
Synthesis of nanostructured Mg2FeH6 hydride and hydrogen sorption properties of complex
LI Song-lin(李松林)1 , TANG Sheng-long(汤盛龙)1, LIU Yi(刘 燚)1, PENG Shu-ke(彭书科)1, CUI Jian-min(崔建民)2
1. State Key Laboratory of Powder Metallurgy, Central South University, Changsha 410083, China;
2. Powder Metallurgy Corporation Ltd., Laiwu Iron and Steel Group, Laiwu 271105, China
Received 11 November 2009; accepted 29 January 2010
Abstract: Reactive mechanical alloying (RMA) was carried out in a planetary ball mill for the synthesis of ternary hydride Mg2FeH6 for hydrogen storage. The formation mechanism of Mg2FeH6 in RMA process and the sorption properties of the products were investigated. The results show that Mg2FeH6 has a yield ratio around 80%, and a grain size below 10 nm in the powder synthesized by milling 3Mg+Fe mixture for 150 h under the hydrogen pressure of 1 MPa. The synthesized powder possesses a high hydrogen capacity and good sorption kinetics, and absorbs 4.42% (mass fraction) of hydrogen within 200 s at 623 K under the hydrogen pressure of 4.0 MPa. In releasing hydrogen at 653 K under 0.1 MPa, it desorbs 4.43% (mass fraction) of hydrogen within 2 000 s. The addition of Ti increases the hydrogen desorption rate of the complex in the initial 120 s of the desorption process.
Key words: reactive mechanical alloying (RMA); metal hydride; hydrogen storage material; kinetics; fuel cell
1 Introduction
Mg and Mg-based alloys are a group of attractive materials for hydrogen storage application[1-2]. Dimagnesium iron hydride, Mg2FeH6 , has the highest known volumetric hydrogen density of 150 kg/m3, which is more than double of liquid hydrogen, and a gravimetric hydrogen density of 5.66% (mass fraction, the same below if not mentioned). However, Mg2FeH6 is more difficult to synthesize than the conventional transition metal hydride like Mg2NiH4, mainly due to the absence of intermetallic compound of the type Mg2Fe in the Mg-Fe binary system[3-4]. The traditional way of preparing Mg2FeH6 is by sintering the raw powder at high temperature (723-793 K) under high hydrogen pressure (2-12 MPa)[5]. More recently, progress was made by mechanical alloying. The aim is to have a maximum yield of Mg2FeH6 and to minimize the content of Fe, MgH2, Mg and MgO. SAI RAMAN et al[6] reported a yield of 63% Mg2FeH6 when ball milling 2Mg+Fe under 1 MPa of hydrogen pressure. SHANG et al[7] synthesized Mg2FeH6 by milling 3MgH2+Fe under Ar atmosphere up to 60 h, leading to a yield of 79% of Mg2FeH6 which co-existed with 16% of MgO. In our previous work[8-9], we reported a 57% Mg2FeH6 yield obtained by controlled reactive mechanical milling of Mg and Fe with the mole ratio of 2:1 under hydrogen pressure of 0.8 MPa in a proprietary Uni-Ball-Mill-5 and the product exhibited desorption peak temperature below 573 K in DSC. To improve purity of the Mg2FeH6 yield will facilitate further investigation of the Mg2FeH6 properties. Hydrogen sorption properties are important for application of the magnesium-based hydrides. In recent years, in order to improve the sorption kinetics of the magnesium hydrides, many additives have been tested. The studies [10-16] show that transition metals (TMs), such as Nb, Ti, V and Fe; mixed valence transition metal oxides [TMOs], such as Cr2O3 and WO3; and carbon allotropes, such as graphite and carbon nanotubes can improve the sorption kinetics of the magnesium hydrides like MgH2 and Mg2NiH4. However, little study has been undertaken on the catalytic effect of Mg2FeH6 on the sorption kinetics. SHANG et al[7] mentioned that Cu almost has no effect on the dissociation of Mg2FeH6. HERRICH et al[17] added platinum group metals (PGMs) as additives; however, no catalytic effects on the sorption properties of Mg2FeH6 were observed.
In this work, we obtain a high yield of Mg2FeH6 formation with high hydrogen storage capacity by reactive mechanical alloying of 3Mg+Fe mixture. The formation mechanism of Mg2FeH6 is discussed. Also, the sorption kinetics of the synthesized powder and the effects of Ti addition are investigated.
2 Experimental
Elemental powders of Mg (purity>99%, 883 μm), Fe (purity>99%, 100 μm) and a small amount of Ti (purity 99.7%, 200 μm) were used as raw materials. The powder mixtures with desired composition were mechanically milled for 150 h in hydrogen (purity 99.99%) by using a XQM-4 type planetary ball mill (Nanjing University, China). A few drops of toluene were added, which served as lubricant to prevent the ductile Mg powder adhering and cold-welding to the balls and the vial wall. The composition of starting powder mixtures and reactive ball milling details are shown in Table 1. The powders without and with addition of Ti were designated as 3MFH and 3MFHT, respectively. The figure that came after the powder number expressed the milling time. For example, 3MFH150 meant the product was synthesized by milling the mixture of 3Mg+Fe for 150 h. The inner pressure of milling vial was constantly monitored and refilled to 1 MPa every 0.5 h in the range of 3-15 h, and then refilled every 5 h until milling to 150 h. The milling vial was always evacuated and purged several times with Ar (purity 99.99%) before the final fill up with hydrogen. A small amount of powder was removed at regular intervals for analysis. All the sample handling was performed in an Ar-filled glove-box equipped with purification system, in which the typical H2O and O2 levels were below 1×10-6.
X-ray diffraction (XRD) spectra of milled powders were recorded with Rigaku D/max2550 using Cu Kα radiation (λ=0.154 18 nm) at operating parameters of 300 mA, 40 kV, step size 0.02° and speed 2 (°)/min. The grain size of the phases in the milled powders was calculated from the XRD peaks by Scherrer equation and the abundance of phase in the milled mixtures was calculated by K value method with integrated intensities of the strongest XRD peaks according to the following equations (for a mixture containing phases A and B)[18]:
(1)
(2)
where IA is the integrated intensities of the strongest XRD peaks of phase A;
is a constant; WA is the abundance of phase A in the milled powder.
Microstructure and morphology of the milled powders were carried out using scanning electron microscope (SEM, JSM 6700F), and transmission electron microscope (TEM JSM 3010). The chemical composition of the particles in the powders was determined using quantitative energy dispersive X-ray spectroscope (EDS).
Hydrogen sorption properties of the samples, with a typical amount of about 1 g, were examined by a Sieverts-type apparatus. Absorption/desorption measurements were performed at desired temperatures with an initial hydrogen pressure of 4.0 and 0.1 MPa, respectively, without any activation. The hydrogen supply with a purity of 99.999% was used in this measurement.
3 Results and discussion
3.1 Synthesis of Mg2FeH6
XRD patterns of both 3MFH and 3MFHT powders as a function of reactive milling time are shown in Fig.1. For the 3MFH powder, the Mg diffraction peaks disappear after 20 h of milling, and very strong β-MgH2 peaks together with weak Mg2FeH6 peak appear. Simultaneously, the β-MgH2 peaks reach their maximum intensity and start weakening with further increase of milling time. From 20 to 100 h, both β-MgH2 and Mg2FeH6 hydrides phases are found coexisting with unreacted Fe. With increasing RMA time to 150 h, the peaks of β-MgH2 disappear and the intensities of Mg2FeH6 peaks increase measurably on the XRD pattern. In our previous investigation, the reflections of Mg2FeH6 attained their maximum value after milling for 150 h in this RMA condition. Further milling does not improve the intensity of the Mg2FeH6 reflections, but it increases the formation of unneeded MgO[19]. The XRD pattern of the 3MFHT150 powder is similar to that of the 3MFH150 powder. However, we can also find that the peaks of the 3MFHT150 powder on the XRD pattern are weaker and broader than those of the 3MFH150 mixture (according to the full width at half maximum of the strongest peaks). It could be reasonably deduced that the addition of Ti contributes to grain refinement and more micro-strains. There is no phase corresponding to Ti peaks observed, probably due to the very little amount of Ti addition in the starting milling powder.
Table 1 Composition of raw powder mixtures and processing parameters for RMA

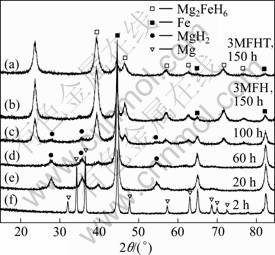
Fig.1 XRD patterns of milled powders as function of reactive milling time: (a) 3MFHT, 150 h; (b) 3MFH, 150 h; (c) 100 h; (d) 60 h; (e) 20 h; (f) 2 h
The content of Mg2FeH6 in 3MFH150 is 80.1%. The yield of Mg2FeH6 in 3MFHT150 powder is 80.4%, which is similar to that in 3MFH150 powder. HUOT et al[20] reported a yield of 56% Mg2FeH6 by milling the mixture of (2MgH2+Fe) in a planetary ball mill under Ar atmosphere for 60 h. Recently, LI et al[21] achieved a yield of 45% Mg2FeH6 and 48% MgH2 by controlled hydriding combustion synthesis(CHCS) in a single process from Mg and Fe elemental powders under 30 MPa of hydrogen pressure. More studies for a higher yield of Mg2FeH6 are needed.
Hydrogen pressure variations inside the milling vial were monitored as a function of milling time by taking periodic readings with the pressure gauge, which can be used to calculate the corresponding amount of hydrogen absorbed onto the starting materials according to the following equations [22]:
(3)
(4)
where n is the amount of substance; w is the mass fraction; P, V and T are the hydrogen pressure, the volume of the milling vial and the inner temperature, respectively; R, a constant (≈8.314) and Z, a compression coefficient which was used to modify the warp between the actual gas and the ideal gas. Fig.2 shows the hydrogen absorption amount of both 3MFH and 3MFHT mixtures with the corresponding ball milling time. It can be seen that the amount of hydrogen absorption increases with ball milling time. The hydrogen contents in 3MFHT and 3MFH increase rapidly in the first 15 h. XRD test shows that the rapid absorption of hydrogen corresponds to the rapid formation of MgH2. Within 15-150 h, the absorption rate of hydrogen decreases and finally the total hydrogen absorption rate reaches about 4.19% and 4.67%, respectively. It can be found that the average absorption rate of 3MFHT is slightly greater than that of 3MFH within the first 15 h. As reported in Ref.[23], Ti may have a catalytic function for the hydrogenation of Mg by dissociating hydrogen molecules efficiently and providing rapid diffusion passageway for hydrogen atoms into Mg matrix.
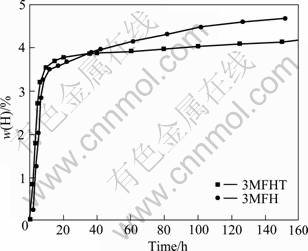
Fig.2 Dependence of hydrogen absorption amount on corresponding ball milling time
3.2 Microstructural characteristics
The morphology of 3MFH powders at different RMA duration time is presented in Fig.3. There is a gradual refinement of powder particle size with increasing RMA time from 2 h to 150 h. The particle size of starting elemental Fe is within 50-100 μm, and the particle size of starting elemental Mg is 500-1 000 μm (estimated via SEM, not shown, seen from Ref.[19]). After 2 h of milling, the particles have sheet shape under high-intensity milling. Subsequent reactive milling leads to substantial powder particle refinement, the particles of 3MFH20 have irregular shape with the particle size decreasing to 0.5-5μm (Fig.3(b)). Cold welding can also be seen in Fig.3(b). Additional milling up to 80 h still reduces the particle size and increases the specific area of the particles. After 150 h of continuous RMA, the 3MFH150 powder is very uniformly refined with a large fraction of powder particles within 100-500 nm.
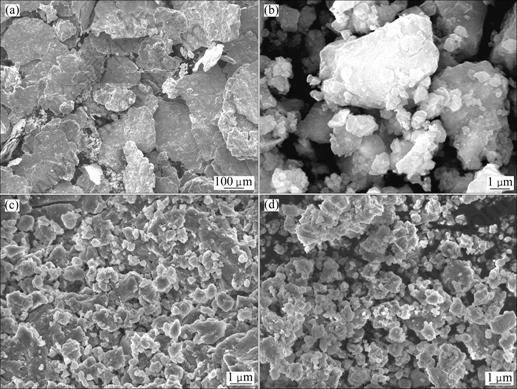
Fig.3 SEM morphologies of 3MFH milled under hydrogen atmosphere for different periods: (a) 2 h; (b) 20 h; (c) 80 h; (d) 150 h
The multiphase nature of the sample was further confirmed by TEM observations (Fig.4). A uniform distribution of Fe (dark particles) with 15-20 nm of grain size can be directly observed in Fig.4(a). According to EDX analyses of the particle (Fig.4(b)), region 1 and region 2 contain Mg and Fe in mole ratios of 0.63:1, 1.5:1, respectively. It can be inferred that region 1 is associated with Fe-rich region (dark gray), where more Fe but less Mg2FeH6 are contained, and region 2 is associated with Mg-rich region (bright gray), where more Mg2FeH6 but less Fe are contained. In the EDX spectra, other elements except Mg and Fe were detected. The presence of C and Cu may be related with the grids and O, Si are probably brought during sample preparation. On the basis of TEM and XRD analyses, the initial formation of Mg2FeH6 may occur according to the following steps. At the initial step, the milling of Mg under hydrogen atmosphere with Fe coexistence promotes the formation of MgH2 and a very uniform mixing of Fe with Mg or MgH2. In the meantime, the grain size of Fe, Mg or MgH2 progressively decreases during milling and the Fe particles embed into the softer MgH2 particle agglomerates. Then Mg2FeH6 is formed via the reaction of MgH2 and Fe according to the following reaction[7, 24]:
3MgH2(s)+Fe(s)
Mg2FeH6(s)+Mg(s) (5)
Reaction (5) shows that there exists unreacted Mg in the mixture, but it is hardly identified by XRD. Perhaps, it exists in an amorphous state [1]. Reaction 5 is a solid-solid phase reaction. The new synthesized Mg2FeH6 forms a shell between MgH2 and Fe. For further formation of Mg2FeH6, the outer MgH2 must react with the inner Fe atoms[20]. So, if the Mg2FeH6 layer is too thick for the outer MgH2 to react, no more Mg2FeH6 will be produced and unreacted Fe and MgH2 are left. This mode probably explains why it is hard for Mg2FeH6 to reach a 100% yield. The ball milling usually creates a nanostructured product. Table 2 lists the grain size of each phase in 3MFH powders. It can be seen from Table 2 that a clear crystallite size reduction of Mg and Fe from >1 000 nm (starting materials) to 28.1 nm and 20.1 nm after 2 h of milling, respectively. The grain size decreases with increase of milling time. Up to 150 h, the grain size of Mg2FeH6 is all below 10 nm and the grain size of Fe is 11-12 nm, which agree well with our previous results[7-8]. These values are smaller than those obtained by mechanical milling (MM) in Ar atmosphere followed by sintering in H2 atmosphere[3] and those obtained by using controlled hydriding combustion synthesis (CHCS)[21]. A small nanograin size may be favorable for improvement of the hydrogen sorption kinetics of hydrogen storage materials[24-26].
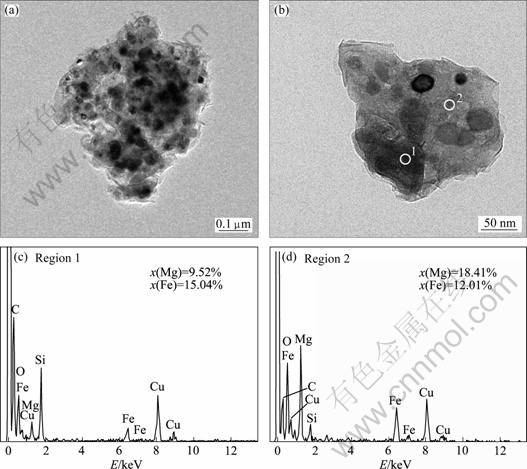
Fig.4 TEM images of composite 3MFH after milling for 150 h (a), (b) and EDX analysis (c), (d)
Table 2 Grain size of each phase in milled powders calculated from XRD (nm)
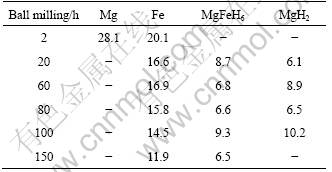
3.3 Hydrogen sorption kinetics
The milled powders were cycled three times in the temperature range of 593-653 K. The milled powders can release/absorb hydrogen directly without any activation step. The hydrogen desorption curves of 3MFH150 powder in the temperature range of 593-653 K under 0.1 MPa of H2 pressure are shown in Fig.5. 90% of hydrogen capacity of the 3MFH150 powder can be desorbed within 1 000 s and the powder completely releases 4.43% hydrogen at 653 K under 0.1 MPa of H2 pressure within 1 800 s. Small particle/grain size could reduce the diffusion path, and high quantity of phase boundaries will enhance diffusion. Therefore, a well desorption kinetics is obtained by reducing particle/grain size and refining microstructure (see Fig.4(a)). The hydrogen desorption rate and amount decrease remarkably with decrease of temperature. It can be deducted that such difference may be associated with the reduced structural defects and grain growth in the restored hydride, compared with the as-milled sample[21].
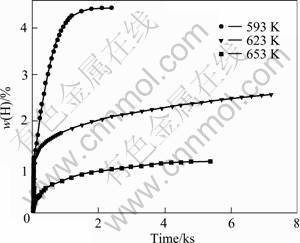
Fig.5 Hydrogen desorption kinetics for 3MFH150 powder in temperature range of 593-653 K under 0.1 MPa of hydrogen pressure
Fig.6 shows the hydrogen desorption curves of 3MFHT150 and 3MFH150 powders at 653 K with an initial hydrogen pressure of 0.1 MPa. The results show the H-desorption rate of 3MFHT150 powder in the first 120 s is faster than that of 3MFH150 powder. The average desorption rates of 3MFHT150 and 3MFH150 powder are ~1.4×10-2%/s and ~1.1×10-2%/s in the first 120 s, respectively. Within 120-600 s, the H-desorption rates of the two powders reduce to ~2.5×10-3%/s and ~4.1×10-3%/s, and finally reduce to 0.6×10-3%/s and 0.9×10-3%/s within 600-1 800 s, respectively. The 3MFHT150 powder releases 80% hydrogen stored within 600 s. However, for 3MFH150 powder, it needs 720 s to release the same hydrogen fraction stored. The 3d-transition metal Ti is a good catalyst for chemisorption of hydrogen. The addition of Ti induces more phase boundaries into the metal hydride and facilitates the dissociation of the hydride and the release of hydrogen from the decomposited hydride[27-28]. In MgH2 and NaAlH4 hydrides, Ti acts as a catalyst which promotes molecular hydrogen activation and hydrogen transfer during their complex phase transformations in the H2 environment [10, 29-30].
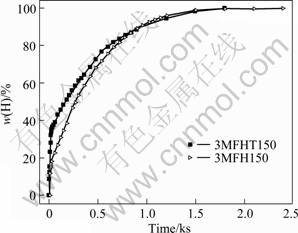
Fig.6 Hydrogen desorption curves of composites 3MFHT150 and 3MFH150 at 653 K under 0.1 MPa of desorption pressure
The hydrogen absorption was carried out under 4 MPa of H2 pressure in the temperature range of 593-623 K and the results are shown in Fig.7. A clear increase of both the absorption rate and the hydrogen storage capacity with increasing absorption temperature is observed. The 3MFH150 powder exhibits the fastest absorption kinetics by completely absorbing hydrogen 4.42% within 200 s at 623 K under 4.0 MPa of H2 pressure, and only 50 s is needed for the accomplishment of 80% hydrogen absorption. The hydrogen absorption kinetics and hydrogen capacity of 3MFH150 powder slightly decrease at 593 K under 4.0 MPa of H2 pressure. Recently, PUSZKIEL et al[3] reported that the 2Mg-Fe mixture absorbed 3.1% hydrogen within 800 s at 573 K under 5.2 MPa of hydrogen pressure. Therefore, our kinetics results for the sample 3MFH150 exhibit a better absorption rate, probably due to the smaller nanograin size and special nanostructure characteristics obtained by high-intensity milling. Fig.8 shows the hydrogen absorption of 3MFHT150 and 3MFH150 powders at 623 K with an initial hydrogen pressure of 4.0 MPa. By comparing hydrogen absorption rate curves of 3MFH150 and 3MFHT150 powder, it can be found that 3MFH150 powder exhibits slightly faster absorption than 3MFHT150 powder. 3MFH150 powder absorbs 100% hydrogen within 200 s. However, for 3MFHT150 powder, it needs more than 400 s to absorb 100% hydrogen. It is shown that Ti in 3MFHT150 powder does not help to increase the absorption rate, which can also be found in Mg2FeH6-Pt composite material[17]. This is possibly due to the fact that formation of Mg2FeH6 during hydrogenation requires the diffusion of metal atoms, and the diffusion process is not enhanced by Ti. The effect of transition metal additive on sorption properties of Mg2FeH6 is needed for further investigation.
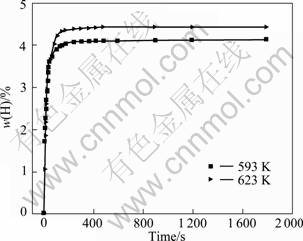
Fig.7 Hydrogen absorption curves of composite 3MFH150 at different temperatures under initial hydrogen pressure of 4 MPa
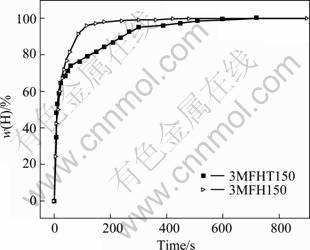
Fig.8 Hydrogen absorption curves of 3MFHT150 and 3MFH150 at 623 K under initial hydrogen pressure of 4.0 MPa
4 Conclusions
1) Mg2FeH6 with a yield of about 80% was successfully synthesized by ball milling Mg and Fe with mole ratio of 3:1 in 1MPa hydrogen atmosphere using a planetary ball mill. There exist unreacted Fe and MaH2 in the substrate because the Mg2FeH6 layer is too thick for the outer MgH2 to react with inner Fe. That is why it is hard for Mg2FeH6 to reach a 100% yield.
2) The synthesized Mg2FeH6 has a grain size of about 7 nm. The 3MFH150 powder possesses a compromised H-capacity and kinetics. It can release 4.43% hydrogen at 653 K under 0.1 MPa of hydrogen pressure and absorb 4.42% hydrogen at 623 K under the initial 4 MPa of hydrogen pressure without any activation process.
3) Ti acts as a catalyst in decomposition process of Mg2FeH6. The addition of Ti increases the hydrogen desorption rate in the initial 120 s of the desorption process. The 3MFHT150 powder releases 80% hydrogen stored within 600 s, while 3MFH150 powder within 720 s.
References
[1] Varin R A, Li S, Calka A, Wexler D. Formation and environmental stability of nanocrystalline and amorphous hydrides in the 2Mg-Fe mixture processed by controlled reactive mechanical alloying (CRMA) [J]. Journal of Alloys and Compounds, 2004, 373 (1/2): 270-286.
[2] ZHOU D w, LI S l, Varin R A, Peng P, Liu J S, Yang F. Mechanical alloying and electronic simulations of 2Mg-Fe mixture powders for hydrogen storage [J]. Materials Science and Engineering A, 2006, 427(1/2): 306-315.
[3] Puszkiel J A, Arneodo Larochette P, Gennari F C. Thermodynamic and kinetic studies of Mg-Fe-H after mechanical milling followed by sintering [J]. Journal of Alloys and Compounds, 2008, 463(1/2): 134-142.
[4] LI Song-lin, LIU Yi, VARIN R A, LIU Huai-fei, CUI Jian-min, CHEN Shi-qi. Effect of balling methods on synthesis and desorption properties of nanocrystalline Mg2FeH6 hydrogen storage materials [J]. The Chinese Journal of Nonferrous Metals, 2008, 18(1): 42-47. (in Chinese)
[5] Isobe S, Ichikawa T, Hanada N, Leng H Y, Fichtner M, Fuhr O, Fujii H. Effect of Ti catalyst with different chemical form on Li-N-H hydrogen storage properties [J]. Journal of Alloys and Compounds, 2005, 404/406: 439-442.
[6] Sai Raman S S, Davidson D J, Bobet J L, Srivastava O N. Investigations on the synthesis, structural and microstructural characterizations of Mg-based K2PtCl6 type (Mg2FeH6) hydrogen storage material prepared by mechanical alloying [J]. Journal of Alloys and Compounds, 2002, 333(1/2): 282-290.
[7] Shang C X, Bououdina M, Gao Z X. Direct mechanical synthesis and characterization of Mg2Fe(Cu)H6 [J]. Journal of Alloys and Compounds, 2003, 351/356: 626-629.
[8] LI S, Varin R A, Morozova O, Khomenko T. Controlled mechano-chemical synthesis of nanostructured ternary complex hydride Mg2FeH6 under low-energy impact mode with and without pre-milling [J]. Journal of Alloys and Compounds, 2004, 384(1/2): 231-248.
[9] Varin R A, Li S, Wronski Z, Morozova O, Khomenko T. The effect of sequential and continuous high-energy impact mode on the mechano-chemical synthesis of nanostructured complex hydride Mg2FeH6 [J]. Journal of Alloys and Compounds, 2005, 390(1/2): 282-296.
[10] Wang P, Wang A M, Zhang H F, DING B Z, HU Z Q. Hydrogenation characteristics of Mg-TiO2 (rutile) composite [J]. Journal of Alloys and Compounds, 2000, 313(1/2): 218-223.
[11] QI J F, SHIK C T. Tin and tin–titanium as catalyst components for reversible hydrogen storage of sodium aluminium hydride [J]. Fuel, 2006, 85(14/15): 2141-2147.
[12] Bogdanovi? B, Schwickardi M. Ti-doped alkali metal aluminium hydrides as potential novel reversible hydrogen storage materials [J]. Journal of Alloys and Compounds, 1997, 253/254: 1-9.
[13] Hanada N, Ichikawa T, Hino S, FUJII H. Remarkable improvement of hydrogen sorption kinetics in magnesium catalyzed with Nb2O5 [J]. Journal of Alloys and Compounds, 2006, 420(1/2): 46-49.
[14] Barkhordarian G, Klassen T, Bormann R. Effect of Nb2O5 content on hydrogen reaction kinetics of Mg [J]. Journal of Alloys and Compounds, 2004, 364(1/2): 242-246.
[15] Bobet J L, Castro F J, Chevalier B. Effects of reactive mechanical milling conditions on the physico-chemical properties of Mg+Cr2O3 mixtures [J]. Journal of Alloys and Compounds, 2004, 376(1/2): 205-210.
[16] de Castro J F R, Santos S F, Costa A L M, Yavari A R, Botta F W J, Ishikawa T T. Structural characterization and dehydrogenation behavior of Mg-5at.%Nb nano-composite processed by reactive milling [J]. Journal of Alloys and Compounds, 2004, 376(1/2): 251-256.
[17] Herrich M, Ismail N, Lyubina J, HANDSTEIN A, PRARR A, GUTFLEISCH O. Synthesis and decomposition of Mg2FeH6 prepared by reactive milling [J]. Materials Science and Engineering B, 2004, 108(1/2): 28-32.
[18] LI S S. The foundation of X-ray crystal diffraction [M]. Beijing: Metallurgical Industry Press, 1990: 141-142. (in Chinese)
[19] LI Song-lin, LIU Yi, CUI Jian-min, YANG Wen-zhi, LI Hao-peng, HE Yi-lun. Synthesis and hydrogen desorption properties of Mg2FeH6 hydrogen storage material by reactive mechanical alloying [J]. Journal of Central South University: Science and Technology, 2008, 39(1): 1-6. (in Chinese)
[20] Huot J, Boily S, Akiba E, Schulz R. Direct synthesis of Mg2FeH6 by mechanical alloying [J]. Journal of Alloys and Compounds, 1998, 280(1/2): 306-309.
[21] Li Q, Liu J, Chou K, Lin G, Xu K. Synthesis and dehydrogenation behavior of Mg-Fe-H system prepared under an external magnetic field [J]. Journal of Alloys and Compounds, 2008, 466(1/2): 146-152.
[22] WANG P. Investigation on preparation microstructure and properties of Mg-based composite for hydrogen storage [D]. Shenyang: Institute of Metal Research, Chinese Academy of Sciences, 2001: 23.
[23] DU A J, SMITH S C, YAO X D, G Q LU. The role of Ti as a catalyst for the dissociation of H2 on a Mg(0001) surface [J]. Journal of Physical Chemistry B, 2005, 109(38): 18037-18041.
[24] Schulz R, Hout J, Liang G, Boily S, van Neste A. Structure and hydrogen sorption properties of ball milled Mg dihydride [J]. Journal of Metastable and Nanocrystalline Materials, 1999, 312/314: 615-622.
[25] Schulz R, Hout J, Liang G, Boily S, Lalande G, Denis M C, Dodeletm J P. Recent developments in the applications of nanocrystalline materials to hydrogen technologies [J]. Materials Science and Engineering A, 1999, 267(2): 240-245.
[26] Czujko T, Varin R A, Chiu C, WRONSKI Z. Investigation of the hydrogen desorption properties of Mg+10wt.%X (X=V, Y, Zr) submicrocrystalline composites [J]. Journal of Alloys and Compounds, 2006, 414(1/2): 240-247.
[27] LIANG G, Huot J, Boily S, van Neste A, Schulz R. Hydrogen storage in mechanically milled Mg-LaNi5 and MgH2- LaNi5 composites [J]. Journal of Alloys and Compounds, 2000, 297: 261-265.
[28] LIANG G, Huot J, Boily S, Van Neste A, Schulz R. Catalytic effect of transition metals on hydrogen sorption in nanocrystalline ball milled MgH2-Tm (Tm=Ti, V, Mn, Fe and Ni) systems [J]. Journal of Alloys and Compounds 1999, 292: 247-252.
[29] Bogdanovi?, Brand R A, Marjanovi? A, Schwickardi M, Tolle J. Metal-doped sodium aluminium hydrides as potential new hydrogen storage materials [J]. Journal of Alloys and Compounds, 2000, 302(1/2): 36-58.
[30] Charbonnier J, de Rango P, Fruchart D, Miraglia S, Pontonnier L, Rivoirard S, Skryabina N, Vulliet P. Hydrogenation of transition element additives (Ti, V) during ball milling of magnesium hydride [J]. Journal of Alloys and Compounds, 2004, 383(1/2): 205-208.
(Edited by LI Xiang-qun)
Foundation item: Project(50574105) supported by the National Natural Science Foundation of China; Project(10JJ2037) supported by Hunan Provincial Natural Science Foundation of China; Project(200902) supported by Innovation Foundation of State Key Laboratory for Powder Metallurgy, Central South University, China
Corresponding author: LI Song-lin; Tel: +86-731-88830614; E-mail: lisl@mail.csu.edu.cn
DOI: 10.1016/S1003-6326(10)60641-3