
A new variable stiffness absorber based on magneto-rheological elastomer
DONG Xiao-min(董小闵)1, YU Miao(余 淼)2, LIAO Chang-rong(廖昌荣)2, CHEN Wei-min(陈伟民)2
1. State Key Laboratory of Mechanic Transmission, Chongqing University, Chongqing 400044, China;
2. College of Opto-Electronic Engineering, Key Lab of Opto-Electronic Technology and System of Education Ministry, Chongqing University, Chongqing 400044, China
Received 10 August 2009; accepted 15 September 2009
Abstract: A new adaptive variable stiffness absorber was proposed based on a smart material, magnetorheological elastomer (MRE), and its vibration control performance was investigated. Before developing the proposed absorber, the MREs were firstly fabricated by curing a mixture of 704 silicon rubber, carbonyl iron particles and a small amount of silicone oil under an external magnetic field. Then the mechanical properties of the fabricated MREs were measured. On the basis of the measured mechanical characteristics, the MRE absorber was developed and its working characteristics were also tested under various input currents and excited frequencies. Finally, the control responses of a two-degree-of-freedom dynamic system with a MRE absorber were presented under a chirp input and used to evaluate the effectiveness of the MRE absorber.
Key words: magneto-rheological elastomer; variable stiffness; absorber
1 Introduction
Recently, a very attractive and effective semi-active absorbers featuring magneto-rheological (MR) materials such as MR fluids (MRFs) or MR elastomers (MREs) have been proposed by many investigators[1-3]. These absorbing devices based on MR technique have a number of attractive characteristics for use in vibration control, such as fast response characteristic to magnetic field, wide control bandwidth and compact size[4].
MR materials include MRFs, MR foams and MREs, whose rheological properties can be controlled by the application of an external magnetic field[5]. The most common MR material is MRFs, which is magnetically polarizable particles suspended in viscous fluids. Since their invention in 1948, MRF technique has made significant advancements[6]. The MRFs have been proved to be commercially viable and well suited for many applications, such as the automotive suspension vibration control[7], the earthquake resistance[8], clutch[9]. However, MRFs are prone to particle settling with time due to the density mismatch of particles and the carrier fluid, which may degrade the MR effect. In addition, the wear of the magnetic particles can also lead to a reduction in the fluid’s performance and eventual failure of the MR device[6]. Hence, another smart material, MRE, has received much attention in recent years.
Solid analogs of MRFs and MREs can avoid those disadvantages such as settling of particles normally associated with MRFs. MREs include a wide variety of composite materials, which typically consist of magnetically polarizable particles dispersed in a polymer medium. The mechanical properties of MREs such as the storage and loss modulus are altered reversibly by the application of an external magnetic field. Moreover, MREs do not need channels or seals to hold or prevent leakage, are more stable and avoid the particle sedimentation associated with MRFs. Therefore, MREs have many potential engineering applications for vibration control in damping and vibration isolation systems. However, there are only few application reports about MREs compared the MRFs. GINDER et al[10] developed a tunable automotive mounts and bushings based on MREs and found the suspension resonances excited by torque variation could be suppressed by shifting the resonance away from the excitation frequency. DENG et al[11] developed an adaptive tuned vibration absorber based on MREs. The results show that the natural frequency of the absorber based on MREs can be tuned from 55 Hz to 82 Hz. In their later work[12],the shift-frequency capability of the adaptive absorber was theoretically and experimentally evaluated. The results demonstrate that the natural frequency of the proposed absorber can be tuned from 27.5 Hz to 40 Hz. COLLETTE et al[13] numerically investigated two systems based on MREs according to the measured characteristics. The numerical results show that the commandability of the elastomer improves the isolation performance of the MRE isolator under a varying excitation, and decreases the stress of the MRE dynamic vibration absorber under a random excitation. In order to propose a new adaptive variable stiffness absorber based on MREs and evaluate its vibration control performance in this work MRE composed of magnetically polarizable particles dispersed in a 704 silicone rubber was firstly developed. Then, the mechanical properties of the developed MREs were measured experimentally under different input currents and excited frequencies. Subsequently, a new vibration absorber based on the fabricated MREs was developed and its control model was formulated on the basis of measured working characteristics. At last, the control responses of a two-degree-of-freedom dynamic model with the proposed MRE absorber under a chirp input were presented and evaluated through numerical simulation.
2 Magneto-rheological elastomer materials
2.1 Material preparation
MREs were processed by mixing polymer matrices with magnetic iron particles. A 704 silicone rubber produced by Wuxi Xida Adhesive Factory and silicone oil with a viscosity of 0.1 Pa?s were chosen as the polymer matrix, since silicone rubber has some advantages because it can be easily processed from liquid precursors. Carbonyl iron particles produced by BASF with a size of 3-5 μm was also prepared for the magnetic iron particles. Firstly, the carbonyl iron particles were immersed in silicone oil and mixed with 704 silicone rubber. Then the mixture was packed into an aluminum mold and placed in the vacuum to remove the air bubbles in the mixture. At last, the mixture was cured for 24 h at room temperature with a magnetic field of 1 T. A sample of MREs with 60% (mass fraction) carbonyl iron particle is shown in Fig.1.
2.2 Materials characterization
Mechanical characteristics of MRE sample were measured with a system developed by GONG et al[14]. The measurement system includes a dynamic mechanical analyzer (DMA) system produced by Triton Co. and a controllable electromagnet which can provide magnetic
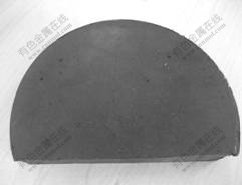
Fig.1 MRE sample
field intensity up to 1.1 T. With this system, both the shear modulus and the loss factor under various magnetic fields and excited frequencies were measured. The experimental results are shown in Fig.2. From Fig.2, it can be found that the shear modulus increases as the excited magnetic field increases. Moreover, the modulus demonstrates an increase with the increase of excited frequency. Therefore, variable stiffness devices can be developed with MREs. On the other hand, the loss factor tends to be independent of excited magnetic field and
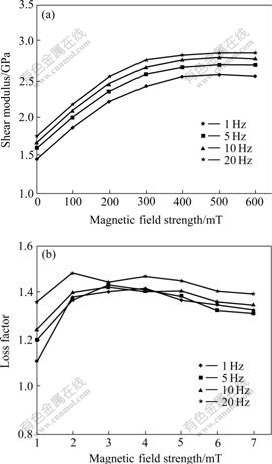
Fig.2 Shear modulus and loss factor with different magnetic fields and excited frequencies
frequency from Fig.2(b). As a result, the damping characteristic was assumed as a constant in this study.
3 Development of MRE absorber
To implement variable stiffness characteristics of an absorber, an adaptive variable stiffness absorber based on MREs was designed and manufactured. Fig.3 shows its schematic configuration and photograph. The absorber consists of a coil, two smart MREs, the outer cylinder and the piston. The MREs are clung to both the outer cylinder and the piston. The magnetic field is generated by the coils and can be controlled by tuning the coil current. By the motion of the piston, the shear deformation of MRE appears. The magnetic field exists in the MRE which is perpendicular to the motion of the piston after the current is applied to the coil. The shear modulus of the MRE is altered when it is subjected to the magnetic field. Thus, the elastic force of the absorber is controlled by the intensity of the magnetic field.
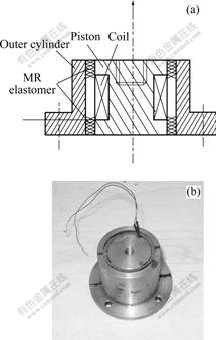
Fig.3 Schematic configuration(a) and photograph(b) of MRE absorber
In the absence of magnetic field, the absorber produces an elastic force only caused by the 704 silicone rubber’s shear resistance. However, if a certain level of magnetic field is supplied to the absorber, the MRE absorber produces an additional elastic force owing to the increased shear modulus of the MRE. The elastic force of the MRE absorber can be continuously tuned by controlling the intensity of the magnetic field. To simplify the analysis of the MRE absorber, a Kelvin-Voigt model was adopted in this study. The model consists of a constant stiffness spring, a variable stiffness spring and a damper with constant damping coefficient in parallel. In the shear direction, k is given by[11]
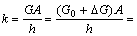
(1)
where G denotes the shear modulus of MRE and consists of two terms, i.e. an initial shear modulus (G0) without a magnetic field, and a shear modulus increment (?G) while applying a magnetic field; A is the shear area, and h is the thickness of MRE; ke is the equivalent stiffness coefficient; FMRE is the controllable elastic force of the MRE stiffness. For simplification, FMRE can be described as a quadratic function of the input current: FMRE=dI2+eI+f, and d, e, f are constants obtained by fitting the measured experimental data.
To measure the working feature of the MRE absorber, the tests of MRE absorber were conducted. A vibrator produced by B&K Co. was used to drive the
MRE absorber. The displacement and force were measured. The velocities were calculated using a central differences approximation. Sinusoidal command signals were used. In this study, the excitation frequencies were 25, 50 and 75 Hz and the displacement amplitude is 0.5 mm. Various constant currents were applied to the MRE absorber to observe the characteristics of the absorber. The applied input current is from 0 to 2 A with increments of 0.5 A. For brevity, only the force- displacement hysteresis under the excitation frequency of 25 Hz is given in Fig.4. The equivalent stiffness of MRE absorber is calculated and shown in Fig.5. From Figs.4 and 5, it can be seen that the elastic force increases with the increase of input current. The enclosed area of the force-displacement remains invariable and is independent of input current, which represents the damping characteristics can not be controlled by the application of magnetic field.
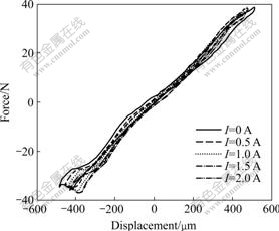
Fig.4 Relationship between force and displacement
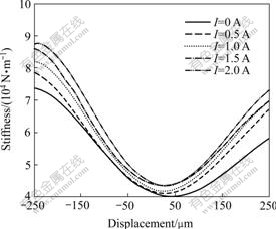
Fig.5 Relationship between stiffness and displacement
4 Numerical simulation
To check the vibration control performance of the MRE absorber, two degrees of freedom dynamic model with a MRE absorber was adopted in this work, as shown in Fig.6. It can be seen from Fig.6 that a MRE absorber is attached to a primary structure. The primary structure undergoes the external displacement excitation of z0. The primary structure has mass of m1, stiffness coefficient of k1 and damping coefficient of c1. m2 is the mass of MRE absorber. The model of MRE absorber consists of three parts including the equivalent damping coefficient of ce, the basal stiffness coefficient of ke and the controllable elastic force FMRE. According to the Newton’s 2nd law, the governing equations of this model can be written as:
(2)

(3)
where z2,
and
represent the absolute displacement, the absolute velocity and absolute acceleration of MRE absorber, respectively; z1,
and
are the absolute displacement, the absolute velocity and absolute acceleration of the primary structure, respectively; z0 and
denote the external displacement input and velocity input, respectively.
If the new state variable is
, Eqns.(2) and (3) can be written as state equation:
(4)
where
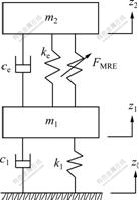
Fig.6 Mathematic model of semi-active tuned vibration absorber
,
,
, 
After deriving the dynamic equations, a simple and effective control algorithm, displacement-based groundhook control, were adopted. The control strategy was studied by KOO et al[15] in the application of vibration control of structure with a MR damper. Their experimental results demonstrate that the displacement- based groundhook control is the most suitable control among four considered groundhook control strategies. Therefore, the control strategy was also adopted in this work. The control law can be expressed as:
≥
(5)
where Gground is the groundhook control gain.
In the following, the semi-active controller and the mathematic model were joined to develop the numerical model. The Matlab/Simulink was used to build block diagrams for the numerical model. For comparison, the passive MRE absorber without control was also considered. For the simulation input, a chirp input was applied to the numerical model to identify the dynamic response of the system. The chirp’s sweep frequency used in this study ranges from 0.01 Hz to 10 Hz in 10 s, which is shown in Fig.7. A fourth order Rung-Kutta integration scheme with a fixed step of 0.001 s was adopted to solve the numerical models. The nominal parameters for these simulations are k1=859.05 kN/m, ke= 41.32 kN/m, m1=1 360 kg, m2=68 kg, ce=500 N?s/m, c1=683 N?s/m. The time responses of the primary structure are shown in Figs.8 and 9. From the results, it can be seen that the MRE absorber can greatly reduce the vibration displacement and acceleration of the primary near its resonance frequency. The maximum reduction of acceleration is over 25%.
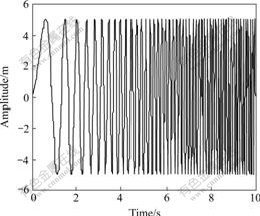
Fig.7 Input excitation
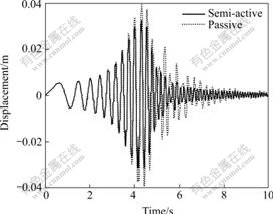
Fig.8 Displacement response of primary structure

Fig.9 Acceleration response of primary structure
5 Conclusions
1) The shear modulus increases with the increase of magnetic field and the loss factor tends to be independent of excited magnetic field.
2) The MRE absorber is developed and its control model is also formulated. On the basis of a two-degree- of-freedom dynamic model, the absorbing ability of the MRE absorber is validated under a chirp input.
3) The MRE absorber can effectively reduce the vibration of the primary structure in a wide range of frequency.
Acknowledgments
We would like to thank Prof. GONG Xing-long for providing the MREs sample and the material test device.
References
[1] SASSI S, CHERIF K, MEZGHANI L, THOMAS M, KOTRANE A. An innovative magnetorheological damper for automotive suspension: From design to experimental characterization [J]. Smart Materials and Structures, 2005, 14(4): 811-822.
[2] LAM H F, LIAO W H. Semi-active control of automotive suspension systems with magneto-rheological dampers [J]. International Journal of Vehicle Design, 2003, 33(1/2/3): 50-75.
[3] NGUYEN Q H, CHOI S B. Optimal design of MR shock absorber and application to vehicle suspension [J]. Smart Materials & Structures, 2009, 18(3): 1-11.
[4] LEE H S, CHOI S B. Control and response characteristics of a magneto-rheological fluid damper for passenger vehicles [J]. Journal of Intelligent Material Systems and Structures, 2000, 11(1): 80-87.
[5] CARLSON J D, JOLLY M R. MR fluid, foam and elastomer devices [J]. Mechatronics, 2000, 10(4/5): 555-569.
[6] GONCALVES F D, KOO J H, AHMADIAN M. A review of the state of the art in magnetorheological fluid technologies—Part I: MR fluid and MR fluid models [J]. The Shock and Vibration Digest, 2006, 38(3): 203-219.
[7] IOAN B. Damper with magnetorheological suspension [J]. Journal of Magnetism and Magnetic Materials, 2002, 241(2/3): 196-200.
[8] XU Z D, GUO Y Q. Fuzzy control method for earthquake mitigation structures with magnetorheological dampers [J]. Journal of Intelligent Material Systems and Structures, 2006, 17(10): 871-881.
[9] GORDANINEJAD F K, BARKAN M, WANG X J. Study of a magneto-rheological grease (MRG) clutch [C]//Active and Passive Smart Structures and Integrated Systems 2007. San Diego: Proceedings of the SPIE, 2007, 6525: 65250C.1-65250C.7.
[10] GINDER J M, NICHOLS M E, ELIE L D, CLARK S M. Controllable-stiffness components based on magnetorheological elastomers [C]// Proceedings of the SPIE. Newport Beach, 2000, 3985: 418-425.
[11] DENG H X, GONG X L, WANG L H. Development of an adaptive tuned vibration absorber with magnetorheological elastomer [J]. Smart Materials and Structures, 2006, 15(5): N111-N116.
[12] DENG H X, GONG X L. Application of magnetorheological elastomer to vibration absorber [J]. Communications in Nonlinear Science and Numerical Simulation, 2008, 13(9): 1938-1947.
[13] COLLETTE C, KROLL G, SAIVE G, GUILLEMIER V, AVRAAM M, PREUMONT A. Isolation and damping properties of magnetorheologic elastomers [J]. Journal of Physics: Conference Series, 2009, 149: 1-4.
[14] GONG X L, ZHANG X Z, ZHANG P Q. Fabrication and characterization of isotropic magnetorheological elastomers [J]. Polymer Testing, 2005, 24: 669-676.
[15] KOO J H, AHMADIAN M. Qualitative analysis of magneto- rheological tuned vibration absorbers: experimental approach [J]. Journal of Intelligent Material Systems and Structures, 2007, 18: 1137-1143.
(Edited by CHEN Can-hua)
Foundation item: Projects(60804018, 50830202) supported by the National Natural Science Foundation of China; Project (20070420719) supported by the Post doctoral Fund of China; Project(CSTC.2008BB6184) supported by Chongqing Natural Science Foundation, China
Corresponding author: DONG Xiao-min; Tel: +86-23-60607468; E-mail: xmdong@cqu.edu.cn