
Influence of graphite content on sliding wear characteristics of
CNTs-Ag-G electrical contact materials
WANG Juan(王 娟), FENG Yi(凤 仪), LI Shu (李 庶), LIN Shen(林 森)
Department of Materials Science and Engineering, Hefei University of Technology, Hefei 230009, China
Received 9 January 2008; accepted 31 July 2008
Abstract: CNTs-Ag-G electrical contact composite material was prepared by means of powder metallurgical method. The influence of the graphite content on sliding wear characteristics of electrical contact levels was examined. In experiments, CNTs content was retained as 1% (mass fraction), and graphite was added at content levels of 8%, 10%, 13%, 15% and 18%, respectively. The results indicate that with the increase of graphite content, the contact resistance of electrical contacts is enhanced to a certain level then remains constant. Friction coefficient decreases gradually with the increase of graphite content. Wear mass loss decreases to the minimum value then increases. With the small content of graphite, the adhesive wear is hindered, which leads to the decrease of wear mass loss, while excessive graphite brings much more worn debris, resulting in the increase of mass loss. It is concluded that wear mass loss reaches the minimum value when the graphite mass fraction is about 13%. Compared with conventional Ag-G contact material, the wear mass loss of CNTs-Ag-G composite is much less due to the obvious increase of hardness and electrical conductivity, decline of friction surface temperature and inhibition of adhesive wear between composites and slip rings.
Key words: CNTs-Ag-G electrical contact material; graphite; contact resistance; friction coefficient; wear mass loss
1 Introduction
Sliding contacts as essential parts of the electrical circuits are used to transmit electric power and signal between moving and stationary parts of motor[1-3]. This type of contact has been well known for many years. However, they are still important in various applications, for example, commutator brush of dc motors, sliding contact systems of ac generators. In this kind of application, a number of factors have to be considered to keep the efficiency of the motor, such as high wear resistance of both brush and rotor materials, and good electric and thermal conductivity, even after prolonging serving time[4-7].
Many kinds of sliding contact materials have been used in severe condition. Recently, among novel materials, Ag and its alloys are often chosen because of significant electric conductivity and oxidative stability.
In conventional Ag-G electrical contact material, with the increase of graphite content, its lubricating property and wear-resisting property are improved, but electrical conductivity, thermal conductivity and strength decline. However, with the increase of silver contents, the electrical conductivity and thermal conductivity are improved, but lubricating and wear-resisting property decline[8-11].
In most cases, the development of new brush materials is accomplished by empirical selection of the composition of composites that can resist to wear and have the required electrical characteristics.
In this work, the effects of the graphite content on the tribological properties of the composites are examined to provide essential information about the interrelation between the graphite content and tribological behavior of electrical contact materials.
2 Experimental
Due to large ratio of length to diameter and van der Walls attraction, the initial nanotubes showed in twist and cluster[12-15]. In order to increase the surface roughness so as to improve the interfacial strength and the dispersion, carbon nanotubes were subjected to an oxidation treatment in the mixture of nitric acid and sulphuric acid. The oxidation made carbon nanotubes short and improved their dispersion[16-17].
Composites were fabricated by means of powder metallurgy method. The silver powder, natural flake graphite and nanotubes were homogeneously mixed by hand grinding using a agate pestle and mortar for 30 min and the mixture was uniaxially pressed in steel dies under a pressure of 200 MPa for 5 min and then isothermally sintered for 1 h in H2 atmosphere at 700 ℃ to form CNTs-Ag-G composites. Composites were finally repressed at 400 MPa. The specimens were 24 mm long, 12.5 mm thick and 20 mm high[18]. Morphology of composite material is shown in Fig.1. The graphite distributed in matrix uniformly, which guaranteed the good self-lubricating property of brush.
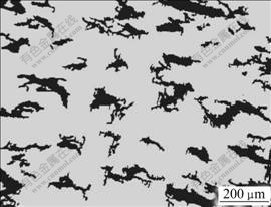
Fig.1 Microstructure of CNTs-Ag-G composite material
The friction and wear tests were conducted using a ring-brush wear test machine (Fig.2). The rings used in the experiment were made of Cu-5%Ag alloy and had a diameter of 320 mm and a width of 60 mm. The hardness of rings was HB105.
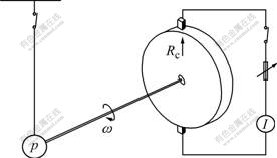
Fig.2 Schematic diagram of wear tester
The worn surface of the tested samples was observed using scanning electron microscope. The composition of the lubricating film was analyzed by X-ray photoelectron spectroscopy. In this series of tests, the sliding velocity of ring was 10 m/s, the normal loads were 2.5 N/cm2 and the total sliding time was 30 h.
3 Results and discussion
3.1 Contact resistance
Fig.3 presents the influence of graphite content on the contact resistance of positive and negative brush, respectively. From Fig.3, we can see that both contact resistances increase to a certain level then remain constant with the increase of graphite content.
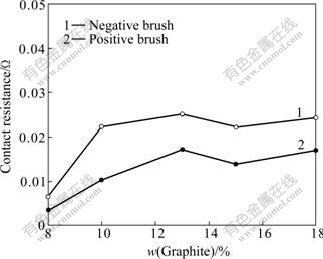
Fig.3 Influence of graphite content on contact resistances
Since all solid surfaces are rough on the microscale, real contact area between ring and brush is only a small fraction of the apparent contact area, known as “α- spots”. When electrical current passes through contact spots, it is distorted and constricted, resulting in constriction resistance[19-20].
It is concluded that the formation of a thin, uniform and continuous film at the interface is basically needed. Formation of lubricating film is related not only with the material of brush and ring, their surface conditions and working environment, but also with a series of physical and chemical reactions[21].
The contact resistance Rc during electrical wear is the sum of constriction resistance Rs and resistance of lubricating film Rf[22]:
(1)
where ρ is the electrical resistivity of composites, p is experimental press, n is the number of contact spots, H is Brinell hardness of material, σ is the resistance of unit area of the film, and α is the contact spot radius.
From Table 1, we find that, the electrical resistivity of composite material increases but its Brinell hardness decreases with the increase of graphite contents. For simplicity, in the evaluation of constriction resistance, only ρ and H are assumed as variances. It is calculated that the constriction resistance values are approximately equivalent and the resistance of lubricating film is responsible for the variation of contact resistance with the increase of graphite content.
Table 1 Brinell hardness and electrical resistivity of composite materials
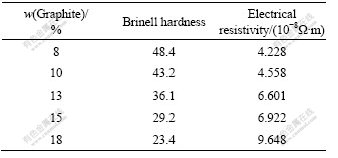
Fig.4 shows the morphologies of lubricating films of composites with different graphite contents (8% and 18%). The coverage area of lubricating film increases with the increase of graphite content. With small amount of graphite, material cannot provide enough graphite to form lubricating film, and the film layer is discontinuous and easy to be removed from interface, thus the resistance of lubricating film is low. As the graphite content increases, lubricating film becomes thicker and more continuous, which makes the resistance of lubricating film increased simultaneously. Due to the grinding function of carbon nanotubes(CNTs), lubricating film is prevented from further thickening, but in a state of dynamic equilibrium. It is shown that the resistance of lubricating film increases to a certain level then remains constant.
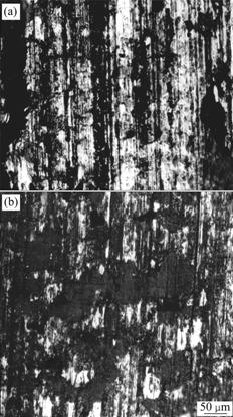
Fig.4 Morphologies of lubricating film with different graphite contents: (a) 8%; (b) 18%
3.2 Friction coefficient
Fig.5 shows the dependence of friction coefficient on graphite content with and without current. From Fig.5 we can see that the friction coefficient decreases gradually with the increase of graphite content. It is suggested that graphite improves the friction properties of composite materials.
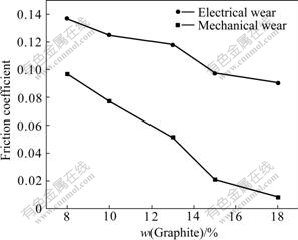
Fig.5 Influence of graphite content on friction coefficient
During friction and wear process, graphite debris accumulates and gradually spreads out of the contact interface, forming a layer of lubricating film. This film changes the nature of contact from metal-metal to metal- lubricating film-metal and thus results in low friction coefficient. As for composites with a low graphite content (e.g. 8%), it is very difficult to form the lubricating film, thus high probability of adhesion between the matrix materials and the ring is resulted. With the increase of graphite content in composites, more continuous lubricating film is formed, therefore the friction coefficient becomes lower.
XPS results (Fig.6) show that the carbon contents in lubricating film is about 63.24% and 95.68%, respectively, far more than the graphite content in composites (8% and 18%). Graphite has good self- lubricating properties due to its special crystal structure[23]. During wear process, superficial graphite in composites is stripped and milled into debris under friction and forces. The graphite debris spreads out and enriches at the interface between the ring and brush, forming lubricating film, which improves lubricating property and decreases the friction coefficient of composites.
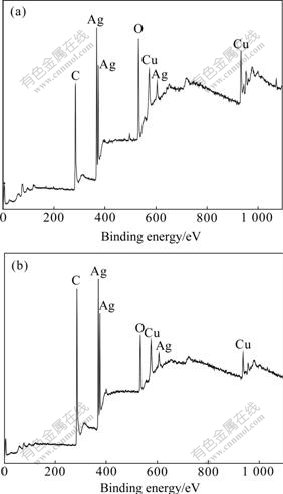
Fig.6 XPS patterns on lubricating film of composites: (a) CNT- Ag-18%G; (b) CNT-Ag-8%G
From Fig.5, we can also see that friction coefficient of composites with current is greater than that without current. This is attributed to the difference of power loss in two wear processes.
The total power loss is the sum of mechanical loss Wm and electrical loss We:
Wm=μ?p?v (2)
We=J2?Rc (3)
where μ is friction coefficient of brush, p is contact press, v is rotating speed of ring, and J is experimental current density.
In electrical wear (with current density of 10 A/cm2), the combined effects of electrical and mechanical losses cause extremely high temperature, damaging the lubricating film partially, making deep wear scars, and finally increasing the roughness of worn surface (shown in Fig.7), which explains the greater value of friction coefficient in electrical wear.
3.3 Wear mass loss
Fig.8 presents the influence of graphite contents on wear mass loss of composites with and without current, respectively. The wear mass loss decreases to the minimum value then enhances with the increase of graphite content.
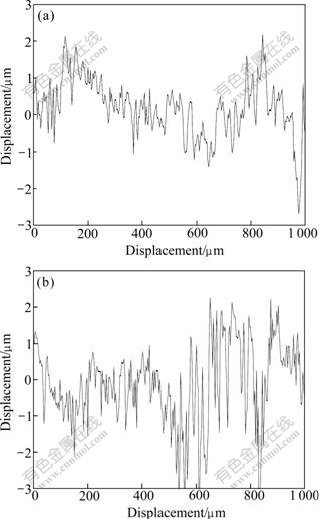
Fig.7 Outline of worn surface of CNT-Ag-18%G composite: (a) Mechanical wear; (b) Electrical wear
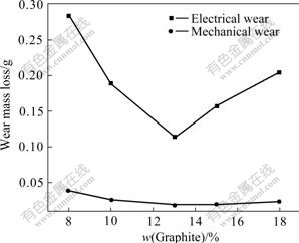
Fig.8 Influence of graphite content on wear mass loss of composite
As for composites with a low graphite content, small amount of graphite is extruded out of brush because of the high hardness (Table 1), thus lubricating film is difficult to form, and scuff and adhesion occur (shown in Fig.9), which hinders the movement between the ring and the brush. Consequently, the wear mass loss becomes high. However, with graphite content increasing in composites, the formation of lubricating film becomes easier and adhesive wear attenuates, which explains the descent of wear mass loss with the increase of graphite content.
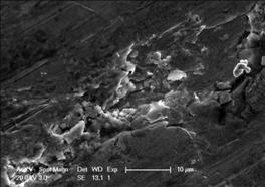
Fig.9 SEM micrograph of worn surface of CNTs-Ag-8%G composite
However, with the further increasing graphite content (more than 13%), brush becomes much softer. During wear process, the hard protruding point of the ring presses into the brush, and the plastic deformation along the sliding direction occurs on the worn surfaces so that the naked graphite comes into being finally. The graphite is milled into fine particles, spreads out at the interface between ring and brush, forming a layer of film which acts as a solid lubricant or becomes constituent of wear loss. As much graphite is added in composites, more debris is generated during experiment, resulting in larger wear mass loss. It is concluded that the wear mass loss reaches the minimum value, when graphite mass fraction is about 13%.
From Fig.8, we can also see that, wear mass loss of composites with current is grater than that without current. Firstly,worn surface becomes rougher, and lubricating film is more difficult to form continuously in electrical wear, thus much wear debris is peeled off under friction force. And Joule heat released on the contact spots is another important factor leading to greater wear mass loss in electrical wear. It makes the lubricating film flaky and discontinuous and easy to be removed.
In electrical wear, the water vapor in atmosphere is decomposed into hydrogen and oxygen under electrolysis effect:
H2O→H++OH- (4)
In electric field, hydroxide radical moves to positive brush and has oxidation reaction with graphite on the surface of positive brush:
4OH--4e→2H2O+O2 (5)
C+O2→CO2 (6)
Thus, the particles of graphite are easily pulled out under friction force because the binding force is weakened among the particles of graphite as well as between graphite particle and silver matrix. As a result, the wear mass loss of electrical wear and its amplitude of variation are higher than those in mechanical wear.
3.4 Comparison of wear performance between 1%CNTs-Ag-13%G and conventional composite Ag-13%G
Table 2 shows the wear performance of Ag-G and 1%CNTs-Ag-G with the same graphite content of 13%. As can be seen in Table 2, the composite of 1%CNTs- Ag-13%G has a 45.7% increase in Brinell hardness, and a 14% decrease in electrical resistivity compared with the conventional composite Ag-G.
Table 2 Wear performances of Ag-13%G and 1%CNTs-Ag- 13%G
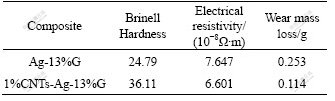
After compacting and sintering, the high strength CNTs fibers with diameter of 30-50 nm can well distribute in composite material. As CNTs have high specific strength and excellent electric conductivity, the hardness and electric conductivity of composite increase significantly.
The wear property of composite added with 1% CNTs is enhanced greatly, and its wear mass loss decreases by 55% compared with Ag-13%G. As for composites without CNTs having lower hardness, local plastic deformation and weld between the micro peaks of Ag in brush and Cu in slip ring easily occur during experiments. These weld joints would be sheared off in the following sliding cycles, thus the hardness of weld joints increases owing to the effect of work hardening. In the following sliding, the fractured joints with very high hardness are easily embedded in the matrix, plow the composite surface and make grooves on it, resulting in very heavy wear mass loss. However, the hardness of composite with 1% CNTs has a significant increase and the CNTs in matrix are definitely the obstacles of embedding and scuffing of weld joints. Also the obvious decrease of electrical resistivity with the addition of CNTs leads to the decline of electrical power loss and the friction surface temperature, as a result, the adhesive wear between composite and slip ring is inhibited and the wear mass loss of 1%CNTs-Ag-13%G is much less than the composite without CNTs.
4 Conclusions
1) The lubricating film is responsible for the variation of contact resistance. Due to the adsorption of graphite and grinding function of CNTs, the film resistance and contact resistance is enhanced to a certain level, then remains constant with the increase of graphite content.
2) With the increase of graphite content in composites, more continuous lubricating film is formed, thus friction coefficient becomes lower. And in electrical wear, the combined effects of electrical and mechanical loss cause the greater value of friction coefficient.
3) The wear mass loss decreases to the minimum value then increases with the increase of graphite content because graphite not only hinders the adhesive wear but also generates large amount of debris. It is concluded that the wear mass loss reaches the minimum value, when graphite mass fraction is about 13%.
4) The addition of CNTs in composite improves the Brinell hardness and electric conductivity greatly, lowers the friction surface temperature, inhibits the adhesive wear during the wear process, as a result, the wear mass loss of composite is much less than that of conventional composite with the same graphite content.
References
[1] PAPATHOMAS K I, KATNANI A D. Oxidative stability of lubricants for dry circuit sliding contacts [J]. Journal of Thermal Analysis and Calorimetry, 1989, 35(1): 153-161.
[2] CHUNG D D L. Electrical applications of carbon materials [J]. Journal of Materials Science, 2004, 39(8): 2645-2661.
[3] YU C C, KEER L M. Edge effect on elastic-plastic rolling/sliding contacts [J]. Computational Machanics, 1996, 18(4): 259-268.
[4] NOVYTSKYY V G, HAVRYLIUK V P, PANASENKO D D. Effect of tin on the wear resistance and secondary structure of cast composites of the Fe-Cr-Cu-Ti-C system under sliding friction [J]. Metal Science and Heat Treatment, 2007, 49(7/8): 346-353.
[5] JUBAULT I, MOLIMARD J, LUBRECHT A A, MANSOT J L, VERGNE P. In situ pressure and film thickness measurements in rolling/sliding lubricated point contacts [J]. Tribology Letters, 2003, 15(4): 421-429.
[6] TAS N R, GUI C, ELWENSPOEK M. Static friction in elastic adhesion contacts in MEMS [J]. Journal of Adhesion Science and Technology, 2003, 17(4): 547-561.
[7] ECCLESTON W. Carbon as an electronics material [J]. Journal of Materials Science: Materials in Electronics, 2006, 17(6): 399-404.
[8] BENABDALLAH H S, BONESS R J. Tribological behaviour and acoustic emissions of alumina, silicon nitride and SAE52100 under dry sliding [J]. Journal of Materials Science, 1999, 34(20): 4995-5004.
[9] SAPOZHNIKOV S A, ASTASHKEVICH B M. Structure and properties of iron piston rings manufactured by continuous cyclic casting [J]. Metal Science and Heat Treatment, 2003, 45(3/4): 91-94.
[10] KURILOV G V, SENTYURIKHINA L N, LYUBARSKII I M, UDOVENKO V F. Mass-spectrometric investigation of solid lubricating coatings subjected to friction in a deep vacuum [J]. Mechanics of Composite Materials, 1970, 6(6): 930-934.
[11] DOLINSKII Y M, ZINOV’EV V V, NOVICHENKO A N. Effect of the composition of the cermet composite silver-nickel-graphite on the operational characteristics of contact material [J]. Powder Metallurgy and Metal Ceramics, 1987, 26(7): 550-553.
[12] BERDINSKY A S, SHAPORIN A V, YOO J B, PARK J H, ALEGAONKAR P S, HAN J H, SON G H. Field enhancement factor for an array of MWNTs in CNT paste [J]. Applied Physics A: Materials Science & Processing, 2006, 83(3): 377-383.
[13] ROSLANIEC Z, BROZA G, SCHULTE K. Nanocomposites based on multiblock polyester elastomers(PEE) and carbon nanotubes (CNT) [J]. Composite Interfaces, 2003, 10(1): 95-102.
[14] RAO L, REDDY N K, COULOMBE S, MEUNIER J L, MUNZ R J. Carbon nanotubes as nanoparticles collector [J]. Journal of Nanoparticle Research, 2007, 9(4): 689-695.
[15] UNGER E, DUESBERG G S, LIEBAU M, GRAHAM A P, SEIDEL R, KREUPL F, HOENLEIN W. Decoration of multi-walled carbon nanotubes with noble- and transition-metal clusters and formation of CNT-CNT networks [J]. Applied Physics A: Materials Science & Processing, 2003, 77(6): 735-738.
[16] FENG Y, YUAN H L. Electroless plating of carbon nanotubes with silver [J]. Journal of Materials Science, 2004, 39(9): 2973-3267.
[17] KAWAKAME M, BRESSANL J D. Study of wear in self-lubricating composites for application in seals of electric motors [J]. Journal of Materials Processing Technology, 2006, 179(1): 74-80.
[18] FENG Y, ZHANG M, XU Y. Effect of the electric current on the friction and wear properties of the CNT-Ag-G composites [J]. Carbon, 2005, 43(13): 2685-2692.
[19] RUBTSOV V E, PSAKH’E S G, KOLUBAEV A V. Study of the formation of contact between rough surfaces based on the particle method [J]. Technical Physics Letters, 1998, 24(3): 178-179.
[20] MURPHY T E, BLASZCZAK J O, MOAZZAMI K, BOWEN W E, PHILLIPS J D. Properties of electrical contacts on bulk and epitaxial n-type ZnO [J]. Journal of Electronic Materials, 2005, 34(4): 389-394.
[21] KONCHITS V V, KIM C K. Electric current passage and interface heating [J]. Wear, 1999, 232(1): 31-40.
[22] HANEY P B, WILSDORF D K, WILSDORF H G F. Production and performance of metal foil brushes [J]. Wear, 1981, 73(2): 261-282.
[23] KAWAKAME M, BRESSAN J D. Study of wear in self-lubricating composites for application in seals of electric motors [J]. Journal of Materials Processing Technology, 2006, 179(1): 74-80.
Foundation item: Project(50271021) supported by the National Natural Science Foundation of China; Project(ZD2008003) supported by Key Science Foundation of the Education Department of Anhui Province, China; Project(CF07-10) supported by the Innovation Center for Postgraduates at HFNL (USTC), China; Project(KF0702) supported by the Open Project Program of Ministry of Education of China; Project supported by Nippon Sheet Glass Foundation of Japan for Materials Science and Engineering
Corresponding author: WANG Juan; Tel: +86-551-2902557; E-mail: wang.juan.1108@163.com
DOI: 10.1016/S1003-6326(08)60237-X
(Edited by YANG Bing)