
Aging behavior of Al2O3 short fiber reinforced Al-Cu alloy composites
GENG Lin(耿 林), XU Hong-yu(许虹宇), YU Kuai(余 快), WANG Hong-lin(王洪林)
School of Materials Science and Engineering, Harbin Institute of Technology, Harbin 150001, China
Received 27 February 2007; accepted 28 May 2007
Abstract: Al2O3 short fiber reinforced Al-Cu composites containing 1%, 3%, 5% and 7% Cu were fabricated by a squeeze casting technique. The as-cast Al2O3/Al-Cu composites were solution treated at 535 ℃ and then aged at 170, 190 and 210 ℃, respectively. Age hardening behavior of the Al2O3/Al-Cu composites was analyzed by measuring the hardness of the samples at different aging temperatures and aging time. Microstructures of the composites were observed by transmission electron microscope(TEM). The results indicate that the hardness of the Al2O3/Al-Cu composites containing 7% Cu is much higher than that containing 1%-5% Cu because of the large amount of CuAl2 precipitant in the Al2O3/Al-Cu composite. With the increase of Cu content from 1% to 7%, the time needed for the appearance of peak hardness shortened, indicating that the addition of Cu can accelerate the kinetic of CuAl2 precipitation in the Al2O3/Al-Cu composites. The Al2O3/Al-Cu composite containing 7% Cu shows the highest increment of hardness by aging treatment. Therefore, in order to get a higher peak hardness, the Al2O3/Al-Cu composites need more Cu addition as compared with the un-reinforced Al-Cu alloys.
Key words: Al-Cu composites; Al2O3 short fiber; aging; hardness
1 Introduction
Discontinuously reinforced metal matrix composites have received much attention because of their improved specific strength and modulus, good wear resistance and modified thermal properties[1-3]. Short fiber or whisker reinforced aluminum alloy matrix composites have shown more advantages in mechanical and thermal properties because of the higher load transfer between reinforcement and matrix[4-6]. Al2O3 short fiber is promising for metals matrix composites because of the high performance and low cost of the Al2O3 short fiber. However, it was found that Al2O3 of other fibers containing Al2O3, such as Al18B4O33 whisker, can react easily with Mg containing aluminum alloys, resulting in a decrease of properties of the composites[6-7]. Therefore, Al-Cu alloy becomes a suitable matrix alloy for the composite reinforced by Al2O3 short fiber.
The aging behavior of discontinuously reinforced metal matrix composites has been a subject of great interest, which is beneficial to optimizing the aging treatment and providing the experimental and theoretical information for designing the properties of the composites[8-9]. Different results have been reported in the case of hardening behavior of discontinuously reinforced Al-Cu alloy composites[10-11]. KIM et al[12] reported significant retardation in the kinetics of hardening during aging of SiC reinforced Al4Cu alloy composites. On the contrary, it was also reported that the hardening kinetics was enhanced by the addition of ceramic reinforcements[11,13-14]. The nature of the change in age hardening behavior during aging of discontinuously reinforced metal matrix composites depends mainly upon matrix material, size, morphology and volume fraction of reinforcement, interface between matrix and reinforcement, composite processing route and aging temperature[15-18]. In the present research, Al2O3 short fiber reinforced Al-Cu alloy composites with different Cu contents are fabricated by a squeeze casting technique, and the age-hardening behavior and microstructure evolution during aging of the Al2O3/Al-Cu composites are investigated.
2 Experimental
Al-Cu alloys with mass fraction of Cu of 1%, 3%, 5% and 7%, respectively, were used as the matrix material. Al2O3 short fibers with average diameter and length of 5 μm and 150 μm, respectively, were used as the reinforcements. Al2O3/Al-Cu composites with Al2O3 volume fraction of 40% were fabricated by a squeeze casting technique. The process of the squeeze casting was as follows: 1) the Al-Cu alloy was melted and heated up to 800 ℃, meanwhile, the Al2O3 short fiber preform was heated to 500 ℃, and 2) the melted Al-Cu alloy was then infiltrated into the preform under a low pressure (about 2 MPa) and solidified under a high pressure (about 50 MPa).
The as-cast Al2O3/Al-Cu composite samples were solution treated at 535 ℃ for 1 h, water quenched and then aged at 170, 190 and 210 ℃, respectively, for 20 h. Age hardening behavior of the Al2O3/Al-Cu composites was analyzed by measuring the hardness of the samples at different aging temperatures and aging time using a Vickers hardness testing machine. Morphology of precipitants in the Al2O3/Al-Cu composites at different aging stages was observed and analyzed using a Philips CM-12 transmission electron microscope(TEM).
3 Results and discussion
3.1 Age hardening behavior of Al2O3/Al-Cu com- posites
The morphologies of the Al2O3 short fiber and Al2O3/Al-Cu composite are shown in Fig.1 observed by scanning electron microscope(SEM). It can be seen that the Al2O3 short fibers are well separated and distributed uniformly in the as cast Al2O3/Al-Cu composite.
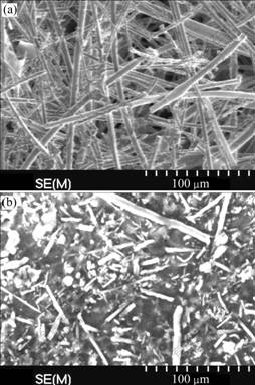
Fig.1 SEM morphologies of Al2O3 short fiber (a) and Al2O3/Al-Cu composite (b)
Fig.2 shows the effect of Cu content on the hardness of the Al2O3/Al-Cu composites as a function of aging time during aging at 170, 190 and 210 ℃, respectively. It can be seen that the age hardening rate of the composite increases with increasing Cu content for all the aging temperatures. When the aging temperature is 190 ℃ as shown in Fig.2(b), the peak hardness of the composite with 7% Cu appears at the aging time of 11 h, while, the peak hardness of the composites with Cu content of 5% and 3% appear at the aging time of 12.5 h and 14 h, respectively.
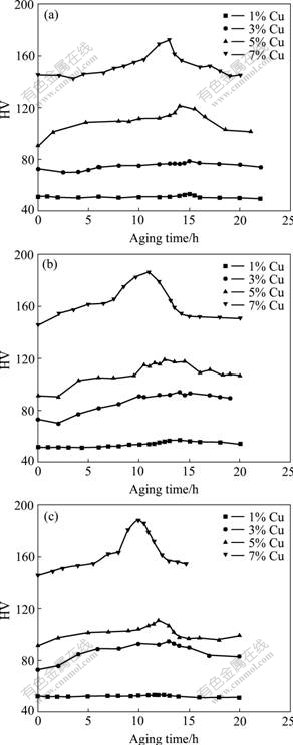
Fig.2 Effect of Cu content on hardness of Al2O3/Al-Cu composites as function of aging time during aging at 170 ℃ (a), 190 ℃ (b) and 210 ℃ (c)
It has been reported that the reduction of the retained vacancy sites in the composite due to the absorption of quench-in vacancies in the high dislocation density matrix, which is caused by the large difference of the coefficient of thermal expansion between ceramic reinforcement and matrix alloy, inhibits the GP zone formation because the nucleation of the GP zone requires vacancy clusters[10]. Therefore, the time needed for the appearance of peak hardness depends on the precipitation rate of θ" (CuAl2) phase that accounts for the peak hardness[12]. With increasing Cu content in the composites, it becomes easier for the Cu atoms to diffuse and aggregate in the matrix, which accelerates the nucleation and growth of the CuAl2 phase and increases the hardening rate of the composites.
With increasing Cu content from 1% to 7% in the Al-Cu alloys, the hardness of the Al2O3/Al-Cu composite in both solution and aging state increases greatly as shown in Fig.2. It is also found from Fig.2 that the increment of the peak hardness compared with solution state increases obviously with increasing Cu content. When the Cu content is 1%, there is almost no peak hardness, while, the peak hardness increases by about 20% compared with solution state when the Cu content is 7%.
The most important reason for the increasing age hardening effect of the composite is that the amount of the CuAl2 phase increases with increasing Cu content. For the unreinforced Al-Cu alloys, the Cu content is usually less than 5%, which is enough to form required precipitant for the appearance of peak hardness. In the Al2O3/Al-Cu composite some Cu elements will be captured by the high density dislocations in the Al-Cu alloy matrix, and these Cu elements cannot contribute to the formation of CuAl2 precipitant in the composite. Therefore, in order to get higher age hardening effect, more Cu element is needed to form enough CuAl2 phase in the matrix compared with unreinforced Al-Cu alloy. However, for the composite with 7% Cu content, the hardness decreases sharply after peak hardness because of the overaging. Therefore, it is important to select an optimum aging time for obtaining the peak hardness of the Al2O3/Al-Cu composites.
3.2 Precipitation behavior of Al2O3/Al-Cu composites
It can be seen from Fig.2 that the Al2O3/Al-Cu composite containing 7% Cu shows higher hardness during aging at 190 ℃ and 210 ℃ compared with that at 170 ℃. It is also found from Fig.2(b) that when the composites are aged at 190 ℃, the hardness of the Al2O3/Al-Cu composite containing 7% Cu is much higher than that containing 5% Cu. Fig.3 shows the TEM morphologies of the CuAl2 precipitants of the Al2O3/Al-Cu composite containing 5% Cu after aging at 190 ℃ for different time. It can be seen that both amount and size of the CuAl2 precipitant increase with increasing aging time. At the aging time of 4 h, the amount of the CuAl2 precipitant is lower, corresponding to a lower hardness of the composite. At the aging time of 14 h, the amount of the CuAl2 precipitant increases and the size of the CuAl2 precipitant is almost not increased. The large amount of CuAl2 precipitant with small size accounts for the peak hardness of the composite. At the aging time of 20 h, the size of the CuAl2 precipitant increases greatly, meanwhile, the amount of the CuAl2 precipitant does not increase, leading to a decrease of the hardness of the composite.
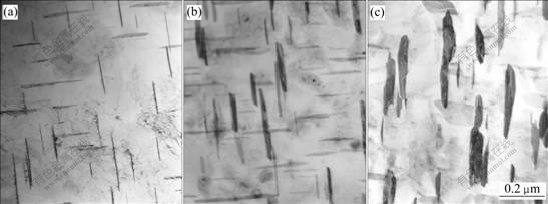
Fig.3 TEM images of CuAl2 precipitants in Al2O3/Al-Cu composites containing 5% Cu after aging at 190 ℃ for 4 h (a), 14 h (b) and 20 h (c)
Fig.4 shows the TEM morphologies of the CuAl2 precipitants in the Al2O3/Al-Cu composite containing 7% Cu after aging at 190 ℃ for different time. It shows similar characteristic of morphology as that shown in Fig.3. By comparing Fig.4 with Fig.3, it can be seen that the amount of the CuAl2 precipitant in the composite containing 7% Cu is larger than that containing 5% Cu for all the aging stages. It is also found that the size of the precipitants in both composites is similar to that at different aging stages. Therefore it can be concluded that the large amount of CuAl2 precipitant is the main reason for the higher hardness of the Al2O3/Al-Cu composite containing 7% Cu, which can be seen clearly in Fig.2.
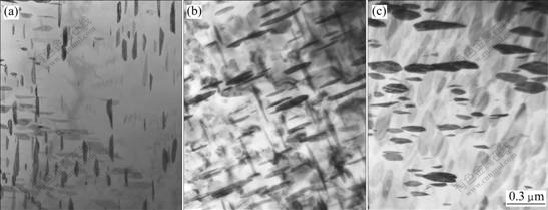
Fig.4 TEM images of CuAl2 precipitants in Al2O3/Al-Cu composites containing 7% Cu after aging at 190 ℃ for 4 h (a), 12 h (b) and 20 h (c)
4 Conclusions
1) The hardness of the Al2O3/Al-Cu composite containing 7% Cu is much higher than that containing 1%-5% Cu. The large amount of CuAl2 precipitant is the main reason for the higher hardness of the Al2O3/Al-Cu composite containing 7% Cu.
2) With the increase of Cu content from 1% to 7%, the time needed for the appearance of peak hardness decreases, indicating that the addition of Cu can accelerate the kinetics of CuAl2 precipitation in the Al2O3/Al-Cu composites.
3) The Al2O3/Al-Cu composite containing 7% Cu shows the highest increment of hardness by aging treatment. Therefore, in order to get a higher peak hardness, the Al2O3/Al-Cu composite needs more Cu addition as compared with the un-reinforced Al-Cu alloys.
References
[1] JIANG C H, WU J S, WANG D Z. Relaxation of residual stresses in 20%SiCw/6061Al composite as extruded at high temperature [J]. Trans Nonferrous Met Soc China, 2001, 11(5): 729-732.
[2] DONG S L, MAO J F, YANG D Z, CUI Y X, JIANG L T. Age-hardening behavior of a SiCw/AL-Li-Cu-Mg-Zr composite [J]. Materials Science and Engineering A, 2002, 327: 213-223.
[3] YUAN W H, CHEN Z H, XU H Y, ZHANG F Q, FU D F. Properties and microstructures of 7075/SiCp composites prepared by spray deposition [J]. Trans Nonferrous Met Soc China, 2003, 13(5): 1160-1163.
[4] GENG L, YAO C K. SiC-Al interface bonding mechanism in a squeeze casting SiCw/Al composite [J]. Journal of Materials Science Letters, 1995, 14: 606-608.
[5] JIANG C H, WU J S, WANG D Z. Elastic modulus of SiCw/6061Al alloy composites as-squeeze-cast [J]. Trans Nonferrous Met Soc China, 2001, 11(6): 900-903.
[6] MOMDAL D P, BASU K. NARAYAN S P, GOVINDARAJU K V. Effect of processing history and aging temperature on age-hardening kinetics of 2014-Al alloy-SiC whisker composite [J]. Journal of Materials Science Letters, 2000, 19: 1189-1191.
[7] HU J, FEI W D, LI C, YAO C K. Interfacial reaction in aluminum borate whisker-reinforced aluminum composite [J]. Journal of Materials Science Letters, 1994, 13(24): 1797-1799.
[8] FEI W D, JIANG X D, LI C, YAO C K. Effect of interfacial reaction on fracture behavior of aluminum borate whisker reinforced aluminum composite [J]. Materials Science and Technology, 1997, 13(11): 918-922.
[9] SHEU C Y, LIN S J. Aging behavior of SiCp-reinforced AA 7075 composites [J]. Journal of Materials Science, 1997, 32: 1741-1747.
[10] GENG L, ZHANG X N, WANG G S, ZHENG Z Z, XU B. Effect of aging treatment on mechanical properties of (SiCw+SiCp)/2024Al hybrid nanocomposites [J]. Trans Nonferrous Met Soc China, 2006, 16(2): 387-391.
[11] DAOUD A, REIF W. Influence of Al2O3 particulate on the aging response of A356 Al-based composites [J]. Journal of Materials Processing Technology, 2002, 123: 313-318.
[12] KIM T S, KIM T H, OH K H, LEE H I. Suppression of θ" formation in the SiC whisker-reinforced Al-4wt%Cu composites [J]. Journal of Materials Science, 1992, 27: 2599-2602.
[13] SURESH S, CHRISTMAN T, SUGIMURA Y. Accelerated aging in a cast alloy-SiC particulate composite [J]. Scripta Mater, 1989, 23: 1599-1602.
[14] SHARMA S C, SASTRY S, KRISHNA M. Effect of aging parameters on the microstructure and properties of ZA-27/aluminite metal matrix composites [J]. Journal of Alloys and Compounds, 2002, 346(1): 292-301.
[15] DUTTA B, SURAPPA M K. Age-hardening behaviour of Al-Cu-SiCp composites synthesized by casting route[J]. Scripta Mater, 1995, 32: 731-736.
[16] MCNELLEY T R, KALU P N. The effects of thermomechanical processing on the ambient temperature properties and aging response of a 6061 Al-Al2O3 composite [J]. Scripta Mater, 1991, 25: 1041-1046.
[17] SRINIVASAN D, SURAPPA M K. Effect of iron impurity and thermomechanical processing on the age-hardening behaviour of 6061 Al-SiCp MMC produced by casting route [J]. Scripta Mater, 1992, 27: 1139-1144.
[18] WANG N, WANG Z R, WEATHERLY G C. Formation of magnesium aluminate (spinel) in cast SiC particulate-reinforced Al(A356) metal matrix composites [J]. Metall Trans A, 1992, 23: 1423-1430.
Foundation item: Project(2006CB605203-3) supported by the National Basic Research Program of China
Corresponding author: GENG Lin; Tel: +86-451-86413907; Fax: +86-451-86413922; E-mail: genglin@hit.edu.cn
(Edited by YUAN Sai-qian)