
Microstructural evolution and its effects on mechanical properties of spray deposited SiCp/8009Al composites during secondary processing
CHEN Zhi-gang(陈志钢), CHEN Zhen-hua(陈振华), CHEN Ding(陈 鼎),
HE Yi-qiang(贺毅强), CHEN Gang(陈 刚)
College of Materials Science and Engineering, Hunan University, Changsha 410082, China
Received 2 June 2008; accepted 11 March 2009
Abstract: 15% (volume fraction) SiCp/8009Al metal matrix composites(MMCs) prepared by spray co-deposition were hot-extruded and rolled to investigate the effects of porosity and local SiCp clusters on mechanical properties. The microstructures were examined by using optical microscopy(OM), scanning electron microscopy(SEM), X-ray diffractometry(XRD) and transmission electron microscopy(TEM). The mechanical properties were measured by tensile testing. The experimental results show that lamellar structure is composed of pores and SiCp clusters and can be improved by secondary processing, enhancing mechanical properties. The main strengthening mechanism and fracture behavior of MMCs were discussed too.
Key words: spray co-deposition; SiCp/8009Al composites; lamellar structure; porosity; secondary processing
1 Introduction
With their low density, high strength, high specific modulus, stiffness, wear and creep resistance, discontinuously reinforced aluminum alloy based metal-matrix composites are increasingly attractive for extensive applications in aerospace, transportation and other fields[1-2]. Dispersion-strengthened Al-Fe-V-Si alloys (8009Al) prepared by rapid solidification technique have been the subject of extensive research during the last two decades due to their excellent mechanical properties at both room temperature and elevated temperature[3-5]. Among various preparation technologies, spray atomization and co-deposition approach[6-8] has gained considerable attention as viable process to produce near-net shaped particle reinforced metal matrix composites. Some benefits, such as high cooling rates (>103 K/s) and uniformly distributed particle reinforcement (e.g. SiCp) without any wetting problems with aluminum matrix are gained. However, spray deposition has its inherent disadvantages. Improper control of some process parameters can result in some defects in deposited preform such as porosity and local non-uniform distribution of reinforcements [9-11]. As a result, the application of spray deposited materials is limited due to poor mechanical properties. Therefore, further secondary operations by densification techniques such as hot isostatic pressing(HIP), forging, extrusion as well as rolling are necessary to reduce or even eliminate pores, break up reinforcement clustering, improve metallurgical bonding and crush brittle oxide films. All of these will be helpful to improving microstructures and mechanical properties of aluminum alloy matrix composites[11-15]. Based on this, in the present work, SiCp/8009Al composite preform prepared by spray co-deposition process was subjected to further densification using extrusion and rolling. The evolution of microstructures during hot-working and its effects on mechanical properties were investigated, and fracture behavior of the composites at room temperature was also discussed.
2 Experimental
The initial porous SiCp/Al-8.5Fe-1.3V-1.7Si (mass fraction, %) cylindrical preform was prepared by multi-layer spray co-deposition technology developed by the authors and the major process parameters are given in Table 1. SiC particles with mean size of about 10 μm were selected as the reinforcement with volume fraction of about 15%. The initial relative density of the deposited preform, which is defined as the ratio of the density of deposits to its theoretical density, was about 86%.
Table 1 Process parameters of multi-layer spray co-deposition experiment
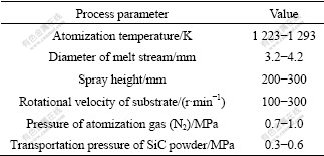
After spray co-deposition, the porous composite preform was machined into a cylinder in the size of d 155 mm×400 mm and extruded into a plate of cross- section of 125 mm×20 mm with an extrusion ratio of 7.5 at 480 ℃. The hot rolling was performed on a two- high rolling mill with rolls of 360 mm in diameter and 600 mm in length. The nominal rolling speed was 0.43 m/s. The plate was preheated for 1 h before rolling and reheated for 20 min between each pass in a furnace operated at 480 ℃. The obtained sheet was 1.3 mm in thickness.
The microstructures of the composites were examined by using optical microscopy(OM), scanning electron microscopy(SEM), X-ray diffractometry(XRD) and transmission electron microscopy(TEM). Tensile specimens with axis parallel to longitudinal direction were cut from sheets of as-extruded and as-rolled materials. The tensile testing was conducted on an Instron machine at room temperature according to GB/T 228—2002.
3 Results and discussion
3.1 Microstructure
Fig.1 shows the microstructure evolution of the spray-deposited composites during hot working. The as-deposited preform was a coalesced bulk consisting of deposited particles, reinforcements and pores (Fig.1(a)). The deposited particles were in spherical, ligament and irregular shapes, and the distribution of reinforcements and pores appeared somehow non-uniformly. Pore is an inherent problem associating with discrete droplet processes during spray deposition. The primary sources of porosity in deposited materials generally include gas entrapment, solidification shrinkage and interstitial porosity[9]. After extrusion, most of pores have disappeared (Fig.1(b)). Compared with those of as-deposited composite, SiC particles presented relatively uniform distribution except for occasional local clustering, indicating a better densification. The decreased porosity of MMCs during extrusion is ascribed to the flow of matrix alloy under applied shear force, resulting in filling the voids. No evident pores and SiC particle aggregation were observed in the rolled material (Fig.1(c)). SiC particles in as-rolled sheet exhibited larger space distance from each other due to further metal flow during rolling.
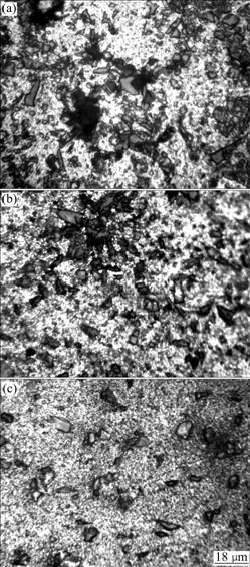
Fig.1 OM images of as-deposited (a), as-extruded (b) and as-rolled (c) composites after extrusion
Moreover, as shown in Fig.2, lamellar structure could be observed in both deposited and extruded materials in macro-scale. The formation of lamellar structure was related to the rotating movement of substrate during spray deposition. This was resulted from the discrepancies of liquid phase thin film and unit mass during droplets impinging on deposition surface. The lamellar structure seemed to be ‘inherited’ when being submitted to extrusion. SEM examination showed that the interface of layers was composed of deposited particles, small pores and aggregated SiC particles (Fig.3(a)). The extrusion process considerably reduced large interstitial pores, but some smaller intra-layer pores still remained in SiC particle clusters. The possible reason for residual porosity and gathered SiC particles lies in the smaller extrusion ratio (7.5) used here. The subsequent rolling effectively eliminated pores and caused SiC particles to flow along rolling direction, resulting in more homogeneous distribution (Fig.3(b)). This may in turn explain the more effective densification of composites during rolling in which the clusters were broken up and the voids inside were filled. X-ray diffractometry(XRD) was performed to identify phase composition of the composites before and after secondary processing. From Fig.4, there exist mainly α(Al), SiC and Al12(Fe,V)3Si phases in hot-worked materials, which are the same as those of spray-deposited preform. There was no definitive evidence for the presence of equilibrium phase θ-A113Fe4 and neither of other intermetallics phases was found on XRD patterns due to their lower concentrations.
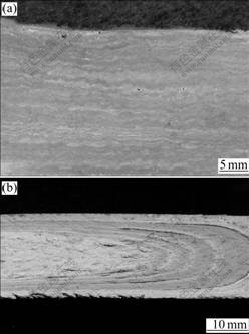
Fig.2 Lamellar macrostructures in as-deposited preform (a) and as-extruded plate (b)
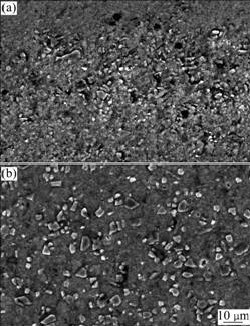
Fig.3 Local SiC particle clustering and pores in lamellar structure of as-extruded plate (a) and homogeneous SiC particle distribution in as-rolled sheet (b)
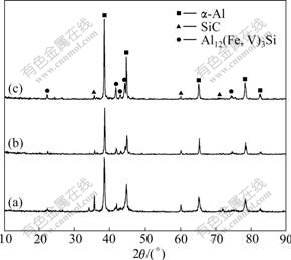
Fig.4 XRD patterns of spray-deposited (a), extruded (b) and rolled (c) composites
Fig.5 shows TEM images of dispersoid strengthening phase Al12(Fe,V)3Si in deposited and thermomechanically processed materials. The ultra-fine dispersoids were homogeneously distributed both in α(Al) grains and at their boundaries. Upon hot extrusion and rolling, the average size of Al12(Fe,V)3Si particles experienced slightly coarsening from about 80 nm to about 120 nm, which is a clear indication of their excellent thermal stability. The matrix grain size ranged from 300 to 700 nm. At the same time, more dislocations were observed in the rolled matrix materials.
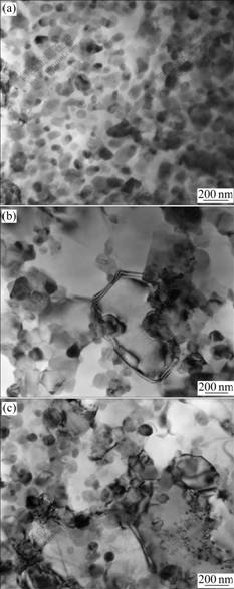
Fig.5 TEM images of as-deposited (a), as-extruded (b) and as-rolled (c) composites after extrusion
3.2 Mechanical properties
Previous investigation[16] revealed that the forgeability/mechanical properties of co-sprayed MMCs were significantly affected by the unique metallurgical pattern termed as tree ring structure(TRS), i.e., lamellar structure. Metallurgical examination showed that the TRS comprises bands with high and low concentrations of particles. In general, mechanical properties of the spray co-deposited composite depend strongly upon its microstructure. With severe shear deformation, most pores were collapsed and closed; brittle oxide films between deposited particles were broken down resulting in stronger metallurgical bonding, and the distribution of SiC particles was improved substantially. Therefore, the resultant mechanical properties can be increased significantly due to higher dislocation density, stronger metallurgical bonding between deposited particles and SiC reinforcements, as listed in Table 2. Those defects mentioned above can be used to rationalize the lower mechanical properties of as-deposited and extruded composites, which may lead to premature fracture during tensile testing.
Table 2 Mechanical properties of spray co-deposited SiCp/ 8009Al MMCs
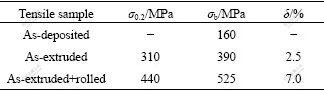
The Al-Fe-V-Si alloys derived their strength from interaction of dislocations and high volume fraction fine intermetallics Al12(Fe,V)3Si. After hot extrusion and rolling, sizes of dispersoids were similar to those of deposited materials, suggesting that the dispersoids were more thermally stable than the precipitates found in conventional age-hardening aluminum alloys, whereas dislocations and grain boundaries were expected to be pinned effectively. Three major strengthening mechanisms contributed to the outstanding mechanical properties of spray deposited SiCp/8009Al composites. First, finer grain size resulted from high cooling rate during spray deposition gave rise to higher strength in terms of well-known Hall-Petch equation. Second, according to Orowan mechanism, tiny dispersive Al12(Fe,V)3Si particulates formed during rapid solidification strengthen matrix alloy where dislocations are pinned and immovable. Meanwhile, recrystallization and grain growth were restricted effectively too by dispersoids during hot working[17]. Third, the added SiC particles efficiently undertook loads transferred from matrix, resulting in particulate reinforcement in MMCs.
The SEM fractographs of as-extruded (Fig.6(a)) and as-rolled (Fig.6(b)) tensile samples showed more plastic deformation occurred in rolled specimen than that in extruded one. The fractograph of rolled specimen was characterized by dominant dimples with lots of tear edges, which is consistent well with total elongation listed in Table 2. On the other hand, some larger broken SiC particles were observed on both fracture surfaces. Pits resulted from small SiC particle extractions were also found in Fig.6(b). These findings allow us to suggest that the fracture initiated from large SiC particles cracking together with small particles debonding followed by pores nucleation, growth and connection in the matrix.
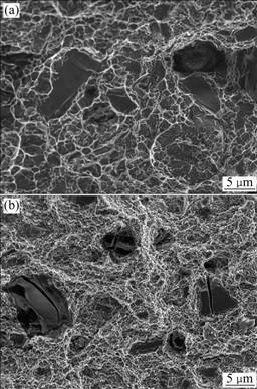
Fig.6 SEM fractographs of as-extruded (a) and as-rolled (b) composites
4 Conclusions
1) The spray-deposited SiCp/8009Al composites preform exhibited lamellar structure in macro-scale and it also appeared in extruded plates. The interface of lamellar structure was composed of deposited particles, local SiC particle clusters and pores.
2) Most defects such as SiC particle clusters and pores can be reduced effectively after extrusion by strong shear stress. Mechanical properties were improved significantly after subsequent rolling due to elimination of porosity and uniformly distributed SiC particles. In addition, for the as-rolled MMCs, SEM observation of tensile fracture indicated that fracture was initiated from large SiC particles cracking and small particles debonding followed by pores nucleation, growth and connection in the matrix.
References
[1] IBRAHIM I A, MOHAMED F A, LAVERNIA E J. Particulate reinforced metal matrix composites—A review [J]. Journal of Materials Science, 1991, 26: 1137-1156.
[2] SRIVATSAN T S, SUDARSHAN T S, LAVERNIA E J. Processing of discontinuously-reinforced metal matrix composites by rapid solidification [J]. Progress in Materials Science, 1995, 39: 317-409.
[3] SKINNER D J, BYE R L, RAYBOULD D, BROWN A M. Dispersion strengthened Al-Fe-V-Si alloys [J]. Scripta Metall, 1986, 20(6): 867-872.
[4] YAN Qi-qi, FU Ding-fa, DENG Xue-feng, ZHANG Hui, CHEN Zhen-hua. Tensile deformation behavior of spray-deposited FVS0812 heat-resistant aluminum alloy sheet at elevated temperatures [J]. Materials Characterization, 2007, 58: 575-579.
[5] WANG Feng, ZHU Bao-hong, XIONG Bai-qing, ZHANG Yong-an, LIU Hong-wei, ZHANG Rong-hua. An investigation on the microstructure and mechanical properties of spray-deposited Al-8.5Fe-1.1V-1.9Si alloy [J]. Journal of Materials Processing Technology, 2007, 183: 386-389.
[6] GRANT P S. Spray forming [J]. Progress in Materials Science, 1995, l39: 497-545.
[7] RAJU K, OJHA S N, HARSHA A P. Spray forming of aluminum alloys and its composites: An overview [J]. Journal of Materials Science, 2008, 43: 2509-2521.
[8] SRIVASTAVA V C, SCHNEIDER A, UHLENWINKEL V, BAUCKHAGE K. Spray processing of 2014-Al+SiCP composites and their property evaluation [J]. Mater Sci Engg A, 2005, 412: 19- 26.
[9] CAI W D, LAVERNIA E J. Modeling of porosity during spray forming [J]. Mater Sci Eng A, 1997, 226/228: 8-12.
[10] DEY A, KORIA S C, DUBE R K. Model prediction and experimental validation of porosity in metal spray deposit [J]. Powder Metallurgy, 2007, 50: 359-366.
[11] SUN Y P, YAN H G, CHEN Z H, CHEN D, CHEN G. Effect of a novel sequential motion compaction process on the densification of multi-layer spray deposited 7090/SiCp composite [J]. Journal of Materials Science, 2008, 43: 6200-6205.
[12] CHEN Z H, CHEN Z G, YAN H G, CHEN D, HE Y Q, CHEN G. Novel method for densification of porous spray deposited Al-Fe-V-Si alloy tube preforms [J]. Materials Science and Technology, 2009, 25(1): 111-116.
[13] XIAO Yu-de, LI Wen-xian, TAN Dun-qiang, MA Zheng-qing, WANG Ri-chu. Effect of processing parameters on microstructures and mechanical properties of rapidly solidified AlFeVSi hot-extruded product [J]. Trans Nonferrous Met Soc China, 2003, 13(3): 558-563.
[14] ZHAN Mei-yan, CHEN Zhen-hua, YAN Hong-ge, XIA Wei-jun. Deformation behaviors of porous 4032 Al alloy preform prepared by spray deposition during hot rolling [J]. Journal of Materials Processing Technology, 2007, 182: 174-180.
[15] EUH K J, KANG S B. Effect of rolling on the thermo-physical properties of SiCp/Al composites fabricated by plasma spraying [J]. Mater Sci Eng A, 2005, 395: 47-52.
[16] SEE K S, DEAN T A. The effects of the disposition of SiC particles on the forgeability and mechanical properties of co-sprayed aluminium-based MMCs [J]. Journal of Materials Processing Technology, 1997, 69: 58-67.
[17] CARRENO F, PEREZ-PARDO M T, GONZALEZ-DONCEL G. Texture stability of a rapidly solidified dispersion strengthened Al-Fe-V-Si material [J]. Scripta Materialia, 1998, 38(9): 1427-1433.
Foundation item: Project(50304008) supported by the National Natural Science Foundation of China
Corresponding author: CHEN Zhen-hua; Tel: +86-731-88821648; E-mail: chenzhenhua45@hotmail.com
DOI: 10.1016/S1003-6326(08)60416-1
(Edited by YANG Bing)