
Damping properties of silicone rubber/polyacrylate sequential interpenetrating networks
WANG Yan-bing(王雁冰), HUANG Zhi-xiong(黄志雄), ZHANG Lian-meng(张联盟)
School of Materials Science and Technology, Wuhan University of Technology, Wuhan 430070, China
Received 10 April 2006; accepted 25 April 2006
Abstract: Silicone rubber/polyacrylate sequential interpenetrating polymer networks(IPNs) were prepared by silicone rubber sheet dipped into the solution composed of different acrylate monomers and benzoyl peroxides(BPOs) for different time at room temperature and then acrylate polymerized at 80 ℃ for 2 h. The molecular structure and damping properties of sequential IPNs were studied by means of FT-IR and dynamic mechanical analysis(DMA), respectively. The FT-IR spectrum shows that polyacrylate distributes unevenly along the thickness direction of IPNs, i.e. the concentration of polyacrylate decreases from the midst to the surface of the IPNs. The DMA shows that cold crystallization of silicone in the temperature range from -47 ℃ to -30 ℃ is reduced and loss factor of IPNs is improved after interpenetrating with polyacrylate. This suggestes that IPNs can be used as damping materials.
Key words: silicone rubber; polyacrylate; sequential interpenetrating networks; damping properties
1 Introduction
Vibration and noise often leads to undesirable consequences such as unpleasant noise, fatigue and failure of structures, decreased reliability and degraded performance[1,2]. The application of polymer damping materials is the most effective and widely used vibration control method. The reduced vibration is achieved by converting the vibration energy into heat energy dissipated by the polymer under cyclic loading. Polymers have pronounced energy absorption based on its glass-to-rubber transition within a certain frequency and temperature range[3].
Silicone rubbers are particular attractive as damping materials because their mechanical properties are reliable and steady in a rather wide temperature range from -50 ℃ to 200 ℃ [3]. However, their damping properties are low at room temperature for the efficient energy absorption temperature range lies in their glass temperature range from about -120 ℃ to -70 ℃, depending on different structures of silicone rubber. Many modifying methods have been used to increase the glass temperature of silicone rubber, such as blending, co-polymerizing or interpenetrating with high damping polymers at room temperature, such as polyurethane [4-12]. However the improvement of damping properties is still limited for their incompatibility with other polymers. In this study, sequential interpenetrating networks of silicone rubber with polyacrylate were prepared by swelling and polymerization method. Swelling and dynamic mechanical properties were also studied.
2 Experimental
Acrylate and methacrylate monomer, i.e. methyl acrylate(MA), methyl methacrylate(MMA), ethyl acrylate(EA), ethyl methacrylate(EMA), butyl acrylate (BA), butyl methacrylate(BMA) all purchased from Sinopharm Chemical Reagent Co, Ltd, and benzoyl peroxide(BPO)was purchased from Chemical Plant of Hubei University.
First, BPO of 102 mg was dissolved in acrylate or methacrylate monomer of 60 g. Silicone sheets(45 mm×24 mm×2 mm) of 2.5 g vulcanized with dicumylperoxide(DCP) were dipped into acrylate (methacrylate) solution and swollen at 25 ℃ for different times(0.5-15 h). Then the swollen silicone sheet was put into a glass tube equipped with vacuum drying oven and acrylate polymerized at 80 ℃ for 2 h.
FOURIER transform infraed (FT-IR) spectra of different samples were measured on a Nicolet Nexus Fourier Transform Infrared Spectroscopy. Dynamic mechanical measurements were performed on Perkin-Elmer DMA 7e. The samples were measured in the compression mode at a fixed frequency of 1 Hz from -130 ℃ to 130 ℃ using a heating rate of 5 ℃/min. The test specimens were 2.3-3.5 mm in thickness and 18-19 mm in diameter.
3 Results and discussion
We chose different acrylate monomers to swell the silicone rubber sheet for different times. Swelling degrees(SD) of silicone sheet in different acrylate monomers are shown in Table 1. SD is characterized by the ratio of increased mass to the initial mass of silicone rubber. SD in BA or BMA is more than in MA, MMA, EA, EMA under the same condition, as shown in Table 1. According to the solubility parameter similitude principle, the components with similar solubility can be compatible, so SD in BA or BMA is more than other acrylates, as shown in Table 2. So BA and BMA are selected as the the acrylate component to prepare the sequential IPNs.
FT-IR were used to characterize the surface and internal molecular structure of IPN. FT-IR spectra of the silicone/polybutyl acrylate(PEA) and silicone/polybutyl methacrylate(PEMA) IPN with swelling time of 15 h and polymerized for 2 h are shown in Fig.1.
As shown in Fig. 1, there is obvious difference in the surface and internal structure of sequential IPN. The spectra of the surface structure is similar to that of
Table 1 SD of silicone sheet in different acrylates
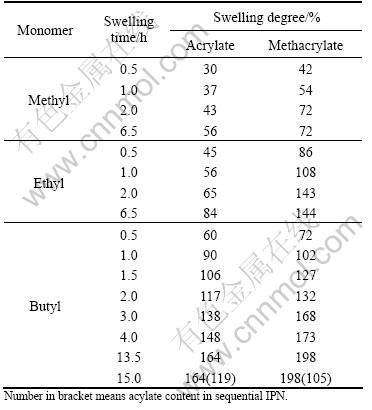
Table 2 Solubility parameter of acrylate and silicone
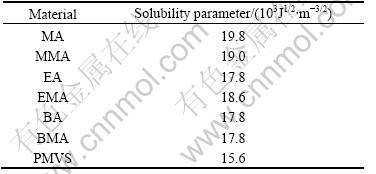
silicone and nearly no absorption peak is observed at 1 730 cm-1(assigned to the C== O streching vibration of saturated polyacrylate)[13], while a sharp absorption peak near 1 730 cm-1 appears in the spectra of the internal of sequential IPN. These results show that the sequential IPN is a kind of component gradient materials. The content of PEA or PEMA increases from either surface to the middle of the sequential IPN. Another absorption peak at 1 160 cm-1 assigns to the C—O symmetrical streching vibration of polyacrylate. No absorption peak is observed at 1 660-1 630 cm-1 (assigned to the C==C streching vibration of unsaturated
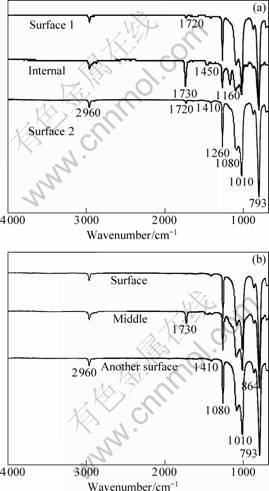
Fig.1 FT-IR spectra of silicone/BA IPNs (a) and silicone/BMA (b) with swelling time of 15 h
acrylate), which shows that BA or BMA polymerized almost completely.
As shown in Table 1, while silicone rubber is swollen for 15 h, the swelling progress reaches equilibrium. However, after polymerization BA or BMA distributes unevenly along the thickness of sequential IPN. This phenomenon is attributed to the volatilizaition of BA or BMA monomer during polymerization. After polymerization, the acrylate mass decreases to a large extent. For example, after swelling for 15 h and polymerization, BA/PMVS decreases from 164% to 119%, and BMA/PMVS decreases from 198% to 105%. This shows that BMA has higher volatilization rate and more mass loss than BA in polymerization.
As mentioned above, sequential IPNs obtained by swelling and polymerization method are acrylate gradient component materials. In order to investigate the influence of acrylate gradient on damping mechanical properties, we study the dynamic mechanical properties of sequential IPN. The dynamic mechanical properties of sequential IPN were characterized by the storage moduli(E′), loss moduli(E″) and loss factor (tan δ) and these parameters were functions of temperature and frequency. The materials with a high and wide loss factor peak can be used as good damping materials. Dynamic mechanical properties of silicone rubber and IPN were studied using Perkin-Elmer DMA 7e from -130 ℃ to 130 ℃. Dynamic mechanical spectra of silicone rubber, PMVS/PBA IPNs with different swelling time, 2 h and 15 h, are shown in Figs.2-4.
From Figs.2-4, as the temperature increases, the materials go through three region, glass region, glass transition region and rubbery region and the loss factor goes through a maximum in the glass transition region and then decreases in the rubbery region. The loss factor is low below the glass transition temperature because the chain segments are frozen and the molecular motions are primarily changes of bond length and bond angle and the deformations are mainly elastic. Above the glass transition temperature, the loss factor is low because molecular chain obtained enough energy and the molecules are free to move. The loss factor is high in the
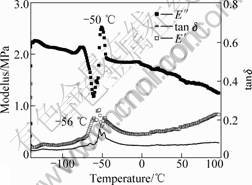
Fig.2 DMA of silicone rubber
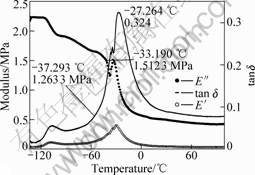
Fig.3 DMA of silicone/PBA with swelling time of 2 h
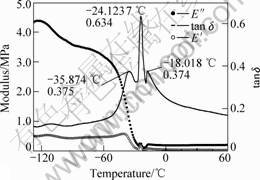
Fig.4 DMA of silicone/PBA with swelling time of 15 h
glass transition region because the chain segments begin to move but move unfreely for high system viscosity.
The loss factor maximum of PMVS is only 0.14 in Fig.2 and that of all sequential IPNs are higher than PMVS, which shows that sequential interpenetrating could improve the damping properties of silicone rubber.
At about -110 ℃ loss factor shows a peak in Figs.2-4, which corresponds to the glass temperature of silicone rubber. In Fig.2, E′ increases rapidly in the temperature range from -56 ℃ to 50 ℃, which shows the cold crystal formation of silicone rubber. After -50 ℃, E′ decreases quickly and the silicone rubber enters elastic region indeed.
The maximum loss factor appearing at -27.3 ℃ and -24.1 ℃ in Figs.3 and 4 corresponds to the glass temperature of PBA. Loss factor maximum of silicone/PBA with swelling time of 15 h is much higher than that of silicone/PBA with swelling time of 2 h. This is ascribed to higher content of PBA of IPNs with more swelling time.
The crystallization degree of IPN in the temperature range from -40 ℃ to -30 ℃ decreases to a low extent, especially that of PMVS/PBA obtained with swelling time of 15 h. This shows that interpenetrating can decrease the cold crystal of silicone rubber and improve the practical application.
In conclusion, damping properties of the sequential IPN obtained by silicone rubber dipped in acrylate and acyalate is improved and crystal degree decreases.
4 Conclusions
To increase the damping properties of silicone, different acrylate monomers were used to prepare sequential silicone/PBA(or PBMA )IPNs by swelling crosslinked silicone rubber in acrylate monomer containing BPO as initiator and by varying sweeling time. Dynamic mechanical analysis shows that IPNs have higher loss factor than silicone rubber and can be used as vibration and acoustic dampers.
References
[1] BARBER A. Handbook of Noise And Vibration Control[M]. Amsterdam: Elsevier Science, 2002.
[2] JONES D I G. Handbook of Viscoelastic Vibration Damping[M]. New York: Wiley Interscience, 2001.
[3] CHUNG D D L. Review: materials for vibration damping[J]. Journal of Materials Science, 2001, 36(24): 5733-5737.
[4] ABBS F. Comparison of polydimethylsiloxane- poly(2-hydroxyethyl methacrylate) IPNs with their physical blends[J]. Journal of Applied Polymer Science, 2002, 86: 3480-3485.
[5] ADHIKARI R. Low-modulus siloxane-based polyurethanes. I. Effect of the chain extender 1,3-bis(4-hydroxybutyl)1,1,3,3- tetramethyldisiloxane (BHTD) on properties and morphology[J]. Journal of Applied Polymer Science, 2002, 83(4): 736-746.
[6] ADHIKARI R. Mixed macrodiol-based siloxane polyurethanes: effect of the comacrodiol structure on properties and morphology[J]. Journal of Applied Polymer Science, 2000, 78(5): 1071-1082.
[7] IOAN S, GRIGORESCU G, STANCIU A. Dynamic-mechanical and differential scanning calorimetry measurements on crosslinked poly(ester-siloxane)-urethanes[J]. Polymer, 2001, 42(8): 3633-3639.
[8] IOAN S, GRIGORESCU G, STANCIU A. Effect of segmented poly(ester-siloxane)urethanes compositional parameters on differential scanning calorimetry and dynamic-mechanical measurements[J]. European Polymer Journal, 2002, 38(11): 2295-2303.
[9] FAN Qu-li. Synthesis and properties of polyurethane modified with aminoethylaminopropyl poly(dimethyl siloxane)[J]. Journal of Applied Polymer Science, 1999, 74(10): 2552-2558.
[10] JIANG Xi-qun. Study on segmented polyurethane with mixed soft segments of polychloromethyl methyl siloxane and polytetramethylene oxide[J]. Chinese Journal of Polymer Science(English Edition), 1994, 12(3): 228-236.
[11] BISCHOFF R. Polysiloxanes in macromolecular architecture[J]. Progress in Polymer Science,1999, 24: 185-219.
[12] DAHROUCH M. Synthesis and properties of poly(butylene terephthalate)-poly(ethylene oxide)-poly(dimethylsiloxane) block copolymers[J]. Macromol Symp, 2003, 199: 147-162.
[13] KE Yi-kan. Analyzed Chemical Handbook—Spectrum Analysis[M]. Beijing: Chemical Industry Press, 1985. 356.(in Chinese)
(Edited by YANG You-ping)
Foundation item: Project (50473013) supported by the National Natural Science Foundation of China
Corresponding author: WANG Yan-bing; Tel:+86-27-63049095; E-mail:henanwyb@126.com