Article ID: 1003-6326(2005)02-0423-04
Oxidation protection of NiCoCrAlY coatings on γ-TiAl
WANG Qi-min(王启民), GUO Ming-hu(郭明虎), KE Pei-ling(柯培玲),
GONG Jun(宫 骏), SUN Chao(孙 超), WEN Li-shi(闻立时)
(Division of Surface Engineering of Materials, Institute of Metal Research,
Chinese Academy of Sciences, Shenyang 110016, China)
Abstract: The effect of NiCoCrAlY overlay coatings on the oxidation resistance of γ-TiAl was studied at 900℃ in static air. To hinder the interdiffusion of the elements, the Al/Al2O3 layer was added between the coating and the alloy. The results show that the TiAl alloy exhibits poor oxidation resistance. NiCoCrAlY coating can not effectively protect the γ-TiAl substrate from high temperature oxidation because of the serious interdiffusion between the coating and the substrates. With Al/Al2O3 diffusion barrier, the NiCoCrAlY coating exhibits excellent oxidation protection on γ-TiAl alloy.
Key words: γ-TiAl; NiCoCrAlY; high temperature oxidation; diffusion barrier CLC number: TG172.8; TG174.44
Document code: A
1 INTRODUCTION
TiAl intermetallic alloy, based on the γ-TiAl, is expected to be one of the candidates for high temperature systems such as aircraft engine because of its high modulus of elasticity, low density and good creep resistance at high temperature[1, 2]. However, there are two major drawbacks with γ-TiAl alloy as an engineering material: one is its poor room temperature ductility and the other is the poor oxidation resistance above 800℃[3]. A large amount of efforts have been focused on improving the oxidation resistance of TiAl alloy. It was shown that alloying or ion implantation could effectively improve the oxidation resistance of Ti3Al and TiAl[4, 5], e.g, by addition of Nb[6, 7], Cr[8], Mo[9] and Si[10]. In addition, some good results by surface coatings for improvement of the oxidation resistance have indeed been achieved by silicides/aluminide coatings made by pack cementation, coating of MCrAlY type, TiAl-based coatings with Cr and Ag additions[11], etc. However, a simpler and less expensive method is still desirable. MCrAlY overlay coatings are being widely used on superalloys because dense and adherent scales can be formed during service, thus preventing further environmental attack[12, 13]. But when applied on TiAl alloys, the MCrAlY coatings encountered problems due to the very serious interdiffusion between the coatings and the substrates[14]. To solve this problem, a diffusion barrier must be included in the coating system. In this paper, the effect of NiCoCrAlY overlay coatings on the oxidation resistance of γ-TiAl was studied at 900℃ in static air. To hinder the interdiffusion of the elements, the Al/Al2O3 diffusion barrier was added between the coating and the alloy. The influence of the diffusion barrier on the behavior of the oxidation and the interdiffusion was investigated.
2 EXPERIMENTAL
The nominal composition of the γ-TiAl alloy is Ti-48Al-2Cr-2Nb(mole fraction, %). The coupons of 10mm×15mm×2mm were cut from this material by means of a spark erosion saw. The samples were polished to 800-grit, peened (200-grit glass ball), ultrasonically cleaned in ethanol and dried in cold air. Then the coupons were loaded into an arc ion plating facility to deposit the Al/Al2O3 diffusion barrier and NiCoCrAlY coating. The nominal composition of the NiCoCrAlY coating is Ni-32Co-20Cr-8Al-0.5Y(mass fraction, %). The time for depositing the Al/Al2O3/NiCoCrAlY coating was 10min, 30min, 4h, respectively. Oxidation tests were conducted in static air at 900℃ for 100h. The mass changes of the specimens were measured at regular intervals. The sensitivity of the balance was 10-5g. Subsequent to oxidation, the specimens were evaluated by X-ray diffraction(XRD, CuKα), scanning electron microscopy(SEM) and energy dispersive X-ray analysis(EDX).
3 RESULTS AND DISCUSSION
Mass gain vs time data of the γ-TiAl alloy and its protective coatings exposed to air at 900℃ in furnace tests is shown in Fig.1. It is clearly shown that the bare alloys have high mass gains in the first 20-30h. After that, obvious mass loss occurs, which shows scale spallation on the bare alloy during oxidation. The mass gains of the coated specimens are much lower and obey the parabolic law during the oxidation process. The mass gains of the NiCoCrAlY coatings decrease by the addition of the Al/Al2O3 barriers at 900℃. The TiAl/Al/Al2O3/NiCoCrAlY system shows excellent oxidation resistance, with the mass gain of only 0.57256mg/cm2 after 100h oxidation. Scale spallation takes place on the uncoated specimen, while no spallation can be found for the coated specimens.
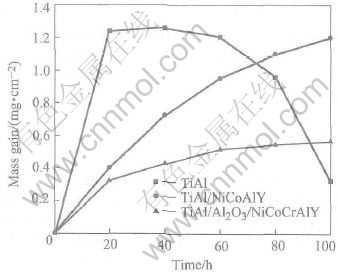
Fig.1 Curves of mass gains vs time
Fig.2 shows the cross-section morphology of the oxidized TiAl alloy. It is clearly shown that flaking of the oxide scale occurs somewhere on the bare alloys. Alternative layers of TiO2 and Al2O3, which correspond to the XRD results in Fig.3, are formed on the specimen surface. Beneath the scale, it can be seen that an Al impoverished layer forms. The scale of mixed TiO2 and Al2O3 has no protective effect and is prone to scale off. As a result, the bare alloy exhibits rather poor oxidation behavior at 900℃.
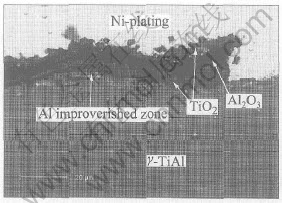
Fig.2 SEM image of cross-section of γ-TiAl alloy after oxidation for 100h at 900℃
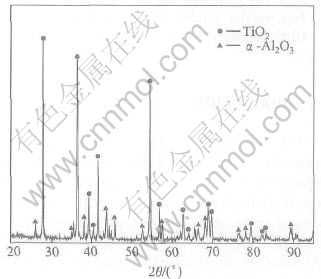
Fig.3 XRD pattern of γ-TiAl alloy after oxidation for 100h at 900℃
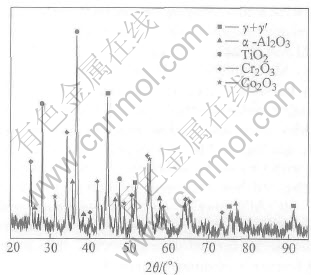
Fig.4 XRD pattern of γ-TiAl /NiCoCrAlY after oxidation for 100h at 900℃
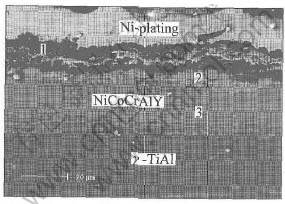
Fig.5 SEM image of cross-section of NiCoCrAlY coating on γ-TiAl alloy after oxidation for 100h at 900℃
For the NiCoCrAlY coatings without diffusion barrier, the oxidation product consists mainly of Cr2O3 and TiO2, and also a small amount of Al2O3 and Co2O3 (Fig.4). The peaks of the metallic phases are very low, which show that the coating experiences serious oxidation and a large amount of coatings were consumed. Fig.5 displays the cross-section morphology of the NiCoCrAlY coatings on the TiAl alloy after oxidation for 100h at 900℃. The scale on the specimens is porous mixed oxide of Cr, Al, Ni, Co and Ti instead of protective Al2O3 (Table 1). The mixed oxide has little protective effect, which results in the fast consumption of the NiCoCrAlY coating. Serious interdiffusion occurs between the coatings and the substrates. Ti in the substrate diffuses into the coating, whereas Ni and Co in the coating diffuses into the substrate at the same time. The remaining coating can hardly be detected. Two diffusion layers are formed between the coating and the substrate: the brighter layer labeled “2” is rich in Co, Ni and also large amount of Ti and Al; the darker layer is rich in Ti, Al and also large amount of Ni (Table 1).
Table 1 EDX results for microzones in Fig.5(mole fraction, %)
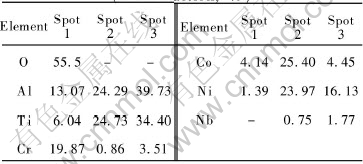
The NiCoCrAlY coatings with Al/Al2O3 barrier show very different phenomenon during oxidation. The interdiffusion between the coating and the substrates is very limited. From the cross-section morphology in Fig.6, it can be seen that no interdiffusion zone can be detected at the interface. No Ti can be detected in the NiCoCrAlY coating, and at the same time, no Ni, Co and Cr can be detected in the substrate. A very dense and adherent scale of Al2O3 formed on the coating. According to the XRD results in Fig.7, only α-Al2O3 can be identified as the oxidation product and the peaks of γ-Ni and γ′-Ni3Al phases were still very high after oxidation for 100h at 900℃. That is, the NiCoCrAlY coating on the Al/Al2O3 barrier remains almost unattacked after 100h oxidation at 900℃ due to the excellent protection of the dense and adherent scale of Al2O3 formed at the initial stage of oxidation.
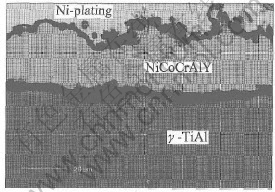
Fig.6 SEM image of cross-section of Al/Al2O3/NiCoCrAlY coating on γ-TiAl alloy
after oxidation for 100h at 900℃
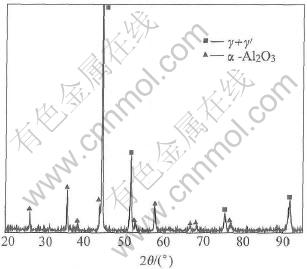
Fig.7 XRD pattern of γ-TiAl /Al/Al2O3/NiCoCrAlY after oxidation for 100h at 900℃
The NiCoCrAlY coatings dont perform well on γ-TiAl substrates because of significant interdiffusion between the coatings and the substrates. The serious interdiffusion influences the oxidation behavior of the coatings in two ways. On one hand, the outward diffusion of Ti increases the Ti content in the NiCoCrAlY coatings. The high mobility of Ti atoms makes it possible for Ti to migrate into the oxide scale and formed Ti oxides quickly[15]. Ti oxides destroy the continuity of the alumina scale. As a result, no continuous alumina scale can be formed on the surface of the coating. The coating experiences fast degradation during oxidation. On the other hand, the outward-diffused Ti and Al react with the inward-diffused Ni and Co. The reaction may produce new brittle intermetallic phases that will deteriorate the mechanical properties of whole systems. Other researchers have reported similar results[14]. With Al/Al2O3 diffusion barriers, the interdiffusion between the coating and the substrates decreases significantly. Both the out-diffusion of Ti and inward-diffusion of Ni and Co are suppressed. The stabilization of the NiCoCrAlY coatings on the γ-TiAl alloys results in the excellent oxidation behavior of the coatings similar to that on the superalloys. The dense and uniform scale consisting only of α-Al2O3 is formed on the coating surface. Oxygen in the environment cannot easily permeate through the alumina scale into the coating. Consequently, the degradation of the coating is very slow. In addition, no interdiffusion zone containing brittle intermetallic phases such as AlCo2Ti and AlNi2Ti[14] that will deteriorate the mechanical properties of the whole systems can be formed. As a result, the NiCoCrAlY coatings with Al/Al2O3 barriers provide excellent protection for the γ-TiAl alloys.
4 CONCLUSIONS
The interdiffusion between the coating and substrate is a very serious problem for the NiCoCrAlY coating on the TiAl substrate. No protective alumina scale but mixed oxide is formed on the surface of the specimen owing to the fast outward diffusion of Ti from the substrate into the coatings. With an Al/Al2O3 diffusion barrier, a dense and adherent protective scale of α-Al2O3 is formed on the surface of the NiCoCrAlY coating. The Al/Al2O3 can act as an excellent diffusion barrier. The Al/Al2O3/NiCoCrAlY coating provides good protection for the γ-TiAl alloys.
REFERENCES
[1]Lipsitt H A, Shechtman D, Schafrik R E. The deformation and fracture of Ti3Al at elevated temperatures[J]. Metall Trans A, 1980, 11A: 1369-1375.
[2]Appel F, Brossman U, Christoph U, et al. Recent progress in the development of grammar titanium aluminide alloys[J]. Adv Eng Mater, 2000, 11: 699-720.
[3]Taniguchi S. Oxidation of intermetallics-Japanese activity[J]. Mater Corros, 1997, 48: 1-9.
[4]Schumacher G, Dettenwanger F, Schutze M, et al. Microalloying effects in the oxidation of TiAl materials[J]. Intermetallics, 1999, 7:1113-1120.
[5]Li X Y, Taniguchi S, Zhu Y C, et al. Oxidation behavior of TiAl protected by Si+Nb combined ion implantation[J]. Intermetallics, 2001, 9: 443-449.
[6]Perez P, Haanappel V A C, Stroosnijder M F. The effect of niobium on the oxidation behaviour of titanium in N2/20%O2 atmosphere[J]. Mater Sci Eng A, 2000, A284: 126-137.
[7]Eckert M, Kath D, Hilpert K. Thermodynamic activities in the alloys of the Ti-Al-Nb system[J]. Metall Mater Trans A, 1999, 30A: 1315-1326.
[8]Brady M P, Smialek J L, Humphrey D L, et al. The role of Cr in promoting protective alumina scale formation by γ-based Ti-Al-Cr alloys(Ⅱ)—oxidation behavior in air [J]. Acta Mater, 1997, 45: 2371-2382.
[9]Shida Y, Anada H. The effect of various ternary additives on the oxidation behavior of TiAl in high-temperature air[J]. Oxid Met, 1996, 45: 197-219.
[10]Maki K, Shioda M, Sayashi M. Effect of silicon and niobium on oxidation resistance of TiAl intermetallics[J]. Mater Sci Eng A, 1992, A153: 591-596
[11]Swadzba L, Maciejny A, Mendala B, et al. Structure and resistance to oxidation of an Al-Si diffusion coating deposited by arc-PVD on a TiAlCrNb alloy[J]. Surf Coat Technol, 2003, 165: 273-280.
[12]Nicholls J R. Advances in coating design for high-performance gas turbines[J]. MRS Bulletin, 2003, 9: 659-670.
[13]Wang Q M, Wu Y N, Ke P L, et al. Hot corrosion behavior of AIP NiCoCrAlY(SiB) coatings on nickel base superalloys[J]. Surf Coat Technol, 2004, 186: 389-397.
[14]Tang Z L, Wang F H, Wu W T. Effect of MCrAlY overlay coatings on oxidation resistance of TiAl intermetallics [J]. Surf Coat Technol, 1998, 99: 248-252.
[15]Abe F, Araki H, Yoshida H, et al. The role of aluminum and titanium on the oxidation process of a nickel-base superalloy in steam at 800℃[J]. Oxid Met, 1987, 27: 21-36.
Foundation item: Project(KGCX2-212-02) supported by the Directional Items of Chinese Academy of Sciences
Received date: 2004-11-29; Accepted date: 2005-01-18
Correspondence: SUN Chao, Professor, PhD; Tel: +86-24-83978232; Fax: +86-24-23843436;
E-mail: qmwang@imr.ac.cn; csun@imr.ac.cn
(Edited by LI Xiang-qun)