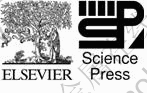
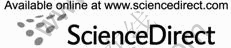
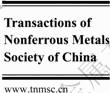
Trans. Nonferrous Met. Soc. China 22(2012) 2327-2333
Microstructure characterization on Mg-2Nd-4Zn-1Zr alloy during heat treatment
LIANG Min-jie1, 2, LIAO Hai-hong1, DING Wen-jiang2, PENG Li-ming2, FU Peng-huai2
1. School of Materials Science and Engineering, North University of China, Taiyuan 030051, China;
2. National Engineering Research Center of Light Alloy Net Forming,
Shanghai Jiao Tong University, Shanghai 200240, China
Received 9 July 2012; accepted 20 August 2012
Abstract: The microstructures of Mg-2Nd-4Zn-1Zr alloy in the as-cast state and after heat treatment were investigated. Several kinds of secondary phases were found and characterized by transmission electron microscopy (TEM), scanning electron microscopy (SEM) and X-ray diffraction (XRD). In the as-cast alloy, the existing eutectic compounds are Mg-Nd-Zn ternary phases: T phases and W phases. After the heat treatment, with increasing the temperature or time, it was found that T phase almost dissolved into the α-Mg matrix, while a large amount of W phase remained in the matrix. On the other hand, with prolonging the time, the morphology of the phase changed from continuous network to the spherical shape along the grain boundary. The density of the W phase gradually decreased and finally it was coarsened and stabilized in the treatment process.
Key words: Mg-Nd-Zn alloy; heat treatment; microstructure; T phase; W phase
1 Introduction
The addition of rare-earth metals can improve the corrosion resistance, as well as the mechanical properties, especially the mechanical properties of magnesium alloys at elevated temperatures [1-5]. Many fundamental studies on developing new magnesium alloys containing RE elements have been conducted. Mg-RE-Zn-Zr alloys are widely used for their high strength, good plasticity and corrosion resistance [6,7]. Nd is considered an effective additional rare earth element. Addition of rational neodymium (Nd) to the Mg–Zn–Zr alloy can effectively improve the yield strength, hardness and ultimate tensile strength of the alloy at higher temperatures as a result of grain refinement and the formation of the Mg12Nd phase [8-10], which could make it possible to develop a high-strength and low-cost magnesium alloy.
NUTTALL et al [2] examined the metallography and kinetics of precipitation in Mg-2.8Nd-1.3Zn alloy and found the equilibrium γ phase. Recently, FU et al [11,12] studied in detail the microstructure and mechanical properties of gravity cast Mg-2.75Nd- xZn-Zr (x=0-2.0%) alloys and found that Mg-Nd alloy with less Zn contains Mg12Nd phase, while the Mg-Nd alloy with more Zn up to 2.0% contains a new Mg-Nd-Zn ternary phases (γ-phase) with FCC structure. Microstructure of Mg-Nd-Zn ternary phases and mechanical properties of Mg-Nd-Zn alloy with Zn content more than 4 were reported [13-15]. However, there is still lack of investigation on phase transformation of Zn-containing Mg-Nd alloy, especially when the alloy is heat treated at a higher temperature.
In the present work, attention is given to the phase constitution and microstructure of secondary phases in the as-cast and heat-treated Mg-Nd-Zn alloy. Considering the effects of Zn element, in order to investigate phase evolution the Zn was added into the Mg-2Nd-1Zr alloy. Specifically, the objective is to identify the secondary phases, to study their structure, morphology and composition in Mg-2Nd-4Zn-1Zr alloy subjected to different heat treated time at 500 ℃, at different heat treated temperatures of 480-520 ℃ for 10 h. The structure of phases is examined using transmission electron microscopy (TEM).
2 Experimental
The Mg–2Nd–4Zn–1Zr (mass fraction, %) alloy was prepared in an electrical resistance furnace using steel crucible with a protective gas consisting of SF6 (1% in volume fraction) and CO2 (Bal.) in order to prevent burning of the melts. Pure magnesium was melt in a steel crucible, with pure Zn (99.99%) added at temperature of 730-740 ℃ and then Nd and Zr were added as Mg-25%Nd and Mg-30%Zr master alloys at 760 ℃. After stirring, the melt was held at 780 ℃ for 30 min to make sure that Zr was completely dissolved. JDMJ refine flux was used to reduce the loss of Nd element. The alloy was poured into a steel moulds holding at (200±5) ℃. By inductively coupled plasma (ICP), the actual chemical composition of the alloy was determined as 1.95Nd-3.91Zn-0.92Zr- Bal Mg (mass fraction, %). The samples were annealed at 500 ℃ for 6-48 h and at 480-520 ℃ for 6 h followed by quenching in cold water.
The microstructures of the alloy were observed by using an optical microscope (OM) and a JEOL JSM-6460 scanning electron microscope (SEM) equipped with X-ray energy dispersive spectrometer (EDS). The phases in the as-cast and heat treated alloys were examined by D/Max 2550VL/PC X-ray diffraction (XRD). The detailed investigations were also performed on a TECNAI G2 20F transmission electron microscope (TEM) operated at 200 kV. The TEM foils were prepared by a twin-jet electron polisher in a solution of ethanol with 1% perchloric acid at -30 ℃, followed by ion beam thinning on a Gatan precision ion polisher for about 0.5 h with an incidence angle of 5°.
3 Results and discussion
3.1 As-cast microstructure and phase constitutions
The optical micrograph (OM) and scanning electron microscopy (SEM) image of the as-cast Mg-2Nd-4Zn-1Zr alloy are shown in Fig. 1. A typical dendritic solidification microstructure can be seen, and is comprised of interdendritic phases formed by the eutectic reaction and α-Mg matrix. A large number of intermetallic compounds distribute along the grain boundaries, and some of them appear as particles and exist inside the grains, as shown in Fig. 1(a). Figure 1(b) shows the magnified microstructure of secondary phases, which appear in a bone-like precipitates along the boundaries and are thickened.
XRD analysis on the as-cast alloy is given in Fig. 2. The peaks from the as-cast Mg-2Nd-4Zn-1Zr alloy can be indexed as α-Mg, and the others are unknown peaks. But the result shows that no distinct peaks belong to Mg12Nd phases, and the localization of others small diffraction peaks are well close to the T phase determined by WEI et al [6,7] and W phase reported by PADEZHNOVA et al [16] using XRD in Mg-Zn-Y alloy. In the as-cast Mg-2Nd-4Zn-1Zr alloy, combining XRD and EDS results intermetallic compounds here may be regarded as the T phase and W phase with both different kinds of Mg-Nd-Zn ternary phases. WEI et al [7] indicated that for the Mg-4Zn-1.5RE alloy, only T phase was found after solidification, and YANG et al [13] observed no W phases emerging in the Mg-2Nd-4.5Zn alloy. However, in this paper, it is interesting that W phase was found and cannot completely dissolve into the matrix after high temperature treatment in the as-cast Mg-2Nd-4Zn-1Zr alloy.
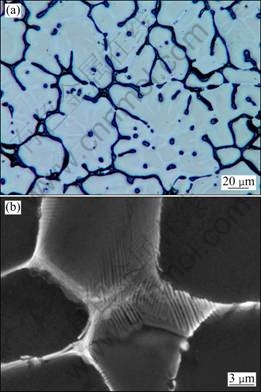
Fig. 1 Optical micrograph (OM) (a) and scanning electron microscopy image (b) of as-cast Mg-2Nd-4Zn-1Zr alloy etched with HNO3-ethanol solution
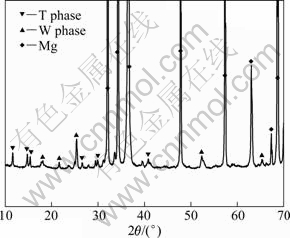
Fig. 2 XRD pattern of as-cast Mg-2Nd-4Zn-1Zr alloy
Up to now, types of phases are still unidentified and need further work on Mg-Nd-Zn alloy. To better clarify the chemical composition and the structure of phases, the TEM bright field images (BFIs) and the corresponding selected area diffraction patterns (SADPs) are observed in this as-cast alloy. Two different intermetallic compounds can also be clearly seen in the TEM images, as shown in Fig. 3. From Fig. 3(a), the typical characterization of a lamellar morphology is observed, which is constituted of intermetallic compound and eutectic α-Mg. The incident electron beam is parallel to [102] zone axis and [001] zone axis direction. From the corresponding diffraction pattern (Fig. 3(a)), it is indicated that this phase has a c-base-centered orthor- hombic (CBCO) crystal structure with a Cmcm space group and mmm point group, which is consistent with the investigation of T phase elsewhere [7,15]. T phase had the following lattice parameters: a=0.97 nm, b=1.13 nm, c=0.95 nm. The composition of T phase in the as-cast alloy was determined using scanning transmission electron microscopy/energy dispersive X-ray (STEM/ EDX) to be (mass fraction, %) 25.4Mg, 39.8Nd, 34.7Zn, corresponding to the mole composition of Mg56.4Nd14.9Zn28.7. Typical spectra are shown in Fig. 4(a).
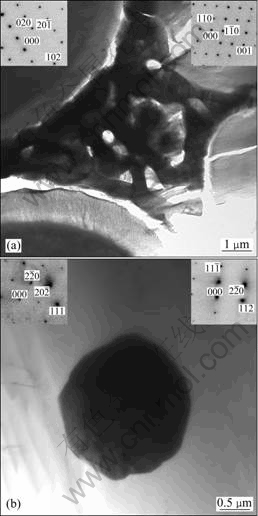
Fig. 3 Bright field TEM image and corresponding selected area diffraction pattern (SADPs) of ternary phase in Mg-2Nd-4Zn- 1Zr as-cast alloy: (a) T phase; (b) W phase
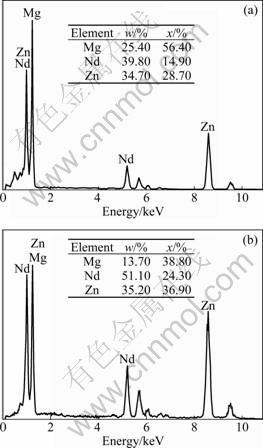
Fig. 4 EDS microanalyses of T phase (a) and W phase (b) in as-cast Mg-2Nd-4Zn-1Zr alloy
On the other hand, during analysis of intermetallic compounds in this as-cast alloy by STEM/EDX, it was found few spherical particles within the grain, which have the compositions out keeping with the vast bulk of T phase. The typical composition is to be approximately (mass fraction, %) 13.7Mg, 51.1Nd, 35.2Zn (Fig. 4(b)), corresponding to the mole composition of Mg38.8Nd24.3Zn36.9. Through the SADPs from [111] zone axis and [112] zone axis direction (Fig. 3(b)), the crystal structures of these phases were determined. It was found that this phase has the same crystal structure as W phase which has been reported by PADEZHNOVA et al [16] and they confirmed the existence of Mg3Y2Zn3 (W phase). Moreover, LI et al [15] also observed the Mg3Nd2Zn3 (W phases) in the as-cast Mg-5Zn- 2Nd-0.6Zr alloy. W phase possesses a face-centered cubic in the Mg-Nd-Zn-Zr alloy, with lattice parameter a=0.711 nm. Thus, combining with STEM/EDX and XRD analysis results, it can be concluded that except α-Mg, mainly two types of ternary Mg-Nd-Zn phases coexist in the as-cast Mg-2Nd-4Zn-1Zr alloy, that is, the lamellar morphology phase is T phase and spherical particle is Mg3Y2Zn3 (W phase).
The present Mg-2Nd-4Zn-Zr alloy shows a different microstructure evolution process from the alloy with lower Zn contents. FU et al [11,12] reported that, when Zn content is lower than 2%, only Mg12Nd phase exists in Mg-3Nd-XZn-Zr (%) alloy; however, when Zn content is 2%, the γ phase with FCC structure forms and coexists with Mg12Nd phase in Mg-3Nd-2Zn-Zr alloy. Some researchers [6,13,15] reported chemical composition and types of ternary phases in the as-cast Mg-Nd-Zn alloy with a higher Zn content, which suggested that the formation process of W phase and T phase is related with the mole ratio of Nd to Zn.
Therefore, it can be concluded that for Mg-2Nd-4Zn-Zr alloy, the eutectic phases have shifted from Mg12Nd phase to ternary Mg-Nd-Zn phase when mole ratio of Nd to Zn is high enough; in addition to the existence of T phases, W phase will also formed.
3.2 Heat-treated microstructure evolution
3.2.1 Temperature effects on microstructure
Through the experimental measurement, second phases are dissolved at 481-510 ℃ for Mg-2Nd-4Zn, therefore, solid solution temperature of alloy is approximately designed at 480-520 ℃. Heat treatment of this alloy was carried for 6 h at 480, 500, 510, 520 ℃, respectively. OM observations were performed in order to elucidate the solution behavior of this alloy at various temperatures (see Fig. 5). From Fig. 5, it can be seen that after heat treatment at 480 ℃ (Fig. 5(a)), the previous continuous network of eutectic compound distributed along the grain boundaries in the as-cast alloy has partially dissolved into Mg Matrix and a large number of fine particle clusters distributed along the grain boundaries, and secondary phase morphology shows an obvious change. With the increase of temperature, many finer secondary phase particles disappear and become more disperse at the grain boundaries. Meanwhile, from 500 ℃ to 520 ℃ the volume fraction of residual secondary phases almost has no change (the statistical results of the volume fraction of secondary phase (see Table 1), and then partial particles of residual secondary phases already began to become coarser than before, that is to say, this coarsening phenomenon becomes obvious more and more with increasing the temperature (Figs. 5(c) and (d)).
On the other hand, it is found that if further elevating the temperature, some undissolved phases still remain in this alloy and above 520 ℃ the alloy will present the overroasting phenomenon. Therefore, it could be preliminary deduced that T phase and W phase exist in the as-cast alloy, one of which may be dissolved into the α-Mg; however, another phase only seems to partial dissolve or completely undissolve in the α-Mg. This implies that Mg-2Nd-4Zn-1Zr alloy contains a kind of higher thermally stabile Mg-Nd-Zn ternary phase. Generally, the dissolving process can be fulfilled at higher solution temperatures for Mg-Nd-Zn alloy. However, the present higher Zn-added alloy shows the different microstructure evolution processes from the lower Zn alloy (see Refs. [9,11]).
Table 1 Volume fraction of secondary phases in Mg-2Nd- 4Zn-1Zr alloy after heat-treatment at different temperatures

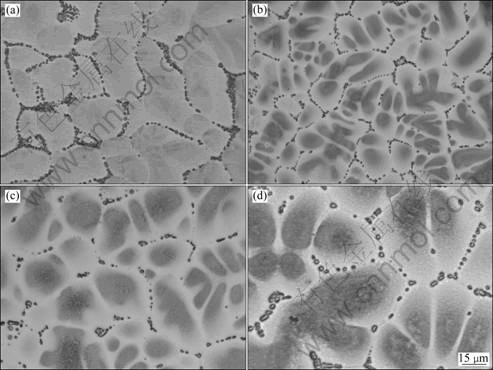
Fig. 5 Optical micrographs (OM) of solution-treated Mg-2Nd-4Zn-1Zr alloys at different temperatures for 6 h: (a) 480 ℃; (b) 500 ℃; (c) 510 ℃; (d) 520 ℃
3.2.2 Time effect on microstructure
In the Mg-2Nd-4Zn-1Zr alloy, microstructure evolution at 500 ℃ was also investigated at different holding time between 8 and 48 h. Figure 6 presents SEM images of intermetallic compounds formed at 500 ℃ for different time. It is clearly seen that a large amount of secondary phase almost continuously distributes along the grain boundary in the alloy after heat treatment for 8 h (Figs. 6(a) and (b)). With prolonging the heat-treatment time, secondary phase gradually dissolved into the Mg matrix, which led to an obvious reduction of the amount of the secondary phase along the grain boundaries. And the morphology of the phase changed from almost continuous network to a randomly distributed spherical shape (Figs. 6(b) and (d)). However, it should be pointed out that when the solution time was extended to 48 h, the secondary phase still kept most undissolved state, as shown in Figs. 6(c) and (d). It is also seen that the residual secondary phases coarsened gradually.
According to X-ray microanalysis (Fig. 7), it can be seen that only W phase left after heat treatment. More detailed investigation was completed by TEM bright field image (BFI) observations, EDS microanalysis and the corresponding micro-beam diffraction patterns for the heat-treated alloy (see Fig. 8). Through calculation from the corresponding SADPs, it is confirmed that the residual secondary phase is W phase with FCC structure. By EDS microanalysis, the composition of secondary phase is determined to be Mg21.4Nd35.9Zn42.7. Consequently, combining with XRD and SADP analysis, it can be concluded that after heat treatment, T phase almost completely dissolved into the α-Mg and the residual secondary phase is W phase.
From above investigations, it can be seen that heat treatment at a high temperature has been carried out for a longer time in order to allow the secondary phase to fully dissolve into the Mg matrix. Generally, the dissolving process can be fulfilled at a suitable temperature for Mg-Nd-Zn alloy. However, the presence of high Zn- containing alloy shows a different microstructure evolution process during heat treatment. As the heat-treatment temperature is very high, it seems impossible to make the W phase dissolve into the matrix during solution treatment, while the T phase can be dissolved, which means that Zn plays a very important role during this process.
Based on the microstructure observation and analysis above, the formation process of ternary phases may be deduced as follows: 1) Once mole ratio of Nd to Zn is high enough, the transformation of Mg12Nd phase to ternary phase will start and both T phase and W phase will present in the as-cast Mg-Nd-Zn alloy; 2) When the heat-treatment temperature is high enough, the Nd and Zn atoms diffuse from T phase and W phase to the α-Mg matrix, but T phase almost dissolves into the matrix during solution treatment, while W phase may not be completely dissolved, which means that W phase is a kind of higher thermally stabile ternary phases.
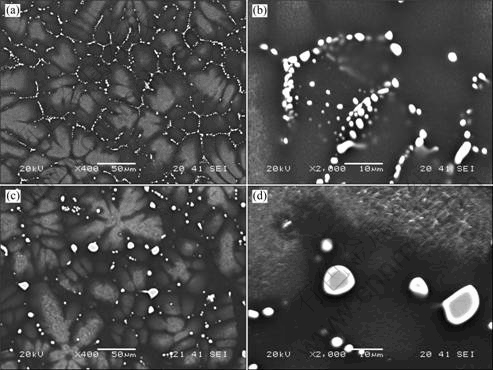
Fig. 6 SEM images showing microstructure evolution of Mg-2Nd-4Zn-1Zr alloy during heat treatment at 500 ℃ for different time: (a),(b) 8 h; (c),(d) 48 h

Fig. 7 XRD pattern of heat-treated Mg-2Nd-4Zn-1Zr alloy
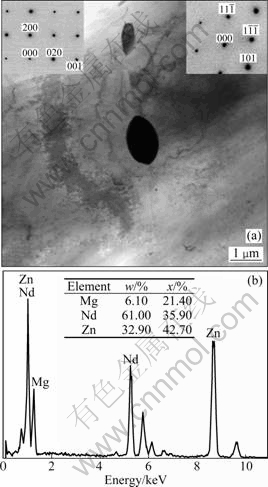
Fig. 8 Bright field TEM images and corresponding selected area diffraction patterns (SADPs) (a) and EDS (b) of W phase in solution-treated Mg-2Nd-4Zn-1Zr alloy
4 Conclusions
1) The microstructure of the as-cast Mg-2Nd-4Zn-1Zr alloy mainly consists of two types of Mg-Nd-Zn ternary phases and α-Mg. One of Mg-Nd-Zn ternary phases is T phase with c-base-centered orthorhombic (CBCO) crystal structure and W phase with FCC structure. The composition of T phase is approximately (mass fraction) 25.4% Mg, 39.8% Nd, 34.7% Zn, corresponding to the mole composition of Mg56.4Nd14.9Zn28.7. The W phase contains approximately (mass fraction) 13.7% Mg, 51.1% Nd, 35.2% Zn, corresponding to the mole composition Mg38.8Nd24.3Zn36.9.
2) After heat treatment at high temperatures, the T phase almost completely dissolved into the α-Mg, while part of W phase cannot dissolve into the α-Mg. With increasing temperature, it seems that the total volume fraction of the residual W phase remains unchanged but it coarsened. This means that W phase is thermally stabile ternary phase at the higher temperatures.
3) With prolonging the heat-treatment time, the amount of W phase decreased gradually and its morphology began to change from continuous networks to spherical shape randomly distributed along the grain boundary. Finally, the coarsened W phase formed during the heat treatment process and remained stable despite the long-term treatment.
References
[1] LI Jie-hua, JIE Wan-qi, YANG Guang-yu. Effect of gadolinium on aged hardening behavior, microstructure and mechanical properties of Mg-Nd-Zn-Zr alloy [J].Transactions of Nonferrous Metals Society of China, 2008, 18(s1): s27-s32.
[2] NUTTALL P A, PIKE T J, NOBLE B. Metallography of dilute Mg-Nd-Zn alloys [J]. Metallography, 1980, 13(s1): 3-20.
[3] QI H Y, HUANG G X, BO H, XU G L, LIU L B, JIN Z P. Thermodynamic description of the Mg-Nd-Zn ternary system [J]. Journal of Alloys and Compounds, 2011, 509(7): 3274-3281
[4] WEI L Y, DUNLOP G L, WESTENGEN H. Precipitation hardening of Mg-Zn and Mg-Zn-RE alloys [J]. Metallurgical and Materials Transactions A, 1995, 26(7): 1705-1716.
[5] LE Qi-chi, ZHANG Zhi-qiang, SHAO Zhi-wen, CUI Jian-zhong, XIE Yi. Microstructures and mechanical properties of Mg-2%Zn-0.4%RE alloys [J]. Transactions of Nonferrous Metals Society of China, 2010, 20(s2): s352-s356.
[6] WEI L Y, DUNLOP G L, WESTENGEN H. The intergranular microstructure of cast Mg-Zn and Mg-Zn-rare earth alloys [J]. Metallurgical and Materials Transactions A, 1995, 26(8): 1947-1955.
[7] WEI L Y, DUNLOP G L, WESTENGEN H. Solidification behaviour and phase constituents of cast Mg–Zn–misch metal alloys [J]. Journal of Materials Science, 1997, 32(12): 3335-3340.
[8] NING Z L, WANG H, LIU H H, CAO F Y, WANG S T, SUN J F. Effects of Nd on microstructures and properties at the elevated temperature of a Mg–0.3Zn–0.32Zr alloy [J]. Materials & Design, 2010, 31(9): 4438-4444.
[9] HUANG M L, LI H X, DING H, TANG Z Y, MEI R B, ZHOU H T, REN R P, HAO S M. A ternary linear compound T2 and its phase equilibrium relationships in Mg-Zn-Nd system at 400℃ [J].Journal of Alloys and Compounds, 2010, 489(2): 620-625.
[10] HUANG Ming-li, LI Hong-xiao, YANG Jin-yan, REN Yu-ping, DING Hua, HAO Shi-ming. Research on a ternary compound T(1) at the low Nd side in the Mg-Zn-Nd alloy [J]. Acta Metallurgica Sinica, 2008, 44(4): 385-390. ( in Chinese)
[11] FU Peng-huai, PENG Li-ming, JIANG Hai-yan, MA Lan, ZHAI Chun-quan. Chemical composition optimization of gravity cast Mg–yNd–xZn–Zr alloy [J].Materials Science and Engineering A, 2008, 496(1-2): 177-188.
[12] FU Peng-huai, PENG Li-ming, JIANG Hai-yan, CHANG Jian-wei, ZHAI Chun-quan. Effects of heat treatments on the microstructures and mechanical properties of Mg-3Nd-0.2Zn-0.4Zr (wt.%) alloy [J].Materials Science and Engineering A, 2008, 486(1-2): 183-192.
[13] YANG Jie, WANG Jian-li, WANG Li-dong, WU Yao-ming, WANG Li-min, ZHANG Hong-jie. Microstructure and mechanical properties of Mg-4.5Zn-xNd (x=0, 1 and 2, wt%) alloys [J].Materials Science and Engineering A, 2008, 479(1-2): 339-344.
[14] LI Qiang, WANG Qu-dong, ZHOU Hai-tao, ZENG Xiao-qing, ZHANG Ya, DING Wen-jiang. High strength extruded Mg-5Zn-2Nd-1.5Y-0.6Zr-0.4Ca alloy produced by electromagnetic casting [J]. Materials Letters, 2005, 59(19-20): 2549-2554.
[15] LI Qiang, WANG Qu-dong, WANG Ying-xin, ZENG Xiao-qin, DING Wen-jiang. Effect of Nd and Y addition on microstructure and mechanical properties of as-cast Mg-Zn-Zr alloy [J].Journal of Alloys and Compounds, 2007, 427(1-2): 115-123.
[16] PADEZHNOVA E M, MEL’NIK E V, DOBATKINA T V. Examination of phase equilibrium in the Mg-Y-Zn system [J]. Russ Metall (Engl Trans), 1979, 1: 179-182.
热处理过程中Mg-2Nd-4Zn-1Zr合金
微观组织的结构特征
梁敏洁1, 2,廖海洪1,丁文江2,彭立明2,付彭怀2
1. 中北大学 材料科学与工程学院,太原 030051;
2. 上海交通大学 轻合金精密成型国家工程中心,上海 200240
摘 要:对比研究了Mg-2Nd-4Zn-1Zr 合金在铸态和热处理态下显微组织结构的演变。借助TEM、SEM和XRD等研究发现,合金中的第二相有几种不同的种类特征。在铸态下,合金中存在的共晶化合物是由Mg、Nd和Zn 构成的两种不同类型的三元相:T相和W相。然而,经过热处理,随着时间和温度的变化,T相几乎完全溶解进入α-Mg基体中,但W相仍然大量剩余在基体中。此外,随着热处理时间的延长,沿晶界分布的第二相的形貌由连续分布的网状逐渐转变为球状。在热处理过程中,合金中W相是一种高热力学稳定相,其数量随着热处理的进行而逐渐减少,并最终粗化、稳定地存在于基体中。
关键词:Mg-Nd-Zn合金;热处理;微观结构;T相;W相
(Edited by YANG Hua)
Foundation item: Project (50971089) supported by the National Natural Science Foundation of China; Project (20100470125) supported by China Postdoctoral Science Foundation; Project (2009021028) supported by Science and Technique Foundation for Young Scholars of Shanxi Province, China
Corresponding author: LIANG Min-jie; Tel: +86-18734159668; Fax: +86-351-3557519; E-mail: lmj2005686@sina.com
DOI: 10.1016/S1003-6326(11)61467-2