J. Cent. South Univ. Technol. (2010) 17: 659-665
DOI: 10.1007/s11771-010-0537-x 
Superplastic deformation behavior and mechanism of 1420 Al-Li alloy sheets with elongated grains
ZHANG Xin-ming(张新明), ZHENG Da-wei(郑大伟), YE Ling-ying(叶凌英), TANG Jian-guo(唐建国)
School of Materials Science and Engineering, Central South University, Changsha 410083, China
? Central South University Press and Springer-Verlag Berlin Heidelberg 2010
Abstract: True stress-true strain curve, microstructure and texture information were obtained to investigate the superplastic deformation behavior of 1420 Al-Li alloy sheets with initial elongated grains. From the true stress-true curve, the stress increases with the increase of strain to 0.15, then dramatically decreases with the increase of strain to 0.80, and finally keeps almost a horizontal line. Meanwhile, initial elongated grains are gradually changed into equiaxed grains and the initial strong Brass {0 1 1} <2 1 1> and S {1 2 3} <6 3 4> orientations are turned into nearly random orientation with increasing strain. All these results suggest that dislocation activity is the dominant mechanism during the first stage, then dynamic recrystallization occurs, and grain rotation is expected as an accommodation for grain boundary sliding (GBS). At larger strains, grain boundary migration (GBM) becomes necessary to accommodate GBS.
Key words: 1420 Al-Li alloy; superplasticity; microstructure; texture; dislocation
1 Introduction
Generally, the fine equiaxed grains (<10 μm) are the typical microstructural conditions for the superplastic deformation of metallic materials at high temperatures and intermediate strain rate [1-3]. The sheets with such microstructures can be prepared by [4]: (1) thermo- mechanical processing (TMP) or severe plastic deformation before superplastic deformation (SPD); and (2) dynamic recrystallization during SPD.
For the microstructure induced by way (1), there is a strongly promoted, although not unanimous, view that the grain boundary sliding (GBS) plays a dominant role in SPD [1]. However, for several materials such as AA8090 alloy and Al-Li-Cu-Mg alloy [1-2], which initially contain elongated or banded microstructures, the flow behavior of the materials showing superplasticity by dynamic recrystallization is reported to be quite different from the GBS.
Although a number of literatures reported the superplasticity of the 1420 Al-Li alloy sheets, most of them mainly concentrated on the development of the methods for the material with fine equiaxed grains [5-7] and the optimization of superplastic condition [8]. The investigation on superplastic behavior of the alloy sheets with an initial elongated grain microstructure is limited.
In this work, the evolution of microstructure and texture during SPD of 1420 Al-Li alloy sheets with elongated grains was examined, with the objective to find out how equiaxed grains microstructure and nearly random orientation evolve from elongated grains microstructure and strong Brass and S orientations, and then the superplastic mechanism of the alloy sheets was explored.
2 Experimental
1420 alloy sheets with a thickness of 2.0 mm and a composition of Al-5.3Mg-2.12Li-0.11Zr (mass fraction, %) were used in this work. The SPD specimens had a gage length of 10.0 mm and a width of 5.8 mm. The tensile tests were performed on a RWS50 testing machine with the constant cross-head at an initial strain rate
of 8×10-4 s-1 and temperature of 500 ℃. Before the tensile test, the samples were first heated to 500 ℃ and held for 15 min to stabilize the microstructure. To study the process of the microstructure evolution, the samples were stretched to the true strains of 0.10, 0.15, 0.35, 0.55, 0.80, 1.20 and 1.70, respectively, which encompassed all major regions where the microstructure and texture were changed dramatically according to the true stress-strain curve.
The samples observed by the optical microscope (OM) were first mechanically polished and then chemically etched by a special solution (HF-4HCl- 4HNO3-15H2O, volume fraction, %). The mean grain size was determined from more than 350 grains.
Samples for texture analysis were prepared in the rolling plane (cross section of the rolling direction (RD) and the transverse direction (TD)) at the half-thickness layer of the sheet. After chemically etched by NaOH (5%, mass fraction), the samples were measured on a Bruker D8 Discover X-ray goniometer.
3 Results
3.1 Initial microstructure
The initial grains of 1420 Al-Li alloy sheets used comprise an elongated grain microstructure as shown in Fig.1(a), which suggests that the sheets are not recrystallized.
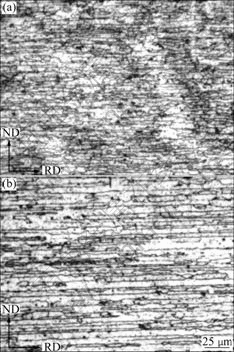
Fig.1 Optical photographs from longitudinal section (cross section of normal direction (ND) to RD) of specimens: (a) As- received; (b) Annealed at 500 ℃ for 1 h
When the specimens are annealed at 500 ℃ for 1 h, the elongated grain shape is retained (Fig.1(b)), which indicates that the process may be associated with recovery but no recrystallization including the nucleation of new grains and their growth occurs. The addition of Zr in 1420 Al-Li alloy results in the formation of fine dispersion of cubic β′ (Al3Zr) particles, which are usually not affected by the solution-heat treatment at 530 ℃ [9]. Thus, during the whole stretching conducted at 500 ℃ β′ particles are conserved, which are very fine and homogeneously distributed, and effective in preventing the grain boundary migration during annealing. Therefore, β′ particles in the alloy sheets suppress recrystallization.
3.2 True stress-true strain curves
Fig.2(a) shows the ideal superplastic deformation curve [10], representing the material flow at a constant stress level. However, the true stress-true strain curve from the present tensile test, which shows the elongation of 480% to failure, is quite different from Fig.2(a) (see Fig.2(b)). This suggests that the process of the superplastic deformation of the sheets with elongated grains can be divided into three stages: during the initial stage (ε≤0.15), the true tress increases rapidly with a peak at the true strain of 0.15 and then dramatically decreases until true strain of 0.8 (0.15<ε≤0.80). At larger true strains (ε>0.8), the true stress tends to be independent of true strain.
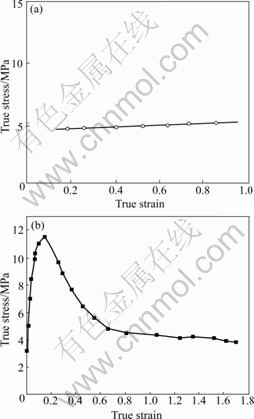
Fig.2 True stress-true strain curves of different samples: (a) Mode of superplastic deformation (Sn-Pb eutectic alloy) [10]; (b) Plot from superplastic tensile test of 1420 Al-Li alloy sheets at initial strain rate of 8×10-4 s-1 and 500 ℃
3.3 Microstructural evolution
Fig.3 illustrates the evolution of the grain microstructure of specimens with the change of strain. It can be seen that along with grain widening, its shape changes but still remains elongated during the initial stage (ε≤0.15).
During the second stage (0.15<ε≤0.80), the elongated grains are changed to nearly equiaxed at the true strain of 0.80 (see Fig.4).
At larger true strains (ε>0.80), weak grain growth is observed according to Fig.5, and the grain shape seems to be equiaxed. Meanwhile, some large cavities appear.
Table 1 shows the mean grain sizes at different stages. During the initial stage (ε≤0.15), grain coarsening occurs, dn increases from 3.5 to 4.9 μm. Then, dr slightly decreases and dn keeps increasing between the true strain range of 0.15-0.80. At larger true strains (ε>0.80), the grains weakly grow, which can be called stable growth.
Fig.6 depicts the relationship between the true strain and the aspect ratio (Ra=dr/dn). Ra decreases weakly during the initial stage (ε≤0.15), and then decreases dramatically from 3.53 to 1.16 (0.15<ε≤0.80), revealing that the elongated grains are changed into the nearly equiaxed ones. At larger true strains (ε>0.80), the aspect ratio almost does not change, meaning that the grain shape keeps equiaxed.
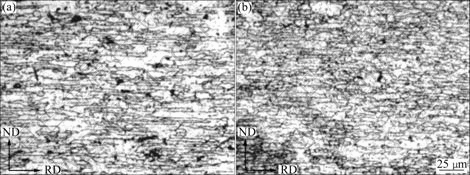
Fig.3 Optical photographs of specimens showing evolution of grain microstructures on longitudinal section: (a) ε=0.10; (b) ε=0.15
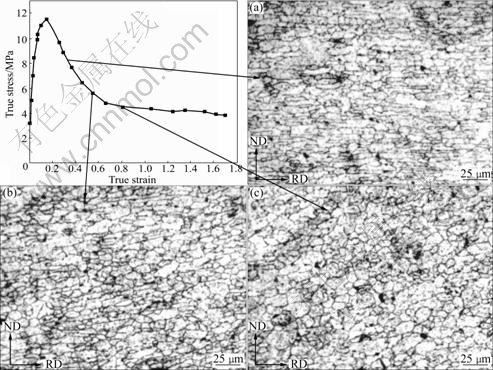
Fig.4 Optical photographs of specimens showing evolution of grains on longitudinal section: (a) ε=0.35; (b) ε=0.55; (b) ε=0.80
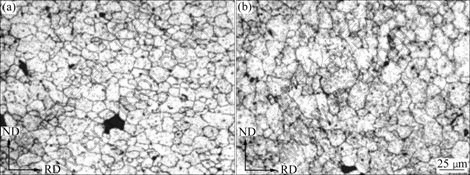
Fig.5 Optical photographs of specimens showing evolution of grains on longitudinal section: (a) ε=1.20; (b) ε=1.70
Table 1 Average grain size, dn and dr in undeformed and deformed samples
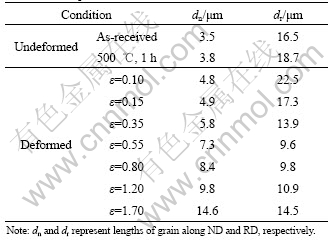
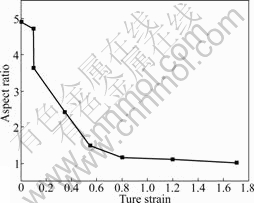
Fig.6 Relationship between aspect ratio and true strain
3.4 Texture evolution
To further study the superplastic mechanism of the alloy sheets, texture information was also applied.
The Brass {0 1 1} <2 1 1> and P {0 1 1} <5 6 6> orientations in α-fiber and S {1 2 3} <6 3 4> and S/Brass orientations in β-fiber are observed to be the preferential in the as-received alloy sheets, as shown in Fig.7.
After annealing at 500 ℃ for 1 h, it is noted that the texture remains unchanged. This suggests that discontinuous recrystallization does not occur.
A slight increase in the density of Brass and S orientations is observed during the initial stage (ε≤0.15), however, the P orientation disappears at the same time.
A weak texture is demonstrated at true strains from 0.15 to 0.80. Fig.8 shows that the maximum density of Brass orientation decreases from 35.4 to 8.7 with increasing strain, and the density of S/Brass orientation also significantly decreases during this stage, as shown in Fig.7.
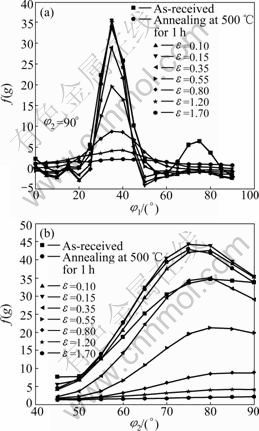
Fig.7 Orientation density f(g) along α-fiber (a) and β-fiber (b) at different true strains during SPD
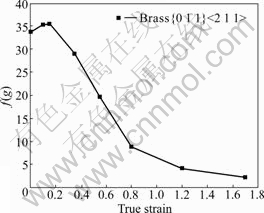
Fig.8 Changes of maximum density of Brass orientation during SPD
At larger true strains (ε>0.80), the orientation becomes almost random (see Fig.7).
4 Discussion
4.1 At initial stage of SPD (ε≤0.15)
The initial microstructure of 1420 Al-Li alloy sheets used comprises elongated grains, which are the characteristics of the deformation microstructure. During the initial stage of SPD, true tress increases rapidly with increasing true strain. There are two possibilities for the case [11]: (1) grain widening during SPD, and (2) the conventional dislocation-related strain hardening.
Generally, when the material is subjected to SPD, strain hardening is negligible and the true stress (σ) just depends on the strain rate
and the true stress can be expressed by:
(1)
where K1 is the material constant depending on the test temperature and the microstructure of the material; and m is the strain rate sensitivity index.
From Ref.[12],
can be represented as
(2)
where A is the dimensionless constant that depends on the creep mechanism; D0exp[-Q/(RT)] is the diffusion coefficient; E is the elastic modulus; b is the Burgers vector; d is the grain size; p is the grain size exponent; n is the stress exponent; Q is the active energy; R and T are the ideal gas constant and thermodynamic temperature, respectively.
So, at a constant temperature and strain rate, the relationship between true stress and grain size can be expressed as
σ∝
(3)
From most models for SPD, the values of both p and n are found to be equal to 2 [12]. Hence, Eq.(3) can be deduced as follows:
σ1=d1σ0/d0 (4)
The grains grow slightly during the initial stage of SPD (ε≤0.15). According to Table 1, the length of the grain along ND increases from 3.5 to 4.9 μm, which, according to Eq.(4), is not enough to fully account for the increase in true stress with increasing strain. Fig.9 shows the difference between the calculated stress by Eq.(4) and that by experiment. Therefore, the dislocation activity might be involved in the stage, which was also suggested in Refs.[11-12].
As the grains have the elongated shape, which may be less for GBS but more favorable for dislocation activity, the density of the Brass orientation shows a slight increase.
In summary, the dramatic increase in the true stress and the slight increase in orientation density suggest that the dislocation activity plays an important role during the initial stage.
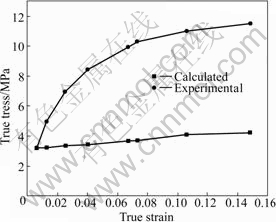
Fig.9 Comparison of true stress obtained from experiment with that from calculation
4.2 At second stage of SPD (0.15<ε≤0.8)
At the true strains from 0.15 to 0.80, the true stress decreases dramatically, which may come from: (1) the gradual decrease in strain rate, and (2) the changes in microstructure of the sheets.
As the tensile tests are conducted at a constant cross-head,
can be represented as [13]
(5)
where li is the actual length of the samples when the strain is εi; t is the deformation time; and v represents the velocity of the constant cross-head.
On the basis of Eqs.(1) and (5), it is clear that with increasing strain li grows up, which leads to the decrease in
and therefore the true stress decreases.
Fig.4 shows that the elongated grains are changed to nearly equiaxed shape during this stage, and the aspect ratio decreases from 3.53 to 1.16 (see Fig.6). The appearance of nearly equiaxed grains suggests that recrystallization occurs, which can account for the drop of flow stress through the maximum stress point. Along with dynamic recrystallization, the misorientation between grains becomes larger, which is more favorable for grain rotation and GBS. The dramatic weakening of the orientation density can be ascribed to the grain rotation, which is also considered to be an accommodating step to GBS.
Fig.10 shows the process of dynamic recrystallization during SPD. The initial elongated deformation microstructures are characterized by grain subdivision in differently oriented regions with low orientation density [14-15]. During the initial stage of SPD, the orientation density increases due to the dislocation activity [16], then, dynamic recrystallization occurs, by which GBS is possibly operative and the grain rotation occurs as an accommodation to GBS.
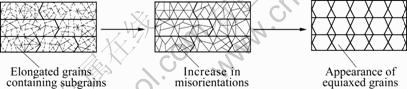
Fig.10 Sketch of process of dynamic recrystallization during SPD
4.3 At last stage of superplastic deformation (ε> 0.80)
At larger strains (ε>0.80), the σ-ε dependence is weak. The grains continue to grow, which, according to Eq.(4), results in strain hardening. However, strain softening occurs with the decrease of true strain rate. At last, two contrary effects may be equal to each other.
During the stable flow stage, grain growth is observed according to the optical metallographs (see Fig.5). The increase in grain size can be due to dynamic grain growth by the imposed strain at the elevated temperature (500 ℃). The relationship between grain size and true strains can be represented as [12]
d=K2εq (6)
where d is the grain size; and K2 and q are constant calculated from the plot of ln d vs ln ε.
For single phase materials q=0.5, however, the values of q are smaller (≈0.1) in aluminum alloys with the dispersion of the second phase particles [12]. In the present study, according to the grain size dn listed in Table 1, q is calculated to be 0.299 as depicted in Fig.11, implying that the microstructures are considered to be stable owing to the contribution of dispersion of β′(Al3Zr) particles. Grain growth is attributed to grain boundary migration, which becomes necessary to accommodate stress concentration built up by GBS.
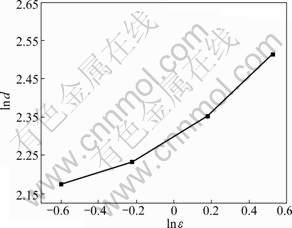
Fig.11 Relationship between ln d and ln ε
Fig.12 shows the Ashby-Verrall superplastic model [13]. The characteristic of it is the fact that the grain shape does not change during stretching. Fig.13 shows the deformation process of this stage. The specimen elongation is accomplished by grain rearrangement that in turn takes place by GBS.
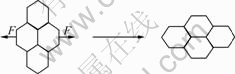
Fig.12 Ashby-Verrall model [13]
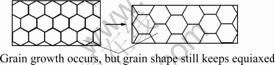
Fig.13 Sketch of deformation process of last SPD
Therefore, at this stage the superplastic mechanism is dominated by GBS, and grain boundary migration, which makes contribution to grain growth, becomes the accommodation process.
5 Conclusions
(1) At the initial stage (ε≤0.15), the misorientation increase and dislocation activity play a key role in the SPD of 1420 Al-Li alloy sheets.
(2) Dynamic recrystallization begins to occur when the true strain reaches 0.15. With recrystallization, the misorientation between grains becomes larger, which is favorable for grain rotation and GBS. At the second stage (0.15<ε≤0.80), GBS is possibly operative and the grain rotation occurs as an accommodation to GBS.
(3) At larger true strains (ε>0.80), grain growth continues, but the microstructure still keeps stable owing to the contribution of β′(Al3Zr) particles. The superplastic mechanism is dominated by GBS, and grain boundary migration, which makes contribution to grain growth, becomes the accommodation process during the last stage.
References
[1] BATE P S, RIDLEY N, ZHANG B. Mechanical behavior and microstructural evolution in superplastic Al-Li-Mg-Cu-Zr AA8090 [J]. Acta Materialia, 2007, 55(15): 4995-5006.
[2] SAKAI G, HORITA Z, LANGDON T G. Grain refinement and superplasticity in an aluminum alloy processed by high-pressure torsion [J]. Materials Science and Engineering A, 2005, 393(1/2): 344-351.
[3] ZHANG Xin-ming, LUO Zhi-hui, DU Yu-xuan, YE Ling-yin. Effect of two-stage ageing on superplasticity of 1420 Al-Li alloy [J]. Materials and Heat Treatment, 2007, 28(4): 55-58. (in Chinese)
[4] KAIBYSHEV R, OSIPOVA O. Superplastic behavior of an Al-Li-Cu-Mg alloy [J]. Materials Science and Technology, 2005, 21(10): 1209-1216.
[5] ZHANG Xin-ming, YE Ling-ying, DU Yu-xuan, LUO Zhi-hui. Particle stimulated nucleation of recrystallization in 01420 Al-Li alloy [J]. Journal of Central South University: Science and Technology, 2007, 38(1): 19-23. (in Chinese)
[6] FIGUEIREDO R B, MEGUMI K, CHENG X, LANGDON T G. Achieving superplastic behavior in fcc and hcp metals processed by equal-channel angular pressing [J]. Materials Science and Engineering A, 2008, 493: 104-110.
[7] MAZILKIN A A, MYSHLYAEV M M. Microstructure and thermal stability of superplastic aluminium-lithium alloy after severe plastic deformation [J]. Journal of Materials Science, 2006, 41(12): 3767-3772.
[8] ZHANG Yan-ling, GUO He-ping, LI Zhi-qiang. The experimental research on superplastic performance of fine-grained 1420 Al-Li alloy [J]. Journal of Plasticity Engineering, 2009, 16(4): 134-137. (in Chinese)
[9] FURUKAWA M, IWAHASHI Y, HORITA Z, NEMOTO M, TSENEV N K, VALIEV R Z, LANGDON T G. Structural evolution and the Hall-Petch relationship in an Al-Mg-Li-Zr alloy with ultra-fine grain size [J]. Acta Materialia, 1997, 45(11): 4751-4757.
[10] PADMANABHAN K A, DAVIES G L. Superplasticity [M]. Berlin: Springer, 1980: 7-37.
[11] LIUJ, CHAKRABARTID J. Grain structure and microtexture evolution during supperplastic forming of a high strength Al-Zn-Mg-Cu alloy [J]. Acta Materialia, 1996, 44(12): 4647-4661.
[12] FAN Wen-jie. Flow behavior and microstructural evolution during superplastic deformation of AA8090 Al-Li alloy [D]. Ottawa: Manitoba, 1998: 11-116.
[13] WU Shi-chun. Theories on superplastic deformation [M]. Beijing: National Defence Industry Press, 1997: 12-92. (in Chinese)
[14] DOHERTY R D, HUGHES D A, HUMPHREYS F J, JONAS J J, JUUL JENSEN D, KASSNER M E, KING W E, MCNELLEY T R, MCQUEEN H J, ROLLETT A D. Current issues in recrystallization: A review [J]. Materials Science and Engineering A, 1997, 238(2): 219-274.
[15] FAN W J, KASHYAPB B P, CHATURVEDI M C. Anisotropy in flow and microstructural evolution during superplastic deformation of a layered-microstructured AA8090 Al-Li alloy [J]. Materials Science and Engineering A, 2003, 349(1/2): 166-182.
[16] LIU Qing, HUANG Xiao-xu, YAO Mei, YANG Jin-feng. On deformation-induced continuous recrystallization in a superplastic Al-Li-Cu-Mg-Zr alloy [J]. Acta Metall, 1992, 40(7): 1753-1762.
Foundation item: Project(2006DFA53250) supported by the International Science and Technology Cooperation Program of China; Project(2005CB623706) supported by the National Basic Research Program of China
Received date: 2009-12-03; Accepted date: 2010-03-16
Corresponding author: ZHANG Xin-ming, PhD, Professor; Tel: +86-731-88830265; E-mail: xmzhang@mail.csu.edu.cn
(Edited by CHEN Wei-ping)