
Voltage-induced material removal mechanism of copper for electrochemical-mechanical polishing applications
Sang-Jun HAN1, Yong-Jin SEO2
1. Nano-Information Material & Device Laboratory, Daebul University, Chonnam, 526-702, Korea;
2. School of Fusion Technology, Daebul University, Chonnam, 526-702, Korea
Received 2 March 2009; accepted 30 May 2009
Abstract: The current—voltage (I—V) curves, such as linear sweep voltammetry (LSV) and cyclic voltammetry (CV), were employed to evaluate the effect of electrolyte concentration on the electrochemical reaction trend. From the I—V curve, the electrochemical states of active, passive, transient and trans-passive region could be characterized. And then, the mechanism of the process of voltage-induced material removal in electrochemical mechanical polishing (ECMP) of copper was investigated. Scanning electron microscopy (SEM) and energy dispersive spectroscopy (EDS) analyses were used to observe the surface profile. Finally, the oxidation and reduction processes of the Cu surface were monitored by the repetition of anodic and cathodic potential from cyclic voltammetry (CV) method in acid- and alkali-based electrolyte.
Key words: electrochemical mechanical polishing; linear sweep voltammetry; cyclic voltammetry; HNO3; KNO3; electrolyte
1 Introduction
The chemical mechanical polishing (CMP) process has been widely used to obtain the global planarization of inter-metal dielectric (IMD) layers, inter-layer dielectric layers (ILD) and pre-metal dielectric (PMD) layers[1-2]. Also, the CMP is the most commonly used planarization technique in semiconductor process for ultra-large scale integrated circuit (ULSI) applications [3-4]. As its name indicates, the CMP process depends on the chemical interaction of the slurry with polishing wafer and mechanical down force applied to the wafer. Recently, the application of CMP has been especially popular in the fabrication of copper (Cu) damascene structures and multi level interconnection process[5-7]. However, low-k materials at 65 nm and below device structures, because of fragile property, require low down-force mechanical polishing for maintaining the structural integrity of under layer during their fabrication[8]. Also, the problems faced by Cu-CMP process are the lower removal rate due to the low mechanical down force required by the low-k dielectric, and to reduce dishing and erosion. To overcome these problems, the electrochemical mechanical polishing (ECMP) technology, a new planarization technology that uses electrolyte chemistry instead of abrasive slurry, was developed[8-11]. In this paper, the current—voltage (I—V) curves were employed to evaluate the effect of electrolyte concentration on the electrochemical surface reaction of Cu electrode. From this I—V curve, the electrochemical states of active, passive and trans- passive region could be characterized[12-13]. It is difficult to distinguish between adsorption and desorption (or anodic and cathodic) processes. And then, we investigated how this chemical electrolytes affect the process of voltage induced material removal in Cu-ECMP. To selectively probe the electrochemical effect of ECMP, all these measurements were performed in the absence of mechanical polishing.
2 Experimental
In brief, Cu disks of 2 cm×2 cm size with a purity of 99.99% were used as an experimental species in a standard two-electrode glass cell containing a Pt counter electrode (CE) of mesh type and a Cu working electrode (WE) as shown in Fig.1. Electrical connection to the sample was made through a modified alligator clip at the upper part of the Cu disk, while the sample was electro- chemically controlled by a DC power supply system, interfaced with a personal computer as shown in Fig.1. All experiments were performed at room temperature, in the absence of the mechanical polishing. De-ionized water and reagent grade chemicals were used to prepare the electrolytes of KNO3 and HNO3, with different concentration levels as follows: 5%, 10% and 20% (mass fraction), respectively. Keithley 236 model I—V measurement system, which consists of source measure unit (SMU) and 2361 trigger, was used to analyze the I—V curves of a Cu electrode in various electrolyte concentration and to find out the proper operating voltage at each electrochemical state. The I—V curves were plotted for each of the electrolyte concentration. From the I—V curves, the electrochemical states of active, passive, transient and trans-passive region could be characterized[12]. Appropriate operating voltages would be selected from these curves for the following quantitative tests. In quantitative analyses, the electrochemical process without the mechanical polishing process was performed in order to verify the relationship between the dissolved mass loss and applied voltages, when the selected operating voltages were applied during the constant process time such as 30, 60, 90 and 120 s, respectively. The sample masses before and after the quantitative test were measured on precision electronic scale to calculate the removal thickness of Cu disk. Finally, we fundamentally studied the chemical state and element composition of the Cu surface according to the concentration of the electrolyte and energy dispersive spectroscopy (EDS) analysis, respectively. In this way, we monitored the oxidation and reduction step of the Cu surface by the repetition of anodic and cathodic potential in KNO3 and HNO3 electrolyte.
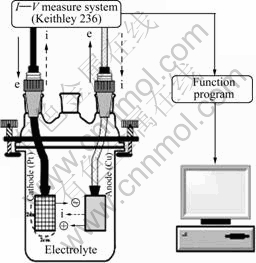
Fig.1 Schematic diagram of I—V measurement system with two-electrode cell
3 Results and discussion
Fig.2 shows the I—V curves as a function of KNO3 and HNO3 electrolyte with concentration of 5%, 10% and 20%. As the concentrations of KNO3 electrolyte are increased, the trans-passive voltages are decreased and the current density is more increased. Thus, a plateau region, so called passive state, is not formed. This reason is because a continuous passive oxide or metallic hydroxide remains on the Cu surface. As the voltage more increases, the potential is great enough to pull the metallic ion through the passive film. Although there are changes of operating voltage and current density according to the electrolytes concentration, we point out that the ranges of proper operating voltage for subsequent ECMP experiment are between 0.5 V and 1.0 V. Also, as the concentration of HNO3 electrolyte increases, the transient voltages are decreased and the curve slope of trans-passive state is more and more steep. This indicates that the I—V relationship strongly depends on the concentration of electrolyte.
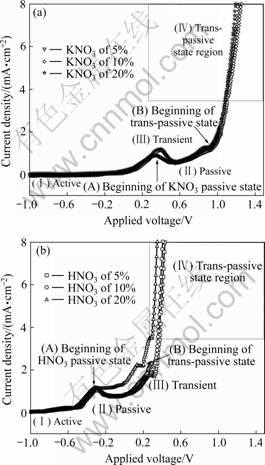
Fig.2 I—V curves of KNO3(a) and HNO3(b) electrolyte with different concentration
Fig.3 shows the Cu removal rates as function of voltage-activated process times in the different concentration of KNO3 and HNO3 electrolytes. As the concentration of electrolyte and operating time increase, the removal amounts are increased. The data points for electrolytes with different concentrations are denoted by the different symbols identified in symbol box of Fig.3. We observed a linear dependence of removal rate on operating process time as shown in Fig.3(a). In the case of KNO3 electrolyte, the respective dependence equations are y= -0.01x+18.18 (solid line, 5% KNO3), y=0.17x-9.79 (dashed line, 10% KNO3), and y= 0.32x-11.19 (dashed-dot line, 20% KNO3), respectively. However, in the case of HNO3 electrolyte, the polynomial dependence is obtained from 20% electrolyte. The respective dependence equations are y=0.33x+21.0 (solid line, 5% HNO3), y=0.58x+48.9 (dashed line, 10% HNO3) and y= -0.02x2+4.3x-2.1 (dashed-dot line, 20% HNO3), respectively. The slopes represent the global averages of Cu removal rates for all the voltage activation treatment using different value of process time and electrolyte concentration.
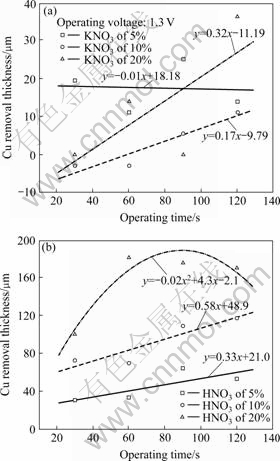
Fig.3 Evaluation of Cu removal rate according to slope of operating time and in different concentration of KNO3(a) and HNO3(b) electrolytes
Fig.4 shows the cyclic voltammograms (CV) of Cu electrode as a function of KNO3 and HNO3 electrolyte concentrations. When the positive-going voltage scans from -2 000 mV to 2 000 mV, this electrochemical reaction corresponds to oxidation (O) step (R→O+ne-; Cu→Cu2++2e-). Whereas, when the negative-going voltage scans from 2 000 mV to -2 000 mV, this electrochemical reaction corresponds to reduction (R) step (R←O+ne-; Cu←Cu2++2e-). In all cases, we observed both anodic and cathodic currents, and the originating surface reactions of these currents determine the surface reactivity of Cu under the given electrolyte conditions. These reactions are well known from previously published studies of ROY’s working group[8, 10-11]. The anodic peak (Epa) in the increasing (positive-going) voltage scan can be associated with anodic stripping of Cu ions. The relatively weak cathodic peak (Epc) occurs in the decreasing (negative-going) voltage scan, and can be attributed to under potential deposition (UPD) of Cu ions.
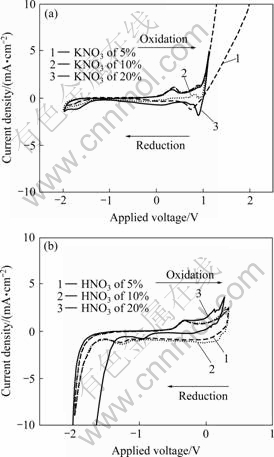
Fig.4 Cyclic voltammograms of Cu electrode as function of concentrations of KNO3(a) and HNO3(b) electrolytes
Fig.5 compares the oxygen and copper contents obtained from metallurgical compositions of Cu by the energy dispersion spectroscopy (EDS) analysis. In the case of passive state, the copper content is decreased, and oxygen content is increased. This indicates the beginning of stripping of Cu ions. Also, this verifies aforementioned stripping mechanism of Cu ions from electrochemical Cu surface as shown in Fig.4. It is guessed that Cu ions generated by dissolution of Cu within the HNO3 and KNO3 electrolyte during the voltage treatment are electrochemically reacted through the repetition of adsorption (re-deposition) and desorption (stripping) procedure.
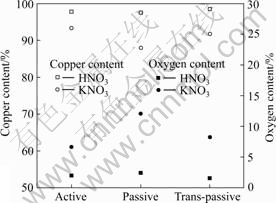
Fig.5 Oxygen and copper contents obtained from metallurgical compositions of Cu by EDS analysis in KNO3 and HNO3 electrolytes
4 Conclusions
From the I—V relationship obtained by linear sweep voltammetry (LSV), the candidates of operating voltages and concentration of electrolyte for next ECMP application could be determined. In order to obtain the high removal thickness under the trans-passive state of 1.3 V (in the case of KNO3) and 0.7 V (in the case of HNO3), it is proper to select a high concentration between 10% and 20%. Also, DC voltage-controlled re-deposition and stripping mechanism of Cu were investigated from the cyclic voltammetry (CV) curve. Distinctly different sign of deposition and stripping of Cu were observed. The cathodic current peaks correspond to deposition of Cu2+, whereas the anodic peaks represent stripping of bulk and under-potentially deposited copper. Although the ECMP experiment using these selected operating voltages could not be directly performed in this work, the above results demonstrate how proper combinations of the voltage activation and electrolyte can provide accurate control of the rate of material removal in an ECMP application.
Acknowledgement
This work was supported by grant No. R01-2006- 000-11275-0 (2008) from the Basic Research Program of the Korea Science & Engineering Foundation.
References
[1] SEO Y J, PARK S W, KIM C B. Global planarization characteristics of shallow trench isolation-chemical mechanical polishing process with and without reverse moat etch step[J]. Journal of the Korean Physical Society, 2003, 42: 421-424.
[2] SEO Y J, LEE W S. Effects of mixed abrasive slurry in oxide-chemical mechanical polishing[J]. Journal of the Korean Physical Society, 2004, 45: 618-621.
[3] SEO Y J, LEE W S. Chemical mechanical polishing characteristics of barium titanate thin films using mixed abrasive slurry[J]. Journal of the Korean Physical Society, 2006, 48(6): 1651-1656.
[4] SEO Y J, PARK S W. A study on the electrochemical and the chemical mechanical polishing behaviors of W and Ti film[J]. Journal of the Korean Physical Society, 2007, 50(3): 643-649.
[5] LU J, GARLAND J E, PETTIT C M, BABU S V, ROY D. Relative roles of H2O2 and glycine in CMP of copper studied with impedance spectroscopy[J]. Journal of Electrochemical Society, 2004, 151(10): 717-722.
[6] SEAL S, KUIRY S C, HEINMEN B. Effect of glycine and hydrogen peroxide on chemical-mechanical planarization of copper[J]. Thin Solid Films, 2003, 423: 243-251.
[7] SERDAR AKSU, FIONA M. DOYLE. The role of glycine in the chemical mechanical planarization of copper[J]. Journal of Electrochemical Society, 2002, 149(6): 352-361.
[8] GOONETILLEKE P C, ROY D. Electrochemical-mechanical planarization of copper: Effects of chemical additives on voltage controlled removal of surface layers in electrolytes[J]. Materials Chemistry and Physics, 2005, 94: 388-400.
[9] HEWITTA T D, GAOA R, ROY D. Effects of surface charge on the second harmonic generation from a Cu electrode[J]. Surface Science, 1993, 291(1/2): 233-241.
[10] ASSIONGBON K A, EMERY S B, PETTIT C M, BABU S V, ROY D. Chemical roles of peroxide-based alkaline slurries in chemical-mechanical polishing of Ta: Investigation of surface reactions using time-resolved impedance spectroscopy[J]. Materials Chemical and Physics, 2004, 86: 347-357.
[11] GARLAND J E, PETTIT C M, WALTERS M J, ROY D. Analysis of potentiostatic current transients at metal/liquid interfaces: resolving the effects of a finite step interval[J]. Surface Interface Analysis, 2001, 31(6): 492-503.
[12] LEE S J, LEE Y M, DU M F. The polishing mechanism of electrochemical mechanical polishing technology[J]. Journal of Materials Processing Technology, 2003, 140: 280-286.
[13] CHEN Y L, ZHU S M, LEE S J, WANG J C. The technology combined electrochemical mechanical polishing[J]. Journal of Materials Processing Technology, 2003, 140: 203-205.
Corresponding author: Yong-Jin SEO; E-mail: syj@mail.daebul.ac.kr
(Edited by YUAN Sai-qian)