
Environmentally friendly anodization on AZ31 magnesium alloy
DAI Dan(戴 丹), WANG Hui(王 慧), LI Jian-zhong(李建忠), WU Xue-dong(乌学东)
Ningbo Institute of Materials Technology and Engineering, Chinese Academy of Sciences, Ningbo 315201, China
Received 12 June 2008; accepted 5 September 2008
Abstract: A novel anodization which is environmentally friendly, low voltage and low energy consumption was developed to improve corrosion resistance of AZ31 magnesium alloy. The corrosion resistance of the anodic films was studied by electrochemical impedance spectroscopy (EIS) and potentiodynamic polarization techniques. The microstructure and compositions of films were examined by SEM, XPS and XRD. A new kind of organic additive used in the electrolyte is friendly to the environment. The compact, intact and uniform coating with high hardness can be prepared on AZ31 magnesium alloy by the environmentally friendly anodization, which enhances the corrosion resistance of AZ31 Mg alloy significantly.
Key words: magnesium alloy; corrosion; anodization; environmentally friendly
1 Introduction
Magnesium is an attractive metal due to its low density, high specific strength, good machinability and excellent castability. As a structural material, it is used in automotive, aerospace, electronic and telecommunication industries. Unfortunately, its practical applications are limited because it is characterized by low corrosion resistance and wear characteristics[1-5]. In contrast to other surface treatments, anodization can produce a relatively thick, hard, adherent and abrasion-resistant film, which achieves the best corrosion resistance for magnesium and its alloy surfaces[6-8].
The traditional anodization usually contains chromate, fluoride or phosphate which can cause ecological and health problems and also require high energy consumption because high current density and voltage[9]. Therefore, the development of non- chromate, non-fluoride or non-phosphate anodization with low energy consumption will be important to the AZ31 magnesium alloy[10-12].
A novel environmentally friendly anodization without chromate, fluoride or phosphate, which is low voltage and low energy, will be described, and the grayish-white films with excellent corrosion resistance on AZ31 magnesium alloys are obtained.
In this work, the anodization of AZ31 magnesium alloy in an environmentally friendly electrolyte was investigated and the corresponding corrosion resistances of the films were evaluated. The structure, chemical compositions and properties of the anodizing film were studied by SEM, XRD, XPS and potentiodynamic polarization curves.
2 Experimental
AZ31 Mg alloy with chemical composition of 2.96% Al, 0.828% Zn and 0.433% Mg (mass fraction) was chosen. The 2 mm-thick ingot plate was cut into square samples. All samples were connected with copper wire in one side and then enveloped by epoxy resin adhesive leaving an area of 10 mm×10 mm exposed as the working surface. Before anodizing in the electrolyte, the working surface was polished firstly to 800# grit, then to 1 500# grit and successively finished and carefully degreased with acetone and rinsed with distilled water. A stainless steel plate was used as the cathode and the sample was the anode. The composition of the electrolyte bath was 40 g/L NaOH+90 g/L Na2SiO3+30 g/L Na2B4O7·10H2O+6.0g/L additive A, which was prepared with analytical grade reagent and distilled water. The temperature of the anodization process was kept at 298 K and the current density used in the anodization process was fixed at 30 mA/cm2.
Films were acquired and the corrosion resistant properties of the films were measured by electrochemical impedance spectroscopy (EIS) tests and potentiodynamic polarization curves. Electrochemical tests were carried out in 17 mmol/L NaCl + 0.1 mol/L Na2SO4 solution using a computer-monitored electrochemical workstation (Autolab 302). The amplitude of the perturbation signal was 10 mV and the frequency range was 10 mHz-100 kHz. After the EIS measurements, the potentiodynamic electrochemical tests were carried out with scanning rate of 1 mV/s. All of the tests were carried out at room temperature about 25 ℃.
Besides the electrochemical tests, the morphologies of the as-obtained film and corresponding cross-section were observed using scanning electron microscope (manufactured by Hitachi, Japan). The structures and composition of the film were examined by X-ray diffractions (Bruker AXS, Germany). The elemental compositions were determined by X-ray photo spectroscopy (Thermo ESCALAB 250) after the coating surface was cleaned by argon-ion-etching for 1 min.
3 Results and discussion
3.1 Anodizing behaviour
The anodizing process of AZ31 magnesium alloy always coupled with sparking behaviour and oxygen evolution. The variations of the cell voltage of the specimens anodized with tine are shown in Fig.1. The increase of cell voltages indicates the growth of the anodized coatings.
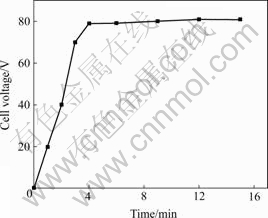
Fig.1 Relationship between cell voltage and time of AZ31 Mg alloy
According to Fig.1, an anodization process can be divided into two stages. In the initial stage, it shows a rapid increase with anodizing time. After 4 min, the cell voltage reaches a relatively stable value and a thick porous anodic layer is formed. From Fig.1, it can be deduced that, with the prolongation of anodizing time, the previously formed oxide film evolves into porous outer layer and thicken with time increasing, while a more compact inner layer simultaneously forms onto the AZ31 magnesium alloy matrix. The outer layer offers little resistance against cell voltages, so the cell voltage remains almost the same during the last anodizing time. After 15 min, a continuous oxide film is found on the working surface of the AZ31 magnesium alloy. It is also deduced that the anodic film is truly composed of two layers [13-16].
3.2 Influences of additive
Additives not only level the anodized film of the AZ31 magnesium alloy, but also modify the structures and consequently improve the anti-corrosive resistances. After adding many organic and inorganic, the results show that the effective organic additive A has excellent effect to form the anodic film with the increase of corrosion resistance (see Fig.2). And the optimized dosage of additive A under experimental conditions is 6.0 g/L. Additive A is a kind of innocuous organic compounds. Additive A improves the anodizing dis- charge voltage, which decreases to 79 V. Consequently, this way can save the energy efficiently. It is not only environmentally friendly but also industrial applicability.
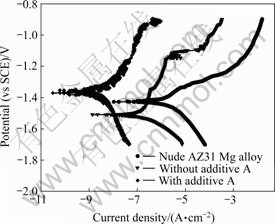
Fig.2 Potentiodynamic polarization curves of anodized AZ31 Mg alloy obtained in electrolytes with different additives
3.3 Characterization of optimized anodization film
Surface and cross-sectional morphologies of the anodized specimens were examined. Fig.3 shows the SEM images of the optimized anodized film obtained in the solution containing 40 g/L NaOH+90 g/L Na2SiO3+ 30 g/L Na2B4O7·10H2O+6.0 g/L additive A at 30 mA/cm2 for 15 min. From Fig.3(b), grayish-white film with thickness of 10 μm is uniform and with low porosity may be caused by the contraction of the anodic film when the molten oxides formed by anodization are cooled by electrolyte. From Fig.3(c), the binding strength between the AZ31 substrate and the coating is excellent.
It can be see from the potentiodynamic polarization curve (see Fig.2) of the optimized anodized film (see
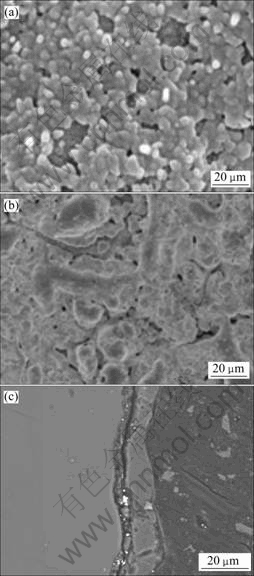
Fig.3 SEM images of surface (a, b) and cross-section(c) of optimized anodization film (40 g/L NaOH+90 g/L Na2SiO3+30 g/L Na2B4O7·10H2O+6.0 g/L additive A, 15 min, 25 ℃)
Fig.3) that, the corrosion current of the optimized anodization film is one thousand times more positive than that of the un-anodized (see Fig.2), which indicates that the former is a much thermodynamically steady system.
In order to probe into the influences of additive A on the structure and the anti-corrosion performance of anodic film, some anodic films obtained at the same anodizing conditions without the additive A were investigated by SEM (see Fig.4) and potentiodynamic polarization techniques (see Fig.2). Comparing Fig.4 and Figs.3(a), 3(b), it can be obviously seen that the surface of the latter possesses much lower porosity and shorter pore diameter, which indicates the surface has much more excellent anti-corrosion performance.
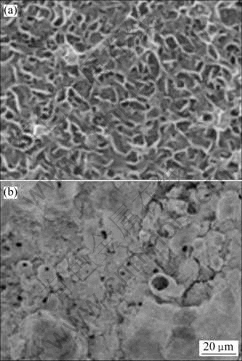
Fig.4 Surface morphologies of anodized AZ31 Mg alloy film without additive A (40 g/L NaOH+90 g/L Na2SiO3+30 g/L Na2B4O7·10H2O, 15 min, 25 ℃)
The structure and the elemental compositions of the optimized anodic film were examined by X-ray diffraction (see Fig.5) and X-ray photon spectroscopy (see Table 1).
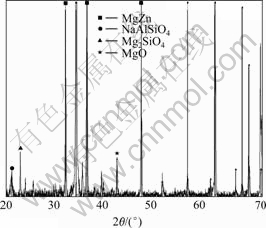
Fig.5 XRD pattern of optimized anodic film (40 g/L NaOH+90 g/L Na2SiO3+30 g/L Na2B4O7·10H2O+6.0 g/L additive A, 15 min, 25 ℃)
Table 1 Chemical compositions of anodized coatings tested by XPS (mole fraction, %)
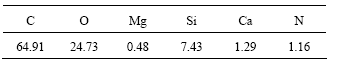
The compositions of the anodization coatings are listed in Table 1. The area detected by XPS was about 1 mm×1 mm. In this area, there are plenty of pores. The coating is thin inside the pores and thick outside the pores. Therefore, the thick film outside the pores and the thin film inside the pores were measured. Hence, the XPS results represent the average composition of an anodization coating. The anodization coatings contain mainly carbon, oxygen and silicon. The content of carbon is near 64.91%, the oxygen content is 24.73% and the content of silicon is 7.43%. A high content of carbon in these coatings is noticed. This can be simply ascribed to the absorption of carbon dioxide, which form the atmosphere after anodizing[17]. The high content of silicon in the coating results from the deposition of the natrium silicate from the bath electrolyte. Combining with the X-ray pattern in Fig.5, it is revealed that the compositions of MgO and Mg2SiO4 have good anti-corrosive properties.
In order to study the corrosion mechanism of the anodized AZ31alloy, the sample prepared after 15min anodization was immersed in 17 mmol/L NaCl+0.1 mol/L Na2SO4 solution and the evolution of the EIS with time was measured. The results are shown in Fig.6. For comparison, the EIS of the blank AZ31magnesium alloy is also plotted. According to the EIS spectra and the physical structures of the electrode and solution interface, the equivalent circuit of Fig.7 can be put forward to fit the EIS of Fig.6. In Fig.7, Rs, Cdl and Rct represent for solution resistance on electrode surface, the double layer capacitance between the magnesium alloy matrix and the electrolyte and charge transfer resistance, respectively. It can be seen from Table 2 that the charge transfer resistance (Rct) of the anodized AZ31 Mg alloy is 6.387×104 ?/cm2, which is above 30 times of that of the nude AZ31 Mg alloy. Consequently, the anodized films
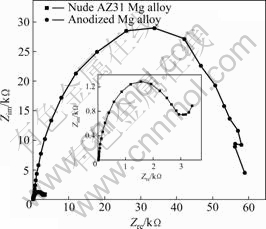
Fig.6 EIS curves of AZ31 Mg alloys covered or uncovered by anodic film in 17 mmol/L NaCl+0.1mol/L Na2SO4 solution for 15 min
on AZ31 magnesium alloy have an excellent protective function and show greater enhancement of the impedance of the anodized films.
The fitted results quantitatively analyzed by ZSimpWin software are listed in Table 2.
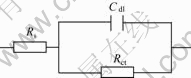
Fig.7 Equivalent circuit of anodized nude and anodized AZ31 Mg alloys (17 mmol/L NaCl+0.1 mol/L Na2SO4)
Table 2 EIS results of nude and anodized AZ31 Mg alloys
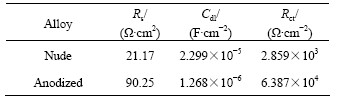
4 Conclusions
1) A new environmentally friendly anodizing process, which is low voltage and low energy, was developed, and the grayish-white films with excellent corrosion resistance on magnesium alloys were obtained.
2) A new kind of organic additive A was used to efficiently form a kind of grayish-white anodic film on AZ31 magnesium alloys, which possesses high corrosion resistance and excellent binding strength to substrate.
3) The anodized samples prepared by the environmentally friendly electrolyte for 15 min at 25 ℃ have the large Rct value and show the nice corrosion resistance property. Compared with blank sample, the charge transfer resistance increases nearly 30 times.
References
[1] GRAY J E, LUAN B. Protective coatings on magnesium and its alloys-A critical reviews?[J]. J Alloys Compd, 2002, 336(1/2): 88-113.
[2] UMEHARA H, TAKAYA M, TERAUCHI S. Chrome-free surface treatments for magnesium alloy[J]. Surface and Coatings Technology, 2003, 69/170: 666-669.
[3] SONG G L. Recent progress in corrosion and protection of magnesium alloys—An over of cast’s research work[J]. Advanced Engineering Materials, 2005, 7(7): 563-586.
[4] SONG G L. Corrosion and protection of magnesium alloys-An overview of research undertaken by cast[J]. Materials Science Forum, 2005, 488/489: 649-652.
[5] SONG G L, ATRENS A, STJOHN D, XU X, NAIRN J. The anodic dissolution of magnesium in chloride and sulphate solution [J]. Corrosion Science, 1997, 39(10/11): 1981-2004.
[6] BARTAK D E, LEMIEUX B E, WOOLSEY E R. Hard anodic coating for magnesium alloys. US 5470664[P]. 1995-10-28.
[7] FUKUDA H, MATSUMOTO Y. Effects of Na2SiO3 on anodization of Mg-Al-Zn alloy in 3 M KOH solution[J]. Corrosion Science, 2004, 46(9): 2135-2142.
[8] HSIAO H Y, TSUNG H C, TSAI W T. Anodization of AZ91D magnesium alloy in silicate-containing electrolytes[J]. Surface and Coatings Technology, 2005, 199(2/3): 127-134.
[9] DABALA M, BRUNELLI K, NAPOLITANI E, MAGRINI M. Cerium-based chemical conversion coating on AZ63 magnesium alloy[J]. Surface and Coatings Technology, 2003, 172(2/3): 227-232.
[10] MA Y, NIE X, NORTHWOOD D O, HU H. Systemic study of the electrolytic plasma oxidation process on a Mg alloy for corrosion protection [J]. Thin Solid Films, 2006, 494(1/2): 296-301.
[11] ZHANG Y J, YAN C W, WANG F H, LOU H Y, CAO C N. Study on the environmentally friendly anodizinig of AZ91D magnesium alloy [J]. Surface and Coating Technology, 2002,161(1): 36-43.
[12] BLAWERT C, HEITMANN V, DIETZEL W, NYKYFORCHYN H M, KLAPKIV M D. Influence of process parameters on the corrosion properties of electrolytic conversion plasma coated magnesium alloys[J]. Surface and Coatings Technology, 2005, 200(1/4): 68-72.
[13] DECKER R F. The renaissance in magnesium[J]. Advanced Materials and Processes, 1998, 154(9): 31-33.
[14] ZHANG R F, SHAN D Y, HAN E H, GUO S B. Development of microarc oxidation process to improve corrosion resistance on AZ91HP magnesium alloy[J]. Trans Nonferrous Met Soc China, 2006, 16(s2): s685-s686.
[15] CHENG Y L, WU H L, CHEN Z H, WANG H M, ZHANG Z, WU Y W. Corrosion properties of AZ31magnesium alloy and protective effects of chemical conversion layers and anodized coatings[J]. Trans Nonferrous Met Soc China, 2007, 17(3): 502-508.
[16] Wu H L, CHENG Y L, Li L L, CHEN Z H, WANG H M, ZHANG Z. The anodization of ZK60 magnesium alloy in alkaline solution containing silicate and the corrosion properties of the anodized films[J]. Applied Surface Science, 2007, 253(24): 9387-9394.
[17] FUKUDA H, MATSUMOTO Y. Formation of Ti-Si composite oxide films on Mg-Al-Zn alloy by electrophoretic deposition and anodization[J]. Electrochimica Acta, 2005, 50(27): 5329-5333.
(Edited by LI Yan-hong)
Corresponding author: WU Xue-dong; Tel: +86-574-86685165; E-mail: daidan1666@yahoo.com.cn