
High temperature dephosphorization behavior of
monazite concentrate with charred coal
XING Peng-fei(邢鹏飞), ZHUANG Yan-xin(庄艳歆), TU Gan-feng(涂赣峰), GUO Jing(郭 菁)
School of Materials and Metallurgy, Northeastern University, Shenyang 110004, China
Received 17 December 2009; accepted 27 April 2010
Abstract: Dephosphorization behavior of monazite concentrate with charred coal at high temperature was investigated. It is found that the roast temperature is the main factor for the dephosphorization of the monazite. The high dephosphorization efficiency can be reached at the temperatures ranging from 1 200 to 1 400 °C. When the monazite pellets, made by pressing mixture of the monazite, charred coal and water into mould, were roasted at 1 400 °C for 2 h, 98% of phosphorus was removed from the monazite pellets. The roast time has little effect on the dephosphorization efficiency. Meanwhile, the particle size of the charred coal also has great influence on the dephosphorization efficiency of the monazite, and it is better to control particle size around 150 mm, while Fe and Fe2O3 have neglectable effect on the dephosphorization of the monazite.
Key words: dephosphorization; monazite concentrate; charred coal; high temperature
1 Introduction
Rare earth (RE) ferrosilicon alloys have been widely used as intermediate alloys in iron and steel, machinery, automotive and military industry[1-2]. The rare earth intermediate alloys are mainly fabricated by silicon thermal reduction method (SRM) and carbon thermal reduction method (CRM)[3]. The CRM can be regarded as a short, low-cost and environment-friendly process, which has great potential industrial application[4]. Nevertheless, up to now, the CRM is only successful in preparing RE-alloys from the bastnaesite ore[5], and cannot be applied to the Baotou ore due to its high phosphorus content (w(P2O5) of 4%-10%). Baotou ore is a mixed ore, which consists of 60% monazite and 40% bastnaesite. The main component of the monazite is rare earth phosphate (REPO4). In the metallurgy process, the reaction between the phosphorus and RE will take place, and results in the formation of various phosphides, which causes pulverization of the RE-alloys[6-7]. Therefore, it is very important to remove the phosphorus from the ore and to decrease the amount of the phosphorus entering into the alloys[8]. ZHAO et al[9] studied the carbon-thermal reduction process of rare earth concentrate with high-content phosphorus. WU et al[10] investigated the thermal-decomposition mechanisms of the mixed rare earth concentrate containing monazite. ZHANG et al[11] explored the dephosphorization techniques of high-content phosphor concentrate in electric arc furnace. TU et al[12] reported the dephosphorization kinetics of lanthanum phosphate using carbon. However, to our knowledge, there is no report about the dephosphorization behavior of the monazite with charred coal.
Due to its high thermal stability, the rare earth phosphate is very difficult to decompose even at a high temperature, and hereby it is infeasible to dephosphorize through high temperature roasting. In chemical industry, it has been well known that the phosphorus can be fabricated through reduction of calcium phosphate using carbon followed by evaporation and condensation of the phosphorus (Ca3(PO4)2+5C=3CaO+P2+5CO)[13-14], similar mechanism can be used to remove the phosphorus from the monazite. We have reported the dephosphorization behavior of the monazite using coking coal as a reductant[15]. In this work, the dephosphorization of the monazite using charred coal is also investigated by the same technique under different conditions. The effects of particle size of the charred coal, roast temperature, roast time, Fe and Fe2O3 on the dephosphorization behavior were investigated. The results provide technical support for realization of preparing RE alloy from the Boutou ore using the CRM in the future.
2 Experimental
The monazite concentrate powder with the particle size of 75 mm was from Hunan Taojiang smelter, China. It consisted of 62.20% RE oxide (REO) and 9.74% P2O5. Among the REO, the main materials were CeO2, La2O3, Pr6O11 and Nd2O3. The charred coal, used as a reductant, consisted of 76.3% carbon, 17.2% volatile and 6.5% ash. The particle sizes of the charred coal were 75, 109, 150, 250, and 380 mm, respectively. A residual oil, which consisted of 50% carbon and 50% volatile, was added as an adhesive to improve the compressive strength of pellets. The purities of Fe and Fe2O3 were larger than 99 %, and the particle size was 75 mm.
In the process of CRM, the monazite is firstly reduced to RE2O3 by carbon in the submerged arc furnace, and the reaction can be expressed as
2REPO4+5C=RE2O3+P2+5CO (1)
Then, the RE2O3 further reacts with carbon to form REC2 according to the following reaction:
RE2O3+7C=2REC2+3CO (2)
The total reaction between REPO4 and C is
2REPO4+12C=2REC2+P2+8CO (3)
The theoretical mass ratio of materials used in the dephosphorization process of the monazite can be calculated from reaction(3). Considering the burning loss of carbon, the amount of carbon was actually 1.2 times the theoretical amount. The mass ratio of the materials of monazite, charred coal, water and residue oil was 100:43: 10:5 (The average molecular mass of RE used in the calculation is 140). The pellets were fabricated by pressing the mixture of above materials at the pressure of 18 MPa. Then the pellets were heated up to 500 °C for baking.
To remove the phosphorus, the pellets were roasted at 1 100, 1 200, 1 250, 1 300, 1 350, and 1 400 °C, respectively. The pellets were placed into a graphite crucible, covered with charred coal powder, and then loaded into a furnace that was preheated to the desired temperatures. After being kept at the temperature for a given time, the pellets were taken out from the furnace and cooled down to room temperature for further analysis. The content of phosphorus in the pellets was determined by quantitative chemical analysis method. The structure of the samples was characterized 5 22299 14 12
tetragonal phase; h, k, l are index of reflection phanes, Laboratory of Luminescence and Opticalby X-ray diffractometer (XRD) using Cu Ka radiation (Rigaku-D/max).
3 Results and discussion
3.1 High temperature dephosphorization of monazite
After being roasted at high temperature, the baked pellets became light with unchanged volume. When the roasting temperature was higher than 1 200 °C, a large number of white smokes generated after pellets were loaded into furnace. Afterwards, a lot of brown solid powders, which are red phosphorus as determined by XRD, have been found at the end of the furnace, meaning that the phosphorus have been significantly removed from the pellets at 1 200 °C. Fig.1 illustrates the dephosphorization efficiency of the monazite as a function of the roasting temperature and time, where the particle size of the charred coal is 150 mm. The roasting temperature has great impact on the dephosphorization efficiency. The dephosphorization rate reaches atxide (ntration of effluent.o 18.2% at 1 100 °C for 1 h, suggesting that the dephosphorization process starts at 1 100 °C even though the dephosphori- zation rate is relative low. The dephosphorization ratio increases with the increase of roasting temperature. Especially, at the temperature between 1 200 °C to 1 400 °C, the dephosphorization rate increases rapidly with the increase of temperature, meaning that the temperature has stronger effect on the reaction rate. The dephosphorization rate reaches 98 % at 1 400 °C for 2 h, indicating that most of the phosphorus in the pellets has been removed and further higher roasting temperature will be unnecessary. The dephosphorization behavior is also enhanced by increasing the roasting time. The longer roasting time is helpful for removing phosphorus in the system. However, with increasing the temperature, the time becomes less important. For example, at 1 400 °C, further longer roasting time than 2 h is not necessary since the most of phosphorus has been removed after 2 h. It can be concluded that the temperature is a main factor for the dephosphorization of the monazite.
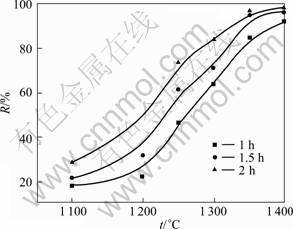
Fig.1 Relationship between dephosphorization rate R of monazite and roasting temperature t and time
Fig.2 shows the XRD patterns of the charred coal and pellets of the monazite roasted at various temperatures for 2 h. The main contents of the charred coal are carbon and small amount of SiO2. After being roasted at 1 100 °C for 2 h, the pellets consists of REPO4 and a small amount of La2O3, Ce2O3, Pr2O3 and Nd2O3, indicating that only small amount of REPO4 is reduced to the REO, and the reaction rate is relative low. However, at 1 300 oC, the most of REPO4 in the pellets was reduced to REO, indicating that the reaction rate increases with the increase of temperature. At 1 400 °C, only the peaks of La2O3, Ce2O3, Pr2O3 and Nd2O3 have been found on the XRD pattern, no REPO4 has been found in the limitation of XRD detection, suggesting that the REPO4 in the pellets has been reduced to REO, which is in agreement with the conclusions above. Therefore, the charred coal is very effective to remove phosphorus from the monazite in the temperature range of 1 200 -1 400 °C.
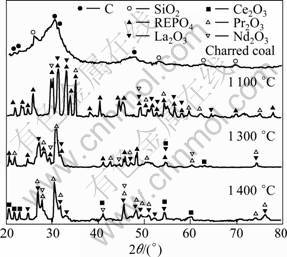
Fig.2 XRD patterns of charred coal and pellets of monazite after being roasted at various temperatures for 2 h
Table 1 gives the standard Gibbs free energy and theoretical initial reaction temperature of the reaction between REPO4 with carbon, which are obtained from the thermodynamic calculation at the standard state. The theoretical initial reaction temperature is 1 231 °C for the reduction reaction between LaPO4 and C, 1 325 °C for the reaction between CePO4 and C, 1 225 °C for the reaction between PrPO4 and C, and 1 251 °C for the reaction between NdPO4 and C, respectively. However, the partial pressure of P2 and CO in the reaction system has effect on the initial reaction temperature. For example, in the reaction system, the CePO4 reacts with C to form Ce2O3, the theoretical initial reaction temperature is 1 598 K (1 325 °C) as given in Table 1. However, when the pressure ratio of P2 to CO is 5:1, Gibbs free energy for the reaction is
DG2=
+RTln
=1 822 806-1 140.68T+8.314Tln
=1 822 806-1 163.16T (4)
Assuming DG2=0, then the initial reaction temperature is 1 293 °C for the practical reaction system, meaning that the real initial reaction temperature is lower than the theoretical one. The real initial reaction temperatures at the condition of V(CO):V(P2)=5:1 for all the five reactions are also given in Table 1 for comparison.
In the practical production, under the conditions of temperature larger than 1 000 °C and larger amount of carbon existing, most of carbon will become CO. Meanwhile, the pressure of P2 is very small in the reaction system, meaning that the volume ratio of CO to P2 will be significantly larger than 5:1. On the other hand, there are other impurities in the system, which cause other reduction gas such as H2O and SiO presenting at high temperature. Considering all the practical condition, the dephosphorization reaction of the monazite will actually start at even lower temperature. This is the reason why the dephosphorization starts even at 1 100 °C as found in the work. The higher temperature will enhance the dephosphorization of the monazite according to Eq.4. The results above suggest that the charred coal is an effective agent for dephosphorization.
Table 1 Standard Gibbs free energy
, theoretical initial reaction temperature t0 and real initial reaction temperature t at condition of V(CO):V(P2)=5:1 for reaction of rare earth phosphate with carbon
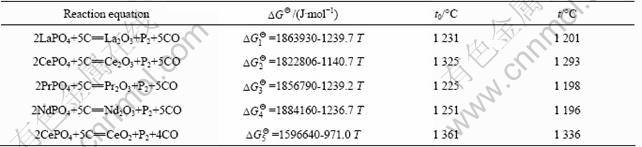
3.2 Effect of charred coal sizes on dephosphorization
Since the pellets made of the monazite and reductant powder were used in the process of the CRM, the contact area between the monazite and charred coal, i.e. the particle size of the reaction materials is very important for the reaction rate. Fig.3 shows the dephosphoriation rate as a function of particle size of the charred coal, where the particle size of the monazite remains 75 mm, and the pellets are roasted at 1 400 °C for 2 h. It can be seen that the dephosphorization rate increases with the decrease of the particles size of the charred coal. However, when the particle size is smaller than 150 mm, the particle size of the charred coal has less important effect on the dephosphorization efficiency. Therefore, the optimized particle sizes of the charred coal should be about 150 mm.

Fig.3 Influence of particle size d of charred coal on dephosphorization rate R of monazite
3.3 Effect of Fe and Fe2O3 on dephosphorization
It is well known that the electrodes of the submerged arc furnace are covered with a layer of iron. During the reaction, the iron will be continuously melted into the reaction system. In the production process, some of iron will be unavoidablly introduced into the alloys. Meanwhile, there are a small amount of iron oxides in the Baotou ore. Therefore, it is necessary to know the effect of iron and iron oxide on the dephosphorization rate of the monazite.
Fig.4 shows the dephosphorization rate as a function of iron content, where the particle size of the monazite and the charred coal are 75 and 150 μm, respectively. It can be found that the iron has little effect on the dephosphorization of the monazite at 1 300, 1 400 and 1 500 °C. The dephosphorization rate increases from 86 % to 98 % with the roasting temperature increasing from 1 300 °C to 1 400 °C. However, it increases only 1% from 1 400 to 1 500 °C. This suggests that most of phosphorus has been removed at 1 400 °C, and the temperature is one of the main factors to affect dephosphorization efficiency of the monazite.

Fig.4 Influence of Fe mass fraction on dephosphorization rate of monazite under different conditions
Fig.5 illustrates the effect of Fe2O3 on the dephosphorization efficiency of the monazite with charred coal, where the particle sizes of the monazite and charred coal are 75 and 150 μm, respectively. It can be found that Fe2O3 has no obvious effect on the dephosphorization efficiency under the conditions investigated, which is similar to Fe. However, the roasting temperature has a great impact on the dephosphorization efficiency of the monazite.
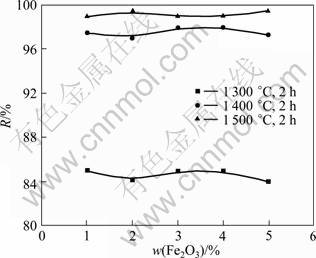
Fig.5 Influence of Fe2O3 content on dephosphorization rate of monazite
Fig.6 shows the XRD pattern of the monazite pellets roasted at 1 500 °C for 2 h, where 5% Fe2O3 has been added to the monazite pellets. No diffraction peaks of REPO4 have been found on the XRD pattern, suggesting that all of the REPO4 have been reduced to REO. Meanwhile, no Fe2O3 has been found in the limitation of XRD, while only a small amount of Fe has been found. At the temperature over 1 000 °C, carbon exists in the systems as CO. According to thermodynamics calculation, Fe2O3 in the systems will be reduced to Fe by CO at temperature higher than 710 °C. This is the reason why there is no Fe2O3 detected in XRD patterns. Therefore, the effect of Fe2O3 on the dephosphorization efficiency in the temperature region is the same as Fe. It also can be found that Fe has no obvious effect on the carbon thermal reduction of REPO4, and does not reacted with P to form any compounds.
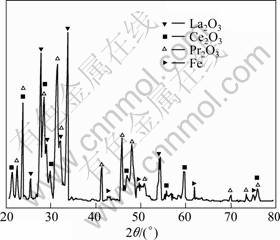
Fig.6 XRD pattern of pellet of monazite mixed with 5% Fe2O3 after roasting at 1 500 °C for 2 h
4 Conclusions
1) The charred coal is an effective candidate for removing phosphorus to form monazite. There is large dephosphorization efficiency when the roasting temperature is between 1 200 and 1 400 °C. The dephosphorization rate reaches 98 % when the pellets of the monazite and charred coal are roasted at 1 400 °C for 2 h.
2) The roasting temperature is the main factor influencing the dephosphorization efficiency of the monazite using the charred coal, and the roasting time has less effect on it.
3) When the particle size of the monazite is 75 mm, the particle size of the charred coal has a significant influence on the dephosphorization efficiency of the monazite. High dephosphorization efficiency can be reached only when the particle size of the charred coal is about 150 mm.
4) Fe and Fe2O3 have no obvious effect on the dephosphorization efficiency of the monazite using the charred coal when the temperature is lower than 1 500 °C.
References
[1] YU Zong-sen. Application of rare earth in iron and steel [M]. Beijing: Metallurgical Industry Press, 1987. (in Chinese)
[2] WU Zhi-wei, ZHANG Jin-dong, CHEN Yi, MENG Liang. Effect of rare earth addition on microstructural, mechanical and electrical characteristics of Cu-6%Fe microcomposites [J]. Journal of Rare Earths, 2009, 27(1): 87-89.
[3] XU Guang-xian. Rear earth [M]. 2nd ed. Beijing: Metallurgical Industry Press, 2002. (in Chinese)
[4] LIN Xiao-ying, LI Shu-jiang, LU Yue-mei, CHEN Shao-chun, SHEN Da, LI Meng-dong. Effect of melting method of rare earth ferrosilicon alloy on spheroidzing ability of spheroidizer [J]. Chinese Rare Earth, 2006, 27(5): 40-43. (in Chinese)
[5] ZHANG Cheng-xiang, REN Cun-zhi, LI Chun-chai, TU Gan-feng, JING Mei-hui. Preparation of rare earth ferrosilicon alloy by carbothermal reduction of bastnaesite: China, 92109998.3[P]. 1994-06-15.
[6] ZHAO Qun, TU Gan-feng, REN Cun-zhi, ZHANG Shi-rong. Micro-mechanism of disintegration of RE-silicide alloy containing phosphorus [J]. Journal of Rare Earths, 2001, 19 (4): 284-287.
[7] XIANG Jun, ZHANG Cheng-xiang, TU Gan-feng, REN Cun-zhi. Thermal decomposition behaviour of natural bastnasite crystal in calcination [J]. Transaction of Nonferrous Metals Society of China, 1994, 14(4): 34-36.
[8] REN Cun-zhi, TU Gan-feng, LI Chun-chai, ZHANG Cheng-xiang. Resistance powderization analysis of rare earth silicide alloys [J]. Chinese Rare Earth, 1997, 18(2): 54-56. (in Chinese)
[9] ZHAO Qun, TU Gan-feng, QIU Zhu-xie. Studies on carbon-thermal reduction process of rare earth concentrate with high content of phosphorus [J]. Chinese Rare Earth, 2003, 24 (4): 39-41. (in Chinese)
[10] WU Wen-yuan, SUN Shu-chen, YU Qing-chun. Heat decomposing mechanism of mixed rare earth concentrate composed of bastneasite and monazite [J]. Chinese Journal of Rare Metals, 2002, 26(1): 76-79.
[11] ZHANG Xian-heng, JIA Yan-hua, XU Sheng-hua. Dephosphorization techniques research of high-content phosphorate concentrate[J]. Ferro-alloy, 2003, 1: 27-30. (in Chinese)
[12] TU Gan-feng, XING Peng-fei, REN Cun-zhi, LI Chun-cai, ZHANG Cheng-xiang. Kinetics of the dephosphorization of lanthanum phonspate with carbon [J]. Journal of Northeastern University, 1998, 19 (s1): 50-53.(in Chinese)
[13] Chemical Industry Books Editing Room. Phosphorus and phosphate [M]. Beijing: Chemical Industry Press, 1963. (in Chinese)
[14] ABDEL A M. Physical and thermal treatment of phosphate ores—Overview [J]. Inter Journal of Mineral Proc, 85(4): 59-84.
[15] XING Peng-fei, TU Gan-feng, GAO Hao-jun, WU Wen-yuan. On the high-temperature dephosphorization of monazite concentrate with coking coal [J]. Journal of Northeastern University, 2010, 31(4): 536-539. (in Chinese)
(Edited by LI Xiang-qun)
Foundation item: Project (59804003) supported by the National Natural Science Foundation of China
Corresponding author: XING Peng-fei; Tel: +86-24-83681320; E-mail: xingpf@smm.neu.edu.cn
DOI: 10.1016/S1003-6326(10)60660-7