文章编号: 1004-0609(2005)08-1311-06
硫化锑精矿还原造锍熔炼一步炼锑
陈永明, 黄 潮, 唐谟堂, 姚维义, 唐朝波, 皮关华
(中南大学 冶金科学与工程学院, 长沙 410083)
摘 要: 为了彻底解决我国火法炼锑厂普遍存在的低浓度二氧化硫烟气污染问题, 提出了一种新的火法炼锑工艺——硫化锑矿还原造锍熔炼, 并采用单因素实验法考察了熔炼温度、 时间以及造锍剂和添加剂的加入量等因素对金属锑直收率的影响。 确定的最佳工艺条件: 先在1100℃下熔炼2h, 再迅速升温至1200℃下保温50min; 烧渣加入量为其理论量的1.2倍; 添加剂总钠量为精矿量的10%, 其中碳酸钠和芒硝加入量分别为精矿量的5%和24.2%。 在最优条件下, 锑的直收率和总收率分别为82.07%和97.79%, 固硫率大于99%。
关键词: 硫化锑精矿; 还原造锍熔炼; 固硫; 清洁冶金
中图分类号: TF111.13
文献标识码: A
Production of antimony by directly reducing-matting smelting
of stibnite concentrate
CHEN Yong-ming, HUANG Chao, TANG Mo-tang, YAO Wei-yi,
TANG Chao-bo, PI Guan-hua
(School of Metallurgical Science and Engineering,Central South University, Changsha 410083, China)
Abstract: In order to eliminate the serious environment pollution of the low concentration sulfur dioxide smoke produced commonly in our antimony smelters, the reducing-matting-smelting process, which is a new smelting process, was proposed. The effect of technical conditions such as smelting temperature, smelting time, the amount of pyrite cinder and additive on the direct recovery ratio of antimony were investigated by the method of single-factor experiment. The results show that the optimum conditions are that the reducing-matting smelting is carried out at 1100℃ for 2h, then the smelting temperature raise to 1200℃ for 50min. The amount of pyrite cinder is 1.2 times of its theoretical amount, the addition amount of soda and sodium sulfate is 5% and 24.2% to the amount of stibnite concentrate respectively, when the total amount of sodium is 10%. Under the optimum conditions, the direct and total recovery ratio of antimony is 87.02% and 97.79%, respectively, and the fixed ratio of sulfur is larger than 99%.
Key words: stibnite concentrate; reducing-matting smelting; sulfur fixation; clean metallurgy
金属锑的现代生产方法[1-4]可分为火法与湿法两大类, 目前以火法为主。 火法炼锑的主要工艺有挥发焙烧-还原熔炼、 挥发熔炼-还原熔炼[5]、 非挥发焙烧低温还原法[6]、 熔池熔炼连续烟化法[7]以及一些直接炼锑方法(如沉淀熔炼、 碱性熔炼、 反应熔炼、 造锍熔炼、 氢还原等)。 而湿法炼锑工艺按所用溶剂的性质又可分为碱性湿法炼锑和酸性湿法炼锑。 其中, 目前工业应用的湿法炼锑工艺主要是硫化钠浸出-硫代亚锑酸钠溶液电积法。 酸性湿法炼锑一般采用氯盐体系, 主要工艺有氯化浸出电积法、 新氯化水解法[8]、 氯化-干馏法[9]以及矿浆电解法[10-12]等。 目前, 由于我国主要采用鼓风炉挥发熔炼工艺, 普遍存在着严重的低浓度二氧化硫烟气污染。 随着经济发展和社会进步, 人们的环保意识日益增强, 严峻的环境污染形势也迫使各国政府迅速提高三废的排放标准。 因此, 能否有效地解决低浓度二氧化硫烟气的污染问题成为各火法炼锑厂生死存亡的关键所在。 对于低浓度二氧化硫烟气污染的治理, 方法各异, 工艺繁多, 但总体上看来主要有两种思路: 第一种是补救性的末端治理, 即将烟气进行脱硫处理, 主要分为用吸附剂进行吸附或转化(这是各国对低浓度SO2烟气的主要治理方法)和将低浓度SO2烟气直接制酸(具体有硫磺配气法、 非稳态法和托普索WSA工艺等); 第二种思路则着眼于环境治理上源头控制, 即开发清洁冶金新工艺, 从源头上彻底治理烟气污染。 前一种思路治标不治本, 虽能解决高空污染问题, 但低空污染依然存在, 且运营成本高昂, 投资大, 最后的尾气也难以达标排放, 还易造成产物的二次污染等。 因此, 为从根本上治理低浓度SO2烟气的污染, 必须改变传统火法炼锑工艺, 依据“绿色制造流程”和“无污染冶金”的原则, 重新开发一种高效率、 高效益和环境友好的一步火法炼锑新工艺。 本文作者提出了还原造锍熔炼一步炼锑新工艺[13-16], 即以黄铁矿烧渣为固硫剂, 将锑精矿中的硫固定于铁锍中, 使烟气中的SO2浓度远远低于国家排放标准。 显然, 这对消除我国炼锑行业中普遍存在的低浓度二氧化硫烟气污染具有重要意义。
1 实验
1.1 实验原料及试剂
实验所用的硫化锑精矿为锡矿山的硫化锑精矿和南丹茶山锑矿, 其化学成分如表1所列。
表1 硫化锑矿的化学成分
Table 1 Chemical composition of stibnite ore(mass fraction, %)

实验所用的辅助原料包括黄铁矿烧渣(A、 B两种)、 还原煤、 添加剂(苏打、 芒硝、 食盐)以及生石灰。 黄铁矿烧渣、 还原煤和生石灰的成分如表2所列, 所用添加剂均为工业级试剂。
表2 实验用辅助原料化学成分
Table 2 Chemical composition of assistant material(mass fraction, %)

1.2 实验设备和方法
熔炼实验设备为1台6kW的三相硅碳棒箱式马弗炉, 装原料的容器为石墨坩锅(直径为90mm, 高为70mm, 容积为445cm3)。 每次实验用天平称取100g硫化锑精矿, 按配料计算结果加入不同量的烧渣、 还原煤、 添加剂以及生石灰后, 研磨混匀, 装入石墨坩锅, 然后放入马弗炉中。 在各自实验条件下熔炼一定时间后, 将炉温升至1200℃保温一段时间后, 取出石墨坩锅, 在室温下急冷, 然后将金属锑、 铁锍及炉渣分离, 分别取样称量、 分析。
实验原则流程图如图1所示。
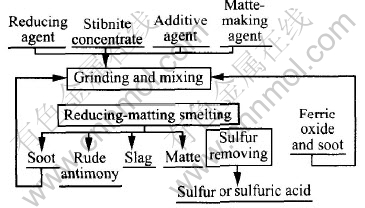
图1 硫化锑精矿还原造锍熔炼原则流程
Fig.1 Principle flow sheet for reducing-matting smelting of stibnite concentrate
2 实验原理
还原造锍熔炼的原理: 在1000~1300℃及有过剩碳质还原剂的情况下, 造锍剂中的高价态氧化物先被还原成低价, 然后FeO与硫化锑及碳质还原剂发生还原造锍反应, 生成粗金属或合金、 锍及炉渣, 反应式为
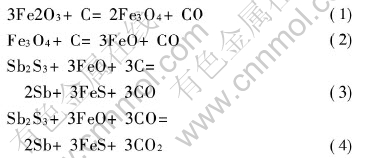
此外, 原料中的脉石成分与氧化亚铁反应, 生成熔点高、 粘度较大的多元炉渣。 添加剂也与硫化锑发生还原造锍反应, 反应式为
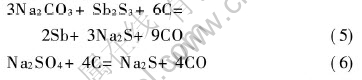
生成的硫化钠降低了炉渣及铁锍的熔点和粘度。
3 结果及讨论
3.1 熔炼温度的影响
按锑精矿、 煤粉、 纯碱、 无水芒硝和食盐的质量比为100∶20∶10∶5∶2配制炉料, 烧渣和石灰加入量为其理论量。 先在熔炼温度下反应120min, 再在10min内升温至1200℃, 保温澄清30min。
实验结果图2所示。 由图2可知, 当温度由800℃提高至1100℃时, 锑的直收率由65.72%增加至79.99%。 但当温度继续提高至1200℃时, 金属锑的直收率反而下降, 这主要是由于温度高于1100℃时, 金属锑的挥发显著增加所致。 由此可知, 在还原造锍熔炼过程中始终存在这样一对矛盾: 一方面是由于熔炼过程为还原过程, 需要大量的热量, 且较高的熔炼温度有利于FeO-SiO2-CaO三元渣的熔化。 降低其粘度和比重, 保持良好的流动性, 有利于炉渣与铁锍和粗锑的分层, 降低炉渣含锑量; 另一方面, 金属锑是一种比较容易挥发的金属, 过高的熔炼温度将使粗锑的挥发损失加剧。 为妥善解决这一矛盾, 本文作者一方面通过渣型的选择尽量降低三元渣的熔点、 粘度以及比重等物化性质; 另一方面采用两段温度制度, 即先在1100℃下进行熔炼反应, 再在1200℃的高温下进行澄清分层和放渣。
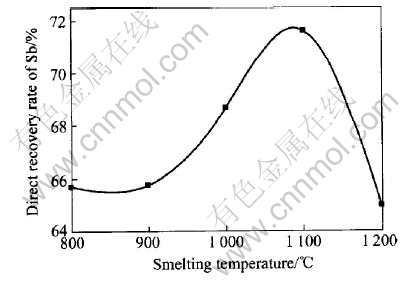
图2 熔炼温度对锑直收率的影响
Fig.2 Effect of smelting temperature on direct recovery rate of antimony
3.2 熔炼时间的影响
按上述配比配制炉料。 熔炼温度为1100℃, 保温温度为1200℃。 改变反应时间和保温时间, 考察它们对金属锑直收率的影响, 实验结果如图3所示。
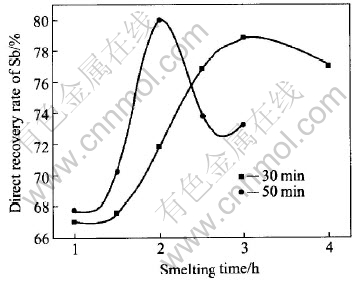
图3 熔炼时间对金属锑直收率的影响
Fig.3 Effect of smelting time on direct recovery rate of antimony
由图3可知, 不同的保温时间下, 金属锑直收率随反应时间的变化趋势有所不同。 当保温时间为30min时, 随反应时间的延长, 金属锑的直收率缓慢增加。 反应时间由1h增加至为3h时, 金属锑直收率也随之由67.04%上升至78.79%。 但此后继续延长反应时间, 金属锑的直收率反而下降, 这主要是由于金属锑的挥发加剧所致。 当保温时间为50min时, 金属锑的直收率对反应时间的变化要敏感的多。 在2h内, 金属锑的直收率迅速地增加至79.99%, 此后继续延长反应时间, 金属锑的直收率随之下降。 由此可以判断, 硫化锑精矿的还原造锍反应很迅速, 于1~1.5h内即可达到平衡。 当保温时间为30min时, 由于保温时间不够, 反应3h后才达到最高金属锑的直收率。 为了缩短熔炼时间, 提高生产效率, 同时追求最高金属锑直收率, 最佳反应时间为2h, 保温时间为50min。
3.3 烧渣加入量的影响
按上述配比配制炉料, 改变固硫所用的烧渣量, 造渣用的烧渣量和石灰加入量均为其理论值。 先在1100℃温度下反应2h, 再将炉温迅速升至1200℃, 并保温50min。 实验结果如图4 所示。
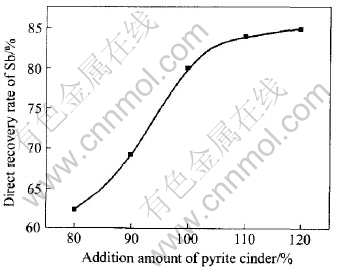
图4 烧渣加入量对金属锑直收率的影响
Fig.4 Effect of pyrite cinder addition amount on direct recovery rate of antimony
由图4可知, 烧渣的加入量对金属锑直收率的影响很大。 随着烧渣加入量的增加, 金属锑的直收率也随之显著上升; 但当固硫用的烧渣加入量超过理论量的110%后, 金属锑直收率的提高比较缓慢。 在实验中还发现, 随着烧渣加入量的增加, 炉渣的熔点和粘度也随之下降, 熔体流动性明显改善。 这说明由于体系的强还原性气氛使得炉渣成分偏离了选定渣型。 因此, 为了获得较高的金属锑直收率, 加入过量的烧渣是很必要的, 最终选定烧渣加入量为其理论量的120%。
3.4 添加剂加入量的影响
按锑精矿、 煤粉、 食盐的质量比为100∶20∶2的配比加入煤粉和食盐。 烧渣和石灰加入量为其理论量的120%。 熔炼温度为1100℃, 反应时间为2h, 在1200℃温度下保温50min, 分别控制总钠量为精矿量的4%、 8%和10%, 再改变苏打加入量, 考察不同添加剂加入量对熔炼过程的影响。 实验结果如图5所示。
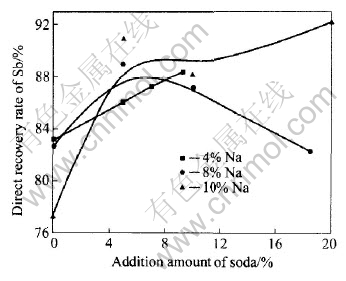
图5 苏打加入量对金属锑直收率的影响
Fig.5 Effect of soda addition amount on direct recovery rate of antimony
由图5可知, 添加剂加入量对熔炼过程的影响很复杂。 当总钠量固定不变时, 增加苏打的加入量, 金属锑的直收率随之上升, 但当总钠量为80%时, 苏打量超过一定量后, 金属锑的直收率反而下降。 由于加入添加剂的主要作用在于降低铁锍相的密度和熔点, 因此, 当总钠量小于8%时, 产物中并无单独铁锍相出现, 主要为金属锑和铁锍的混合物, 其中, 金属锑的含量小于40%。 如果不加硫酸钠而只加苏打时, 产生的铁锍很少且难以与金属锑分离。 这可能是由于加入的硫酸钠在熔炼过程中被碳还原成Na2S而进入铁锍相, 铁锍相中Na2S与FeS的相对含量影响铁锍的性质, 如密度、 熔点以及对金属锑的溶解度等。 根据实验结果, 综合考虑金属锑的直收率和产物分离的简便性, 苏打和芒硝的加入量为5%和24.2%(锑精矿的质量分数), 总钠量为精矿量的10%最合适。
3.5 最优条件综合实验
根据前面条件实验结果, 称取南丹锑矿200g, 进行最佳条件综合实验, 实验结果列于表3。 最佳条件实验的金属平衡列于表4。
从表3和4可以看出, 金属锑的直收率较高, 达到82.07%。 由于炉渣中含锑较低, 可以直接弃去, 但铁锍及烟尘中含锑较高, 需要返回熔炼工序, 这样金属锑的总回收率可达到97.79%。 粗锑中铁和硫的含量较高, 分别达到31.94%和8.68%, 需要设置单独的精炼工序。 按产物计算, 总的固硫率为99.20%, 基本消除了含硫气体对环境的污染。 原料中的银主要进入粗锑中, 银的直收率为77.65%, 总回收率为99.15%。 从理论上讲, 金的行为与银相似, 但由于原料中金的含量很低, 其在产物中分布比较分散。 主要是由于分析的准确性较差, 可靠性较低所致。
表3 最佳条件的实验产物量及其成分
Table 3 Mass of product and its chemical composition under optimum condition

表4 最佳条件实验的金属平衡
Table 4 Metal balance under optimum condition
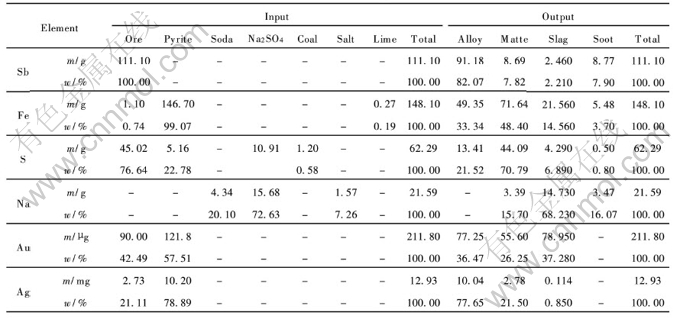
3.6 铁锍的处理
硫化锑精矿还原造锍熔炼的主要产物为粗锑、 铁锍、 炉渣及烟尘。 在这些产物中, 铁锍是一种重要的产物, 其主要成分为FeS和Na2S。 另外, 铁锍中Sb和Ag的含量也较高。 因此, 为了提高Sb和Ag的总收率, 必须将铁锍处理后返回熔炼工序。 由于含有硫化钠, 铁锍很容易吸水风化。 用水浸出硫化钠, 再用蒸发结晶法可得到硫化钠产品。 因此, 铁锍处理工艺的关键在于如何将其中的FeS转化为氧化铁并回收其中的硫。 总的看来, 将铁锍中的FeS转化为氧化铁有如下两种方法: 第一种方法是将FeS湿氧化为氧化铁和元素硫; 第二种方法则是将铁锍焙烧, 所得的高浓度SO2烟气用于制酸, 而氧化铁渣含有金属锑以及金银, 可返回熔炼工序以回收其中的有价金属。
4 结论
1) 熔炼温度、 时间以及造锍剂和添加剂加入量等因素对金属锑直收率有重大影响。 最佳的工艺条件: 先在1100℃下熔炼2h, 再迅速升温至1200℃保温50min, 烧渣加入量为其理论量的120%, 添加剂总钠量为精矿量的10%, 其中碳酸钠和芒硝加入量分别为精矿量的5%和24.2%。
2) 硫化锑精矿的还原造锍熔炼是可行的。 在最佳工艺条件下, 金属锑的直收率和总回收率可达到82.07%和97.79%, 固硫率为99.20%, 基本消除了含硫气体对环境的污染。
3) 原料中的银主要进入粗锑中, 银的直收率和总回收率分别为77.65%和99.15%。 从理论上讲, 金的回收与银相似, 但由于原料中金的含量很低, 其在产物中分布比较分散。
4) 粗锑中含铁为30%, 含硫为8%~9%, 需要进一步火法精炼处理以除去铁和硫。
REFERENCES
[1] 赵天从. 锑[M]. 北京: 冶金工业出版社, 1987. 95-99.
ZHAO Tian-cong. Antimony[M]. Beijing: Metallurgical Industry Press, 1987. 95-99.
[2] 王德润, 张 驾, 王钟慈, 等. 重有色金属冶炼设计手册(锡锑汞贵金属卷) [M]. 北京: 冶金工业出版社, 1995. 258-361.
WANG De-yun, ZHANG Jia, WANG Zhong-ci, et al. The Designation Handbook of Heavy Nonferrous Metal Smelting[M]. Beijing: Metallurgical Industry Press, 1995. 258-361.
[3] 杜 启, 张晓岚. 我国锑冶金技术的发展及其展望[J]. 锡矿山科技, 1996(2): 16-18.
DU Qi, ZHANG Xiao-lan. The development of antimony metallurgy technology and its prospect in our country[J]. Science and Technology of Xikuangshan, 1996(2): 16-18.
[4] 王成彦, 邱定蕃, 江培海. 国内锑冶金技术现状及进展[J]. 有色金属(冶炼部分), 2002(5): 6-10.
WANG Cheng-yan, QIU Ding-fan, JIANG Pei-hai. Status and development of antimony metallurgy technology in China[J]. Nonferrous Metals(Extractive Metallurgy), 2002(5): 6-10.
[5] 赵天从, 汪 键. 有色金属提取冶金手册(锡锑汞卷)[M]. 北京: 冶金工业出版社, 1999. 272-359.
ZHAO Tian-cong, WANG Jian. A Handbook for Extractive Metallurgy of Nonferrous Metals[M]. Beijing: Metallurgical Industry Press, 1999. 272-359.
[6] 孙克萍, 先晋聪. 锑的低温冶炼新工艺[J]. 有色金属(冶炼部分), 1996(1): 19-22.
SUN Ke-ping, XIAN Jin-cong. A new extractive process of antimony at low temperature[J]. Nonferrous Metals(Extractive Metallurgy), 1996(1): 19-22.
[7] 王吉坤, 雷 霆. 熔池熔炼-连续烟化法处理低品位锑矿研究[J]. 有色金属, 2000, 52(2): 44-48.
WANG Ji-kun, LEI Ting. Treating low grade antimony ore by bath smelting-continuous fuming process[J]. Nonferrous Metals, 2000, 52(2): 44-48.
[8] TANG Mo-tang, ZHAO Tian-cong, LU Jun-yue, et al. Principle and application of the new chlorination-hydrolization process[J]. J Cent Soth Univ Thenol, 1992, 23(4): 405-411.
[9] 唐谟堂. 氯化-干馏法的研究——理论基础和实际应用[D]. 长沙: 中南工业大学, 1986.
TANG Mo-tang. The Study on the Chlorination-Dry Distillation Process—Its Basic Theory and Application[D]. Changsha: Central South University of Technology, 1986.
[10] 邱定蕃. 矿浆电解[M]. 北京: 冶金工业出版社, 1999. 1-12.
QIU Ding-fan. Slurry Electrolysis[M]. Beijing: Metallurgical Industry Press, 1999. 1-12.
[11] 杨显万, 张英杰. 矿浆电解原理[M]. 北京: 冶金工业出版社, 2000. 52-55.
YANG Xian-wan, ZHANG Ying-jie. Slurry Electrolysis Theory[M]. Beijing: Metallurgical Industry Press, 2000. 52-55.
[12] 王成彦, 邱定蕃, 江培海. 复杂锑铅矿矿浆电解研究[J]. 矿冶, 2002, 11(3): 51-55.
WANG Cheng-yan, QIU Ding-fan, JIANG Pei-hai, et al. Study on slurry electrolysis for treating complex antimony lead concentrate[J]. Mining & Metallurgy, 2002, 11(3): 51-55.
[13] 唐谟堂, 唐朝波, 张多默. 一种无二氧化硫排放的有色金属冶炼方法-有色金属硫化矿及其含硫富集物料还原造锍熔炼[J]. 有色金属, 2000, 52(4): 58-60.
TANG Mo-tang, TANG Chao-bo, ZHANG Duo-mo. Nonferrous metal smelting process without SO2 formation-reducing-matting making—smelting of nonferrous metal sulfide ores and sulfur bearing material[J]. Nonferrous Metal, 2000, 52(4): 58-60.
[14] 唐朝波, 唐谟堂, 姚维义, 等. 脆硫铅锑精矿的还原造锍熔炼[J]. 中南工业大学学报, 2003, 34(5): 502-505.
TANG Chao-bo, TANG Mo-tang, YAO Wei-yi, et al. Reducing-matting smelting of jamesonite concentrate[J]. J Cent South Univ Thenol, 2003, 34(5): 502-505.
[15] 唐朝波. 还原造锍熔炼的理论及工艺研究[D]. 长沙: 中南大学, 2003.
TANG Chao-bo. Theory and Application Studies on reducing-matting Smelting[D]. Changsha: Central South University, 2003.
[16] TANG Chao-bo, TANG Mo-tang, YAO Wei-yi, et al. The laboratory research on reducing-matting smelting of jamesonite concentrate[A]. Proceedings 132th Annual Meeting and Exhibition[C]. Boston: TMS, 2003.
收稿日期: 2005-01-21;
修订日期: 2005-05-13
作者简介: 陈永明(1980-), 男, 硕士研究生.
通讯作者: 陈永明, 电话: 0731-8830470; E-mail: chenyming_307@sina.com.cn
(编辑 李艳红)