
Influence of homogenizing on mechanical properties of as-cast AZ31 magnesium alloy
ZHANG Bao-hong(张宝红)1, ZHANG Zhi-min(张治民)2
1. School of Materials Science and Engineering, North University of China, Taiyuan 030051, China;
2. Engineering Technology Research Center for Integrated Precision Forming of Shanxi Province,North University of China, Taiyuan 030051, China
Received 23 September 2009; accepted 30 January 2010
Abstract: Forward extrusion experiments of as-cast AZ31 magnesium alloy were conducted at different temperatures and different extrusion ratios using the as-cast billets with and without homogenizing treatment. The mechanical properties of pre- and post-extrusion of the two kinds of billets were investigated. Experimental results show that the mechanical properties of post-extrusion of the two kinds of billets all are obviously improved compared with those of pre-extrusion. The elongation of post-extrusion using the billet with homogenizing is higher than that without homogenizing, but the tensile strength is lower than that without homogenizing. When the extrusion ratio increases, the elongation and tensile strength of post-extrusion of two kinds of billets all will increase obviously. When the extrusion temperature of billet without homogenizing increases, the tensile strength of post-extrusion will decrease obviously and the elongation of post-extrusion will change to a small extent. For the billet with homogenizing, the tensile strength of post-extrusion will decrease in some sort when extrusion temperature increases.
Key words: as-cast AZ31 magnesium alloy; forward extrusion; tensile strength; elongation; homogenizing treatment; microstructure
1 Introduction
Magnesium alloys have the merits of light weight, high specific strength and shock resistance, strong thermo-conductivity and electromagnetic shielding, being easy to recycle, and have been regarded as “the green material” with the greatest application potential in the 21st century[1-3]. In aerospace, electronics fields and particularly in automobile industry, magnesium alloys have found their wide usage.
Today, magnesium parts are commonly made by casting processes. But the mechanical properties of these parts are not sufficient for the use in safety relevant applications. Plastic deformation can obviously improve the mechanical properties of magnesium compared with casting[4-9]. However, magnesium alloys exhibit poor ductility at room temperature because of limited availability of slip systems in hexagonal crystal structure, and plastic deformation is difficult to them, which restricts the application of magnesium alloys[10-12]. Therefore, research of plastic deformation on magnesium has great significance for the wider use of magnesium alloy products.
Plastic deformation for casting blank to fabricate components is an advanced technology. The feature of this technology synthesizes the advantages of casting and plastic deformation together, which can achieve the dual goal of forming and improving the properties at the same time[13-16]. In this work, the influence of homogenizing on mechanical properties of post- extrusion of as-cast AZ31 magnesium alloy is studied, which can provide an experimental basis for the ulterior developing of the plastic forming technology of as-cast magnesium.
2 Experimental
In this work, casting rods of AZ31B magnesium alloy were used as the experimental materials and the chemical compositions are shown in Table 1. In order to study the effect of homogenizing of billet before extrusion on mechanical properties of post-extrusion, the casting rods were divided into two groups. A group was directly machined into the billets for extrusion and no heat treatment was done. The another group was firstly treated by homogenizing, which was heated to 400 ℃ and held at this temperature for 16 h, then was machined into the billets for extrusion. The diameters of machined billet for extrusion were 67, 89 and 106 mm, respectively, and forward extrusion was conducted at 250, 300, 350, 400 and 450 ℃. The extruded workpiece had a diameter of 15 mm. Thus, the extrusion ratios (λ) was 20, 35 and 50 for the billets of three different diameters. The experimental setup is shown in Fig.1. The punch and female die of the experimental setup can be changed according to the diameter of billet. In experiment, the experimental setup was heated to the same temperature as the extrusion temperature of billets. Forward extrusion was conducted in YA32-630 hydraulic press and the speed of slide block was 8 mm/s. The extruded workpiece was cooled in air to room temperature after extrusion. The homogenized and non-homogenized casting rod and extruded workpiece were machined into tension test pieces of 10 mm in diameter and tensile test was conducted in WDW-E100D electronic universal testing machine. The microstructure of homogenized casting rod and extruded workpiece were measured by NEOPHOT21 optical microscope.
Table 1 Composition of AZ31 magnesium alloy (mass fraction, %)
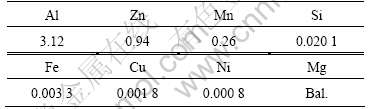
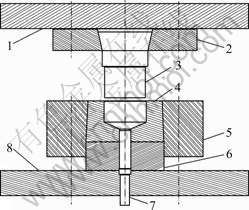
Fig.1 Schematic diagram of extrusion: 1—Upper shoe; 2—Punch holder; 3—Punch; 4—Female die; 5—Die holder; 6— Insert ring; 7—Ejector; 8—Lower die shoe
3 Results and discussion
3.1 Influence of homogenizing on initial billet
Table 2 shows the mechanical properties of casting rods before and after homogenizing. It can be seen from Table 2, tensile strength decreases and plasticity obviously increases for as-cast AZ31 magnesium alloy after homogenizing treatment. Fig.2 shows the microstructures of as-cast AZ31 magnesium alloys before and after homogenizing. It can be seen from Fig.2, the average grain size is about 50 ?m for the as-cast AZ31 magnesium alloy before homogenizing. There is coarse phase at the border of grain and there is also a small quantity of second-phase Mg17Al12 between grain boundary and dendritic crystal. After homogenizing treatment, the grain size increases slightly. The quantity of dendritic crystal decreases obviously and it is nearly disappeared. There is still a small quantity of second-phase Mg17Al12 between grain boundary and dendritic crystal. The second-phase Mg17Al12 has turned
Table 2 Mechanical properties of casting rods before and after homogenizing
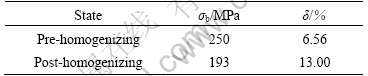
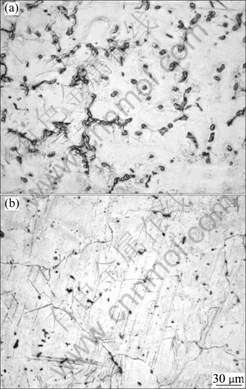
Fig.2 Microstructures of as-cast AZ31 magnesium alloys before (a) and after (b) homogenizing
into small grain from the shape of coarse skeleton, and it is evenly distributed in the α-Mg matrix. The distribution of ingredient of matrix is more even than pre- homogenizing. This shows that, because of the dissolution of non-equilibrium phase, the collection of residual phase and the spheroidization after the homogenizing treatment, which meliorate the inhomogeneity of chemical composition and microstructure and eliminate the coring segregation and internal stress, so the plasticity at room temperature and processing property of cold and hot deformation are improved. Consequently, homogenizing treatment can decrease the possibility of crack when as-cast magnesium is processed by plastic deformation. The erosion resistance can be improved with the elimination of inhomogeneity of chemical composition of cast ingot.
3.2 Influence of extrusion temperature on extruded workpiece
Fig.3 shows curves of tensile strength of as-extruded AZ31 by the billets with homogenizing and without homogenizing when extrusion temperature is different. It can be seen from Fig.3, when the extrusion temperature increases, the tensile strength of as-extruded AZ31 will fall at first, then rise, and fall again, and it has peaks respectively at 250 ℃ and 350 ℃. On the whole, the tensile strength of as-extruded AZ31 will fall when the extrusion temperature increases. When extrusion ratio is 20, extrusion temperature is 250 ℃ and the billet is not treated by homogenizing, the as-extruded AZ31 has the highest tensile strength and the value is 370 MPa. When the billet is not treated by homogenizing, the tensile strength of as-extruded AZ31 will obviously decrease with increasing extrusion temperature. When the billet is treated by homogenizing, the tensile strength of as-extruded AZ31 will decrease in some sort with increasing extrusion temperature.
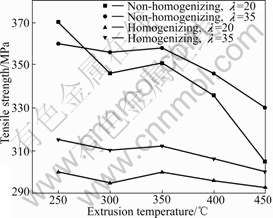
Fig.3 Tensile strength of as-extruded AZ31 vs extrusion temperature
Fig.4 shows curves of elongation of as-extruded AZ31 by the billets with and without homogenizing when extrusion temperature is different. It can be seen from Fig.4, the elongation of as-extruded AZ31 by the billet without homogenizing changes in a small range and it is not regular. However, the elongation of as-extruded AZ31 by the billet with homogenizing is higher than that without homogenizing. But it has downtrend when extrusion temperature increases. Grain growth is the reason causing this phenomenon. It also can be seen from Fig.4, when extrusion ratio is 35 and extrusion temperature is 250 ℃, the elongation of as-extruded AZ31 by the billet with homogenizing comes up to 25%. This shows that, at the combined role of low extrusion temperature and large extrusion ratio, the toughness of magnesium can be effectively improved.
3.3 Influence of extrusion ratio on extruded work- piece
Fig.5 shows the mechanical properties of as-extruded AZ31 by homogenized billets at extrusion
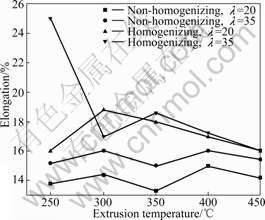
Fig.4 Elongation of as-extruded AZ31 vs extrusion temperature
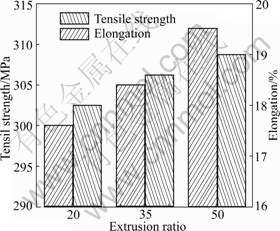
Fig.5 Mechanical properties of as-extruded AZ31 by homogenized billets at extrusion temperature of 350 ℃
temperature of 350 ℃ with different extrusion ratios. It can be seen from Fig.5, when extrusion ratio increases, the elongation and tensile strength of as-extruded AZ31 by the billet with homogenizing will obviously increase. It can be seen from Figs.3-5, when extrusion ratio increases, both the tensile strength and elongation of post-extrusion will obviously increase no matter the billet has been treated by homogenizing or not.
Fig.6 shows the microstructures of as-extruded AZ31 by homogenized billets at extrusion temperature of 350 ℃ with different extrusion ratios. It can be seen from Fig.6, when the extrusion ratio is 20, grains are relatively coarse and the average grain size is 4 ?m; when the ratio is 35, grains are refined, but part of them are not refined, thus the grains are uneven; when the ratio is 50, grains are more refined, and moreover, the distribution of grains is uniform. This shows that the fine grain can improve the tensile strength and the elongation at the same time. Therefore, the effective method improving the mechanical properties of AZ31 magnesium

Fig.6 Microstructures of as-extruded AZ31 by homogenized billets at extrusion temperature of 350 ℃ with extrusion ratio of 20 (a), 35 (b) and 50 (c)
alloy is increasing the extrusion ratio. In other words, increasing the plastic deformation extent can effectively improve the the mechanical properties of AZ31 magnesium alloy.
4 Conclusions
1) Elongation will increase and tensile strength will decrease when the as-cast AZ31magnesium alloy is treated by homogenizing.
2) No matter the billets have been treated by homogenizing or not, the mechanical properties of post-extrusion are obviously improved by comparing with pre-extrusion.
3) The elongation of post-extrusion by the billet with homogenizing is higher than that without homogenizing, but the tensile strength is lower than that without homogenizing.
4) When extrusion ratio increases, both the tensile strength and elongation of post-extrusion will obviously increase no matter the billet has been treated by homogenizing or not.
5) When extrusion temperature of billet without homogenizing increases, the tensile strength of post-extrusion will decrease obviously and the elongation of post-extrusion will change to a small extent.
6) For the billet with homogenizing, the tensile strength of post-extrusion will decrease in some sort when the extrusion temperature increases. The elongation of post-extrusion will decrease obviously when the extrusion temperature is higher than 350 ℃.
References
[1] ZHANG Tong-jun, LI Guo-xing. Applications of magnesium alloys and progress of metallic magnesium industry in China [J]. Materials Review, 2002, 16(7): 11-13. (in Chinese)
[2] ZI Bing-tao, WANG Hui. Magnesium alloy and its applications in industry [J].Chinese Journal of Rare Metals, 2004, 28(1): 229-232. (in Chinese)
[3] POLMER I J. Magnesium alloys and applications [J]. Materials Science and Technology, 1994, 10(1): 1-16.
[4] MORDIKE B L, EBERT T. Magnesium properties-applications- potential [J]. Materials Science and Engineering A, 2001, 302(1): 37-45.
[5] ZHANG Kui, LI Xin-gang, LI Yong-jun, MA Ming-long. Effect of Gd content on microstructure and mechanical properties of Mg-Y-RE-Zr alloys [J].Transactions of Nonferrous Metals Society of China, 2008, 18(s1): s12-s16.
[6] YAMASHITA A, HORITA Z, LANGDON T G. Improving the mechanical properties of magnesium and a magnesium alloy through severe plastic deformation [J].Materials Science and Engineering A, 2001, 300(1/2): 142-147.
[7] MUELLER K, MUELLER S. Severe plastic deformation of the magnesium alloy AZ31 [J]. Journal of Materials Processing Technology, 2007(187/188): 775-779.
[8] BEHRENS B A, SCHMIDT I. Improving the properties of forged magnesium parts by optimized process parameters [J]. Journal of Materials Processing Technology, 2007(187/188): 761-765.
[9] DOBRZANSKI L A, TANSKI T, CIZEK L, BRYTAN Z. Structure and properties of magnesium cast alloys [J]. Journal of Materials Processing Technology, 2007(192/193): 567-574.
[10] DECKER R F. The resistance in magnesium [J]. Advanced Materials & Processes, 1998, 154(3): 31-33.
[11] OGAWA N, SHIOMI M, OSAKADA K. Forming limit of magnesium alloy at elevated temperatures for precision forging [J]. International Journal of Machine Tools & Manufacture, 2002, 42(5): 607-614.
[12] JI Y H, PARK J J. Incremental forming of free surface with magnesium alloy AZ31 sheet at warm temperatures [J]. Transactions of Nonferrous Metals Society of China, 2008, 18(s1): s165-s169.
[13] JIANG Peng, HE Xiao-mao, WU Ying, XIE Hua. New compound plastic forming technologies and their applications [J].Forging & Stamping Technology, 2000(1): 38-41. (in Chinese)
[14] ZHANG Bao-hong, ZHANG Xing, WANG Qiang, ZHANG Zhi-min, LI Bao-cheng. Influence of plastic deformation on microstructure and mechanical properties of as-cast AZ31 magnesium alloy [J]. Journal of Materials Engineering, 2005(5): 45-47. (in Chinese)
[15] WANG S I, SEO M K, CHO J R, BAE W B. A study on the development of large aluminum flange using the casting/forging process [J]. Journal of Materials Processing Technology, 2002(130/131): 294-298.
[16] ZHANG Bao-hong, ZHANG Zhi-min, WANG Xiang-dong, WANG Qiang. Influence of forward extrusion on microstructure and mechanical properties of as-cast AZ31B magnesium alloy [J]. Steel Research International, 2008, 79(s1): 699-703.
(Edited by YANG Hua)
Foundation item: Projects(50605059, 50735005) supported by the National Natural Science Foundation of China; Project(2009081012) supported by International Cooperation of Shanxi Province, China; Project(20090319ZX) supported by Program for the Top Young Academic Leaders of Higher Learning Institutions of Shanxi Province, China
Corresponding author: ZHANG Bao-hong; Tel: +86-351-3921778; Fax: +86-351-3921398; E-mail: zhangbh@nuc.edu.cn