
Oxidation and thermal fatigue of EB-PVD thermal barrier coatings on tube superalloy substrate
GAO Yu, ZHANG Chun-xia, ZHOU Chun-gen, GONG Sheng-kai, XU Hui-bin
Department of Materials Science and Engineering, Beijing University of Aeronautics and Astronautics,
Beijing 100083, China
Received 20 April 2006; accepted 30 June 2006
Abstract: Two-layer structure thermal barrier coatings (TBCs) (NiCoCrAlY (bond coat)+(6%-8%, mass fraction) Y2O3-stabilized ZrO2(YSZ top coat)) were deposited by electron beam physical vapor deposition (EB-PVD) on tube superalloy substrates. The samples were investigated by isothermal oxidation and thermal shock tests. It is found that the mass gains of the substrate with and without TBCs are 0.165 and 7.34 mg/cm2, respectively. So the TBCs system is a suitable protection for the substrate. In thermal shock tests the vertical cracks initiate at the top coat and grow into the bond coat, causing the oxidation of the bond coat along the cracks. Failure of the TBCs system occurs by the spallation of the YSZ from the bond coat, and some micro-cracks are found at the location where the fragment of the YSZ top coat spalled from.
Key words: thermal barrier coatings; electron beam physical vapor deposition; oxidation; thermal shock
1 Introduction
Since 1980s, the thermal barrier coatings (TBCs) have been used as powerful protection for aircraft gas turbine superalloy components to improve the durability and efficiency of the gas turbine engines in severe temperature environments[1,2]. Typical TBCs have a two-layer structure: a PtAl diffusion or an MCrAlY overlay bond coat and a ceramic topcoat of partially yttria stabilized zirconia (P-YSZ) which can be deposited by electron beam physical vapor deposition (EB-PVD) or by plasma spraying. Many studies have shown that the TBCs deposited by EB-PVD are superior to those deposited by plasma spraying because of the following reasons: 1) achieving a columnar structure for the ceramic coating, which exhibits a higher strain; 2) forming a smooth surface on the coating to avoid disturbing the aerodynamic flow around turbine blades; 3) varying the microstructures of the deposited ceramics by adjusting the deposition process parameters[3,4].
To guarantee the reliability of the gas turbine components, the lifetime assessment of the TBC and the failure prediction are very important[1]. Many studies have been conducted to reach a general agreement that several crucial factors strongly influence the eventual occurrence of the TBC failure, including the bond coat oxidation and creep, ZrO2 phase transformation, deposition residual stress, and vertical surface cracking. The vertical surface cracking in TBC is often the result of thermal shocks associated with fuel ignitions in an engine or turbine[5].
The objective of the work is to investigate the oxidation and fatigue behaviors of the TBCs on a tube superalloy substrate. Then NiCoCrAlY+(6%-8%) Y2O3 –stabilized ZrO2 (YSZ) two-layer structure TBCs was deposited by EB-PVD on a tube superalloy substrate in this study. An iso-thermal oxidation experiment was carried out to examine the mass gain. And then a thermal shock test was applied with an infrared heating system. The surfaces of the samples were first examined by optical microscopy. Then the cross-sectional microstructures of the TBC system were studied by SEM.
2 Experimental
The two-layer structure thermal barrier coatings were deposited by the EB-PVD method. Superalloy tubes with an outer diameter of 10mm and inner diameter of 8mm were used as substrate. A bond coat with an approximate composition of Ni-23Co-20Cr-8.5Al-1Y (mass fraction, %) was first deposited by EB-PVD with a thickness of about 50 μm. Then 8%Y2O3 partially stabilized ZrO2 (YSZ) was deposited on the bond coat with a thickness of about 100 μm.
Before the YSZ deposition, pre-treatments were carried out in vacuum at 1 323 K to improve the oxidation-resistance of the bond coat, and then surface shot-peening was applied to enhance the adherence of the bond coat and the YSZ top coat[6].
The isothermal oxidation was carried out at 1 323 K in air. A BS 224S electronic balance was used to measure the mass gain of the samples during oxidation. When the mass gain was measured, the sample was taken out of the heating furnace and cooled down in air. The lifetime was defined as the time until macro-crack or any spallation was observed by the naked eye. For comparison, the oxidation of the substrate was conducted.
Thermal shock test was carried out with an infrared heating system. The system can heat and cool the sample rapidly. During one cycle of the thermal shock test, the sample was first heated to 1 327 K (center, outer wall) in 20 s and held at the temperature for 2 min, then it was cooled down to 297K in 20 s and held for 2 min.
Only the center part of the sample was heated to get a longitudinal temperature gradient. The temperatures were about 1 327 K and 673 K for the center and the edge of the heated area, respectively. The room temperature compressed air was flowing through the tube sample during the thermal shock procedure, a radial temperature gradient existed. While the temperature of the top layer of the coat was about 1 327 K, that of the substrate was only about 1 027 K.
A scanning electron microscope(SEM) with energy disperse spectrum (EDS) was used to study the composition and microstructure of cross-sectioned samples after isothermal oxidation and thermal shock tests. Optical microscopy was used to examine the samples with low magnification.
3 Results and discussion
3.1 Isothermal oxidation behavior
Fig.1 shows the mass gain curves during isothermal oxidation for the substrate with and without coatings. It can be seen from Fig.1 that the mass gain for the uncoated substrates increases rapidly with the increase of the oxidation time, which is about 7.34 mg/cm2 after

Fig.1 Mass gain curves during isothermal oxidation for substrate with and without coatings
oxidized in air at 1 323 K for 200 h. For the coated sample, however, the mass gain gradually saturates with the increase of oxidation time after an increase of mass gain before 80 h. After 600 h of oxidation, the mass gain was only about 0.165 mg/cm2 which is much smaller than that of uncoated sample shown above. This indicates that the TBCs system is an excellent oxidation protection layer[7].
Fig.2 shows the cross-sectional SEM images of the
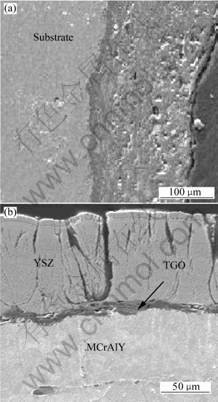
Fig.2 SEM cross-sectional images of sample after isothermal oxidation for 600 h: (a) Inner wall without TBCs; (b) Outer wall with TBCs
tube sample oxidized at 1 323 K for 600 h. Fig.2(a) shows the inner (wall without TBCs) and the outer wall (with TBCs) of the sample, respectively. The compositions obtained from EDS patterns of location A in Fig.2(a) is shown in Table 1. It can be seen clearly from Fig.2(a) that without the protection of the TBCs, the substrate is heavily oxidized with an oxidation layer as thick as over 200 μm. On the contrary, Fig.2(b) shows that, with the protection of TBCs, only a thin layer of TGO is formed on the surface of the bond coat during isothermal oxidation. This TGO layer can prevent further oxidation of the bond coat.
Table 1 Composition of location A in Fig.2(a)
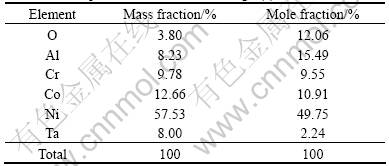
3.2 Thermal shock behavior
Fig.3 shows a cross-sectional SEM image of the TBCs after isothermal oxidation at 1 323 K in air for 160 h. It can be seen that the TBCs failed by the spallation of YSZ. During the isothermal oxidation, micro-cracks are initiated in the YSZ top coat along the columnar grain boundaries, and then grow through the whole top coat down to the TGO layer. The cracks in the TGO cause the bond coat to oxidize abnormally. Because of the volume increase, stresses are built up, which weak the combination of the interface between the top coat and the bond coat[3]. When the sample is cooled in air, a compressive stress is produced, which separates the bond coat from the bond coat and finally causes the failure of the TBCs system.
Fig.4 shows the cross-sectional SEM images taken from the center part of the tube sample after 6 000 cycles
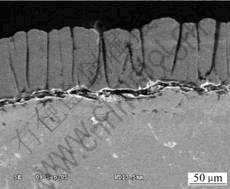
Fig.3 Cross-sectional SEM image of TBCs system after isothermal oxidized at 1 323 K in air for 160 h
of thermal shock. Fig.4(a) shows an image of the whole TBCs system, and Fig.4(b) shows the magnification of the bond coat. As can be seen from the figures, similar to image shown in Fig.3, vertical cracks are formed in the YSZ top coat. What different from Fig.3, however, is that the cracks also exist in the bond coat. During the thermal shock tests, the temperature of the surface of the YSZ can be as high as 1 373 K, while that of the substrate is only about 673 K because of the compressive air flowing through the tube, thus forming a radial thermal gradient. What is more, the high surface temperature and large temperature gradient across the coating thickness are produced very quickly during the test. In the heating process, the YSZ layer’s trend of thermal expend is limited by the inner layers due to their relatively lower temperature. Thus the YSZ top coat is under compressive stresses. Subsequent cooling causes the layers near the surface to develop significantly large tensile stresses and the gradient in tensile stresses is through the whole TBCs thickness[8]. Because of the tensile stresses, vertical cracks initiate and/or propagate in the YSZ top coat and then grow into the bond coat. The cycles of thermal shock make the change of state of strain like that of material in a traditional fatigue test, which may accelerate the cracks initiation and/or propagation process.
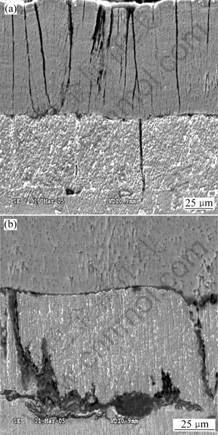
Fig.4 Cross-sectional SEM images of TBCs system after thermal shock for 6 000 cycles
From Fig.4(b), it can be seen that the bond coat is oxidized after thermal shock test for 6 000 cycles. After the vertical cracks initiate in the YSZ top coat, it acts as a channels through which the oxygen can reach the bond coat. At such a high temperature, the bond coat is oxidized in the presence of oxygen and the oxidation of the bond coat tends to happen along the cracks in it. From the above discussion, it can be concluded that the failure mechanism for the isothermal oxidation is different from that for thermal shock test.
Fig.5 shows an optical image of the outer sample surface after 9 376 cycles of thermal shock test. As shown in the image, many surface cracks are formed and a large fragment of YSZ top coat with the radius of about 200 μm spall from the bond coat. Moreover, three cracks exist in the spalled area of the YSZ top coat, which can be seen from the inset shown in Fig.5 clearly. The formation of such cracks is mainly due to the presence of cracks in the bond coat and the oxidation of the layer during the thermal shock test. As shown in Fig.4, before the spallation of YSZ top coat from the bond coat, vertical cracks have already initiated, along which the
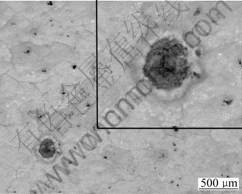
Fig.5 Optical image of surface of sample after thermal shock test for 9 376 cycles
bond coat is then oxidized. After the YSZ top coat is spalled, the bond coat is then exposed. In the cycles of heating and cooling, the stresses concentration at the vertical cracks in the bond coat leads to the horizontal propagation of the cracks.
4 Conclusions
1) The mass gain of the substrate oxidized at
1 323 K in air for 200 h is approximately 7.34 mg/cm2, while with TBCs, the mass gain of the TBCs system is only about 0.165 mg/cm2 after 600 h. This indicates that the TBCs system is suitable for the protection for the substrate at high temperature.
2) In the thermal shock test vertical cracks initiate at the top coat and grow into the bond coat, and then the bond coat is oxidized along the cracks.
3) The TBCs system fails by the spallation of the YSZ from the bond coat, and micro-cracks initiate in the bond coat where the fragment of the YSZ top coat spall from.
References
[1] LIU Y, PERSSON C, WIGREN J. Journal of Thermal Spray Technology, 2004, 13(3): 415-424.
[2] TOMIMATSU T, ZHOU S, KAGAWA Y. Acta Mater, 2003, 51: 2397-2405.
[3] BI X F, XU H B, GONG S K. Surf Coat Technol, 2000, 130: 122-127.
[4] MOVCHAN B A. JOM, 1996, 48(11): 40-45.
[5] ZHOU B, KOKINI K. Surf Coat Technol, 2004, 187: 17-25.
[6] GUO H B, GONG S K, KHOR K A, XU H B. Surf Coat Technol, 2003, 168: 23-29.
[7] ZHANG D B, GONG S K, XU H B, ZHANG H T, HAN Y F. Surf Coat Technol, 2003, 168: 78-83.
[8] RANGARAJ S, KOKINI K. Acta Mater, 2004, 52: 455-465.
(Edited by LONG Huai-zhong)
Foundation item: Project (50571005) supported by the National Natural Science Foundation of China
Corresponding author: XU Hui-bin; Tel: +86-10-82317117; Fax: +86-10-82317116; E-mail: xuhb@buaa.edu.cn