过共晶Al-Si合金快速凝固组织演变
梁红玉1, 2, 毛协民1, 胡志恒1
(1. 上海大学 材料科学与工程学院, 上海 200072;
2. 中北大学 机电工程系, 太原 030008)
摘 要: 以群体动力学模型为基础, 在充分考虑合金的热物性参数、 过饱和度以及第二相形核率变化的基础上, 提出描述该合金快速凝固组织演变的数学模型, 并结合A390合金进行计算。 结果表明: 随着雾化合金液滴尺寸的减小, 平均冷却速度增加, 而初生Si相长大时间减少, 所析出初生Si相的尺寸及体积分数也不断减小; 当粉末尺寸减小到某一临界值时, 初生Si相消失, 从而使不同尺寸粉末的微观组织发生很大的变化。 计算结果与实验结果吻合较好, 说明此提出的模型可以较好地预测过共晶Al-Si合金快速凝固组织的形成, 从而为进一步研究高硅合金材料的组织演变奠定基础。
关键词: 快速凝固; 雾化液滴; 微观组织演变; 模拟; 群体动力学 中图分类号: TG244; TB115
文献标识码: A
Microstructure evolution of hypereutectic Al-Si alloy during rapid solidification
LIANG Hong-yu1, 2, MAO Xie-min1, HU Zhi-heng1
(1. School of Material Science and Engineering, Shanghai University,Shanghai 200072, China;
2. Department of Mechanical and Electronic Engineering, Zhongbei University,Taiyuan 030008, China)
Abstract: Based on both the population dynamics model and the continuous variety of thermo-physical parameters, supersaturation and nucleation rate, a model was developed to describe the microstructure evolution of hypereutectic Al-Si alloy during rapid solidification, and was solved for A390 alloy. The results show that, with the droplet size decreasing, the average quenching velocity increases and the growth time, size and volume fraction of primary Si decrease. The primary Si of powder particle is extinct under a critical size, which result in the different microstructures of various powder particles. The results of atomization experiments of hypereutectic Al-Si alloys show a good agreement with the theoretical calculations. The model can be used to predict satisfactorily the microstructures evolution of hypereutectic Al-Si alloys.
Key words: rapid solidification; atomized droplets; microstructure evolution; simulation; population dynamics
在快速凝固过程中, 过共晶Al-Si合金液迅速通过固液两相区, 可以得到细小初生Si相均匀分布于基体中的微观组织[1-3], 当合金液冷却速度足够大时, 初生Si相形核和长大将被抑制, 熔体过冷进入共晶耦合区时可以获得伪共晶组织, 而熔体过冷进入非共晶耦合共生区发生凝固, 则可以获得初生α或β相与(α+β)共晶的混合组织(见图1)[4-6] 。 初生Si相尺寸及体积分数的改变, 对材料各种性能将产生很大的影响[2]。 研究过共晶Al-Si合金材料在快速凝固过程中组织演变规律, 对于该材料, 特别是高硅合金材料在实际生产中的应用具有很大的指导意义[2-3]。
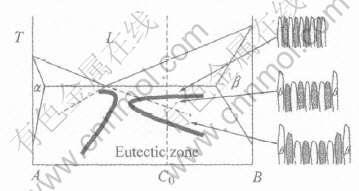
图1 α、 β相与(α+β)共晶的竞争生长[4-5]
Fig.1 Competitive growth of α, β and (α+β)[4-5]
Grant等[7]运用Scheil方程, 模拟了不同参数下雾化液滴的凝固行为。 Lee等[8]在假设一个液滴只形成一个晶核前提下, 模拟了气体初速度和液体金属过热, 特别是润湿角对单个液滴凝固行为的影响。 但是这些模拟计算都假定液滴凝固过程受形核或晶粒长大单一因素控制, 因而很难准确描述两种因素共同作用的凝固[9-10]。 在偏晶合金领域, Zhao等[11-12]成功发展了能描述在形核和晶粒长大共同作用下液-液相变过程中组织演化的群体动力学模型, 这种模型经过适当修正也适合描述液-固相变过程中等轴晶组织的凝固过程[10]。
在实际快速凝固过程中, 温度降低时, 液-固相变发生, 同时合金的热物性参数、 过饱和度以及第二相形核率也不断变化[13] 。 本文作者在群体动力学模型的基础上, 充分考虑了以上变化条件, 提出了描述过共晶Al-Si合金快速凝固过程中组织演变的数学模型, 研究初生Si相形核扩散长大及其生长变化行为, 从而为进一步研究高硅合金材料组织演变奠定了基础。
1 数学模型的建立
1.1 温度演变规律
对于Si含量较高的过共晶铝硅合金材料, 在快速凝固条件下, 当温度下降到Tl(合金液相线温度)以下某一温度Tx时, 初生Si相作为先导相开始形核, 本文作者假设剩余液相开始形成共晶组织的温度为Ts, 则合金熔体从Tx冷却到Ts所需的时间即初生Si相长大时间。
在快速凝固雾化制粉过程中, 不同尺寸液滴的平均冷却速度也不相同。 研究表明[7]在假设液滴为球状, 考虑液滴对流散热, 忽略液滴内部的温度梯度的条件下, 雾化铝硅合金液滴温度随时间的变化可描述为[7-8]

式中 L为析出相的结晶潜热; ρd, cd分别为液态金属密度和热容; φs为液滴中的固相分数; Tg为雾化气体的温度; h为热传递系数。
1.2 均匀形核及实际过冷度
雾化形成的液滴尺寸越小, 所获得的冷却速度越大, 同时小液滴中含有异质晶核的概率也越小, 因而获得的过冷度越大。 根据Hirth[14]及Turbull等[15]理论, 均匀形核过冷度ΔTc及实际形核过冷度ΔT分别为:
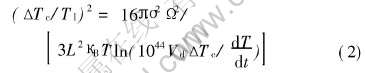

式中 σ为固液两相之间的界面张力; Ω为平均原子体积; κB为Boltzmann常数; Vd为液滴的体积, Vd=πd3/6(d为原子直径)。
1.3 形核率
通常情况下用经典形核理论来描述初生Si相的形核, 则稳态形核速率可表示为[13, 16]
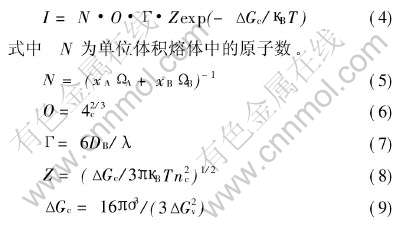
式中
为形核驱动力; ΩA, ΩB和xA, xB分别为A, B组元的原子体积和摩尔分数; nc为临界晶核(半径R=2σ/ΔGv)中的原子数; DB为溶质原子Si的扩散系数; λ为溶质原子的平均跳动距离, 取为Al原子的直径; Tl为合金液相线温度; ΔGc为形核能量障碍。
1.4 初生Si相生长
初生Si相在过饱和的熔体中形核, 通过扩散长大, 生长速率可表示为[13, 17]

式中 cm(t)为t时刻基体熔体溶质的平均浓度; cB(t)为第二相的溶质浓度; cI(R, t)为第二相与基体界面处基体中溶质的浓度; R为第二相的半径。
假设界面的生长总处于局部平衡, 则界面处溶质浓度满足Gibbs-Thomson关系:

式中 αs=(2σΩd)/(κBT)为毛细长度; Ωd为第二相中平均原子体积; c∞(t)为平界面处的平衡成分。
1.5 群体动力学
考虑到形核, 扩散长大的共同作用, 则初生Si相的半径分布函数f(R, t)满足以下的连续性方程

式中 f(R, t)dR为单位体积熔体中半径在R到R+dR之间的初生Si相的数目。 由于第二相的形核和生长, 基体液相的平均浓度随时间不断变化, 根据溶质守恒:

式中 c0为熔体原始成分; φ(t)为第二相体积分数。

2 计算方法及模拟结果分析
为简化计算, 本研究在计算过程中作如下假设:
1) 所有液滴都在雾化喷嘴的出口处(z=0)形成, 其初速度为0, 初始温度973K;
2) 液滴在飞行过程中不考虑彼此间的碰撞[10];
3) 气体喷射压力为0.3MPa, 气体初速度340m/s[7], 气体初始温度、 最终温度分别为298K、 348K。
以A390合金为例, Ts为850K, 材料的热物性参数如表1所示。 计算过程如下: 首先利用式(1)~(3)计算液滴的温度及过冷度变化, 由此可以获得不同尺寸液滴的平均冷却速率及相应的Si相长大时间(t)。 假设初始合金熔体以相应的冷却速率从形核温度Tx开始冷却, 直至时间逐渐增至t(时间步长为dt)。 在每一时间步长的开始, 假设新形成的晶核的半径为此时临界晶核半径R, 然后利用式(4)、 (11)、 (13)和(15)计算Si相形核率、 长大速率, 从而得到在液固相变过程中初生Si相半径分布、 平均半径及体积分数的变化, 求解式(14)可以得到此时基体液相的浓度, 然后返回求解下一时刻各物理量的变化。
表1 A390合金的热物性参数[1]
Table 1 Thermo-physical properties of A390 alloy
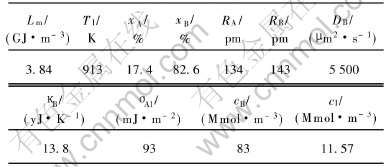
计算表明, 各液滴温度演变如图2所示。 不同尺寸液滴的形核率如图3所示。 从图2和3可以看出, 液滴尺寸越小, 所获得的平均冷却速度越大, 而初生Si相的粗化时间逐渐减小。 随着液滴尺寸的减小, 所能达到的最大形核率增加, 但当液滴尺寸不大于152μm时, 液滴所能达到的最大形核率开始下降; 当液滴尺寸为90μm时, 液滴内部不能形成Si相的结晶核心, 分析认为主要是由于液滴尺寸减小使冷却速度增加, 抑制了初生Si相的形核。
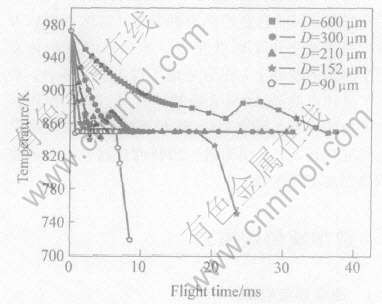
图2 不同尺寸液滴的温度演变曲线
Fig.2 Change curves of temperature evolution of droplets with different diameters
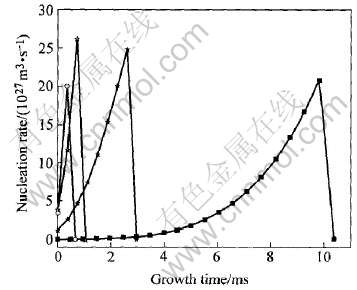
图3 不同尺寸液滴初生Si相形核率
Fig.3 Change curves of nucleation rate of primary Si of droplets with different diameters
图4所示为直径为600μm的液滴内部初生Si相尺寸分布及不同尺寸Si相的长大速度。 由图4可以看出, D=600μm液滴内部的初生Si相尺寸分布于3.8~5.4μm之间。 计算表明, 当初生Si相尺寸为3.8μm时, 其长大速度为1.02×103m/s, 而初生Si相尺寸为5.4μm时, 其长大速度为7.35×102m/s, 且随着Si相尺寸的增加其长大速度减小。
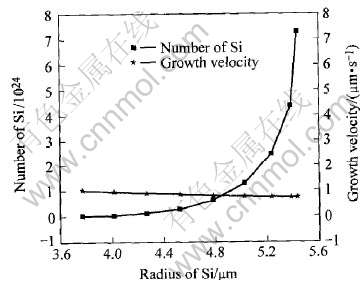
图4 初生Si相尺寸分布及长大速度(D=600μm)
Fig.4 Size distribution and growth velocity of primary Si(D=600μm)
图5和6所示分别为不同尺寸液滴初生Si相平均半径及基体液相浓度随时间的变化曲线。 由图5和6可看出, 在冷却开始阶段, 液滴中初生Si相尺寸迅速增加, 但由于Si相数量较少, 基体液相浓度下降缓慢。 随着液滴温度下降, 液相中不断形成大量新的初生Si相晶核, 在较低温度下, 由扩散控制的晶核长大变得缓慢。 随着Si相的不断析出、 长大, 基体液相的浓度逐渐降低, 然而直至初生Si相不再析出时, 剩余的液相仍具有一定的过饱和度。
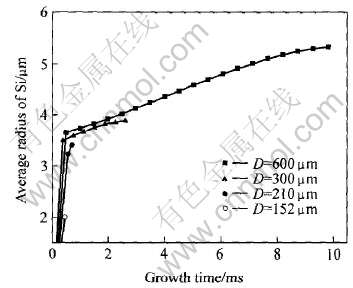
图5 初生Si相平均半径随时间的变化曲线
Fig.5 Change curves of average radius of primary Si with growth time
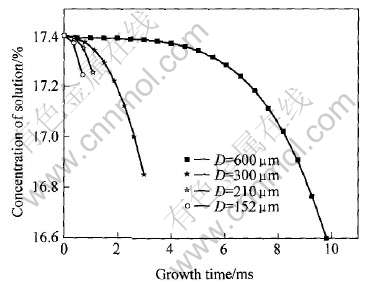
图6 基体液相浓度随时间的变化曲线
Fig.6 Relationship between concentration of solution and growth time
图7所示为液滴尺寸与初生Si相体积分数的关系。 从图7中可以看出, 随着液滴尺寸的减小, 所析出初生Si相的体积分数不断减少, 当粉末直径为90μm时, 初生Si相消失, 标志着冷却速度的增加使初生Si 相的形核生长被完全抑制, 因而导致不同尺寸的液滴内部组织发生变化。
3 实验验证
实验在自制的雾化装置上进行, 实验装置如图8所示。 A390合金在石墨坩埚中重熔, 熔体温度T
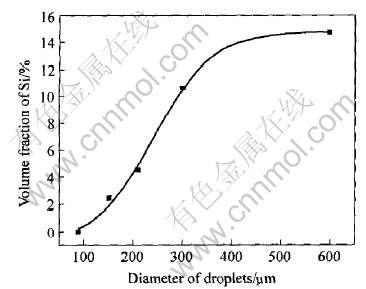
图7 不同尺寸粉末颗粒初生Si相体积分数
Fig.7 Volume fraction of primary Si for different sizes of powder particles
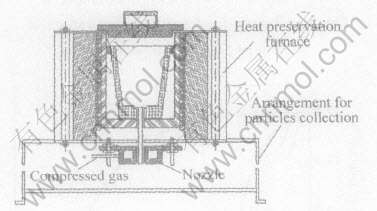
图8 气体雾化装置示意图
Fig.8 Schematic diagram of gas-atomizer arrangement
为973K。 50g熔融的合金液从雾化保温炉底部的陶瓷管中流出, 陶瓷管直径为6.4mm。 采用压缩空气作雾化介质, 选定进气压力p为0.3MPa, 喷嘴缝隙宽度δ为0.55mm, 出液口与喷嘴的高度差Δh为48.5mm。
对雾化制得的铝合金粉末用8411型电动振筛机进行筛分, 并用光电分析天平TG328B进行称量。 使用JXB-1型光学金相显微镜对不同粒度粉末的微观组织进行观察并做定量分析, 实验测得的不同粒度粉末中Si相尺寸与模拟结果比较如图9所示。 不同粒度粉末的微观组织如图10所示。 从图9中可以看出, 模拟结果与计算结果基本吻合。
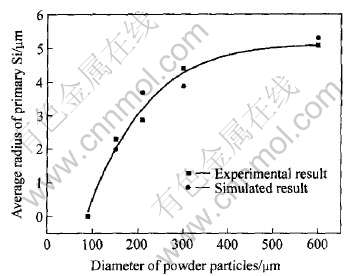
图9 初生Si相平均半径实验与模拟结果比较
Fig.9 Comparison of average radius of experimental and simulated results of primary Si
4 讨论
某一成分的合金随着液滴尺寸的减小, 含有异质晶核的概率越小, 获得的过冷度就越大。 对于过共晶合金, 当过冷到TE温度以下时, 热力学上出现了亚稳共晶组织析出的可能性, 如果固相的生长速率足够大, 则同时又具备了实际发生亚稳相析出的动力学条件。 从热力学上讲, 发生在TE线以下的凝固都可能按析出亚稳相的模式进行, 但是由于所形成的亚稳相并非处于最低吉布斯自由能状态, 如果界面上出现偶然的扰动, 溶质元素在固液间的再分配很容易发生, 导致亚稳转变的失稳和系统向平衡态的过渡。 因此, 发生亚稳转变的温度应低于TE温度, 如在Tx以下才能保持。 当过冷熔体在Tx温度以下某一温度TN开始形核生长时, 由于界面上存在的很大过冷(Tl-TN)通常都伴随着很高的生长速率, 凝固潜热很快释放。 如果生长界面的温度回升至Tx以上, 则亚稳转变的模式将不再能保持, 只有在开始凝固之前, 使熔体过冷到Tx以下更低的温度, 温度回升的结果也不至于超过Tx, 这样才能保证整个凝固过程按亚稳转变模式进行。 为此, 必须使熔体向外界的传热速率足够快, 满足

式中 h为避免温度回升至Tx以上所必须的最低界面传热系数; ρ为固相密度。
将h=Nuκg/d代入式(16), 可知对于确定的合金系在一定的雾化条件下进行的快速冷却, 应当保证液滴尺寸足够小, 才能使(16)式成立。

则发生亚稳转变的临界液滴尺寸为

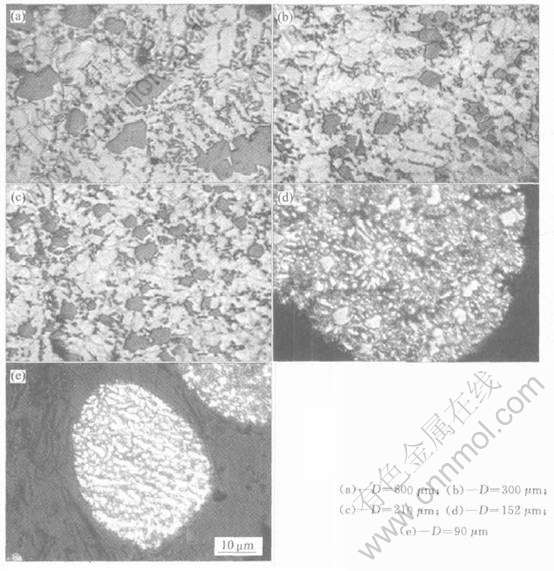
图10 不同尺寸粉末颗粒内部微观组织
Fig.10 Microstructures of powder particles with different sizes
5 结论
1) 以群体动力学模型为基础, 在充分考虑合金的热物性参数, 过饱和度以及第二相形核率变化的条件下, 提出了一个描述雾化过共晶Al-Si合金液滴快速凝固过程中组织演变的数学模型, 并结合A390合金进行了计算。
2) 计算表明, 在A390合金中, 随着液滴尺寸的减小, 平均冷却速度增加, 而初生Si相的长大时间减少, 所析出初生Si相的尺寸及体积分数也不断减小, 当粉末直径为90μm时, 初生Si相消失, 过共晶Ai-Si合金液滴发生亚稳共晶组织转变的临界尺寸为

计算结果与实验结果基本吻合。
3) 本研究所提出的模型可以较好地预测过共晶Al-Si合金在快速凝固过程中的组织形成, 从而为进一步研究高硅合金材料的组织演变奠定了基础, 该模型对于其它共晶系合金同样具有一定的指导意义。
REFERENCES
[1]Kurz W, Fisher D J. Fundamentals of Solidification 3rd Edition[M]. Switzerland: Trans Tech Publications Ltd, 1989: 292-294.
[2]Allen D R, Gremaud M, Perepezko J H. Nucleation-controlled microstructural development in Al-Si alloys[J]. Mater Sci Eng A, 1997, 226-228: 173-177.
[3]Das S K, Perepezko J H, Wu R I, et al. Undercooling and glass formation in Al-based alloys[J]. Mater Sci Eng A, 2001, 304-306(1-2): 159-165.
[4]Suk M J, Choi G H , Moon I H. Formation of halo in Sb-InSb and Sn-Bi eutectic alloy systems[J]. Cryst Growth, 1992, 123(6): 5-16.
[5]Suk M J, Leonartz K J. Halo growth during unidirectional solidification of camphor-naphthalene eutectic system[J]. Cryst Growth, 2000, 213(5): 141-149.
[6]李双明, 马伯乐, 李晓历, 等. 定向凝固下共晶合金中相的竞争生长[J]. 中国科学E辑, 2005, 35(5): 479-489.
LI Shuang-ming, MA Bo-le, LI Xiao-li, et al. Phases competitive growth of eutectic alloys during directional solidification[J]. Science in China E, 2005, 35(5): 479-489.
[7]Grant P S, Cantor B, Katerman L. Modeling of droplet dynamic and thermal histories during spray forming Ⅰ—Individual droplet behavior[J]. Acta Metall Mater, 1993, 41(11): 3097-3108.
[8]Lee E S, Ahn S. Solidification progress and heat transfer analysis of gas-atomization alloy droplets during spray forming[J]. Acta Metall Mater, 1994, 42(9): 3231-3243.
[9]柳百成, 荆涛. 铸造工程的模拟仿真与质量控制[M]. 北京: 机械工业出版社, 2001: 154-164.
LIU Bai-cheng, JING Tao. Numerical Simulation and Quality Control for Casting Engineering[M]. Beijing: China Machine Press, 2001: 154-164.
[10]刘东明, 赵九洲, 叶恒强. 喷射成形中金属液滴凝固过程的计算机模拟[J]. 金属学报, 2003, 39(4): 375-380.
LIU Dong-ming, ZHAO Jiu-zhou, YE Heng-qiang. Modeling of the solidification of gas-atomized alloy droplets during spray forming[J]. Acta Metallurgica Sinica, 2003, 39(4): 375-380.
[11]Zhao J Z, Drees S, Ratke L. Strip casting of Al-Pb alloys—A numerical analysis[J]. Mater Sci Eng A, 2000, 282(1): 262-269.
[12]Zhao J Z, Ratke L, Feuerbacher B. Microstructure evolution of immiscible alloys during cooling through the miscibility gap[J]. Modelling and Simulation in Materials Science and Engineering, 1998, 6(2): 123-139.
[13]郭景杰, 刘源, 贾均, 等. 过偏晶合金快速凝固过程中第二相液滴在液-液相变区内的粗化[J]. 金属学报, 2001, 37(4): 363-368.
GUO Jing-jie, LIU Yuan, JIA Jun, et al.Coarsening process of minority phase droplets during rapid cooling an immiscible alloy through the miscibility gap[J]. Acta Metallurgica Sinica, 2001, 37(4): 363-368.
[14]Hirth J P. Nucleation, undercooling and homogeneous structure in rapid solidified powders[J]. Metallurgical Transactions A (Physical Metallurgy and Materials Science), 1978, 9(3): 401-404.
[15]Turbull D, Cech R E. Microscopic observation of the solidification of small metal droplet[J]. Journal of Apply Physics, 1950, 21(3): 804-808.
[16]Zhao J Z, He J, Hu Z Q, et al. Microstructure evolution in immiscible alloys during rapid directional solidification[J]. Materials Research and Advanced Techniques, 2004, 95(5): 362-368.
[17]Xu Q, Lavernia E J. Influence of nucleation and growth phenomena on microstructural evolution during droplet-based deposition[J]. Acta Mater, 2001, 49(18): 3849-3861.
(编辑李艳红)
基金项目: 兵器装备预研基金资助项目(514120203)
收稿日期: 2006-04-08; 修订日期: 2006-09-20
通讯作者: 梁红玉, 副教授; 电话: 021-56337342; E-mail: lhy0351@163.com