
Preparation of semisolid A356 alloy slurry with larger capacity cast by serpentine channel
YANG Xiao-rong1, MAO Wei-min2, SUN Bin-yu1
1. School of Materials Science and Engineering, Taiyuan University of Science and Technology,
Taiyuan 030024, China;
2. School of Materials Science and Engineering, University of Science and Technology Beijing,
Beijing 100083, China
Received 22 March 2010; accepted 20 July 2010
Abstract: The integral microstructure of semisolid A356 alloy slurry with larger capacity cast by serpentine channel was studied and the influence of cooling ability of serpentine channel on the microstructure was investigated. The results indicate that ideal slurry with larger capacity can be prepared through serpentine channel with good cooling ability. When the serpentine channel was continuously cooled, both the longitudinal and the radial microstructure of the slurry was composed of granular primary phase and the integral microstructure uniformity of the slurry was good. However, uncooled serpentine channel can only produce larger slurry with fine grains in positions adjacent to its centre and with a large number of dendrites in positions close to its edge, thus, the radial microstructure of larger slurry is nonuniform. The pouring temperature is set up to 680 °C and the solid shell inside the channel can be avoided at this pouring temperature.
Key words: semisolid; serpentine channel; A356 aluminum alloy; larger capacity
1 Introduction
A key step of semisolid metal forming technology is an economical production of semisolid slurry with fine grain microstructure. To develop this microstructure, mechanical stirring method and electromagnetic stirring method are widely employed, however, the former readily pollutes the metal and the latter has low electromagnetic stirring efficiency[1]. In recent years, a new process has been reported to obtain desired semisolid slurry. The process, dubbed controlled nucleation method[2-3], does not require stirring. It is simple, practical and less expensive, and hence attracted more attention. According to the controlled nucleation idea, several techniques were demonstrated, including the cooling slope method[4-8], rotating duct[9], damper cooling tube method[10], wavelike sloping plate[11] and the vertical pipe[12-13]. Nonetheless, either the mechanical stirring method or the electromagnetic stirring method or the controlled nucleation method, most of them use low pouring temperatures to gain semisolid alloy slurry, which is not convenient for practical operation. On the basis of the controlled nucleation method, the serpentine pipe process was presented[14-15], in which higher pouring temperatures can be adopted. At present, a large majority of these processes mentioned above are typically used for slurry with small diameters[16-19]. The production of larger diameter slurry was carried out in some industrial countries in order to provide semisolid metal slurry with enough size for manufacturing bigger components. On this aspect, some studies on serpentine channel and a stainless steel mould with size of d 130 mm×160 mm were conducted, and the pouring temperature is as high as 680 °C. In this work, the integral microstructure of semisolid A356 alloy slurry with larger capacity cast by serpentine channel process was studied and the influence of the cooling ability of the serpentine channel on the semisolid microstructure was investigated.
2 Experimental
The experimental work was conducted using a commercial A356 aluminium alloy with a theoretical liquidus temperature of 615 °C and binary eutectic temperature of 577 °C. The composition of the alloy is listed in Table 1. The alloy charged into a crucible in an electrical resistance furnace was melted. The resulting melt was then cooled to the chosen pouring temperature of 680 °C, and cast into a stainless steel mould with size of d 130 mm×160 mm via serpentine graphite channel which was continuously cooled with cold water. The semisolid slurry was then rapidly water-quenched so that the microstructure of the slurry was kept. To check the effect of the cooling ability of the serpentine channel on the semisolid microstructure, samples were also prepared by uncooled serpentine channel according to the same stages described above.
Table 1 Chemical composition of A356 alloy (mass fraction, %)

The schematic diagram of the slurry preparation process is shown in Fig.1. The resulting solidified slurry was sectioned longitudinally from the top, middle and bottom, respectively, as shown in Fig.2. The thickness of the wafer was about 10 mm. The sector samples were fetched from the three wafers (through the circle center of the wafer). A transverse section of each sample was polished for microstructural observation. Each metallographic sample was etched with an aqueous solution of 0.5% HF and then was cleaned by cool water. The microstructure of the samples was examined using optical microscopy. Four zones of interest were considered during the metallographic examination: 1) centre, 2) radial middle part, 3) transitional region and 4) edge.
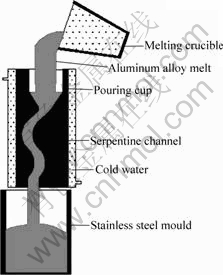
Fig.1 Schematic diagram of slurry preparation process
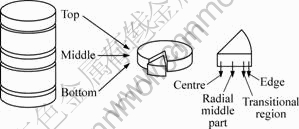
Fig.2 Schematics of metallographic samples intercepted from solidified slurry
3 Results
3.1 Integral microstructure of larger slurry obtained via cooled serpentine channel
The larger the slurry size, the harder the slurry obtained with uniform integral microstructure. Hence, several representative positions in the larger slurry were considered during the metallographic examination of integral microstructure (see Fig.2).
The longitudinal microstructure of solidified slurry is shown in Fig.3, which shows the microstructures in the central area at the top, middle and bottom of the semisolid A356 alloy slurry with larger capacity prepared by cooled serpentine channel. The light phase is primary α(Al) and the dark area is the quenched liquid. It can be seen that the morphology and size of the primary α(Al) grain appear almost similar in the central area at the top and middle of the larger slurry. Both of them generate granular primary α(Al) phase distributed uniformly in the eutectic matrix, and rosettelike primary α(Al) grains are hardly observed, as illustrated in Figs.3(a) and (b), respectively. As shown in Fig.3(c), in the central area at the bottom of the larger slurry, primary α(Al) with a granular grain structure is dominant, and rosettelike primary α(Al) occurs, but the amount of rosettes is relatively small and their morphology is quite fine. According to the analysis stated above, the morphology of the primary α(Al) in the centre of the larger slurry does not vary obviously across the longitudinal section, mainly featuring a large number of granular particles. The results indicate that fine grain microstructure can be obtained in the centre of the slurry with larger capacity prepared by cooled serpentine channel and its longitudinal microstructure is uniform.
The radial microstructure of solidified slurry is illustrated in Fig.4, which compares the microstructures in radial different positions at the top of the semisolid A356 alloy slurry with larger capacity prepared by cooled serpentine channel. Comparing Fig.4 and Fig.3(a), there is no evident structural change in the centre, radial middle part and transitional region at the top of the slurry. The three microstructures are quite granular, as shown in
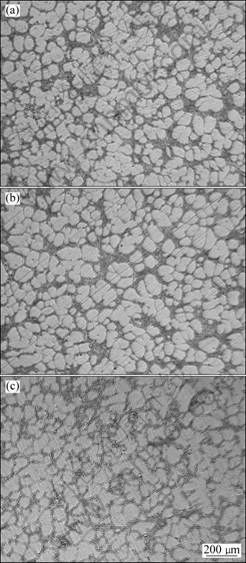
Fig.3 Microstructures of centre at top(a), middle (b) and bottom (c) of A356 alloy semisolid solidified slurry obtained with cooled serpentine channel at pouring temperature of 680 °C
Figs.3(a), 4(a) and 4(b). The transitional region of semisolid alloy slurry is usually located in the area of 3-5 mm from the edge of slurry, where the transition of microstructures takes place easily and the primary phase with multiple shapes often exists. The microstructure in Fig.4(b) reveals that transitional region disappears in semisolid A356 alloy slurry with larger capacity cast by serpentine channel process. Primary α(Al) phase in the top edge of the slurry still exhibits an ideal granular structure with a very few quantity of fine rosettes, and no dendrites are commonly observed in the edge of slurry, as shown in Fig.4(c). Since little structural change is observed in radial different positions at the top of the slurry, it can be concluded that the microstructure distribution in the radial direction at the top of the slurry with larger capacity prepared by cooled serpentine

Fig.4 SEM images of top surface across radial direction of A356 alloy semisolid solidified slurry obtained with cooled serpentine channel at pouring temperature of 680 °C: (a) Radial middle part; (b) Transitional region; (c) Edge
channel is uniform.
The homogeneous distribution of microstructure described above in radial direction at the top and in axial area at the centre of the slurry is also seen in other radial and axial directions of the solidified slurry. The foregoing microstructures indicate that ideal semisolid A356 alloy slurry with larger capacity can be prepared through continuously cooled serpentine channel, both the longitudinal and radial microstructure of the slurry is composed of granular primary phase and the integral microstructure in the semisolid slurry is good, which has an apparent significant impact on subsequent steps. In the present work, the pouring temperature is up to 680 °C, which is much higher than the liquidus temperature of the alloy employed, and the solid shell inside the channel can be avoided at this pouring temperature, thereby it is convenient for industrial operation. The microstructures of solidified slurry poured at 660 °C and 700 °C were also investigated, as illustrated in Figs.5(a) and (b), respectively. The slurry poured at 660 °C has a desired microstructure but the solid shell inside the channel appears easily. When the pouring temperature is 700 °C, solid shell does not appear inside the channel; however, the microstructure of the slurry contains some dendrites.
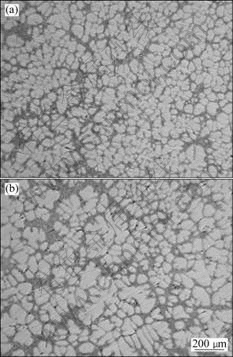
Fig.5 SEM images of centre mid-axial position of A356 alloy semisolid solidified slurry obtained with cooled serpentine channel at pouring temperatures of 660 °C (a) and 700 °C (b)
3.2 Radial microstructure of larger slurry prepared by uncooled serpentine channel
The cooling ability of the serpentine channel has a significant effect on the microstructure of larger slurry. Figure 6 shows the radial microstructures of the solidified larger slurry obtained with the uncooled serpentine channel at a pouring temperature of 680 °C. A microstructural inhomogeneity along the radial direction of the slurry is shown apparently in Figs.6(a)-(d). The microstructure of the centre of the slurry shown in Fig.6(a) is ideal, consisting of a mixture of a large number of spheroidal grains and a very small quantity of rosettes. The morphology from radial middle part of the slurry is also appropriate, as shown in Fig.6(b), in which there are still a lot of spherical primary α(Al) phases and some fine rosettes. In transitional region, the morphological evolution of a globular microstructure toward a dendritic morphology is evident, as illustrated in Fig.6(c), in which the microstructure in left is quite spheroidal, however, the microstructure in right becomes quite dendritic and some fragmentary dendrites and rodlike grains can be also observed. In Fig.6(d), the microstructure from the edge of the slurry is almost composed of dendrites with various sizes. Figures 6, 4 and 3(a) reveal that the uncooled serpentine channel can only produce the larger slurry with granular primary phase in positions adjacent to its centre and middle part, and with a large number of dendrites in positions close to its edge, thus the radial microstructure of the larger slurry is nonuniform. However, the continuously cooled serpentine channel can prepare larger slurry with fine grains in its integral microstructure. Thus, it can be concluded that good cooling ability of the serpentine channel should be applied during pouring to gain larger slurry with ideal microstructure. This requirement of maintaining a low channel temperature is necessary in continuous casting processes.
4 Discussion
A number of theories about grain microstructure formation in the solidification of semisolid metal alloys were described in Ref.[20]. The possible mechanism that serpentine channel process prepares larger slurry with good microstructure is owed to the strong nucleation ability of cooled serpentine channel. As molten A356 aluminum alloy flows through the low temperature serpentine channel, the high temperature melt is in contact with the channel wall, which provides rapid heat extraction; thus, the melt has a higher degree of supercooling because of the chilling action from the channel wall and the nucleation of primary α(Al) is decreased. Hence, primary crystals are nucleated on or near the relatively cold channel wall. The serpentine channel has a certain radian and is closed, making the melt constantly change the flow direction, and thereby turbulent flows come into being and collide with each other. Subsequent melt in turbulent condition continually washes those primary crystals on or near the channel wall, leading to primary crystals dissociate from the channel wall and enter the stainless steel mould. Owing to the dissociation of primary crystals from the channel wall, abundant primary α(Al) nuclei exist in the structure of the slurry in the mould. When the serpentine channel is continuously cooled and the pouring temperature is 680 °C, the measured temperature of the melt at the channel exit is 618 °C, which is close to the liquidus temperature of A356 alloy, and further temperature will drop for the melt flowing into the mould, so those nuclei in the mould can be conserved. The interaction of multiple nuclei makes significant contributions to the
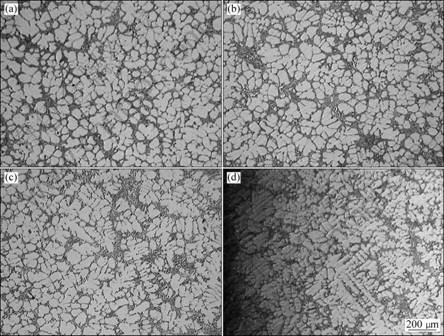
Fig.6 SEM images across radial direction in A356 alloy semisolid solidified slurry obtained with uncooled serpentine channel at pouring temperature of 680 °C: (a) Centre; (b) Radial middle part; (c) Transitional region; (d) Edge
grain structure formation.
Besides the nucleation from the channel wall, dendrite arm fractured by stirring resulting from pouring also has an influence on the grain structure formation. The melt reaching the channel exit maintains a high velocity in that the serpentine channel has a certain height and vigorously stirs the melt in the mould. The stirring can promote uniform distribution of those nuclei in the mould and also can aid the homogenization of the melt temperature field, favoring the ripening of primary α(Al) nuclei, i.e. promoting the detachment of dendrite arms. Fragmentary dendrite arms and rodlike grains shown in Fig.5(c) are the outcome of dendrite arm fracture. Furthermore, dendrite arm fragments may melt off and provide multiple nuclei.
A large number of nuclei and detached dendrite arms are present in the melt as a result of these two mechanisms. Continuous impact and abrasion between solid particles or between solid particles and liquid phase promote gradual spheroidisation of solid grains and contribute to the formation of a globular integral microstructure.
The cooling ability of the serpentine channel has a significant effect on the microstructure of larger slurry. The bulk of melt is needed for manufacturing larger slurry and much heat of melt transfers to the channel during pouring period, so the channel obtains considerable heat for manufacturing larger slurry. The uncooled channel cannot rapidly dissipate the heat, and the degree of supercooling near the channel wall would be reduced and less significant nucleation would also occur on the channel wall, leading to a less number of crystals when the melt reaches the mould. Furthermore, the melt temperature fall inside the channel decreases, thereby the melt entering into the mould has a higher temperature and some nuclei will be remelted by superheated melt in the mould, making only a small amount of nuclei survive. With decreasing nucleation density, spaces of nuclei expand and therefore the interactions of suppression between particles weaken, resulting in the coarsening of the particles and thus a gradual increase in the number of rosettes and dendrites. This may account for the primary phase with multiple shapes existing in the larger slurry prepared by uncooled serpentine channel and its less uniform microstructure.
5 Conclusions
1) Ideal semisolid A356 alloy slurry with larger capacity can be prepared through the serpentine channel with good cooling ability.
2) When the serpentine channel is continuously cooled with cold water, both the longitudinal and the radial microstructure in the semisolid A356 alloy slurry are composed of granular primary phase with larger capacity and the integral microstructure in the semisolid slurry is good, which has an apparent significance on subsequent procedures. However, the uncooled serpentine channel only can produce the larger slurry with fine grains in positions adjacent to its centre and with a large number of dendrites in positions close to its edge, thus the radial microstructure of the larger slurry is nonuniform.
3) The pouring temperature is up to 680 °C and the solid shell inside the channel can be avoided at this pouring temperature, thereby it is convenient for industrial operation.
References
[1] MAO Wei-min. Semisolid metal forming technology [M]. Beijing: China Machine Press, 2004: 6. (in Chinese)
[2] WANG H, St JOHN D H, DAVIDSON C J, NING Z. Controlled nucleation method for formation of feedstock [C]//ALEXANDROU A, APELIAN D. Proc of the 8th Int Conf on the Processing of Semi-Solid Alloys and Composite. Limassol, Cyprus, 2004: 269-276.
[3] XIA K, TAUSIG G. Liquidus casting of a wrought Al alloy 2618 for thixoforming [J]. Mater Sci Eng A, 1998, 246(1-2): 1-10.
[4] KAUFMANN H, WABUSSEG H, UGGOWITZER P J. Metallurgical and processing aspects of the NRC semi-solid [J]. Casting Technology Aluminum, 2000, 76(1-2): 70-79.
[5] LUKASSON M, APELIAN D, DASGUPTA R. Alloy characterization for the new UBE rheocasting process [J]. AFS Transactions, 2002, 110: 271-284.
[6] POTZINGER R, KAUFMANN H, UGGOWITZER P J. Magnesium new rheocasting—A novel approach to high quality magnesium- castings [C]//CHIARMETTA G L, ROSSO M. Proc of the 6th Int Conf on the Processing of Semi-Solid Alloys and Composite. Turin, Italy, 2000: 85-90.
[7] TOSHIO H. Semi-solid strip casting using a twin roll casting equipped with a cooling slope [C]//TSUTSUI Y, KIUCHI M, ICHIKAWA K. Proc of the 7th Int Conf on the Processing of Semi-Solid Alloys and Composite. Tsukuba, Japan, 2002: 107-112.
[8] TOSHIO H, KAPRANOS H P. Simple rheocasting processes [J]. Journal of Materials Processing Technology, 2002, 130-131: 594-598.
[9] GUO Hong-min, YANG Xiang-jie, HU Bin. Effects of parameters of slurry-making process with rotating duct on semi-solid microstructure of A356 alloy [J]. The Chinese Journal of Nonferrous Metals, 2004, 14(12): 2049-2054. (in Chinese)
[10] XIE S S, YANG H Q, WANG H, LI X G, LI L. Damper cooling tube method to manufacture semisolid slurry of magnesium alloy [C]//ALEXANDROU A, APELIAN D. Proc of the 8th Int Conf on the Processing of Semi-Solid Alloys and Composite. Limassol, Cyprus, 2004.
[11] GUAN Ren-guo, SHI Lu, XING Zhen-huan, WANG Chao, MA Ting-wei, SHANG Jian-hong. Preparing semisolid AlSi6Mg2 alloy by novel sloping plate process and thixoforming [J]. Foundry, 2007, 56(7): 694-697. (in Chinese)
[12] YANG Xiao-rong, MAO Wei-min, PEI Sheng. Influence of process parameters on microstructure of semisolid A356 alloy slug cast through vertical pipe [J]. Transactions of Nonferrous Metals Society of China, 2008, 18(1): 99-103.
[13] YANG Xiao-rong, MAO Wei-min, PEI Sheng. Preparation of semisolid A356 alloy feedstock cast through vertical pipe [J]. Materials Science and Technology, 2007, 23(9): 1049-1053.
[14] YANG Xiao-rong, MAO Wei-min, GAO Chong. Preparation of semi-solid feedstock by serpentine pipe pouring [J]. The Chinese Journal of Nonferrous Metals, 2009, 19(5): 869-873. (in Chinese)
[15] YANG Xiao-rong, MAO Wei-min, GAO Chong. Semisolid A356 alloy feedstock poured through a serpentine channel [J]. International Journal of Minerals, Metallurgy and Materials, 2009, 16(5): 603-607.
[16] LI Yuan-dong, WEN Jing, CHEN Ti-jun, YANG Jian, MA Ying, JIANG Xiang-dong. Effects of SiC addition on microstructure of AZ91D alloy initial billet with various size during semisolid isothermal treatment. [J]. The Chinese Journal of Nonferrous Metals, 2010, 20(3): 407-414. (in Chinese)
[17] MANEL D S, ALAIN L, CHEN X G. Characterization of semi-solid slurry using a novel "Rheo-Characterizer" apparatus [J]. Journal of Materials Processing Technology, 2009, 209(18-19): 5892-5901.
[18] LEE S Y, OH S I, SOHN K Y. Defects, microstructures, and mechanical properties of thixoformed aluminum suspension parts for electric vehicle [C]//TSUTSUI Y, KIUCHI M, ICHIKAWA K. Proc of the 7th Int Conf on Semi-solid Processing of Alloys and Composites. Tsukuba, Japan, 2002: 725-730.
[19] CHEN C M, YANG C C, CHAO C G. A new method thixo-casting of gas-atomized hypereutectic Al-Si alloy powder [C]//TSUTSUI Y, KIUCHI M, ICHIKAWA K. Proc of the 7th Int Conf on Semi-solid Processing of Alloys and Composites. Tsukuba, Japan, 2002: 759-764.
[20] TONG Lei-lei, LIN Xin, ZHAO Li-ning, HUANG Wei-dong. Morphological stability of globular crystal during semi-solid processing [J]. Acta Metallurgica Sinica, 2009, 45(6): 737-743. (in Chinese)
采用蛇形通道制备较大容量A356铝合金半固态浆料
杨小容1,毛卫民2,孙斌煜1
1. 太原科技大学 材料科学与工程学院,太原 030024;2. 北京科技大学 材料科学与工程学院,北京 100083
摘 要:采用蛇形通道制备较大容量的A356铝合金半固态浆料,对制备的半固态浆料的整体组织和管道冷却能力对组织的影响进行研究。结果表明,采用冷却能力良好的蛇形通道可制备出理想的较大容量半固态A356铝合金浆料。蛇形通道连续通冷却水时,较大容量半固态A356铝合金浆料轴向和径向的组织均由颗粒状的初生相组成,浆料的整体均匀性良好;而未通冷却水的蛇形通道只能在较大容量浆料的心、中部获得颗粒状初生相,靠近浆料的边部区域则主要为树枝状初生相,整个浆料径向的组织不均匀。浇注温度达到680 °C,可以解决合金熔体在浇注过程中容易堵塞的问题。
关键词:半固态;蛇形通道;A356铝合金;较大容量
(Edited by FANG Jing-hua)
Foundation item: Project (50774007) supported by the National Natural Science Foundation of China; Project (20082022) supported by the Scientific Research Foundation for Doctors from Taiyuan University of Science and Technology, China
Corresponding author: YANG Xiao-rong; Tel: +86-351-6963332; E-mail: yxr78@163.com
DOI: 10.1016/S1003-6326(11)60736-X