文章编号:1004-0609(2015)-07-1920-09
超音速火焰喷涂碳化钨-钴涂层磨粒磨损行为
王 群,屈帮荣,唐瞾肸,熊浩奇
(湖南大学 材料科学与工程学院,长沙 410082)
摘 要:采用超音速火焰喷涂工艺在16Mn钢上制备了WC-12Co涂层,并测试了该涂层的力学性能特别是其抗磨粒磨损性能。结果表明:WC-12Co涂层的主相为碳化钨,显微硬度为(1341.0±134.3)HV,孔隙率为0.21%±0.04%。该涂层的磨损率随着磨粒硬度、磨粒粒度和加载载荷的增加而增加。当磨粒的硬度低于涂层硬度时,涂层的磨损机制以磨耗磨损为主,磨损率低;当磨粒的硬度超过涂层的硬度时,涂层的磨损以微切削为主,磨损率高。另外,WC-12Co涂层的耐磨性相对于16Mn钢也是随着磨粒的硬度变化而变化。
关键词:WC-Co涂层;超音速火焰;磨粒磨损
中图分类号:U177.2 文献标志码:A
Abrasive wear behavior of WC-Co coating deposited by high velocity oxygen flame process
WANG Qun, QU Bang-rong, TANG Zhao-xi, XIONG Hao-qi
(College of Materials Science and Engineering, Hunan University, Changsha 410082, China)
Abstract: WC-12Co coating was deposited on the 16Mn steel by high velocity oxygen flame (HVOF) process. The mechanical performances, especially, the abrasive wear behavior, of WC-12Co coating were investigated. The results show that the hardness and porosity of the coating are (1341.0±134.3) HV and 0.21%±0.04%, respectively. The wear rate of the WC-12Co coating increases with increasing the hardness, the size and the employed loadings of the abrasives. The abrasive wear mechanism of the WC-12Co coating is mainly abrasion wear and the wear rate is low when the hardness of the abrasive is lower than that of the coating. However, the wear mechanism of the WC-12Co coating is mainly micro-cutting and the wear rate is very high when the hardness of the abrasive is higher than that of the coating. In addition, compared to the 16Mn steel, the relative abrasive wear resistance of the WC-12Co varies with the change of hardness of the abrasives.
Key words: WC-Co coating; high velocity oxygen flame; abrasive wear
摩擦磨损在工程实践中是非常普遍现象,其中以磨粒磨损所造成的危害最大。在所有因磨损而失效的零部件中,磨粒磨损大约占40%~50%[1-2],因此,开展抗磨粒磨损材料、工艺和相关磨损机理研究具有重要的理论意义和实践应用价值。热喷涂(特别是超音速火焰喷涂(HVOF))金属碳化钨(WC)涂层作为抗磨粒磨损涂层具有高硬度和高抗磨损性能的特点,被广泛地应用于能源、航空航天、冶金、机械等领域[3-8]。采用湿沙橡胶轮磨粒磨损实验机来评定金属WC涂层抗磨粒磨损性能是一种常用的检测方法。当前,通常采用恒定的载荷、磨粒种类和尺寸来评价材料的磨粒磨损性能[9-10],这种方法只能初步对比材料在一般情况下的相对耐磨性。众所周知,在生产实践中,用于抗磨粒磨损材料的使用工况有很大差别,其所受的应力、磨粒种类和尺寸也不尽相同。因此,有必要开展载荷、磨粒种类和尺寸等因素变化对材料磨粒磨损性能和行为影响的研究。MACHIO等[11]研究了超音速火焰喷涂WC-VC-Co涂层在不同载荷下的磨粒磨损行为,发现涂层的磨损率会随着所用载荷的增加而增加,但磨损率的增加幅度远小于载荷的增加幅度。FERN
NDEZ等[12]研究了等离子喷涂NiCrBSi和NiCrBSi+WC涂层的湿砂磨粒磨损行为,发现这两种涂层的磨损率都随着所用磨粒尺寸和载荷的增加而增加。THAKARE等[13]研究了不同尺寸SiC磨粒对超音速火焰喷涂WC-10Co4Cr涂层磨粒磨损行为的影响,发现随着SiC粒度的增大,涂层磨损率出现先降低后增加的现象。刘明等[14]研究了磨粒磨损条件对钛合金磨损行为的影响,发现影响钛合金磨粒磨损行为的各因素的显著程度由高到低依次为料浆浓度、载荷、滑移速度、磨粒及滑移距离。倪继良等[15]也开展了超音速火焰喷涂金属WC涂层磨粒磨损性能研究,发现涂层中的WC粒度越大,其相应的抗磨粒磨损性能越好。虽然研究人员开展了一些磨损参数变化或材料自身性能对材料磨损性能影响的研究,但并没有在磨粒尺寸对被测试样品磨痕尺寸的影响以及载荷变化对橡胶轮变形程度影响等方面开展研究。另外,相对耐磨性在磨粒磨损评价中被广泛采用,而金属WC涂层相对于基体材料的相对耐磨性也会受到磨粒种类的影响。为了更好地评价金属WC涂层在不同工况下的抗磨损性能、磨损机理以及磨粒种类对其耐磨性的影响,本文作者在改变载荷、磨粒尺寸和种类的条件下,研究采用超音速火焰喷涂工艺制备WC-12Co涂层的磨粒磨损行为及相应机理。另外,还将基体材料16Mn钢在相同工况下进行测试,评价磨粒种类对WC-12Co涂层相对耐磨性的影响,以期为生产实践中合理地选择金属WC涂层提供参考。
1 实验
喷涂材料是采用团聚烧结工艺制备的WC-12Co粉末,粉末的粒度分布为5~45 mm。采用Praxair公司最新生产的JP8000型HVOF设备进行喷涂。使用航空煤油作为燃料,氧气作为助燃气,氮气作为送粉载气。前期的研究结果表明[16]:对于采用煤油为燃料,氧气作为助燃剂的超音速火焰喷枪,随着煤油和氧气流量的增加,喷枪燃烧室的压力增大,喷枪产生的焰流速度及相应的粒子速度都会随之增加,从而可以获得高结合强度、高致密和高硬度的涂层。在本研究中,选择较高的煤油和氧气流量以期获得性能较好的涂层,表1所列为WC-12Co涂层的喷涂工艺参数。
喷涂前,对厚度为5mm的16Mn钢板进行除锈、除油。然后采用250 μm刚玉进行粗化处理,涂层设计厚度约为0.35 mm。为了防止基体过热,在喷涂过程中采用间歇喷涂,并结合压缩空气冷却的方式使得基体样块的温度不超过150 ℃,直到涂层达到预定的厚度。
表1 WC-12Co涂层喷涂工艺参数
Table 1 Spraying parameters of WC-12Co coating
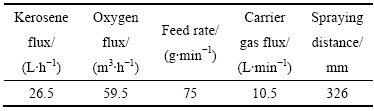
根据松散磨粒磨料磨损试验方法,即湿砂橡胶轮法标准(JB T 7705-1995)[10],选择MLS-225型湿砂橡胶轮磨粒磨损实验机来测试材料的磨粒磨损性能,采用的橡胶轮转速、样品尺寸以及磨损介质中水和砂的用量均按标准规定进行设置。橡胶轮转速为240 r/min,磨粒通常为212~380 μm石英砂,磨损介质为1.5 kg砂和1 kg水构成的砂浆,采用的最大载荷为225 N,样品的长和宽分别为57 mm和25 mm。为了研究磨粒磨损条件变化对相应磨损结果的影响,在标准规定的范围内,按照一定的梯度对载荷、砂粒种类和粒度作适当的调整,以探讨这些因素对WC-12Co涂层磨粒磨损性能和相对耐磨性的影响。表2所列为具体的磨粒磨损实验条件。
表2 磨粒磨损实验条件
Table 2 Test conditions of abrasive wear

WC-12Co涂层喷涂态表面粗糙度为Ra=3左右。为了减小样品表面粗糙度不同对磨损结果带来的影响,在正式磨损实验之前,先进行预磨损处理。结合JB T 7705-1995标准,第一组和第二组涂层采用每个试块预磨500 r,再正式磨3轮,每轮3000 r。所采用橡胶轮的直径为178 mm,邵氏硬度为70±2。在计算磨程时,由于橡胶轮尺寸变化很小,故视其直径不变,磨程为相应的转数乘以橡胶轮周长。第三组中选用的是碳化硅(SiC)作为磨粒,初步实验发现SiC磨粒对涂层的磨损率非常大,所以,在进行磨损实验时,橡胶轮的转数也大大地减少。结合初步磨损实验结果,当使用SiC作为磨粒时,橡胶轮预磨转数设为25 r,正式磨3轮,每轮75 r。本实验还将没有涂层的基体材料16Mn钢在100 N的载荷下,分别选用SiO2和SiC作为磨粒进行磨损测试。将磨损后的质量损失除以其理论密度和总磨程,获得这种材料的磨损率。另外,为了研究不同类型磨粒对涂层磨损性能的影响,还选择了预粒度相近的24号和36号各占50%(质量分数)的SiC作为磨粒进行磨损实验。图1所示为相应的SiO2和SiC磨粒形貌和能谱。
采用RigakuD/max-2550型X衍射仪(铜靶)测试WC-12Co粉末和涂层的相结构。采用泰明显微硬度计(HXD-1000TM)在涂层截面上测试硬度,并取10个点的平均值作为涂层的硬度(载荷为2.94 N)。对涂层截面的金相照片采用“灰度法”测量其孔隙率,并取10个点的平均值作为涂层的孔隙率。
2 结果与分析
2.1 涂层相结构
图2所示为WC-12Co粉末及涂层的XRD谱。由图2可以看出,采用超音速火焰喷涂工艺制备WC-12Co涂层的相结构与粉末类似,涂层和粉末的主相都是WC相,涂层中新生成了少量的W2C。由此可以看出,在喷涂过程中WC仅仅发生了轻微的氧化脱碳。另外,涂层中未见明显的Co相,一方面是因为X衍射仪采用Cu靶时,获得的Co峰较弱,另一方面是因为焰流中熔融的金属Co相沉积到基体上时凝固速度非常快,部分Co变成了非晶态的原因[7, 9, 16]。
2.2 涂层的基本性能和显微组织
WC-12Co涂层显微硬度为(1341.0±134.3)HV,孔隙率为0.21%±0.04%。图3所示为涂层截面的SEM像。
由图3(a)可以看出,WC-12Co涂层非常致密,且涂层与基体的结合也非常紧密。由图3(b)所示的涂层截面的背散射像可以看出,涂层中分布着大量不同大小的灰色WC颗粒、少量高亮显示的细小白色颗粒和包裹在WC颗粒周围的环状白色物质(见图3(b)箭头所指的位置)。结合文献[7, 9, 16]和图2和3(b)可以推测,这些高亮显示的物质是W2C。另外,由于Co的原子量要小于W和WC的,所以,图3(b)中部分较暗的为Co相,部分区域的粘结相较亮,是由于该部分的Co在焰流中充分熔融,溶入了部分原子较高的金属W的缘故[9, 16]。
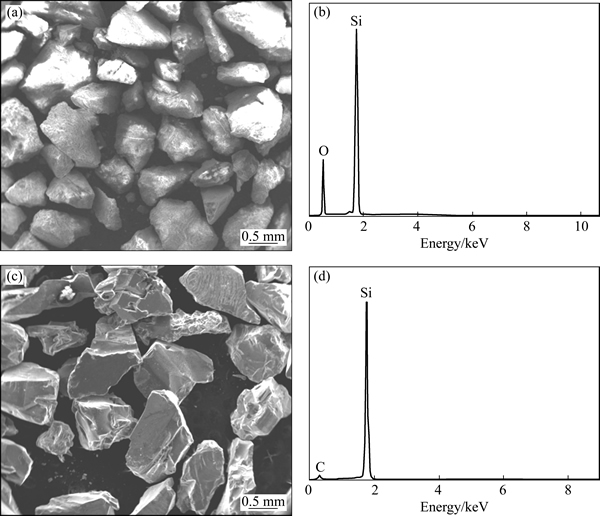
图1 SiO2和SiC磨粒的形貌和能谱
Fig. 1 Morphologies and EDS spectra of SiO2 ((a), (b)) and SiC ((c), (d))

图2 WC-12Co粉末和涂层的XRD谱
Fig. 2 XRD patterns of WC-12Co powder and coating
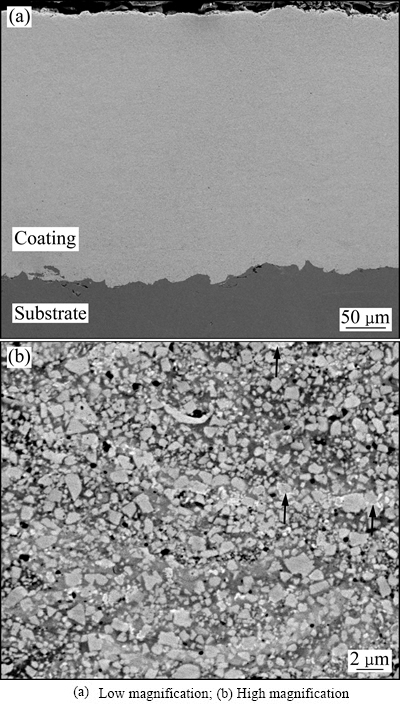
图3 WC-12Co涂层的截面SEM像
Fig. 3 Cross-sectional SEM image of WC-12Co coating
2.3 磨损实验条件对WC-12Co涂层磨粒磨损性能的影响
2.3.1 载荷对WC-12Co涂层的磨损性能的影响
WC-12Co涂层在同种磨粒(380~830 μm SiO2),不同载荷(25、50、100、200 N)下,图4所示为涂层的磨损率曲线。由图4可知,涂层磨损率随着载荷的增加而增加,在不同载荷作用下,涂层的磨损率都是前期较大,后期减小。这是因为喷涂态涂层表面虽然经过500 r的预磨损,但是其表面粗糙度仍然较大,所以涂层前期磨损率较大。在磨损实验后期,由于其磨损表面粗糙度减小,涂层中低硬度的金属粘结相被磨粒切削后,高硬度的WC颗粒突出在突出表面,从而涂层中材料的损失变得缓慢。
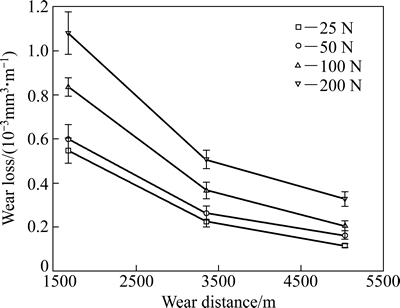
图4 WC-12Co涂层在不同载荷下涂层的磨损率
Fig. 4 Volume wear loss of WC-12Co coating under different loads
图5所示为WC-12Co涂层在25和200 N载荷下磨损表面的宏观照片和SEM像。由图5可知,涂层磨损后的表面在高载荷作用下要比涂层在低载荷作用下更为粗糙,这主要是因为磨粒在高载荷作用下对涂层表面的冲击和刮削作用强,粘结相Co更容易被切除。另外,硬质WC颗粒在更大冲击力的作用下也更容易破碎或从粘结相中脱离,从而导致涂层呈现出更粗糙的磨损表面和更大的磨损率。
2.3.2 磨粒尺寸对WC-12Co涂层的磨损性能的影响
图6所示为WC-12Co涂层在同种载荷(100 N)下SiO2粒度分别为45、75~150、212~380和380~830 μm的磨损率曲线。由图6可以看出,涂层的磨损率随着磨粒尺寸的增加而增加。
图7所示为涂层在不同粒度的磨粒作用下磨损表面的宏观照片和SEM像。由图7所示的涂层宏观磨损形貌可以看出,当磨粒尺寸较小时,涂层表面被磨损区域的磨痕短而浅;而当磨粒尺寸较大时,涂层表面被磨损区域的磨痕长而深。由细磨粒造成的短而浅的磨痕对应着较小的磨损率,由粗磨粒造成的长而深的磨痕对应着较大的磨损率。磨痕长度不同是由湿砂橡胶轮磨粒磨损实验机的特点决定的,当橡胶轮硬度和试样上所受的载荷一定时,磨粒大小直接影响磨痕的长度。
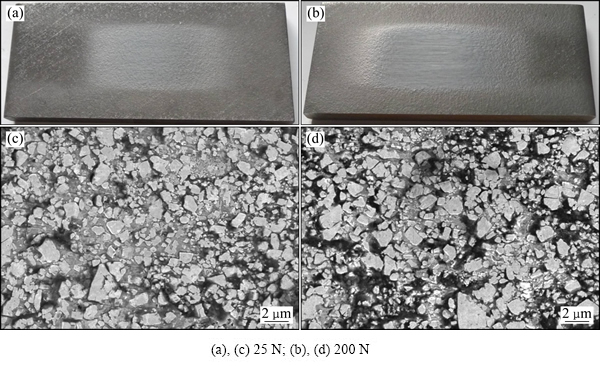
图5 WC-12Co涂层在不同载荷下磨损表面的照片和SEM像
Fig. 5 Photos and SEM images of WC-12Co coatings worn surface under different loads

图6 WC-12Co涂层在不同粒度SiO2作用下的磨损率
Fig. 6 Volume wear loss of WC-12Co under abrasives with different sizes
图8所示为磨粒尺寸对被磨损涂层试样表面磨痕长度影响的示意图。图8中橡胶轮直径为178 mm,被磨损试样长度为57 mm。当橡胶轮作用在试样上的载荷为100 N时,橡胶轮与试样接触部分长度的测量值L0为20.17 mm。当橡胶轮与被磨损试样之间存在磨粒时,磨粒尺寸会影响橡胶轮将载荷通过磨粒作用到被磨损试样的起点位置和磨粒离开时的终点位置。理论上的起点位置为该磨粒中最大尺寸磨粒的最大轮廓截面来计算。当磨粒的粒度为380~830 μm,磨粒理论上最大的尺寸为750 μm;当磨粒粒度为45 μm时,该磨粒理论上最大的尺寸为50 μm。磨粒最大截面轮廓外接圆同时与橡胶轮和被磨损试样表面相切(将最大磨粒看成是理想的球形),左右两点的圆心极限位置分别为S1(粗磨粒中最大磨粒与试样表面作用的起点),E1(粗磨粒中最大磨粒与试样表面作用的终点)和S2(细磨粒中最大磨粒与试样表面作用的起点),E2(细磨粒最大磨粒与试样表面作用的终点)。大、小磨粒最大截面外接圆两相切位置圆心距离分别为L1=S1E1=30.64 mm和L2=S2E2=20.96 mm,用该方法计算得出的磨痕长度与实际被磨损试样表面的磨痕长度很接近。由图8可见,采用较大磨粒获得的涂层表面磨痕较长原因如下:相对于细颗粒,尺寸较大的磨粒被橡胶轮“咬入”时间早,且“离开”的时间晚的缘故,即大颗粒的磨粒在被测试样品表面会作用更长的时间。
由涂层在不同磨粒作用下的磨损形貌可知(见图7(b)和(d)),当磨粒尺寸较小时,涂层的磨损表面较平整;而当磨粒尺寸较大时,涂层的磨损表面较为粗糙。
当橡胶轮静止时,橡胶轮施加到试样上的力由两部分构成,一部分由橡胶轮直接作用到试样表面,另一部分通过磨粒作用到试样表面。大尺寸磨粒使橡胶轮产生的弹性变形大,根据虎克定律:F=kx,当变形x较大时,橡胶轮作用在大尺寸磨粒上的力要比作用在小颗粒上的力要大的多,即F1=(D1/d2)F2,再加上用来传递压力的大尺寸磨粒数目(接触面积与单个大尺寸磨粒的最大截面积之比)少,所以大尺寸的磨粒作用到试样表面的力要比小尺寸磨粒作用到试样表面的力要大的多。当橡胶轮旋转时,磨粒对被磨损试样表面的作用力,可以分解为两个分力,一个是垂直于被磨损表面的正压力,使得磨粒“刺入”试样表面;另一个便是平行于试样表面的水平分力,使磨粒在试样表面产生切向运动,从而“切削”被磨损材料。正压力越大,磨粒压入试样的深度越大;水平分力越大,磨粒对粘结相的切削作用力越大。同时,对硬质WC粒子的冲击也越大,使得粘结相更易被切除、WC粒子更容易疲劳开裂、松动,最终导致从粘结相上脱离。即犁沟或切削速度越快,造成涂层的磨损率也越大,相应的涂层磨损表面也更为粗糙。
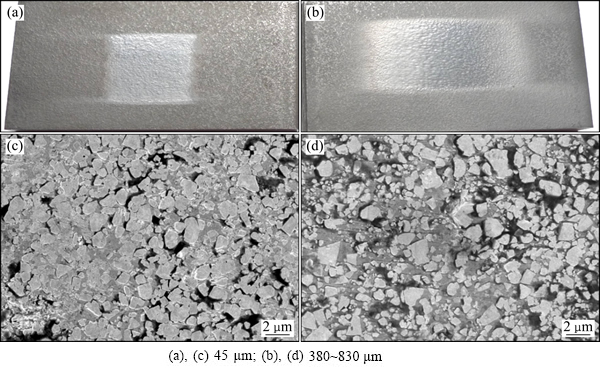
图7 不同粒径磨粒作用下WC-12Co涂层磨损表面的照片和SEM像
Fig. 7 Photos and SEM images of WC-12Co coatings worn surface under abrasives with different sizes

图8 磨粒尺寸对被磨损试样表面磨痕长度影响的示意图
Fig. 8 Schematic diagram of effect of abrasives size on worn scar length of scar sample
2.3.3 磨粒类型对WC-12Co涂层的磨损性能的影响
图9所示为在两种不同磨粒作用下涂层每轮的磨损率。由图9可以看出,SiC磨粒对涂层的磨损非常大,远远高于SiO2磨粒。
图10所示为涂层在粒度尺寸相同的SiO2和SiC磨粒作用下的磨损形貌。
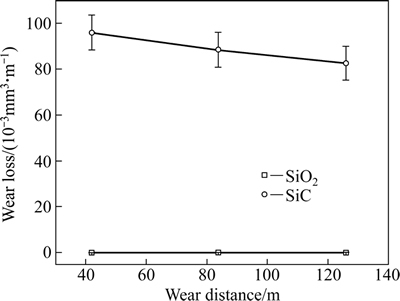
图9 WC-12Co涂层在不同磨粒作用下的磨损率
Fig. 9 Volume wear loss of WC-12Co coating under different abrasives
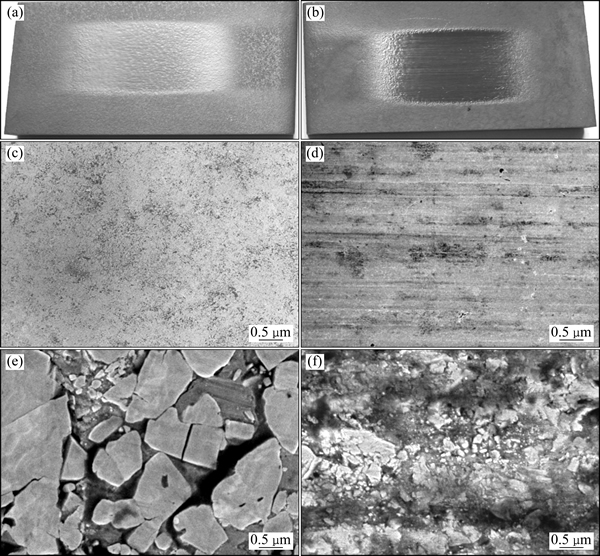
图10 WC-12Co涂层在SiO2和SiC磨粒作用下的磨损表面形貌
Fig. 10 Morphologies of worn surfaces of WC-12Co coatings under SiO2 ((a), (c), (e)) and SiC ((b), (d), (f)) abrasives
由图10可以看出,涂层的磨损表面出现了明显的“切槽”和“犁沟”,涂层在两种不同磨粒作用下的磨损形貌有很大差别。当磨粒是硬度低于涂层硬度的SiO2时,磨粒只能压入涂层中WC颗粒间硬度较低的金属粘结相中,切削部分粘结相并伴随着轻微的犁沟过程;然后,随着粘结相不断被切除及犁沟区域材料的疲劳,WC粒子逐渐破裂、脱落(见图10(c)和(e)),这时涂层的磨损率很低。当磨粒是硬度高于涂层硬度的SiC时,SiC对涂层表面的WC和粘结相都能产生切削作用,从而在涂层表面产生明显的切削沟槽(见图10(d)和(f)),在沟槽内WC粒子被切削成小块和更小的碎屑,涂层磨损率很高。根据表2中的实验条件,在相同实验参数下,当磨粒为SiO2时,16Mn钢的体积磨损率为WC-12Co涂层的170.7倍;而当磨粒为SiC时,16Mn钢的体积磨损率仅为WC-12Co涂层的5.8倍。因此,当磨粒改变时,WC-12Co涂层相对于16Mn钢的相对耐磨粒磨损性能变化很大。图11所示为涂层在这两种不同硬度磨粒作用下,单个磨粒划过涂层表面后单个粒子对涂层磨损表面的作用过程。
根据GAHR[17]提出了被磨材料的磨损率与磨粒的硬度(Ha)与被磨材料的硬度(Hm)之间的比值(λ)有关。当l<0.8,被磨材料的磨损率小;当0.8<l<1.25,被磨材料处于过渡磨损区,磨损率适中;当l>1.25,被磨材料的磨损率偏大。16Mn钢和WC-12Co涂层的平均维氏硬度分别为156.3HV和1341.0HV,SiO2硬度约为850.0HV[18]。因此,当磨粒是SiO2时,被磨损材料为16Mn钢时,
,被磨损材料磨损率偏大;当被磨损材料为WC-12Co涂层时,
,此时WC-12Co属于过渡磨损区,磨损率较小。此时,相对于16Mn钢,WC-12Co涂层具有非常优异的抗磨粒磨损性能,即表现出较高的相对耐磨性。当磨粒为SiC(2800 HV [19]),被磨损材料为16Mn钢时,
,被磨损材料磨损偏大;当磨粒为SiC,被磨损材料为WC-12Co涂层时,
被磨损材料磨损量也较大。
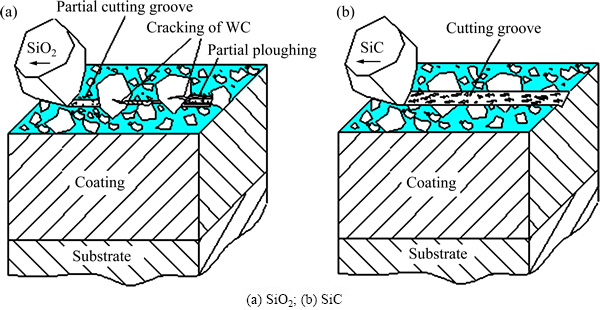
图11 不同磨粒作用下WC-12Co涂层磨损过程示意图
Fig. 11 Schematic diagram of wear mechanism of WC-12Co coating under different abrasives
此时,相对于16Mn钢,WC-12Co涂层的抗磨粒磨损性能的优势就没有那么明显了,即涂层的相对耐磨性降低。
3 结论
1) 涂层的磨损率随着磨粒的硬度、磨粒的粒度和载荷的增加而增加。
2)当磨粒的硬度低于涂层硬度时,涂层的磨损机制以磨耗磨损为主,磨损率低;当磨粒硬度超过涂层硬度时,涂层的磨损机制为微切削为主,磨损率高。
3)当磨粒的硬度较低时,相对于16Mn钢,WC-12Co涂层的抗磨粒磨损性能十分优异;当磨粒硬度高时,WC-12Co涂层的抗磨粒磨损性能优势不显著。
REFERENCES
[1] 薛群基. 中国摩擦学研究和应用的重要进展[J]. 科技导报, 2008, 26(23): 1.
XUE Qun-ji. Progress in Chinese tribology research and application[J]. Science and Technology Review, 2008, 26(23): 1.
[2] 何奖爱, 王玉玮. 材料磨损与耐磨材料[M]. 沈阳: 东北大学出版社, 2001: 4-5.
HE Jiang-ai, WANG Yu-wei. Material wear and abrasion resistant materials[M]. Shenyang: Northeastern University Press, 2001: 4-5.
[3] 李松林, 向锦涛, 周伍喜, 李玉玺, 陈 文. 超音速火焰喷涂WC-10Co4Cr涂层的耐滑动磨损行为[J]. 中国有色金属学报, 2012, 22(5): 1371-1376.
LI Song-lin, XIANG Jin-tao, ZHOU Wu-xi, LI Yu-xi, CHEN Wen. Sliding wear behavior of high velocity oxy-fuel sprayed WC-10C04Cr coatings[J]. The Chinese Journal of Nonferrous Metals, 2012, 22(5): 1371-1376.
[4] MA N, GUO L, CHENG Z X, WU H T, YE F X, ZHANG K K. Improvement on mechanical properties and wear resistance of HVOF sprayed WC-12Co coatings by optimizing feedstock structure[J]. Applied Surface Science, 2014, 320(30): 364-371.
[5] PICAS J A, RUP
REZ E, PUNSET M, FORN A. Influence of HVOF spraying parameters on the corrosion resistance of WC-CoCr coatings in strong acidic environment[J]. Surface and Coatings Technology, 2013, 225: 47-57.
[6] VENTER A M, OLADIJO O P, LUZIN V, CORNISH L A, SACKS N. Performance characterization of metallic substrates coated by HVOF WC-Co[J]. Thin Solid Films, 2013, 549: 330-339.
[7] DING Z X, CHEN W, WANG Q. Resistance of cavitation erosion of multimodal WC-12Co coatings sprayed by HVOF[J]. Transactions of Nonferrous Metals Society of China, 2011, 21(10): 2231-2236.
[8] WANG L J, QIU P X, LIU Y, ZHOU W X, GOU G Q, CHEN H. Corrosion behavior of thermal sprayed WC cermet coatings containing metallic binders in saline environment[J]. Transactions of Nonferrous Metals Society of China, 2013, 23(9): 2611-2617.
[9] WANG Q, ZHANG S Y, CHENG Y L, XIANG J. Wear and corrosion performance of WC-10Co4Cr coatings deposited by different HVOF and HVAF spraying processes[J]. Surface and Coatings Technology, 2013, 218: 127-136.
[10] ASTM G 105-02. Standard test method for conducting wet sand/rubber wheel abrasion tests[S].
[11] MACHIO C N, AKDOGAN G, WITCOM M J, LUYCKX S. Performance of WC-VC-Co thermal spray coatings in abrasion and slurry erosion tests[J]. Wear, 2005, 258(1/4): 434-442.
[12] FERN
NDEZ J E, del ROCI
O FERN
NDEZ M, DIAZ R V, NAVARRO R T. Abrasive wear analysis using factorial experiment design[J]. Wear, 2003, 255(1/6): 38-43.
[13] THAKARE M R, WHARTON J A, WOOD R J K, MENGER C. Effect of abrasive particle size and the influence of microstructure on the wear mechanisms in wear-resistant materials[J]. Wear, 2012, 276/277: 16-28.
[14] 刘 明, 王振国, 黄伟九. Hank’s 模拟体液中医用TLM 合金的微磨粒磨损行为[J]. 中国有色金属学报, 2014, 24(5): 1293-1299.
LIU Ming, WANG Zhen-guo, HUANG Wei-jiu. Micro-scale abrasive wear behavior of medical material TLM alloy in Hank’s simulated body fluids[J]. The Chinese Journal of Nonferrous Metals, 2014, 24(5): 1293-1299.
[15] 倪继良, 程涛涛, 丁坤英, 王志平. WC粒度对WC-10Co-4Cr涂层磨粒磨损性能的影响[J]. 材料保护, 2013, 46(1): 19-21.
NI Ji-liang, CHENG Tao-tao, DING Kun-ying, WANG Zhi-pin. Effect of the WC size on the abrasive wear performance of WC-10Co-4Cr coating[J]. Materials Protection, 2013, 46(1): 19-21.
[16] WANG Q, CHEN Z Z, LI L X, YANG G B. The parameters optimization and abrasion wear mechanism of liquid fuel HVOF sprayed bimodal WC-12Co coating[J]. Surface and Coatings Technology, 2012, 206(8/9): 2233-2241.
[17] GAHR K H Z. Microstructure and wear of materials[M]. Amsterdam: Elsevier Science Publishers, 1987: 340-345.
[18] JOSEPH H T, ALBANY O. ASM handbook (Vol. 18): Friction, lubrication and wear technology[M]. USA: ASM International, 1992: 353.
[19] ASL M S, KAKROUDI M G, NOORI S. Hardness and toughness of hot pressed ZrB2-SiC composites consolidated under relatively low pressure[J]. Journal of Alloys and Compounds, 2015, 619: 481-487.
(编辑 王 超)
基金项目:湖南省科学计划项目(2013WK3027);湖南省青年骨干教师项目(521298863)
收稿日期:2014-10-30;修订日期:2015-05-19
通信作者:王 群,副教授,博士;电话:13787113453,E-mail:13787113453@163.com