
Reduction mechanism of natural ilmenite with graphite
WANG Yu-ming(王玉明)1, 2, YUAN Zhang-fu(袁章福) 1, 3, GUO Zhan-cheng(郭占成)1,
TAN Qiang-qiang(谭强强)1, LI Zhao-yi(李肇毅)2, JIANG Wei-zhong(姜伟忠)2
1. State Key Laboratory of Multi-phase and Complex Systems,
Institute of Process Engineering, Chinese Academy of Sciences, Beijing 100190, China;
2. Institute of Ironmaking Research, Baoshan Iron and Steel Co., Ltd, Shanghai 201900, China;
3. Department of Energy and Resources Engineering, College of Engineering, Peking University,
Beijing 100871, China;
Received 28 November 2007; accepted 7 April 2008
Abstract: Reduction of Bama ilmenite concentrate containing 49.78% TiO2 and 27.96% total Fe by graphite was studied using thermogravimetric analysis system under argon gas ambient from 850 to 1 400 ℃. The reduction degree of Bama ilmenite is enhanced with increasing temperature and the molar ratio of carbon to oxygen, and the reaction rate varies with temperature and reduction time simultaneously. The phase transformation, chemical composition, microstructure and morphology of reduced samples were investigated by using X-ray diffractometry, scanning electron microscopy, and energy disperse spectroscopy, respectively. The high content of impurities in Bama ilmenite evidently bates the reduction of ilmenite. Forming the enrichment zone of manganese prevents complete reduction of Fe2+. The reduction products are mostly reduced iron, rutile, reduced rutiles, Ti3O5 and pseudobrookite solid solution. The reduction kinetics was also discussed. The results show that the reduction temperature is a key factor to control reaction rate.
Key words: Bama ilmenite; reduction; thermogravimetry; impurity; kinetics
1 Introduction
Ilmenite(FeTiO3), iron titanate naturally occurring, is an important and abundant mineral. As sources of high-grade titanic mineral decrease worldwide, the processes involving low-grade minerals such as ilmenite are given more attention. However, due to the high content of impurities, especially iron oxides, it is necessary to be refined to obtain titanium-rich material [1]. The demand for titanium is increasing in aerospace and commercial applications. Furthermore, the demand for titanium dioxide which is widely used is increasing rapidly in paper, plastics and pigment industries[2]. Ilmenite gradually becomes an alternative raw material for natural rutile.
Over the past several decades, many studies have been conducted on the mechanism and kinetics of the reduction of ilmenite. WOUTERLOOD[3], EL- GUINDY and DAVENPORT[4], SURESH et al[5-6] investigated the reduction of ilmenite with carbon. WOUTERLOOD[3] conducted experiments from 900 to 1 200 ℃ and found that the reaction consisted of a fast first stage representing the reduction of ferric to ferrous iron, and a slower second stage in which ferrous iron was reduced to metallic iron. In GUINDY and DAVENPORT’s experiments[4], the reaction had been observed to initiate near 950 ℃, and gas diffusion was the rate-controlling step in the temperature range of 1 075-1 140 ℃. Carbothermic reduction of synthetic and weathered ilmenite was investigated by SURESH et al[5-6] from 1 000 to 1 100 ℃, in which the rate of reduction and the size of iron particles were found to decrease with increasing degree of weathering of the concentrate. Many workers[7-13] studied the systems of Fe-Ti-O and Fe-Mn-Ti-O. It was found that the reduction path for pure ilmenite predicted by the Fe-Ti-O phase diagram was not followed by natural ilmenite because of presence of manganese. GIOVANNI and his coworkers[14-15] employed different reductive gaseous agents H2, CH4, NH3 and H2O to investigate the high temperature reduction of ilmenite in order to acquire the oxygen production from lunar materials. Ilmenite reduction with carbon monoxide had been studied intensively by a few research groups[16-20]. The reduction rate increased with increasing temperature. However, the rate and the degree of reduction depended on the formation of a metallic shell of iron which inhibited the transfer of CO to the reaction zone. EUNGYEUL and OLEG[21], SUN et al[22-23] and ZHAO and SHADMAN[24] examined the reduction of ilmenite by hydrogen in which the reduction proceeded through the stages of ferric to ferrous iron and ferrous iron to metallic iron. Diffusion of gaseous species through product layer and intrinsic chemical reaction were rate controlling factors during reduction.
The aim of the present work is to investigate the effect of temperature on the reduction rate and degree, the changes of phase composition, the morphology and the reductive kinetics in the reduction process.
2 Experimental
The chemical compositions of Bama ilmenite concentrate as raw material are listed in Table 1. Graphite (98% fixed carbon) is used as reductant.
Table 1 Chemical compositions of ilmenite concentrate (mass fraction, %)
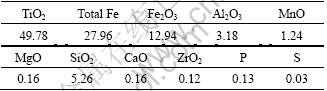
Bama ilmenite was ground and screened for particle size range of 71-150 μm. Graphite powder was supplied in the size range of 100-150 μm. The phase characteristics of ilmenite samples were obtained by XRD (Philips 1140, Cu Kα, current 40 mA, voltage 30 kV). The microzone chemical composition was analyzed by EDS (JSM-6301F, America).
The ilmenite and graphite were thoroughly mixed by stirring over 30 min. The mixtures containing adhesive were pressed in a closed die of 9 mm in diameter under 15 MPa to produce cylindrical pellets with mass of about 2 g and height of 8 mm.
Fe2O3·3TiO2+3C→2Fe+3TiO2+3CO (1)
FeO·TiO2+C→Fe+TiO2+CO (2)
According to reactions (1) and (2), in order to make all oxygen from Fe2O3 and FeO convert to CO, the molar ratio of C to double O (n(C)/n(O2)=2) from iron oxides should be 2. According to that, the ilmenite-graphite mixtures were adjusted for converting all the oxygen to carbon monoxide. The experiment was conducted in an electric furnace. In the heating process, the schematic diagram of the thermogravimetric apparatus is shown in Fig.1. It consisted of a vertical tubal furnace, a computer monitor system and a Pt-Rh thermocouple. The ilmenite-graphite pellets were heated in an alumina crucible suspended in the argon ambience furnace tube. The flow rate of argon in the tube was 1 L/min. When the experiments were finished, the samples were withdrawn from the furnace and quenched in water, and mass loss was determined at different temperatures.
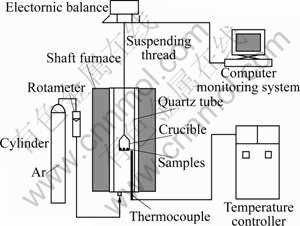
Fig.1 Schematic diagram of apparatus
3 Results and discussion
During the reduction of Bama ilmenite by graphite, an direct correlation between total mass loss and oxygen loss could be assumed since the gas resultants mainly consist of CO of more than 99%. The percentage(W) of total mass loss was calculated by
(3)
where wt is the mass of sample after time t, and w0 is starting mass of sample after removal of moisture and volatile matter, and w is the total possible mass loss for the reduction of Bama ilmenite by graphite. According to reactions (1) and (2) and Table 1, if the iron oxides were reacted fully, the total possible mass loss w is 0.136 w0 (w=0.136 w0).
The porous samples after the reduction were analyzed. The reduction kinetics is discussed in detail as follows.
3.1 Effect of temperature
Plots of the degree of the ilmenite reduction by graphite as a function of time are shown in Fig.2 and Fig.3. Temperature obviously influences the reduction rate and degree. With increasing temperature, the reduction rate increases. At constant temperature from 1200 to 1 400 ℃, initially the reduction proceeds rapidly. After 30 min only a gradual increase in reduction is observed. At high reduction temperatures, the oxygen removal increases with increasing the temperature although in practice the reduction of iron is generally not complete and reduction of rutile will occur. Fig.2 shows that the reaction rate becomes negligible after 2 h from 850 to 1 000 ℃. And the reduction degree remains less than 42%. It can be seen from Fig.3 that the reduction is not still complete after heating for 2 h at 1 300 ℃. The reduction degree reaches more than 90% after heating for 40 min at 1 350 and 1 400 ℃.
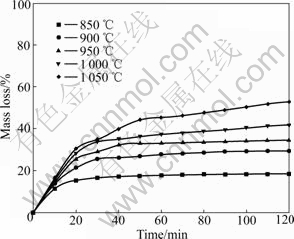
Fig.2 Effect of temperature on reduction of ilmenite with graphite from 850 to 1 050 ℃
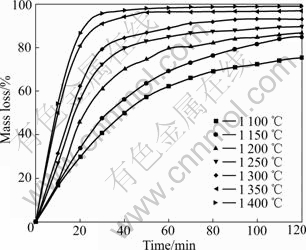
Fig.3 Effect of temperature on reduction of ilmenite with graphite from 1 100 to 1 400 ℃
The above results suggest that the reduction of ilmenite ore is inadequate below 1 000 ℃. And the significant reduction occurs above 1 000 ℃. The results are in agreement with the study of earlier workers[6,25]. Compared with the study of WOUTERLOOD[3], the reduction degree of Bama ilmenite is lower owing to the high content of impurities including manganese, silica and aluminum oxides. It is known that manganese and aluminum oxides inhibit the reduction kinetics of the ilmenite due to the barrier effect, which yields a lower reduction degree[6,26]. Above 1 100 ℃, it has been concluded that the reaction is brought about by carbon monoxide which acts as a gaseous medium in the reduction with carbon. During the Bama ilmenite reduction, Mn2+ replacing Fe2+ firstly diffuses at the reaction interface. Then the Mn2+ enrichment zone baffles carbon monoxide diffusion to result in lower activity of Fe2+. Finally, the manganese ion concentration becomes so high and the iron ion activity becomes so low that Fe2+ is impossibly reduced to the metallic iron. The silica oxide also inhibits reduction due to the formation of fayalite during the reduction process, which decreases the reactivity of the iron oxides. Compared with the study of LI et al[2], the reduction degree of the ilmenite is higher due to the lower content of impurities such as magnesium and calcium oxides. However, magnesium oxide has somewhat larger effect on the reduction kinetics than manganese oxide. This might be due to the fact that magnesium oxide forms a more stable solid solution with titanium and iron oxide than manganese oxide.
3.2 Effect of reductant content
Effect of graphite content on the reduction of Bama ilmenite was studied by reaction of ilmenite with graphite at 1 100 ℃. The molar ratio of carbon to oxygen varied from 2 to 6. The reduction curves are presented in Fig.4.
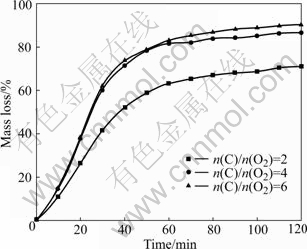
Fig.4 Effect of graphite content on reduction at 1 100 ℃
As shown in Fig.4, increase in the molar ratio of carbon to oxygen from 2 to 4 causes a sharp increase in the reduction rate and the reduction degree is enhanced by approximately 20%. But further increase to 6 has a relatively slight effect. In fact, when carbon content is improved, the Boudouard reaction proceeds at a much faster rate to provide the reductant CO. This is also probably caused by the shortening of the diffusion paths for CO that is created by reaction between Bama ilmenite particles and carbon particles when an ore particle is well surrounded by carbon particles.
3.3 Phase transformation during reduction of ilmenite
In the Bama ilmenite reduction, the phases of the samples were analyzed by XRD. Fig.5 shows that the mineral composition of Bama natural ilmenite ore is principally ilmenite and partly pseudorutile. Fig.6 shows the intensity for graphite decreases but that for ilmenite increases, and the peaks of rutile and iron emerge but those of pseudorutile disappear when the sample is reduced for 1 h at 1 000 ℃. The intensity for graphite decreases further and that for iron increases. The intensity for ilmenite decreases when the sample is reduced for 2 h at 1 000 ℃. The phase analysis results of the reduced samples are given in Table 2, Fig.6 and Fig.7, respectively. The samples contain the same phases including iron, ilmenite, rutile, and graphite after being reduced for 2 h at 900 and 1 000 ℃. But the pseudorutile phase disappears at 1 000 ℃. However, the reduced rutiles appear and the trace of pseudorutile is not found at 1 100 ℃. At 1 200 ℃, the ilmenite phase disappears, and pseudobrookite solid solution and Ti3O5 appear. No ilmenite is observed at 1 300 and 1 400 ℃; instead, a Ti3O5 phase is found together with iron, reduced rutiles, Fe3C and pseudobrookite solid solution.
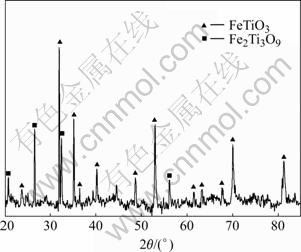
Fig.5 XRD pattern of Bama natural ilmenite
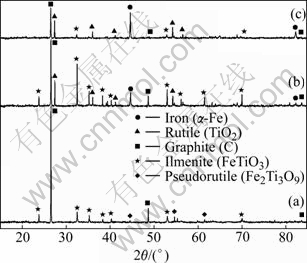
Fig.6 XRD patterns of samples before and after reduction: (a) Sample before reduction; (b) 1 000℃, 1 h; (c) 1 000℃, 2 h
Table 2 X-ray diffraction analysis results of reduced samples
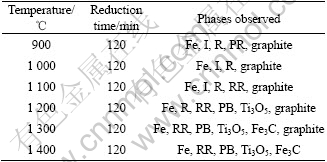
Fe—Metallic iron; I—Ilmenite (FeTiO3); R—Rutile (TiO2); PR—Pseudorutile (Fe2Ti3O9); RR—Reduced rutiles (Ti5O9, Ti4O7); PB—Pseudobrookite (Fe2TiO5) solid solution
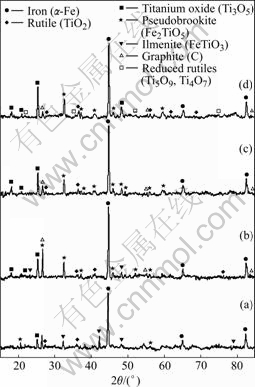
Fig.7 XRD results of reduced samples at 1 200 ℃ for different reduction time: (a) 0.5 h; (b) 1.0 h; (c) 1.5 h; (d) 2.0 h
From 900 to 1 400 ℃, as listed in Table 2, the ilmenite is reduced and iron, rutile, reduced rutiles, Fe3C and M3O5 are formed (where M represents a combination of iron and titanium). At 1 200 ℃, it is shown in Fig.7 that the intensity for iron increases with reduction time increasing. The rutile is still present when the samples are reduced for 2 h. The ilmenite phase disappears after reduction for 1 h. X-ray diffraction pattern indicates the presence of pseudobrookite structure with d-spacing characteristic of M3O5 solid solution (M=Fe, Ti, Mn, Mg, etc). In M3O5, the manganese and magnesium, despite their low concentration, tie up a large amount of irons, which remain unreduced. Due to the impurities of manganese and magnesiums, the composition of solid solution is stable at 1 200 ℃.
3.4 Energy disperse spectroscopy analysis
SEM images of the samples after being reduced for 2 h at 1 200 and 1 100 ℃ are shown in Fig.8 and Fig.9, respectively. The micrographs reveal three distinct regions which appear as bright, dark gray and black phases. To identify the present phases, EDS was performed at regions marked in SEM image of Fig.8. The results of EDS analysis show that region 1 consists of approximately 96.87% Fe and 3.13% Ti, so the bright phase is primarily iron phase. Region 2 is made up of approximately 4.69% Fe and 95.31% Ti with little amounts of aluminum, vanadium and manganese. Therefore, the dark gray phase is mainly titanium oxides. Region 3 consists of approximately 67.76% C, 20.45% Ti and 9.48% Si. The black phase is mainly carbon phase mixed with some carbides. However, the coalescence of grains is observed in the sample reduced for 2 h at 1 200 ℃. The EDS analysis of the samples indicates that the phase enriched in titanium is depleted in iron and vice versa. This confirms the high degree of segregation of Fe and TiO2 of the reduction samples.
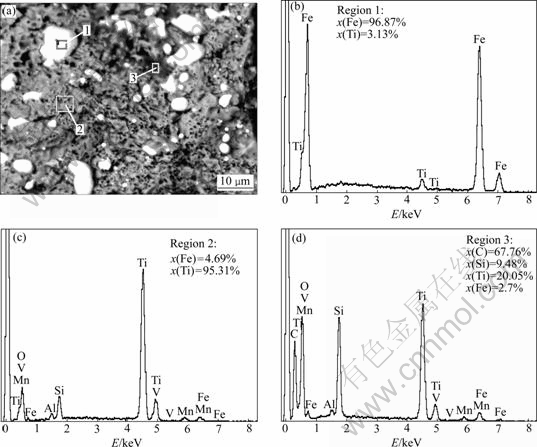
Fig.8 SEM image (a) of reduced sample at 1 200 ℃ and EDS results of regions 1 (b), 2 (c) and 3 (d)
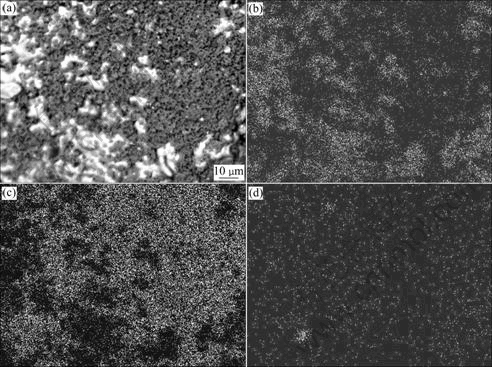
Fig.9 SEM images of reduced sample at 1 100 ℃: (a) Morphology; (b) Fe Kα X-ray mapping; (c) Ti Kα X-ray mapping; (d) C Kα X-ray mapping
X-ray Kα mappings of iron, titanium and carbon are shown in Fig.9. Figs.9(b-d) show the distribution of main elements in SEM image of Fig.9(a). These three maps confirm the forgoing analyses. It is seen from three maps that the products of Fe and TiO2 have good segregation. The reductant carbon is incompletely reacted.
3.5 Reaction kinetics
According to the solid-state kinetics, chemical reaction at the interface is the rate-controlling factor. This leads to the equation[3]:
1-(1-x)1/3=kt (4)
where x is fractional reduction, t is time and k is rate constant. If diffusion process controls the reaction, the following equation is gotten:
1-2/3x-(1-x)2/3=kt (5)
Both chemical reaction and diffusion have a controlling influence upon the reaction. The equation is of the following form:
3k1[1-(1-x)1/3]+3/2k2[1-2/3x-(1-x)2/3]=t (6)
Based on the foregoing results of Fig.2 and Fig.3, by applying the solid state kinetics equations, the plots of curve-fitting are shown in Fig.10 and Fig.11. As shown in Fig.10, experimental values are in agreement with simulated results over 120 min below 1 150 ℃. Therefore, chemical reaction equation has a good applicability and chemical reaction is the rate-controlling step below 1 150 ℃. Fig.11 shows that experimental results are consistent with simulated ones for the reaction time less than 100 min at 1 200 ℃, 50 min at 1 250 ℃, 40 min at 1 300 and 1 350 ℃, and 30 min at 1 400 ℃. Because the reaction is nearly completed during the period, diffusion equation has a good applicability and diffusion controls the reaction above 1 200 ℃. The natural logarithms are used to calculate the activation energies of reduction reaction according to Arrhenius equation. As shown in Fig.12, the activation energies are 265 kJ/mol and 157 kJ/mol below 1 150 ℃ and above 1 200 ℃, respectively.
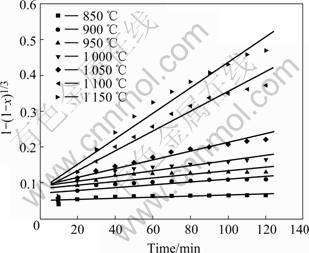
Fig.10 Applicability of chemical reaction model
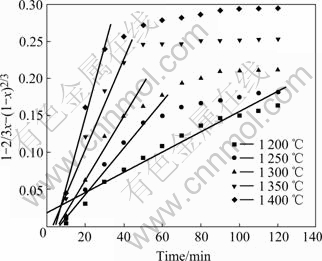
Fig.11 Applicability of diffusion model
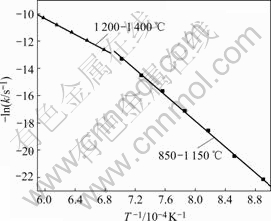
Fig.12 Arrhenius plot of reduction reaction
4 Conclusions
1) The reduction degree decreases owing to the impurities in Bama ilmenite. Manganese and aluminum oxides form an enrichment zone that baffles complete reduction of Fe2+.
2) The reduction rate and degree increase with the molar ratio of carbon to oxygen up to 4. However, the effect is negligible with the further increase of the molar ratio.
3) The phase of reduced products consists of iron, ilmenite, rutile, reduced rutiles, pseudorutile and graphite below 1 200 ℃. But the reduced rutiles are absent from 900 to 1 000 ℃. Above 1 200 ℃, a Ti3O5 phase appears together with iron, rutile, reduced rutiles, Fe3C and pseudobrookite solid solution.
4) Below 1 150 ℃, chemical reaction is the rate- controlling step. Above 1 200 ℃, diffusion through the product layer controls the reaction. The activation energies of the two steps are 265 kJ/mol and 157 kJ/mol, respectively.
References
[1] YUAN Z F, WANG X Q. A new process for comprehensive utilization of complex titania ore [J]. Min Eng, 2006, 19: 975-978.
[2] LI W B, YUAN Z F, XU C. Effect of temperature on carbothermic reduction of ilmenite [J]. J Iron & Steel Res Int, 2005, 12(4): 1-5.
[3] WOUTERLOOD H J. The reduction of ilmenite with carbon [J]. J Chem Tech Biotechnol, 1979, 29: 603-618.
[4] EL-GUINDY M I, DAVENPORT W G. Kinetics and mechanism of ilmenite reduction with graphite [J]. Metall Trans, 1970, 1: 1729-1734.
[5] SURESH K G, RAJAKUMAR V, GRIEVESON P. Kinetics of reduction of ilmenite with graphite at 1 000 to 1 100 ℃ [J]. Metall Trans B, 1987, 18B: 713-717.
[6] SURESH K G, RAJAKUMAR V, GRIEVESON P. The influence of weathering on the reduction of ilmenite with carbon [J]. Metall Trans B, 1989, 18B: 735-745.
[7] GREY I E, REID A F. Reaction sequences in the reduction of ilmenite: 3-reduction in a commercial rotary kiln; an X-ray diffraction study [J]. Trans Instn Min Metall, 1974, 83: C39-C46.
[8] GREY I E, JONES D G, REID A F. Reaction sequences in the reduction of ilmenite (1): Introduction [J]. Trans Instn Min Metall, 1973, 82: C151-C152.
[9] PISTORIUS P C. The relationship between FeO and Ti2O3 in ilmenite smelter slags [J]. Scan J of Metall, 2002, 31: 120-125.
[10] PESL J, ERIC R H. High temperature carbothermic reduction of Fe2O3-TiO2-MxOy oxide mixtures [J]. Min Eng, 2002, 15: 971-984.
[11] ZIETSMAN J H, PISTORIUS P C. Process mechanisms in ilmenite smelting [J]. J of the South AIMM, 2004, 104: 653-660.
[12] SATOSHI I. Phase equilibria in the titanium-iron-oxygen system in the temperature range of 1 173 to 1 373 K [J]. ISIJ Int, 1999, 39(11): 1107-1115.
[13] GREY I E, REID A F, JONES D G. Reaction sequences in the reduction of ilmenite: 4-interpretation in terms of the Fe-Ti-O and Fe-Mn-Ti-O phase diagrams [J]. Trans Instn Min Metall, 1974, 83: C105-C111.
[14] GIOVANNI D M, BRUNO B, GIUSEPPE T. High temperature interaction between H2, CH4, NH3 and ilmenite [J]. AIP Conf Proc, 2003, 654: 1142-1148.
[15] GIOVANNI D M, BRUNO B, GIUSEPPE T. High temperature interaction between H2O and hydrothermal reduced ilmenite [J]. AIP Conf Proc, 2004, 699: 1060-1066.
[16] SATOSHI I, AUSUSHI K. Reduction kinetics of natural ilmenite ore with carbon monoxide [J]. Mater Trans, 2001, 42(7): 1364-1372.
[17] DAVID G J. Kinetics of gaseous reduction of ilmenite [J]. J Appl Chem Biotechnol, 1975, 25: 561-582.
[18] ZHAO Y, SHADMAN F. Kinetics and mechanism of ilmenite reduction with carbon monoxide [J]. AICHE Journal, 1990, 36(9): 1433-1438.
[19] EUNGYEUL P, OLEG O. Effects of preoxidation of titania-ferrous ore on the ore structure and reduction behavior [J]. ISIJ Inter, 2004, 44(1): 74-81.
[20] EUNGYEUL P, OLEG O. Reduction of titania-ferrous ore by carbon monoxide [J]. ISIJ Inter, 2003, 43(9): 1316-1325.
[21] EUNGYEUL P, OLEG O. Reduction of titania-ferrous ore by hydrogen [J]. ISIJ Inter, 2004, 44(6): 999-1005.
[22] SUN K, TAKAHASHI R, YAGI J. Reduction kinetics of cement-bonded natural ilmenite pellets with hydrogen [J]. ISIJ Inter, 1992, 32(4): 496-504.
[23] SUN K, TAKAHASHI R, YAGI J. Kinetics of the oxidation and reduction of synthetic ilmenite [J]. ISIJ Inter, 1993, 33(5): 523-528.
[24] ZHAO Y, SHADMAN F. Reduction of ilmenite with hydrogen [J]. Ind Eng Chem Res, 1991, 30(9): 2080-2087.
[25] EL-TAWIL S Z, MORSI I M, FRANCIS A A. Kinetics of solid-state reduction of ilmenite ore [J]. Can Metall Q, 1993, 32(4): 281-288.
[26] MERK R, PICKLES C A. Reduction of ilmenite by carbon monoxide [J]. Can Metall Q, 1988, 27(3): 179-185.
Corresponding author: YUAN Zhang-fu; Tel: +86-10-62533383; E-mail: yuanzhf@home.ipe.ac.cn, afuyuan@coe.pku.edu.cn
(Edited by YANG Bing)