
Deduction of plastic work rate per unit volume for
unified yield criterion and its application
ZHAO De-wen(赵德文), LI Jing(李 婧), LIU Xiang-hua(刘相华), WANG Guo-dong(王国栋)
State Key Laboratory of Rolling and Automation, Northeastern University, Shenyang 110004, China
Received 30 October 2008; accepted 20 February 2009
Abstract: A unified linear expression of plastic work rate per unit volume is deduced from the unified linear yield criterion and the associated flow rule. The expression is suitable for various linear yield loci in the error triangle between Tresca’s and twin shear stress yield loci on the π-plane. It exhibits generalization in which the different value of criterion parameter b corresponds to a specific linear formula of plastic work rate per unit volume. Finally, with the unified linear expression of plastic work rate and upper-bound parallel velocity field the strip forging without bulge is successfully analyzed and an analytical result is also obtained. The comparison with traditional solutions shows that when b=1/(1+
) the result is the same as the upper bound result by Mises’ yield criterion, and it also is identical to that by slab method with m=1, σ0=0.
Key words: π-plane; flow rule; unified linear plastic work rate; deduction; application
1 Introduction
Nowadays, the studies on metal forming are most of numerical analysis, such as FEM[1-4] and UBEM[5]. However, almost no theoretical analytical solution can be obtained without simplifying the Mises’ yield criterion because of its non-linearity. In recent years, one concern regarding linearization of yield criteria has been put forward and become much more extensive. In 1983, YU[6] proposed a linear twin shear stress yield criterion, called TSS criterion for short. HUANG and ZENG[7] deduced its plastic work rate per unit volume in 1989. The works of YU gave us much interesting to apply his criterion in metal forming. However, it showed a greater calculated result than that by Mises’ yield criterion[8-9].
By notice of non-linearity of Mises’ criterion, YU [10] proposed a unified linear yield criterion, called UY criterion, in which yield criterion parameter b represents the effect of the intermediate principal shear stress on the yield of materials and 0≤b≤1. The UY criterion is not a single yield criterion but a series of continuously variable linear yield criteria. Therefore, its application will play significant role in metal forming, and the plastic work rate per unit volume must be the key procedure.
This work is to deduce the linear plastic work rate per unit volume by UY criterion firstly and then apply it in strip forging, and compare its calculated results with traditional solutions.
2 Derivation of plastic work rate
The UY criterion is usually presented by
(1)
where b is the yield criterion parameter, σ1, σ2 and σ3 are principal stresses.
Assuming the stress tensor satisfies f(σij)=0, then Levy-Mises’ flow rule[11] gives
(2)
From Eq.(2) and the first formula in Eq.(1), there is

From Eq.(2) and the second formula in Eq.(1), there is

Because λ≥0, μ≥0, taking linear combination of above two formulas yields

Since magnitudes of λ and μ are arbitrary, taking
μ/(1+b)+λ, it yields
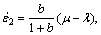
(3)
Among them, 
thus


so,
(4)
Taking note of Eq.(3) and σ2=(σ1+σ3)/2 at the point E, as shown in Fig.1, plastic work rate per unit volume is


so,
(5)
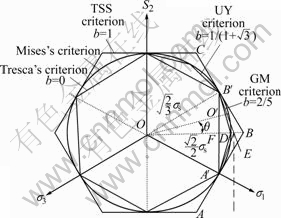
Fig.1 Yield loci in π-plane
Simultaneously solving formulas in Eq.(1) as angular point E yields
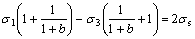
Then,
0≤b≤1 (6)
Substituting Eqs.(6) and (4) into Eq.(5), the plastic work rate done per unit volume for UY criterion is derived by
(7)
3 Generalization of Eq.(7)
Substituting b=1 into Eq.(7) yields the specific plastic work rate per unit volume for TSS criterion as follows:
(8)
Substituting b=0 into Eq.(7), the specific plastic work rate per unit volume for Tresca’s criterion is
(9)
Substituting b=2/5=0.4 into Eq.(7), the specific plastic work rate for geometric midline(GM) criterion [12] also results in
(10)
In the same way, substituting b=1/3 and b=0.529 into Eq.(7) yields the single plastic work rate for mean yield (MY) criterion[13] and equi-area(EA) criterion[11]. They are respectively
(11)
(12)
Above deduction shows generalization of Eq.(7). It is not a single plastic work rate per unit volume, but a series of linear plastic work rate expressions corresponding to different specific yield criteria with b values from 0 to 1. So, it can be called unified or generalized linear plastic work rate per unit volume.
4 Representation on π-plane
The projection of the principal stress components on the π-plane[14] is shown in Fig.2, where
(13)
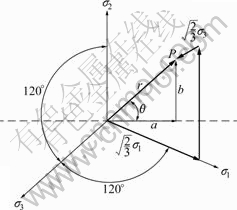
Fig.2 Polar coordinates of point P on π-plane
and
is lode stress parameter[14].
As shown in Fig.1, θ is also the included angle
between any linear yield locus (hypotenuse B′E) with Tresca’s locus (right angled side B′F) in error triangle FB′B on π-plane. As shown in Fig.3, sides of the angle
are perpendicular to those of θ=π/6, B′F=
for
any θ in the triangle FB′B:
(14)
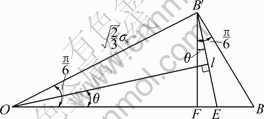
Fig.3 Linear locus and polar angle on 30? sector on π-plane
Eq.(14) shows that the presentation of UY linear criterion on π-plane is a cluster right lines lying in the error triangle FB′B made of TSS yield locus B′B (hypotenuse) and Tresca’s yield locus B′F (right angled side), which starts from point B′ and aims at different points on FB. As criterion parameter b changes from 0 to 1, the included angle θ is from 0 to π/6 covering all regimes from the lower bound (Tresca’s) to the upper bound (TSS).
5 Application of Eq.(7)
In order to verify practicability and precision of Eq.(7), strip forging without bulge between two parallel platens is taken as an example. As shown in Fig.4. the top platen moves at a velocity, -v0, while the bottom platen moves at a velocity, v0. Assuming that the velocity component vy varies linearly with the y coordinate, the
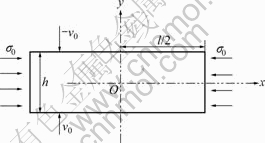
Fig.4 Strip forging without bulge
kinematically admissible velocity and strain rate fields are respectively[15]
(15)
(16)
Above strain rates satisfy
(17)
Substituting Eq.(7) into following and noticing Eq.(17) yield

(18)
From Eq.(15), velocity discontinuity at interface is

Let friction stress is τf=mk=
then
(19)
Noticing Eq.(15), the power to overcome the resistance of external pressure σ0 is
(20)
Summing Eqs.(18), (19) and (20) results in upper bound power:

Let the applied power
then
(21)
Eq.(16) belongs to plane strain, where[16], the parameter
Substituting it into Eq.(21) and taking
then rearranging yields
(22)
It is obviously that Eq.(22) is the same result with upper bound solution deduced by AVITZUR[15] with Mises’ criterion. When m=1, σ0=0, it becomes
(23)
Eq.(23) is also identical to that of strip forging solved by Slab method[17] with sticking friction without resistance of external pressure.
According to the universality of Eq.(7), we can also get specific linear plastic work rate per unit volume for plane stain by substitute parameter
[16] into Eq.(7):
(24)
Eq.(24) is specific linear plastic work rate per unit volume with
. For plane strain, it is the same with plastic work rate per unit volume by Mises’ criterion, because the yield locus corresponding to Eq.(24) is a inscribed dodecagon, with its apex just lying on Mises’ yield locus[16], as shown in Fig.1. Therefore, integrating Eq.(24) yields directly also the result of Eq.(22). For other plane strain deformations, integrating Eq.(24) to get internal deformation power is also recommended.
6 Conclusions
1) The unified linear plastic work rate done per unit volume is first deduced for the UY criterion. It corresponds to various specific linear criteria according to suitable b values.
2) The representation of UY yield criterion on the π-plane is a cluster right lines lying in the error triangle, which includes different angles with Tresca’s yield locus and passes apex of Tresca’s hexagon.
3) With the parallel velocity field, the unified linear plastic work rate per unit volume is first applied to analysis of strip forging and an analytical solution of average pressure is obtained.
4) For plane strain, taking
for Eq.(21) or integrating Eq.(24) all yields the same upper bound solution with that by Mises’ criterion. When m=1, σ0=0, it is the same with solution by Slab method.
References
[1] PITTMAN J F T. Numerical analysis of forming processes [M]. New York: John Wiley & Sons, 1984.
[2] WANG Guang-chun, ZHAO Guo-qun, XIA Shi-sheng, LUAN Yi-guo. Numerical and experimental study on new precision forging technique of super gears [J]. Trans Nonferrous Met Soc China, 2003, 13(4): 798-802.
[3] YANG H, ZHAN M, LIU Y L, XIAN F J, SUN Z C, LIN Y, ZHANG X G. Some advanced plastic processing technologies and their numerical simulation [J]. J Mater Processing Tech, 2004, 151(1): 63-69.
[4] HARTLEY P, PILLINGER I. Numerical simulation of the forging process [J]. Computer Methods in Applied Mechanics and Engineering, 2006, 195: 6676-6690.
[5] ALFOZAN A, GUNASEKERA J S. An upper bound element technique approach to the process design of axisymmetric forging by forward and backward simulation [J]. J Mater Processing Tech, 2003, 142(3): 619-627.
[6] YU Mao-hong. Twin shear stress yield criterion [J]. Int J Mech Sci, 1983, 25(1): 71-79.
[7] HUANG Wen-bin, ZENG Guo-ping. Application of twin shear stress yield criterion to solve some problems in plastic mechanics [J]. Acta Mechanica Sinica, 1989, 21(2): 249-256. (in Chinese)
[8] ZHAO De-wen, XU Jian-zong, YANG Hong. Application of twin shear stress yield criterion in axisymmetrical indentation of a semi-infinite medium [C]// Proceedings of International Symposium on Strength Theory. Beijing: Science Press, 1998: 1079-1084.
[9] ZHAO D W, XIE Y, LIU X H WANG G D. Three dimensional analysis of rolling by twin shear stress yielding criterion [J]. J Iron & Steel Res Int, 2006, 13(6): 21-26.
[10] YU Mao-hong, HE Li-nan, LIU Chun-yang. Generalized twin-shear stress yield criterion and its generalization [J]. Chinese Science Bulletin, 1992, 37(24): 2085-2089.
[11] ZHAO De-wen, WANG Xiao-wen, LIU Xiang-hua, WANG Guo-dong. A dodecagon linear yield criterion with optimal approximation to Mises criterion [C]// Proceedings of the 2nd International Conference on New Development in Rock Mechanics & Rock Engineering. Princeton: Rinton Press Inc, 2002: 554-558.
[12] ZHAO De-wen, XIE Ying-jie, LIU Xiong-hua WANG Guo-dong. New yield criterion based on geometric midline of error triangles between Tresca and twin shear stress yield loci [J]. Journal of Northeastern University: Natural Science, 2004, 25(2): 121-124. (in Chinese)
[13] ZHAO De-wen, XIE Ying-jie, WANG Xiao-wen, LIU Xiang-hua. Derivation of plastic work rate done per unit volume for mean yield criterion and its application [J]. J Mater Sci Technol, 2005, 21(4): 433-438.
[14] SLATER R A C. Engineering plasticity theory and application to metal forming processes [M]. London: The MaCMILLAN Press Ltd, 1977.
[15] AVITZUR B. Metal forming: Processes and analysis [M]. New York: McGRAW-HILL Inc, 1968.
[16] YU Mao-hong. Unified strength theory and its applications [M]. Berlin: Springer-Verlag, 2004.
[17] HOSFORD W F. Metal forming mechanics and metallurgy [M]. Englewood Cliffs: Prentice-Hall Inc, 1983.
Foundation item: Project(50474015) supported by the National Natural Science Foundation of China; Project(RAL–SD-2008-2) supported by RAL Self-determination Science Foundation
Corresponding author: ZHAO De-wen; Tel: +86-24-83686423; E-mail: cral@mail.neu.edu.cn
DOI: 10.1016/S1003-6326(08)60329-5
(Edited by YANG Hua)