J. Cent. South Univ. Technol. (2009) 16: 0038-0042
DOI: 10.1007/s11771-009-0006-6 
Corrosion resistance of cerium conversion film electrodeposited on Mg-Gd-Y-Zr magnesium alloy
Yi jian-long(易建龙), Zhang Xin-ming(张新明), Chen Ming-an(陈明安),
Gu Rui(古 瑞), DENG Yun-lai(邓运来)
(School of Materials Science and Engineering, Central South University, Changsha 410083, China)
Abstract: The cerium conversion film was applied to improving the corrosion resistance of Mg-Gd-Y-Zr magnesium alloy. The film was electrodeposited on the surface of the Mg-RE alloy in cerium nitrate solution. The compositions and morphologies were analyzed by X-ray diffraction(XRD), scanning election microscopy (SEM). The corrosion behaviors of the film were investigated electrochemical impedance spectroscopy (EIS), potentiodynamic polarization tests and immersion tests. The results show that the optimum parameters for electrochemical deposition are as follows: pH 10.0, time 30 min, 50 mmol/L Na2CO3 and temperature 25 ℃ by the designed experiments according to the orthogonal table L(9, 34). The corrosion protection efficiency is dependent on the deposition parameters. The cerium conversion film shows better corrosion protection behavior than chromate conversion film on Mg-Gd-Y-Zr magnesium alloy.
Key words: Mg-Gd-Y-Zr magnesium alloy; conversion film; corrosion
1 Introduction
Magnesium alloys are used in consumer applications (e.g., cases for laptop computers and cameras), the automotive industry (transmission casings, engine blocks), and the aerospace industry (helicopter transmission and rotor housings)[1]. Mg-Gd-Y-Zr magnesium alloys were widely investigated due to their outstanding mechanical properties[2]. They exhibit higher specific strength at both room and elevated temperature and better creep resistance than other Mg-RE alloys such as WE54 and QE22[3-4]. Low corrosion resistance of Mg-RE alloys has the potential impact on long term economics. The corrosion behavior of magnesium and its alloys and the principles research are behind successful use of these materials. Mg-RE alloys require surface protection when they are used in corrosive environments. Coatings provide an important strategy for protecting magnesium alloys from corrosion. The chrome-pickle treatment is a popular and effective pretreatment[5]. However, chromium is among the top toxic substances because of its hexavalent form which is a known carcinogen. Recent research of environmentally acceptable alternatives has led to the development of other conversion film[6-7]. One of the most promising systems is based on RE elements. DABALA et al[8] reported that the cerium conversion film enhanced the corrosion resistance of AZ63 magnesium alloy in chloride media. RUDD et al[7] reported that the corrosion rate of pure magnesium and WE43 in borate buffer solution dropped greatly after they were treated by cerium salts. The active corrosion protection effect in cerium conversion film was revealed in the case of the anion-exchanged hydrotalcite pigments[9]. It is significant for Mg-RE alloys to provide long term protection by cerium conversion film. This work aims at exploring the optimum electrochemical deposition parameters, and investigating the morphology and the corrosion resistance of cerium conversion films on Mg-RE alloys.
2 Experimental
2.1 Pre-treatment
The chemical composition (mass fraction) of magnesium alloy is 8.11% Gd, 3.28% Y, 0.51% Zr and the balance of Mg. Sample dimensions are 10 mm×15 mm×2 mm. Before electro-deposition, the samples were mechanically polished. The polished samples were degreased using an alkaline cleaner, washed with distilled water, and dried in hot air. Aqueous solutions of 1 mmol/L Ce(NO3)3+50 mmol/L Na2CO3+2.5% H2O2, were used as the treatment solutions. The film was deposited potentiostatically using a CHI660C electro- chemical station. Once the deposition was completed,specimens were removed from the electrolyte, rinsed with distilled water, and dried in hot air.
2.2 Techniques
The electrochemical impedance spectroscopy (EIS) measurements were performed using a three-electrode, cerium filmed Mg-Gd-Y-Zr alloys (1 cm2 of exposed area) served as a working electrode, with saturated calomel electrode (SCE) as reference and stainless steel as counter electrode. AC impedance measurements were conducted at the corrosion potential. The amplitude of AC signal was 5 mV, and the measuring frequency ranged from 105 to 10-2 Hz. The immersion test experiments were performed during immersion of the samples in solutions of 3.5% NaCl at (35±1)℃. In the potentiodynamic polarization the scanning rate was 10 mV/s. The morphologies of the cerium conversion film were examined by scanning electron microscopy (SEM).
3 Results and discussion
3.1 Orthogonal experimental designs
Table 1 shows four factors and three levels of electrochemical deposition cerium conversion film: solution temperature, electrolyte pH, deposition time and concentration of Na2CO3, where Rp represents the polarization resistance, and 1/Rp is proportional to the corrosion rate[10]. It is reasonable to characterize cerium conversion film by Rp. The optimization of electrochemical deposition parameters can be obtained by the range analysis. The influence of the four factors on the corrosion resistance is in a sequence: pH> electrochemical deposition time>concentration of Na2CO3> temperature. The most important parameter is pH of the solution. As the pH of solution was above 8[11],
Table 1 orthogonal table L (9, 34): four factors and three levels in electrodeposited process
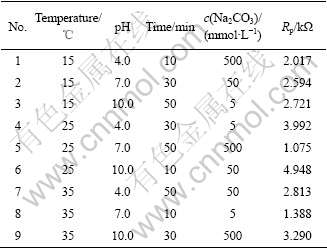
Ce(Ⅲ) was oxidized to Ce(Ⅳ) in solution by the reaction:
4Ce3++O2+2H2O+4OH-=4Ce(OH)22+ (1)
The critical pH for Eqn.(1) was 8.7, above which Ce(OH)22+will be stable in aqueous solution in the presence of oxygen. The alkali required in Eqn.(1) for the oxidation of cerium ions was generated in the vicinity of the magnesium due to oxygen reduction, leading to the precipitation of insoluble tetravalent cerium:
Ce(OH)22++2OH-=CeO2+2H2O (2)
The formation of CeO2 is very important to improve the corrosion resistance of cerium conversion film because it is the most stable oxide of cerium. As for the second factor, better electrochemical deposition time is 30 min. The addition of Na2CO3 improved the anticorrosion, and the mechanism was discussed in Ref.[9]. The solution temperature is related to the velocity of the electrochemical process. In conclusion, the optimum parameters of electrochemical deposition are as follows: pH 10.0, time 30 min, 50 mmol/L Na2CO3 and temperature 25 ℃.
3.2 Electrochemical analysis
Fig.1 shows the evolution of chronoamperometry curves in electrochemically deposited cerium conversion film at optimum parameters. According to Fig.1, several stages can be identified during the process of the film. In the first 20 s of electro-deposition, the current moves towards more negatively, which may be ascribed to the anodic and cathodic partial reactions.
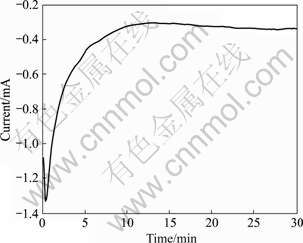
Fig.1 Curve of electro-deposition cerium conversion film in 1 mmol/L Ce(NO3)3+50 mmol/L Na2CO3+2.5% H2O2
Mg=Mg2++2e (3)
2H2O+2e=H2+2OH- (4)
The magnesium hydroxide film is formed by the chemical precipitation reaction:
Mg2++2OH-=Mg(OH)2 (5)
The passivation process for electrode is possible for the mixed magnesium-cerium oxides or hydroxides. SONG et al[12] reported that magnesium could be reduced to hydride by the following electrochemical reaction:
Mg+2H++2e=MgH2 (6)
The formation of MgH2 in Eqn.(6) is an important stage. The bubbling of hydrogen cannot be seen in the first 20 s. But MgH2 is not stable in the aqueous solution and further reacts to form hydrogen:
MgH2+2H2O=Mg2++2OH-+2H2 (7)
From 20 s to 10 min of electro-deposition, the current descends quickly, indicating a modification of magnesium alloys surface owing to the formation of cerium oxides/hydroxides. After 10 min the current of electro-deposition rises slowly, which is caused by the thickness of cerium oxides/hydroxides, and the hydrogen bubbling happens on the magnesium alloy surface. The protective coatings form on the surface after 30 min. X-ray photoelectron spectroscopy (XPS) studies indicate that cerium in the film presents in both the trivalent and tetravalent state by MONTEMOR et al[13]. The molar ratio of Ce(Ⅳ) to Ce(Ⅲ) in cerium conversion film is found to increase with the increase of electrochemical deposited time. XRD patterns of Mg-RE alloys substrate and the film are shown in Fig.2. X-ray peaks of magnesium in the film are stronger than those of substrate, which is superposed by Zr3O. The crystalline peaks of CeO2 appear in the film. The formation of CeO2 is very important with respect to the corrosion resistance of cerium conversion films because it is a stable oxide of cerium and is less soluble than magnesium compounds. The hydrated cerium oxide film is formed, which stifles further cathodic reaction[14].
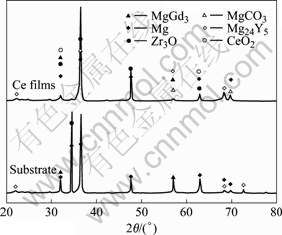
Fig.2 XRD patterns of Mg-RE alloy substrate (a) and cerium conversion film (b)
Fig.3 shows SEM micrograph of a thin and cracked layer with ‘dry-mud’ morphology. Cerium is detected both in the agglomerates and in the film. From energy-dispersive X-ray spectroscopy (EDS) analysis, the amount of cerium in the agglomerates is slightly less than that in the bulk of film. The film is principally composed of magnesium-cerium oxides/hydroxides. The magnesium oxides/ hydroxides form earlier than those of the cerium when the electrochemical reaction happens.
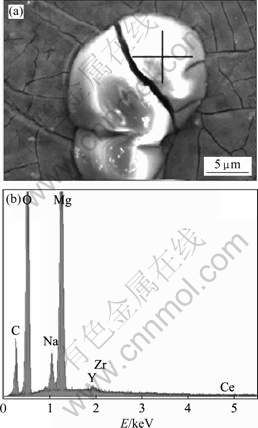
Fig.3 SEM image of film morphology (a) and EDS spectrum of agglomerates of cerium conversion film (b)
Fig.4 shows the polarization curves of cerium conversion film in immersion tests after 0, 3, 15 and 39 h, respectively. The corrosion potential of cerium conversion film moves positive quickly in the first 3 h, which is probably contributed to a partial dissolution of the film. Passivation behavior is observed in the anodic branches of the polarization curves from 3 to 15 h. The cathodic reaction shows a slight inhibition. The corrosion potential shifts towards the anodic direction further and the corrosion current density increases sharply after 39 h. Fig.5 shows the cerium conversion film, which covers with silk after immersion tests for 39 h. The silk in cerium conversion film is caused by the attacking of water and Cl-. The chloride is detected in the cerium conversion film from its corresponding EDS spectrum.
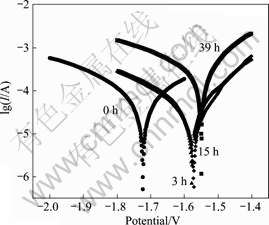
Fig.4 Potential-dynamic polarization curves of samples in immersion tests after 0, 3, 15, 39 h, respectively
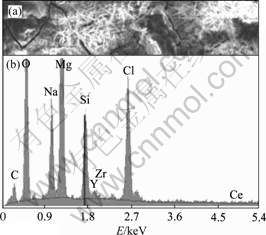
Fig.5 SEM image (a) of conversion film and its corresponding EDS spectrum (b) after immersion test for 39 h
The impedance spectra for the cerium conversion film are shown in Fig.6(a). All spectra are recorded at the corrosion potential immediately after the stabilization of the open circuit potential in 3.5% NaCl solution. The EIS measurements are performed in order to investigate the corrosion resistance of the film for different immersion time. The Nyquist plots of the film at open circuit exhibit one capacitive loop with different diameters for different immersion time. This means that the corrosion mechanisms of the film are similar in NaCl solution for different immersion time. The equivalent circuit used to fit the EIS measurements is shown in Fig.6(b). In the model, Rs is the resistance of solutions, Rcoat represents the resistance due to defects in the conversion film, Rp and Cdl represent the polarization resistance and the intrinsic capacitance of the film, respectively, and Ccoat is the capacitance of the intact film. The values of the elements in the equivalent circuit are listed in Table 2. It can be seen that both Rs and Rcoat increase when the cerium conversion film is immersed in NaCl solution all the time. It is caused by the attacking of Cl- and water. The Stern-Geary equation provides a direct relationship between the steady state corrosion current and the “dc”
resistance across the interface
.
Rp increases sharply while Cdl decreases in the first 15 h, which is attributed to the significant anticorrosion performance of the film. Rp reduces while Cdl rises rapidly after 39 h. This is caused by water in the conversion film. Cdl is associated to the real corroding areas of the coated samples, and a smaller capacitance Cdl is related to a lower real corroding area[15]. Thus the corrosion resistance of Mg-RE alloys is significantly enhanced by the cerium conversion film.
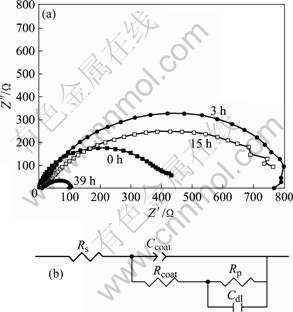
Fig.6 Nyquist plots of electro-deposition cerium conversion film after 0, 3 h, 15 and 39 h respectively (a), and equivalent circuit model developed for fitting EIS measurements (b)
Table 2 Fitting results of equivalent circuit elements in immersion tests
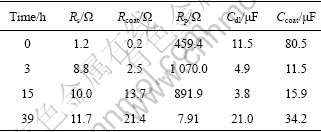
Fig.7 shows the photographs of chromate (a, b) and cerium (c, d) conversion film after 0 h (a, c) and 39 h (b, d) immersion in 3.5% NaCl solution at 35 ℃. Cerium- filmed Mg-Gd-Y-Zr magnesium alloy panels have been evaluated using salt immersion tests for 39 h in parallel with chromated specimens. Cerium conversion film scrubbed before salt immersion test. The corrosion products on the surface of cerium conversion film are less than those of chromated specimens. The results suggest the electro-deposition cerium conversion film perform better anticorrosion than chromate conversion film.
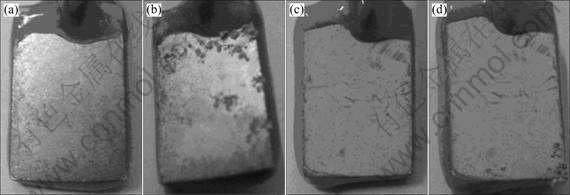
Fig.7 Chromate (a, b) and cerium (c, d) conversion films after 0 (a, c) and 39 h (b, d) immersion in 3.5% NaCl solution at 35 ℃, respectively
4 Conclusions
(1) The optimum parameters of electrochemical deposition are as follows: pH 10.0, time 30 min, 50 mmol/L Na2CO3 and temperature 25 ℃.
(2) The structure of cerium conversion film is not homogeneous and large agglomerates in the film with dry-mud morphology.
(3) The mixed magnesium-cerium oxides/hydroxides are detected by XRD and EDS spectra. The protective properties of cerium conversion film are attributed to the formation of mixed magnesium-cerium oxides/ hydroxides. The cerium conversion film improves the corrosion resistance of Mg-RE alloys in chloride media.
References
[1] WINSTON REVIE R, UHLIG H H. Corrosion and corrosion controll [M]. 4th ed. Hoboken: John Wiley & Sons Inc, 2008: 399.
[2] Xiao Yang, Zhang Xin-ming, Chen Jian-mei, Jiang Hao. Microstructures and mechanical properties of Mg-15Gd-0.6Zr alloy [J]. The Chinese Journal of Nonferrous Metals, 2006, 16(4): 709-714. (in Chinese)
[3] Ben-Hamu G, Eliezer D, Shin K S, Cohen S. The relation between microstructure and corrosion behavior of Mg-Y-RE-Zr alloys [J]. Alloys and Compounds, 2007, 431: 269-276.
[4] Gao Yan, Wang Qu-dong, Gu Jin-hai, Zhao Yang, Tong Yan. Behavior of Mg-15Gd-5Y-0.5Zr alloy during solution heat treatment from 500 to 540 ℃ [J]. Materials Science and Engineering A, 2007, A459: 117-123.
[5] pINC W, GENG S, O'KEEFE M, FAHRENHOLTZ W, O'KEEFE T. Effects of acid and alkaline based surface preparation on spray deposited cerium based conversion coatings on Al2024-T3[J]. Applied Surface Science, 2009, 255: 4061-4065.
[6] Zhao M, Wu S S, An P, Fukuda Y, Nakae H. Growth of multi-elements complex coatings on AZ91D magnesium alloy through conversion treatment [J]. Alloys and Compounds, 2007, 427: 310-315.
[7] Rudd A L, Breslin C B, Mansfeld F. The corrosion protection afforded by rare earth conversion coatings applied to magnesium [J]. Corrosion Science, 2000, 42: 275-288.
[8] Dabala M, Brunelli K, Enrico N, Maurizio M. Cerium chemical conversion coatings on AZ63 magnesium alloy [J]. Surface Coating Technology, 2003, 172: 227-232.
[9] Yi Jian-long, Zhang Xin-ming, Chen Ming-an, Gu Rui. Effect of Na2CO3 on corrosion resistance of cerium conversion film on Mg-Gd-Y-Zr magnesium alloys [J]. Scripta Materialia, 2008, 59: 955-958.
[10] Bonora P L, Andrei M, Eliezer A, Gutman E M. Corrosion behaviour of stressed magnesium alloys [J]. Corrosion Science, 2002, 44: 729-749.
[11] Xuan Lin, OKeefe T J, STOFFER J O. An environmentally compliant cerium conversion coating for aluminum protection [D]. Rolla: University of Missouri-Rolla, 1998.
[12] Song G, Atrens A, Stjohn D, Nairn J, Li Y. The electrochemical corrosion of pure magnesium in 1 N NaCl [J]. Corrosion Science, 1997, 39(5): 855-875.
[13] Montemor M F, Simoes A M, Carme M J. Characterization of rare-earth conversion film formed on the AZ31 magnesium alloy and its relation with corrosion protection [J]. Applied Surface Science, 2007, 253: 6922-6931.
[14] ARDELEAN H, FIAUD C, MARCUS P. Enhanced corrosion resistance of magnesium and its alloys through the formation of cerium (and aluminium) oxide surface film [J]. Materials and Corrosion, 2001, 52: 889-895.
[15] Brunelli K, Dabala M, CALLIARI I, MAGRINI M. Effect of HCl pre-treatment on corrosion resistance of cerium-based conversion coatings on magnesium and magnesium alloys [J]. Corrosion Science, 2005, 47: 989-1000.
Foundation item: Project (5133001E) supported by the Major State Basic Research and Development Program of China
Received date: 2008-04-10; Accepted date: 2008-06-30
Corresponding author: ZHANG Xin-ming, Porfessor; Tel: +86-731-8830265; E-mail: xmzhang_cn@yahoo.cn
(Edited by YANG You-ping)