中央扩散式精矿喷嘴气粒混合特性数值模拟
孙彦文,艾元方,陈红荣
(中南大学 能源科学与工程学院,湖南 长沙,410083)
摘要:为解决中央扩散式精矿喷嘴生产时存在的下生料、塔体寿命缩短、氧利用率下降等问题,建立离散分散风孔型精矿喷嘴数学模型,数值模拟研究工艺风和分散风变化对喷嘴出口附近区域气粒混合流动的影响。结果表明:工艺风集中于圆环状柱体区域内流动;颗粒分散受控于分散风与工艺风动量比,动量比过小塔中心区域出现料柱、动量比过大塔近壁区域出现料环;小动量比可实现颗粒适度分散和气粒良好混合。喷嘴气粒混合仿真规律和冷模实验吻合。
关键词:中央扩散式精矿喷嘴;气粒混合;工艺风;分散风;闪速炉
中图分类号:TF811 文献标志码:A 文章编号:1672-7207(2014)11-3727-06
Numerical simulation on gas-particle mixing characters of CJD burner
SUN Yanwen, AI Yuanfang, CHEN Hongrong
(School of Energy Science and Engineering, Central South University, Changsha 410083, China)
Abstract: To solve the non-uniform gas-particle mixing problems such as the falling raw concentrate remain, shorter reactor shaft lifetime and less oxygen utilization at the high loading flash smelting process with a CJD burner, a mathematical model of a CJD burner with distribution air was built up. The changing rule of gas-particle mixing with the momentum ratio of distribution air to process air near the nozzle was simulated. The results show that the process air is concentrated inside the circular cone under the nozzle, the particle distribution is effectively controlled by the momentum ratio. Too smaller momentum ratio leads to the particles concentrated inside the cylinder center, and too large leads to the particles near the tower wall. The small distribution air can give a suitable distribution of particles and a moderate gas-particle mixing. This numerical simulation matches cold model test very well.
Key words: CJD burner; gas-particle mixing; process air; distribution air; flash smelting furnace
闪速炼铜已占全世界粗铜冶炼能力的50%[1]。闪速炉核心设备中央扩散式精矿喷嘴的气粒混合问题一直是铜冶炼行业研究的热点问题,在当今普遍实施的高强度闪速冶炼生产形势下尤为突出。现有喷嘴在加大投料量生产时,易出现下生料、塔体寿命缩短、氧利用率下降等气粒混合不佳的问题。数值模拟可揭示反应塔内气粒混合机理,为上述问题的解决提供有效的理论指导[2]。Koh等[3]发现颗粒入口速度大有利于塔内气粒混合,分散锥直径和角度影响颗粒分布。Debrincat等[4]发现200~7 000 μm结块固体以紊流形式存在,颗粒堆积程度影响颗粒分布。Solnordal等[5]仿真Olympic Dam闪速炉时发现计算结果对颗粒组分的粒度敏感。Higgins等[6]建立稳态轴对称模型,仿真塔内熔体颗粒的聚集情况,发现颗粒聚集程度主要受颗粒气流质量比、粒径和塔入口处湍流强度影响。在冶炼现场存在“分散风流量大”和“分散风流量小”等2种观点。Solnordal等[5, 7]采用CFX仿真发现气相运动在塔中心区域,颗粒运动也集中于塔中心区域。Sasaki[8]通过仿真发现颗粒呈伞状弥散分布于塔内,颗粒分散均匀有利于强化气粒混合。李欣峰等[9-10]采用CFX仿真发现颗粒轨迹呈伞状弥散分布。梅炽等[11]仿真研究提出高温、高颗粒浓度和高氧浓度等三集中的高效反应区观点。陈卓等[12-15]采用Fluent仿真发现投料速度增加时,气粒两相混合变差,塔内颗粒着火明显延迟等问题突出。塔内气粒混合过程具有影响因素多、反应慢、呈非线性和大滞后等多重特性[16],仿真结果的准确性取决于研究者对塔内气粒混合过程的正确理解。本文作者借助Fluent仿真平台,以喷嘴出口附近区域气粒混合为研究对象,建立中央扩散式喷嘴气粒混合冷模数学模型,数值模拟研究喷嘴2个主要影响因素即工艺风和分散风变化对喷嘴气粒混合流动的影响,并辅以喷嘴气粒混合冷模实验验证,以寻找闪速炉操作参数优化的有效途径方法,增强喷嘴在大投料量闪速冶炼中的适应性。
1 精矿喷嘴气粒混合仿真模型
1.1 物理模型简化
精矿喷嘴(图1)由工艺风通道、精矿粉通道、中央氧通道、分散风孔和分散锥组成。工艺风使物料沿塔内轴向运动,分散风使物料沿径向均匀分布,两者配比关系直接影响着颗粒分散和气粒混合结果。仿真计算主要侧重于喷嘴出口附近区域内常温气粒两相流动混合过程的解析,因此,物理模型包括闪速炉中央扩散型精矿喷嘴(CJD)、反应塔上部区域,即模型反应塔高0.683 m,直径为1.1 m,分散风通道简化为150 个均布小孔。采用混合网格结构(结构化网格+非结构化网格)划分,自喷嘴中心沿半径方向由密变稀。为保证计算精度,对喷嘴附近区的网格进行局部加密处理。
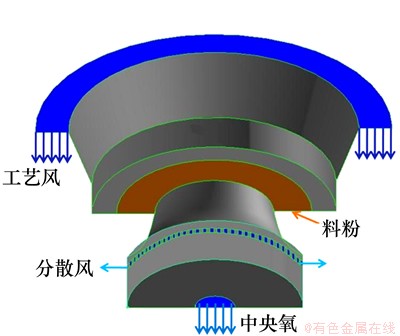
图1 CJD精矿喷嘴仿真模型
Fig. 1 Computational geometry of CJD burner
1.2 数学模型
气粒两相流仿真采用欧拉法来求解气相方程,通过拉格朗日法求解颗粒相方程,气粒两相通过PSIC方法进行耦合。将反应塔内气粒两相视为轴对称分布,且不存在切向运动(不存在旋转),气相守恒方程可表达成
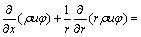
(1)
式中:
为通用因变量;
为输运系数;
为气相本身的源项;
为气粒两相相互作用产生的源项。每个方程中的
,
,
和
如表1所示。
颗粒从入口壁面注入,采用拉格朗日法求解颗粒
运动轨迹。以直角坐标系x方向为例,其控制方程可写为
(2)
式中:up为颗粒速度;u为气流速度;gx为重力加速度;Fx为颗粒相附加加速度项;
为颗粒密度;
为气流密度;FD(u-up)为单位质量颗粒所受拖曳力,
;CD为常数,
;dp为颗粒的平均直径;μ为连续相的黏度,Re为气流流过颗粒时的绕流雷诺数,
。
表1 通用方程中有关各项的组成
Table 1 Related forms in general equation
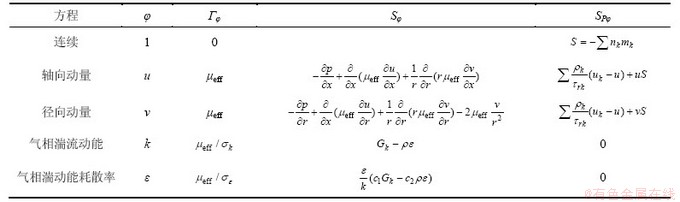
仿真颗粒密度为2.7 t/m3,最大粒径为0.25 mm,最小粒径为0.074 mm,采用 Rosin-Rammler方法计算质量平均粒径为0.132 mm。
分散风与工艺风动量配比影响气粒混合和颗粒分散结果。定义分散风与工艺风动量比为
(3)
式中:m为质量流量;v为风速;r为密度;V为体积流量。下标p为工艺风,d为分散风。
2 仿真计算结果整理分析
选取了相同动量比工况1组,不同动量比6组工况(见表2)研究不同配风条件下气粒混合流动和颗粒分散规律。
2.1 气相速度分布
图2所示为变化动量比条件下气相速度分布云图,图3为图2对应工况反应塔出口面轴向速度曲线图,其中图6(a)和图6(c)动量比相同,图6(b),图6(c)和图6(d)动量比不同。
表2 仿真模型操作参数
Table 2 Operation parameters of numerical model
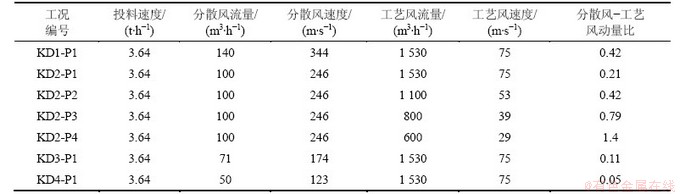
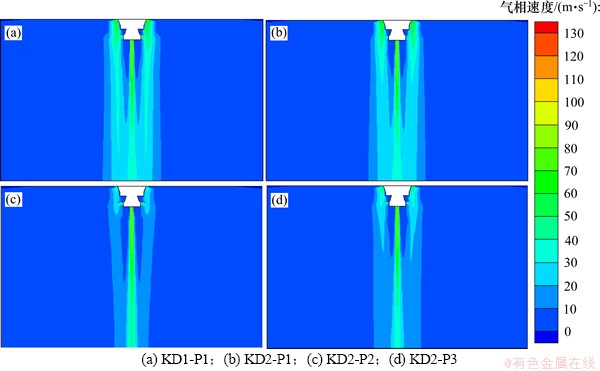
图2 变化动量比时气相速度分布云图
Fig. 2 Velocity contours at varied momentum ratios
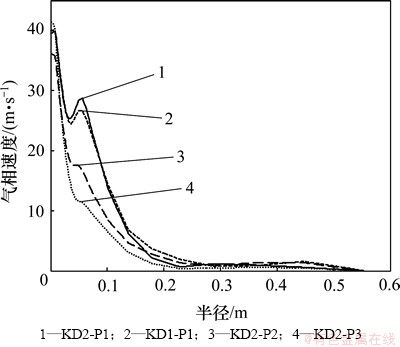
图3 塔出口面速度分布
Fig. 3 Velocity at outlet of flash furnace
在中央氧作用下,反应塔中心区域气流速度大。除反应塔轴线上速度最大外,沿径向向外还存在另一个速度峰值,即在气粒两相流作用下喷嘴正下方存在中空的环形工艺风射流。对K=0.42的2个工况相比较,工艺风都是集中于喷嘴正下方环形区域内流动,环形射流外轮廓明显,外径相近,以气流速度10 m/s为界,环形射流外径约为0.26 m。在相同工艺风流量条件下,K越大,环形射流外径越小。随着K增加,工艺风环形射流形状由圆柱状逐渐变化到底部渐缩的倒锥状。K=0.21时环形射流外径约为0.27 m,K=0.42时环形射流外径约为0.26 m,K=0.79时环形射流外径约为0.15 m,环形射流底部呈明显的渐缩状,这说明气粒两相流作用下的工艺风主要集中于塔内喷嘴正下方环状柱体区域流动。分散风和工艺风动量比决定工艺风环形射流直径,动量比越大,环形射流区域越小。气粒两相流作用下的颗粒分布集中于环状工艺风环形射流内则达到气粒混合良好效果,因动量比过小,颗粒被限制在工艺风环形射流内圆以内的塔中心区域流动,或因动量比过大颗粒穿过工艺风环形射流在射流外圆以外区域流动,均会出现气粒混合不佳问题。
2.2 颗粒相分析
变化动量比条件下颗粒运动轨迹如图4所示,反应塔出口面颗粒浓度分布如图5所示。
由图4可见:气粒两相流作用下颗粒能沿半径方向呈辐射伞状均匀分散运动。当K相同(K=0.42)在大分散风时,颗粒扩张角约为110°,下落约0.4 m后碰触反应塔壁;小分散风时,颗粒扩张角约为90°,且因回流近壁区细微颗粒处于悬浮状态。颗粒穿过工艺风环形射流后受工艺风环形射流影响小。在大分散风作用下,颗粒能穿过工艺风环形射流,并借助自身惯性而向外运动至触及塔壁。在相同工艺风条件下,K增加,颗粒扩张角增大,颗粒分散越远。K=0.21时颗粒扩张角约为65°,塔出口面料锥外延距塔壁0.2 m;K=0.79时,颗粒扩张角约为125°,下落约0.35 m后碰触塔壁,且细微颗粒悬浮更明显。K增大,分散风作用加大,颗粒径向运动作用力加强,颗粒径向射程变大。过大的动量比会导致颗粒冲出工艺风环形射流,烟尘率增加,高温颗粒冲刷腐蚀塔壁。
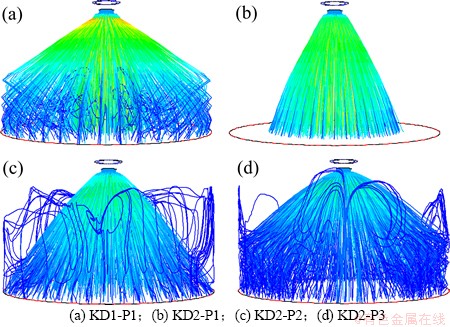
图4 变化动量比时颗粒运动轨迹
Fig. 4 Particle tracks at varied momentum ratios
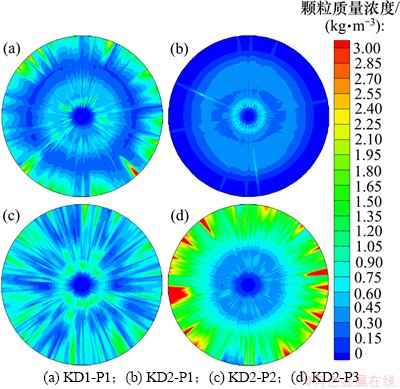
图5 变化动量比时颗粒相质量浓度云图
Fig. 5 Particle concentration contours at varied momentum ratios
由图5所见:4个工况射流型的高颗粒质量浓度在集中区域出现,是分散风出口为均匀分布的离散型
小孔而非水平风环[12-15]所致。把塔出口面划分为塔轴线、塔中心、塔中间和塔近壁4个同心圆或圆环区域,分析颗粒分布规律。4个工况塔轴线区域都是颗粒极少,说明中央氧流量可以调小。K=0.42时2个工况颗粒分布不同。图5(c)中,分散风和工艺风流量小,颗粒分布均匀。图5(a)中,分散风和工艺风流量大,颗粒分布于塔中心区域和塔近壁区域,环状塔中间区域颗粒少,颗粒分布不均匀。在相同工艺风条件下,K增大,颗粒分布越宽。当K=0.21时,颗粒分布集中于塔中心区域,近塔壁区域颗粒少;当K=0.42时,颗粒分布均匀;当K=0.79时,颗粒分布集中于近塔壁区域,塔中心区域颗粒少。颗粒分布调节性良好,分散风与工艺风动量比是颗粒分布主要影响因素,动量比由小变大,颗粒分布由集中于塔中心(过度集中)区域变到集中于塔近壁(过度分散)区域。
气粒流量比在化学当量比附近,能促使塔内气粒混合反应完全。综合图2和图5可知:当K=0.42时,2个工况气粒混合不佳;小分散风和小工艺风流量工况环状塔中间区域工艺风略微过剩,塔近壁区域有颗粒无工艺风;在大分散风和大工艺风流量工况下,环状塔中间区域有工艺风无颗粒,塔近壁区域有颗粒无工艺风;在相同工艺风流量条件下,K从0.21增大到0.79,环状塔中间区域工艺风颗粒混合良好逐渐变化到颗粒相对于工艺风过剩,塔近壁区域逐渐增多的颗粒找不到工艺风混合。分散风与工艺风动量比小,有利于塔内气粒混合良好,不会出现工艺风过剩或颗粒过剩现象,但过小的动量比会导致颗粒穿透工艺风射流能力差而出现“中心料柱”现象。结合图2所示的工艺风分布规律,合适的动量比应达到使颗粒主要分布于塔中心区域,其次塔中间区域的颗粒适度分布效果。“分散风流量小”的现场操作参数有利于塔内气粒混合。
3 喷嘴数学模型准确性验证
按同心圆布置方式在反应塔出口面上布置49个网格进行接粒。定义质量偏析函数,表征反应塔出口面上颗粒分布整体均匀性:
(4)
式中:
,无因次变量;
为第i网格颗粒质量分数,
;
为第i网格面积分数,
。
定义喷嘴正下方中心区颗粒质量分数
,表征中心颗粒的聚集程度为:
(5)
将文献[2]中24个实验工况的分散风和工艺风流量转化成动量比形式。K变化时px和xcent仿真与实验对比分别如图6和图7所示。
由图6和图7可见:模拟结果与文献[2]变化趋势基本一致,说明喷嘴气粒混合数学模型准确,仿真结果可信;随着K增加,px更小,xcent更小,喷嘴正下方颗粒分布更少,塔出口面上颗粒分布整体上更均匀,但仿真px和xcent均比实验结果偏小。这是仿真模型简化、喷嘴加工安装存在误差、管道气流局部阻力和沿程阻力损失、实验操作等因素所致。
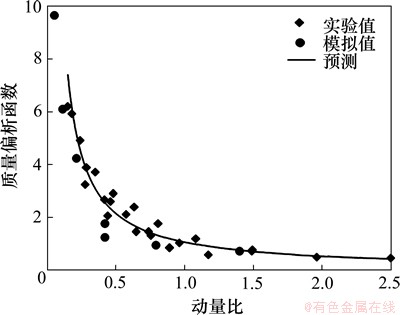
图6 动量比对颗粒均匀性的影响
Fig. 6 Effect of momentum ratio on mass uniformity

图7 动量比对中心颗粒质量分数的影响
Fig. 7 Effect of momentum ratio on central mass fraction
4 结论
1) 建立中央扩散式精矿喷嘴离散分散风孔数学模型,用于研究工艺风和分散风变化对喷嘴出口附近区域气粒混合流动的影响规律,寻找到合理的闪速炉操作参数优化方案。
2) 塔内颗粒分布调节性良好,颗粒分布主要受到分散风与工艺风动量比控制。动量比增大,颗粒分布逐渐接近塔近壁区域;动量比过小,塔中心区域出现“中心料柱”,颗粒过度集中;动量比过大,塔近壁区域出现“近壁料环”,颗粒过度分散;合适的动量比使颗粒主要分布于塔中心,其次为塔中间区域。
3) 分散风与工艺风动量比小,有利于塔内气粒混合良好,避免塔中心生料堆和氧利用率低等问题出现,“小分散风”方案可以提高现场操作参数优化效率。喷嘴气粒混合实验结果与仿真结果一致。
参考文献:
[1] Boryczko B, Donizak J, Hoida A, et al. Comparison of shaft and flash smelting processes of copper production using thermo-ecological cost method[C]// ECOS 2006: Proceedings of the 19th International Conference on Efficiency, Cost, Optimization, Simulation and Environmental Impact of Energy Systems Athens: ICECOPSEIES, 2006: 663-668.
[2] 宋修明, 陈卓. 闪速炼铜过程研究[M]. 北京: 冶金工业出版社, 2012: 46-88.
SONG Xiuming, CHEN Zhuo. Research of copper flash smelting process[M]. Beijing: Metallurgical Industry Press, 2012: 46-88
[3] Koh P T L, Jorgensen F R A, Elliot B J. Solids falling in flash furnace burner concentrate chutes[J]. Int J Miner Process, 2007, 83: 81-88.
[4] Debrincat D P, Solnordal C B, Van J S J. Deventer. Influence of particle properties on the size of agglomerated metallurgical powders[J]. Miner Process, 2008, 87(1/2): 17-27.
[5] Solnordal C B, Jorgensen F R A, Koh P T L, et al. CFD modelling of the flow and reactions in the Olympic Dam flash furnace smelter reaction shaft[J]. Applied Mathematical Modelling, 2006, 30(11): 1310-1325.
[6] Higgins D R, Gray N B, Davidson M R. Simulating particle agglomeration in the flash smelting reaction shaft Original[J]. Minerals Engineering, 2009, 22(14): 1251-1265.
[7] Koh P T L, Nguyen T V, Jorgensen F R A. Numerical modelling of combustion in a zinc flash smelter[J]. Applied Mathematical Modelling, 1998, 22(11): 941-948.
[8] Sasaki Y. Prediction of combustion phenomena in flash smelting furnace for production enhancement using a mathematical model[C]// Int Symp Advanced Processing of Metals and Materials. Int Symp on Sulfide Smelting. Sohn, California: Wiley Press, 2006, 8: 545-559.
[9] 李欣峰, 梅炽, 张卫华. 铜闪速炉数值仿真[J]. 中南工业大学学报(自然科学版), 2001, 32(3): 262-266.
LI Xinfeng, MEI Chi, ZHANG Weihua. Simulation of copper flash smelter[J]. Journal of Central South University of Technology (Science and Technology), 2001, 32(3): 262-266.
[10] LI Xinfeng, PENG Shiheng, HAN Xiangli, et al. Influence of operation parameters on flash smelting furnace based on CFD[J]. Journal of University of Science and Technology, 2004, 11(2): 115-119.
[11] 梅炽, 谢锴, 陈红荣. 闪速炼铜“高效反应区”的形成条件与应用效果[J]. 有色金属, 2003, 55(4): 85-88.
MEI Chi, XIE Kai, CHEN Hongrong. Generating condition and applying results of high efficiency reaction core in copper flash smelting[J]. Nonferrous Metals, 2003, 55(4): 85-88.
[12] CHEN Zhuo, WANG Yunxiao. Simulation study of intensified flash smelting process[C]// Copper, 2010. Hamburg, Germany: DGBM, 2010: 1313-1323.
[13] 陈卓, 王云霄, 宋修明, 等. 高投料量下炼铜闪速炉内熔炼过程的数值模拟[J]. 中国有色金属学报, 2011, 21(11): 2916-2921.
CHEN Zhuo, WANG Yunxiao, SONG Xiuming, et al. Numerical simulation of smelting process in copper flash smelters at high loading rate[J]. Chinese Journal of Nonferrous Metals, 2011, 21(11): 2916-2921.
[14] 陈卓, 毛永宁, 赵荣升, 等. 闪速炉熔炼配风对反应过程的影响[J]. 中南大学学报(自然科学版), 2012, 43(2): 730-737.
CHEN Zhuo, MAO Yongning, ZHAO Rongsheng, et al. Influences of reaction air parameters on smelting process in flash furnace[J]. Journal of Central South University (Science and Technology), 2012, 43(2): 730-737.
[15] 陈卓, 殷术贵, 周俊, 等. 铜闪速炉分散风旋流喷吹的数值模拟[J]. 过程工程学报, 2012, 12(2): 1-8.
CHEN Zhuo, YIN Shugui, ZHOU Jun, et al. Numerical simulation of copper flash smelting process with rotarily distributed air[J]. The Chinese Journal of Process Engineering, 2012, 12(2): 1-8.
[16] MEI Chi, ZHOU Jiemin, PENG Xiaoqi, et al. Simulation and optimization of furnaces and kilns for nonferrous metallurgical engineering[M]. Berlin: Springer, 2010: 221-232.
(编辑 邓履翔)
收稿日期:2013-12-19;修回日期:2014-03-28
基金项目(Foundation item):国家高技术研究发展计划(“863”计划)项目(2010AA065200);中南大学中央高校基本科研业务费专项资金资助项目(2012zzts087) (Project(2010AA065200) supported by the National High-technology R&D Program (“863” Program), China; Project(2012zzts087) supported by the Basic Research Foundation for Central Universities, China)
通信作者:艾元方(1968-),男,湖南邵阳人,博士,副教授,从事可控燃烧反应机理与技术研究;电话:13574170397;E-mail: yfai@csu.edu.cn