
Corrosion resistance of Mg-Mn-Ce magnesium alloy modified by polymer plating
SANG Jing(桑 静), KANG Zhi-xin(康志新), LI Yuan-yuan(李元元)
School of Mechanical and Automotive Engineering, South China University of Technology, Guangzhou 510640, China
Received 12 June 2008; accepted 5 September 2008
Abstract: Polymeric nano-film on the surface of Mg-Mn-Ce magnesium alloy was fabricated by polymer plating of 6-dihexylamino-1, 3, 5-triazine-2, 4-dithiol monosodium (DHN) to improve its corrosion resistance. The electrochemical reaction process was analyzed by cyclic voltammetry and two obvious peaks of oxidation reaction were observed. The static contact angle of distilled water on polymer-plated surface can be up to 106.3? while on the blank surface it is 45.8?. Potentiodynamic polarization results show that the polymeric film can increase the corrosion potential from -1.594 V vs SCE for blank to -0.382 V vs SCE. The results of electrochemical impedance spectroscopy indicate that the charge transfer resistances of blank and polymer-plated Mg-Mn-Ce alloy are 485 Ω?cm2 and 2 717 Ω?cm2, respectively. The method of polymer plating can provide a novel approach for fabricating hydrophobic film on Mg-Mn-Ce alloy surface and improving its anti-corrosion property.
Key words: magnesium alloy; polymer plating; nano-film; hydrophobic film; potentiodynamic polarization; electrochemical impedance spectroscopy; corrosion resistance
1 Introduction
Magnesium and its alloys are increasingly being used as attractive materials in several industrial applications especially in the automotive and aerospace industries according to their low density, high strength/mass ratio, easy machining, good recycling efficiency and good castability[1-2]. Magnesium materials also present specific electromagnetic shielding properties, which widens the range of application to different electronic industry sectors[3]. Unfortunately, the potential use of many magnesium alloys has been seriously limited because of their susceptibility to corrosion. In aqueous media the magnesium alloys corrode easily when even a small amount of aggressive ions is present in the solution. The standard electrochemical potential of magnesium is 2.4 V (NHE), even though in aqueous solutions it shows a potential of about 1.5 V due to the formation of Mg(OH)2 film. This film is unstable in acid or neutral solutions but quite stable under alkaline conditions. Accordingly, under nearly neutral conditions, even in the presence of a very small concentration of aggressive ions, there is dissolution of the Mg hydroxide and corrosion develops at a high rate. Therefore, there are many researches on some effective methods to increase the corrosion resistance and improve the paint adhesion properties of magnesium alloys[4-5].
There are mainly four approaches for the protection of Mg against corrosion[6], which are electroless nickel and electroplating[7], anodization and micro-arc oxidation [8], chemical conversion coating[9] and surface modification [10]. Electrochemical method by way of one of the surface modification methods has been used in many researches and practical applications in recent years[11]. In previous work, by means of electrochemical polymerization of the triazine dithiol derivatives, nano- scale polymeric films were deposited on the surface of conductive metallic substrates such as magnesium alloys, copper, iron and aluminum alloy by polymer plating method[12-15]. In addition, plenty of practical applications were carried out successfully, for instance, direct joining of metals to rubbers, inhibiting metallic corrosion, fabricating hydrophilic surfaces and preparation of the high dielectric film by polymer plating[16-19]. However, the polymer plating electrochemical process on the surface of magnesium alloys should be further studied.
2 Experimental
2.1 Materials
The magnesium alloy is Mg-Mn-Ce alloy and its chemical composition is listed in Table 1. Tested samples (30 mm×50 mm×1.5 mm) were cut from a sheet of Mg-Mn-Ce alloy. The surfaces of sample were smoothed with a series of abrasive grinding papers finally with No. 2000 emery papers up to 8 μm. Prior to experiment the smoothed plates were rinsed with acetone and dried in cold air.
Table 1 Chemical composition of Mg-Mn-Ce alloy (mass fraction, %)

The solute of the polymer plating solution is the monomer of 6-dihexylamino-1, 3, 5-triazine-2, 4-dithiol monosodium (Abbrev, DHN). This kind of organic material with thiol radicals which have a strong affinity to bivalent metals was synthesized. NaOH was used as the supporting electrolyte. The concentrations of DHN and NaOH were kept constant at 5 mmol/L and 0.15 mol/L, respectively. All of the chemical reagents used were analytical reagent (AR), and the distilled water was used as the solvent.
2.2 Polymer plating
The polymer plating of DHN was performed using the electrochemical workstation (IM6ex, Zahner). The electrolytic cell was equipped with a tri-electrode electrochemical unit which contained Mg-Mn-Ce alloy plate as working electrode, two smoothly polished SUS304 plates (30 mm×50 mm×1.5 mm) as the counter electrodes and saturated calomel electrode (SCE) as the reference electrode. The polymer plating on Mg-Mn-Ce alloy surfaces used the electrochemical method of cyclic voltammograms (CV), whose potential ranged from the rest potential to 2.0 V (vs SCE, the same as below) at a scanning rate of 5 mV/s. The whole process of CV was performed in aqueous solution containing DHN and NaOH by three scanning cycles. In order to well research the process and mechanism of polymer plating, four characteristic points on CV curves were investigated. At those points, the measurements of CV were terminated. The CV polymer plating was performed at 15 ℃ in the aqueous solution without any stirring. After the polymer plating, the working electrode was immediately removed from the electrolytic cell and rinsed with distilled water and ethanol, and dried in cool air.
2.3 Measurements
The contact angles of polymer-plated Mg-Mn-Ce alloy plates with diverse terminated potentials were measured by optical contact angle measuring instrument (OCA35, Dataphysics) at ambient temperature with 1 μL distilled water. Water droplets were dropped carefully onto the surfaces and the average value of three measurements in different positions of the sample was adopted as the contact angle. The film thickness formed on the Mg-Mn-Ce alloy surface was determined by a spectroscopic ellipsometer(UVISEL-NIR-FGMS, Horiba Jobin Yvon).
The corrosion tests were carried out by the electrochemical measurements of potentiodynamic polarization and electrochemical impedance spectroscopy (EIS). The electrolytic cell was also equipped by a tri-electrode electrochemical unit. Besides, the work electrode, the reference electrode and the counter electrode were SCE in a luggin capillary and Pt plate respectively. Both electrochemical measurements were carried out in a 0.1 mol/L NaCl aqueous solution at 25 ℃ with an IM6ex electrochemical system. The potentiodynamic polarization test was carried out at 1 mV/s scanning rate. The potential range of the potentiodynamic polarization was between -2.0 V and -1 V on the blank Mg-Mn-Ce alloy, while the potential of the polymer-plated samples was performed between -1 V and 0.2 V. The EIS measurement was recorded at 5 mV potential amplitude and the frequency of the potential perturbation was varied from 30 kHz to 10 mHz.
3 Results and discussion
3.1 Electrochemical reaction during polymer plating
The conventional CV is regarded as a large potential amplitude technique. Additionally, it is still a very convenient tool that provides a general view of electro-chemical reaction process. Qualitative differences in the shape of CV curves of electrodes may provide useful information on the impact of the changes on electrochemical response[20-21]. In the present research, the work electrode was polarized from rest potential to 2.0 V and back to 0 V for the first cycle. After the first cycle, the potential was performed between 0 V and 2.0 V. The whole process of CV was made at a potential scanning rate of 5 mV/s.
Fig.1 shows the typical CV process of the first to third cycle recorded during the polarization of Mg-Mn- Ce alloy only in a 0.15 mol/L NaOH aqueous solution without DHN monomer. The rest potential is -1.55 V,
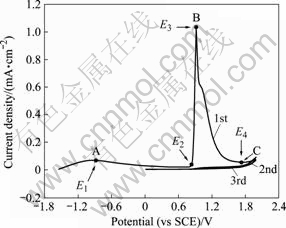
Fig.1 Cyclic voltammograms of Mg-Mn-Ce plate in 0.15 mol/L NaOH solution without DHN monomer
then two peaks can be observed, which are marked as A and B. Basically, two electrochemical action steps of magnesium (Mg) in the NaOH aqueous solution can be distinguished in the CV curves, corresponding to two obvious peaks A and B, respectively.
According to the thermodynamic theory, the transformation of Mg to Mg2+ in reaction (2) was realized by the interim reaction (3). At the beginning of the reaction, the current density increased with the increasing potential. After transcending the highest point of 0.11 mA/cm2, the current density decreased and the peak A formed at -0.85 V. It is supposed that magnesium was oxidized to Mg+. The anodic dissolution of Mg+ hardly underwent to produce the bivalent magnesium ions because reaction (3) was limited to the low potential.
Mg→ Mg+ +e (1)
Mg→ Mg2+ +2e (2)
Mg+ + H2O→Mg2++OH-+(1/2)H2 (3)
The second step of Mg being oxidized (reaction (3), oxidation-peak B in Fig.1) into Mg2+ is due to the aqueous alkali environment of the reaction. Peak B can be observed as a sharp rise of current density measured at 0.91 V attributed to the vigorous oxidation of the magnesium and development of univalent magnesium to bivalent magnesium ions. The current density of peak B is up to 1.11 mA/cm2 resulting from the adequately high potential and the accumulation of Mg+ at the first step. A mount of Mg+ ions promoted the transformation from Mg to Mg2+. From the appearance of work electrode, the color was darker than that of the blank magnesium plate. This indicates that the magnesium oxides of MgO and/or Mg(OH)2 are produced. The third peak C, seen after 1.8 V, is supposed that water is hydrolyzed under such high potential as numerous bubbles are observed on the surfaces of the Mg-Mn-Ce alloy plate, two counter electrodes and solution through vision inspection.
To examine the response of the magnesium electrode polarized in the 0.15 mol/L NaOH aqueous solution with 5 mmol/L DHN monomer, the CV curves are presented in Fig.2. We can see that the flat stage marked as A at the beginning of the reaction becomes longer, but lower in current density, as the solution changes from without DHN to with DHN (0.11 to 0.017 mA/cm2). This flat stage A clarifies that the reaction between Mg ions and DHN produces a thin film on the Mg-Mn-Ce substrate, and the lower current density indicated the oxidation of magnesium to form Mg+ is depressed.
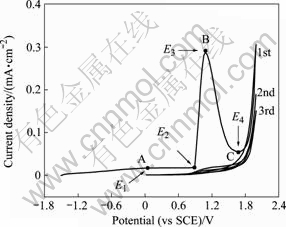
Fig.2 Cyclic voltammograms of Mg-Mn-Ce plate in 0.15 mol/L NaOH solution containing 5 mmol/L DHN
After the flat stage A, an obvious peak of oxidation reaction signed as B can be observed during polymer plating. It is considered that the electrochemical polymerization of organic species happens, and the film thickness increases. Moreover, peak B has the higher potential but lower current density than that in blank solution (from 0.91 V to 1.086 V and from 1.11 mA/cm2 to 0.288 mA/cm2, respectively). It can be accounted for some reasons, first, the reaction between DHN and magnesium substrate restrains the further oxidation of magnesium; second, the forming and increasing of organic film improve the impedance of the magnesium surface (see discussion on the result obtained by EIS below), which makes the current density decrease; third, at this step of polymerization reaction there are still DHN monomers reacted with the magnesium substrate to make the formed film more compact. After the polymer plating of CV for 1 cycle and 3 cycles, the film thicknesses are 35.1 nm and 47.5 nm, respectively.
3.2 Wettability of polymeric films on Mg-Mn-Ce alloy surface
To fully understand the formation and growth of nano-film, the qualities of nano-film during cyclic voltammograms of polymer plating were studied by the wettability of those polymeric films on the Mg-Mn-Ce alloy surface.
We defined the potentials of four typical points terminated at E1, E2, E3, E4 on CV curves, as seen in Fig.2. Fig.3 and Fig.4 show the relations between the contact angle of distilled water and E corresponding to CV curves with and without DHN monomer. It is clearly observed that the contact angle decreases from 45.8? for the blank Mg-Mn-Ce of the distilled water alloy to 31.2? for that polarized by the cyclic voltammogram process stopping at E4, while the polymer-plated sample polarized in DHN solution increases to 106.3? at E4. It is considered that the contact angle of ample without polymer plating decreases due to the loose and porous oxide formation on the Mg-Mn-Ce alloy surface. However, the polymer-plated sample gained the hydrophobic surface, because PDH polymerized on magnesium by the electrochemical method modified the wettability of its surface.
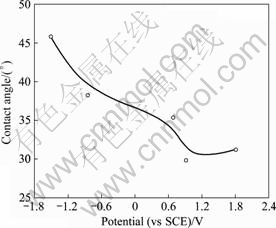
Fig.3 Relationship between contact angle and potential in NaOH solution
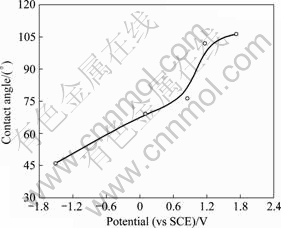
Fig.4 Relationship between contact angle and potential in DHN solution
To research the changing trend of the contact angles after E4 during the CV reaction, we also measured the contact angles of plates after 1 cycle, 2 cycles and 3 cycles, as shown in Table 2. It can be found that the contact angles almost keep constant after E4 both with DHN. Therefore, it can be concluded that the packed polymeric thin film is formed on its surface after E4, while the continuous decrease of contact angles of plates polarized in solution without DHN after E4 demonstrated that magnesium surface was continually oxygenized to form MgO and/or Mg(OH)2.
Table 2 Relationship between potential and contact angle

3.3 Corrosion resistance of polymer-plated Mg-Mn- Ce alloy
The corrosion current density Jcorr and corrosion potential Ecorr of the Mg-Mn-Ce alloy were measured in the range of -2--1 V for blank one and -1-2 V for DHN polymer-plated one by potentiodynamic polarization in 0.1 mol/L NaCl solution. In Fig.5, it is clearly shown that Jcorr declines from 42 000 nA/cm2 for the blank (Fig.5(a)) alloy to 26.2 nA/cm2 for the polymer-plated one at E3 (Fig.5(b)). Ecorr of polymer-plated sample becomes much nobler than the blank one which increases from -1.512 V to -0.463 V.
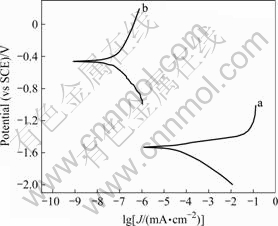
Fig.5 Polarization curves for Mg-Mn-Ce plates in 0.1 mol/L NaCl solution: (a) Blank; (b) Polymer-plated terminated at E3
During the potentiodynamic polarization of the blank magnesium, plentiful bubbles were observed, visible localized attack occurred, and amounts of erodent product formed. But no visible localized attack occurred on the polymer-plated ones.
Table 3 presents Jcorr and Ecorr of potentiodynamic polarization at different terminating potentials. It can be seen that the polymeric film reduces the corrosion rate of the Mg-Mn-Ce and increases its corrosion potential rapidly before E4. Compared with the blank one, the corrosion current density of the polymer-plated plate reduces more than 2 000 times. Afterward, Jcorr ascends a little while the corrosion potential decreases slightly. It can be considered that the hydrolysis process destroys the nano-film to a certain extent.
Table 3 Corrosion parameters from potentiodynamic polarization
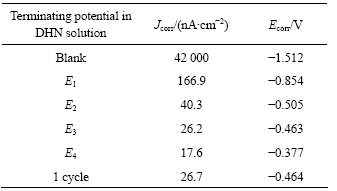
The protection efficiency (PE) was calculated by the following expression[13]:
PE(%)=100×(1-J/J0) (6)
where J and J0 in the expression are the corrosion current density of the DHN polymer-plated and the blank Mg-Mn-Ce, respectively. The protection efficiency calculated from potentiodynamic polarization data can be as high as 99.96%. This reveals that the PDH film acts as a protective layer on the Mg-Mn-Ce surface and improves the overall corrosion performance.
EIS was carried out in order to well investigate the stability of the nano-scale polymeric film during an exposure to 0.1 mol/L NaCl solution. Fig.6 shows the typical Nyquist plots of plate for the blank (Fig.6(a)) and the PDH-covered Mg-Mn-Ce plates at E3 (Fig.6(b)).
EIS measurement curves exhibit the same shape, which means they have the same corrosion mechanism, and the capacitive loop at high and intermediate frequencies has been attributed to the charge transfer process[22-23]. Moreover, the charge transfer resistance (Rct) values can be evaluated according to the diameter of semicircles. It is supposed that the corrosion mechanism of the blank Mg-Mn-Ce alloy and the polymer-plated one
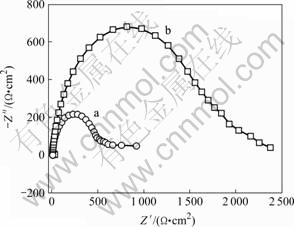
Fig.6 Nyquist plots for Mg-Mn-Ce plates in 0.1 mol/L NaCl solution: (a) Blank; (b) Polymer-plated terminated at E3
are extremely similar. In Table 4, Rct of the polymer-plated Mg-Mn-Ce at E4 is 2 717 Ω?cm2 that is higher than that of the blank one (485 Ω?cm2). The trend of Rct goes along with the experimental results of the potentiodynamic polarization.
Table 4 Relation between terminating potential in DHN solution (Et) and charge transfer resistance (Rct)
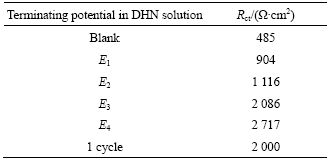
4 Conclusions
1) Excellent poly(6-dihexylamino-1, 3, 5-triazine-2, 4-dithiol) films have successfully fabricated on the Mg-Mn-Ce alloy by the polymer plating. The result of the cyclic voltammograms reveals that the formation and growth processes of the polymeric film consist of two steps. The first step is the reaction between the Mg-Mn-Ce and the DHN monomer to produce the Mg-DHN complexes, and the second step is the polymerization between the DHN monomers for the increasing of film thickness.
2) The polymer-plated Mg-Mn-Ce alloy surface is modified from hydrophilic into hydrophobic characteristic. The contact angle of the distilled water is high to 106.3?.
3) The potentiodynamic polarization and the EIS measurements reveal that the PDH acts as a protective layer against corrosion in the 0.1 mol/L NaCl solution. The protection efficiency of the polymer-plated one is as high as 99.96%. The corrosion current density decreases from 42 000 nA/cm2 for the blank to 17.6 nA/cm2 for the polymer-plated one when the CV experiment terminated at E4, over 2 000 times lower than blank one. Furthermore, the charge transfer resistances increase from 485 Ω?cm2 for the blank to 2 717 Ω?cm2, respectively. Hence, the polymer-plated surface modified with the hydrophobic characteristics has excellent anti-corrosion property.
References
[1] ANIK M, CELIKTEN G. Analysis of the electrochemical reaction behavior of alloy AZ91 by EIS technique in H3PO4/KOH buffered K2SO4 solutions [J]. Corrosion Science, 2007, 49(4): 1878-1894.
[2] BARCHICHE C E, ROCCA E, JUERS C, HAZAN J, STEINMETZ J. Corrosion resistance of plasma-anodized AZ91D magnesium alloy by electrochemical methods [J]. Electrochimica Acta, 2007, 53(2): 417-425.
[3] MONTEMOR M F, SIMOES A M, FERREIRA M G S, CARMEZIM M J. Composition and corrosion resistance of cerium conversion ?lms on the AZ31 magnesium alloy and its relation to the salt anion [J]. Applied Surface Science, 2008, 254(6): 1806-1814.
[4] BRUNELLI K, DABALA M, CALLIARI I, MAGRINI M. Effect of HCl pre-treatment on corrosion resistance of cerium-based conversion coatings on magnesium and magnesium alloys [J]. Corrosion Science, 2005, 47(4): 989-1000.
[5] WELLMAN R G, NICHOLLS J R. A review of the erosion of thermal barrier coatings [J]. Journal of Physics D-Applied Physics, 2007, 40(16): R293-R305.
[6] SONG G, ATRENS A. Recent insights into the mechanism of magnesium corrosion and research suggestions [J]. Advanced Engineering Materials, 2007, 9(3): 177-183.
[7] BAKKAR A, NEUBERT V. Electrodeposition onto magnesium in air and water stable ionic liquids: from corrosion to successful plating [J]. Electrochemistry Communications, 2007, 9(9): 2428-2435.
[8] DUAN H P, DU K Q, YAN C W, WANG F H. Electrochemical corrosion behavior of composite coatings of sealed MAO film on magnesium alloy AZ91D [J]. Electrochimica Acta, 2006, 51(14): 2898-2908.
[9] YAMAUCHI N, UEDA N, OKAMOTO A, SONE T, TSUJIKAWA M, OKI S. DLC coating on Mg-Li alloy [J]. Surface & Coatings Technology, 2007, 201(9/11): 4913-4918.
[10] TAMAR Y, MANDLER D. Corrosion inhibition of magnesium by combined zirconia silica sol-gel films [J]. Electrochimica Acta, 2008, 53(16): 5118-5127.
[11] BJO1REFORS F, PETORAL R M, Jr, UVDAL K. Electrochemical impedance spectroscopy for investigations on ion permeation in ω-functionalized self-assembled monolayers [J]. Analytic Chemistry, 2007, 79(21): 8391-8398.
[12] KANG Z X, MORI K, OISHI Y. Surface modification of magnesium alloys using triazine dithiols [J]. Surface & Coatings Technology, 2005, 195(2/3): 162-167.
[13] YE Q, KANG Z X, LI Y Y. Electrochemical performance of organic film on copper surface by polymer plating of 6-mercapto-1, 3, 5-triazine-2, 4-dithiol monosodium [J]. Trans Nonferrous Met Soc China, 2007, 17(s): s747-s751.
[14] MORI K, KANG Z X, OISHI Y. Effect of 6-dioctylamino-1, 3, 5-triazine-2, 4-dithiol concentration on the polymer plating on iron plates [J]. Polymer Journal, 2005, 37(11): 862-865.
[15] WANG F, MORI K, KANG Z X, OISHI Y, Magnetic field effects on the polymerization of 6-N, N-dioctylamino-1, 3, 5-triaziene-2, 4-dithiol [J]. Heteroatom Chemistry, 2007, 18(1): 60-64.
[16] KANG Z X, LI Y Y, ZHONG C W, SHAO M, XIA W. Direct joining of acrylic rubber to cast iron with functional nanofilm by polymer plating [J]. Key Engineering Materials, 2006, 315/316: 491-495.
[17] KANG Z X, LI Y Y, MORI K. Application of polymer plating to inhibit corrosion of magnesium alloy [J]. Materials Science Forum, 2005, 488/489: 661-664.
[18] MORI K, KANG Z X, ORAVEC J, OISHI Y. Direct adhesion of PPS to polymer-plated magnesium alloys [J]. Materials Science Forum, 2003, 419/422: 921-926.
[19] MORI K, KANG Z X, WANG F, OISHI Y. Polymer plating of 6-(N-allyl-1, 1, 2, 2-tetrahydroperfluorodecyl)amino-1, 3, 5-triazine-2, 4-dithiol monosodium on aluminum in magnetic field and its electrostatic capacity [J]. IEEE Transactions on Applied Superconductivity, 2004, 14(2): 1177-1180.
[20] SURESH G S, LEVI M D, AURBACH D. Effect of chalcogen substitution in mixed Mo6S8-nSen (n=0, 1, 2) Chevrel phases on the thermodynamics and kinetics of reversible Mg ions insertion [J]. Electrochimica Acta, 2008, 53(11): 3889-3896.
[21] KONG X H, WANG M, LEI S B, YANG Y L, WANG C. Electronic sensory behavior of titanylphthalocyanine revealed by scanning tunneling spectroscopy and cyclic voltammetry methods [J]. Journal of Materials Chemistry, 2006, 16(43): 4265-4269.
[22] HUR E, BEREKET G, SAHIN Y. Corrosion inhibition of stainless steel by polyaniline, poly(2-chloroaniline), and poly (aniline-co-2- chloroaniline) in HCl [J]. Progress in Organic Coatings, 2006, 57(2): 149-158.
[23] AMIRA S, LAFRONT A M, DUB? D, TREMBLAY R, GHALI E. Electrochemical study of AXJ530 magnesium alloy behavior in alkaline NaCl solution [J]. Advanced Engineering Materials, 2007, 9(11): 973-980.
(Edited by LI Xiang-qun)
Foundation item: Project(50673028) supported by the National Natural Science Foundation of China; Project(04020090) supported by Guangdong Natural Science Foundation, China
Corresponding author: KANG Zhi-xin, Tel: +86-20-87113851; E-mail: zxkang@scut.edu.cn