文章编号: 1004-0609(2005)05-0734-05
微量元素Sr对Al-Mg-Si-Cu基合金
车身板腐蚀性能的影响
卢广玺, 关绍康, 陈海军, 林敦文
(郑州大学 材料工程学院, 郑州 450002)
摘 要: 采用全浸腐蚀实验、 盐雾实验和电化学实验研究了微量元素Sr对Al-Mg-Si-Cu合金车身板腐蚀性能的影响。 全浸腐蚀实验结果表明: 合金加入Sr后, 其质量损失速度由2.76mg/(h·cm2) 降为1.39mg/(h·cm2), 盐雾实验结果表明: 合金加入Sr后, 其质量损失速度由8.56×10-3mg/(h·cm2) 降为5.90×10-3mg/(h·cm2), Sr可以明显减缓合金的腐蚀速度。 电化学实验结果表明: 合金加入Sr后, 合金稳定电位较负, 稳定时间长, 合金钝化区较短, 腐蚀电位φcorr更负, 且腐蚀电流密度较小。
关键词: Al-Mg-Si-Cu基合金; 车身板; Sr; 腐蚀性能 中图分类号: TG146
文献标识码: A
Effect of microelement Sr on corrosion properties of Al-Mg-Si-Cu based alloy auto sheets
LU Guang-xi, GUAN Shao-kang, CHEN Hai-jun, LIN Dun-wen
(School of Materials Engineering, Zhengzhou University, Zhengzhou 450002, China)
Abstract: The effect of microelement Sr on the corrosion properties of Al-Mg-Si-Cu based alloy auto sheets was studied by means of immersion corrosion, salt spray corrosion and electrochemistry test. The results of immersion tests show that the rate of mass loss is depressed from 2.76 to 1.39mg/(h·cm2) when Sr is added into the alloy and the rate of mass loss is depressed from 8.56×10-3 to 5.90×10-3mg/(h·cm2) in salt spray tests. Sr can minish the corrosion rate of the alloy obviously. The results of electrochemistry tests show that when Sr is added into alloy, the steady voltage of alloy is more negative, the steady time is prolonged, the passivation area of alloy becomes shorter, φcorr is negative and the density of corrosion current becomes smaller.
Key words: Al-Mg-Si-Cu based alloy; auto sheet; strontium; corrosion property
汽车车身铝合金化对减轻车身质量具有重要的意义, 也是近几年来国内外研究的一个热点, 其中6000系Al-Mg-Si-Cu基合金车身板受到了关注[1-4]。 美国Alcoa铝业公司开发的6013合金具有很优异的焊接性能、 成形性能及耐腐蚀性能[5]。 在Al-Mg-Si-Cu铝合金中添加微量Sr, 可以对合金进行变质, 有助于合金性能的改善[6]。 从腐蚀的角度研究Sr在Al-Mg-Si-Cu铝合金的作用具有重要的意义, 目前国内外尚未见有关报道。 本文作者探讨了微量Sr对Al-Mg-Si-Cu基合金腐蚀性能的影响。
1 实验
在石墨坩埚中熔炼合金, 合金主成分基本相同。 采用金属模铸造, 将合金制成45mm×230mm×350mm的板坯。 合金成分列于表1。 板坯经540℃、 12h均匀化处理。 然后在二人不可逆轧机上进行热轧, 开轧温度540℃ , 终轧温度290℃。 每次下压量控制在40%左右, 轧制道次4次, 轧至厚度3.6mm。 然后进行冷轧, 轧制道次3次, 成品厚度1.0mm。
表1 Al-Mg-Si-Cu基合金成分
Table 1 Chemical compositions of Al-Mg-Si-Cu based alloys (mass fraction, %)
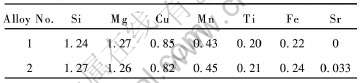
板材热处理工艺为: 540℃、 30min 固溶, 水淬, 150℃、 5min 预时效, 175℃、 30min 人工时效。 然后进行各种实验。
全浸腐蚀实验的试样尺寸为d30mm , 每组3个试样。 实验前先将试样磨至粒径70μm, 酒精清洗、 烘干, 然后称量, 准确到0.1mg 。 处理后的试样悬挂在5%HCl 的腐蚀溶液中30min 。 腐蚀后用70% HNO3 溶液去除试样表面的腐蚀产物, 然后酒精清洗、 烘干、 称取质量。 以上实验程序均按照GB10124-88 进行。
盐雾腐蚀实验的试样尺寸为d30mm , 每组3个试样。 实验前先将试样磨至粒径70μm, 酒精清洗、 烘干, 然后称量, 精确到0.1mg 。 将底面和侧面用胶带封好。 然后将试样放入FQY025型盐雾腐蚀实验箱, 试样放置角度15°~30°, 实验周期24h, 连续喷雾, 实验温度(35±2)℃, 3.5% NaCl 溶液, 溶液pH值控制在6.5~7.2。 腐蚀后用70% HNO3 溶液去除试样表面的腐蚀产物, 然后酒精清洗、 烘干, 称量。
电化学阳极极化实验的试样首先用水砂纸从70μm磨至7μm, 然后机械抛光。 试样的测定面以外进行覆膜保护。 阳极极化曲线在EG&G M351腐蚀测量仪上进行, 参比电极为饱和甘汞电极, 电解液为室温下的3.5 % NaCl 溶液, 电位扫描速度为5mV/min。
2 结果与分析
2.1 全浸腐蚀实验和盐雾腐蚀实验
腐蚀实验数据如表2所示。 从表2数据可以看出, 在同样的实验条件下, 全浸腐蚀实验中, 1号合金的腐蚀质量损失速度比2号合金的腐蚀质量损失速度几乎大一倍。 盐雾腐蚀实验中, 1号合金的腐蚀质量损失速度比2号合金的腐蚀质量损失速度大45.1%。 实验表明, 当合金中加入微量元素Sr, 可以明显减缓合金的腐蚀质量损失速度。
表2 实验合金的质量损失速度
Table 2 Rate of mass loss of alloys (mg·h-1·cm-2)
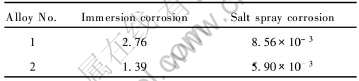
微量元素Sr是作为变质剂加入合金的。 汪沛雨等[7]的研究认为Al-Si-Cu合金加入Sr进行变质, 其共晶Si由粗大板块状变为针条状或松树枝状, 晶粒度明显变小。 Sr的加入可能使Al较易生核, 因而使共晶组织细化, 分配系数小, 浓度梯度大, 阻碍晶体成长, 使晶粒细化[7]。 本实验所使用的1号和2号合金轧制后的金相如图1所示。 从图中可以看出, 加入Sr后, 晶粒明显细化。 合金中第二相主要在晶间形成, 晶界较为干净, Sr抑制了部分第二相在晶界的形成。

图1 实验合金的金相照片
Fig.1 Metallographs of tested alloys
合金的耐蚀性与晶界处析出相的大小和分布密切相关。 含过剩Si的Al-Mg-Si合金在晶界处析出Si、 AlFeSi等阴极相以及Mg2Si阳极相, 构成了点蚀源[8]。 Al-Mg-Si合金中加入一定量的Cu, 还出现含Cu的强化相Q(Al1.9CuMg4.1Si3.3)相。 强化相Mg2Si的电位比α-Al更负, 是阳极相。 在时效过程中, Mg2Si在晶内和晶界形成, 而且在晶界析出, 但由于Mg2Si在α-Al的溶解度较小, 在晶间不能构成连续的阳极通道, Mg2Si没有晶间腐蚀倾向。
Si、 AlFeSi、 Q相的电位都比α-Al正, 是阴极相, 其数量的多少直接影响合金的耐蚀性能[9]。 当第二相数量少且不连续时, 使得合金构成腐蚀电偶的面积相对较小, 合金的耐腐蚀性能好。 图2所示是实验合金全浸腐蚀实验断面观察照片。 从图2可以看出, 加入Sr的实验合金, 合金晶粒小, 晶界析出相不连续, 腐蚀沿晶界的扩展受到阻挡, 合金的晶间腐蚀受到抑制。 不加Sr的实验合金, 晶粒粗大, 晶界比较宽, 在腐蚀介质的侵蚀下, 晶界析出相优先发生溶解, 促进了晶界的选择性溶解。 如果晶界析出相连续分布, 裂纹沿着晶界通道不受阻碍的一直扩展下去, 导致晶间腐蚀。
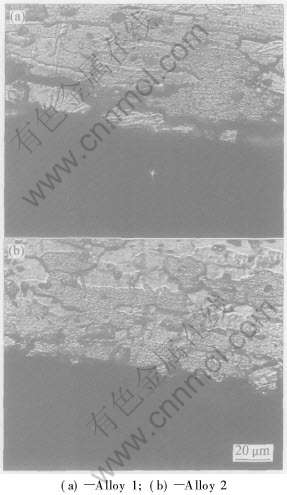
图2 实验合金全浸腐蚀实验断面照片
Fig.2 Cross-sectional images of alloys after immersion corrosion test
Mulazimoglu等[10]研究认为, 在6000系铝合金中, 存在β、 α两种AlFeSi相, 它们在均匀化过程中实际上是不溶解的。 合金中加入Sr, 可将β(Al5FeSi)相转变为α(Al8Fe2Si)相。 β-AlFeSi属单斜晶。 呈粗大针状或片状, 性脆, 对合金性能非常有害, 挤压和加工中易引起裂纹, 降低材料的强度和延展性, 并影响表面粗糙度。 α-AlFeSi为体心立方, 呈汉字结构, 脆性小, 塑性好[11, 12]。 另外, TEM分析表明, 在β型粒子情况下, Al和β粒子间界面极为明显, 显然在粒子周围存在着应力场, 认为β粒子的生长机理是由弯晶平面凹角边沿生长的, 它限制了晶体在生长期间产生的弯曲和扭转能力, 结果形成平板状晶形貌。 而α粒子不是小平面或弯晶生长, 它具有扩散的界面, 在晶粒周围没有应力场。 α-AlFeSi与Al基体有较大的扩散界面, 比β针状相的内部应力集中小, 产生了较强的界面连接[13]。 由于两种铁相相和基体的热膨胀系数不同, 第二相的体积效应导致应力场不同, 因而在相界面上引起电化学不均匀性有差异, 使得β-Al5FeSi相周围更易溶解腐蚀。 从图3 所示的实验合金的X射线衍射图谱可看出, 不加Sr的1号合金中主要存在β-Al5FeSi, 而加Sr的2号合金中主要存在α-Al8Fe2Si。 由于α-Al8Fe2Si与Al基体有较强的界面连接, 使得2号合金在HCl溶液合NaCl溶液中的耐蚀性增加。
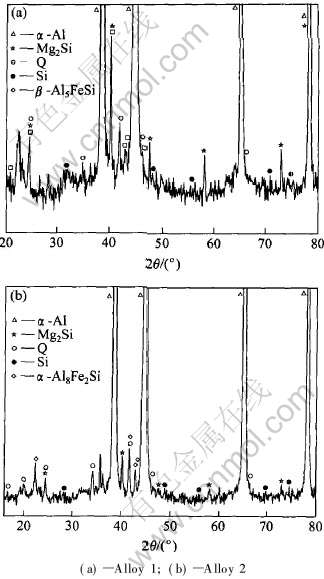
图3 实验合金相组织的X射线衍射谱
Fig.3 XRD patterns of phase structures of alloys
2.2 电化学实验
腐蚀电位是腐蚀电化学的最基本参数之一。 从热力学的角度看, 电位越正的金属越稳定, 耐蚀性越好。 电位越负的金属越不稳定, 有发生腐蚀的趋势。 铝是强钝化合金, 金属由活化态变成钝化态的过程中, 其电极电位向正的方向移动。 金属铝的标准电极电位是-1.66V, 钝化后, 其腐蚀电位为-0.5~-0.7V, 比平衡电位高1V左右[9]。 测量铝合金的腐蚀电位测定对研究它的腐蚀行为有重要意义。 通过测量铝合金在海水中的腐蚀电位, 可以确定它们对点蚀的相对敏感性。 黄等[14, 15]研究纯铝、 防锈铝、 锻铝、 硬铝和超硬铝在海水中的腐蚀电位发现, 耐海水腐蚀性能较好的防锈铝初始电位、 稳定电位均较负, 稳定时间长, 稳定电位波动较大; 耐海水腐蚀性能较差的硬铝和超硬铝初始电位、 稳定电位均较正, 稳定时间短, 稳定电位波动较小。 铝合金的耐蚀性好坏与腐蚀电位的正负顺序刚好相反。 这是由于加入的合金元素所起的作用不同造成的。 当φcorr向正电位方向变化, 腐蚀电流密度Jcorr增大, 表明阴极相面积增大, 使得合金腐蚀程度恶化[16]。
实验合金的平衡电位曲线和阳极极化曲线如图4和5所示。 图4中所示的自腐蚀电位表明, 加入Sr的2号合金稳定电位为-0.663V, 且稳定时间长, 稳定电位波动较大; 而无Sr的1号合金稳定电位为-0.658V, 与加Sr的2号合金比较, 其腐蚀电位较正, 稳定时间短, 稳定电位波动较大。 从图5中实验合金的阳极极化曲线可以看出, 加入Sr的合金钝化区较短, φcorr更负, 且Jcorr小。 加入Sr使得合金的电化学性能变化的原因可能是: 1) Sr抑制了第二相在晶界的形成, 并且使晶界的宽度减小, 2) Sr使合金中的β-Al5FeSi相转变为α-Al8Fe2Si相。 从而使得合金的腐蚀电位向负的方向移动。 加入Sr的实验合金耐腐蚀性能更好。
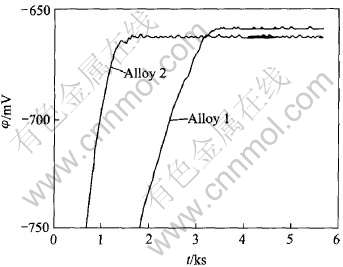
图4 实验合金的自腐蚀电位曲线
Fig.4 Self-corrosion curves of alloys
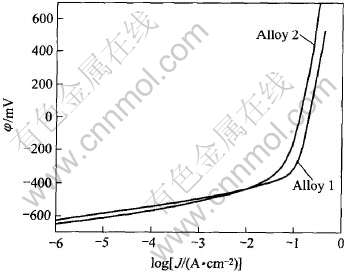
图5 实验合金的阳极极化曲线
Fig.5 Anodic polarization curves of alloys
3 结论
1) 在Al-Mg-Si-Cu合金车身板中加入微量元素Sr, 可使合金晶粒细化, 晶界宽度减小, 使晶界析出物不连续, 并且使粗大针状或片状的β-AlFeSi转变为与Al 基体有较大的扩散界面的呈汉字状的α-AlFeSi。
2) 合金加入Sr后, 全浸腐蚀其质量损失速度由2.76mg/(h·cm2) 降为1.39mg/(h·cm2)。 盐雾腐蚀其质量损失速度由8.56×10-3 mg/(h·cm2) 降为5.90×10-3mg/(h·cm2) 。 Sr可以明显减缓合金的腐蚀速度。
3) 合金加入Sr后, 合金稳定电位较负, 稳定时间长, 合金钝化区较短, φcorr负, 且Jcorr小。
REFERENCES
[1]关绍康, 姚波, 王迎新. 汽车铝合金车身板的研究现状和发展趋势[J]. 机械工程材料, 2001, 25(5): 12-14.
GUAN Shao-kang, YAO Bo, WANG Ying-xin. The progress and prospect of research on aluminum alloys for auto body sheets[J]. Materials For Mechanical Engineering, 2001, 25(5): 12-14.
[2]Huang Z W, Loretto M H, Smallman R E, et al. Mechanism of nucleation and recipitation in 6061-Li alloys[J]. Sci Technol, 1994, 10: 867-878.
[3]Hirsch J. The application of aluminum alloy in automotive[J]. Materials Science Forum, 1997, 242(10): 33-50.
[4]关绍康, 姚波, 王迎新. Ti和Ce对AlMgSi基合金板材成形性能的影响[J]. 中国有色金属学报, 2002, 12(4): 759-763.
GUAN Shao-kang, YAO Bo, WANG Ying-xin. Effect of Ti and Ce on forming properties of new type AlMgSi based alloy sheets[J]. The Chinese Journal of Nonferrous Metals, 2002, 12(4): 759-763.
[5]Readings K H. Aluminum structures used in aerospace status and prospect[J]. Materials Science Forum, 1997, 242: 11-24.
[6]高泽生. Sr在变形铝合金中的应用[J]. 轻合金加工技术, 1997, 25(8): 34-37.
GAO Ze-sheng. The application of Sr in wrought aluminum alloys[J]. Light Alloy Fabricate Technology, 1997, 25(8): 34-37.
[7]汪沛雨, 徐淑清, 张新颖. Al-Si-Cu合金加入Sr复合变质剂的变质效果[J]. 特种铸造及有色金属, 1995(2): 6-8.
WANG Pei-yu, XU Shu-qing, ZHANG Xin-ying. The modification effect of strontium-containing composite modifier on Al-Si-Cu alloy[J]. Special Casting And Nonferrous Alloys, 1995(2): 6-8.
[8]方百友, 卢燕平, 余庆, 等. 6063铝型材表面过腐蚀的研究[J]. 腐蚀科学与防护技术, 1998, 10(1): 28-32.
FANG Bai-you, LU Yan-ping, YU Qing, et al. Overcorrosion on the surface of 6063 aluminum extrusion[J]. Corrosion Science and Protection Technology, 1998, 10(1): 28-32.
[9]赵麦群, 雷阿丽. 金属的腐蚀与防护[M]. 北京: 国防工业出版社, 2002. 143-149.
ZHAO Mai-qun, LEI A-li. Corrosion and Protection of Metal[M]. Beijing: National Defence Industry Press, 2002. 143-149
[10]Mulazimoglu M H, Zaluska A, Gruzleski J E, et al. Electron microscope study of Al-Fe-Si intermetallics in 6201 aluminum alloy[J]. Metall Mat Trans, 1996, 27A(4): 926-936.
[11]Mulazimoglu M H, Zaluska A, Paray F, et al. The effect of strontium on the Mg2Si precipitation process in 6201 aluminum alloy[J]. Physical Metallurgy and Materials Science, 1977, 28(6): 1289-1295.
[12]Mulazimoglu M H, Paray F, Stephen G, et al. Modification of intermetallics phases by strontium in aluminum wrought alloys[J]. Publ Transp Int, 1994, 43(2): 1047-1056.
[13]Paray F, Gruzleski J E, Kulunk B, et al. Metallurgical effects of strontium on wrought 6061 alloys[A]. Light Metals: Proceedings of Sessions, TMS Annual Meeting[C]. Anaheim, CA, USA: TMS, 1996. 707-711.
[14]黄桂桥. 铝合金在海水中的耐腐蚀性与腐蚀电位的关系[J]. 腐蚀科学与防护技术, 1998, 10(3): 150-154.
HUANG Gui-qiao. Relationship between corrosion resistance and corrosion potential aluminum alloy in sea water[J]. Corrosion Science and Protection Technology, 1998, 10(3): 150-154.
[15]黄桂桥. 金属在海水中的腐蚀电位研究[J]. 腐蚀与防护, 2000, 2(1): 8-11.
HUANG Gui-qiao. Study of the corrosion potential of metal in sea water[J]. Corrosion & Protection, 2000, 21(1): 8-11.
[16]何立子, 张晓博, 孙秋霞, 等. Cu 及热处理制度对Al-Mg-Si系合金晶间腐蚀敏感性的影响[J]. 中国有色金属学报, 2001, 11(2): 231-234.
HE Li-zi, ZHANG Xiao-bo, SUN Qiu-xia, et al. Effects of Cu and age treatment on susceptibility to intergranular corrosion of Al-Mg-Si alloys[J]. The Chinese Journal of Nonferrous Metals, 2001, 11(2): 231-234.
基金项目: 河南省杰出人才创新基金资助项目(0321001100)
收稿日期: 2004-10-28; 修订日期: 2005-03-14
作者简介: 卢广玺(1966-), 男, 博士研究生.
通讯作者: 关绍康, 教授, 博士; 电话: 0371-63887508; E-mail: skguan@zzu.edu.cn
(编辑龙怀中)