文章编号:1004-0609(2009)12-2210-06
微弧氧化非连续成膜对膜层结构及性能的影响
张欣盟1,杨学勤2,田修波1,巩春志1,杨士勤1
(1. 哈尔滨工业大学 材料科学与工程学院 现代焊接生产技术国家重点实验室,哈尔滨 150001;
2. 上海航天技术研究院 800所,上海 201600)
摘 要:在含有Na2SiO3和KOH的电解液中以恒定电压氧化方式对工业纯铝进行微弧氧化处理,研究电压对非连续微弧氧化成膜特性的影响。采用XRD及SEM对微弧氧化膜的相组成及表面形貌进行分析。结果表明:非连续微弧氧化的电流在工作间隔处出现一定程度的降低;非连续工作模式的膜层生长速率与连续模式基本相同,并且都随工作电压的增加而增加;不同成膜模式所生长的微弧氧化膜均由较多的γ-Al2O3和少量的α-Al2O3相组成;非连续成膜方式对微弧氧化陶瓷膜的形貌影响不大,且未造成氧化膜分层现象;不同成膜模式下所形成的微弧氧化陶瓷层的耐磨性能和耐腐蚀性能随工作电压变化具有相同的变化规律,均随电压的增加而增大;非连续成膜提高了微弧氧化控制的灵活性。
关键词:纯铝;微弧氧化;非连续模式;耐磨性;耐蚀性
中图分类号:TG 174.451 文献标识码: A
Effect of discontinuous micro-arc oxidation on structure and properties of fabricated coatings
ZHANG Xin-meng1, YANG Xue-qin2, TIAN Xiu-bo1, GONG Chun-zhi1, YANG Shi-qin1
(1. State Key Laboratory of Advanced Welding Production and Technology, School of Materials Science and Engineering, Harbin Institute of Technology, Harbin 150001, China;
2. The 800th Institute, Shanghai Academy of Spaceflight Technology, Shanghai 201600, China)
Abstract: Pure aluminum was treated by micro-arc oxidation in electrolyte containing Na2SiO3 and KOH at constant voltage mode. The effect of voltage on the properties of the coating prepared by discontinuous micro-arc oxidation was investigated. The phase composition and surface morphologies of MAO coatings were analyzed by XRD and SEM. The results show that, for the discontinuous MAO, the current drops to some extent at the interrupted point. MAO coatings fabricated by different modes show the similar thickness that increases with increasing oxide time. The processing mode has slight effects on the phase composition of MAO coatings, which are mainly composed of γ-Al2O3 and α-Al2O3. The surface morphology of the MAO coatings is hardly influenced by processing mode and no lamination is observed for the coatings prepared by discontinuous mode. The coatings fabricated by different modes possess the similar changing rules of wear resistance and corrosion resistance. This discontinuous mode improves the control flexibility during micro-oxidation processes.
Key words: pure aluminum; micro-arc oxidation; discontinuous mode; wear resistance; corrosion resistance
微弧氧化(Micro-arc oxidation, MAO)技术是一种能在Al、Mg和Ti等有色金属及其合金表面原位生长陶瓷膜的新技术。该技术是在传统阳极氧化的基础上发展而来,但其施加几百伏的高压,突破了阳极氧化对电压的限制。它利用微弧放电区局部瞬间高温高压作用直接把基体金属变成氧化物陶瓷[1]。该技术制备的陶瓷膜具有结合力强、耐磨、耐蚀、抗热冲击及良好的绝缘性等优点[2-4]。目前,国内外关于微弧氧化技术的研究主要集中在功能陶瓷膜层制备、溶液配方优化[5-7]等方面,整个成膜过程一般一次完成,而关于非连续微弧氧化工作模式的研究却未见报道。
非连续微弧氧化成膜具有非常重要的现实意义。一方面,当处理工件尺寸较大、氧化电流较高时,如果电解液冷却系统能力不足,可以采用间歇工作方式以控制溶液温度。另一方面,为了使所制备的微弧氧化膜层获得较好的综合性能,有时需要利用不同的溶液体系进行处理,成膜过程发生中断。另外在实验过程中有时也需要暂停处理,对已生成的膜层进行分析判断,调整工艺参数,以达到对所制备膜层精确控制的目的。因此,本文作者对非连续微弧氧化进行了研究,以探索此处理模式对所形成陶瓷膜组织结构和性能的影响。
1 实验
实验材料为工业纯铝,试样规格为60 mm×25 mm×0.5 mm。采用自行研制的20 kW微弧氧化设备进行微弧氧化处理,其装置包括高压直流脉冲电源、不锈钢工作槽、搅拌装置、冷却系统。实验以铝试样为阳极,不锈钢槽作阴极,所用溶液为硅酸钠和氢氧化钾复合体系。在微弧氧化过程中保持电压不变,具体实验方案如下:总工作时间10 min,频率 500 Hz,脉宽200 μs,在电压依次为420、460、500和540V的条件下对试样分别进行连续性成膜和非连续性成膜处理。非连续微弧氧化成膜实验具体如下:当工作到总时间的一半时(5 min),将电压迅速调至0 V,停留5 min后再将电压加至工作值。
采用测量误差小于1%的TT240型(北京时代)涡流测厚仪对膜层厚度进行测量。利用X射线衍射(XRD)、扫描电子显微镜(SEM)对不同成膜方式制备的陶瓷膜的相组成、表面及截面形貌进行分析。通过球-盘式摩擦磨损实验机,在载荷1 N、旋转半径3 mm、转速50 r/min的条件下对处理试样的摩擦性能进行考察。利用CHI604C型(上海华辰)电化学分析仪在3.5% NaCl溶液中对膜层的抗腐蚀性能进行评估。
2 结果与分析
2.1 电流随时间的变化曲线
图1所示为不同成膜电压下连续成膜和非连续成膜微弧氧化电流随时间的变化曲线。从图1可以看出,不同工作电压的微弧氧化电流都随工作时间的延长逐渐减小。这是因为放电开始时,表面生成的微弧氧化层的厚度较薄,比较容易被击穿,故同时放电点较多,电流较大。随着氧化时间的延长,微弧氧化膜变厚,击穿越来越困难,发生放电的点变少,因此,电流随之变小。同时,从图1中还可以看出,非连续模式的微弧氧化电流在工作中断处都有一定程度的降低。因溶液电导率与其温度密切相关,当温度较低时,溶液电导率较小[8],从而导致在恒压条件下,施加在陶瓷膜上的分压减少,致使工作电流降低。因非连续微弧化模式在工作间断时溶液温度有所降低,所以出现再次工作时氧化电流减小的现象。
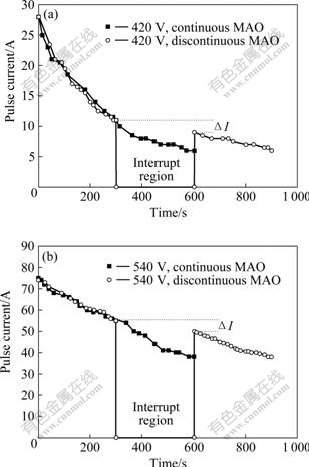
图1 微弧氧化电流随时间的变化曲线
Fig.1 Changing curves of pulse current with time during MAO process: (a) 420 V; (b) 540 V
2.2 陶瓷层的厚度测试
图 2所示为不同电压条件下成膜方式对微弧氧化陶瓷层厚度的影响。从图2可以看出,连续成膜和非连续成膜所形成的陶瓷膜的厚度基本相同,并且都随着工作电压的增加而增加。这说明在不同处理电压条件下两种成膜方式的成膜速率大体相同,成膜速率并没有因非连续成膜时中途的放电中断而减缓。
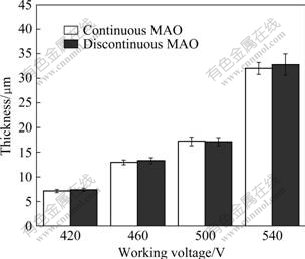
图2 不同电压条件下成膜方式对微弧氧化陶瓷层厚度的影响
Fig.2 Effect of MAO mode on coating thickness at different voltages
2.3 陶瓷层的相组成分析
用X射线衍射仪(XRD) 分别对电压为500 V时不同成膜方式制备的陶瓷膜的相组成进行了分析,结果如图3所示。由图3可知,对于不同的成膜方式, 陶瓷膜内的生成相大体相同(均由较多的γ-Al2O3和少量的α-Al2O3相组成),只是峰强略有差别。因对于非连续成膜方式而言,当放电再次开始时,已形成的陶瓷层被再次击穿、熔融,陶瓷膜随之继续生长。膜层的成分、形成条件并没有发生根本性的变化,因此,不同模式所形成的陶瓷膜的相也不会有太大的差别。但又因在连续成膜时,微弧放电相对连续,陶瓷膜所处温度一直较高,这更有利于氧化物相的形成。因此,连续模式所形成的陶瓷膜的氧化物峰略强。
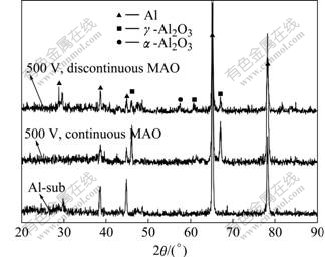
图3 电压为500 V时不同成膜方式制备的陶瓷层XRD谱
Fig.3 XRD patterns of MAO coatings prepared by different coating processing modes at 500 V
2.4 陶瓷层的微观形貌
图4所示为电压不同时不同成膜方式所制得的陶瓷膜表面形貌。由图4可知,不同成膜方式制备的陶瓷膜的表面形貌具有相似的变化趋势。当电压较低时,膜层表面都是由一个个微小的,类似于“火山锥”状的物质相互结合所构成。这是因为微弧放电区瞬间温度高达7 000 K[9],使氧化膜表面出现微区熔化,一些熔化物喷出后沉积在膜表面所致。随着电压的增加,两种成膜方式制备的陶瓷层都呈现出明显的烧结痕迹,且放电微孔多被熔融的物质覆盖。这是因为,微弧氧化电压的增加将导致从放电微孔中喷出的熔融物质增加,熔融氧化物凝固后在表面形成较完整的凝固结晶层,导电通道多被封闭。
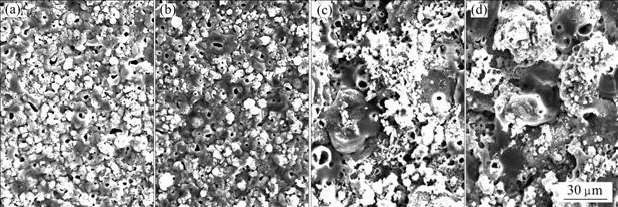
图4 电压不同时不同成膜方式制备的微弧氧化陶瓷膜的表面形貌
Fig.4 Surface morphologies of coatings prepared with different modes at different voltages: (a) 420 V, continuous MAO; (b) 420 V, discontinuous MAO; (c) 540 V, continuous MAO; (d) 540 V, discontinuous MAO
图5所示为电压500 V时非连续膜微弧氧化的截面形貌。由图5可知,膜厚约为20 μm,同涡流测厚仪测试值基本一致。膜层较为致密,并且从陶瓷层的截面上未发现分层现象。可见,因在微弧氧化过程中,介电击穿总是在膜的较薄弱处发生,每个放电火花存在的时间很短,因此膜层的生长并不是靠某些放电通道的长时间工作而实现,而是通过大量的、不断游动的微放电所形成的新堆积物覆盖原有的表面,经过多次重熔堆积而不断增厚所致[10]。因此,在非连续微弧氧化时,陶瓷膜的生长并不会因微弧放电的中途中断而受到很大程度的影响,因此,膜层不会出现分层 现象。
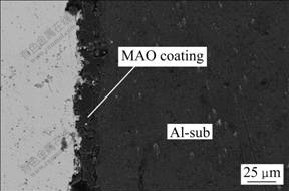
图5 电压为500 V时非连续成膜微弧氧化膜截面形貌
Fig.5 Cross-section morphology of MAO coating prepared by discontinuous MAO at 500 V
2.5 微弧氧化陶瓷层的耐磨性
图6(a)所示为不同成膜方式下微弧氧化陶瓷层的摩擦因数随摩擦时间变化曲线。由图6(a)可见,连续微弧氧化和非连续微弧氧化所形成的陶瓷层的摩擦因数基本相同,且都随摩擦时间的延长而缓慢增大。与铝基体相比,两种成膜方式制备的微弧氧化陶瓷层的摩擦因数曲线光滑,且增加平缓。
图6(b)所示为不同工作电压时不同成膜方式制备的陶瓷层的平均摩擦因数(μm)。平均摩擦因数的计算方法是通过对摩擦因数曲线在相同摩擦时内(600 s)积分,再求平均而得,具体求解如式(1)所示:
(1)
式中:f(t)为摩擦因数随时间的变化函数。从图6(b)中可以看出,不同电压下,不同成膜方式的微弧氧化陶瓷层的摩擦因数基本相同,且都随电压的增加而逐渐减小。由于微弧氧化陶瓷层的耐磨性能与膜层的表面形貌、硬度等因素密切相关[11-13]。因当微弧氧化电压较大时,试样表面所形成的结晶层较为完整、膜层相对致密。另外,当电压增加时,膜层中生成的氧化物含量增多[14],致使膜层硬度增大。因此,工作电压较高时所形成的陶瓷膜的耐磨性较好。

图6 不同成膜方式对陶瓷膜摩擦因数的影响
Fig.6 Effect of MAO modes on friction coefficient: (a) Friction coefficient curves; (b) Mean friction coefficient
铝基体及不同成膜方式微弧氧化陶瓷层与GCr15钢球对磨后的表面形貌如图7所示。从图7(a) 可以看出,铝基体表面沿滑动方向产生了划痕,甚至出现严重的磨伤、撕裂、粘着和塑性流动。而不同成膜方式制得陶瓷膜的磨痕形貌基本相同,磨痕轻微,且表面形成许多细小磨屑,如图7(b)所示。由于钢球硬度高于铝基体,在摩擦时磨球对铝基体表面产生犁削和微切削作用,导致在基体表面产生划痕和磨屑。而微弧氧化陶瓷层表面呈“火山喷射状”[15]组织特征,因此,摩擦时摩擦表面是以最凸出的不平处与摩擦钢球接触,即是以点接触。陶瓷层的凸起粒子在机械剪切应力作用下易发生断裂并在反复碾压的作用下碎化成细小的磨屑粒子,分布在摩擦表面,起到一定的缓冲与固体润滑作用。另外,微弧氧化陶瓷层的硬度明显高于铝基体的硬度,这些都有助于减少膜层表面的磨损。
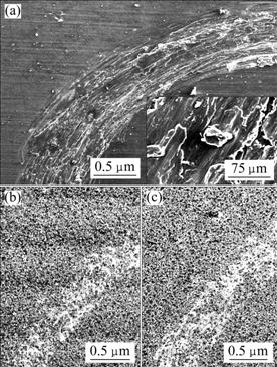
图7 不同成膜方式陶瓷膜的磨痕形貌
Fig.7 Morphologies of wear scars: (a) Al substrate; (b) Coating prepared by 500 V continuous MAO; (c) Coating prepared by 500 V discontinuous MAO
由以上分析可知,两个成膜模式所形成的陶瓷层的表面形貌、组成相和厚度等大体一致,又因为这些因素与膜层的耐磨性紧密相关,因此,两种成膜方式制备的陶瓷层耐磨性能基本相同。
2.6 不同成膜方式微弧氧化陶瓷膜耐腐蚀性分析
图8(a)所示为工作电压变化时两种成膜方式制得的微弧氧化陶瓷膜的极化曲线。从图8(a)可以看出,不同成膜方式所形成的陶瓷膜耐腐蚀性能基本相同, 都随着电压的增加,腐蚀钝化区明显增大,耐腐蚀性能显著增强。与裸基体相比,由于微弧氧化陶瓷涂层的阻挡作用,腐蚀介质难以与基体金属接触,因此耐腐蚀能力得到显著提高[16]。因氧化膜的耐腐蚀性与氧化膜厚度、表面孔隙率有关[17-18]。根据前面的分析可知,两种成膜方式所制备的陶瓷层具有相同的厚度和显微结构,因此他们的耐腐蚀性能大体相同。
图8(b)所示为电压为500 V时不同成膜方式制备的微弧氧化陶瓷膜浸入到3.5% NaCl溶液中的开路电位(Open potential circuit, OPC)随时间的变化曲线。由图8(b)可见,两种成膜方式下所形成的陶瓷膜的OPC相同。因OPC反应了膜层的结构和表面孔隙[19],因此,这进一步说明了非连续成膜对微弧氧化陶瓷膜的结构和表面形貌影响不大。
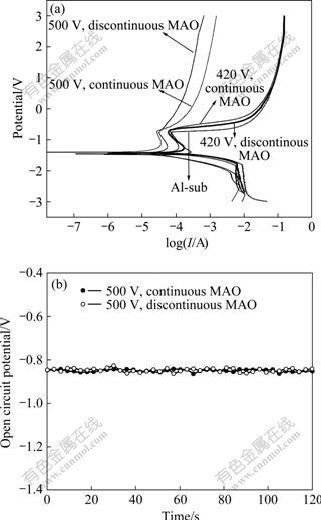
图8 不同成膜方式所得的微弧氧化试样的电化学曲线
Fig.8 Electrochemical curves of MAO coating prepared by different processing modes: (a) Polarization curves; (b) Open potential circuit curves
3 结论
1) 在微弧氧化过程中,通过非连续成膜方式可以制备性能良好的陶瓷膜。非连续方式制备的微弧氧化陶瓷膜在成膜速率、相组成和表面形貌等方面与一次性成膜相比并没有明显的差别,陶瓷膜没有因成膜过程中的放电中断而出现分层现象。
2) 非连续微弧氧化制得的陶瓷层与连续成膜所形成的陶瓷膜在耐磨、耐蚀性能方面具有相同的变化规律,且都随工作电压增加而提高。
REFERENCES
[1] YEROKHIN A L, SNIZHKO L O, GUREVINA N L, LEYLAND A, PILKINGTON A, MATTHEWS A. Discharge characterization in plasma electrolytic oxidation of aluminium[J]. Journal of Physics D: Applied Physics, 2003, 36(17): 2110-2120.
[2] YEROKHIN A L, NIE X, LEYLAND A, MATTHEWS A, DOWEY S J. Plasma electrolysis for surface engineering[J]. Surface and Coating Technology, 1999, 122(2/3): 73-93.
[3] CURRAN J A, CLYNE T W. The thermal conductivity of plasma electrolytic oxide coatings on aluminium and magnesium[J]. Surface and Coating Technology, 2005, 199(2/3): 177-183.
[4] NIE X, MELETIS E I, JIANG J C, LEYLAND A, YEROKHIN A L, MATTHEWS A. Abrasive wear/corrosion properties and TEM analysis of Al2O3 coatings fabricated using plasma electrolysis[J]. Surface and Coating Technology, 2002, 149(2/3): 245-251.
[5] RUDNEV V S, LUKIYANCHUK IV, BOGUTA DL, KON’SHIN V V, RUDNEV A S, GORDIENKO PS. Spark-anodic oxide coatings formed on Al and Ti alloys in tungstate-containing phosphate- vanadate baths[J]. Protection of Metals, 2002, 38(2): 191-195.
[6] 郭洪飞, 安茂忠, 霍慧彬, 徐 莘. 电解液组成对AZ91D镁合金微弧氧化的影响[J]. 材料科学与工艺, 2006, 14(2): 116-119.
GUO Hong-fei, AN Mao-zhong, HUO Hui-bin, XU Shen. Effect of constituents of electrolyte on micro-arc oxidation of AZ91D Mg alloys[J]. Materials Science and Technology, 2006, 14(2): 116-119.
[7] 彭继华, 过 萍, 李文芳, 黄京浩, 揭 军. 电解质对镁合金微弧氧化表面膜组织与腐蚀性能的影响[J]. 中国有色金属学报, 2007, 17(11): 1860-1864.
PENG Ji-hua, GUO Ping, LI Wen-fang, HUANG Jing-hao, JIE Jun. Effect of electrolyte on microstructure and corrosion resistance of micro-arc coatings of AZ91D magnesium alloy[J]. The Chinese Journal of Nonferrous Metals, 2007, 17(11): 1860-1864.
[8] 阎峰云, 林 华, 马 颖, 范送岩. 镁合金微弧氧化电极液电导率的研究[J]. 轻合金加工技术, 2007, 35(5): 28-31.
YAN Fen-yun, LIN Hua, MA Ying, FAN Song-yan. Study on electrolyte conductivity of magnesium alloy micro-arc oxidation [J]. Light Alloy Fabrication Technology, 2007, 35(5): 28-31.
[9] XUE Wen-bin, DENG Zhi-wei, CHEN Ru-yi, ZHANG Tong-he. Growth regularity of ceramic coatings formed by microarc oxidation on Al-Cu-Mg alloy[J]. Thin Solid Films, 2000, 372(1/2): 114-117.
[10] SUNDARARAJAN G, RAMA K L. Mechanisms underlying the formation of thick alumina coatings through the MAO coating technology[J]. Surface and Coatings Technology, 2003, 167(2/3): 269-277.
[11] KRISHNA L R, SOMARAJU K R C, SUNDARARAJAN G. The tribological performance of ultra-hard ceramic composite coatings obtained through microarc oxidation[J]. Surface and Coating Technolgoy, 2003, 163/164: 484-490.
[12] 郭宝刚, 陈建敏, 梁 军, 田 军. Ti-6Al-4V微弧氧化陶瓷膜的微观结构及摩擦磨损性能研究[J]. 摩擦学学报, 2005, 25(6): 510-514.
GUO Bao-gang, CHEN Jian-min, LIANG Jun, TIAN Jun. Microstructure and frictioin and wear properties of micro-arc oxidation coating on Ti-6Al-4V alloy[J]. Tribology, 2005, 25(6): 510-514.
[13] 来永春, 邓志威, 宋红卫, 薛文斌, 陈如意. 耐磨性微弧氧化膜的特性[J]. 摩擦学学报, 2000, 20(4): 304-306.
LAI Yong-chun, DENG Zhi-wei, SONG Hong-wei, XUE Wen-bin, CHEN Ru-yi. Properties of micro arc oxidation films on aluminum alloy substrate[J]. Tribology, 2000, 20(4): 304-306.
[14] WEI Da-qing, ZHOU Yu, JIA De-chang, WANG Ya-ming. Effect of applied voltage on the structure of microarc oxidized TiO2-based bioceramic films[J]. Materials Chemistry and Physics, 2007, 104(1): 117-182.
[15] 蒋百灵, 吴国建, 张淑芬, 雷廷权. 镁合金微弧氧化陶瓷层生长过程及微观结构的研究[J]. 材料热处理学报, 2002, 23(1): 5-8.
JIANG Bai-ling, WU Guo-jian, ZHANG Shu-fen, LEI Ting-quan. Research on micromechanism and growth procedure of ceramic coating formed by micro-arc oxidation on magnesium alloy[J]. Transactions of Materials and Heat Treatment, 2002, 23(1): 5-8.
[16] GHASEMI A, RAJA V S, BLAWER C, DIETZEL W, KAINER K U. Study of the structure and corrosion behavior of PEO coatings on AM50 magnesium alloy by electrochemical impedance spectroscopy[J]. Surface and Coatings Technology, 2008, 202(15): 3513-3518.
[17] 郝建民, 陈 宏, 张荣军, 蒋百灵. 镁合金微弧氧化陶瓷层的耐蚀性[J]. 中国有色金属学报, 2003, 13(4): 988-991.
HAO Jian-min, CHEN Hong, ZHANG Rong-jun, JIANG Bai-ling. Corrosion resistance of magnesium alloy micro-arc oxidation ceramic coating[J]. The Chinese Journal of Nonferrous Metals, 2003, 13(4): 988-991.
[18] DUAN Hong-ping, DU Ke-qin, YAN Chuan-wei, WANG Fu-hui. Electrochemical corrosion behavior of composite coatings of sealed MAO film on magnesium alloy AZ91D[J]. Electrochimica Acta, 2006, 51(14): 2898-2908.
[19] 王立世, 潘春旭, 蔡启舟, 魏伯康. 镁合金表面微弧氧化陶瓷膜的腐蚀失效机理[J]. 中国腐蚀与防护学报, 2008, 28(4): 219-224.
WANG Li-shi, PAN Chun-xu, CAI Qi-zhou, WEI Bo-kang. Corrosion failure mechanism of micro-Arc oxidation coatings formed on AZ91D magnesium alloy[J]. Journal of Chinese Society for Corrosion and Protection, 2008, 28(4): 219-224.
基金项目:新世纪优秀人才支持计划资助项目(NCET-05-0349):哈尔滨市优秀学科带头人基金资助项目(2006RFXXS012)
收稿日期:2009-02-15;修订日期:2009-04-20
通信作者:田修波,教授,博士;电话: 0451-86418791;E-mail: xiubotian@163.com
(编辑 龙怀中)