
Preparation of primary Al-Si alloy from bauxite tailings by carbothermal reduction process
YANG Dong(杨 栋), FENG Nai-xiang(冯乃祥), WANG Yao-wu(王耀武), WU Xiao-lei(武小雷)
School of Materials and Metallurgy, Northeastern University, Shenyang 110004, China
Received 17 June 2009; accepted 15 August 2009
Abstract: Effects of various reaction parameters such as atmospheric pressure, treating temperature, sintering time and bituminite content on the preparation of primary Al-Si alloy by carbothermal reduction of bauxite tailings were investigated by XRD,XRF,infrared absorption carbon-sulfur analysis unit and SEM coupled with EDS. Meanwhile, the mechanism of carbothermal reduction of Al2O3 and SiO2 was discussed. It is found that pressure and temperature are major factors that influence the carbothermal reduction of bauxite tailings. The appropriate conditions for preparation of primary Al-Si alloy are as follows: atmospheric pressure of 0.1 MPa, heating temperature of 1 900 ℃,bituminite content of 95% (mass fraction) of theoretic bituminite content and sintering time of 1 h. Among four mechanisms of carbothermal reduction of Al2O3 and SiO2, the theory of the formation and decomposition of carbides might be the best one to interpret the reaction process.
Key words: primary Al-Si alloy; bauxite tailings; carbothermal reduction process; reduction mechanism
1 Introduction
Al-Si alloy has been widely used in many fields such as automotive, aerospace and military industries, owning to its excellent castability, weldability, thermal conductivity and corrosion resistance[1-3]. Furthermore, according to Ref.[4], of all the Al-based alloys, the consumption of Al-Si alloy is the largest. At present, production of Al-Si alloy includes mainly fusion and carbothermal reduction methods. Compared with fusion method,carbothermal reduction method owns lots of merits such as more simple process, lower price equipments, higher energy usage ratio, and lower requirement of raw materials[5]. Bauxite tailing, generated during the flotation-Bayer process, is a kind of waste product. At present, most of them are deposited on land surface, which not only occupies mass land but also pollutes environments[6]. On the other hand, the bauxite tailings, whose Al/Si(A/S) ratio is about 1.5, is a kind of secondary resources[7]. Therefore, preparation of Al-Si alloy by carbothermal reduction of bauxite tailings is both environmentally necessary and economically feasible.
In recent years, much attention has been paid to using bauxite tailings to produce refractory, building and luminescent materials[8-11]. There are less literatures, however, published on the application of them in preparation of primary Al-Si alloy. Therefore, in this study,effects of reaction parameters on carbothermal reduction of bauxite tailings to prepare primary Al-Si alloy, which was used as deoxidant in steel-making process or to make cast Al-Si alloy, were investigated. Meanwhile, the mechanism of carbothermal reduction of Al2O3 and SiO2 was discussed.
2 Experimental
2.1 Materials
In the present work, the floated bauxite tailings (Zhengzhou, Henan Province, China) and industrial grade alumina were chosen as raw materials. Table 1 gives a chemical composition of tailings, while Fig.1 shows its X-ray diffraction pattern. It is observed that this mineral was well crystallized, and Al2O3, SiO2 and Fe2O3 constituted the major components in the mineral. The quality bituminite (Shenfu, Shannxi Province, China) and sulphite pulp liquor were used as reductive agent and binder, respectively.
Table 1 Chemical composition of bauxite tailings (mass fraction, %)

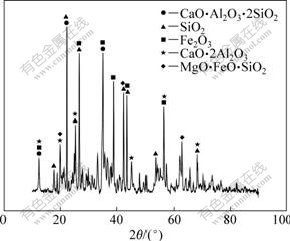
Fig.1 XRD pattern of bauxite tailings
2.2 Pelleting and heating treatment
The predetermined amounts of the above-mentioned materials were mixed uniformly and pressed into pellets of 20 mm in diameter and 25-30 mm in height under 22.5 MPa. Then, the pellets were dried in bake oven at 120 ℃ for 8 h to remove the moisture completely. After that, the green pellets were loaded into graphite crucible and heated in a vacuum graphite furnace with argon as the protective atmosphere to temperatures of 1 600-2 000 ℃ and then soaked for 0.5-1.5 h. The heating rate was 20 ℃/min from room temperature to 1 200 ℃ and 5 ℃/min from 1 200 ℃ to 2 000 ℃.
2.3 Analysis methods
The phase composition of the reaction products obtained was carried out by D/max-rB X-ray diffractometer (XRD). The microstructural study and energy dispersive analysis of X-ray (EDS) were performed by SSX-550 scanning electron microscope (SEM). Considering that Si plays an important role in the study and it is susceptible to oxidation, the reaction products were not subjected to decarburization in the XRD and SEM tests. XRF (100-E) and infrared absorption carbon-sulfur analysis unit (CS-244) were used to examine the reduction rate of Al2O3 and yield of SiC. The reaction products to be measured were washed with dilute hydrochloric acid to remove interfering materials such as metallic Al and aluminium carbide, and oxidized at 800 ℃ for 5 h in air to remove excess carbon.
3 Results and discussion
3.1 Effects of reaction parameters on carbothermal reduction process
3.1.1 Effect of atmospheric pressure
In order to study the effect of atmospheric pressure on the carbothermal reduction of tailings, two reaction systems were designed. System 1 consisted of a graphite crucible without a lip. When the soaking temperature was achieved, the external atmospheric pressure was 0.03 MPa. System 2 consisted of a graphite crucible with a lip, and in the centre of the lip there were small holes for the pellets to communicate and equilibrate with the outside atmosphere at high temperature, and to keep the vapor products from escaping quickly. When the reaction proceeded, the external atmosphere was 0.1 MPa.
Figs.2(a) and (b) show the XRD patterns of the reacted products at 1 900 ℃ for 1 h through systems 1 and 2, respectively. It is observed that the phases constitute of System 1 is different distinctly from that of System 2. With the System 1, the products were Al4C3 and SiC, and the Al-Si-Fe alloy only accounted for marginal content; while with the System 2, the products composed mainly of Al-Si-Fe alloy, Al4C3 and SiC. These differences might be ascribed to the following reactions [11]:
SiO2+Si=2SiO(g) (1)
Al2O3+4Al=3Al2O(g) (2)
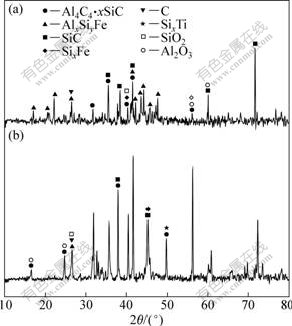
Fig.2 XRD pattern of products by systems 1 (a) and 2 (b)
As can be seen in Eqs.(1) and (2), the gaseous products under low atmospheric pressure would push the reaction to move right constantly, resulting in the Si and Al loss. So, this indicates that low pressure is not good for the preparation of Al-Si alloy although it is favored in the case of thermodynamics view[12].
3.1.2 Effect of heating temperature
Fig.3 gives the XRD patterns of the products prepared from bauxite tailings at 1 600, 1 700, 1 800, 1 900 and 2 000 ℃, respectively. It is observed that the heating temperature has great effect on the phase composition of the products. Al2O3, SiO2 and CaO were the major phase components when the treating temperature was 1 600 ℃; and partial SiO2 began to convert to SiC. When the temperature rose to 1 700 ℃, there appeared peaks indexed as Al4C3?xSiC. According to the reaction: 2Al2O3+9C=Al4C3+6CO, the ΔGΘ, standard Gibbs free energy changes, turning to negative value at 1 991 ℃,which was much higher than that at 1 700 ℃. The main reason laid in the thermodynamic analysis on the assumption that all the pressure of gas phase was 0.1 MPa, while the actual pressure of CO was very low in the treating temperature. Meanwhile, with the temperature rising, the peaks of Al4C3?xSiC became weak, which may be due to the following reactions:
3Si+Al4C3=4Al+3SiC (3)
Al4C3+Al2O3=6Al+3CO (4)
SiO2+2Al4C3=8Al+3Si+6CO (5)
3SiC + Al2O3 = 2Al + 3Si + 3CO (6)
2SiC+SiO2=3Si+2CO (7)
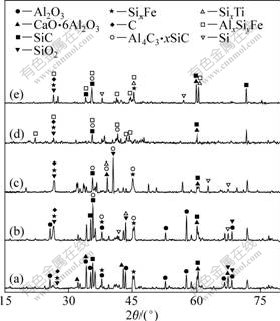
Fig.3 XRD patterns of products prepared from bauxite tailings at various temperature: (a) 1 600 ℃; (b) 1 700 ℃ (c) 1 800 ℃; (d) 1 900 ℃; (e) 2 000 ℃
When being treated at 1 900 ℃, the products obtained were composed mainly of Al-Si-Fe alloy (primary Al-Si alloy) and carbides. With the reaction temperature further rising, the change of components of reaction products was not pronounced. Thus, it is concluded that, for preparation of primary Al-Si alloy by carbothermal reduction of bauxite tailings, the optimal temperature is 1 900 ℃. Furthermore, it is noteworthy that, from 1 600 ℃ to 2 000 ℃, SiC always exists in the products owning to the fact that it is prone to form and is difficult to decompose, which enhances the difficulties of preparation of primary Al-Si alloy by carbothermal reduction significantly.
3.1.3 Effects of soaking time and bituminite content
The reduction rate of Al2O3 (mass ratio of reacted Al2O3 to total Al2O3) and the yield of SiC (mass ratio of Si ion in SiC to Si ion in total SiO2) are the important indexes of carbothermal reduction process of tailings. The high reduction rate of Al2O3 means the high recovery rate of metal and the reduction reaction proceeding relatively completely; while the high yield of SiC does not favor the preparation of primary Al-Si alloy,owning to too much SiC content leading to the hearth of electric arc rising up, and even the production breaking off[13].
Table 2 shows the reduction rate of Al2O3 and yield of SiC with soaking time of 0.5, 1 and 1.5 h. With prolonging soaking time, the reduction rate of Al2O3 increased, but the increasing ratio was not pronounced. On the other hand, the SiC content decreased constantly, meaning that SiC was decomposed. And when the soaking time exceeds 1 h, the decreasing ratio became small. Based on these, it is concluded that too long soaking time is not necessary, and 1 h is appropriate.
Table 2 Effect of soaking time on reduction rate of Al2O3 and yield of SiC
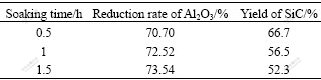
Fig.4 shows the effect of the different relative content of bituminite (the percentage of bituminite content of theoretic one) on the reduction rate of Al2O3 and yield of SiC. It is observed that, the reduction rate of Al2O3 increased firstly with increasing bituminite content up to 95% and decreased with further increasing bituminite content. The yield of SiC increasing firstly was not obvious; while when the bituminite content increased over 95% of theoretic one, the yield of SiC increased apparently. Thus, it is concluded that the best bituminite content is 95% of theoretic one. This may be due to the fact that carbothermal reduction of SiO2 is much easier than Al2O3. A little larger C amount is good for production of SiC owning to the reaction: SiO2+3C=SiC+2CO. The SiC produced needed to consume lots of C, resulting in the phenomenon that the C content used to reduce Al2O3 was deficient[13]. Therefore, when the bituminite content is larger than 95% of theoretic one, the reduction rate of Al2O3 decreased inversely.
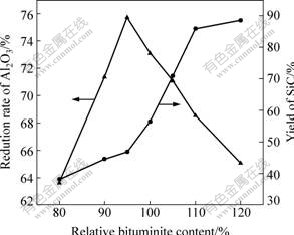
Fig.4 Effect of bituminite content on reduction rate of Al2O3 and yield of SiC
3.1.4 SEM study
Fig.5(a) shows the back scatted electron image of sintered products by carbothermal reduction under argon atmosphere at 1 900 ℃ for 1 h. As seen in Fig.5(a), six phases were found from the contrast of the back scatted electron image. EDS analysis was preformed to get the chemical composition of each phase and the results are represented in Fig.5(b) and Table 3, respectively. It can be known that the white phase consists mainly of Al-Si-Fe-Ti alloy, including small amounts of C and P. Both the gray white and the gray phases are the intermetallic Al-Si-Fe alloys, and the diversity between them is the different elements content. The gray black phase is constituted mainly of Al and the O content is marginal. This means that there is free Al, but is not detected by XRD, which might be due to its content not high enough. The dark gray strip-like and the dark plate-like phases are the Al-Si-C alloys. From Table 3 and XRD results, one could learn that, the both phases are Al4C3?SiC and Al4C3?46SiC.
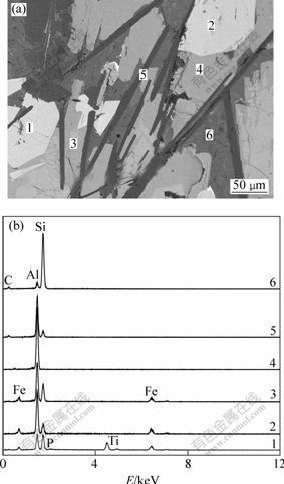
Fig.5 Backscattered electron image and EDS spectra of sample treated at 1 900 ℃ for 1 h
Table 3 EDS results of sintering products
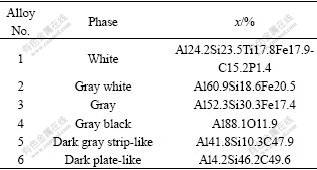
It is noteworthy that the carbon content cannot be confirmed with great assurances (weak intensities of carbon’s peak in spectra) because of EDS method limitations (The EDS scintillation detector is capable of identifying elements with atomic numbers equal to or greater than 5 but for those below 8 the quantification becomes very difficult).
3.2 Reduction mechanism
In terms of mechanism of carbothermal reduction of Al2O3 and SiO2, there are mainly four theories[5, 11-12]: 1) silicothermic reduction; 2) two-step reduction; 3) the formation and decomposition of carbides; 4) the formation and decompose of Al-oxycarbides. Up to date, the reduction mechanism has not been clarified. So, in this work, the reduction mechanism of the carbothermal reduction of Al2O3 and SiO2 was discussed.
The course of the reactions and the products formed at various stages could be followed through analysis of XRD patterns of products. Fig.6 shows the XRD patterns of the products prepared from industrially pure alumina and silica at 1 600, 1 700, 1 800, 1 900 and 2 000 ℃ for 1 h. XRD patterns of samples reacted at 1 600 and 1 700 ℃ contained peaks of SiC, Al4C3 and Si due to the fact that the following reactions began to perform:
SiO2(s)+3C(s)=SiC(s)+2CO (8)
2C+SiO2=Si+2CO (9)
2Al2O3+9C=Al4C3+6CO (10)
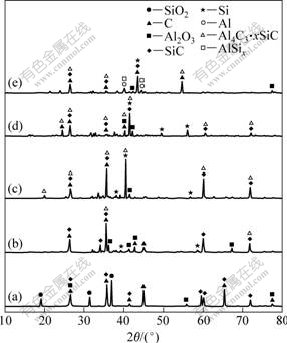
Fig.6 XRD patterns for samples prepared from industrially pure alumina and silica at different temperatures: (a) 1 600 ℃; (b) 1 700 ℃; (c) 1 800℃; (d) 1 900 ℃; (e) 2 000 ℃
The SiC and Al4C3 contents increased firstly with reaction temperature rising up to 1 800 ℃ and then decreased with reaction temperature further rising, and at 2000 ℃ there were Al and Al-Si peaks emerged. It is ascribed to the phenomenon that Eqs.(3)-(7) began to proceed. Furthermore, according to Ref.[14], Eqs.(5) and (7) were capable of proceeding which had been verified by experiment. Based on these, it is clear that the process of carbothermal reduction of Al2O3 and SiO2 is accompanied by the formation and decomposition of carbides.
In the case of silicothermic reduction theory, the key step can be represented by
Al2O3+3Si=2Al+3SiO(g) (11)
The initiative temperature of above-mentioned reaction is 2 128 ℃; while according to Ref.[12], Al was capable of forming by Eq.(11) at 1 900 ℃, which was also demonstrated by our experiment. However, using silicothermic reduction theory to interpret the carbothermal reduction of Al2O3 and SiO2 may not be feasible. It is attributed to the yield of SiC of 65.9% and the residual ratio of SiO2 of 24.7%, which were tested by infrared absorption carbon-sulfur analysis unit and XRF, resulting in the Si content used to reduce Al2O3 is very low. Besides, Eq.(3) is much easier to perform than Eq.(11), because Eq.(3) is spontaneous and exothermic at even much lower temperature.
As for two-step reduction theory, the initiative temperature of Eq.(12) is higher than that of Eq.(10) by almost 100 ℃. So, the formation rate of Al2O is very low, and meanwhile, the formation rate of SiO is low because of the high formation rate of SiC and high residual ratio of SiO2. Therefore, the two-step reduction theory may not interpret carbothermal reduction of Al2O3 and SiO2 process:
Al2O3+2C=Al2O+2CO (12)
Considering that there are no Al4O4C peaks from 1 600 to 2 000 ℃, the process of carbothermal reduction of Al2O3 and SiO2 may not be interpreted by the formation and decomposition of Al-oxycarbides theory.
In addition, according to Refs.[15-16], Fe2O3 plays an important role in carbothermal reduction of Al2O3 and SiO2, due to the fact that Fe could improve the reduction rate of Al2O3 and decompose the carbides such as Al4C3 and SiC at high temperature, resulting in the reduction reaction easier to perform. Therefore, from this point of view, it is also shown that using the theory of the formation and decomposition of carbides to interpret the process of carbothermal reduction of Al2O3 and SiO2 may be feasible.
4 Conclusions
1) Atmospheric pressure and reaction temperature are major factors that influence the carbothermal reduction of bauxite tailings. The appropriate conditions for the preparation of primary Al-Si alloy are as follows: atmospheric pressure 0.1 MPa, heating temperature 1 900 ℃, bituminite content of 95% of theoretic bituminite content, and sintering time 1 h.
2) The primary alloy obtained consists of six phases. Besides Al-Si-Fe alloy with high content of Al, there are some carbides in the alloy, which are not in favor of preparation of primary Al-Si alloy.
3) Among four mechanisms of carbothermal reduction of Al2O3 and SiO2, the theory of the formation and decomposition of carbides may be the most appropriate one to interpret the carbothermal reduction process.
References
[1] YOU Jing,WANG Yao-wu, FENG Nai-xiang, YANG Ming-sheng. Preparation of casting alloy ZL101 with primary Al-Si alloy [J]. Transactions of Nonferrous Metals Society of China, 2008, 18(1): 116-120.
[2] OS?RIO W R, GOULART P R, GARCIA A. Effect of silicon content on microstructure and electrochemical behavior of hypoeutectic Al-Si alloys [J]. Materials Letters, 2008, 62: 365-369.
[3] ZEREN M, KARAKULAK E. Influence of Ti addition on the microstructure and hardness properties of near-eutectic Al-Si alloys [J]. Journal of Alloys and Compounds, 2008, 450: 255-269
[4] ZHANG Wan-fu. Building our country’s electrothermal Al-Si alloy factory by Russian technology [J]. Transactions of Nonferrous Metals Society of China, 1998, 8(s2): 425-427. (in Chinese)
[5] QIU Zhu-xian. Nonferrous metals metallurgy [M]. Beijing: Metallurgical Industry Press, 1998: 86-87. (in Chinese)
[6] YANG H Z, CHEN C P, SUN H W, LU H X , HU X. Influence of heat-treatment schedule on crystallization and microstructure of bauxite tailings glass-ceramics coated on tiles [J]. Journal of Materials Processing Technology, 2008, 97: 206-211.
[7] YUAN Ming-liang, WANG Yan-mei, HU Yue-hua. Removing of titanium and iron from bauxite tails and its surface modification [J]. The Chinese Journal of Nonferrous Metals, 2007, 17(12): 2059-2064. (in Chinese)
[8] HU Yue-hua, WANG Yu-hua, WANG Dian-zuo. Flotation chemistry of Al-Si minerals and desilication from bauxite [M]. Beijing: Science Press, 2004: 256. (in Chinese)
[9] WANG Y H, LAN Y, HU Y H. Adsorption mechanisms of Cr(VI) on the modified bauxite tailings [J]. Minerals Engineering, 2008, 21: 913-917.
[10] GARCIA-GUINEA J, RUBIOB J, CORRECHERC V. Luminescence of α-Al2O3 and α-AlOOH natural mixtures [J]. Radiation Measurement, 2001, 33: 653-658.
[11] School of Metallurgy of Northeastern University. Light metals metallurgy [M]. Beijing: Metallurgical Industry Press, 1960: 397-399. (in Chinese)
[12] YAO Guang-chun. Preparation of Al-Si alloy by electrothermal process [M]. Shenyang: Northeastern University Press, 1998: 20. (in Chinese)
[13] YAO Guang-chun, SUN Ting, ZHANG Xiao-ming, YU Xian-jin, WANG Gui-min. Effects of carbon content etc. parameters on the parathion of aluminum-silicon alloy by electrothermal reduction [J]. Nonferrous Metals: Extrctave Metallurgy, 1998(3): 36-38. (in Chinese)
[14] LIU Lian-shun. Preparation of Al-Si alloy by electrothermal process—The shortcut of proceeding aluminum industry [J]. Light Metals, 1996(6): 40-44. (in Chinese)
[15] LI Zu-shu, XU Chu-shao, CHEN Jie. Thermodynamics study of AlSi [J]. Ferro-alloys, 1995(4): 14-17. (in Chinese)
[16] ZHANG Feng, LI Meng-ji. Technology of producing aluminum-silion alloys (50%) [J]. Ferro-alloys, 2003(4): 17-21. (in Chinese)
Foundation item: Project(2007AA06Z116) supported by the Hi-tech Research and Development Program of China
Corresponding author: YANG Dong; Tel: +86-24-83686463; E-mail: ydong508@yahoo.cn
DOI: 10.1016/S1003-6326(09)60112-6
(Edited by YANG Hua)