J. Cent. South Univ. (2012) 19: 887-891
DOI: 10.1007/s11771-012-1088-0
Fabrication and plasma arc thermal shock resistance of
HfB2-based ultra high temperature ceramics
WENG Ling(翁凌)1, HAN Wen-bo(韩文波)2, HONG Chang-qing(洪长青)2
1. School of Material Science and Engineering, Harbin University of Science and Technology,Harbin 150040, China;
2. Center for Composite Materials and Structures, Harbin Institute of Technology, Harbin 150001, China
? Central South University Press and Springer-Verlag Berlin Heidelberg 2012
Abstract: Two hafnium diboride based ceramic matrix composites containing 20% (volume fraction) SiC particle and with or without AlN as sintering additives were fabricated by hot-pressed sintering. The mechanical properties and microstructures of these two composites were tested and the thermal shock resistances were evaluated by plasma arc heater. The results indicate that the composite with AlN as sintering additive has a denser and finer microstructure than composite without sintering additive, and the mechanical properties, thermal shock resistance of the composite with AlN as sintering additive are also higher than those of the composite without AlN. Microstructure analysis on the cross-section of two composites after thermal shock tests indicates that a compact oxidation scale contains HfO2 and Al2O3 liquid phase is found on the surface of composite with AlN, which could fill the voids and cracks of surface and improve the thermal shock resistance of composite.
Key words: hafnium diboride; thermal shock resistance; plasma arc test; microstructure
1 Introduction
Due to their excellent properties such as high melting point, high electrical conductivity, high oxidation resistance and good chemical stability, transition metal diboride (ZrB2, HfB2) based ceramics have good potential for various aviation applications, such as hypersonic flight, atmospheric reentry or rocket propulsion. Such severe usage environment requires a good oxidation resistance and thermal shock resistance (TSR) of ultra high temperature ceramics (UHTC) [1-3]. In recent years, the oxidation resistance of refractory ceramic matrix composites has been studied by many researchers [4-7]. However, the investigation based on the thermal shock resistance (TSR) of UHTCs was reported deficiently and the TSR mechanism of composites, especially when doped sintering aids, was still unclear [8-11]. On-ground arc-jet testing has recently shown as a more effective way on investigating the thermal shock behavior of UHTCs than conventional water quenching method [12], because it can provide a very good ground-based simulation of the hypersonic flight conditions, including rapid temperature rising, high temperature (>2 000 °C), high heat flow and relatively high gas pressure. The testing results can help researchers to well understand the thermal shock performance of UHTCs under controlled aerothermal heating conditions.
In the present work, two HfB2-based ultra high temperature ceramics were prepared by hot-pressing. The thermal shock resistance was evaluated by alternating plasma arc heating heater. The purpose of this work was to study the thermal shock mechanism of different HfB2-based UHTCs in order to measure the application possibilities of composites in aerothermal environment.
2 Experimental
2.1 Preparation of composites
Commercial available HfB2 powder (purity >96%, mass fraction, Northwest Institute For Non-ferrous Metal Research, China), SiC powder (purity >99.5%, Xuzhou Hongwu Nanometer Materials Co., Ltd., China) and AlN powder (purity >98%, Hefei Kiln Nanometer Technology Development Co., Ltd, China), were used. The compositions of materials were: 1) HfB2-20% (volume fraction) SiC (H20S); 2) HfB2-20%SiC-15%AlN (H20S15A). The starting powder mixtures were milled for 24 h, and hot pressed in Ar gas atmosphere. The sintering temperature was 2 000 °C and 1 800 °C for composites H20S and H20S15A, respectively. The applied pressure was 30 MPa and the soaking time was 30 min for both the materials.
2.2 Composites characterization
Specimens were firstly polished and ultrasonic- cleaned by acetone and pure ethanol. The final densities of composites were measured by Archimedes water-immersion method, and the theoretical density was estimated by the rule of mixture.
Flexural strength was measured with three-point bending tests at a crosshead speed of 0.5 mm/min. The sample size is 36 mm ? 3 mm ? 4 mm with the span of 30 mm. Fracture toughness was evaluated using single-edge notched bend (SENB) beams (2 mm ? 4 mm ? 20 mm, notch depth and radius of 2 mm and 0.2 mm, respectively) with a span of 16 mm and a crosshead speed of 0.05 mm/min. The hardness of composites was measured by a Vickers indenter with 50 N as applied load for 10 s on polished sections.
The thermal shock tests were conducted in a self-building alternating plasma arc heater. The experimental conditions for thermal shock are listed in Table 1. The dimensions of specimens are 15 mm in diameter and 20 mm in height. The microstructure of materials was studied by scanning electron microscope (SEM, Hitachi S-4700) equipped with an energy dispersive X-ray spectroscope. Crystal-phase identification of samples was determined by X-ray diffractometry (Rigaku, Dmax-rb, Cu Kα=1.541 8 ?).
Table 1 Experimental conditions for plasma arc heater
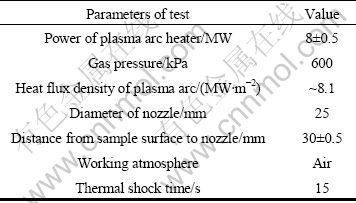
3 Results and discussion
3.1 Microstructures of two composites
Figure 1 shows the SEM-EDS microstructure of H20S and H20S15A composites. The lighter phase in images identified by energy-dispersive X-ray (EDX) analysis is HfB2 and the dark phase is SiC. General configurations of two composites present regularly faceted dibordie grains and intergranular SiC particulates uniformly dispersing in HfB2 bulk. From Fig. 1, it can also be seen that there are some residual porosity scarcely dispersed on grain boundaries of HfB2 (Fig. 1(a)), in accordance with the lowest relative density, 82.6%. Meanwhile, composite H20S15A with AlN as sintering aids shows finer grains and more compact characteristic than composite HS, which should be attributed to the decrease in sintering temperature after AlN addition.
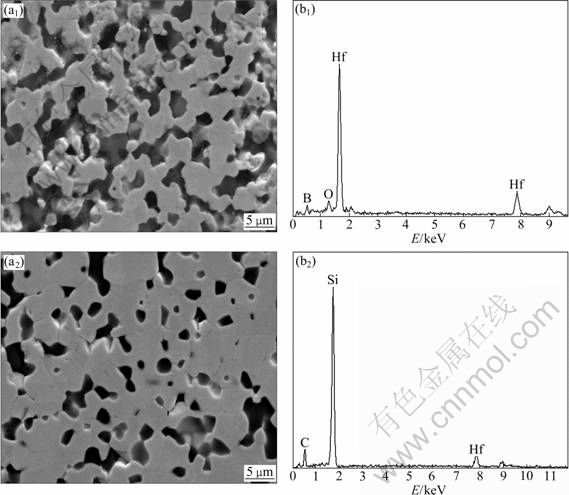
Fig. 1 SEM images and EDS spectra of two composites: (a) H20S; (b) H20S15A
3.2 Mechanical properties of two composites
The three point flexural, micro-hardness (HV1.0) and fracture toughness (KIC) tests of two composites at room temperature were carried out respectively and the results are listed in Table 2. It can be clearly seen that the flexural strength and fracture toughness of composite H20S15A are 732 MPa and 5.3 MPa·m1/2, respectively, which are much higher than those of composite H20S (497 MPa and 4.5 MPa·m1/2). This increase in mechanical properties can be attributed to the more densified and finer grain size of composite H20S15A than H20S. Moreover, the hardnesses of composite H20S and H20S15A are also examined and listed in Table 2. The value is (22.5±2) GPa for H20S and (19.3±1) GPa for H20S15A.
Table 2 Mechanical properties of composites
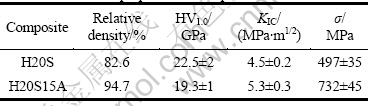
3.3 Plasma arc thermal shock test of two composites
Figure 2 shows the post-thermal shock test morphologies of H20S and H20S15A after 15 s of plasma arc test. For H20S composite (Fig. 2(a)), the uneven and disintegrating surface morphology after plasma arc test shows that there must have a great thermal shock damage acting on the specimen. X-ray diffraction (XRD) result (Fig. 3) indicates that few oxidized phase was found. This is possibly due to the splashing of sample surface during the test. For H20S15A composite, there is a white oxide layer covering the ablation surface (Fig. 2(b)), and no crack is observed on the surface of specimen. XRD analysis reveals that the ablated surface mainly consists of HfO2 as a major phase with minor amount of HfSiO4, demonstrating that HfB2 on the ablated surface is oxidized. Moreover, no peak corresponding to silica or its glassy phase is found on XRD pattern, which is different from other research [13]. The possible reason for the disappearance of silica is the splashing of liquid SiO2 during the tests.
Figure 4 compares the SEM microstructures on cross sections of the two composites after plasma arc tests. It can be clearly seen that the microstructures of these two composites are very different. In the H20S composite, a mass of microcracks are clearly seen under the outmost oxidized layer. The formation of thermal shock microcracks is closely correlated with the giant temperature differences. The procedure of temperature on sample surface during tests recorded by pyrophotometer shows that it increases drastically in a very short time when exposed to the plasma torch arc heater. It only takes about 3-5 s to heat up to 2 800 K. A large thermal stress occurs because of the great temperature difference between the surface area and the bulk of materials. Fracture is inevitable if the thermal stress reaches or exceeds the fracture strength of composite. Then, material would break.
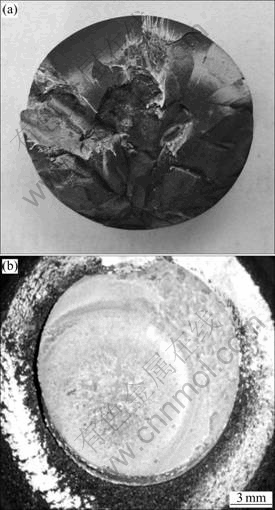
Fig. 2 Post-thermal shock test morphologies of composite H20S (a) and composite H20S15A (b) after 15 s of plasma arc test
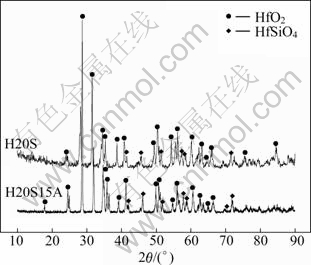
Fig. 3 XRD patterns taken from composite H20S (a) and composite H20S15A (b) after plasma arc test
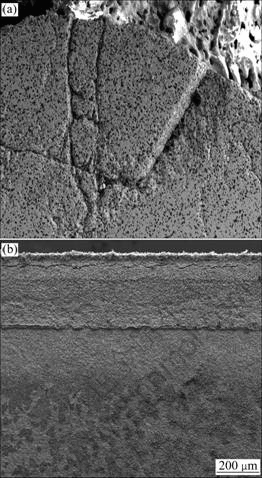
Fig. 4 Cross-section SEM images of composite H20S (a) and composite H20S15A (b) after plasma arc test
For composite H20S15A, a dense, compact and adherent oxidation scale is presented in it. No crack is found, which indicates a better thermal shock resistance than composite H20S. Figures 5(a) and (b) show the typical cross section appearance of HfB2-20%SiC- 15%AlN. A clear evidence of liquid phase formation is found. Energy dispersive X-ray spectroscope (EDS) analysis provides that this liquid phase is the combination of HfO2 and Al2O3 (Fig. 5(c)). The formations of HfO2 and Al2O3 are the oxidation products of HfB2 and AlN. However, HfB2 oxidation itself produces a brittle, non-protective scale, and oxygen diffusion through HfO2 is fast because of the high density of oxygen lattice vacancies similar to that of ZrO2 [14]. Oxidation data for Al2O3 suggest that the melting point of Al2O3 is 2 050 °C, which is lower than the highest surface temperature during plasma arc test, so it is preferable to be liquid phase [15]. Due to its low viscosity, this Al2O3 liquid phase can slightly flow in HfO2 oxidation scale (Fig. 5(b)) and fill in the voids and cracks, which endows the oxidation layer with a moderate strength and prevents it from being broken off.
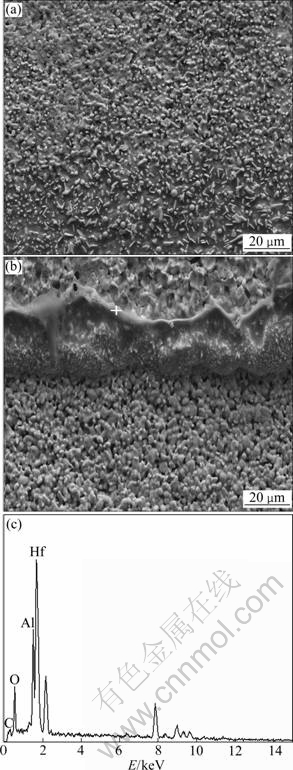
Fig. 5 SEM images and EDS spectrum of cross section of composite H20S15A: (a) Low magnitude SEM image; (b) High magnitude SEM image; (c) EDS spectrum of HfO2-Al2O3 glassy phase
4 Conclusions
1) HfB2-SiC-AlN composite has a better thermal shock resistance than HfB2-SiC composite. Microstructure analysis of cross section of samples shows a different surface morphology.
2) The improvement of thermal shock resistance of HfB2-SiC-AlN composite is mainly due to the formation of HfO2-Al2O3 glassy phase, which fills in the voids and cracks of oxidized layer. This endows it a moderate strength and prevents it from being broken.
References
[1] OPEKA M, TALMYI G, ZAYKOSHIJ A. oxidation-based materials selection for 2 000 °C + hypersonic aerosurfaces: Theoretical considerations and historical [J]. Journal of Materials Science, 2004, 39(19): 5887-5904.
[2] WUCHINA E, OPEKA M, CAUSY S. Designing for ultrahigh-temperature applications: The mechanical and thermal properties of HfB2, HfCx, HfNx and α-Hf(N) [J]. Journal of Materials Science, 2004, 39(19): 5939-5949.
[3] UPADHYA K Y, HOFFMAN J M. Materials for ultra-high temperatures structural applications [J]. The Bulletin of the American Ceramic Society, 1997, 58(4): 51-56.
[4] YANG Xin, ZOU Yan-hong, HUANG Qi-zhong, SU Zhe-an, CHANG Xin, ZHANG Ming-yu, XIAO Yong. Improved oxidation resistance of chemical vapor reaction SiC coating modified with silica for carbon/carbon composites [J]. Journal of Central South University of Technology, 2010, 17(1): 1-6.
[5] CHOI H J, KIM Y W, MITOMO M. Intergranular glassy phase free SiC ceramics retain strength at 1 500 °C [J]. Scripta Materialia, 2004, 50: 1203-1207.
[6] GU Yi, XIA Chang-qing, LI Jia, WU An-ru. Effect of nano-size nickel particles on wear resistance and high temperature oxidation resistance of ultrafine ceramic coating [J]. Journal of Central South University of Technology, 2004, 11(4): 358-361.
[7] MONTEVERDE F, BELLOSI A. Microstructure and properties of an HfB2-SiC composite for ultra high temperature applications [J]. Advanced Engineering Materials, 2004, 6(3): 331-336.
[8] MONTEVERDE F, SCATTEIA L. Resistance to thermal shock and to oxidation of metal diborides-SiC ceramics for aerospace application [J]. Journal of American Ceramic Society, 2007, 90(4): 1130-1138.
[9] CHAMBERLAIN A, FAHRENHOLTZ W G, HILMAS G, ELLERBY D. Oxidation of ZrB2-SiC ceramics under atmospheric and re-entry conditions [J]. Refractory Application Transaction, 2005, 2(1): 1-8.
[10] MONTEVERDE F, SAVINO R. Stability of ultra-high-temperature ZrB2-SiC ceramics under simulated atmospheric re-entry conditions [J]. Journal of European Ceramic Society, 2007, 27(3): 4797-4805.
[11] KOLODZIEJ P. Aerothermal performance constraints for hypervelocity small radius unswept leading edges and nose tips [R]. Huston: NASA Technical Memorandum, 1995.
[12] GASCH M, ELLERBY D, IRBY E, BECHMAN S, GUSMAN M, JOHNSON S. Processing, properties and arc jet oxidation of hafnium diboride/silicon carbide ultra high temperature ceramics [J]. Journal of Materials Science, 2004, 39(19): 5925-5937.
[13] MONTEVERDE F, BELLOSI A. The resistance to oxidation of an HfB2-SiC composite [J]. Journal of European Ceramic Society, 2005, 25(7): 1025-1031.
[14] TABARU T, SHOBU K, SAKAMOTO M, HIRAI H, HANADA S. Oxidation behavior of Mo(Si0.6,Al0.4)2/HfB2 composites as aluminum reservoir materials for protective Al2O3 formation [J]. Scripta Materialia, 2003, 49(8): 767-772.
[15] PINT B A, MARTIN J R, HOBBS L W. The oxidation mechanism of θ-Al2O3 scales [J]. Solid State Ion, 1995, 78(1/2): 99-107.
(Edited by HE Yun-bin)
Foundation item: Project(90505015) supported by the National Natural Science Foundation of China; Project(20060213031) supported by the Research Fund for the Doctoral Program of Higher Education of China
Received date: 2010-12-12; Accepted date: 2011-03-08
Corresponding author: WENG Ling, PhD; Tel: +86-451-86392501; E-mail: wengling79@163.com