J. Cent. South Univ. Technol. (2008) 15: 264-270
DOI: 10.1007/s11771-008-0049-0

VCR and ASR technology for profile and flatness control in hot strip mills
CAO Jian-guo(曹建国)1, WEI Gang-cheng(魏钢城)1, 2, ZHANG Jie(张 杰)1,
CHEN Xian-lin(陈先霖)1, ZHOU Yi-zhong(周一中)2
(1. School of Mechanical Engineering, University of Science and Technology Beijing, Beijing 100083, China;
2. Wuhan Iron and Steel (Group) Corporation, Wuhan 430083, China)
Abstract: The roll contour pattern and variety of work and backup rolls in service and its effect on profile and flatness control performance in 1 700 mm hot strip mill at Wuhan Iron and Steel (Group) Corporation were tested and analyzed by the developed finite element models of different typical roll contours configurations. A rather smooth local work roll contour near strip edges and an increase in rolled length can be obtained by application of long stroke work roll shifting system with conventional work roll contours that is incapable of the crown control. In comparison with the conventional backup and work roll contours configuration, the crown control range by the roll bending force enhances by 12.79% and the roll gap stiffness increases by 25.26% with the developed asymmetry self-compensating work rolls(ASR) and varying contact backup rolls(VCR). A better strip profile and flatness quality, an increase in coil numbers within the rolling campaign and a significant alleviated effect of severe work roll wear contours on performance of edge drop control are achieved by the application of ASR with crown control and wear control ability in downstream stand F5 and VCR in all stands of 1 700 mm hot strip mill.
Key words: hot rolling mill; strip; profile and flatness control; wear; finite element analysis
1 Introduction
Profile and flatness control is an important factor in determining strip quality and mill productivity. New generation high-tech rolling mills, such as HC, FPC, WRS, CVC, PC, SmartCrown, have been applied in the production of wide strip rolling[1-3]. As the key factors to profile and flatness control, it is important to develop profile and flatness technology in 1 700 mm hot strip mill.
The 1 700 mm hot strip mill at the Wuhan Iron and Steel (Group) Corporation(WISCO) was designed and built by Ishikawajima-Harima Heavy Industries Co., Ltd. (IHI) and was commissioned in 1978. From 1992 to 1994, the mill completed a series of upgrades on the finishing mill supplied by Clecim. The mill is one of the largest hot strip mills in China with a capacity of 3.45 Mt/y. It consists of four reheat furnaces, vertical and horizontal scale breakers, four roughing stands, a 7-stand finishing mill, diverter-style laminar cooling system and three down coilers. The finishing mill includes four stands of work roll heavy bending on stands F4 through F7 with a capacity of 2 000 kN/chock, and four stands of work roll shifting system on stands F4 through F7 with a
long stroke of ±150 mm.
2 Affecting factors of roll contour in hot rolling
Roll contours comprise of the original roll ground contour, the roll thermal contour and the roll wear contour. Variation of roll contour is a key factor affecting behavior of strip profile and flatness in hot rolling. Roll contour pattern of the backup and work rolls on different finishing stands is conducted in 1 700 mm hot strip mill.
Since backup rolls remain nearly at ambient temperature, the roll thermal crown can be ignored. In general, the rolling period of a newly ground backup roll set in hot strip mills exceeds two weeks or even three weeks, it is expected that there is a significant non-uniform wear of the backup roll along its entire length[4]. According to the analysis of measured conventional backup roll contour of 145 rolls that were used in WISCO 1 700 mm hot finishing mill, the roll contour pattern on different stands is conducted. According to the backup roll wear data collected at the WISCO 1 700 mm hot strip mill, the amount of backup roll wear per radius at roll center position of the barrel varies from 225 to 715 ?m. These measured data show
the overall backup rolls wear rapidly and local roll wear is generally non-uniform. The amount of differential local roll wear in the 7-stand finishing hot strip mill is very small in the upstream stands F1 and F2, with a maximum value reaching in stands F5, F6 and F7.
The “as-ground” work roll contour is designed by the operators and provides effects on the strip crown magnitude during the initial phase of rolling campaign. The roll thermal contour is a result of thermal expansion during hot rolling that consists of basic and periodic components. Since the periodic component is localized on the roll surface, the roll thermal contour is usually taken into account the basic component only[5-6]. Based on the statistical analysis of the data obtained during rolling at the 1 700 mm hot strip mill, the roll thermal crown increases rapidly during the first 10 coils in a rolling campaign and amounts to the maximum steady value exceeding 300 μm after rolling 30 coils (about 60 min) during the steady mill pace that comprises of the rolling time and the idle or gap time between rolling of coils. If there are some changes during rolling, such as mill pace, variations in strip width and cooling water temperatures, small but rapidly varying changes in the roll thermal contour occur. Work roll wear effect is another major reason for the variation of the roll contour during rolling of a hot strip mill cycle. Systematic measurements are made of 167 work rolls to provide information for the analysis of roll wear and thermal characteristics. These information is the careful recording of the roll contour, the roll surface temperature, the cooling time in air of the roll extracted from the mill, as well as technological parameters of the rolling campaign. A first measurement is made when the roll is freshly ground and again by the mill just before roll change. The measurement on this roll is used to provide the starting point for the roll wear measurements. After the roll is extracted from the mill, a second roll contour and a roll surface temperature distribution are measured at the same time while the roll is hot. A series of measurements are made during the cooling of the roll. These measurements combine the effect of roll wear and roll thermal behavior. When the roll is cooled, a final measurement will be made. The difference between the hot and cold roll measurements will show the thermal effect and the difference between the original first measurement and final cold measurement will provide the roll wear[7-8]. Considering that the work roll is ground while the roll is hot, an easier and more direct method of measurement was performed. There were two measurements made on numerous rolls to determine roll thermal and roll wear characteristics. One measurement consisting of a roll contours measurement and a roll surface temperature pattern measurement is made when the roll is freshly ground, the other measurement is performed immediately when the roll is extracted from the mill. These measurements will provide work roll wear contours conveniently while the roll thermal contours can be calculated from the thermal predictive models.
As can be seen from the collected data, the work roll wear is generally non-uniform along the entire length of the roll barrel. There are different work roll wear contours for different stands. A maximum value of the work roll wear appears in stand F4, whereas the rolls in stands F1 and F2 show a very small increase in roll wear and the rolls in stands F3, F5, F6 and F7 wear rapidly but smaller than those in stand F4. The roll contours of top work rolls appear to wear severer than those of bottom work rolls. There is a marked difference in work roll wear contour after rolling different campaigns as shown in Fig.1 and Fig.2. Generally speaking, work roll wear of
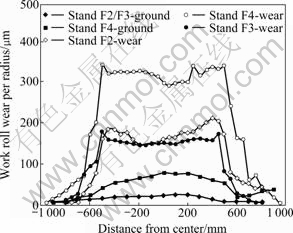
Fig.1 Work roll wear contours for stands F2-F4 in 1 700 mm hot strip mill after rolling a 103-coil rolling campaign (oriented silicon steel sheet)
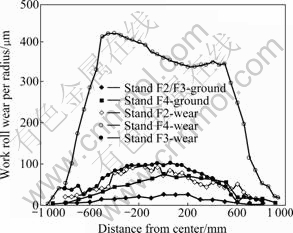
Fig.2 Work roll wear contours for stands F2-F4 in 1 700 mm hot finishing mill after rolling a 114-coil rolling campaign (hot rolling product)
silicon steel sheet rolling campaign increases greater than that of other rolling campaign[9].
As described above, the rolls in upstream stands show a very small increase in roll wear, whereas the rolls in downstream stands wear rapidly[10-13]. It can be seen from Fig.3 that for bottom work roll contours with a maximum value of the work roll wear, there are two forms of work roll wear contours on stand F4, which are recognized as overall and local in downstream stands. The overall work roll wear contours are generally non-uniform. The local work roll wear contours, i.e. “cat ear” near strip edges, are significant without work roll shifting. As the main factors affecting the overall work roll wear are closely related to the strip width, length or tonnage rolled and type of strip rolled, the overall work roll wear contours cannot be generally alleviated. The significant local work roll wear contours must be improved by work roll shifting technology. Three types of shifting technologies can be included from various work roll shifting systems. The work roll shifting with varying contact line, i.e. the contact line between the backup and work rolls varying with the roll shifting stroke, such as Hitachi HCW, can provide a decrease in strip crown. The work roll shifting with short stroke (about ±100 mm), such as CVC-4Hi, can provide a wide crown control range. The work roll shifting with long stroke (about ±150 mm or more), such as K-WRS, can provide a smooth local work roll wear contour. In order to investigate the effect of long stroke work roll shifting system, comparison experiments were made for the bottom work roll contours on stand F4 with the same type wide, heavy gauge rolling campaigns. As shown in Fig.3, rather smooth local work roll contours near strip edges, favorable to decreasing body crown and edge drop, are obtained by application of long stroke work roll
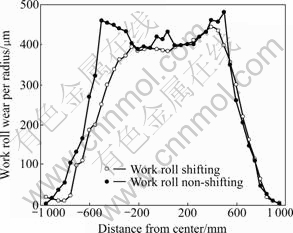
Fig.3 Effect of long stroke work roll shifting system on local work roll wear contours of stand F4 (bottom) in 1 700 mm hot strip mill from wide and heavy gauge rolling campaigns
shifting system with conventional work roll contours. It is worth noting that the length rolled of the 139-coil rolling campaign with shifting is 89.45 km, increased by 14.78% compared with that of the 128-coil rolling campaign without shifting by making the best characteristic of overall work roll wear contours’ non- uniform.
3 Effect of roll contour on performance of roll gap profile
The roll gap profile under load is a decisive factor for determining the exit strip profile, the distribution of reduction across strip width, the unevenness of elongation and eventually the strip flatness. Accordingly, the essence of strip profile and flatness control is the control of roll gap profile.
In order to investigate the effect of the roll contour on the roll gap profile, a finite element model was developed to compute the roll gap profile under load. A three-dimensional finite element model based on ANSYS, can provide the most accurate representation of the physical components of the investigated system. However, much attention must be paid to the calculation time and cost[6, 14-15]. The two-dimensional finite element analysis model with varying thickness of the 4-high hot finishing mill system was developed for the investigation with flexibility and economy[16-17].
A systematic simulation was made under different conditions. The variables involved included the backup roll ground contours, the backup roll wear contours, the work roll contours during different phases of the rolling campaign, strip width and roll pressure per unit strip width and work roll heavy bending force applied.
The conclusion obtained from the effect of backup roll contours can be summarized as follows: 1) The roll gap profile or strip crown, increases linearly with increasing backup roll wear contours. 2) The strip crown decreases linearly with decreasing strip width during the entire rolling campaign.
The results conducted from the effect of work roll contours are drawn as follows: 1) The roll gap profile, as well as strip crown, increases linearly with increasing work roll wear contours. 2) The strip crown decreases linearly with decreasing strip width in the most cases of the rolling campaign, whereas strip crown increases with decreasing strip width in the case of rolling the widest strip. 3) Since the resulting work roll wear contour imprinted on the strip crown is significant at downstream stands F4-F7, the work roll heavy bending provides an appropriate adjustment of the roll gap profile under load from 900 kN/chock to 1270 kN/chock.
4 Development and application of VCR and ASR
In a conventional 4-high mill, the length of contact line between the work and backup rolls is beyond the width of the strip rolled, which has a direct influence on the profile of the roll gap. In order to achieve a decrease in the crown of the roll gap and an increase in the roll gap stiffness for the stability of the roll gap crown during rolling, much effort, such as stepped backup rolls system, 6-high rolling mill with roll shifting system, has to be made by eliminating the undesirable overhung sections. However, the stepped backup rolls system is only suitable for the mill that produces strip with a constant width. The solution of the 6-high rolling mill with roll shifting system is effective but expensive and time consuming in installation. This explains why it is more convenient to use 6-high rolling mill with roll shifting system in the new mill, rather than the modification of an existing mill.
Another effective solution is the application of varying contact rolling(VCR) technology in 4-high rolling mill conveniently developed by the project team of University of Science and Technology Beijing, Wuhan Iron and Steel (Group) Corporation (USTB-WISCO). The idea of VCR began early in 1987. A varying contact backup roll has been developed in the WISCO 1 700 mm tandem cold rolling mill, and then applied to the Shanghai Baoshan Iron and Steel Complex (Baosteel) 2 030 mm continuous cold tandem rolling mill[18]. Since 1997, the VCR has been improved and applied in stands F1-F7 in the WISCO 1 700 mm hot strip mill[19-20]. The main subjects of VCR are the varying contact backup rolls with special roll contours, corresponding work roll contours, technological parameters setup and control strategies.
It can be seen from Fig.3 that significant wear contour patterns of conventional work roll contours in downstream stands of hot rolling lead to transverse thickness profile difference, i.e. body crown and especially edge drop (Fig.4). The rolling period of a newly ground backup roll set in hot strip mills exceeds two weeks, the varying contact backup rolls, being geared to different steel kinds and sizes, only go halfway towards solving the problem of significant transverse thickness profile difference by wear contour patterns of conventional work roll contours. As mentioned above, a rather smooth local work roll contour near strip edges and an increase in length rolled can be obtained by application of long stroke work roll shifting system with conventional work roll contours that is incapable of the
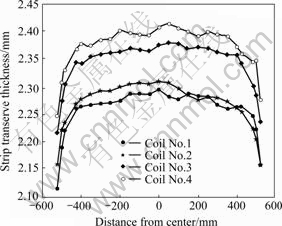
Fig.4 Measured transverse thickness profile of non-oriented electrical steel strip rolled with long stroke work roll shifting system of conventional work rolls in 1 700 mm hot strip mill (2.3 mm×1 050 mm)
crown control. Having the ability to control crown and wear, the asymmetry self-compensating work rolls(ASR) and corresponding work roll shifting and bending have been developed and applied to downstream stand F5 of 1 700 mm hot strip mill at WISGCO for test[17].
As the disturbance variables, such as the change in roll contours, strip width and the roll force fluctuation, exist during the rolling, especially in downstream stands, leading to the variation of the roll gap crown, they are expected that the crown control range by the roll bending force can increase and the roll gap can maintain its crown relatively stable. The roll gap stiffness can be defined as the ratio of the roll force fluctuation to the correspondingly change of the roll gap crown. As shown in Fig.5, the two-dimensional(2D) finite element analysis model with varying thickness of the 4-high hot finishing mill system was developed for effect of typical roll contour configuration on the characteristics of roll gap
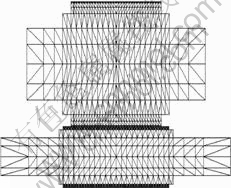
Fig.5 2D finite element model with varying thickness of roll stacks in 1 700 mm hot strip mill
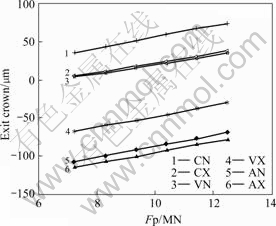
Fig.6 Effect of VCR and ASR on characteristic of roll gap profile applied in 1 700 mm hot strip mill (F5)
profile[16-17]. The effect of VCR and ASR on characteristic of roll gap profile applied in 1 700 mm hot strip mill (F5) is shown in Fig 6. In Fig.6, CN represents conventional backup and work rolls, 0% of roll bending force; CX represents conventional backup and work rolls, 100% of roll bending force; VN represents varying contact backup rolls and conventional work rolls, 0% of roll bending force; VX represents conventional backup rolls and conventional work rolls, 100% of roll bending force; AN represents varying contact backup rolls and asymmetry self-compensating work rolls, 0% of roll bending force; AX represents conventional backup rolls and asymmetry self-compensating work rolls, 100% of roll bending force. It can be seen from Fig.6 that the crown control range by the roll bending force on stand F5 with varying contact backup rolls and conventional work rolls, i.e. the area between the lines VN and VX, is enhanced from 103.5 μm before application of varying contact backup rolls to 112.0 μm, increased by 8.23% compared with that of the lines CN and CX with conventional backup and work rolls. The crown control range by the roll bending force with VCR and ASR, i.e. the area between the lines AN and AX, is 116.7 μm, increasing 12.79% greater than that with conventional backup and work rolls. And at the same time the roll gap stiffness shows an increase from 0.1350 MN/μm with conventional backup and work rolls to 0.1578 MN/μm
with VCR and conventional work rolls, and to 0.1691 MN/μm by increasing 25.26% with VCR and ASR.
Since the relative strip crown produced in the hot wide strip mill takes on a permanent aspect and cannot be modified by the subsequent cold rolling process, the change in relative strip crown has to be done when the strip thickness is still reasonable, i.e. in the hot wide strip mill[21]. In the cold rolling process stages, the roll gap profile must be adapted to the entry strip profile so that the strip is uniformly elongated over its entire width, i.e. ratio of relative strip crown is equal to 1.0. The deterioration of strip flatness does not occur as long as the values for the change in relative strip crown are within a certain range that is known as flatness dead band, i.e. ratio of relative strip crown is greater than 1.0. It is expected that the requisite crown is obtained in the upstream stands. As mentioned above, the upstream three stands are conventional 4-high mills in the 1 700 mm hot finishing mills that do not provide an effective adjustment of the roll gap profile. In order to improve the controllability of profile and flatness at the 1 700 mm hot strip mill, a varying contact backup roll has been applied first in stand F3. Some sample strips of the hot-rolled coil were taken before and after application of the varying contact backup rolls. As listed in Table 1, the ratio of relative strip crown with varying contact backup rolls amounts to 1.58 or even 1.61, increased by 31% compared with that of relative strip crown with conventional backup rolls. Due to the existing larger dead flatness band range in upstream stands, the buckles or waves in the rolled strip do not occur in the production mill.
The ASR technology has applied to the production of 2.3 mm×1 050 mm electrical steel sheets rolling campaign successfully since November 2004. As listed in Table 2 by the production test, the rate of measured crown less than 52 μm is increased from 13.7% to 81.25% and the rate of measured crown longer than 60 μm is decreased from 65.6% to 6.60%, the life of rolls expands from 60 coils to 80 coils and more. From July 2005 to present, the ASR technology has applied continuously to the production of 2.3 mm×1 050 mm electrical steel sheets rolling campaign. The rate of measured crown less than 45 μm is increased from 42.03% of the first half to that of 82.38% of the second half of 2005 by annual continuous statistics. The rate is increased to 93.15% in the first quarter of 2006.
Table 1 Effect of varying contact backup rolls on crown control applied in upstream stand F3 of 1 700 mm hot strip mills
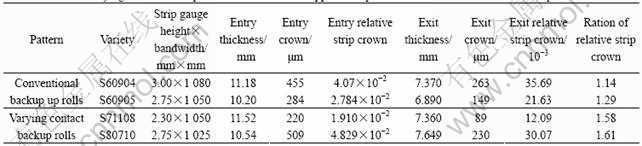
Table 2 Comparison of crown of non-oriented electrical steel sheets with ASR and conventional work roll contours

In contrast to an existing generally non-uniform wear that leads to a significant variation of roll contour for a conventional backup and work rolls, the asymmetry self-compensating work rolls and varying contact backup rolls have almost the same roll contour during a hot strip mill cycle. Accordingly, the VCR and ASR not only can play its performance in an entire hot strip mill cycle as described above, but also the rolling period of a newly ground asymmetry self-compensating work rolls set expands from 60 coils to 80 coils and more within a 2.3 mm×1 050 mm electrical steel sheet rolling campaign, and that of varying contact backup roll set can prolong to 3 weeks or even 5 weeks in upstream stands from 2 weeks.
5 Conclusions
1) Variation of roll contours is a key factor affecting strip profile and flatness in hot strip mills. The key mill type configuration of strip profile and flatness is realization of crown control in upstream stands and the ability of both crown and wear control in downstream stands of hot strip mills. A rather smooth local work roll contour near strip edges and an increase in length rolled can be achieved by application of long stroke work roll shifting system with conventional work roll contours that is incapable of the crown control, especially in downstream stands. CVC technology is suitable for upstream stands with excellent crown control ability and if being applied to downstream stands, the technology is not equipped with ability for the wear control.
2) The requisite crown can be obtained conveniently by application of varying contact backup rolls in the upstream stands that have almost the same roll contours during an entire hot strip mill cycle. And at the same time the crown control range by bending force and the roll gap stiffness with varying contact backup rolls are greater than those with conventional backup rolls in hot finishing mills. The application of VCR and ASR configuration in downstream stands, having the ability of both crown and wear control, gives better strip profile and flatness quality, an increase in coil numbers within the rolling campaign and the significant alleviated effect of severe work roll wear contours on performance of edge drop control in hot strip mills.
References
[1] CHEN Xian-lin. Flatness control in new generation high-tech mills for wide strip rolling [J]. Journal of University of Science and Technology Beijing, 1997, 19(S1): 1-4. (in Chinese)
[2] SHIMIZU Y, IWATANI J, YAMASAKI Y, TAKEGUCHI T, KAMETANI A. Development of new hot rolling process for thin strip rolling [J]. Technical Review-Mitsubishi Heavy Industries, 2000, 37(2): 45-47.
[3] SEILINGER A, MAYRHOFER A, KAINZ A. SmartCroum—A new system for improved profile and flatness control [J]. Aluminium International Today, 2003, 15(2): 26-28.
[4] CAO Jian-guo, CHEN Xian-lin, ZHANG Qing-dong, HE An-rui. Roll wear pattern and appraisal of roll contour in hot wide strip mill [J]. Journal of University of Science and Technology Beijing, 1999, 21(2): 188-190, 194. (in Chinese).
[5] ZHANG Xiao-ming, JIANG Zheng-yi, TIEU A K, LIU Xiang-hua, WANG Guo-dong. Numerical modeling of the thermal deformation of CVC roll in hot strip rolling [J]. Journal of Materials Processing Technology, 2002(130/131): 219-223.
[6] GINZBURG V B. High-quality steel rolling: Theory and practice [M]. New York: Marcel Dekker Inc, 1993.
[7] DEREK A S, PATRICK J M, CARLOS J M, ROBCRT J A, RODNEY R A. Control strategies for high production and quality: US steel Gary 84-in. hot strip mill [J]. Iron and Steel Engineer, 1998, 75(6): 31-39.
[8] JOHN S, SIKDAR S, MUKHOPADHYAY A, PANDIT A. Roll wear prediction model for finishing stands of hot strip mill [J]. Ironmaking and Steelmaking, 2006, 33(2): 169-175.
[9] CAO Jian-guo, ZHANG Jie, GAN Jian-bin, SU Yi, TANG Ben-li, YAN Tan-li. Work roll wear prediction model of non-oriented electrical steel sheets in hot strip mills [J]. Journal of University of Science and Technology Beijing, 2006, 28(3): 286-289. (in Chinese)
[10] XU Le-jiang, XU Yao-huan, ZHANG Yong, HUA Jian-xin, CHEN Xian-lin, ZHANG Jie, YANG Quan, ZHANG Qing-dong. CVC technology in China’s largest cold strip mill [J]. Steel Technology International, 1994/1995(yearly): 203-208.
[11] CHEN Lian-sheng, HUANG Chuan-qing, LIAN Jia-chuang. Comparative analysis on predicted and measured wears of PFC at finishing rolling train of 2050 hot rolling mill [J]. Research on Iron and Steel, 2000(1): 24-27. (in Chinese)
[12] ARATANI H, OZONO R, NAKANO T. Expansion of pair cross (PC) mill applications to hot and cold rolling mills [J]. Iron and Steel Engineer, 1993, 70(3): 32-37.
[13] GINZBURG V B, AZZAM M. Selection of optimum strip profile and flatness technology for rolling mills [J]. Iron and Steel Engineer, 1997, 74(7): 30-38.
[14] PENG Yan, LIU Hong-min. Study on increasing calculation precision and convergence speed of streamline strip element method [J]. Journal of Central South University of Technology, 2004, 11(1): 105-108.
[15] PENG Yan, LIU Hong-min, WANG Dong-cheng. Simulation of type selection for 6-high cold tandem mill based on shape control ability [J]. Journal of Central South University of Technology, 2007, 14(2): 278-281.
[16] CHEN Xian-lin, ZOU Jia-xiang. A specialized finite element model for investigating controlling factors affecting behavior of rolls and strip flatness [C]// Proceedings of the 4th International Conference on Steel Rolling. Deauville: 1987, E4.1-E4.7
[17] CAO Jian-guo, ZHANG Jie, SONG Ping, SU Yi, YAN Tan-li. ASR technology for controlling profile and flatness of non-oriented electrical steel strip in hot rolling [J]. Iron and Steel, 2006, 41(6): 43-46. (in Chinese)
[18] CHEN Xian-lin, YANG Quan, ZHANG Qing-dong, ZHANG Jie, CUI Zhen-bin, GUO Lei, LIU He, YANG Da-ke, XU Le-jiang, XU Yao-huan. Varying contact backup roll for improved strip flatness [J]. Steel Technology International, 1994/1995(yearly): 174-178.
[19] CHEN Xian-lin, ZHANG Jie, ZHANG Qing-dong, WANG Chang-song, YANG Quan, LIU Ben-ren, WANG Ling, WEI Gang-cheng, HUANG Si-qing, YANG Jin-an. Development in profile and flatness control system of hot strip mills [J]. Iron and Steel, 2000, 35(7): 28-33. (in Chinese)
[20] CAO Jian-guo, ZHANG Jie, CHEN Xian-lin, WEI Gang-heng. Control of roll contour for strip profile and flatness in hot rolling [C]// 44th Mechanical Working and Steel Processing Conference Proceedings & 8th International Conference on Steel Rolling Proceedings. Florida, 2002: 1001-1010.
[21] WILMS W, VOGTMANN L, KL?CKNER J, BEISEMANN G, ROHDE W. Profile and flatness control in hot strip mills [J]. Metallurgical Plant Technology, 1985, 8(6): 74-90.
(Edited by YANG Hua)
Foundation item: Project(20040311890) supported by the Science and Technology Development Foundation of University of Science and Technology Beijing
Received date: 2007-10-13; Accepted date: 2007-12-15
Corresponding author: CAO Jian-guo, PhD, Associate Professor; Tel: +86-10-62332835; E-mail: geocao@me.ustb.edu.cn