Twinning during hot compression of ZK30+0.3Yb magnesium alloy
YE Cheng-wu(叶呈武), LIU Zhi-yi(刘志义),ZHANG Kun(张 坤), ZHENG Qing-chun(郑青春)
(School of Materials Science and Engineering, Central South University, Changsha 410083, China)
Abstract: The twinning process of ZK30+0.3Yb magnesium alloy was studied. The results show that twinning occurs at the initial stage of deformation, and decreases during further deformation. The original grain is fragmented after small straining. It is investigated that the twinning boundary activates the occurrence of the non-basal slip system due to the stress concentration at the vicinity of twin boundary introduced by the dislocation pile-ups at the vicinity of twinning boundary. The rearrangement of dislocation after dislocation climb introduces new grain boundary. Simultaneously, twinning occurs to form “polygonization” due to the stress concentration relaxation, and the “polygonization” will transform into low angle boundary to refine the original grain under the shear stress with further straining.
Key words: magnesium alloys; twinning; dislocation rearrangement; grain refinement CLC number: TG111.7
Document code: A
1 INTRODUCTION
In the most previous studies[1-4], twinning occurred at the initial stage of deformation, but it was not observed in the other studies[5, 6]. This indicated that twinning was sensitive to the deformation condition. Twinning process was restrained by such factors as the refinement of initial grain, the increase of the volume fraction of precipitates and deformation temperature, and the decrease of strain rate[1-4, 7]. Furthermore, the stress condition or the original texture affected the twinning process complexly[1, 5, 6].
The occurrence and the role of twinning were completely studied through theoretical calculation and computer simulation[7-9], or investigated as part of the experimental work for the necessity of theory integrality in the previous literatures[1-6]. Most of these researches focused on the pure magnesium, only a few as-deformed AZ or ZK magnesium alloys were studied. We all know that the original texture existing at the as-deformed magnesium would affect the twinning.
There is no literature specially reporting the characteristic and role of twinning in the as-cast ZK30+0.3Yb magnesium alloy. The grain refinement of twinning occurred at the early stage of ZK30+0.3Yb magnesium alloy would be studied in this paper through compression experiment.
2 EXPERIMENTAL
The magnesium alloy Mg-3.0Zn-0.7Zr-0.3Yb used in the present study was cast in water-cooled mould. After casting, the ingot was homogenized at 673K for 24h. Cylindrical specimens of d8mm×10mm were machined from the ingot parallelly to the casting direction. Then 0.1mm-deep grooves were machined on the end faces of cylinders in order to promote the retention of a graphite lubricant.
Compression tests were carried out at constant strain rate of 0.1s-1 on Gleeble 1500 thermal mechanical simulation machine at 573K, 623K, 663K and 723K. The strain was set to be 5%, 10%, 20%, 30%, 50% and 70% (the corresponding true strain is 0.05, 0.11, 0.22, 0.36, 0.69 and 1.20), respectively. To investigate the effect of strain rate, at 663K, the compression experiments were also taken at strain rate of 0.001s-1 and 1s-1. All the specimens were quenched to room temperature in water immediately after compression.
Each deformed specimen was cut along the plane parallel to compression axis, mechanically polished, chemically etched in a solution of 5g picric acid+5mL acetic acid+100mL ethanol+10mL water, then observed by Poly-met optical microscopy(OM).
3 RESULTS
Few twins are observed in the undeformed alloy(Fig.1(a)), but only after a small amount of
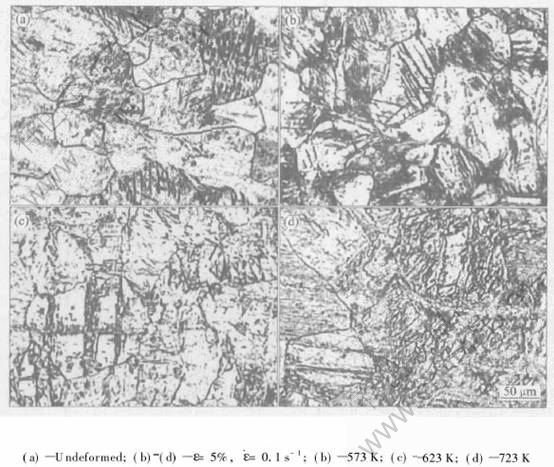
Fig.1 Microstructures of ZK30+0.3Yb alloy at various deformation temperatures
stain are exerted, does large amplitude serrate appear on the flow stress curves. Such flow stress behavior shows the characteristic of twinning, and indicates that twinning has occurred at the initial stage of deformation(Fig.2). Simultaneously, abundance of twins are observed in the micro-structure (Fig.1(b)-(d)). At low temperature(573K), the grain is coarse and the twins are parallel to each other in each grain. At higher temperature(623K), second twins are observed in some part of the grains; at the highest temperature(723K), more intensive twinning was observed.
Fig.3 shows the microstructures of alloy after compression to 5% at various strain rates at 663K. At low strain rate, the volume fraction of twinsis large and second twinning occurs within almost all the grains. At high strain rate, twins “disappear” in some grains.
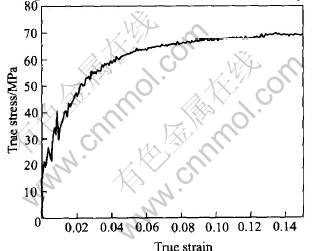
Fig.2 True stress—true strain curve of ZK30+0.3Yb magnesium alloy compressed at 663K
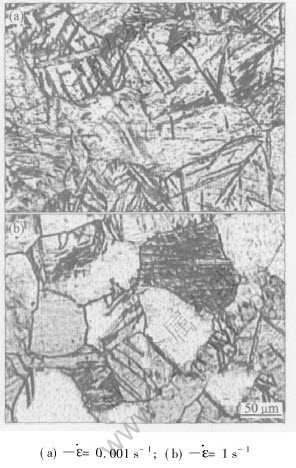
Fig.3 Microstructures of ZK30+0.3Yb alloy at various strain rates(T=663K, ε=5%)
The microstructure evolution during compression at 663K is depicted in Fig.4(strain rate of 0.1s-1). At the initial stage of straining, abundance of twins are observed in the grain. During subsequent straining(Fig.4(b)), the amount of the observed twins decreases, and fine new dynamic recrystallization(DRX) grains and some small grains pointed out by black arrows evolve along the grain boundaries. With further straining(Fig.4(c)), twins “disappear”, the rest grains are elongated, the DRX grain-layers are thickened, and DRX volume fraction increases; but until at strain of 70%, the DRX is not completed (Fig.4(d)).
4 DISCUSSION
4.1 Formation of twin
Generally, twinning occurs after local dislocation slip, that is to say, the embryo of twin exists in the core structure of dislocation before deformation, and it grows into nucleus while the micro slip occurs under the applied stress, then the nuclei will grow into twins during subsequent deformation[8, 9]. With further straining, the size of twins are enlarged, and their orientation are unified. The sideway growth of twinned plates occurs, until the twins have entirely consumed the original grains[1, 2], thus resulting in an equiaxed grain structure identical in appearance to that in undeformed grains. The twin boundary may transform into new grain boundary, causing the twin losing the typical characteristic of twins, such as the twin in grain “G1” in Fig.5(b).
4.2 Twinning induced grain refinement
The grains pointed out in Fig.4(b) can be observed more clearly in Fig.5. The dislocations will pile up at the vicinity of twinning boundary. The stress concentration caused by dislocation pile-up activates non-basal slip system[10-12], then the non-basal dislocations rearrange themselves to form the morphology identical in appearance to that of the low energy dislocation in FCC structure alloy[13](the morphology is very similar to the grain “G1” in Fig.5(e)). At the high temperature of the experiment, the dislocation climbing of non-basal dislocation is quite easy, which means that the original grain is subdivided into several irregular areas with small misorientation[5, 14]. The new grain boundary is pointed out in Fig.5 by black arrows.
The activation of non-basal slip system is one of the ways of stress concentration relaxation of twinning. If the edge of first twin terminates at second twins rim, like the morphology in Fig.5(a) and (c), the edge of twin “T1” terminates at the rim of twin “T2” and the stress concentration of “T1” will be relaxed by the deformation of twin “T2” [15]. At the same time, if the twins arrange
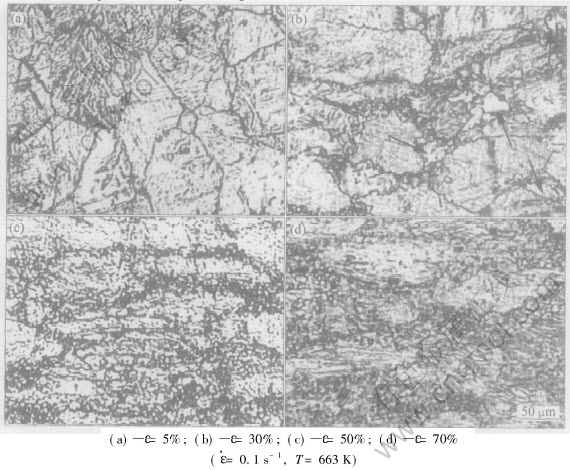
Fig.4 Microstructure evolution of ZK30+0.3Yb alloy during compression
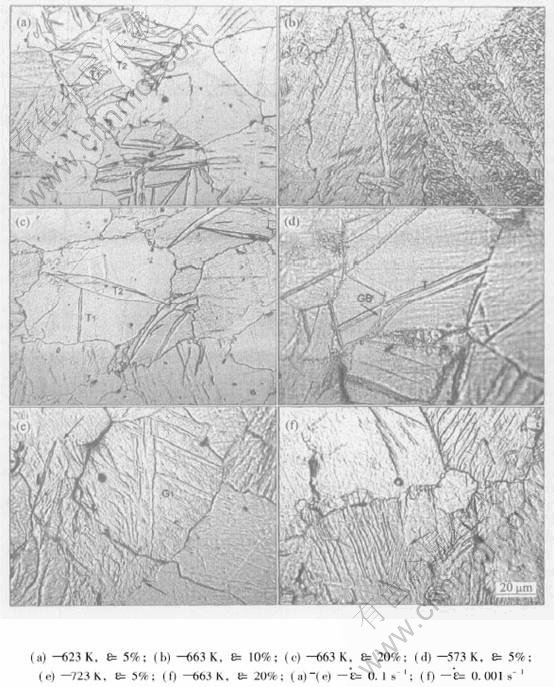
Fig.5 Microstructures of grains in ZK30+0.3Yb alloy
themselves in parallel rows like the morphologies in Fig.5(f), the stress concentration will be relaxed too, which is schematically illustrated in Fig.6. If the parallel twin edges A1, A2, …, rearrange in a perpendicular row to twin planes to start twining, and the stress concentration will be relaxed too, thus resulting in a steady configuration like “polygonization”. Then the polygonization will import an misorientation between the twinned and untwined regions under the effect of shear stress, thus low angle boundary(LAB) initiates within a twinned grain[15].
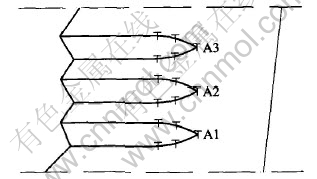
Fig.6 Schematic diagram of stress concentration near twin edge relaxed by repeated twin[14]
In Fig.5(d), the twin “T” changes its twin orientation by a little angle after it crosses through the grain boundary “GB”, which indicates that the grain boundary “GB” is LAB. It is the direct evidence of LAB induced in the grain after small strain.
5 CONCLUSIONS
The twinning occurs at the initial stage of deformation of ZK30+0.3Yb magnesium alloy. The twinning boundary activates the occurrence of the non-basal slip system due to the stress concentration at the vicinity of twin boundary introduced by the dislocation pile-up. Then the rearrangement of dislocation after non-basal dislocation climb introduces new grain boundary. Simultaneously, repeated twinning might occur to form “polygonization” due to the stress concentration relaxation, and the “polygonization” will transform into low angle boundary to refine the original grain under the shear stress with further straining.
REFERENCES
[1]Ion S E, Humphreys F J. Dynamic recrystallization and the development of microstructure during the high temperature deformation of magnesium[J]. Acta Mater, 1982, 30: 1909-1919.
[2]Klimanek P, Ptzsch A. Microstructure evolution under compression plastic deformation of magnesium at different temperature and strain rates[J]. Mater Sci Eng A, 2002, 324: 145-150.
[3]Myshlyaev M M, McQueen H J, Mwembela A, et al. Twining, dynamic recovery and recrystallization in hot worked Mg-Al-Zn alloy[J]. Mater Sci Eng A, 2002, 337: 121-133.
[4]Koike J, Kobayashi T, Mukai T, et al. The activity of non-basal slip systems and dynamic recovery at room temperature in fine-gained AZ31B magnesium[J]. Acta Mater, 2003, 51: 2055-2065.
[5]Yang X Y, Miura H, Sakai T. Dynamic evolution of new grains in magnesium alloy AZ31 during hot deformation[J]. Mater Trans, 2003, 44: 197-203.
[6]del Valle J A , Pérez-Prado M T, Ruano O A. Texture evolution during large-strain hot rolling of the Mg AZ61 alloy[J]. Mater Sci Eng A, 2003, 335: 68-78.
[7]Meyers M A, Vhringer O, Lubarda V A. The onset of twining in metals: a constitutive description[J]. Acta Mater, 2001, 49: 4025-4039.
[8]Yoo, M H, Lee J K. Deformation twinning in hcp metals and alloys[J]. Phil Mag, 1991, 63A(5): 987-1000.
[9]Serra A. A new model for {1012} twin growth in hcp metals[J]. Phil Mag, 1996, 73A(2): 333-343.
[10]Serra A, Bacon D J. Computer simulation of screw dislocation interactions with twin boundaries in hcp metals[J]. Acta Mater, 1995, 43: 4465-4481.
[11]Minonishi Y, Ishioka S. The core structure of a 1/3〈1123〉{1122} edge dislocation under applied shear stresses in an hcp model crystal[J]. Phil Mag A, 1982, 45: 835-850.
[12]Galiyev A, Kaibyshev R, Gottstein G. Correlation of plastic deformation and dynamic recrystallization in magnesium alloy ZK60[J]. Acta Mater, 2001, 41: 1199-1207.
[13]Bay B, Hansen N, Hughes D A, et al. Evolution of FCC deformation structure in polyslip[J]. Acta Metal Mater, 1992, 40(2): 205-219.
[14]Kaibyshev G A. Microstructure evolution in ZK60 magnesium alloy during severe plastic deformation[J]. Mater Trans, 2001, 42(7): 1190-1199.
[15]Friedel J. Dislocations[M]. Beijing: Science Press, 1984:128. (in Chinese)
(Edited by YANG Bing)
Received date: 2004-09-12; Accepted date:2005-01-25
Correspondence: YE Cheng-wu; Tel:+86-731-8836011; E-mail: chengwu.yea@163.com