
Influence of hot extrusion on microstructure and mechanical properties of AZ31 magnesium alloy
WANG Ling(王 岭), TIAN Su-gui(田素贵), MENG Fan-lai(孟凡来), DU Hong-qiang(杜洪强)
1. College of Materials Science and Engineering Shenyang University of Technology, Shenyang 110023, China;
Received 28 July 2006; accepted 15 September 2006
Abstract: Extrusion treatment is a common method to refine the grain size and improve the mechanical properties of metal material. The influence of hot extrusion on microstructure and mechanical properties of AZ31 magnesium alloy was investigated. The results show that the mechanical properties of AZ31 alloy are obviously improved by extrusion treatment. The ultimate tensile strength (UTS) of AZ31 alloy at room temperature is measured to be 222 MPa, and is enhanced to 265.8 MPa after extrusion at 420℃. The yield tensile strength (YTS) of AZ31 alloy at room temperature is measured to be 84 MPa, and is enhanced to 201 MPa after extrusion at 420℃. The effective improvements on mechanical properties result from the formation of the finer grains during extrusion and the finer particles precipitated by age treatment. The features of the microstructure evolution during hot extruded of AZ31 alloy are dislocation slipping on the matrix and occurrence of the dynamic recrystallization.
Key words: AZ31 magnesium alloy; hot extrusion; mechanical properties; recrystallization; deformation features
1 Introduction
Magnesium, with its rich reserves in the earth, is an important engineering material, but has not been fully developed and utilized till now. With its low density, magnesium has a higher specific strength and stiffness than other engineering materials such as aluminum, steel and polymer-based composites, so magnesium alloys are emerging as potentially good candidates for numerous applications especially in automobile industry[1].
However, the magnesium applicants are limited to the components that are exposed to low temperatures because of the poor strength at temperature in excess of 120 ℃[2]. The mechanical properties of magnesium alloys can be enhanced by additional elements. The fact that Al2Ca–phase is distributed on the grain boundaries and in the grain interior can enhance the mechanical properties of Mg-Al-Ca alloys at room temperature[3]. The addition of the elements Y and La to AM50 alloy may modify the microstructure of magnesium ingot, so that the mechanical properties of alloys are increased both at ambient and elevated temperature due to the stable rare earth compound formed at grain boundary[4]. The additions of trace Sb element can enhance the ultimate tensile strength (UTS) of AZ91 alloy to 264 MPa from 222MPa at room temperature[5]. The additions of the elements Be, Sn and Bi also have the effect of improvement on the mechanical properties of Mg alloys[6-8]. Mg alloys containing rare earth elements developed in the past few years have the better mechanical properties than containing other elements even at moderate temperature. But the alloys containing rare earth are more expensive than common Mg alloys such as AZ31 alloy. Hot extrusion treatment can improve the mechanical properties of AM50 alloy, especially the yield strength of them at temperature over 150 ℃[9]. And the products of the extruded Mg alloy have much better size precision and surface quality than the ones by rolling and forging[10], therefore, the influence of hot extrusion on the microstructure and properties of Mg alloys is widely investigated. A few papers reports on the influence of hot extruded on the microstructure and properties of AZ31 alloy, however, the regularity of the microstructure evolution during hot extruded is still unclear.
In this paper, the influence of hot extruded on the mechanical properties of AZ31 alloy is investigated, and the regularity of the microstructure evolution during hot extruded is briefly discussed.
2 Experimental
AZ31 Mg alloy was prepared in a mild steel crucible placed in a resistance furnace under an atmosphere of mixture SF6 and CO2. The alloy was melted at 720 ℃ and held for 20 min, then mold cast into a block with 273 mm×200 mm×35 mm. The billets were heat treated at 420 ℃, held for 12 h.
After machined into the block of 35 mm in diameter, AZ31 alloy was extruded into the bar of 13 mm in diameter under the extruded speed of 70 mm/min at 320, 360 and 420 ℃, respectively. After the extruded AZ31 Mg alloy was aged at 180 ℃ for 16 h, the alloy was machined into cylindrical specimens with a cross-section of 6mm in diameter and 25 mm in gauge length according to ASTMB557M for mechanical properties testing. The ultimate tensile strength (UTS) of the alloys was measured at room temperature(RT), 150 ℃ and 200 ℃, respectively, using a CSS-55100 tensile testing machine, with an initial strain rate of 1×10-2 s-1. The microstructures of the extruded AZ31 alloy at different states were observed by OM, SEM and TEM.
3 Results and analysis
3.1 Influence of ageing time on hardness
After extruded at 320, 360 and 420 ℃, respectively, the AZ31 alloys are aged for different time at 180 ℃. The relationship between the hardness values of the extruded AZ31 alloy and the ageing time is shown in Fig.1. This indicates that the peak hardness of the extruded AZ31 alloys appears when aged for 16 h. Therefore, the optimal ageing time of the extruded alloy is determined as 16 h at 180 ℃.
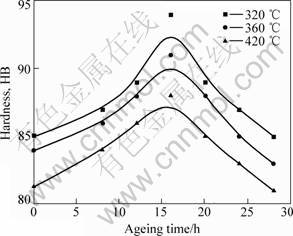
Fig.1 Relationship between hardness of extruded AZ31 alloy and ageing time
3.2 Influence of hot extrusion on properties
The relation between ultimate tensile strength (UTS) of AZ31 alloy at different states and the testing temperature is shown in Fig.2(a). This indicates that the UTS value of AZ31 alloy at room temperature is measured to be 222 MPa, and after extruded at 420 ℃, the UTS of the alloy is enhanced to 265.8 MPa. As testing temperature is increased to 200 ℃, the UTS value of the alloy is still maintained at 180 MPa.
The yield tensile strength (YTS) of AZ31 alloy at RT is measured to be 84 MPa, after extruded at 420 ℃, the YTS of the alloy is enhanced to 201 MPa, the extent of the enhancing YTS is up to 139% as shown in Fig.2(b). And the YTS value of the alloy is still measured to be 124 MPa when the testing temperature elevated to 200 ℃. This indicates that the hot extrusion technique may effectively improve the UTS and YTS of the alloy at RT and elevated temperature.
The influence of the ageing treatment on the mechanical properties of the extruded AZ31 alloy is shown in Fig.3. This indicates that the UTS value of the extruded alloy measured at RT, after ageing, is enhanced from 265.8 to 281.6 MPa, and the extent of the enhancing UTS is up to 10%. And the UTS value of the alloy is enhanced from 180 to 189 MPa as the testing temperature elevated to 200 ℃. Therefore, it shows that the aged treatment in the same extent can improve the UTS of the extruded AZ31 alloys.
3.3 Microstructure of AZ31 alloy
The microstructures of AZ31 alloy at different shown in Fig.4. The typical microstructure of as-cast alloy consists of α-Mg matrix and fine particle that are homogeneously distributed in the matrix, as shown in Fig.4(a). After the alloy is extruded at 320 ℃, the finer size of the grains formed during hot extrusion are measured to be about 5 mm, as shown in Fig.4(b). Therefore, it may be deduced that the dynamic recrystallization occurs during hot extrusion of the AZ31 alloy. Improvement on the mechanical properties of the extruded alloy, as shown in Fig.2, attributes to the finer grains.
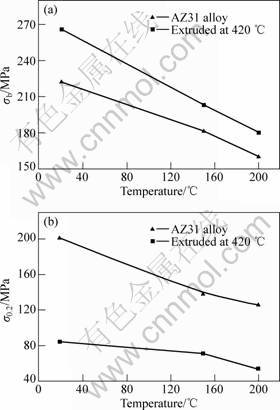
Fig.2 Relations between mechanical properties of AZ31 alloy and testing temperature: (a) UTS; (b) Yield strength

Fig.3 UTS of AZ31 alloy at different temperatures
The microstructure of AZ31 alloy extruded at 320 ℃ and 420 ℃ are shown in Fig.5, and the grain size of the alloy extruded at 320 ℃ is measured to be 3-5 mm as shown in Fig.5(a), and the one of the alloy extruded at 420 ℃ is measured as 10-20 mm as shown in Fig.5(b). This indicates that the different grain sizes are distributed in the matrix of AZ31 alloy extruded at different temperatures, and the grain size of AZ31 alloy increases obviously with the elevated extrusion temperature. Therefore, it may be deduced that the phenomena of the dynamic recrystallization occurs during hot extrusion of the alloy, thereafter, the size of the grain in the alloy increases slightly with time.
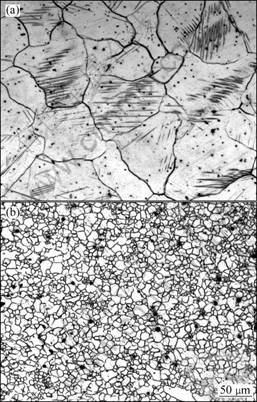
Fig.4 Microstructures of AZ31 alloy at different states: (a) As-cast AZ31 alloy; (b) AZ31 alloy extruded at 320 ℃
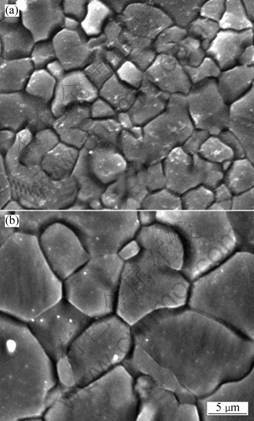
Fig.5 Microstructures of AZ31 alloy extruded at different temperatures: (a) 320 ℃; (b) 420 ℃
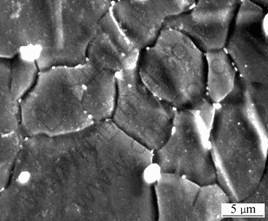
Fig.6 Microstructure of hot extruded AZ31 alloy aged at 180 ℃ for 16 h
After aged at 180 ℃ for 16 h, some of the finer particles are precipitated along the grain boundaries in the extruded alloy, as shown in Fig.6. Compared with the extruded alloy shown in Fig.5, in which a few finer particles are precipitated in the alloy, the grains of the alloy have the same size in two states. Therefore, it may be thought that the dispersed particles precipitated during ageing treatment can effectively enhance the mechanical properties of alloy.
3.4 Deformation features during hot extrusion
The microstructures of AZ31 alloy extruded at 420 ℃ are shown in Fig.7. This indicates that the finer grains are distributed in the local areas of the extruded alloy, and significant amount of dislocations have been piled up within the finer grains as shown in Fig.7(a), no twinning feature of the deformation is detected in the alloy. Therefore, it may be deduced that the deformation feature of AZ31 alloy during hot extrusion is dislocation slipping on the matrix of alloy. The deformation of the dislocation slipping can improve the ductility of AZ31 alloy.
The fact that the finer grains are formed in the hot extruded alloy indicates that the dynamic recrystalli- zation occurs in the process of extrusion. No dislocation is detected within the bigger grains as marked by C in Fig.7(b), this shows that the dislocation tangles within the grains disappear when the finer grains grow up slightly in some extent, but the dislocation tangles exist still in some of the grains as marked by A and B in Fig.7(b).
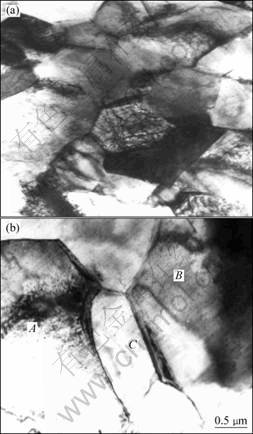
Fig.7 Microstructures of AZ31 alloy after extruded at 420 ℃: (a) Dislocations tangle piled up within finer grains; (b) No dislocation detected within grain as marked by C
4 Conclusions
1) The optimal aged time after the AZ31 alloy extruded at different temperatures is determined as 16 h at 180 ℃.
2) Hot extrusion technique may obviously improve the mechanical properties of AZ31 alloy. This is attributed to the formation of the finer grains during hot extrusion of alloy.
3) After aged treatment, the finer particles are precipitated along the grain boundaries of alloys, this may effectively hinder the dislocation movement during deformation, so that the mechanical properties of the extruded alloy are enhanced.
4) The features of the microstructure evolution during hot extruded of AZ31 alloy are dislocation slipping on the matrix and occurrence of the dynamic recrystallization.
References
[1] TIAN Su-gui, KEUN Y S. Microstructure and creep of AM50-Sb-Gd alloys[J]. Material Science Forum, 2005, 488/489: 749-752.
[2] TIAN Su-gui, WANG Ling. Mechanical properties and deformation features of AZ31-0.84%Sb alloy[J]. Journal of Materials and Metallurgy, 2005, 14: 138-141.
[3] LIU Man-ping, WANG Qu-dong, ZENG Xiao-qin, YUAN Guang-yin, ZHU Yan-ping, DING Wen-jiang. Mechanical Properties and creep behavior of Mg-Al-Ca alloys[J]. Material Science Forum, 2005, 488/489: 763-766.
[4] HUANG Xiao-feng, WANG Qu-dong, ZENG Xiao-qin. Influence of rare earth on mechanical properties and high temperature creep properties of AM50 magnesium alloy[J]. Journal of the Chinese Rare Earth Society, 2004, 22(4): 493-496.(in Chinese)
[5] YUAN Guang-yin, ZENG Xiao-qin, LV Yi-zheng, DING Wen-jiang, SUN Yang-Shan. Mechanical properties improvement of Mg-Al based alloy with Sb addition[J]. Journal of Materias Engineering, 2001, 4: 10-15.
[6] YUAN Guang-yin, SUN Yang-san, ZHANG Wei-min. Effect of Bismuth on the microstructure and mechanical properties of cast magnesium alloys[J]. Foundry, 1998, 5: 5-7.
[7] SUN Yang-san, WANG Zhong-kun, YUAN Guang-ying. Effects of Sn addtion on microstructure and mechanical properties of magnesium alloys[J]. Trans Nonferrous Met Soc China, 1999, 9(1): 55-60.
[8] ZHAO Yun-Hu, WANG Qu-Dong, DING Wen-Jiang. Effect of Be on the microstructure of cast Mg alloy[J]. Special Casting and Nonferrous Alloys, 2000, 3: 10-13.
[9] WANG Qu-Dong, CHEN Yong-Jun, PENG Jian-Guo,LIU Man-Ping, DING Wen-Jiang, SUERY M, BLANDIN J J. Microstucture and mechanical properties of AM50+x Ti magnesium alloys extruded from as-cast and solution treatment conditions[J]. Material Science Forum, 2005, 488/489: 629-632.
[10] ZHOU Ming, GAO Jian-yong, YU Fu-lin, WEI Xia. Evalution of magnesium extrusion production[J]. Material Science Forum, 2005, 488/489: 483-486.
(Edited by HE Xue-feng)
Foundation item: Projects(200220331) supported by the Natural Science Foundation of Liaoning Province, China
Corresponding author: WANG Ling; Tel: +86-24-25691315; E-mail: hill-wang2005@163.com