. As for water cooled scale, the outer Fe3O4 layer is relatively thin and pores and cracks exist, so the corrosive medium is easy to contact with the FeO layer and matrix through the pores or cracks.
5 Conclusions
1) Due to the fact that the coefficient of heat transfer of oil–water emulsion is relatively low, the self-tempered temperature of the rebar cooled by oil–water emulsion is higher than that of water cooled rebar by about 90 °C. Eventually the scale cooled by oil–water emulsion is thicker than water cooled scale by about 5 μm.
2) The scales obtained by two different cooling methods are both divided into three layers: an outer Fe3O4 layer, an intermediate FeO layer with island- shaped pro-eutectoid Fe3O4, an inner eutectoid Fe3O4 layer. Two cooling methods have a little effect on the thickness ratio of the each layer. For water cooled case, the thickness ratio of the three layers is 2:4:1, and that of oil–water emulsion cooled scale is 2:3:1.
3) The results of wet/dry cyclic accelerated corrosion test show that the anti-rust property of rebar cooled by oil–water emulsion is better than that by water. The rebar cooled by oil–water emulsion has still no rust after 12 cycles of accelerated corrosion tests. The main reason is that the outer Fe3O4 layer of the scale (12 μm) cooled by oil–water emulsion is thicker and more compact than that (7 μm) by water cooled under the experiment conditions.
References
[1] WEI Feng-yu, HU Fang, HUANG Deng-luan. Corrosion performance of rebar quenched in a novel agent [J]. Transactions of Materials and Heat Treatment, 2011, 32(12): 152–154. (in Chinese)
[2] CHEN R Y, YUEN W Y D. A study of the scale structure of hot-rolled steel strip by simulated coiling and cooling [J]. Oxidation of Metals, 2000, 53(5, 6): 539–560.
[3] CHEN R Y, YUEN W Y D. Oxide-scale structures formed on commercial hot-rolled steel strip and their formation mechanisms [J]. Oxidation of Metals, 2001, 56(1, 2): 89–118.
[4] BHATTACHARYA R, JHA G, KUNDU S, SHANKAR R, GOPE N. Influence of cooling rate on the structure and formation of oxide scale in low carbon steel wire rods during hot rolling [J]. Surface and Coating Technology, 2006, 201: 526–532.
[5] ZHANG Juan-juan, WEI Lian-qi, ZHANG Xiao-meng, ZHOU Xun, WANG Chun-xiao, LI Jing, YE Shu-feng. Study on corrosion resistance of high temperature anti-rust agent on rebar [J]. Computers and Applied Chemistry, 2011, 28(11): 1362–1366. (in Chinese)
[6] WEI Jie, DONG Jun-hua, KE Wei. Corrosion resistance of hot rolled rebar quenched with a new chemical reagent [J]. Corrosion Science and Protection Technology, 2009, 21(5): 468–471. (in Chinese)
[7] LIN Fang-ting, SHI Wang-zhou, MA Xue-ming. Influence of cooling rate on microstructure of oxide scales formed on low-carbon steel wires [J]. Journal of East China Normal University: Natural Science, 2006(4): 23–28. (in Chinese)
[8] PAIDASSI J. The precipitation of Fe3O4 in scales formed by oxidation of iron at elevated temperature [J]. Acta Metallurgica, 1955, 3(4): 447–451.
[9] BAUD J, FERRIER A, MANENC J. Study of magnetite film formation at metal-scale interface during cooling of steel products [J]. Oxidation of Metals, 1978, 12(4): 331–342.
[10] CAO Guang-ming, HE Yong-quan, LIU Xiao-jiang, LIU Zheng-yu. Tertiary oxide scale structure transition of low carbon steel during continuous cooling after coiling process [J]. Journal of Central South University: Science and Technology, 2014, 45(6): 1790–1796. (in Chinese)
[11] CAO Guang-ming, SUN Bin, LIU Xiao-jiang, ZHANG Lin. Oxidation kinetics and oxide scales control of hot-rolled high strength steel [J]. Journal of Northeastern University: Natural Science, 2013, 34(1): 71–74. (in Chinese)
[12] YANG Xi-yun, GONG Zhu-qing, LIU Feng-liang. Kinetics of Fe3O4 formation by air oxidation [J]. Journal of Northeastern University, 2004, 11(2): 152–155.
[13] CAO Guang-ming, LIU Xiao-jiang, SUN Bin, LIU Zheng-yu. Morphology of oxide scale and oxidation kinetics of low carbon steel [J]. Journal of Iron and Steel Research, 2014, 21(3): 335–341.
[14] HU Xian-jun, ZHANG Bi-ming, CHEN Shao-hui, FANG Feng, JIANG Jian-qing. Oxide scale growth on high carbon steel at high temperatures [J]. Journal of Iron and Steel Research, 2013, 20(1): 47–52.
[15] SUN Jian-lin, MA Yan-li, ZHANG Zhi-chao, WANG Jian-zhe. Effect of hot-rolling lubrication on the surface quality of strips [J]. Journal of University of Science and Technology Beijing, 2009, 21(5): 468–471. (in Chinese)
[16] ZITROU E, NIKOLAOU J, TSAKIRIDIS P E, PAADIMITRIOU G D. Atmospheric corrosion of steel reinforcing bars produced by various manufacturing processes [J]. Construction and Building Materials, 2007, 21: 1161–1169.
[17] WEI J, DONG J H, KE W. The influence of cooling processes on the corrosion performance of the rebar scale [J]. Construction and Building Materials, 2010, 24: 275–282.
(Edited by YANG Hua)
Cite this article as: CHEN Qing-an, LIU Li-zhong, LIU Xin, LIU Xiang-hua. Improvement to anti-rust property of hot rolled rebar by compact oxide scale [J]. Journal of Central South University, 2017, 24(12): 2813–2818. DOI:https://doi.org/10.1007/s11771-017-3696-1.
Foundation item: Project(51374069) supported by the National Natural Science Foundation of China
Received date: 2016-01-20; Accepted date: 2016-05-30
Corresponding author: LIU Xiang-hua, PhD, Professor; Tel: +86–24–83682273; E-mail: liuxh@mail.neu.edu.cn