
Microstructures and interfacial quality of diffusion bonded TC21 titanium alloy joints
LIU Hui-jie, FENG Xiu-li
State Key Laboratory of Advanced Welding Production Technology,
Harbin Institute of Technology, Harbin 150001, China
Received 4 January 2010; accepted 12 April 2010
Abstract: Diffusion bonding of TC21 titanium alloy was carried out at temperature ranging from 780 °C to 980 °C for 5-90 min. The interfacial bonding ratio, deformation ratio, microstructures and microhardness of the diffusion bonded joints were investigated. Results show that joints with high bonding quality can be obtained when bonded at 880 °C for 15-30 min. The microhardness increases with increasing the bonding temperature, while it has a peak value (HV367) when bonding time is prolonged up to 90 min. Fully equiaxed microstructures, bi-modal microstructures and fully lamellar microstructures were observed when bonded in temperature range of 780-880 °C, at 930 °C or 980 °C, respectively. The volume fraction of α phase first increases and achieves the maximum when bonded at 880 °C for 60 min, and then descended.
Key words: TC21 titanium alloy; diffusion bonding; microstructure; interfacial quality
1 Introduction
TC21 alloy is a new kind of alpha-beta titanium alloy. As it has many properties such as high strength and high fracture toughness, it has a wide application prospect in aviation, aerospace and related industries[1-3]. The research efforts to date [4-6] have mainly been focused on the phase and properties of TC21 titanium alloy under heat treatment. However, little work has been done on the bonding of TC21 titanium alloy to itself or other materials, which is important for its further application.
According to Hall-Patch theory, fine grain sized titanium alloy has superior properties compared with coarse grain one, making it attract a great deal of attention. However, because titanium alloy is very sensitive to welding heat input, it is hard to control the grain growth during welding[7], which will eliminate the strengthening effect of grain refining. Therefore, the effective bonding of fine grain sized TC21 titanium alloy is an important task.
Among the several existing bonding methods for titanium alloys, brazing and diffusion bonding are performed at a low temperature so that the grain growth can be restrained. However, the interfacial reactions between titanium alloys and brazing filler metals are hard to be controlled[8-9]. Compared with brazing, diffusion bonding is a recommended method for bonding of similar titanium alloys[10]. Furthermore, the successful application in diffusion bonding of other titanium alloys provides samples with the bonding of TC21 titanium alloy[11-13]. Therefore, diffusion bonding of fine grain sized TC21 titanium alloy was carried out in the present study, in order to obtain sound joints and reveal the effect of the parameters on the microstructures of the joint.
2 Experimental
The material used in this study was the annealed TC21 titanium alloy with dimensions of 10 mm×10 mm×2 mm. The alloy had an initial average grain size of 7 μm. The chemical composition of TC21 titanium alloy is listed in Table 1 and the initial microstructure is shown in Fig.1. Prior to diffusion bonding, all the surfaces to be bonded were ground to remove the oxidation film and achieve a predetermined degree of roughness with SiC papers having different grit sizes of up to 1 000. Subsequently, all the surfaces were cleaned in acetone.
Table 1 Chemical composition of TC21 titanium alloy (mass fraction, %)

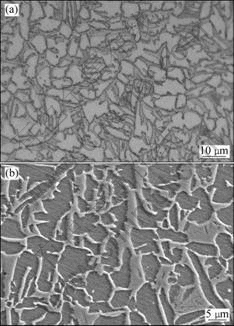
Fig.1 Microstructures of TC21 titanium alloy used: (a) OM; (b) SEM image
Specimens were then assembled and the initial thickness of the specimens (h0) was measured using a vernier caliper to determine the deformation ratio. A layer of yttrium oxide powder was laid between the specimens and the pressure bars to avoid bonding of them.
Diffusion bonding was carried out in the vacuum furnace (Centorr-M60) with a vacuum degree of 6.6 MPa, under a constant bonding pressure of 10 MPa and at the bonding temperature (θ) ranging from 780 °C to 980 oC for a bonding time (t) of 5-90 min. Once the bonding process was completed, the specimens were cooled to room temperature in the chamber.
After bonding, the thickness of the bonded specimens (h) was measured in order to calculate the deformation ratio (k): k=(h0-h)/h0. And then the joints were cross-sectioned perpendicular to the interfaces with a spark discharge machine. The cross-sections of these joints were metallographically polished. They were then etched with a mixture of HF (1 mL), HNO3 (2 mL) and H2O (47 mL) for 3-5 s. Interfacial behaviors were observed by optical microscope (MPG3) and scanning electron microscope (S-4700), and microhardness was measured using a microhardness tester (HVS-1000), with a test load of 4.9 N for 10 s. Bonding quality was evaluated by the interfacial bonding ratio (η), which is the ratio of the total length of voids at the interface to the total length of the interface.
3 Results and discussion
3.1 Interfacial bonding ratio
Fig.2 shows the interfaces of the joints, which were obtained at different temperatures for 30 min. When
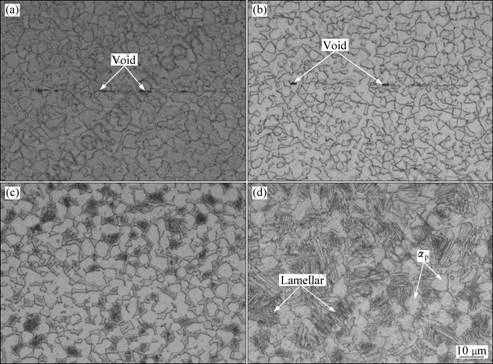
Fig.2 Interface morphologies of joints bonded at different temperatures for 30 min: (a) 780 °C; (b) 830 °C; (c) 880 °C; (d) 930 °C
bonded at 780 °C, many voids (average size about 4 μm) were observed at the interface of the joint. As bonding temperature increases, the amount and size of voids decrease. When bonded at 880 °C or more, voids disappeared completely.
The interfaces of the joints with different bonding times are given in Fig.3. It shows that, when bonded at 880 °C for a short bonding time of 5 min, voids with average size of about 3.6 μm are found at interface. With prolonging the bonding time, the amount and size of voids descend. Voids completely get closed when bonded for 15 min or more.
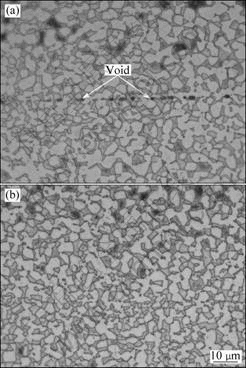
Fig.3 Interface morphologies of joints bonded at 880 °C for different holding time: (a) 5 min; (b) 15 min
The interfacial bonding ratio is shown in Fig.4. From Fig.4(a), the interfacial bonding ratio increases with the increment of bonding temperature. When bonded at 880 °C or more, the interfacial bonding ratio is 100%. From Fig.4(b), at a bonding temperature of 880 °C, when bonded for 5 min, the interfacial bonding ratio is 72%; when bonded for 15 min or more, the interfacial bonding ratio reaches 100%.
The gradual increase of interfacial bonding ratio can be explained by the diffusion mechanisms. The three main diffusion bonding mechanisms are: surface source mechanism, interface source mechanism and bulk deformation mechanism. The diffusion coefficients (Di) under these mechanisms are given as follows:
Di=D0exp[-Qi/(RT)], i=1, 2, 3 (1)
where D0 is prefix coefficient; Qi is diffusion activation energy; R is molar gas constant; and T is bonding temperature. From Eq.(1), the increment of bonding temperature leads to the increase of diffusion coefficients and speed of voids closure. Since prolonged time ensures enough time for voids closure, the interfacial bonding ratio increases as the bonding time increases.

Fig.4 Interface bonding ratio of joints bonded under different conditions: (a) At different temperatures for 30 min; (b) At 880 °C for different time
3.2 Deformation ratio
Fig.5 shows the deformation ratio of the joint under different bonding conditions. From Fig.5(a), increasing bonding temperature leads to serious deformation. When bonded at 930 °C, the deformation ratio is 28.5%. From Fig.5(b), the deformation ratio increases with the increment of the bonding time. When bonded for longer time than 30 min, the deformation ratio exceeds 10%, especially when bonded for 90 min, it comes to 31%. The irreversible deformation of the diffusion bonded joints is caused by instantaneous plastic deformation and creep deformation. With increasing the bonding temperature, the resistance to deformation of the alloy descends, which makes deformation be worse. The increased temperature also results in the microstructure evolution, which has an effect on the deformation. The prolonged bonding time leads to serious creep deformation and higher deformation ratio. Generally, the deformation ratio should be controlled. As a result, the bonding temperature for TC21 titanium alloy should not be higher than 880 °C and the bonding time should be controlled within 30 min when bonded at 880 °C.
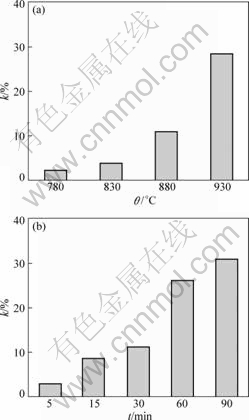
Fig.5 Deformation ratio of joints bonded under different conditions: (a) At different temperatures for 30 min; (b) At 880 °C for different time
3.3 Microstructure evolution
The microstructures of the joints are shown in Fig.6. From Fig.6(a) and (b), one can see that when bonded at lower than 880 °C for 30 min, fully equiaxed structures, which are composed of equiaxed α and β phases, are obtained. As the bonding temperature increases (below 880 °C), the volume fraction of α phase increases, but more α and β phases become long. When bonded at 930 °C for 30 min, most equiaxed α phases transformed into lamellar α phase and they compose the bi-modal microstructure together with the left equiaxed primary α phases (αp) (Fig.6(c)). When the bonding temperature is 980 °C, fully lamellar microstructures are observed (Fig.6(d)). This kind of microstructure is composed of fully lamellar α and β phases without any equiaxed primary α phase, meanwhile, large β grains (average grain size about 244 μm) with clear α phase grain boundaries and different colonies are found (see Fig.7). These colonies have different orientations and consist of parallel lamellar α and β phases.
Bonding time does not affect the type of microstructures, which is evidenced by the fact that fully equiaxed microstructures were observed when bonded at 880 °C for different bonding times (Fig.6(b), (e), (f)). But it has effects on the shape and volume fraction of α and β phases. As the bonding time increases, α and β phases become more and more equiaxed and uniform; however, α phase grows up when bonded for 90 min. Statistic analysis indicates that the volume fraction of α phase first increases and achieves the maximum when bonded for 60 min, and then it descends when bonded for 90 min.
Many researchers have investigated the phase and microstructure of (α+β) titanium alloys[14-16]. Their researches indicated that the important parameters determining the type of microstructures are the temperature and cooling rate. In this study, the joints are obtained at the same cooling rate, therefore the bonding temperature is the primary parameter. When bonded at a temperature lower than 880 °C, α and β phases coexist. As a result, the transformation of α phase to β phase occurs. But many primary α phases are left and grow with the β phase. Increasing temperature and prolonging bonding time enable the growth of α and β phases. These α and β phases remain during cooling and they compose the grown α and β phases together with some α phases which transform from β phase. But when bonded for 90 min, more α phases transform into β phases during heating, and therefore more β phases are left during cooling, which leads to the decrease of the volume fraction of α phases. When bonded at 930 °C for 30 min, most primary α phases transform into β phases and only a small part of α phases are left during cooling, leading to a dramatic decrease of the volume fraction of α phases in the bi-modal microstructures. The α volume fraction together with the αp size defines the most important microstructure feature of the bi-modal structure, namely the β grain size[16], which is about equal to the distance between primary α. As the bonding temperature rises to 980 °C, higher than the (α+β)/β transition temperature of TC21 titanium alloy ((950±5) °C), all α phases transformed into β phases and big β grains are obtained during heating. When cooled, α phases first nucleate at the β grain boundaries because they experience lower activation energy barrier than those inside the grains. And then α phases grow to be lamellae into the prior β grain and form colonies with different orientations. Finally, big β grains with α phases grain boundaries and colonies are left.
3.4 Microhardness
The microhardness values of the joints obtained under different bonding conditions are shown in Fig.8.
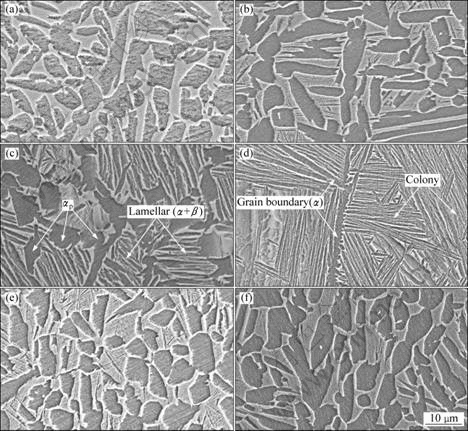
Fig.6 Microstructures of joints bonded under different conditions: (a) 830 °C, 30 min; (b) 880 °C, 30 min; (c) 930 °C, 30 min; (d) 980 °C, 30 min; (e) 880 °C, 60 min; (f) 880 °C, 90 min

Fig.7 Big β grains in fully lamellar microstructures
From Fig.8(a), the microhardness becomes high as the temperature increases. When bonded at 930 °C and 980 °C, the microhardness values are HV380 and HV410, respectively. From Fig.8(b), the microhardness increases with the increment of bonding time, and achieves the maximum (HV367) when bonded for 60 min. As the bonding time is prolonged to 90 min, the microhardness decreases.
The change of the microhardness can be explained by the microstructure evolution. The volume fraction of α phases and sizes of α and β phases play an important role in the microhardness of fully equiaxed microstructure. The more the volume fraction of α phases,
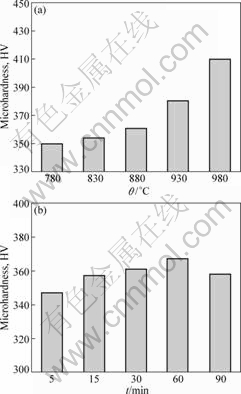
Fig.8 Microhardness values of joints bonded under different conditions: (a) At different temperatures for 30 min; (b) At 880 °C for different time
the higher the microhardness. As a result, when bonded at 780-880 °C for less than 60 min, the microhardness rises; and when bonded for 90 min, it descends. For bi-modal microstructures, the most influential aspect on the mechanical properties of this microstructure is the β grain size, which leads to a small colony size and a short slip length. Therefore, the bi-modal microstructure exhibits a higher yield stress and correspondingly higher microhardness. The most influential parameter of fully lamellar microstructure is the α colony size which determines the slip length. The decrease of the α colony size leads to the decrease of the slip length and the increase of the yield stress and microhardness. Because the α colony size of fully lamellar microstructure is smaller than that of bi-modal microstructure, the former microhardness is higher.
4 Conclusions
1) TC21 titanium alloy can be diffusion bonded at 880 °C for 15-30 min to produce sound joints with high interfacial bonding ratio and low deformation ratio. The microhardness increases as the bonding temperature increases (below 880 °C), but it increases obviously when bonded at 930 °C or 980 °C. While with prolonging bonding time, it first increases and achieves the maximum (HV36) when bonded for 60 min, and then descends when bonded for 90 min.
2) Under the same cooling rate, the type of microstructures is mainly determined by bonding temperature while the characters of them are influenced by both bonding temperature and bonding time. When bonded at 780-880 °C, 930 °C or 980 °C, fully equiaxed microstructures, bi-modal microstructures and fully lamellar microstructures are observed, respectively. In fully lamellar microstructures, β grains with average grain size about 244 μm are found.
3) For bi-modal and fully lamellar microstructures, the short slip length results in high microhardness. For fully equiaxed microstructures, the volume fraction of α phase, shape and size of α and β phases determine the microhardness. As the bonding temperature increases, the volume fraction of α phase increases and α and β phases become big and long. Prolonging bonding time (5-60 min) leads to more equiaxed and uniform α and β phases, while bonded for 90 min, α phases become big. Meanwhile, the volume fraction of α phase first increases and comes to a peak value when bonded for 60 min.
Acknowledgements
The authors wish to express thanks to the Northwest Institute for Non-ferrous Metal Research of China for the support.
References
[1] ZHAO Yong-qing, QU Heng-lei, FENG Liang, YANG Hai-ying, LI Hui, ZHANG Ying-nan, GUO Hong-chao, HUANG Ding-kun. Research on high strength, high toughness and high damage-tolerant titanium alloy-TC21 [J]. Titanium Industry Progress, 2004, 21(1): 22-24. (in Chinese)
[2] ZHU Zhi-shou, WANG Xin-nan, TONG Lu, LIU Dong-sheng. Phase transformation and composition for novel TC21 [J]. Rare Metal Letter, 2006, 25(12): 23-27. (in Chinese)
[3] QU Heng-lei, ZHAO Yong-qing, FENG Liang, XI Zheng-ping, LI Hui, XIA Yuan-ming. Study on microstructures of TC21 alloy under different deformation conditions [J]. J Materials Engineering, 2006(z1): 274-277. (in Chinese)
[4] WANG Yi-hong, KOU Hong-chao, CHANG Hui, ZHU Zhi-shou, ZHANG Feng-shou, LI Jin-shan, ZHOU Lian. Influence of solution temperature on phase transformation of TC21 alloy [J]. Mater Sci Eng A, 2009, 508(1-2): 76-82.
[5] FEI Yu-huan, ZHOU Lian, QU Heng-lei, ZHAO Yong-qing, HUANG Chuan-zhen. The phase and microstructure of TC21 alloy [J]. Mater Sci Eng A, 2008, 494: 166-172.
[6] WANG Yi-hong, KOU Hong-chao, CHANG Hui, ZHU Zhi-shou, SU Xiao-fan, LI Jin-shan, ZHOU Lian. Phase transformation in TC21 alloy during continuous heating [J]. J Alloy Compd, 2009, 472(1/2): 252-256.
[7] SHORT A B. Gas tungsten arc welding of alpha plus beta titanium alloys: A review [J]. Mater Sci Tech, 2009, 25(3): 309-324.
[8] YUE Xin, HE Peng, FENG Ji-cai, ZHANG Jiu-hai, ZHU Feng-qiang. Microstructure and interfacial reactions of vacuum brazing titanium alloy to stainless steel using an AgCuTi filler metal [J]. Mater Charact, 2008, 59: 1721-1727.
[9] ELREFAEY A, TILLMANNA W. Effect of brazing parameters on microstructure and mechanical properties of titanium joints [J]. J Mater Proc Tech, 2009, 209(10): 4842-4849.
[10] CAM G, KOCAK M. Progress in joining of advanced materials part 1: Solid state joining, fusion joining, and joining of intermetallics [J]. Sci Technol Weld Joining, 1998, 3(3): 105-126.
[11] KUNDU S, CHATTERJEE S. Diffusion bonding between commercially pure titanium and micro-duplex stainless steel [J]. Mater Sci Eng A, 2008, 480: 316-322.
[12] KURT B, ORHAN N, EVIN E, CALIK A. Diffusion bonding between Ti-6Al-4V alloy and ferritic stainless steel [J]. Mater Lett, 2007, 61(8): 4004-4008.
[13] BARRENA M I, GOMEZ DE SALAZAR J M, MERINO N, MATESANZ L. Characterization of WC-Co/Ti6Al4V diffusion bonding joints using Ag as interlayer [J]. Mater Charact, 2008, 59: 1407-1411.
[14] CHANG Hui, ZHOU Lian, ZHANG Ting-jie. Review of solid phase transformation in titanium alloys [J]. Rare Metal Mater Eng, 2007, 36(9): 1505-1510.
[15] FILIP R, KUBIAK K, ZIAJA W, SIENIAWSKI J. The effect of microstructure on the mechanical properties of two-phase titanium alloys [J]. J Mater Proc Tech, 2003, 133(1-2): 84-89.
[16] LUTJERING G.. Influence of processing on microstructure and mechanical properties of (α+β) titanium alloys [J]. Mater Sci Eng A, 1998, 243: 32-45.
TC21钛合金扩散连接接头的微观组织及界面质量
刘会杰,冯秀丽
哈尔滨工业大学 现代焊接生产技术国家重点实验室,哈尔滨 150001
摘 要:在780~980 °C的温度下对TC21钛合金进行5~90 min的扩散连接,研究接头的界面结合率、变形率、微观组织及微观硬度。结果表明,在连接温度为880 °C、连接时间为15~30 min的情况下,可以获得高质量的连接接头。接头的微观硬度随着连接温度的升高而增加,并在连接时间达到90 min时取得峰值(HV367)。在连接温度为780~880 °C、930 °C和980 °C时,分别观察到了全等轴组织、双态组织和全层片组织。α相的体积分数随着温度的升高和时间的延长而增加,并在880 °C、60 min时取得极值。
关键词:TC21钛合金;扩散连接;微观组织;界面质量
(Edited by YANG Hua)
Foundation item: Project(2010CB731704) supported by the National Basic Research Program of China
Corresponding author: LIU Hui-jie; Tel: +86-451-86413951; E-mail: liuhj@hit.edu.cn
DOI: 10.1016/S1003-6326(11)60678-X