
Micro-yield behaviors of Al2O3-SiO2(sf)/Al-Si metal matrix composites
LIU Guan-jun(刘贯军)1,2, LI Wen-fang(李文芳)1, PENG Ji-hua(彭继华)1, DU Jun(杜 军)1
1. School of Mechanical Engineering, South China University of Technology, Guangzhou 510640, China;
2 Mechanical and Electrical Department, Henan Institute of Science and Technology, Xinxiang 453003, China
Received 30 August 2006; accepted 15 January 2007
Abstract: Effects of the volume fraction and the size of crystallized alumina silicate short fibers as well as heat treatment processes on micro-yield strength(MYS) of Al2O3-SiO2(sf)/Al-Si metal matrix composite(MMC) that was fabricated by squeezing cast, were investigated by using continuous loading method on an Instron 5569 tester with a special extensometer with an accuracy of 10-7. The results show that MYS of MMC decreases with the increase of volume fraction and length of the alumina silicate short fibers in the metal matrix composite, respectively. MYS of quenched Al2O3-SiO2(sf)/Al-Si MMC is the lowest, MYS of the MMC through peak-aging treatment is higher than that through other heat treatment methods. And before the peak-aging, MYS of MMC aging treated gradually increases with the increase of the aging time. Aging treatment after solution treatment is a preferred way that enhances micro and macro-yield strength of Al2O3-SiO2(sf)/Al-Si MMC.
Key words: Al-Si metal matrix composite; micro-yield strength; alumina silicate short fibers; heat treatment
1 Introduction
Metal matrix composites have attracted a great attention due to their higher specific strength and modulus of elasticity, higher micro plastic strain resistance, adjustable heat conductivity and thermal expansibility[1-4]. They have been applied in precision instruction and optical systems, such as guide for navigation, infrared detector, astronomical telescope, where better dimensional stability is required. Usually, the micro-yield strength(MYS), the stress value corresponding to the material plastic strain of 1×10-6, is identified as one of indicators of the dimensional stability[2-4]. At present, MYS of aluminum alloy matrix composites reinforced with SiC particle and whisker are investigated, and different measurement are employed[2,4-6], which is preliminary stage of the study for MYS of MMCs. Crystallized alumina silicate short fibers, as one of the low-cost reinforcement for Al-Si matrix composites, will result in comprehensive application for the MMCs, which attaches importance to the study of dimensional stability of MMCs. The investigation for the dimensional stability of MMCs has been largely focused on the effect of heat treatments and thermal cycling treatments on them[7-11]. Obviously, the heat treatment processes is one of the main ways that improve dimensional stability of aluminum matrix composites. But the study on effect of heat treatment processes on MYS of Al-Si composites reinforced with crystallized alumina silicate short fibers has not been reported yet. In Refs.[12-15], for MMC reinforced with short fibers, there is a correlation among slenderness ratio, volume fraction of fibers and strain value in metal matrix. Investigation in Ref.[16] proved that heat residual stress in metal matrix, especially heat residual stress around the interface between reinforcement and the matrix can impose on the property of the interfaces so much as the property of the whole MMC. So, the effects of fiber dimension, volume fraction and heat treatment processes on micro-yield strength of Al-Si composites reinforced with crystallized alumina silicate short fibers was investigated in this paper.
2 Experimental
The matrix material used was eutectic Al-Si alloy containing 12.6% Si, which was gained by putting A00 pure aluminium and aluminium-silicon alloy containing 20% Si together at definite proportion and melted, and
the components are listed in Table 1. The reinforcement is low-cost crystallized alumina silicate (Al2O3-SiO2) short fibers with diameter of 10-20 μm, which was obtained by grinding, washing and screen sizing. The metal matrix composite was fabricated by squeeze infiltration method. To investigate the effect of the short fiber dimension on micro-yield strength of the MMC, the volume fraction of fiber in the MMC was fixed at 20%, and three nominal fibers lengths were used: 60, 80 and 125 μm. Fig.1 is the micrograph of Al-Si matrix composite reinforced with alumina silicate short fibers with 20% in volume faction, which shows evenly distributed fibers in the Al-Si alloy matrix. When the effects of fiber volume fraction and heat treatment processes on MYS of MMC were studied, the reinforced fibers with length between 60 and 120 μm were randomly distributed in Al-Si alloy matrix. MMCs with fibers volume fraction of 40% were heat treated and tested. And MMC were conducted in three typical heat treatments listed in Table 2.
Table 1 Components of Al-Si alloy (mass fraction, %)

Table 2 Heat treatment routes used for Al2O3-SiO2(sf)/Al-Si composite
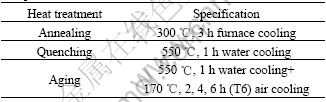
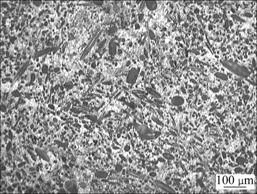
Fig.1 Micrograph of Al2O3-SiO2(sf)/Al-Si composite
Tests were conducted on an Instron 5569 tester equipped with a special extensometer with an accuracy of 10-7. There are two ways to measure MYS of MMCs. One is continuous tension method and the other is loading-unloading method. Compared with the later, the former can avoid some errors induced by micro-cycling strengthening and strain foils bonding loose. In this work, the continuous uniaxial tension method was employed. Dog-bone shaped coupons with 2 mm in thickness, 4 mm in width and 8 mm in gauge length were machined from the various MMCs materials. The strain was measured using an Instron extensometer with a maximum range of 0.006 and an accuracy of 6×10-7. The stress and strain data were obtained by the system microcomputer with Merlin software. Firstly, the modulus of elasticity (E) for each specimen was induced by the formula, E=σ/ε, and the residual plastic strain (εp) was calculated according to the formula, εp=ε-σ/E. Then the curve, εp—σ, was obtained. From the curve, the value of σ corresponding to εp=10-6 was obtained next, which is the micro-yield strength sought[10]. Sequentially, to compare with B-L relation[17],
—σ curves were gained. B-L relation was first presented by both BROWN and LUKENS in 1961. It indicates that there is a parabola relation between micro-yield stress of metal materials, σ, and micro plastic deformation of the metal materials, εp. Afterward, it was rewritten to
for making the research easier. Here, σ0 is the stress driving first dislocation to move; K is a constant relating with shear modulus of the metal material, the grain diameter, movable dislocations density and σ0. The value of K reflects the power of the metal material resisting micro plastic deformation.
3 Results and analysis
3.1 Effect of volume fraction of fibers on MYS of Al-Si MMCs
The preforms were made from Al2O3-SiO2 short fibers with length ranging from 60 μm to 120 μm and random distribution. MMCs with various fiber volume fraction (10%, 20%, 30% and 40%) were fabricated respectively by squeeze infiltration method. The experimental results are given in Fig.2 and Table 3, where each test datum was obtained from arithmetical mean of tests on three specimens (This applies to all the data presented in the paper). Effect of Al2O3-SiO2 short fiber volume fraction on macro and micro mechanical properties of Al2O3-SiO2(sf)/Al-Si MMCs are shown in Table 3 for comparison. In this paper, the macro-yield strength is defined as the stress corresponding to residual plastic strain of 0.2%, and the MYS is the stress corresponding to residual plastic strain of 1×10-6.

Fig.2 Effect of volume fraction of Al2O3-SiO2 short fibers on MYS of Al-Si MMCs
Table 3 Comparison of effects of volume fraction on macroscopical and microcosmic mechanical properties of Al-Si MMCs
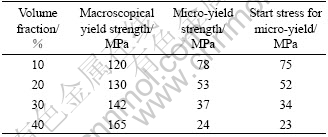
Table 3 shows that, the macro-yield strength of Al2O3-SiO2(sf)/Al-Si composites increases with the increase of short fibers volume fraction, which illustrates that Al2O3-SiO2 short fiber play the reinforcing role effectively. When the interface between reinforced fibers and metal matrix is strong, the higher fiber volume fraction will make them bear more load from metal matrix because of more fiber/matrix interface. Sequentially, the macro mechanical properties are enhanced significantly. However, MYS of Al2O3-SiO2(sf)/ Al-Si MMC decreases with increasing fiber volume fraction. It is obvious that influence trends of the fibers volume fraction on MYS and macro-yield strength are opposite to each other. The explanation for this phenomenon is as follows[11].
Lots of investigations[3,5-7,11] show that the residual thermal stress plays a very important role on the micro-yield strength of MMCs. Larger tensile thermal residual stress in the metal matrix was generated due to the greater difference in thermal expansion coefficients between metal matrix and reinforced fibers during the cooling process of the fabrication and heat treatment of MMCs. If the interface bonding between the reinforced fibers and the metal matrix is good, the rigid reinforcement cannot deform with the ductile matrix, thus dislocations can be generated in the matrix under driving force such as residual thermal mismatch stress or external stress. It has been found that the dislocations do not tangle each other nor form dislocation network, as shown in Fig.3. Most of them may be considered movable dislocations. The dislocations are in the original resting state when the residual thermal mismatch stress is not large enough and cannot make the dislocations move over long-distances. However, when enough external stress is superimposed to the residual thermal mismatch stresses, the dislocations may be driven and subsequent plastic deformation may be induced. For a given MMC, the value of the driving force for the dislocations to move is definite, and the larger the residual thermal mismatch stress, the smaller the external stress needed is. Therefore, if the external stress is high enough, a large number of dislocations in the metal matrix can slide and rapidly contribute to large plastic deformation, which results in the decrease of plastic deformation resistance. That is, during micro plastic deformation, the larger the residual thermal mismatch stress and movable dislocations density, the smaller the micro plastic deformation resistance from the matrix will be. Again, the higher the reinforced volume fraction of fibers, the larger the residual thermal mismatch stress in the matrix is. This is just opposite with that of macro deformation.

Fig.3 TEM image of interface dislocation on longitudinal section of fiber 
3.2 Effect of short fibers length on MYS of Al-Si MMCs
The curve (σ—
) shown in Fig.4 was obtained by tensile tests of Al-Si MMCs reinforced with crystallized Al2O3-SiO2 short fibers with volume fraction of 20% and nominal length of 60, 80 and 125 μm, respectively. Comparison of the effects of fiber length on MYS and macro-yield strength of Al-Si MMCs is listed in Table 4. Fig.4 and Table 4 indicate that MYS of Al-Si MMCs is affected remarkably by the length of Al2O3- SiO2 short fibers. The longer the fibers are, the lower the MYS of the MMC is. The macro yield strength of MMCs, on the other hand, increases with the length of the fibers. The fact that macro-yield strength of Al-Si MMC increases with the increase of the short fiber length may be explained by the study of NARDONE et al[17]. They investigated the plastic deformation in the aluminium matrix accompanied by elastic deformation of SiC fibers for aluminum MMCs reinforced with SiC fibers, and the tensile transfer of load at the ends of the fibers was considered (they assumed that the value of load at the ends of the fibers equals the average strength of the metal matrix). And then, the expression of prediction for yield strength of MMC was first stated. The expression for the yield strength of MMC was first reported as follows [17]:
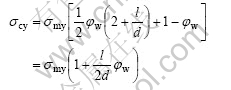
where σcy and σmy are the yield strengths of MMC and matrix alloy, respectively; l/d and φw are the aspect ratio and volume fraction of reinforced fibers, respectively; d is the diameter of the reinforced fibers. The above formula shows that the yield strength of the MMC will increase with the increase of aspect ratio of the reinforced fibers.
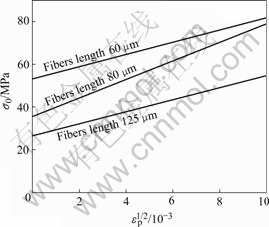
Fig.4 Effect of Al2O3-SiO2 short fibers size on MYS of Al-Si MMCs
Table 4 Comparison of effect of short fibers size on macro and micro mechanical properties of Al-Si MMCs
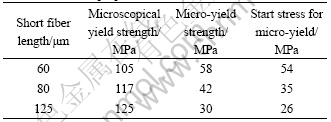
The fact that increasing the length of short fibers results in the decrease of MYS of the MMCs may be explained as follows. The MYS is influenced by two aspects. One is the fiber length and the other is the residual thermal stress. On one hand, a high degree of stress concentration in the matrix a round the ends of the short fibers results in a high dislocation density in these regions. As the volume fraction of the short fibers in MMC is constant, larger fiber length corresponds to fewer fibers and results in smaller area of stress concentration and higher density dislocations, compared with smaller fiber length. As a result, MYS of MMCs would increase with the increase of the length of fiber if the thermal mismatch stress is not considered. On the other hand, what really happens is that there does exist a great difference between coefficients of thermal expansion of the reinforcement and the metal matrix. The longer the fibers, the greater the degree of thermal mismatch along the axial direction is. This high thermal mismatch will induce great stress concentration and dislocation density inside the matrix close to the fibers, which will result in the decrease of MYS of MMC. As a result of the combined effect of the two aspects mentioned above, the increase of the short fiber length results in the decrease of MYS of MMCs.
3.3 Effect of heat treatments on MYS of Al-Si MMCs
Investigations presented in Refs.[2,4-6] show that heat treatment greatly affect the micro-yield behavior of MMCs and suitable heat treatment is an important way to increase MYS and dimensional stability of MMCs. In the study, specimens of the Al-Si MMC reinforced with alumina silicate short fibers were annealed, quenched and aged, respectively, and then tested for MYS by using the data processing method introduced in Section 2.1. The results are shown in Figs.5 and 6. The comparison of the effects of various heat treatments on Al2O3-SiO2(sf)/ Al-Si is shown in Table 5. The data indicates that, MYS of Al-Si MMCs at various heat treatment states obeys BROWN-LUKENS law, and heat treatment state of Al-Si MMC greatly affects MYS of the MMC. MYS of the MMC at as-cast state is higher than that at quenching state but lower than that at annealing state. This is because the great difference between thermal expansion coefficients of reinforcement and metal matrix result in great thermal mismatch stress during sharp cooling. To relax the stress, plastic deformation is generated with great dislocations, and most of them with higher activity and prism or ring[2]. So, when a very small external stress is applied on the MMC, the superposition of internal and external stresses may be high enough to drive the dislocations to move along the direction of the external stress and induce very small strain, namely, micro-yield. For the MMC with a given dislocation state, the driving force of the dislocation movement is constant. The larger the residual thermal mismatch stress, the smaller the external stress needed is. So, under the external stress, some movable dislocations in the metal matrix will start to slide and make contributions to plastic deformation. This will lead to the decrease of the resistance to micro plastic deformation. However, anneal can erase residual thermal mismatch stress generated during casting and quenching. The density of movable dislocations reduces greatly after annealing and as a result MYS of the MMCs increases.
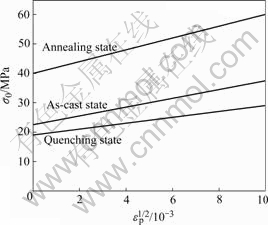
Fig.5 Effect of various heat treatments on MYS of Al-Si MMCs
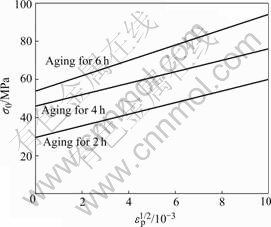
Fig.6 Effect of aging treatments on MYS of Al-Si MMCs
Table 5 Comparison of influences of heat treatments on macro and micro mechanical properties of MMCs
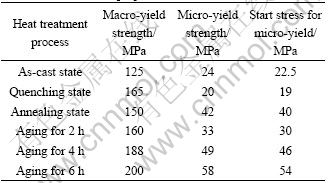
Table 5 shows that the effects of quenching and annealing treatments on MYS of Al-Si MMC are opposite to their effects on macro-yield strength. In other words, macro-yield strength of Al-Si MMC quenched is larger than that of Al-Si MMC annealed and as-cast. But the MYS of the MMC quenched is the lowest among the three states.
The effect trend of aging treatment on MYS of Al-Si MMC is plotted in Fig.6 and Table 5. It can be seen that after aging treatment, MYS of the MMC increases significantly. And the MYS of the MMC increases with prolonging aging time. It has been noticed from Table 5 that the MYS of the MMC aging treated for 6 h is almost twice of that of the MMC quenched. Simultaneously, macro-yield strength of the MMC aging treated increases by about 21% than that of the MMC quenched. The aging treatment can enhance both the macro-yield strength and MYS of the MMCs because of two reasons. One is that the aging treatment relaxes effectively the residual thermal mismatch stress in the metal matrix, which greatly affects mechanical properties of MMCs. The other reason is that a new strengthening phase has been found to precipitate during the process of aging treatment (except over aging). This new phase, S′, is very small and diffusive phase. It is needle-like and about 50 nm long. The even spacing interval of the phases is about 50-100 nm, which is much smaller than both micron spacing interval of alumina silicate short fibers and the matrix grain diameter. Therefore, compared with alumina silicate short fibers and grains of the metal matrix, phase S′ can stop short-range slide of the dislocations much effectively[4].
4 Conclusions
1) Macro-yield strength of Al2O3-SiO2(sf)/Al-Si MMC increases and MYS of the MMC decreases with the increase of volume fraction of Al2O3-SiO2 short fibers, and the effect of volume fraction of the short fibers on MYS of the MMC is greater than that on macro-yield strength.
2) Macro-yield strength of Al2O3-SiO2(sf)/Al-Si MMC increases and MYS of the MMC decreases with the increase of length of Al2O3-SiO2 short fibers.
3) MYS of Al2O3-SiO2(sf)/Al-Si MMC quenched is lower than that of the MMC at as-cast state. MYS of the MMC annealed is obviously higher than that of the former two states.
4) MYS of Al2O3-SiO2(sf)/Al-Si MMC at peak-aging state is higher than that of the MMC at the other heat treatment states, and before the peak-aging, MYS of the MMC aging treated gradually increases with the increase of the aging time.
References
[1] WANG Ri-chu, BI Yu, HUANG Bai-yun, ZHANG Chuan-fu. Effect of surface treatment of SiC particle on mechanical properties of SiCp/6061 Al composites [J]. Journal of Central South University: Science and Technology, 2005, 36(3): 369-374. (in Chinese)
[2] ZHANG Fan, LI Xiao-cui, JIN Cheng, QU Ji-ming, HU Zhong-jun. Microyield behavious of SiCp/2024Al composite and 2024Al alloy [J]. Acta Metallurgica Sinica, 1998, 34(7): 713-718.
[3] ZHANG Fun, SUN Peng-fei, LI Xiao-cui, ZHANG Guo-ding. An experimental study on deformation behavior below 0.2% offset yield stress in some SiCp/Al composites and their unreinforced matrix alloys [J]. Materials Science and Engineering A, 2001, A300: 12-21.
[4] ZHANG Fan, SUN Peng-fei, LI Xiao-cui, ZHANG Guo-ding. A comparative study on microplastic deformation behavior in a SiCp/2024Al composites and their unreinforced matrix alloy [J]. Materials Letters, 2001, 49: 69-74.
[5] HU M, FEI W D, YAO C K. Effect of heat treatment on dislocation states and work hardening behaviors of SiCw/6061Al composite [J]. Materials Letters, 2002, 56: 637-641.
[6] FEI W D, HU M, YAO C K. Effects of thermal residual stress creeping on microstructure and tensile properties of SiC whisker reinforced aluminum matrix composite [J]. Materials Science and Engineering A, 2003, A356: 17-22.
[7] WANG Ling-sen, LIU Ruo-yu, ZHANG Ji-sheng, FAN Yi. The relationship between thermal expansion mismatch and interfacial strength of fiber and matrix in composites [J]. Journal of Central South University of Technology: Natural Science, 1996, 27(6): 689-693. (in Chinese)
[8] WU Jing, LI Wen-fang, MENG Ji-long. Micromechanics analysis of microyield behavior of short fibre reinforced metal material composite [J]. Acta Metallurgica Sinica, 2003, 39(7): 761-766.
[9] LI Yi-chun, FAN Jian-zhong, ZHANG Kui, ZHANG Shao-ming, SHI Li-kai, WU Gao-hui, SUN Dong-li, YANG De-zhang. Effect of thermal cycling treatment on microyield behavior of particle reinforced aluminum matrix composites [J]. The Chinese Journal of Nonferrous Metals, 1998, 8(3): 399-404. (in Chinese)
[10] ZHANG Fan, LI Xiao-cui, SUN Peng-fei. Effects of heat treatment on dimensional stability of SiCp/2024Al composite [J]. The Chinese Journal of Nonferrous Metals, 1999, 9(4): 759-763. (in Chinese)
[11] WU Jing, LI Wen-fang, MENG Ji-long. Microyield behavior of metal matrix composites [J]. Materials Science & Engineering, 2002, 20(4): 594-596.
[12] KANG Guo-zheng, GAO Qing. Stress distribution and deformation characteristics of matrix in short fiber reinforced metal matrix composites [J]. Acta Materiae Compositae Sinica, 2000, 17(2): 20-24.
[13] DING Xiang-dong, LIAN Jian-she, JIANG Zhong-hao, SUN Jun. Thermal residual stresses and stress distributions under tensile and compressive loadings of short fiber reinforced metal matrix composites [J]. Trans Nonferrous Met Soc China, 2001, 11(3): 399-404.
[14] DING Xiang-dong, LIAN Jian-she. JIANG Zhong-hao, SUN Jun. Effect of thermal residual stresses on yielding behavior under tensile or compressive loading of short fiber reinforced metal matrix composite [J]. Trans Nonferrous Met Soc China, 2001, 11(4): 503-508.
[15] LI Ding-qiang, HOJIN Ryu, SOON Hyung-hong. Tensile behavior of SiCp/2124Al composites with various SiC particle sizes at room temperature [J]. Trans Nonferrous Met Soc China, 2000, 10(6): 732-736.
[16] GAO Qing, KANG Guo-zheng, YANG Chuan, ZHANG Jun. Study on microstructure characteristics and thermal residual stress states of interface short fiber reinforced composite at elevated temperature [J]. Acta Materiae Compositae Sinica, 2002, 19(4): 46-50.
[17] NARDONE V C, PREWO K M. On the strength of discontinuous silicon carbide reinforced aluminum composites [J]. Scripta Metal, 1986, 20: 43-48.
Foundation item: Project(19972021)supported by the National Natural Science Foundation of China
Corresponding author: LI Wen-fang; Tel: +86-20-87110201; E-mail: mewfli@SCUT.edu.cn
(Edited by YANG Hua)