Article ID: 1003-6326(2005)02-0340-04
Two-way shape memory effect and its stability in Ti-Ni-Hf high temperature shape memory alloy
MENG Xiang-long(孟祥龙), WU Ye(吴 冶), CAI Wei(蔡 伟), ZHAO Lian-cheng(赵连城)
(School of Materials Science and Engineering, Harbin Institute of Technology, Harbin 150001, China)
Abstract: The two-way shape memory effect(TWSME) in a Ti36Ni49Hf15 high temperature shape memory alloy(SMA) was systematically studied by bending tests. In the TiNiHf alloy, the martensite deformation is an effective method to get two-way shape memory effect even with a small deformation strain. The results indicate that the internal stress field formed by the bending deformation is in the direction of the preferentially oriented martensite variants formed during the bending deformation. Upon cooling the preferentially oriented martensite variants form under such an oriented stress field, which should be responsible for the generation of the two-way shape memory effect. Proper training process benefits the formation of the oriented stress field, resulting in the improvement of the two-way shape memory effect. A maximum TWSME of 0.88% is obtained in the present alloy.
Key words: TiNiHf alloy; high temperature shape memory alloy; two-way shape memory effect; training; stability CLC number: TG139.6
Document code: A
1 INTRODUCTION
The ternary TiNiHf alloy has been considered the most prospective candidate with Hf replacing Ni in the TiNi alloy for applications at high temperature compared with the other high temperature SMAs due to the low cost and excellent workability[1-3]. A lot of investigations have been focused on its constitutional phase, microstructure and substructure, transformation behavior, mechanical property and shape memory effect, and precipitation behavior during aging[4-10]. Ti36Ni49Hf15 alloy shows a one-way shape memory effect with about 3% completely reversible strain when it is deformed at ambient temperature[11]. Yet up to now, except our previous works[12], seldom results about the two-way shape memory effect in the TiNiHf alloys were reported. Dissimilar to TiNi alloys, a small two-way shape memory effect in the aged TiNiHf alloys can be obtained directly by the deformation of the martensite without training[12]. And the corresponding mechanism is not clear so far. However, it is no doubt that the obtained TWSME in TiNiHf alloys would be beneficial to the applications of the TiNiHf alloy on the micro-actuators, micro-switches and so on. In this paper, the effect of martensite deformation and training process on the TWSME in TiNiHf alloys and the stability of TWSME during thermal cycling were investigated.
2 EXPERIMENTAL
The preparation of the Ti36Ni49Hf15 alloy used in the experiment has been described in the previous papers[12]. After homogenized at 1223K for 1.5h, the ingot was hot rolled into a plate of 2.1mm in thickness. The specimens were cut in the rolling direction with the size of 1mm×0.5mm×50mm, mechanically polished and solution-treated at 1273K for 1h in vacuum. The schematic illustration for shape memory effect measurement is shown in Fig.1. The specimens were bent against the cylindrical rod to the deformation position at different temperatures, and then heated up to 600K.
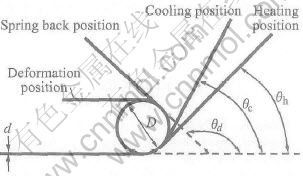
Fig.1 Schematic illustration for TWSME measurement in bending test
The training procedure involves the repeated cycles as follows: 1) bend the specimen to the deformation position; 2) unload and the specimen spring back to the spring-back position; 3) heat the specimen up to 600K; 4) quench the specimen to the water. The bending deformation strain is estimated by εd=d/(D+d). The bending deformation strains in the present experiment are 2%, 3.3%, 4.5%, 5.7% and 7.1%, respectively. The shape recovery strain is calculated by εre= (180-εh)×εd /180°. The TWSME is measured by the value of εtw=(θc-θh)×εd /180°.
3 RESULTS AND DISCUSSION
Fig.2 shows the variation of the strain with the temperature for the Ti36Ni49Hf15 specimens deformed to the different strains. It can be seen that the recovery of the deformation starts at the beginning of the heating process with increasing temperature. When the specimens are heated to a certain temperature above Af, the shape recovery finishs. Moreover, the shape recovery finish temperature increases with the increasing deformation strain, indicating that deformation leads to the increase of the reverse martensitic transformation temperatures of the present alloy. From the curves shown in Fig.2, it can be seen that the shape recovery finish temperature of the specimen deformed to 7.1% is higher than that of the specimen deformed to 2% for about 12K. This suggests that the deformation induces the stabilization of martensite.
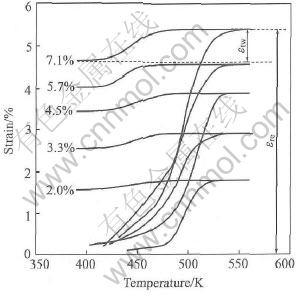
Fig.2 TWSME of Ti36Ni49Hf15 alloy with various deformation strains
Fig.3 depicts the effect of deformation strain on the TWSME in the Ti36Ni49Hf15 alloy. The TWSME almost increases linearly with the increase of the bending deformation strain. When the specimen is deformed to 7.1% at martensite state directly, the obtained maximum TWSME is 0.45%. Training procedure increases the TWSME of the Ti36Ni49Hf15 alloy obviously. After 30 cycles, the maximum TWSME of 0.88% in the Ti36-Ni49Hf15 alloy is obtained when the deformation strain is 7.1%. Dissimilar to that in the TiNi alloy, it is not found that the TWSME decreases with the increasing deformation strain when the deformation strain exceeds a certain value. This is because that the elongation of the experimental alloy at room temperature is only about 10%[11, 12] so that it cannot be trained with a larger strain.
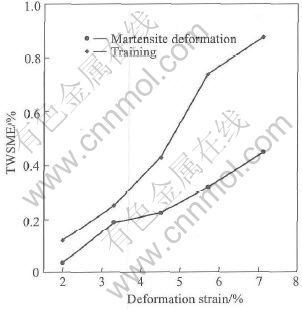
Fig.3 Effect of deformation on TWSME in Ti36Ni49Hf15 alloy
Fig.4 shows the effect of number of training cycles on the TWSME in the Ti36Ni49Hf15 alloy. It can be seen that the TWSME increases rapidly in the beginning several cycles and then does not change with the further increasing number of training cycles. This result indicates that at the onset of training procedure the dislocations are introduced continuously to create an oriented stress field, which is gradually strengthened. Further increasing the number of training cycles, the stress field created by the beginning several cycles would suppress the introduction of more dislocations during the subsequent training process. Thus, the two-way shape memory strain becomes stable rapidly after the beginning several training cycles.
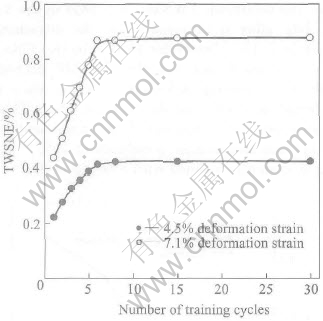
Fig.4 Effect of number of training cycles on TWSME in Ti36Ni49Hf15 alloy
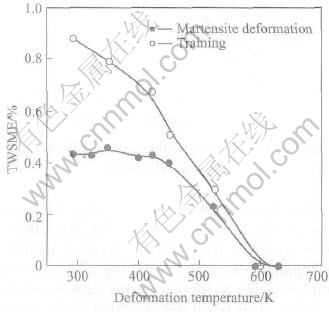
Fig.5 Effect of deformation temperature on TWSME for Ti36Ni49Hf15 alloy with
deformation strain of 7.1%
Fig.5 shows the effect of deformation temperature on the TWSME in the Ti36Ni49Hf15 alloy with the deformation strain of 7.1%. For the specimens deformed at martensite state directly, the TWSME almost does not change with the increasing deformation temperature when the deformation temperature is below 457K. Further increasing the deformation temperature, the TWSME decreases rapidly and reaches zero at about 600K. For the specimens after 30 training cycles, the TWSME decreases continuously with the increasing deformation temperature. When the deformation temperature is over 600K, the TWSME reaches zero. This indicates that during the training process, the amount of the irreversible defects increases with the increasing deformation temperature.
Fig.6 shows the stability of TWSME obtained by martensite deformation and training in the Ti36Ni49Hf15 alloy with the deformation strain of 7.1%. The TWSME decreases and becomes stable with the increasing number of thermal cycles, similar to the degradation of the TWSME during the thermal cycles in the TiNi alloy[13]. For the specimens deformed to 7.1% at martensite state directly and after training, after 30 thermal cycles the TWSME decreases to 0.29% and 0.39% respectively, corresponding to more than 50% of initial value of TWSME before thermal cycling.
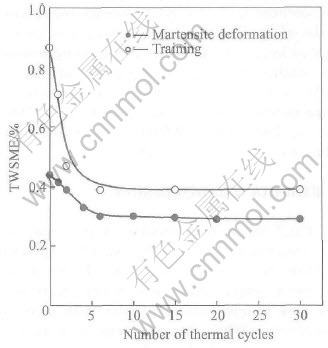
Fig.6 Effect of thermal cycling on TWSME for Ti36Ni49Hf15 alloy with deformation strain of 7.1%
The TWSME of the Ti36Ni49Hf15 alloy arises from the oriented stress field created by the training process. The dislocations introduced by the training create an oriented stress field. Upon cooling, the preferentially oriented martensite would form under such an oriented stress field to induce the TWSME. But compared with the TWSME of the TiNi alloy obtained by the traditional training methods, the TWSME of the Ti36Ni49Hf15 alloy is small. This is because that the deformation mechanisms of the two alloys are different from each other. In the solution-treated TiNi alloy, when it is deformed at full martensite state, its stress-strain curve exhibits a stress plateau corresponding to the reorientation of the martensite variants. In the present alloy, when it is deformed at full martensite state, no obvious stress plateau is observed in the stress-strain curve indicating that the corresponding deformation mechanism is the martensite reorientation accompanied by the slip of dislocations. Moreover, for the Ti36Ni49Hf15 alloy, its strength of the matrix of the martensite is low[11, 14, 15]. So it is understandable that during the training process the dislocation slip is easy to be introduced. On the one hand, the easy introduction of the dislocation leads to that the oriented stress field is created easily to induce a TWSME in the Ti36Ni49Hf15 alloy even with a small deformation strain. On the other hand, the serious dislocation slip would prohibit the movement of the boundaries between the parent phase and the martensite to some extent. Thus the TWSME obtained in the Ti36Ni49Hf15 alloy is small. Increasing the deformation temperature up to near Ms, the critical stress for dislocation slip is almost equal to that for the martensite reorientation. So the serious dislocation slip is introduced when the deformation temperature is high, resulting in the deterioration of the TWSME.
4 CONCLUSIONS
1) The TWSME almost increases with the increase of the deformation strain. Training improves the TWSME of the Ti36Ni49Hf15 alloy high temperature SMA. The TWSME increases and then keeps constant with the increasing training cycles.
2) The TWSME of the Ti36Ni49Hf15 alloy decreases rapidly at the beginning of the thermal cycling and then does not change with the further increasing number of thermal cycles. Compared with the TiNi alloy, the Ti36Ni49Hf15 alloy shows poor stability of the TWSME.
3) The stress field formed by martensite deformation or training should be responsible for the TWSME in the Ti36Ni49Hf15 alloy.
REFERENCES
[1]Besseghini S, Villa E, Tuissi A. Ni-Ti-Hf shape memory alloy: effect of aging and thermal cycling [J]. Mater Sci Eng A, 1999, A273-275: 390-394.
[2]Angst D R, Thoma P E, Kao M Y. The effect of hafnium content on the transformation temperatures of Ni49Ti52-xHfx shape memory alloys [J]. Journal De Physics IV. C8, 1995, 747-752.
[3]Han X D, Wang R, Zhang Z, et al. A new precipitate phase in a TiNiHf high temperature shape memory alloy [J]. Acta Materialia, 1998, 46: 273-281.
[4]Firstov G S, van Humbeeck J, Koval Y N. Comparison of high temperature shape memory behaviour for ZrCu-based, Ti-Ni-Zr and Ti-Ni-Hf alloys [J]. Scripta Materialia, 2004, 50: 243-248.
[5]Liang X L, Chen Y, Shen H M, et al. Thermal cycling stability and two-way shape memory effect of Ni-Cu-Ti-Hf alloys [J]. Solid State Communications, 2001, 119: 381-385.
[6]Hsieh S F, Wu S K. Martensitic transformation of quaternary Ti50.5-xNi49.5Zrx/2Hfx/2(x=0-20%) shape memory alloys [J]. Materials Characterization, 2000, 45:143-152.
[7]Dalle F, Pasko A, Vermaut P, et al. Melt-spun ribbons of Ti-Hf-Ni-Re shape memory alloys: first investigations [J]. Scripta Materialia, 2000, 43: 331-335.
[8]Dalle F, Despert G, Vermaut P H, et al. Ni49.8Ti42.2-Hf8 shape memory alloy strips production by the twin roll casting technique [J]. Mater Sci Eng A, 2003, A346: 320-327.
[9]Zheng Y F, Zhao L C, Ye H Q. HREM study on the intervariant structure of Ti-Ni-Hf B19′ martensite [J]. Scripta Materialia, 1998, 37:1249-1253.
[10]Morawiec H, Leltko J, Koval Y N, et al. High-temperature Cu-Al-Nb shape memory alloys [J]. Materials Science Forum, 2000, 327-328: 291-294.
[11]Meng X L, Zheng Y F, Wang Z, et al. Effect of aging on the phase transformation and mechanical behavior of Ti36Ni49Hf15 high temperature shape memory alloy [J]. Scripta Materialia, 2000, 42(4): 335-340.
[12]Meng X L, Zheng Y F, Wang Z, et al. Shape memory properties of the Ti36Ni49Hf15 high temperature shape memory alloy [J]. Materials Letters, 2000, 45:128-132.
[13]Kudoh Y, Tokonami M, Miyazaki S, et al. Crystal structure of the martensite in Ti-49.2at.%Ni alloy analyzed by the single crystal X-ray diffraction method [J]. Acta Metallurgica, 1985, 33: 2049-2056.
[14]Meng X L, Cai W, Zheng Y F, et al. Stress-induced martensitic transformation behavior of a Ti-Ni-Hf high temperature shape memory alloy [J]. Materials Letters, 2002, 55:111-115.
[15]Meng X L, Cai W, Wang L M, et al. Microstructure of stress-induced martensite in a Ti-Ni-Hf high temperature shape memory alloy [J]. Scripta Materialia, 2001, 45:1177-1182.
Received date: 2004-11-20; Accepted date: 2005-01-18
Correspondence: MENG Xiang-long, Associate Professor, PhD; Tel: +86-451-86418745; E-mail: xlmeng@hit.edu.cn
(Edited by LI Xiang-qun)