Trans. Nonferrous Met. Soc. China 24(2014) 2208-2213
Effect of Si content on laser welding performance of Al-Mn-Mg alloy
Pi-zhi ZHAO1,2, Jing LIU1, Zhi-dong CHI1
1. Suzhou Research Institute for Nonferrous Metals, Suzhou 215026, China;
2. CHINALCO Research Institute of Science and Technology, Beijing 100082, China
Received 17 October 2013; accepted 12 May 2014
Abstract: The correlation between Si content (0.1%-0.5%, mass fraction) and pulse laser welding performance of Al-Mn-Mg aluminum alloy sheets was studied. The sheets were fabricated in the laboratory, with gauge of 0.45 mm, H16 temper by pulse laser welding. It was found that no cracking existed in the welding pool as Si content was below 0.34%. However, when the Si content increased to 0.47%, cracking formed in the welding pool. Microstructure observations indicated that residual eutectic phases distributed at the grain boundaries were discontinuous and appeared to be small particles in lower Si content alloys; the residual eutectic phases distributed at the grain boundaries were partially continuous and appeared to be films in higher Si content alloys. These phenomena could explain why Si content adversely affected the laser welding performance.
Key words: Al-Mn-Mg alloy; laser welding performance; Si content; crack; residual eutectic phase
1 Introduction
Al-Mn-Mg aluminum alloy sheets are commonly used as cases and covers of lithium ion batteries for 3C devices (computer, communication, consumer electronic) due to light weight, high formability and good heat conductivity. Laser welding is often adopted to join the cases and covers of batteries for narrow heat-affected zone (HAZ) and fast welding speed [1,2]. Therefore, it is very important for the Al-Mn-Mg aluminum alloy sheets to have good laser welding performance to guarantee the safety of lithium ion batteries.
The cases of batteries are generally formed by deep drawing and ironing method. Abundant AlFeMnSi intermetallic compounds in the alloy sheets are helpful for cleaning the die during the forming process [3,4]. And an effective way to get more AlFeMnSi phases is to increase Si content [5,6]. However, Si content might have an effect on the laser welding performance of Al-Mn-Mg alloy sheets.
Several works had been carried out to investigate reasons for laser welding cracking. It was found that hot cracking occurred mainly due to the segregation of alloying elements at grain boundaries and the existence of the low-melting point phases [7,8]. HUANG et al [9-11] studied the liquation cracking in the partially melted zone. The results suggested that the liquation initiated at grain boundaries due to a lower melting point. Cracking behaviors during laser welding process are influenced by not only welding parameters, such as peak power, pulse energy and welding speed, but also alloying compositions [12,13]. CHANG et al [14] discussed the effects of the welding parameters on the welding properties of Al-Mn aluminum alloy. The results showed that the welding defect rate of the pulse wave type laser welding was higher than that of the continuous wave type laser welding. And the cracking in the welding bead reduced with decreasing welding speed.
However, as far as we all know, few researches have been done to explain the relationship between chemical compositions of aluminum alloy and laser welding performance. Thus, the objective of this study is to investigate the influence of Si content on laser welding cracking sensitivity in Al-Mn-Mg aluminum alloy sheets. This research will help us to control the Si content in order to get Al-Mn-Mg aluminum alloys with good laser welding performance. The correlation between morphology of the eutectic phase remaining at the grain boundaries of welding pool and laser welding cracking behaviors will be discussed.
2 Experimental
2.1 Samples preparation
The chemical composition of the Al-Mn-Mg alloy used in this study is listed in Table1. Ingots with size of 70 mm were made by direct chill casting (DC casting). The ingots were homogenized at 610 °C for 7 h. After homogenization, the ingots were scalped to 50 mm gauge, and hot rolled to 5 mm gauge, furthermore cold-rolled to 0.9 mm gauge sheets. The cold-rolled sheets were intermediately annealed and then followed by cold-rolling to final 0.45 mm gauge sheets (H16 temper).
Table 1 Chemical composition of alloys used in the present study (mass fraction, %)
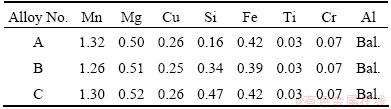
2.2 Laser welding
After the sheets were cleaned with alcohol, laser welding was carried out by welding on the plate with PB600 pulse laser welding machine. The laser beam was emitted onto a lens with a focus distance of 80 mm and formed a 430 μm-diameter optical circle on the sheet. Argon gas was used to shield the surface of the testing sheet with a flowing rate of 15 L/min. Table 2 lists the laser welding parameters.
Table 2 Laser welding parameters
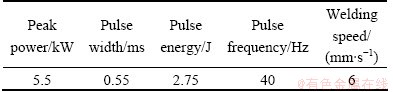
2.3 Evaluation of microstructures
The grain structures of longitudinal sections of the sheets used for welding test were observed on a polarizing microscope after buff grinding and anodizing. The intermetallic compounds were observed by optical microscopy (OM) after buff grinding and etching with 0.5% HF solution, and were measured with an image analyzer.
The surface of welding pool was observed by OM to examine whether cracking existed. Grain structures of the sections of welding pool were observed by the polarizing microscope after buff grinding and anodizing to investigate the fracture path. And the low-melting point eutectic phases in the welding pools were observed by the polarizing microscope after buff grinding and etched with 0.5% HF solution. The morphology of fracture was observed by a scanning electron microscope (SEM), and the composition of the low-melting point eutectic phases was analyzed with an energy-dispersive X-ray spectroscope (EDS).
3 Results and discussion
3.1 Microstructures of testing sheets
Figure 1 shows the grain structures of alloys A (0.16% Si), B (0.34% Si) and C (0.47% Si ) alloy sheets before welding test. It can be seen that the grains in the three alloy sheets are elongating along the rolling direction. This indicates that the variation of Si content has little effect on the grain size.
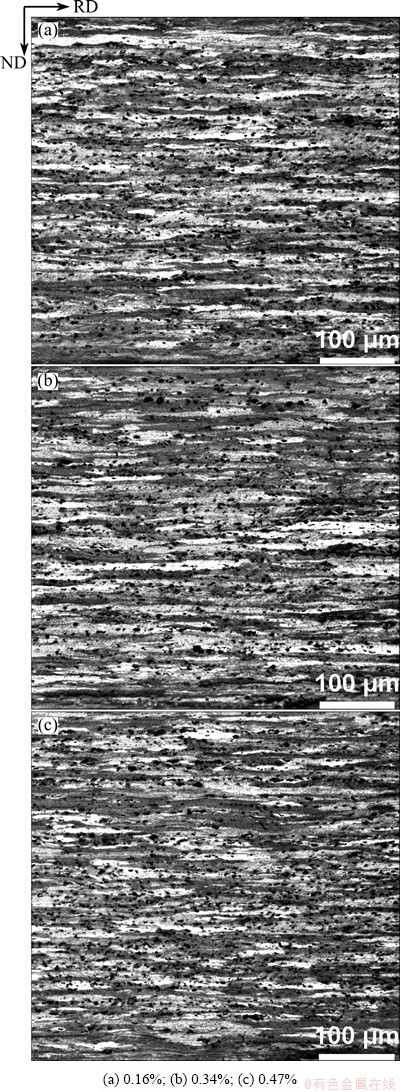
Fig. 1 Grain structure of alloys with different Si contents

Fig. 2 Distribution of intermetallic compounds in alloys with different Si contents
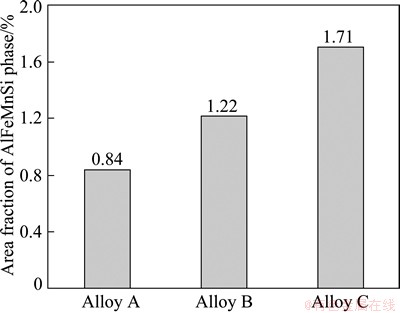
Fig. 3 Area fractions of AlFeMnSi phase in alloys with different Si contents
Figure 2 shows the distribution of intermetallic compounds in A, B and C alloy sheets. AlFeMn and AlFeMnSi phases exhibit different colors and morphologies in the SEM images. The former is grey and sharp, while the latter is black and round. Figure 3 shows the area fractions of AlFeMnSi phase in alloys with different Si contents. It is clarified that the amount of AlFeMnSi phases increases with the increase of Si content. During the homogenization of ingot, an eutectoid reaction as follows will happen [4]:
3(Fe,Mn)Al6+Si→α-Al12(Fe,Mn)3Si+6Al
This transformation would occur step by step, and eventually get into a equilibrium state. More Si content could promote this transformation. AlFeMnSi phase with higher hardness could help cleaning the die during deep stamping [3,4].
3.2 Microstructure of welding pools
Welding pools of the alloys with different Si contents are shown in Fig. 4. It is found that no cracking existing in the alloy A with 0.16% Si (Fig. 4(a)) and alloy B with 0.34% Si (Fig. 4(b)). However, cracking is observed in the alloy C with 0.47% Si (Fig. 4(c)). This indicates that laser welding cracking becomes more susceptible with the increase of Si content in the Al-Mn-Mg alloy sheets.
In order to investigate the reason of cracking occurring in alloy C, the vertical and transverse sections of the alloy were observed. Figure 5 shows the grain structures of the welding pool which has a welding cracking in alloy C. The cracking exists between grains. Figure 6 shows morphology of fracture surface which displays a granular fractography. This means that the cracking is intergranular brittle fracture that is generally induced by fragility phases or slag inclusion at the grain boundaries.
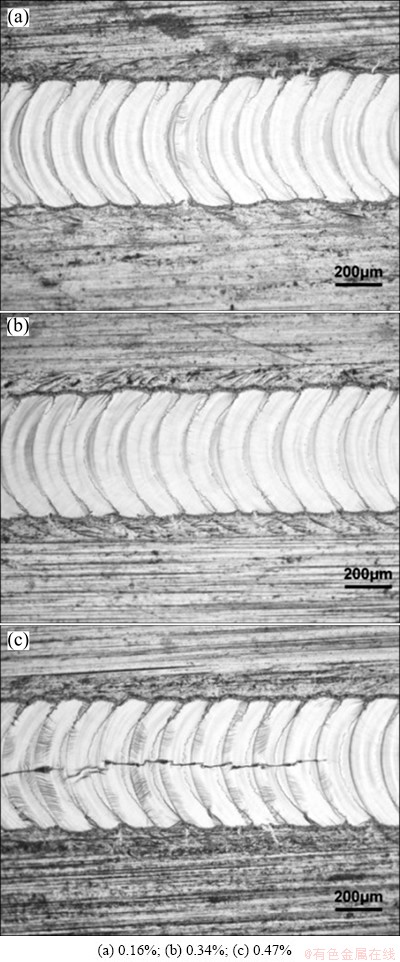
Fig. 4 Welding pools of alloys with different Si contents
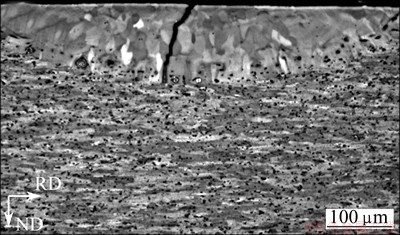
Fig. 5 Grain structure of welding pool in alloy C
3.3 Correlation between laser welding cracking behavior and morphology of residual eutectic phases in welding pool
In order to investigate the initiation of welding cracking, the welding pools were observed in details. Figure 7 shows the welding pool of alloy A . Micro- cracks can be observed in the HAZ between base metal and welding pool, but they do not propagate to the surface of the testing sheet. Thus, the cracking which affects the welding performance will not happen. Figure 8 shows the welding pool of alloy C with cracking. The cracking initiates at the grain boundary in the HAZ, and propagates along grain boundary to the surface of the testing sheet. The similar phenomenon in Al-Cu and Al-Zn-Mg alloys has been observed by HUANG et al [9,10]. During the welding process, grain boundary in HAZ is supposed to be heated to the melting point, and then liquation cracking will form at the grain boundary during the following solidification and shrinking.
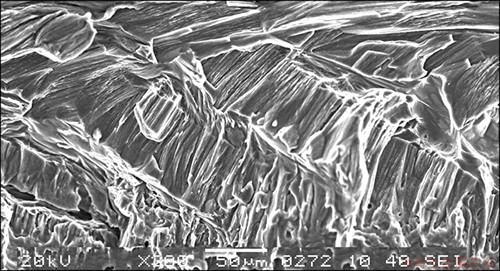
Fig. 6 SEM image showing fracture surface of welding pool in alloy C
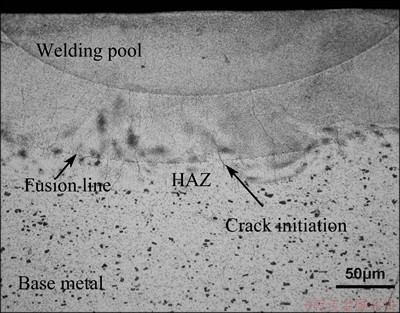
Fig. 7 Welding pool in alloy A showing crack initiation at grain boundary in HAZ
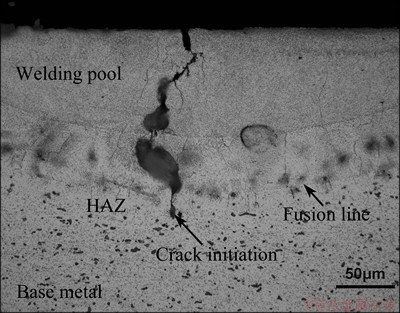
Fig. 8 Welding pool in alloy C showing cracking initiation and propagation at grain boundary
Figure 9 shows microstructures at the grain boundary of welding pool in alloys A and C. The dark particles in Fig. 9(a) and dark lines in Fig. 9(b) are considered as residual eutectic phases, respectively. In the lower Si content alloy A, residual eutectic phases are distributed at the grain boundary discontinuously and appeared to be small particles. In the higher Si content alloy C, residual eutectic phases are distributed at the grain boundary continuously and appear to be films.
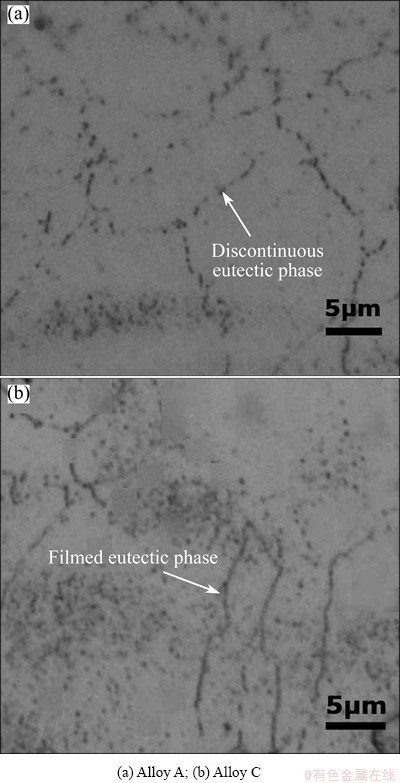
Fig. 9 Residual eutectic phases at grain boundary of welding pools
According to the liquid film-strain theory of welding fracture [15], hot cracking will form at the grain boundary if there are proper amount of low-melting point eutectic liquid phases as films at the grain boundary during solidification after laser welding, which leads to less ductility of the grain boundaries. On the other hand, the hot cracking will not form if the eutectic liquid phases are discontinuous at the grain boundary. Therefore, cracking in alloy C could be attributed to the fact that a large amount of residual eutectic phases formed at the grain boundary as films, which weakened the grain boundary.
The residual eutectic phases were examined by SEM-EDS analysis on the fracture surface of cracking pool in alloy C, as shown in Fig. 10 and Table 3. The residual eutectic phases in Fig. 9 are identified to be Si, Mg, Mn and Fe bearing phases. For the alloys A, B and C, the contents of Mg, Mn, Fe varied little, and the only element whose amount changed largely in the three alloys is Si. Consequently, it can be concluded that the amount of residual eutectic phases is mainly influenced by the Si content.
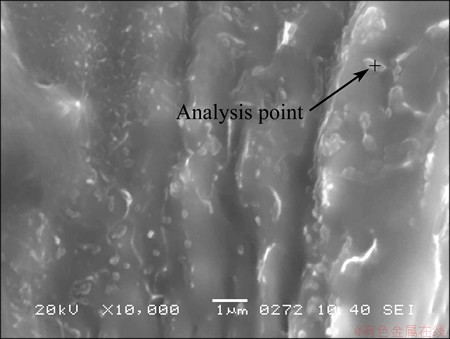
Fig. 10 SEM image of eutectic phase in alloy C at grain boundary
Table 3 EDS analysis results of eutectic phase in alloy C
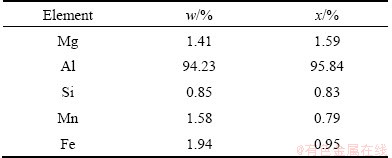
In summary, the correlation between laser welding crack susceptibility and the Si content can be explained by the different morphologies of the residual eutectic phases at the grain boundary. In the low Si content alloy A, the residual eutectic phases exist as particles at the grain boundary, so micro-cracks initiated in HAZ are difficult to propagate along the grain boundary. Otherwise, in the higher Si content alloy C, there are a large number of residual eutectic phases formed as films at the grain boundary, so cracking initiated in HAZ will be easy to propagate.
4 Conclusions
1) The amount of Al-Fe-Mn-Si phases in Al-Mn-Mg alloys increases with the increase of Si content.
2) Laser welding cracking susceptibility changes with Si content. No cracking exists in the welding pools as Si content is below 0.34%. However, cracking occurs as the Si content increases to 0.47%.
3) The effects of Si content on the cracking susceptibility could be understood by the different morphologies of eutectic phases at the grain boundary. Higher Si content alloy has a lot of liquid eutectic phases existing in films at the grain boundary, which facilitates the propagation of cracking.
References
[1] ZENG Da-fu, GAO Wei-qi, BAI Jing-cheng. A discussion on the laser welding technique for Al package encapsulation [J]. Microelectronics, 1997, 27(3): 202-205.
[2] PENG Yun. Prevention of aluminum solidification crack during welding [J]. Welding, 1995, 1: 2-4.
[3] LI Z, MORRIS J G, DING S X. Aluminum alloys—Their physical and mechanical properties [C]//Proceedings ICAA3. Trondheim, Norway: Wiley-VCH, 1992: 373.
[4] ZHANG Yong-hao, ZHANG Zhi-qing, WEN Qing-hong, LIU Qing. Effects of distribution and shape of eutectic compounds on drawability of AA3104 aluminum alloys [J]. Transactions of Materials and Heat Treatment, 2012, 33(12): 53-57.
[5] VASUDEV A K, DOHERTY R D. Aluminum alloys contemporary research and applications [M]. New York: Academic Press Inc, 1998: 76.
[6] SUN Dong-li, JIANG Shi-feng, GAO Xing-xi. Effects of homogenization on the microstructure of 3004 aluminum alloy [J]. Tansactions of Nonferrous Metals Society of China, 1999, 9(3): 556-561.
[7] SENKARA J, ZHANG H. Cracking in spot welding aluminum alloy AA5754 [J]. Material Science Forum, 2000, 7: 194-201.
[8] BALASUBRAMANIAN K. Studies on the effect of vibration on hot cracking and grain size in AA7075 aluminum alloy welding [J]. International Journal of Engineering Science and Technology, 2011, 1: 681-686.
[9] HUANG C, CAO G, KOU S. Liquation cracking in aluminum welds [J]. Material Science Forum, 2007, 539-543: 4036-4041.
[10] HUANG C, KOU S. Partially melted zone in aluminum welds—Liquation mechanism and directional liquation mechanism and directional solidification [J]. Welding Research, 2000, 6(5): 113-120.
[11] HUANG C, KOU S. Liquation cracking in full-penetration Al-Cu welds [J]. Welding Research, 2004, 12(2): 50-58.
[12] ABBASCHIAN L, LIMA M S F D. Cracking susceptibility of aluminum alloys during laser welding [J]. Materials Research, 2003, 6(2): 273-278.
[13] YANG Zhi-kun, LI Ming, YANG Wei-guo. Analysis of 2A12 aluminum alloy part welding crack [J]. Hot Processing Technology and Equipment, 2006(4): 80-92. (in Chinese)
[14] CHANG C C, CHOU C P, HSU S N, HSIUNG G Y, CHEN J R. Effect of laser welding on properties of dissimilar joint of Al-Mg-Si and Al-Mn aluminum alloys [J]. Material Science and Technology, 2010, 26(3): 276-282.
[15] KATAYAMA S, LUNDIN C D. Laser welding of AA2090 [J]. Welding of Light Metal, 1991, 29(9): 403-415.
Si含量对Al-Mn-Mg合金激光焊接性能的影响
赵丕植1,2, 刘 婧1, 迟之东1
1. 苏州有色金属研究院,苏州 215026;
2. 中铝科学技术研究院,北京 100082
摘 要:研究Al-Mn-Mg铝合金板材的Si含量(0.1%~0.5%,质量分数)对其脉冲激光焊接性能的影响。试验材料为实验室制备的0.45 mm厚的H16态板材。激光焊接试验后发现,当Si含量低于0.34%时,焊池里没有产生裂纹;但是,当Si含量增加到0.47%时,焊池里有裂纹产生。微观组织观察表明,当Si含量低的时候,晶界上残留的共晶相呈不连续的点状分布;当Si含量高的时候,晶界上残留的共晶相变成连续分布。这种现象可以解释增加Si含量对激光焊接性能产生的不利影响。
关键词:Al-Mn-Mg 合金;激光焊接性能;Si 含量;裂纹;残留共晶相
(Edited by Xiang-qun LI)
Foundation item: Project (2011KJZD04) supported by the CHINALCO Science and Development Foundation, China
Corresponding author: Pi-zhi ZHAO; Tel: +86-512-88856150; E-mail: zhao_pz@sinr.cn
DOI: 10.1016/S1003-6326(14)63334-3