Ultrasonic echo signal fetures of dissimilar material bonding joints
GANG Tie(刚 铁)1, Yasuo TAKAHASHI2
(1. State Key Lab of Advanced Welding Production Technology, Harbin Institute of Technology, Harbin 150001, China;
2. JWRI, Osaka University, Japan)
Abstract: An ultrasonic evaluation method of echo feature of diffusion bond joint between two dissimilar materials is presented. The echo signal was acquired by an automatic ultrasonic C-scan test system. It is found that the intensity of echo and its phase can be used to evaluate the joint quality, and interface products of dissimilar materials bonding can be evaluated by ultrasonic method.
Key words: non-destructive evaluation; ultrasonic testing; diffusion bonding; dissimilar material CLC number: TG115
Document code: A
1 INTRODUCTION
Diffusion bonding is playing a very important role in precision welding, special materials joining, dissimilar materials joining and so on. It becomes an indispensable assembly and joining technology for aviation, space flight field and other manufacturing industry. The main problem of diffusion bonding is the quality assurance of bonding part. For the nonce, the quality assurance for all most joining processing largely relies on the process control[1]. Ultrasonic test method has been used as a non-destructive test method of joint part often. It is well-known that the gap and inclusion in the joints of diffusion bonding are very small, some-times there are weak bonding and so-called “Kissing bond” too. It is said that the defect size of diffusion bonding can be decided by the surface roughness of samples in principle[2]. An experiment shows that a defect with dimension of less than 50μm in Zr-Ur diffusion bonding joint can be detected out with a high precision ultrasonic scanning device and a high frequency probe[3]. It is reported that ration of the rate of longitudinal wave reflection to the rate of shear wave reflection has been used to judge the quality of joint. Furthermore, the acoustic pressure reflection coefficient, reflective echo intensity and interference and influence between flaw echo wave and interface echo wave etc have been used to study the quality of diffusion bonding joints of stainless steel, and joints of stainless and ductile ingot with Ni interface layer[4-6].
Monitoring the process of diffusion bonding in real time is of great significance and the investigation result can be used to realize the feedback control for diffusion bonding processing. In this field the research work is aimed at testing the reflective echo height of bonding interface and the relationship between the wave height and the bonding intensity in real time[7, 8], but it needs a special device to mount the testing probe etc.
Ultrasonic signal processing is an effective testing method too. The frequency analysis, guided wave and wavelet etc have been used to study the ultrasonic feature of bonding titanium plate[9], ultrasonic propagation mechanics in three layer model[10], shear strength of diffusion bonding joint and the joint quality of friction welding[11].
Ultrasonic image method has been used to detect the joints quality of diffusion bonding, and the C-scan method is used in most cases[4, 12-16], while in some cases the B-scan is used[13]. It is reported that the detection calibration was carried out by means of making artificial defects with coating a stop welding material and inserting refractory materials[17].
This paper deals with the ultrasonic interface signal features of diffusion bonding joints of dissimilar materials Al/Cu, and the relationship between the ultrasonic echo signal and the interface state.
2 EXPERIMENTAL
2.1 Experiment method
The materials used were oxygen-free copper and pure aluminum(1050). The samples were cylinders of 9.7mm in diameter, and 3.2mm for Al and 11mm for Cu in length, respectively(Fig.1). The chemical compositions of the samples are given in Table 1. The samples were polished with emery paper(grade 400#) after machining, and then cleaned by acetone. The surface roughness is shown in Fig.2. Two thermocouples were mounted near the location of the interface of aluminum and copper for measuring the temperature in bonding process. Fig.3 shows the location of thermocouples in heating-furnace. The loading time and soaking time were decided according to the output of thermocouple. The temperature curve of bonding processing is shown in Fig.4. Bonding parameters are as follows: 480-550℃, 5-15MPa, 10-60min.
2.2 Test system
The quality test of the bonding interface was
Table 1 Component of material(mass fraction, %)
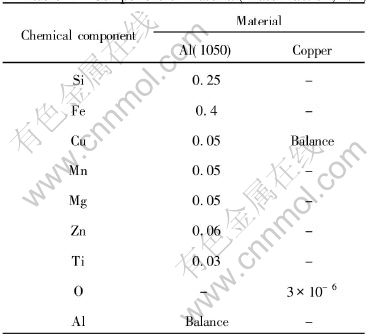
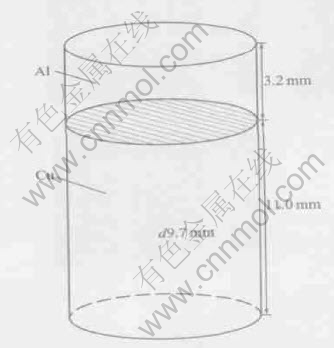
Fig.1 Experimental sample
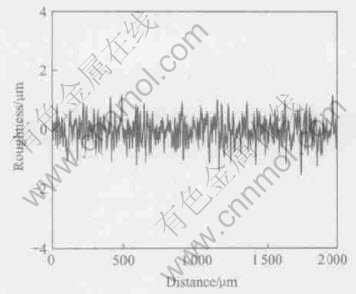
Fig.2 Surface roughness of sample
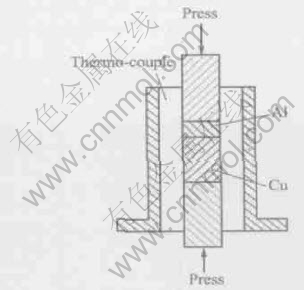
Fig.3 Mounting of thermocouple

Fig.4 Temperature curve of bonding process
carried out by a high frequency immersion ultrasonic C-scan method. The frequency of probe used is 10MHz, the focus in water is 25mm, and the diameter at focus is about 0.37mm. The ultrasonic test system is composed of scanning device, ultrasonic signal emission and reception unit, signal analysis and pre-processing etc. The scanning range and the scanning step length were 12mm×12mm and 0.1mm, respectively, according to sample size.
3 FEATURES OF INTERFACE ECHO
3.1 Echo signal and feature of interfaces
The probe focus was located at Al/Cu interface by adjusting the distance from the end of probe to the surface of sample. The echo wave of different location and different state of bonding are shown in Fig.5. The first echo in Fig.5(a) is from Water/Al interface, which is called surface echo too. The echo wave in testing gate is called interface echo wave. Fig.5(a) is an echo from Al/Cu interface before bonding, Fig.5(b) is an echo from a good bonding zone, and Fig.5(c) is an echo from a bad bonding zone. Fig.5 shows that they are different in intensity and phase for different bonding states.
Fig.6 shows a C-scan result of a bonding joint, and the echo amplitude was displayed by different colors, and red is the highest. The echo in this figure is acquired from different zones within which the quality is different. The echo amplitude in the first picture is higher, and its phase is reversed to the entrance wave, so that it may be confirmed that this zone has not been bonded. The echo in the last picture is from the good bonding zone. Although the sound resistance of aluminum and copper is different, the reflection ratio is lower in a good bonding interface, therefore the echo amplitude is lower, and the phase is the same with entrance wave. The photos of different joint cross-sections are given in Fig.7. It shows that some zones have not been bonded, and there are remarkable differences in the three photos. The information above could be used to recognize the state of bonding interface, and evaluate the quality of joints.
3.2 Interface signal features of different heat processing
In the process of dissimilar material diffusion bonding, a reciprocal diffusion will occur in the in-
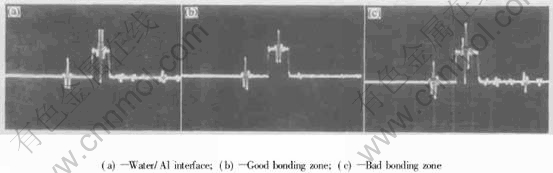
Fig.5 Echo waves from different interfaces
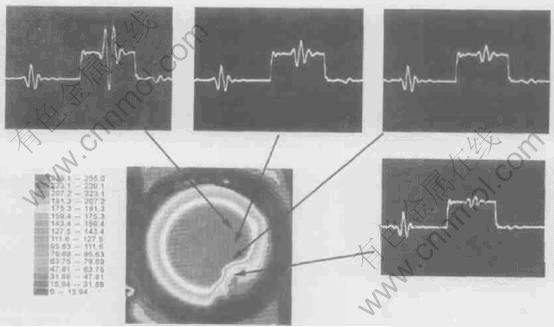
Fig.6 Echo waves from different zones of typical joints
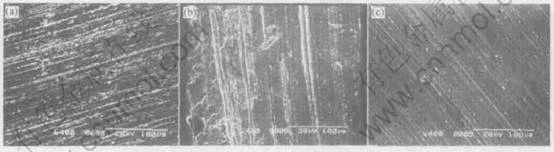
Fig.7 Photos of share cross-sections
terface. Therefore, intermetallic compound will be produced with different bonding processes and different materials. The interface strength will be decreased when the intermetallic compound forms as a sphericity. In this paper, a discussion on evaluation method of intermatallic compound was carried out. First, three samples of diffusion bonding joints were made with the process parameters of 520℃, 10MPa and 10min, and annealed under the conditions of 〈1×10-6Pa, 480℃ and 90h. Then the behavior of ultrasonic echo from bonding interface was studied. The C-scan test results are shown in Fig.8. It shows that the images are quite different, and the reflective echo intensity of all samples is decreased(Fig.9). It may be estimated that a new phase forms in the bonding interface whose acoustic impedance is between aluminum and copper, and acoustic press reflective ratio of interface is decreased. To investigation this phenomenon, the EPMA was carried out to analyze the state of interface. Fig.10 shows that a new layer forms at the interface. The analysis of EPMA shows that they are CuAl2 and Cu2Al3. Although the sound characteristic(acoustic impedance) of two new phases are unknown now, they can be estimated from the compositions that they are in the middle of aluminum and copper. There fore, the interface reflective ratio is lower and the amplitude of reflective echo decreases.
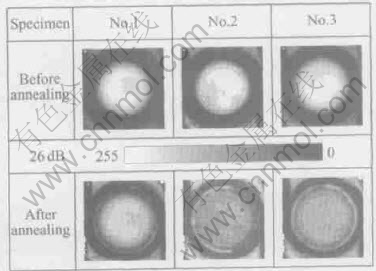
Fig.8 C-scan image of before and after annealing
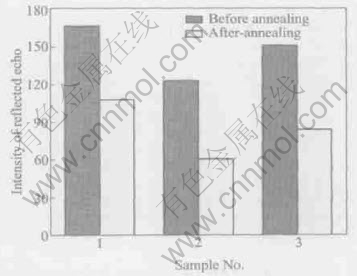
Fig.9 Signal amplitudes of echo before and after annealing
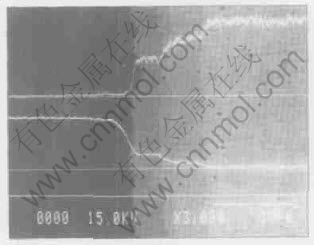
Fig.10 EPMA photo of sample
4 CONCLUSIONS
1) High frequency ultrasonic C-scan technique seems to be a very promising tool for evaluating the dissimilar materials diffusion bonding. With this tool the defects in the diffusion bonding joint and the quality of the joint interface can be evaluated.
2) The echo wave amplitude and the echo phase can be used as the features to evaluate the bonding joints quality, that is the echo amplitude is higher and the phase of echo is reversed to the entrance wave while the reflective echo is from non bonded zone, and they are reversed while the echo is from a good bonded zone.
3) Ultrasonic detection method can be used for the qualitative analysis of interface products of dissimilar materials bonding. For the Al/Cu bonding, the echo reflection ratio is lower when the new phases CuAl2 and Cu2Al3 formed.
REFERENCES
[1]Ohashi O. Diffusion bonding [J]. J of JWS, 2000, 69(5): 91-100. (in Japanese)
[2]Nagg P B, Adler L. Ultrasonic evaluation of solid-state bonds [J]. Materials Evaluation, 1992, 50(11): 1328- 1337.
[3]Kapranos P, Priestner R. NDE of diffusion bonds [J]. Metals and Materials, 1987(4): 194-198.
[4]Kato H. Nondestructive evaluation of bonding character [J]. J of JSNDI, 2000, 49(9): 601-605. (in Japanese)
[5]Ohashi O, Hashimuto T, Kimura K, et al. Study on diffusion welding(report 7) ultrasonic testing of diffusion welding stainless steel [J]. J of JSNDI, 1979, 48(3): 182-186.(in Japanese)
[6]Onozaws K, Tamura H. Detect evaluation in diffusion bonding interface of dissimilar metals using ultrasonic testing method [A]. Proceedings of the 7th European Conference on Non-Destructive Testing [C]. 1998.
[7]Tamura K, Onozaws M. Evaluation of diffusion bonding joints of FCD500-Al alloy during heat treatment using ultrasonic testing [J]. Preprints of the National Meeting of JWS, 2000, 67: 298-299.
[8]Greenberg Y, Itzhak D, Kohn G. Ultrasonic monitoring of a low-temperature diffusion bonding process [J]. J of Testing and Evaluation, 2000, 28(2): 88-95.
[9]Cheng A, Deutsch W. Characterization of diffusion bonds of titanium plates using transmitted ultrasonic signals [J]. NDT&E, 1998, 31(3): 175-182.
[10]Rose J L, ZHU Wen-hao, Zaidi M. Ultrasonic NDT of titanium diffusion bonding with guided waves [J]. M E, 1998, 56(4): 535-539.
[11]CHEN Jian-zhong, SHI Yao-wu, QIU Hai. Wavelet transform of ultrasonic A-scan signals testing solid-state welded joints [J]. NDT, 1999, 21(9): 385-399.(in Chinese)
[12]Debbouz O, Navai F. Nondestructive testing of 2017 aluminum copper alloy diffusion welded joints by an automatic ultrasonic system [J]. Materials Evaluation,1999, 57(12): 1261-1267.
[13]Takahahsi F, Sutsuki K. A foundational testing of diffusiong welds using acoustic imaging method [J]. J of JSNDI, 1981, 30(1): 14-2.(in Japanese)
[14]Abe T. Nondestructive evaluation of foundationally graded materials by ultrasonic imaging [J]. J of JSNDI, 2000, 49(9).(in Japanese)
[15]Fukaya Y, Shirage N, Kimura T, et al. Ultrasonic inspection of ceramics/metal bonded joint [J]. Preprints of the National Meeting of JWS, 1998, 63: 364-365.(in Japanese)
[16]Gripp S. Quality control of dissimilar explosion bonded cladding by ultrasonic testing [J]. NDT Net, 1997, 2(2): .
[17]Matson D M, Lansaw J T, Suits M W, et al. Ultrasonic inspection of a diffusion-bonded platelet rocket chamber liner [J]. Materials Evaluation, 1993, 51(5): 545-551.
(Edited by PENG Chao-qun)
Foundation item: Project(59775063) supported by the National Natural Science Foundation of China; Project supported by the Visiting Scholar Foundation of Key Lab in University of China
Received date: 2004-03-26; Accepted date: 2004-06-30
Correspondence: GANG Tie, Professor, PhD; Tel: +86-451-86413952; Fax: +86-451-86416186; E-mail: gangt@hope.hit.edu.cn