Article ID: 1003-6326(2005)06-1214-05
Growth characteristics of MoS2 coatings prepared by unbalanced bipolar DC magnetron sputtering
WANG Ji-hui(王吉会)1, XIA Yang(夏 扬)1, E.Wieers2, L.M.Stals2, J.P.Celis3
(1. School of Materials Science and Engineering, Tianjin University, Tianjin 300072, China;
2. Institute for Materials Research, Limburg University Centrum, B-3590 Diepenbeek, Belgium;
3. Department of MTM, Katholieke Universiteit Leuven, B-3001 Leuven, Belgium)
Abstract: MoS2 coatings were prepared by unbalanced bipolar DC magnetron sputtering under different argon pressures and for different deposition times, and the structure and morphology of MoS2 coatings were determined and observed respectively by X-ray diffractometry and scanning electron microscopy. The results show that at lower argon pressures of 0.15Pa and 0.40Pa, MoS2 coatings are formed with the (002) basal plane parallel to the surface, whereas the coating deposited at the argon pressure above 0.60Pa has the (002) basal plane perpendicular to the surface. Two stages can be classified for the formation of MoS2 coating. At the initial stage of coating formation, the (002) basal plane with S-Mo-S layer structure grows on the substrate whatever the argon pressure is. And then the coating under 0.40Pa argon pressure still grows with (002) laminate structure, but the coatings under 0.88Pa and 1.60Pa argon pressures turn to grow with the mixed basal and edge orientations. The morphology and structure of MoS2 coatings are highly related to their growth rate and the energy of sputtered particles.
Key words: magnetron sputtering; molybdenum disulfide (MoS2); coating; growth mechanism CLC
number: TH117.2 Document code: A
1 INTRODUCTION
MoS2 coating is widely used as suitable solid lubricant in space and dry cutting technology owing to its hexagonal lamellar crystal structure[1, 2]. However its lubricating properties result directly from the as-deposited structure of MoS2 coatings. It is observed from the experimental tests that MoS2 coatings have a low friction coefficient (less than 0.04), long wear life and high oxidation resistance when their (002) basal plane is parallel to the surface. Whereas MoS2 coatings with (002) basal plane perpendicular to the surface have a high friction coefficient (larger than 0.4), poor wear durability and low oxidation resistance[1-5]. So the as-deposited structure of MoS2 coatings becomes the detrimental factor for the effectiveness of lubricant.
Since MoS2 target is not a good conductor, MoS2 coatings are commonly prepared by reactive DC or RF magnetron sputtering and IBAD techniques[6-11]. MoS2 coatings deposited by these methods mostly have their (002) basal plane perpendicular to the surface. MoS2 coatings with (002) basal plane parallel to the surface could be obtained only under the specific conditions such as low partial pressure of water vapor[12-14], vacuum heating[15] and low argon pressure[16].
Unbalanced bipolar DC magnetron sputtering technique, introduced and designed by Window and Savvides[17], combines the characteristics of DC and alternative current power, and is quite suitable for the preparation of non-conductive coatings (such as MoS2, Teflon) at lower argon pressure. In this work, unbalanced bipolar DC magnetron sputtering method is applied to develop MoS2 coatings under different argon pressures and for different deposition time. Microstructure and morphology of coatings are determined and observed by SEM and XRD techniques to explore the growth mechanism of MoS2 coatings and the precise conditions by which the coating with (002) basal plane parallel to the surface can be prepared.
2 EXPERIMENTAL
2.1 Preparation of coatings
A bipolar-pulse unbalanced DC magnetron sputtering system was used in this work for the deposition of MoS2 coatings[16, 17]. A MoS2 target made by Target Materials Inc. with a diameter of 75mm and a purity of 99% was used. Silicon wafer with (100) orientation was applied as the substrate, and the target-to-substrate distance was maintained at 65mm. The base vacuum pressure was about 1.0×10-3Pa. Before initiating coating deposition, the substrates were etched at a cathode current density of 2mA/cm2 and a bias voltage of -600V for 10min, and then the shutter was closed. MoS2 target was pre-sputtered for 10min under conditions identical to the selected deposition parameters before re-opening the shutter. MoS2 coatings were deposited at the cathodic current density of 10mA/cm2, argon pressures ranging from 0.15Pa to 3.10Pa with the same deposition time (14min), or for different deposition time (1-28min) under the argon pressures of 0.40Pa, 0.88Pa and 1.60Pa.
During the deposition process, the substrate was cooled by the water-cooling system which was mounted at the back of the substrate, and only one parameter was varied at one time.
2.2 Characterization of coatings
[BJ(,,,][BJ)] Vol.15 №.6 Growth characteristics of MoS2 coatings A laser profilometry (Rodenstock RM600) was used to measure the height of the edge between deposited and un-deposited parts on the substrate, and this height was characterized as the coating thickness.
The coatings were analyzed for their crystal orientation by X-ray diffractometer (Siemens D5000, CuKα at a wavelength of 0.154nm). The surface morphology was observed by scanning electron microscopy (Philips XL-30), and the argon content in the coating was determined by energy dispersive spectrometry(EDS).
3 RESULTS
3.1 Effect of argon pressure
The surface morphology and XRD patterns of MoS2 coatings deposited at different argon pressures are shown in Fig.1 and Fig.2, respectively. At lower argon pressures of 0.15Pa and 0.40Pa, MoS2 coatings have a smooth, compact and featureless morphology (Fig.1(a)). And there is only (002) basal plane orientation parallel to the surface in the coatings. (100) and (110) edge orientation peaks are not noticed (Fig.2). This implies that MoS2 coatings deposited at lower argon pressures have (002) plane parallel to the surface.
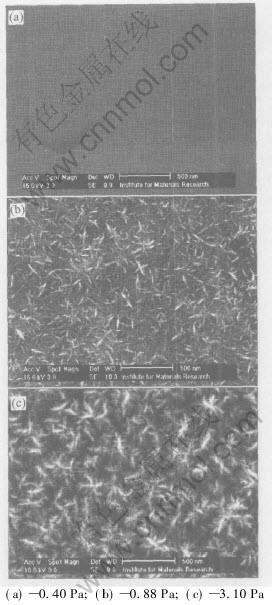
Fig.1 Surface morphologies of MoS2 coatings deposited under different argon pressures
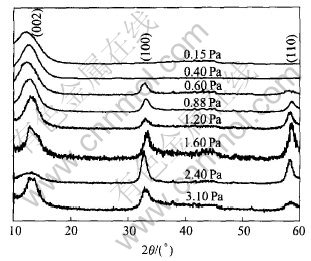
Fig.2 XRD patterns of MoS2 coatings deposited under different argon pressures
At argon pressure of 0.60-3.10Pa, MoS2 coatings have a porous, needle or worm-like microstructure, and the grain size and the porosity of these coatings become greater with the argon pressure increasing (Fig.1(b) and Fig.1(c)). As for the XRD pattern, (002) basal orientation, and (100) and (110) edge orientations coexist in the MoS2 coatings. And it is also found that the ratio of the intensity of edge orientations to basal orientation increases obviously with the deposition argon pressure increasing, i.e. MoS2 coatings deposited at 0.60-3.10Pa have the basal plane perpendicular to the surface or the edge plane parallel to the surface.
3.2 Effect of deposition time
Regarding the effect of argon pressure on the structure of MoS2 coating discussed above, three typical argon pressures of 0.40Pa, 0.88Pa and 1.60Pa are chosen to determine the effect of deposition time or coating thickness. Fig.3 and Fig.4 show the variation of surface morphology and XRD pattern of MoS2 coatings deposited under these three argon pressures with different coating thickness (i.e. deposition time).
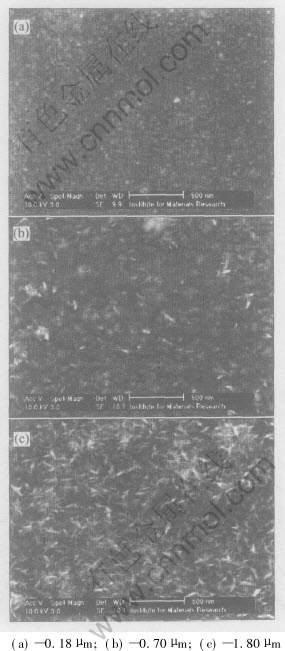
Fig.3 Surface morphologies of MoS2 coatings deposited at 0.88Pa with different coating thickness
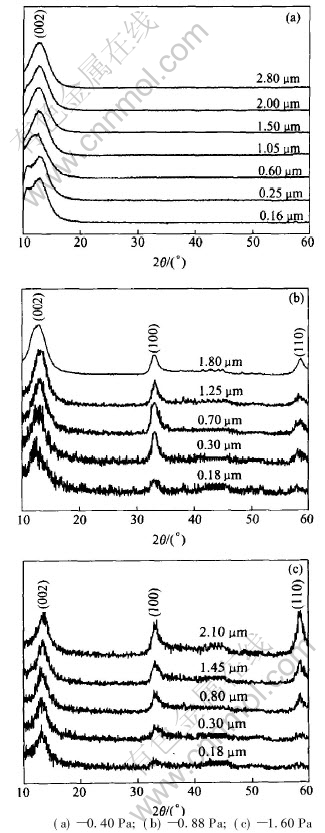
Fig.4 XRD patterns of MoS2 coatings with different coating thickness deposited at different argon pressures
At 0.40Pa argon pressure, the morphology of all MoS2 coatings is featureless whether the film thickness is 0.16μm or 2.80μm (1-28min). There is only a (002) peak in the XRD pattern. (100) or (110) edge orientation peaks are not found (Fig.4(a)). These results demonstrate that MoS2 coatings grow in S-Mo-S lamellar structure throughout the coatings.
At 0.88Pa and 1.60Pa argon pressures, MoS2 coatings have a smooth surface and a fine grain size at the initial stage of formation (the film thickness is about 0.18μm, shown in Fig.3(a)). Corresponding to this morphology, there is only a strong (002) peak in the XRD pattern, and (100) or (110) peak is too small to be noticed. With the elongation of deposition time, MoS2 coatings are gradually evolved with needle-like structure. Meanwhile, the grain size and porosity of the coatings increase (Fig.3(b) and Fig.3(c)). Reflected in the XRD patterns, the intensity of edge orientation (100) and (110) peaks is raised greatly with the coating thickness (Fig.4(b) and Fig.4(c)). At 1.60Pa pressure, the intensity of (100) or (100) peaks is larger than that of (002) peaks at the coating thickness of 2.10μm ( Fig.4(c)). These results indicate that there is a transition from (002) basal plane orientation to the mixed (002) basal and (100) or (110) edge orientations or to the edge dominant orientation for the formation of MoS2 coating at 0.88Pa and 1.60Pa pressures.
4 DISCUSSION
4.1 Growth rate
Fig.5 shows the dependence of coating thickness on argon pressure and deposition time. With the increase of argon pressure, the coating thickness for the same deposition time (i.e. growth rate) increases obviously (Fig.5(a)). At the initial stage of formation, the thickness of MoS2 coatings under different argon pressures is almost the same. But with the prolongation of deposition time, the coating thickness at higher argon pressure is larger than that at lower pressure, i.e. the higher the argon pressure, the larger the growth rate of MoS2 coating (Fig.5(b)).
From the results shown in Fig.1-4, it can be observed that MoS2 coatings will grow with (002) basal plane parallel to the surface under the lower growth rate such as at 0.40Pa or at the initial stage of 0.88Pa and 1.60Pa. Under higher growth rate, especially at higher argon pressure and the final stage of the coating, MoS2 coatings will be formed with the mixed (002) basal and (100) or (110) edge orientations. When forming in basal plane orientation, the deposited coatings have a smooth and compact surface owing to the lower growth rate. Otherwise when growing in the mixed basal and edge orientations, MoS2 coatings will develop in a rough, porous, needle-like morphology, and have a larger grain size because of the higher growth rate. These results are consistent with the Bucks conclusions[18] that the density of MoS2 coating in (002) basal orientation is greater than that in edge orientation.
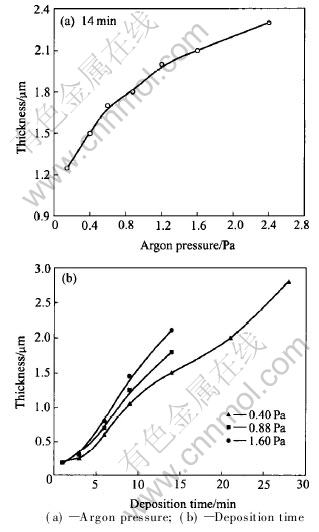
Fig.5 Variation of thickness of MoS2 coatings with argon pressure and deposition time
4.2 Energy of sputtered particles
Its well known that the formation of coating is related not only to the growth rate but also to the energy of the sputtering-deposition particles. The higher the energy of the sputtering-deposition particles, the more easily the coatings are formed in a compact structure (i.e. (002) basal plane orientation) due to the greater bombardment effect of the sputtering-deposition particles to the formerly deposited film[19].
According to the thermodynamics theory, the vacuum chamber contains larger amount of argon atoms at higher argon pressure, and then the argon atoms have a higher collision probability with the sputtered particles. So the argon atoms and sputtered particles lose their energy to reach the substrate, i.e. the bombardment effect of argon atom and sputtered particle to the coating is reduced. Thus the porous and rough structure of MoS2 coatings will be formed, meanwhile the content of argon atoms in the coatings will be dropped down. This conclusion could be supported by the content of argon element in the MoS2 coatings presented in Table 1. With the increase of argon pressure, the content of argon atoms in coatings decreases by about 3%-5%.Considering the effect of growth rate and
Table 1 Contents of argon element in MoS2 coatings deposited at different argon pressures
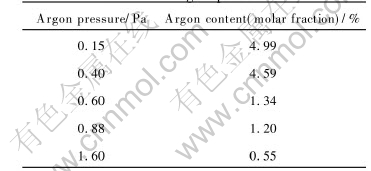
the energy of sputtered particles, it can be seen that MoS2 coatings at 0.40Pa are formed in S-Mo-S layer structure, and have a smooth, compact surface owing to the lower growth rate and higher energy of sputtered particles. Whereas at higher pressures of 0.88Pa and 1.60Pa, the coatings are formed in mixed basal and edge orientations and have a rough, porous surface because of the higher growth rate and lower energy of sputtered particles.
5 CONCLUSIONS
1) At lower argon pressures of 0.15Pa and 0.40Pa, MoS2 coating is formed with the (002) basal plane parallel to the surface; whereas the coatings deposited at the argon pressure above 0.60Pa have the (002) basal plane perpendicular, or (100) and (110) edge planes parallel to the surface.
2) Two stages can be classified for the formation of MoS2 coating. At the initial stage of coating formation, the (002) basal plane with S-Mo-S layer structure is grown on the substrate whatever the argon pressure is. Then the coating at lower argon pressure still grows with the (002) layer structure, but the coating under higher argon pressures will turn to grow with the mixed basal and edge orientations.
3) Under the condition of lower growth rate and higher energy of sputtered particles, MoS2 coatings have a smooth and compact morphology with (002) basal plane orientation parallel to the surface. Otherwise, the rough and porous microstructure, and mixed (002) basal and edge orientations will be evolved.
REFERENCES
[1]Spalvins T. A review of recent advances in solid film lubrication[J]. J Vac Sci Technol, 1987, A5(2): 212-219.
[2]Lince J R, Fleischauer P D. Crystallinity of RF-sputtered MoS2 films[J]. J Mater Res, 1987, 6(2): 827-838.
[3]Fleischauer P D. Effect of crystallite orientation on environmental stability and lubrication properties of sputtered MoS2 thin films[J]. ASLE Transactions, 1989, 27(1): 82-88.
[4]Lauwerens W, WANG Ji-hui, Wieers E, et al. Humidity resistant MoSx films prepared by pulsed magnetron sputtering[J]. Surface & Coatings Technology, 2000, 131(1-3): 216-221.
[5]WANG Ji-hui, CHEN Hua, Wieers E, et al. Comparison of the tribological properties of industrial low friction coatings[J]. Trans Nonferrous Met Soc China, 2002, 12(1): 78-82.
[6]Moser J, Levy F. Growth mechanisms and near-interface structure in relation to orientation of MoS2 sputtered thin films[J]. J Mater Res, 1992, 7(3): 734-740.
[7]Suzuki M. Comparison of tribological characteristics of sputtered MoS2 films coated with different apparatus[J]. Wear, 1998, 218: 110-118.
[8]WANG Ji-hui, ZHANG Hua-yi, LU Xin-chun, et al. Structure and microtribological characters of magnetic sputtering MoS2 thin films[J]. Lubrication Engineering, 1999, 2: 25-27. (in Chinese)
[9]ZHUANG Da-ming, LIU Jia-jun, ZHU Bao-liang, et al. A study on the friction and wear performances of MoSx thin films produced by ion beam enhanced deposition and magnetron sputtering[J]. J of Tribology, 1995, 15(4): 341-347. (in Chinese)
[10]Seitzman L E, Botster R N, Singer I L. IBAD MoS2 lubrication of titanium alloys[J]. Surface & Coatings Technology, 1996, 78: 10-13.
[11]LIU Dao-xin, TANG Bin, CHEN Hua, et al. MoS2 composite films on Ti alloy prepared by ion-beam-enhanced deposition[J]. The Chinese Journal of Nonferrous Metals, 2001, 11(3): 454-460. (in Chinese)
[12]Buck V. A neglected parameter (water contamination) in sputtering of MoS2 films[J]. Thin Solid Films, 1986, 139: 157-168.
[13]Buck V. Preparation and properties of different types of sputtered MoS2 films[J]. Wear, 1987, 114: 263-274.
[14]WANG Ji-hui, Lauwerens W, Wieers E, et al. Effect of power mode, target and liquid nitrogen trap on the structure and tribological properties of MoSx coatings[J]. Surface & Coatings Technology, 2002, 153: 166-172.
[15]Bertrand P A. Orientation of RF-sputter-deposited MoS2 films[J]. J Mater Res, 1989, 4(1): 180-184.
[16]WANG Ji-hui, Lauwerens W, Wieers E, et al. Structure and tribological properties of MoSx coatings prepared by bipolar DC magnetron sputtering[J]. Surface & Coatings Technology, 2001, 139(2-3): 143-152.
[17]Window B, Savvides N. Unbalanced dc magnetron as sources of high ion fluxes[J]. J Vac Sci Technol, 1986, A4(3): 453-456.
[18]Buck V. Structure and density of sputtered MoS2-films[J]. Vacuum, 1986, 36(1-3): 89-94.
[19]Seitzman L E, Bolster R N, Singer I L. X-ray diffraction of MoS2 coatings prepared by ion-beam-assisted deposition[J]. Surface & Coatings Technology, 1992, 52: 93-98. .
(Edited by YANG Bing)
Foundation item: Project(413175) supported by the Scientific Research Foundation for the Returned Overseas Chinese Scholars, Education Ministry of China
Received date: 2005-03-21; Accepted date:2005-06-06
Correspondence: WANG Ji-hui, Associate professor, PhD; Tel: +86-22-27890010; E-mail: jhwang@tju.edu.cn