Trans. Nonferrous Met. Soc. China 22(2012) s764-s768
Ultrasonic-assisted vibration tapping using taps with different coatings
Chung-chen TSAO1, Kei-lin KUO2
1. Tahua University of Science and Technology, Hsinchu 30740;
2. National Taipei University of Technology, Taipei 10608
Received 21 May 2012; accepted 24 September 2012
Abstract: A machine vision for assessing and inspecting the ratio of thread areas associated with fixed frequency (FF) and limited tracing frequency (LTF) ultrasonic-assisted vibration was presented using differently coated taps after tapping of Ti-6Al-4V alloys. Experimental results indicate that TiAlN Micran taps yield the best tapping quality for different coatings and tapping conditions. TiAlN Micran coated taps with LTF make the largest improvement over traditional tapping (TT), with an average increase of 30.2 %.
Key words: tapping; fixed frequency; limited tracing frequency; Ti-6Al-4V alloys
1 Introduction
Increasing demand for advanced materials and better thread quality have stimulated interest in research and the development of new technology for machining. Because of the need for fastening in mechanical structures, conventional tapping still remains one of the most common machining processes for making internal threads in finished structural parts. The tapping process is widely used in the aerospace, automotive and chemical industries.
Titanium alloys have excellent mechanical properties and higher specific strengths than aluminum, magnesium and nickel alloys, so titanium alloys are widely used in the aerospace, automotive, communications, electronics and medical industries. In addition, titanium alloys have low thermal conductivity. Since it is difficult to reduce heat dissipation and titanium alloys have good metal compatibility, the tapping process can produce a built-up edge (BUE). Owing to the low elastic modulus and high chemical activity of titanium alloys, large elastic rebound occurs on the processing surface and the relief face of the tap is prone to the production of severe frictional torque, which can cause small taps to become stuck and break in an internally threaded hole. KUO and TSAO [1] suggested a tracing frequency system to solve this breakage problem in the tapping process.
In industry, machining without the use of cutting fluid is the most efficient way to decrease the need for cooling equipment, reduce production costs, and avoid injuries to operators. Ti-based coatings are used extensively in cutting tools because they have high hardness, low coefficient of friction, corrosion resistance and high adhesive strength [2-5]. Recently, MoS2 and WC/C coatings have attracted increasing interest for various applications, because of their low coefficient of friction and their affinity to alloy materials such as aluminum, titanium and precious metals [6,7]. In some cases productivity and tool life can be increased by 20 [6].
KUMABE [8] found that vibration-assisted cutting reduces cutting force, improves surface quality, and inhibits tool wear. KUMABE and TACHIBANA [9] performed vibration-assisted tapping tests on aluminum, brass and steel, employing frequencies ranging from 59 Hz to 105 Hz. They reported that the torque required for tapping internal threads was considerably reduced with decreases amounting to 1/4 to 2/3 of the conventional tapping torques. In ultrasonic-assisted cutting, the chip and work face are periodically separated, which leads to lower temperature/forces and thereby increases tool life [10]. KUO et al [11] showed that ultrasonic-assisted vibration allowed a reduction in tapping torque of up to 23% at resonance frequency.
Machine vision systems are finding increasing uses in automatic production line applications, such as classification, inspection and process control, to ensure the quality of products and to increase the efficiency of manufacture. SU et al [12] developed an automated machine vision measurement system to inspect the worn-out micro-drills after the drilling of printed circuit boards.
et al [13] utilized computer vision techniques together with classification techniques to estimate the wear levels in cutting inserts in order to ascertain their ideal replacement frequency. Based on the findings of these studies, the use of machine vision for the assessment and inspection of the ratio of thread areas associated with FF and LTF ultrasonic-assisted vibration was examined after the tapping of Ti-6Al-4V alloys using differently coated taps.
2 Experimental
2.1 Experimental set-up
A LEADWELL V30 vertical machining center with a 5.5 kW spindle drive was used in the tapping tests. All tapping tests were conducted without coolant. A vibrator was added under the fixture to provide vibration during the tapping process. In this tracing frequency system, the LabVIEW software program was used to monitor the input signal during tapping of Ti-6Al-4V alloys. A GPIB card transmitted the signal to a digital pulse generator (Tektronix, AFG-310 type). The digital pulse generator then generated the sinusoidal wave required by the vibration head. Finally, a power amplifier (Lapidary & Sonic, LS-600 type) drove the ultrasonic vibration head.
The ultrasonic vibration head and workpiece fixture were integrated into the main unit, and fixed firmly in a vise. During the tapping process, the ultrasonic vibration head vibrates with the workpiece. The natural frequency of the workpiece varies when material is removal and temperature increases. A pure resistance characteristic occurs when resonance takes place in the oscillating circuit, so the resistivity is at a minimum, the current is at a maximum and the output power is at a maximum. To measure the resonance current, an external resistor was used via a NI-PCI-6110S DAQ interface card to send the measured voltage difference to the LabVIEW monitoring program for calculation. After phase compensation, the resonance frequency can be determined. Therefore, automatic adjustment of the vibration frequency of the tapping vibrator can be achieved for the resonance condition. The process flow diagram for the entire tracing frequency system is shown in Fig. 1.
2.2 Differently coated taps and tapping conditions
In order to determine the quality of an internal thread for the tapping processes, three different kinds of coated YAMAWA HSS taps (M3.5×0.6 mm) were investigated in this study. The first was a tap with TiN coating, whilst the other two were taps with TiAlN Micran and TiAlN+WC/C Hardlube coatings. The taps were coated with these various coatings by physical vapor deposition (PVD) using the arc bond sputtering technique. The Ti-6Al-4V workpiece was 10 mm in diameter and 10 mm in length for all tests.
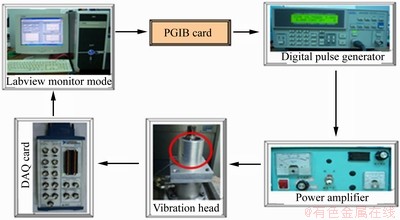
Fig. 1 Process flow diagram for entire tracing frequency system
In general, conventional tapping actions for internal threads can be divided into two types: the first is separation (forward-stop-backward-stop) and the second is stepping (forward-stop-forward-stop). Spiral and crack tapped chips can be obtained by the use of a conventional tapping action with ultrasonic-assisted vibration but repeated separation or stepping is liable to cause small taps to become stuck and break in an internally threaded hole. In order to investigate the effect of FF and LTF ultrasonic-assisted vibration tapping on the quality of the thread area, direct tapping (no backward and stop) was utilized in this study.
During tapping, spindle speed was constant at 70 r/min and the input vibration voltages for ultrasonically assisted tapping were 300, 500 and 700 V, with corresponding amplitudes of 1.37, 2.35 and 3.14 μm, respectively. The input frequencies were 17.0 kHz for fixed frequency (FF) and 17.0-17.3 kHz for limited tracing frequency (LTF). LTF’s tracing frequency range was limited to regular resonance within the 17.0-17.3 kHz range, but the removal of material or the increase of temperature can cause the resonance frequency of the ultrasonic-assisted vibration system to change. FF and LTF ultrasonic-assisted vibration tapping and traditional tapping (TT) (without a deposited coating deposited or ultrasonic-assisted vibration) were compared to investigate their respective effects on the ratio of thread areas. The factors and levels of the experiment for ultrasonic-assisted vibration tapping are shown in Table 1. To maintain precision and accuracy, each set of experiments was repeated three times.
Table 1 Factors and levels of experiment for ultrasonic-assisted vibration tapping
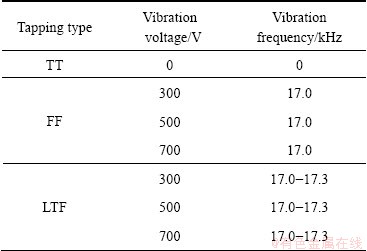
2.3 Calculation of tapped thread area
The quality of the tapped internal thread can affect fastening integrity and life. Machine vision inspection precisely measures thread area and profile and also decreases inspection time and cost compared with conventional manual inspection.
Firstly, the tapped workpieces were cut in half to measure the thread profile and mounted in black-color Bakelite. An image of the tapped thread area was captured on a 10× digital image tool microscope (CURIO VM-99 type). Commercial software (Photo Impact 8.0) was used to extract the image data after tapping to calculate the thread area. Each thread area image was represented by an array of gray scale values (0-255) corresponding to the differences in lamination density. To obtain the processed image, the pixel value of the tapped internal thread zone was set to be 0 (black) because it was less than the threshold value, while the tooth of the internal thread was set to be 255 (white). The proper threshold values were determined by examination of the histogram of array values and verified by comparing the original and binary images. Using the binary images, the tapped internal thread area was calculated. In order to increase the accuracy of the calculation, the reduction in internal thread area was needed. Figure 2 shows the process for the reduced binary image of the tapped internal thread area.
In order to realize the effects on thread area after tapping, the ratio of thread areas (i.e. the ratio of the thread area of different tapping conditions AT to the thread area after manual tapping Am) was calculated to more easily analyze and compare the degree of thread damage after tapping Ti-6Al-4V workpieces. The equation for the ratio of thread areas can be expressed as follows:
(1)
When
approaches 1, the optimal thread quality after tapping was obtained. In this study, the thread area after manual tapping was 13026 pixels.
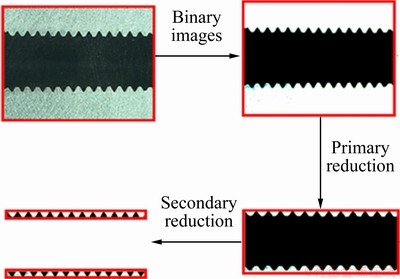
Fig. 2 Process for reduced binary image of tapped internal thread area
3 Results and discussion
3.1 Effects of different ultrasonic-assisted vibration tapping types on ratio of thread areas
The effects of different techniques for ultrasonic-assisted vibration tapping and TT on the ratio of thread areas are shown in Fig. 3. The ratio of thread areas for LTF ultrasonic-assisted vibration tapping is better than that for FF ultrasonic-assisted vibration tapping. In fact, the piezoceramic vibrator is liable to cause drifting of resonance frequencies due to the removal of material, the increase of the temperature or external preloading. LTF ultrasonic-assisted vibration effectively solves the problems associated with resonance frequency drift. Figure 4 shows a comparison of FF (TiN taps) and LTF (TiAlN Micran taps) ultrasonic-assisted vibration tapping using 700 V of voltage in terms of thread profile.
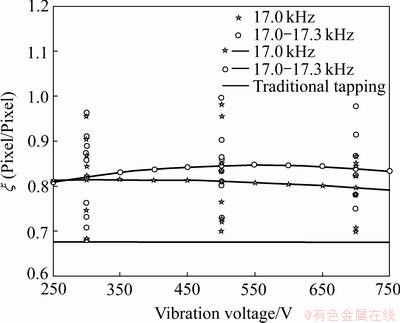
Fig. 3 Effects of different techniques for ultrasonic-assisted vibration tapping and TT on ratio of thread areas
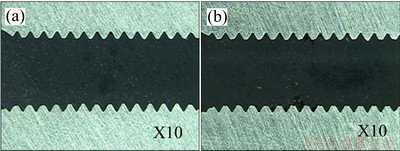
Fig. 4 Comparison of FF (TiN taps) (a) and LTF (TiAlN Micran taps) (b) ultrasonic-assisted vibration tapping using 700 V voltage in terms of thread profile
3.2 Effects of different tap coatings on ratio of thread area
Figures 5 and 6 show the correlation ratios for thread area and vibration voltage for different coated taps for FF and LTF ultrasonic-assisted vibration tapping and TT. From Figs. 5 and 6, it can be seen that the ratio of thread areas for FF and LTF ultrasonic-assisted vibration tapping with different coated taps is larger than that for TT. This is because during ultrasonic-assisted vibration tapping, the chip and work face are periodically separated leading to a reduction in temperature/torque and an increase in the quality of tapping. From Fig. 5, it can be seen that the ratio of thread areas for TiN coated taps increases as vibration voltage increases, until the vibration voltage reaches 500 V, when it decreases as vibration voltage increases. Similar behavior is exhibited by TiAlN Micran taps, as shown in Fig. 5. However, the ratio of thread areas for TiAlN+WC/C Hardlube taps decreases as vibration voltage increases, until the vibration voltage reaches 500 V, when it increases as vibration voltage increases. This is due to the coating thickness of TiAlN+WC/C Hardlube taps.
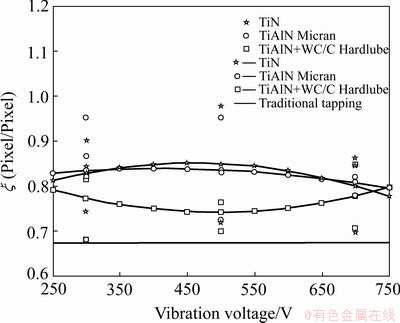
Fig. 5 Correlation ratio for thread area and vibration voltage for differently coated taps for FF ultrasonic-assisted vibration tapping and TT
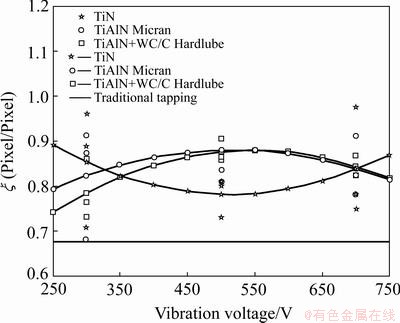
Fig. 6 Correlation ratio for thread area and vibration voltage of different coated taps for LTF ultrasonic-assisted vibration tapping and TT
From Fig. 6, it can be seen that the TiAlN Micran taps have larger values for ratio of thread areas than TiN coated taps and TiAlN+WC/C Hardlube taps. The ratio of thread areas for TiAlN Micran taps increases at first as vibration voltage increases, until the vibration voltage reaches 500 V, when it decreases as vibration voltage increases. Similar behavior is exhibited by TiAlN+WC/C Hardlube taps, as shown in Fig. 6. This is due to the different coefficients of friction for TiN taps, as shown in Fig. 7. Figure 8 shows a comparison of TT and LTF ultrasonic-assisted vibration tapping for TiAlN Micran coating and various voltages in terms of thread profile. The ratio of thread areas for TiN taps decreases as vibration voltage increases, until the vibration voltage reaches 500 V, when it increases as vibration voltage increases.
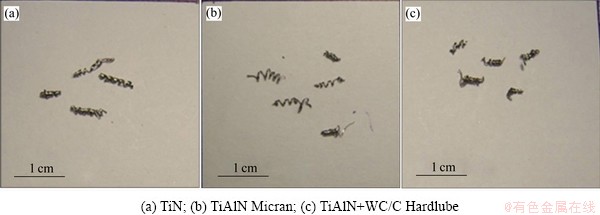
Fig. 7 Comparison of chip morphology for different coated taps using LTF ultrasonic-assisted vibration tapping at input voltage of 700 V
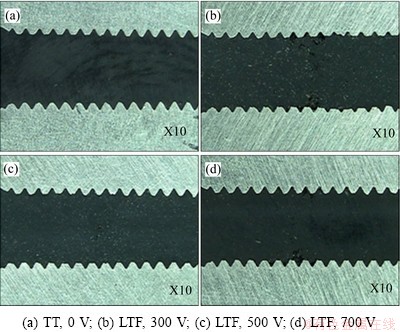
Fig. 8 Comparison of TT and LTF ultrasonic-assisted vibration tapping for TiAlN Micran coating at various voltages in terms of thread profile
4 Conclusions
1) FF and LTF ultrasonic-assisted vibration can substantially improve the tapping quality of the thread area for different tap coatings. FF and LTF type ultrasonic-assisted vibration tapping yield a larger improvement than TT, the ratio of thread areas increases by 20.0% and 25.2%, respectively.
2) FF type ultrasonic-assisted vibration tapping yields an increase in the ratio of thread areas. TiN coated taps give the largest improvement over TT, with an average increase of 26.0%.
3) LTF type ultrasonic-assisted vibration tapping increases the ratio of thread areas. TiAlN Micran coated taps give the largest improvement over TT, with an average increase of 30.2%.
4) TiAlN Micran taps demonstrate superior tapping quality with FF and LTF ultrasonic-assisted vibration.
References
[1] KUO K L, TSAO C C. The study of tracing-frequency type ultrasonic-assisted vibration system in tapping process [C]// 2010 International Conference of Advanced Manufacturing, (2010 ICAM). Hsinchu: National Tsinghua University, 2010.
[2] LI H Z, ZENG H, CHEN X Q. An experimental study of tool wear and cutting force variation in the end milling of Inconel 718 with coated carbide inserts [J]. Journal of Materials Processing Technology, 2006, 180: 296-304.
[3] LU F X, TANG W Z, TONG Y M, MIAO J Q, HE L F, LI C M, CHEN G C. Novel pretreatment of hard metal substrate for better performance of diamond coated cutting tools [J]. Diamond and Related Materials, 2006, 15: 2039-2045.
[4] DEVILLEZ A, SCHNEIDER F, DOMINIAK S, DUDZINSKI D, LARROUQUERE D. Cutting forces and wear in dry machining of Inconel 718 with coated carbide tools [J]. Wear, 2007, 262: 931-942.
[5] GIZESIL W, BARTOSZUK M, NIESLONY P. Finite element modelling of temperature distribution in the cutting zone in turning processes with differently coated tools [J]. Journal of Materials Processing Technology, 2005, 164-165: 1204-1211.
[6] RECHBERGER J, DUBACH R. Soft physical vapour deposition coatings- a new coating family for high performance cutting tools [J]. Surface and Coatings Technology, 1993, 60: 584-586.
[7] RECHBERGER J, BRUNNER P, DUBACH R. High performance cutting tools with a solid lubricant physical vapour-deposition coating [J]. Surface and Coatings Technology, 1993, 62: 393-398.
[8] KUMABE J. Fundamentals and application of vibration cutting [M]. Tokyo: Jikkyo Publisher, 1979: 34-49.
[9] KUMABE J, TACHIBANA T. Precision vibration tapping [J]. Journal of Japan Society Precision Engineering, 1982, 48(8): 1002-1009.
[10] SINGH R, KHAMBA J S, GREWAL J S. Machining characteristics optimization using Taguchi technique in ultrasonic drilling of titanium alloys [C]//Proceeding of International Conference Emergency Technology Intelligent System Control (EISCO-2005). Coimbatore (Tamilnadu), India: Kumaraguru College of Technology, 2005: 81-87.
[11] KUO K L, TSAO C C, LIN Y H. Study on the ultrasonic-assisted vibration in internal thread tapping [C]//Proceedings of 2006 MIICS Mechatronic and Industry Interact Cross Strait Conference. Hsinchu Taiwan, 1993: 312-315. (in Chinese)
[12] SU J C, HUANG C K, TARNG Y S. An automated flank wear measurement of microdrills using machine vision [J]. Journal of Materials Processing Technology, 2006, 180: 328-335.
[13]
M, ALEGRE E, BARREIRO J,
L K. On-line tool wear monitoring using geometric descriptors from digital images [J]. International Journal of Machine Tools and Manufacture, 2007, 47: 1847-1853.
(Edited by CHEN Can-hua)
Foundation item: Project (NSC96-2221-E-233-005-MY2) supported by the National Science Council
Corresponding author: Chung-chen TSAO; Tel: +886-3-5927700-2665; E-mail: aetcc@tust.edu.tw
DOI: 10.1016/S1003-6326(12)61801-9