J. Cent. South Univ. (2016) 23: 1293-1300
DOI: 10.1007/s11771-016-3179-9

Effect of Nb content on microstructure stability and stress rupture properties of single crystal superalloy containing Re and Ru
SHI Zhen-xue(史振学), LIU Shi-zhong(刘世忠), YUE Xiao-dai(岳晓岱),
WANG Xiao-guang(王效光), LI Jia-rong(李嘉荣)
Science and Technology on Advanced HighTemperature Structural Materials Laboratory,
Beijing Institute of Aeronautical Materials, Beijing 100095, China
Central South University Press and Springer-Verlag Berlin Heidelberg 2016
Abstract: Three experimental single crystal superalloys with 0%Nb, 0.5%Nb, 1.0%Nb were cast in the directionally solidified furnace, while other alloying element contents were basically kept unchanged. The effect of Nb on the microstructure, stability at 1100 °C and stress rupture properties at 1070 °C and 160 MPa of the single crystal superalloy were investigated. The experiment results show that the primary dendrite arm spacing decreases and the volume fraction of γ/γ′ eutectic of the alloy increases with the increase of Nb content in the as-cast microstructures. The size of γ′ phase particles becomes small and uniform and the cubic shape does not obviously change with the increase of Nb content. The precipitating rate and volume fraction of TCP phases increase significantly with the increase of Nb content in the process of long term aging at 1100 °C. The stress rupture lives increase and elongation decreases with increasing Nb content at 1070 °C/160 MPa. At last, the relationship between the microstructures stability, stress rupture properties of the alloy and Nb content is discussed based on JMatPro software and the lastest relevant database for single crystal superalloy.
Key words: single crystal superalloy; Nb; microstructure stability; long-term aging; stress rupture properties
1 Introduction
In recent years, nickel based single crystal superalloys have superior mechanical properties at elevated temperature, which makes them the most suitable materials for the manufacture of turbine blades in advanced aero engines [1-2]. The demand for enhanced high temperature mechanical strength in these alloys has led to increasingly higher additions of refractory alloying elements to enhance the degree of solid solution strengthening [3-4]. The superalloys with high fraction refractory elements are susceptible to the precipitation of deleterious topologically close packed (TCP) phases and the creep properties decrease as a result of the TCP formation [5-7]. So it has become increasingly difficult to develop new single crystal superalloys with a balanced combination of strength, environmental resistance, castability and microstructural stability [8]. In the past, the effect of refractory alloying elements Re, Ru, W, and Mo content on the microstructure and mechanical properties of single crystal superalloys has been investigated [9-13]. The role of the γ′ forming elements Al, Ti, Ta, Nb on the phase stability is also important as their total amount determines the quantity of γ′ phase which is close to 70% (volume fraction) in the single crystal superalloys [1]. An excessive amount of γ′ phase brings out the γ matrix more inclined to precipitate TCP phases because of the higher concentration of elements which partition preferentially to it. As a γ′ forming element, Nb can increase γ′ solvus temperature to avoid the dissolution of this phase at lower temperatures and promote the hardener effect of γ′ phase at higher temperatures by increasing its volume fraction and thermal stability [14]. The Nb content in the single crystal superalloy is generally less than 2% (mass fraction). For example, the mass fractions of Nb in the alloys ЖC32, ЖC36, RenéN4 and DD6 are 1.6%, 1.0%, 0.5% and 0.5%, respectively [15-17], the alloys CMSX-10, CMSX-11B and CMSX-11C all contain 0.1% Nb [18-19]. However, there is no research about the action of Nb in the Ni-based single crystal superalloy in open literature.In present work, the effect of Nb content on the microstructure stability and stress rupture properties of a single crystal superalloy containing Re and Ru was examined, with the aim to promote the development of fourth generation single crystal superalloy with high microstructure stability and high mechanical properties.
2 Experimental
Pure raw materials were used in the experimental study. Three single crystals with [001] orientation were cast by means of crystal selection method in the directionally solidified fur nace with high temperature gradient of 80 °C/cm. The mass fractions of Nb of three alloys were 0%, 0.5% and 1.0%, respectively, and the chemical compositions of other alloy elements were the same. The nominal chemical compositions of experimental al loys are shown in Table 1. The crystal orientations of the specimens were determined with Laue X-ray back reflection method, and the crystal orientation deviations of the speci mens were maintained within 10° from the [001] orientation. The dendrite segregation analysis of the alloys was carried out with electron microprobe analysis (EPMA). The single crystal specimens received the same standard heat treatment comprising of a solution treatment (1345 °C for 6 h, air cooling) and a two-step aging treatment (1120 °C for 4 h, air cooling+870 °C for 24 h, air cooling). Then, the alloys were long term aged at 1100 °C for 200 h, 400 h and 1000 h, respectively. The standard cylindrical specimens for stress rupture tests were machined after heat treatment. The stress rupture tests were conducted at 1070 °C/160 MPa in air using a DST-5 testing machine with furnace attachment, respectively. The samples were etched with 5 g CuSO4+25 mL HCl+20 mL H2O+5 mL H2SO4 which dissolves the γ′ phase. Microstructures of the alloys under different conditions were examined by using S4800 scanning electron microscope (SEM). The equilibrium phases and properties of the alloy with different Nb contents were calculated by JMatPro.
Table 1 Nominal chemical compositions of experimental al loys (mass fraction, %).
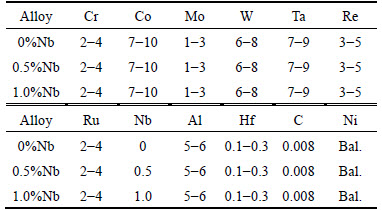
3 Experimental results
3.1 Microstructure
The as-cast microstructures of the alloy with different Nb contents are shown in Figs. 1(a), (b) and (c). The as-cast alloy exhibits the typical dendritic structure with a amount of eutectic in the interdendritic region. These samples are sectioned normal to the solidification direction and show a typical dendritic microstructure of a directionalloy solidified nickel base superalloy. These dendrites are first solid during solidification. The relationship between primary dendrite arm spacing and Nb content is shown in Fig. 1(d). The primary dendrite arm spacing decreases with increasing Nb content. In addition, the structure contains pools of γ/γ′ eutectic in the interdendritic region. The eutectic fraction represents the remaining liquid at the last stage of solidification. The eutectic morphologies of the alloy with different Nb content is shown in Figs. 2(a), (b) and (c). The volume fraction of the γ/γ′ eutectic is observed to increase with increasing Nb content. After quantitative calculation, the volume fractions of eutectic in the alloy with 0%Nb, 0.5%Nb and 1.0%Nb are 11.2%, 12.3% and 14.6%, respectively, as shown in Fig. 2(d).
Nb is a γ′ forming element and a strong positive microsegregation element in the nickel-base superalloys. It is concentrated in the residual liquid in the interdendritic area at the end of solidification. Much of the residual liquid may be forced to reach the eutectic point with increasing the concentration of Nb. This may result in the formation of much more eutectic. So the volume fraction of γ/γ′ eutectic of the alloy increases with the increasing of Nb content in the as-cast microstructures.
Figure 3 shows the typical microstructures of the alloy with different Nb contents after full heat treatment. It can be seen that the primary γ′ and γ/γ′ eutectic dissolve completely after the high temperature solution treatment. They all contain more than 60% γ′ phase in cubic shape and γ matrix channel. The average γ′ phase sizes of the alloy with 0%Nb, 0.5%Nb and 1.0%Nb are 0.42 μm, 0.39 μm and 0.33 μm, respectively. The size of γ′ phase particles becomes small and uniform and the cubic shape do not obviously change with increasing Nb content. Nb can effectively increase the nucleation quantities of γ′ phases, because Nb is a γ′ forming element. Hence, the size of γ′ phase particles becomes small with increasing nucleation quantities.
3.2 Microstructure after LTA
Figure 4 illustrates the microstructures of (001) plane of the alloy with different Nb contents after long term aging (LTA) at 1100 °C for 200 h, 400 h and 1000 h, respectively. It can be seen that with prolonged time, the size of γ′ precipitates in the 0%Nb alloy gradually turns bigger and its morphology is still in cubic shape after long term aging of 200 h. The lateral merging of γ′ precipitates has already begun along the cubic direction. After 400 h, adjacent γ′ particles meet and fuse together producing extended rafts or plates. The γ phase becomes no longer continuous and is thus entirely surrounded by the γ′ phase. No TCP phase is observed even after long term aging of 1000 h, which indicates that the alloy with 0% Nb has a good phase stability.
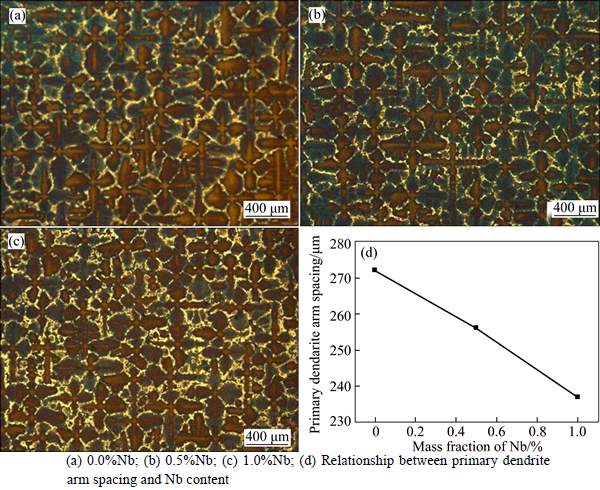
Fig. 1 As-cast dendritic microstructure of alloy:
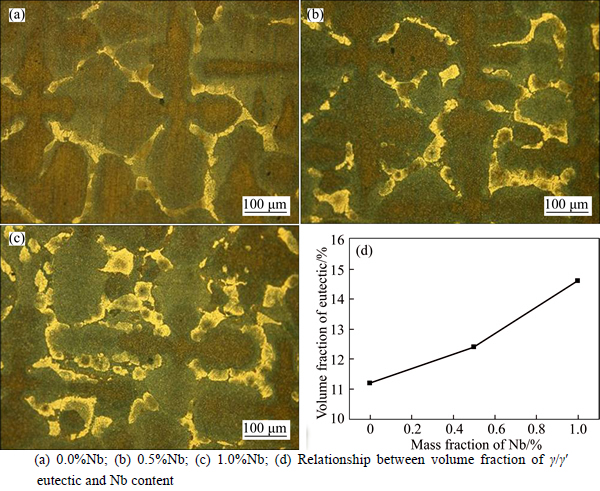
Fig. 2 Eutectic morphologies of alloy:
The rafts have already formed in the 0.5%Nb alloy after long term aging of 200 h. A small amount of needle-shaped TCP phases has already been observed. The coarsening extent of γ′ phases becomes more severe and the amount of TCP phase increases with an increase in aging time.
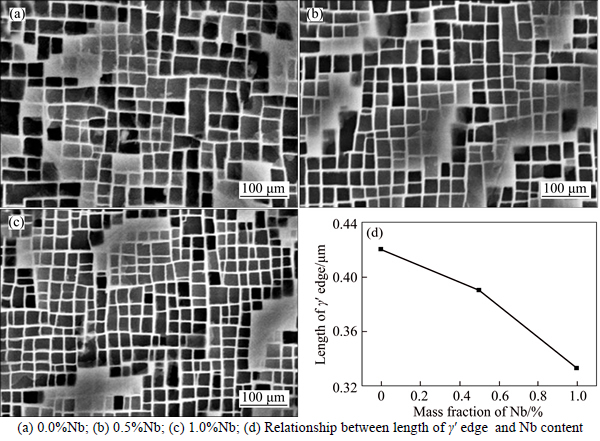
Fig. 3 γ′ morphologies of alloy after heat treatment:
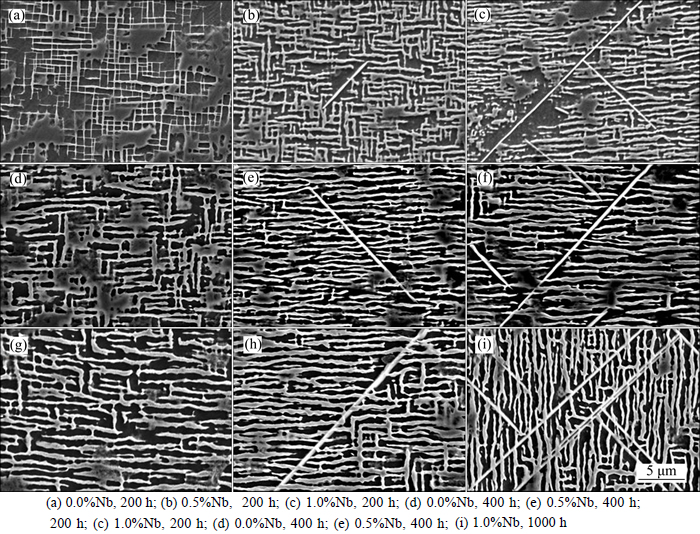
Fig. 4 Microstructure of alloys with different Nb contents after long-term aging at 1100 °C for 200 h:
The regular and perfect rafts have already formed in the 1%Nb alloy after long term aging of 200 h. A large amount of needle-shaped TCP phases is observed. The coarsening extent of γ′ phases becomes more severe and the amount of TCP phase increases with an increase in aging time too.
It can be seen through comparison of the alloys that the coarsening extent of γ′ phases becomes more severe with increasing Nb content and the amount of TCP phase increases.
The microstructure of nickel-based single crystal superalloy changes significantly after LTA at high temperature. The γ′ directional coarsening and rafting can be observed in this process. The γ′ coarsening and rafting are attributed to the directional diffusion of the alloying elements at elevated temperature. Coherency stresses due to the lattice misfit between γ and γ′ phases act as the driving force for these microstructural changes [20]. Because of slight differences in lattice constants of both γ and γ′ phases, a lattice misfit exists. It is well known that the lattice misfit of nickel-based superalloys is strongly influenced by the alloy composition. The alloying element Nb can increase the amount of lattice misfit as it partitions preferentially to the γ′ matrix. Therefore, the rafted rate of γ′ phase increases with increasing Nb content.
Because the TCP phases forming elements such as Re, Mo and W all tend to segregate towards the dendrite core, the TCP phases initially precipitates locally within the dendrite core. Then they gradually spread into the interdendritic area. Furthermore, TCP phases precipitate and grow along fixed direction in all of specimens. The crystal structures of TCP phases are extremely complex and the size of the unit cell is much larger than the lattice of the γ and γ′ phases. A large nucleation barrier serves to prevent the formation of TCP phases in the microstructures of single crystal superalloys [21]. When TCP phases form in the alloys, they nucleate preferentially on close-packed planes, forming a semicoherent interface, and exhibit distinctive orientation relationships with parent crystal [22].
The chemical composition of TCP phases in the 0.5Nb and 1.0% Nb alloy after long term aging for 1000 h using SEM quipped with an energy-dispersive X-ray spectroscope (EDS) is shown in Table 2. Every datum is the mean value of five tests. It is shown that in both of the alloys, Re, W, Co, and Mo are enriched in the TCP phases.
Table 2 Chemical composition of TCP phase in alloys after long-term aging for 1000 h (mass fraction, %)
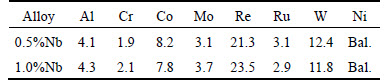
3.3 Stress rupture properties
The stress rupture properties of the alloy with different Nb contents at 1070 °C and 160 MPa are shown in Fig. 5. It can be seen that the stress rupture lives increase and elongation decreases with increasing Nb content. It indicates that Nb can improve the stress rupture lives. The change of elongation may be largely attributed to the TCP phase formation at stress rupture process of the alloy containing Nb. The crack can initiate and propagate on the TCP phases [9, 23]. That makes the elongation decreases with increasing Nb content.
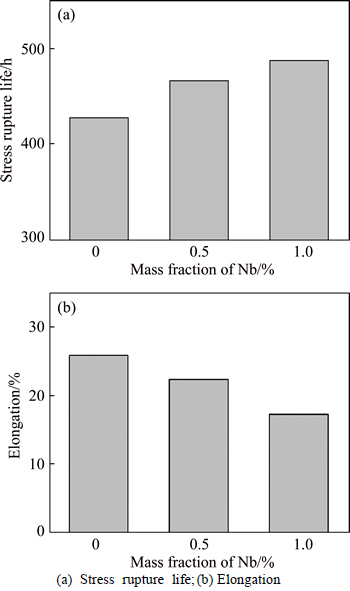
Fig. 5 Stress rupture properties of alloy with different Nb contents at 1070 °C and 160 MPa:
4 Discussion
4.1 Effect of Nb content on microstructure stability
The microstructure stability at elevated temperatures is a key concern for the single crystal superalloys [2]. It can be seen that the alloy precipitates much more TCP phases with increasing Nb content. Moreover, the precipitation rate of TCP phases is significantly influenced by Nb content. It indicates that the increase of Nb content to high refractory content Ni-based single crystal superalloy can decrease high temperature phase stability. The formation of TCP phases in Ni-based single crystal superalloys has generally been attributed to the supersaturation of high melting point refractory elements (Re, W, Mo) within the disordered γ phase [24].
The effect of Nb content on equilibrium phases precipitation behavior is investigated employing the JMatPro software and single crystal superalloy database. The calculation results of precipitation phases of the alloy with different Nb content on temperature are shown in Fig. 6. There are γ′ precipitates, γ matrix, carbide and TCP, the same four phases in the equilibrium phases of the alloy with different Nb contents (see Figs. 6(a), (b) and (c)). However, the volume fraction of γ′ precipitates and TCP phase gradually increase and that of γ matrix accordingly drop off with increasing Nb content. The carbide has almost no obviously change because the alloys contain a very little amount of C. The alloy with different Nb contents contains the same content of Re, W, Mo and other γ forming element. With the decrease of the volume fraction of γ matrix, the concentration of these elements in the γ matrix accordingly increases, which indirectly promotes the nucleation and growth of TCP phase although Nb is not a forming alloying element of TCP phases [25].
Because the segregation of the alloying elements (especially rhenium) can not be fully removed within acceptable homogenization time, superalloys are used with significant residual segregation [26]. The dendrite segregation of the alloying element plays an important role in the formation of the TCP phase. The degree of dendrite segregation can be better characterized with segregation ratio, which is the ratio of the interdendritic composition over the dendrite core composition level. The compositional analysis of the alloys is carried out with standard electron microprobe analysis (EPMA) methods. The results of segregation ratio for the main TCP phase forming alloy element Re, W, Mo and Co are presented in Fig. 7. Every datum is the mean value of five tests. It can be seen from the results that these elements all tend to segregate towards the dendrite core during solidification. The extent of these elements segregation all increases with increasing Nb content. Because the TCP phases initially precipitates locally within the dendrite core, the phase stability of the alloy decreases with the increase of Nb content.
4.2 Effect of Nb content on stress rupture properties
The difference of stress rupture properties of the alloys can largely be attributed to the change of microstructure by Nb content. The Ni-based single crystal superalloy is mainly strengthened by γ′ phase. The property of single crystal superalloy is strongly affected by the size and shape of γ′ phase. The size of γ′phase particles becomes small with increasing Nb content. The γ/γ′ interface is the obstacle of dislocation movement [27]. With the decrease of the size of γ′ particles, the strengthening effect increases.
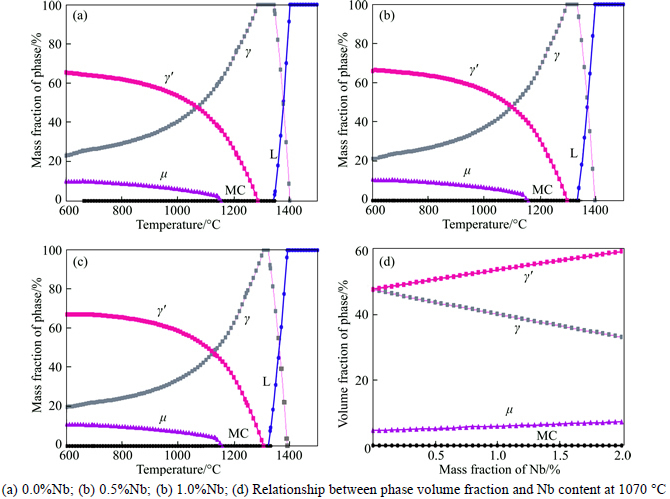
Fig. 6 Calculated dependences of precipitation phases of alloy with different Nb contents on temperature:
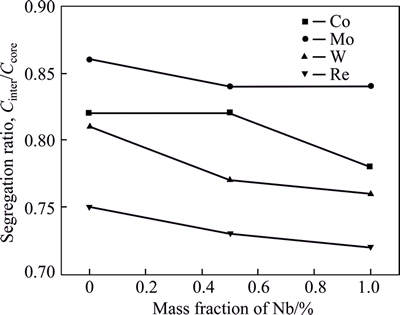
Fig. 7 Element segregation ratio of alloy with different Nb contents
As Nb is a γ′ forming element, it is a strong solid solution strengthener in the γ′ phases. Moreover, Nb can improve the solid solution temperature of γ′ phases. So the single crystal superalloy still has powerful effect of precipitation hardening of γ′ phases at relatively high temperature.
The effect of Nb content on stress rupture properties is investigated employing the JMatPro software. The calculation results are shown in Fig. 8. It indicates that the creep rate decreases and stress rupture life increases with the increase of Nb content. The changed trend is in good agreement with measurements carried out in the experiment, although the stress rupture lives are all low.
5 Conclusions
1) The primary dendrite arm spacing decreases and the volume fraction of γ/γ′ eutectic of the alloy increases with the increase of Nb content in the as-cast microstructures.
2) The size of γ′ phase particles becomes small and uniform and the cubic shape does not obviously change with increasing Nb content.
3) The precipitating rate and volume fraction of TCP phases increase significantly with the increase of Nb content in the process of long term aging at 1100 °C.
4) The stress rupture lives increase and elongation decreases with increasing Nb content at 1070 °C and 160 MPa.
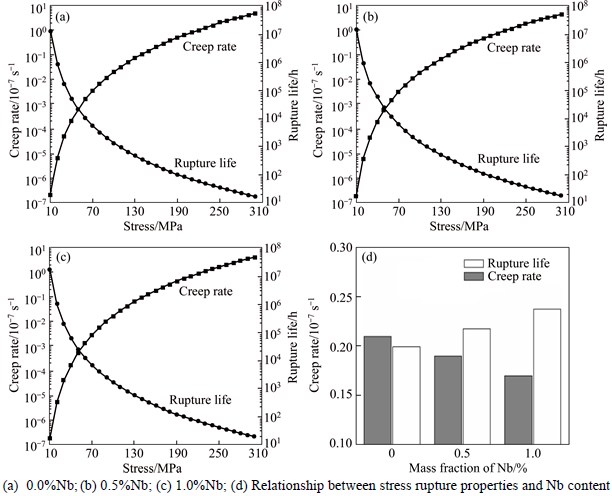
Fig. 8 Calculated dependence of stress rupture properties of alloy with different Nb contents on temperature:
References
[1] CARON P, KHAN T. Evolution of Ni-based superalloys for single crystal gas turbine blade applications [J]. Aerospace Science Technology, 1999, 3: 513-523.
[2] WALSTON S, CETEL A, MACKAY R, O′HARA K, DUHL D, DRESHFIELD R. Joint development of a fourth generation single crystal superalloy [C]// GREEN K A, POLLOK T M, HARADA H, HOWSON T W, REED R C, SCHIRRA J J, WALSTON S ed. Superalloys. Pennsylvania, PA: TMS, 2004: 15-24.
[3] SATO A, HARADA H, YOKOKAWA T, MURAKUMO T, KOIZUMI Y, KOBAYASHI T, IMAI H. The effect of ruthenium on the phase stability of fourth generation Ni-base single crystal superalloys [J]. Scripta Materialia, 2006, 54: 1679-1684.
[4] HOBBS R A, ZHANG L, RAE C M F, TIN S. The effect of ruthenium on the intermediate to high temperature creep response of high refractory content single crystal suepralloy [J]. Materials Science and Engineering A, 2008, 489: 65-76.
[5] ACHARYA M V, FUCHS G E. The effect of long term thermal exposures on the microstructure and properties of CMSX-10 single crystal superalloys [J]. Materials Science and Engineering A, 2004, 381: 143-153.
[6] SHI Z X, LI J R, LIU S Z. Effect of long term aging on microstructure and stress rupture properties of a nickel based single crystal superalloy [J]. Progress in Natural Science: Materials International, 2012, 22(5): 426-4323.
[7] HAN Y F, MA W Y, DONG Z Q, LI S S, GONG S K. Effect of Ruthenium on microstructure and stress rupture properties of a single crystal Nickel-base superalloy [C]// REED R C, GREEN K A, CARON P, GABB P, FAHRMANN G, HURON E S, WOODARD S A ed. Superalloys. Pennsylvania, PA: TMS, 2008: 91-97.
[8] FENG Q, TRYON B, CARROLL L J, POLLOK T M. Cyclic oxidation of Ru-containing single crystal superalloys at 1100 °C [J]. Materials Science and Engineering A, 2007, 458: 184-194.
[9] SHI Z X, LI J R, LIU S Z, WANG X G, YUE X D. Effect of Ru on stress rupture properties of nickel-based single crystal superalloy at high temperature [J]. Transaction of Nonferrous Metal Society of China, 2012, 22: 2106-2111.
[10] LIU Li-rong, JIN Tao, SUN Xiao-feng, GANG Heng-rong, HU Zhuang-qi. Effect of Al, Ti and Ta contents on the microstructure in Ni-base single crystal superalloy during aging [J]. Rare Metal Materials and Engineering, 2008, 37(7): 1253-1256. (in Chinese)
[11] TIAN S G, ZHENG Z, LIANG F S, CHAO Z, CHEN L. Creep behavior of a 4.5%-Re single crystal nickel-based superalloy at intermediate temperatures [J]. Materials Science and Engineering A, 2012, 543: 104-109.
[12] ZHANG J, LI J G, JIN T, SUN X F, HU Z Q. Effect of Mo concentration on creep properties of a single crystal nickel-base superalloy [J]. Materials Science and Engineering A, 2010, 527: 3051-3056.
[13] TIAN Su-gui, DU Hong-qiang, WANG Chun-tao, MENG Fan-lai, SHUI Li, HU Zhuang-qi. Influence of W concentration on microstructure and properties of single crystal Nickel base superalloy [J]. Journal of Aeronautical Materials, 2006, 26(3): 16-19. (in Chinese)
[14] RICARDO P, BALDAN R, ANGELO C, CARVALHO G, MATOS A. Solution heat-treatment of Nb-modified MAR-M247 superalloy [J]. Materials Characterization, 2013, 75: 214-219.
[15] HU Zhuang-qi, LIU Li-rong, JIN Tao, SUN Xiao-feng. Development of the Ni-Base single crystal superalloys [J]. Aeroengine, 2005, 31(3): 1-7. (in Chinese)
[16] ROSS E W, O′HARA K S. René N4: First generation single crystal turbine airfoil alloy with improved oxidation resistance, low angle boundary strength and superior time rupture strength [C]// KISSINGER R D, DEYE D J, ANTON D L, CETEL A D, NATHAL M V, POLLOCK, T M, WOODFORD D Aed. Supperalloys. Warrendale, PA: TMS, 1996: 19-25.
[17] LI J R, ZHONG Z G, TANG D Z, LIU S Z, WEI P, WU Z T, HUANG D, HAN M. A low-cost second generation single crystal superalloy DD6 [C]// Pollock T M, KISSINGER R D, BOWMAN R R, GREEN K A, MCLEAN M, OLSON S, SCHIRRA J J ed. Superalloys. Warrendale, PA: TMS, 2000: 777-783.
[18] ERICKSON G L. The development and application of CMSX-10 [C]// KISSINGER R D, DEYE D J, ANTON D L, CETEL A D, NATHAL M V, POLLOCK, T M, WOODFORD D A ed. Superalloys. Warrendale, PA: TMS, 1996: 35-44.
[19] ERICKSON G L. The development of the CMSX-10B and CMSX-10C alloys for industrial gas turbine application [C]// KISSINGER R D, DEYE D J, ANTON D L, CETEL A D, NATHAL M V, POLLOCK, T M, WOODFORD D A ed. Superalloys. Warrendale, PA: TMS, 1996: 45-52.
[20] PYCZAK F, NEUMEIER S, G
KEN M. Influence of lattice misfit on the internal stress and strain states before and after creep investigated in nickel-base superalloys containing rhenium and ruthenium [J]. Materials Science and Engineering A, 2009, 510-511: 295-300.
[21] NEUMEIER S, PYCZAK F, G
KEN M. The influence of Ruthenium and Rhenium on the local properties of the γ- and γ′-phase in Nickel-base superalloys and their consequences for alloy behavior [C]// REED R C, GREEN K A, CARON P, GABB P, FAHRMANN G, HURON E S, WOODARD S A ed. Superalloys. Pennsylvania, PA: TMS, 2008: 109-110.
[22] RAE C M F, KARUNARATNE M S A, SMALL C J, BROOMFIELD R W, JONES C N, Reed R C. Topologically close packed phases in an experimental Rhenium-containing single crystal superalloy [C]// Pollock T M, KISSINGER R D, BOWMAN R R, GREEN K A, MCLEAN M, OLSON S, SCHIRRA J J ed. Superalloys. Warrendale, PA: TMS, 2000: 767-777.
[23] YEH A C, TIN S. Effect of Ru on the high temperature phase stability of Ni-base single crystal superalloys [J]. Metallurgical and Materials Transactions A, 2006, 37: 2621-2631.
[24] CARROLL L J, FENG Q, MANSFIELD J F, POLLOCK T M. Elemental partitioning in Ru-containing Nickel-base single crystal superalloys [J]. Materials Science and Engineering A, 2009, 457: 292-299.
[25] ZHENG Yun-rong, ZHANG De-tang. Color Metallographic Investigation of Superalloys and Steels [M]. Beijng: National Defence Industry Press, 1999: 8-9. (in Chinese)
[26] EPISHIN A, LINK T, BR
CKNER U, FEDELICH B, PROTELLA P. Effects of segregation in nickel-base superalloys: dendritic stresses [C]// GREEN K A, POLLOK T M, HARADA H, HOWSON T W, REED R C, SCHIRRA J J, WALSTON S ed. Superalloys. Pennsylvania, PA: TMS, 2004: 537-543.
[27] ZHANG J X, MURAKUMO T, KOIZUMI Y, KOBAYASHI T, HARADA H, MASAKI S. Interfacial dislocation networks strengthening a fourth-generation single-crystal TMS-138 superalloy [J]. Metallurgical and Materials Transactions A, 2002, 33: 3741-3746.
(Edited by FANG Jing-hua)
Received date: 2015-03-27; Accepted date: 2015-07-22
Corresponding author: SHI Zhen-xue, Senior Engineer, PhD; Tel: +86-10-62498312; E-mail: shizhenxue@126.com