Trans. Nonferrous Met. Soc. China 20(2010) s1010-s1015

Research and development of gas induced semi-solid process for industrial applications
J. WANNASIN1, S. JANUDOM1, T. RATTANOCHAIKUL1, R. CANYOOK1,
R. BURAPA2, T. CHUCHEEP1, S. THANABUMRUNGKUL1
1. Department of Mining and Materials Engineering, Faculty of Engineering, Prince of Songkla University,
Hat Yai, Songkhla, 90112, Thailand;
2. Department of Industrial Engineering, Faculty of Engineering, Rajamangala University of Technology Srivijaya, Songkhla, 90000, Thailand
Received 13 May 2010; accepted 25 June 2010
Abstract: Several rheocasting processes are developed or applied worldwide in the metal forming industry. One of the new rheocasting processes is the gas induced semi-solid (GISS) process. The GISS process utilizes the principle of rapid heat extraction and vigorous local extraction using the injection of fine gas bubbles through a graphite diffuser. Several forming processes such as die casting, squeeze casting, gravity casting, and rheo-extrusion of the semi-solid slurries prepared by the GISS process have also been conducted. The GISS process is capable of processing various alloys including cast aluminum alloys, die casting aluminum alloys, wrought aluminum alloys, and zinc alloys. The GISS process is currently developed to be used commercially in the industry with the focus on forming semi-solid slurries containing low fractions solid (< 0.25) into parts. The research and development activities of the GISS process were discussed and the status of the industrial developments of this process was reported.
Key words: gas induced semi-solid; rheocasting; die casting; formation mechanism; industrial applications
1 Introduction
Semi-solid metal forming employing the rheocasting approach has attracted interests in recent years[1-3]. The needs to produce high quality parts with lower costs are the driving force for this attention. Several techniques are applied in the worldwide industry including the NRC[4], SLC[5], SSR[6], rheo-die casting[7], rapid-S[8], and several more[9]. One of the newer techniques that are in the research and development stage is the gas induced semi-solid(GISS) process[10-13]. This process utilizes the principle of rapid heat extraction and vigorous local extraction using the injection of fine gas bubbles through a graphite diffuser. Semi-solid slurries with different solid fractions can be obtained simply by varying the diffuser immersion times.
The current focus of the GISS process is on forming semi-solid slurries containing low fractions solid (< 0.25) into parts. This allows prompt exploitation of the benefits of semi-solid metal in several forming processes since little modifications to the current machines and processing steps are required[14]. Previous studies have shown that the GISS process can be applied conveniently and efficiently with a die casting machine, requiring only minimal modifications of the process[13]. In addition, the process has been shown to be able to produce slurries of various alloys, including those with the compositions close to the eutectic composition[12-13].
To demonstrate its commercial potential, it is important that the research and development activities of the GISS process shift from laboratory scale to industrial scale. This work aims to discuss the research and development activities of the GISS process that are carried out and to report the status of the industrial developments of this process.
2 GISS process
Current rheocasting processes use different techniques to produce metal slurries. Most of them, however, utilize the application of agitation to a molten metal coupled with controlled cooling during solidification to achieve grain multiplication by dendrite fragmentation[14-16]. Examples of the processes include mechanical stirring[17], electromagnetic stirring[18], low-temperature casting[19-20], and ultrasonic vibrations[21-22]. These techniques use different media or means to apply agitation to the melt such as solid impellers or cylindrical rods, electromagnetic force, convection from fluid flow, and vibrations, respectively[11]. The GISS process, on the other hand, induces vigorous convection to the melt using fine gas bubbles as the medium. Various configurations may be used to introduce the fine gas bubbles to the melt, including gas injection through a nozzle or through porous media as presented schematically in Fig.1[23]. Currently, the configuration shown in Fig.1(c) is selected to use in the GISS machine due to its efficiency and simplicity. In the GISS process, the steps start by having a molten metal with a predetermined amount at a temperature about 10 to 20°C above the liquidus temperature. Then, the porous graphite diffuser is immersed, injecting fine inert gas bubbles into the melt for a predetermined time until the desired solid fraction is achieved. Consequently, the semi-solid slurry is formed and is ready for a further forming step. Fig.2 shows the processing steps schematically in the GISS process.
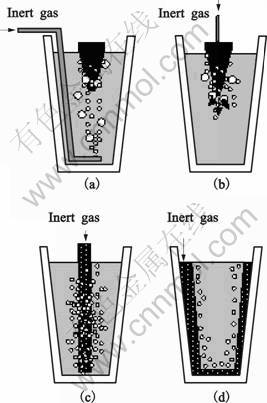
Fig.1 Examples of possible configurations for introducing fine gas bubbles to melt[23]
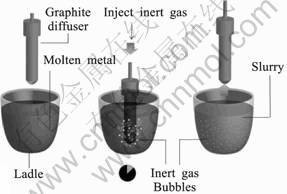
Fig.2 Schematic representation of steps in GISS process
3 Formation mechanism
The exact mechanism for semi-solid metal structure formation is still unclear. However, it is well accepted that the globular structure is obtained when numerous solid grains are present at the early stages of solidification[24]. Then, the high density of the solid grains grows non-dendritically, resulting in semi-solid metal structure[25].
The likely theory that can explain how a large number of solid particles are formed is grain multiplication by dendrite fragmentation[26]. It has been proposed that the convection produced during the solidification causes dendrite arms to be detached by melting off or breaking off. These detached arms then act as secondary nuclei particles. A schematic diagram of the dendrite multiplication theory is shown in Fig.3.

Fig.3 Schematic diagram of dendrite multiplication model[27]
In the GISS process, convection is effectively achieved by the flow of a large number of very fine gas bubbles out of the cold diffuser surfaces into the melt. This vigorous convection is believed to cause grain multiplication, resulting in a large number of fine disintegrated solid particles.
Using a rapid quenching mold, a study has shown the evolution of grain particles of A380 alloy at various time during the GISS process (Fig.4)[28]. The micrographs show that the microstructure consists of a mixture of globular, rosette, and dendrite particles at the early stages of the rheocasting process. These globular and the rosette particles are believed to be the disintegrated particles resulting from the dendrite fragmentation due to the remelting mechanism. This mechanism explains that secondary or tertiary arms are detached by remelting at the roots due to solute enrichment and thermo-solutal convection near the dendrite roots[27, 29].
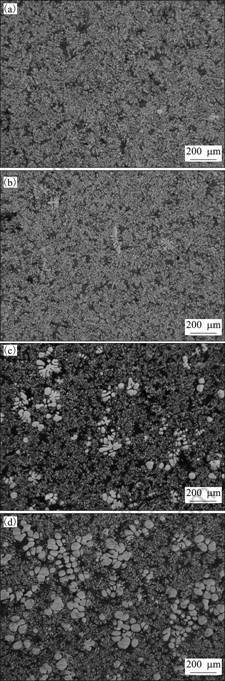
Fig.4 Microstructures of samples quenched after rheocasting time of 15 s (a) , 17 s (b), 20 s (c) and 90 s (d)[28]
Following this mechanism, it can be explained that the cold graphite diffuser that is immersed in the melt with low superheat temperature causes numerous fine dendritic grains to nucleate and grow on the diffuser surfaces. These grains are quickly “pushed” out to the bulk liquid by the flow of gas bubbles. Most of these very fine “mother dendrite” grains will then be re-melted at the first few seconds of the rheocasting process since the bulk liquid still consists of several small pools of superheated liquid. Only few disintegrated particles survive and are left in the melt as observed at the early time in Figs.4(a) and (b). After the superheat temperature is removed from the melt, more disintegrated particles can survive as observed at longer times in Figs.4(c) and (d). These fine particles will then grow and eventually coarsen to yield globular structure.
4 Applications of GISS process
The current focus of the GISS process is on forming semi-solid slurries containing low fractions solid (< 0.25) into parts even though the GISS process can also produce semi-solid metal containing higher fractions solid (0.3-0.6). The key reason for this choice is the prompt exploitation of the benefits of semi-solid metal in the casting industry since little modifications to the current machines and processing steps are required for this approach.
Several forming processes such as die casting, squeeze casting, gravity casting, and rheo-extrusion of the slurries prepared by the GISS process have been researched and developed for the past two years. In these forming processes, the added step is the immersion of graphite diffuser to inject gas bubbles for the duration of about 5-20 s. Semi-solid slurries containing up to 25% solid are then poured into shot sleeve holes, squeeze casting dies, sand molds, or extrusion shot holes for the GISS die casting, squeeze casting, sand casting, and rheo-extrusion, respectively. Fig.5 shows the schematic diagram of these GISS forming processes.

Fig.5 Schematic diagrams of GISS forming processes: (a) GISS die casting; (b) GISS squeeze casting; (c) GISS rheo-extrusion; (d) GISS low pressure casting
Various commercial alloys have been produced using the GISS process. Examples of the alloys, shown in Fig.6, include cast aluminum alloys, die casting aluminum alloys, wrought aluminum alloys and zinc die casting alloys such as 356, A380, A383, 5052, 6061, 2024, 7075, and ZAMAK-3.
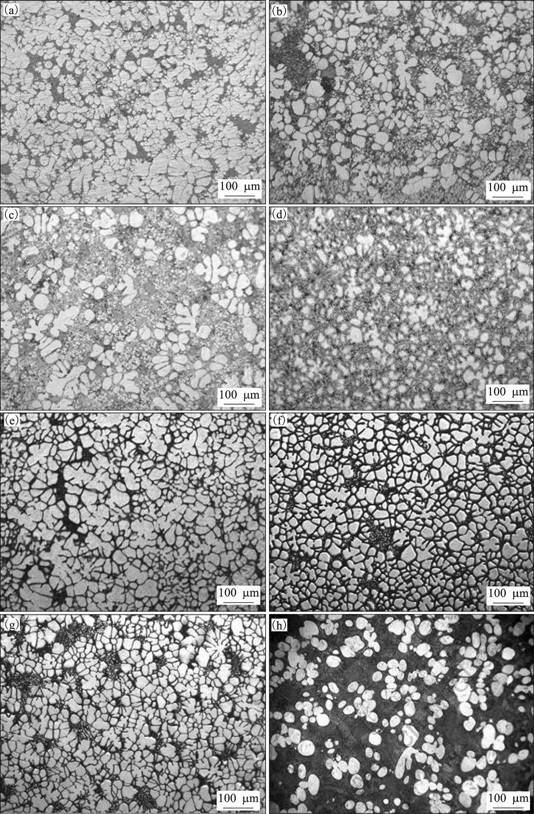
Fig.6 Microstructures of various alloys formed by GISS slurry casting processes: (a) 356; (b) A380; (c) A383; (d) 5052; (e) 6061; (f) 2024; (g) 7075; (h) ZAMAK-3
5 Development of industrial applications
The current industrial developments of the GISS process mainly involve the development of the GISS machines. The first versions of the machines used a handheld graphite diffuser to perform laboratory experiments (Fig.7(a)). Later, a semi-automatic machine (Fig.7(b)) was developed allowing a better control of the solid fractions to be produced. However, this machine still required manual ladling and pouring. Currently, an automatic version is developed to be used with a die casting machine. Fig.7(c) shows the prototype machine tested with an 80 t die casting machine.
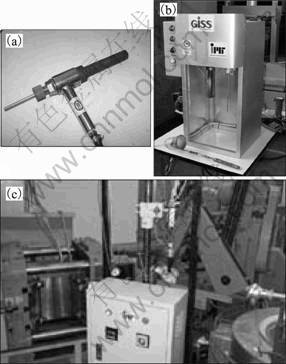
Fig.7 Different versions of GISS machines: (a) Handheld; (b) Semi-automatic; (c) Automatic
Currently, several commercial parts are being developed using the GISS process. Fig.8 shows some of these parts, which include an automotive rotor cover, a prosthesis tube adaptor, and a prosthesis foot adaptor. Other automotive and electronic applications are also considered. All the commercial activities are conducted by GISSCO, Co. Ltd.
6 Summary
This paper describes the gas induced semi-solid (GISS) process, which is developed in the industry. The process is currently focusing on producing low fractions solid for slurry casting processes. The GISS process requires minimal modifications to the machine and processing steps. It also allows the use of several currently available alloys: both casting and wrought alloys. Currently, the process is developed for several commercial applications.
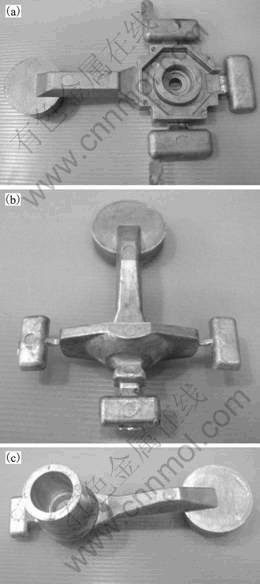
Fig.8 Examples of parts developed using GISS slurry die casting process: (a) Rotor cover; (b) Foot adaptor; (c) Tube adaptor
Acknowledgements
The authors would like to thank the financial supports from several sources including the Thai Research Fund (No. MRG5280215), Prince of Songkla University (No. AGR530031M), the Royal Golden Jubilee Ph.D. Program (No. PHD/0134/2551 and PHD/0173/2550), Prince of Songkla University for Ph.D. 50% Scholarship, the Materials Engineering Research Center, Western Digital, Mattel, the National Metal and Materials Technology Center (MTEC), and the National Science and Technology Development Agency (NSTDA).
The helps from the Innovative Metal Technology team, especially, Miss Buasang, Miss Chalinda, and Mr. Trinnamet are gratefully acknowledged. We also thank our collaborators, Dr. Pongsak Dulyapraphant, GISSCO Co., Ltd., and UMC Die Casting.
References
[1] LADOS D A, APELIAN D. Processing of Alloys and Composites[C]//. Proceedings of the 8th International Conference on Semi-solid. Limassol, Cyprsu, 2004.
[2] KANG C G, KIM S K, LEE S Y. Processing of Alloys and Composites[C]//. Proceedings of the 9th International Conference on Semi-solid. Busan, Korea, 2006.
[3] KNAUF F, BAADJOU R, HIRT G. Processing of Alloys and Composites[C]//. Proceedings of the 10th International Conference on Semi-solid. Aachen, Germany and Liege, Belgium, 2008.
[4] UBE Industries Ltd. Method and apparatus for shaping semisolid metals. EPO 745694A1 [P]. 1996.
[5] JORSTAD J, THIEMAN M, KAMM R. SLC, the newest and most economical approach to semi-solid Metal (SSM) casting [C]// The 7th International Conference on Semi-Solid Processing of Alloys and Composites. Tsukuba, Japan, 2002: 701-706.
[6] YURKO J A, MARTINEZ R A, FLEMINGS M C. Development of the semi-solid rheocasting (SSR) process [C]// The 7th International Conference on Semi-solid Processing of Alloys and Composites. Tsukuba, Japan, 2002: 659-664.
[7] FAN Z. Development of the rheo-diecasting process for magnesium alloys [J]. Materials Science and Engineering A, 2005, 413/414: 72-78.
[8] GRANATH O, WESSEN M, CAO H. Determining effect of slurry process parameters on semisolid A356 alloy microstructures produced by rheo metal process [J]. International Journal of Cast Metals Research, 2008, 21(5): 349-358.
[9] HIRT G, KOPP R. Thixoforming-semi-solid metal processing [M]. Germany: Wiley-VCH, 2009.
[10] WANNASIN J, MARTINEZ R A, FLEMINGS M C. Grain refinement of an aluminum alloy by introducing gas bubbles during solidification [J]. Scripta Materialia, 2006, 55(2): 115-118.
[11] WANNASIN J, MARTINEZ R A, FLEMINGS M C. A novel technique to produce metal slurries for semi-solid metal processing [J]. Solid State Phenomena, 2006, 116: 366-369.
[12] WANNASIN J, THANABUMRUNGKUL S. Development of a semi-solid metal processing technique for aluminium casting applications [J]. Songklanakarin Journal of Science and Technology, 2008, 30(2): 215-220.
[13] WANNASIN J, JUNUDOM S, RATTANOCHAIKUL T, FLEMINGS M C. Development of the gas induced semi-solid metal process for aluminum die casting applications [J]. Solid State Phenomena, 2008, 141/142/143: 97-102.
[14] KIRKWOOD D H, SUERY M, KAPRANOS P, ATKINSON H V, YOUNG K P. Semi-solid processing of alloys [M]. New York, Heidelberg, Dordrecht: Springer, 2009.
[15] FLEMINGS M C. Behavior of metal alloys in the semisolid state [J]. Metallurgical Transactions B, 1991, 22B: 269.
[16] FLEMINGS M C. Behavior of metal alloys in the semi-solid state [J]. Metallurgical Transaction A, 1991, 4: 957-981.
[17] FLEMINGS M C, RIEK RG, YOUNG K P. Rheocasting processes [J]. AFS International Cast Metal Journal, 1976: 11-22.
[18] KENNY M P, COURTOIS J A, EVANS R D, FARRIOR G M, KYONKA C P, KOCH A A, YOUNG K P. Metals handbook [M]. 9th Ed. Ohio: ASM International, 1988: 327.
[19] TAUSIG G, XIA K. Thixoforming of a liquidus cast aluminum alloy [C]// The 5th International Conference on Semi-solid Processing of Alloys and Composites. Golden, Colorado, 1998: 473-480.
[20] XIA K, TAUSIG G. Liquidus casting of a wrought aluminum alloy 2618 for thixoforming [J]. Materials Science and Engineering A, 1998, 246: 1-10.
[21] ABRAMOV V O, ABRAMOV O V, STRAUMAL B B, GUST W. Hypereutectic Al-Si based alloys with a thixotropic microstructure produced by ultrasonic treatment [J]. Materials Design, 1997, 18(4/5/6): 323-326.
[22] JIAN X, XU X, MEEK T T, HAN Q. Effect of power ultrasound on solidification of aluminum A356 alloy [J]. Materials Letters, 2005, 59: 190-193.
[23] WANNASIN J, MARTINEZ R A, FLEMINGS M C. Method to prepare metal structure suitable for semi-solid metal processing. PCT/US2007/002 [P]. 2007.
[24] DE FIGUEREDO A. Science and Technology of Semi-Solid Metal Processing [M]. Illinois: NADCA, 2001.
[25] FLEMINGS M C. Solidification processing [M]. New York: McGraw-Hill Book Company, 1974.
[26] MARTINEZ R A, FLEMINGS M C. Evolution of particle morphology in semisolid processing [J]. Metallurgical and Materials Transactions A, 2005, 36: 2205-2210.
[27] Flemings M C, YURKO J A, Martinez R A. Solidification processes and microstructures [C]//A symposium in Honor of Wilfried Kurz as held at the 2004 TMS Annual Meeting. Charlotte, North Carolina, 2004: 3-14.
[28] WANNASIN J, CANYOOK R, BURAPA R, FLEMINGS M C. Evaluation of solid fraction in a rheocast aluminum die casting alloy by a rapid quenching method [J]. Scripta Materialia, 2008, 59: 1091-1094.
[29] Jackson K A, Hunt J D, Uhlmann D R, Seward T P. On the origin of the equiaxed zone in casting [J]. Transaction of the Metallurgical Society of AIME, 1966, 236: 149-157.
(Edited by LI Xiang-qun)
Corresponding author: J. WANNASIN; Tel: +66-74-287-312; E-mail: jessada.w@psu.ac.th, jessada@alum.mit.edu