
Effect of pressure on microstructures and mechanical properties of Al-Cu-based alloy prepared by squeeze casting
ZHANG Ming(张 明), ZHANG Wei-wen(张卫文), ZHAO Hai-dong(赵海东),
ZHANG Da-tong(张大童), LI Yuan-yuan(李元元)
School of Mechanical Engineering, South China University of Technology, Guangzhou 510640, China
Received 24 October 2006; accepted 11 January 2007
Abstract: A new high-strength aluminum alloy with better fluidity than that of ZL205A was developed. The effect of applied pressure during squeeze casting on microstructures and properties of the alloy was studied. The results show that the fluidity of the alloy is 16% and 21% higher than that of ZL205A at the pouring temperature of 993 K and 1 013 K, respectively. Compared with permanent-mold casting, mechanical properties of the alloy prepared by squeeze casting are much higher. The tensile strength and elongation of the alloy are 520 MPa and 7.9% in squeeze casting under an applied pressure of 75 MPa, followed by solution treatment at 763 K for 1 h and at 773 K for 8 h, quenching in water at normal temperature and aging at 463 K for 5 h. The improvement of mechanical properties is attributed to the remarkable decreasing of the secondary dendrite arm spacing(SDAS) and eliminating of micro-porosity in the alloy caused by applied pressure.
Key words: Al-Cu-based alloy; squeeze casting; microstructure; mechanical property
1 Introduction
Squeeze casting(SC) is a kind of special casting technique which solidification is promoted under high pressure within a re-usable die. It is usually used to fabricate high integrity engineering components with high performance[1-5]. There are two different forms of squeeze casting, i.e. direct SC and indirect SC. In direct squeeze casting process, the pressure is applied to the entire surface of the liquid metal during solidification by a punch, which is available to produce castings of full density. In indirect squeeze casting process, metal is injected into the die cavity by a small diameter piston. Although the cast product produced by indirect squeeze casting is not of the good properties as is obtained from direct squeeze casting process, the products can be formed in complicated shapes[1-2].
Many research work on squeeze casting has been carried out in recent years. Among all of the SC processing parameters, the effect of pressure on the mechanical properties of castings has been studied extensively[6-12]. Many researchers regard that the application of pressure on a molten metal during solidification may cause several effects such as change in the melting point, change of cooling rate, reduction of gas and shrinkage porosities, all of which may lead to the improvement of the alloys properties[1,3-6]. However, influence of pressure on specific alloys is still drawn much attention.
Al-Cu-based alloys are a series of high-strength lightmass structural materials that are used intensively in industry. A typical alloy of this series alloys is ZL205A, named in Chinese norm. This alloy has been widely used in transportation, aerospace and military industry. However, since the castability of this alloy is very poor, it is difficult to produce complex castings with ZL205A through indirect squeeze casting process. New alloys with comparable strength and better castability are desired. Recently, Some high-strength wrought aluminum alloys were developed to be used for squeeze casting process[1, 13-14].
In this paper, a novel aluminum-copper based alloy with good castability was developed, and squeeze casting processing of the alloy was studied. Special attention was paid to the influence of pressure on microstructures and properties of the alloy.
2 Experimental
Based on 2XXX series wrought aluminum alloy, a new alloy with the main elements composition (mass fraction, %, by chemical analysis) of 4.83 Cu, 1.05 Mg, 0.58 Mn and minim elements such as Ti, Zr, V, RE with the total content between 0.2% and 1.0% was developed. The raw materials for preparing the developed alloy are commercial pure aluminum, commercial pure magnesium, and master alloys of Al-50Cu, Al-10Mn, Al-5Ti-1B, Al-10Zr, Al-4V and Al-10RE.
The raw materials were melted in a crucible furnace at 1 073 K and the melt was poured in a cylindrical die (diameter: 80 mm, height: 50 mm) under pressures from 0.1 MPa (atmospheric) to 175 MPa at temperature 1 003 K. The die was preheated to 523 K prior to casting. The samples were squeezed into size of 30 mm in height and 80 mm in diameter.
The fluidity of the investigated alloy and ZL205A alloy with the composition of 5.03 Cu, 0.45 Mn, 0.25 Ti, 0.21 Cd, 0.13 V, 0.15 Zr and 0.04 B was measured by standard three-screw mould.
All samples for tensile test were cut by line-cutting machine from the middle location of the castings in the dimension of 15 mm×15 mm×70 mm. The samples were treated by solution annealing for 1 h at 763 K and for 8 h at 773 K, quenching in water at normal temperature and aging for 5 h at 463 K. The dimension of the tensile specimen is shown in Fig.1. Tensile test was carried out on SANS standard mechanical tester and all data were taken from at least three separated measurements. Samples for optical microstructure observation were prepared from tensile specimens by standard metallographic method. PHILIPS XL-30FEG scanning electron microscope was used to analyze the tensile fracture surface.
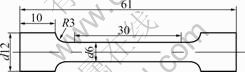
Fig.1 Dimension of tensile specimen (mm)
3 Results
3.1 Fluidity
The fluidity of the studied alloy is shown in Table 1 and the fluidity of high-strength casting aluminum alloy ZL205A, which is equivalent to aluminum alloy 204.0 of American brand, was also list.
Table 1 Fluidity of investigated alloy and ZL205A
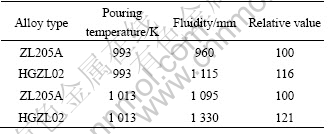
It can be seen from Table 1 that the fluidity of the studied alloy is 16% and 21% higher than that of ZL205A at the pouring temperature 993 K and 1 013 K, respectively.
Fluidity is a key parameter to characterize the castability of alloys. Although squeeze casting has significant benefit over other casting processes to produce components with poor castability, fluidity is still an important factor to be concerned in the forming of complex components, especially in the indirect squeeze casting process. ZL205A is a kind of high-strength casting aluminum alloy, named in Chinese norm. This alloy has been widely used as high-loaded structural parts. The experimental results show that the fluidity of the developed alloy is better than that of ZL205A. Compared with the composition of ZL205A (4.6-5.3 Cu, 0.3-0.5 Mn, 0.15-0.35 Ti, 0.15-0.25 Cd, 0.05-0.3 V, 0.05-0.2 Zr, 0.005-0.06 B), the main difference of the developed alloy is that it contains about 1.0% Mg. According to the phase diagram, it could be concluded that the melt point of the developed alloy would be lower than that of ZL205A. At the same pouring temperature, the alloy with lower melting point can stay in liquid state in a longer period of time. This may be the main reason of the improvement of the fluidity of the developed alloy. If the developed alloy can be used to produce component by squeeze casting process, it will become a substituent alloy for ZL205A.
3.2 Mechanical properties
Tensile strength and elongation of the investigated alloy at different squeeze casting pressures are shown in Fig.2. Both in as-cast and heat-treated states, the tensile strength and elongation of the alloy increase with increasing the applied pressure. However, the increase of tensile strength and elongation is obvious only at the pressure less than 45 MPa and 75 MPa, respectively. After that, the applied pressure has little effect on the tensile properties of the alloy as shown in Fig.2. It is also shown that the tensile strength of the alloy increases remarkably after heat treatment of solution and aging.
However the influence of heat treatment on elongation of the alloy is somewhat complicated. When the pressure is less than 30 MPa, the applied heat treatment of the alloy has no obvious effect on elongation of the alloy but the elongation decreases obviously after heat treatment when the pressure is higher than 50 MPa. As shown in Fig.2, after heat treatment, tensile strength of the alloy squeezed cast under 75 MPa is 520 MPa and its elongation is 7.9%.
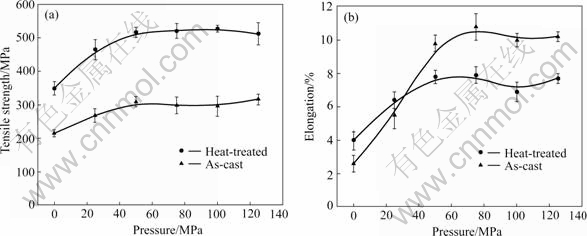
Fig.2 Tensile strength (a) and elongation (b) of alloy at different squeeze casting pressures
3.3 Microstructures
Fig.3 shows the microstructure of the as-cast alloy prepared at different squeezing pressures. It is clear that the squeezing pressure has significant influence on the microstructure of the alloy. The results show that the grain size of the alloy decreases with the increase of the squeezing pressure. Furthermore, the inter-metallic phases in the alloy with no applied pressure are coarser than that under high squeezing pressure.

Fig.3 Optical micrographs of as-cast alloys applied different pressures: (a) 0; (b) 25 MPa; (c) 50 MPa; (d) 75MPa
The fractural morphologies of the as-cast and heat-treated alloys are shown in Figs.4 and 5, respectively. The alloys in all cases are characterized in ductile fracture. There are lots of dimples on fractural surface. With increasing the pressure, the quantity of dimple increases but the dimple size becomes smaller. Micro-porosity can be seen easily in the alloy when the alloy is cast with no applied pressure (see the arrows in Fig.4(a)). As the squeezing pressure reaches 25 MPa, the micro-porosity can be seldom found (see the arrow in Fig.4(b)) and the micro-porosity disappears completely with continuously increasing squeezing pressure (see Figs.4(c) and (d)).
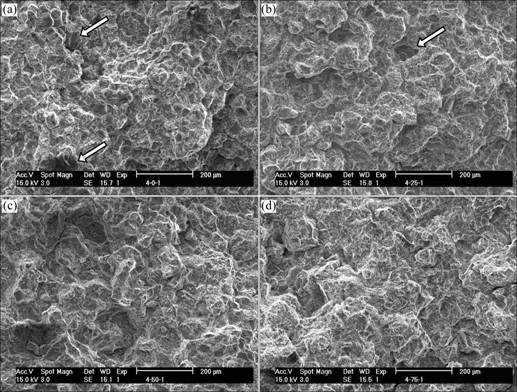
Fig.4 Fracture morphologies of as-cast alloys at different squeezing pressures: (a) 0; (b) 25 MPa; (c) 50 MPa; (d) 75 MPa
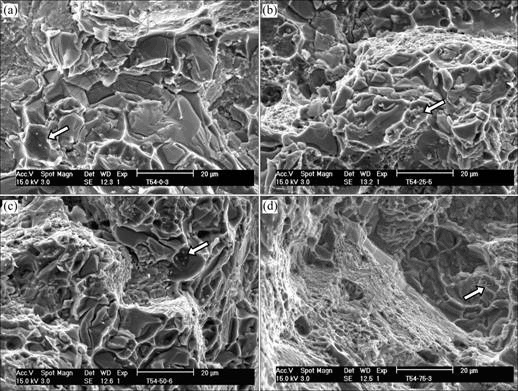
Fig.5 Fracture morphologies of heat-treated alloys at different squeezing pressures: (a) 0; (b) 25 MPa; (c) 50 MPa; (d) 75 MPa
From the fractural surface of the heat-treated alloys, the inter-metallic compounds can be found in the grain boundary. With increasing the squeezing pressure, the size of compounds becomes smaller, in particularly at the initial stage. It can be also found that there are lots of small particles embedded in the dimples of fractural surface in the alloys (see the arrows in Fig.5).
4 Discussion
The grain size of the alloy decreases obviously with increasing the applied pressure, which can be clearly characterized by the secondary dendrite arm spacing (SDAS) as shown in Fig.6.
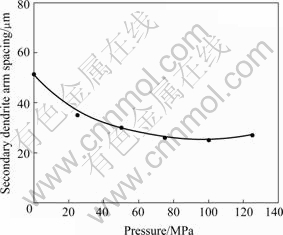
Fig.6 Secondary dendrite arm spacing in as-cast alloys against applied pressure
It is well known that Al-Cu based casting alloys have a long freezing range. Generally, micro-porosity is easy to form in Al-Cu alloy during solidification. Fig.7 shows micro-porosity formed in the alloy with no applied pressure. In squeeze casting, the applied pressure can help the liquid metal to fill into the micro-pores. In this study, it was found that micro-porosity was eliminated completely when the pressure was up to 50 MPa. This is one of the reasons for the mechanical properties improvement.
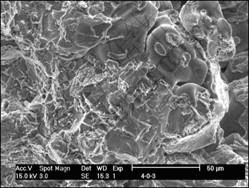
Fig.7 Morphology of micro-porosity of as-cast alloy with no applied pressure
It was reported that the application of pressure during solidification would affect the freezing point of the alloy[7,12,15], which may be deduced by the Clausius-Clapeyron equation[1]:

where Tf is the equilibrium freezing temperature; Vl and Vs are the specific volumes of the liquid and solid, respectively; and Lf is the latent heat of fusion. Substituting the appropriate thermodynamic equation for volume, the effect of pressure on freezing point may roughly be estimated by

where P0, Lf and R are constants. Therefore, Tf should increase with increasing pressure. This change may bring about greater undercooling in an initially superheated alloy.
Apart from the changes in undercooling of the molten alloy caused by applied pressure, greater cooling rates for the solidifying alloy can be realized due to reduction in the air gap between the alloy and the die wall and thus larger effective contact area. Obviously, the increase of undercooling degree and heat-transfer coefficient will result in the refinement of the grain size of squeeze casting alloy. Furthermore, the increase in density of the alloy will be obtained due to reduction of micro-porosity. The consequences of all these changes are a significant improvement in mechanical properties of squeeze casting alloys.
5 Conclusions
1) A high-strength Al-Cu-based alloy with the main elements composition (mass fraction, %) of 4.33 Cu- 1.25 Mg-0.58 Mn and minim elements such as Ti, Zr, V and RE was developed. The fluidity of the alloy is 16% and 21% higher than that of ZL205A at the pouring temperature 993 K and 1 013 K, respectively.
2) The tensile strength and elongation of the alloy are 520 MPa and 7.9% in squeeze casting at the pressure of 75 MPa, followed by solution treatment at 763 K for 1 h and at 773 K for 8 h, quenching in water at normal temperature and aging at 463 K for 5 h.
3) The applied pressure in squeeze casting leads to remarkable decrease of the secondary dendrite arm spacing and disappearance of micro-porosity in the alloy, which are the main reasons for the mechanical properties improvement of the investigated alloy.
References
[1] GHOMASHCHI M R, VIKHROVL A. Squeeze casting: An overview [J]. Journal of Materials Processing Technology, 2000, 101(1): 1-9.
[2] QI Pi-xiang. Survey of squeezing casting technology development home and abroad [J]. Special Casting & Nonferrous Alloys, 2002, 22(2): 20-23. (in Chinese)
[3] FRANKLIN J R, DAS A A. Squeeze casting—A review of the status [J]. British Foundryman, 1984, 77(3): 150-158.
[4] CHEN Wei-ping, LI Yuan-yan, GUO Guo-wen. Squeeze casting of Al-Cu alloy [J]. Journal of Central South University of Technology, 2002, 9(3): 159-164.
[5] LUO Ji-xiang, BAI Xu-bai, CHEN Wei, PAN Xin. Study and application on squeezing casting technology of aluminum alloys [J]. Foundry, 2002, 51(8): 464-469. (in Chinese)
[6] VIJIAN P, ARUNACHALAM V P. Experimental study of squeeze casting of gunmetal [J]. Journal of Materials Processing Technology, 2005, 170(1/2): 32-36.
[7] MALEKI A, NIROUMAND B, SHAFYEI A. Effects of squeeze casting parameters on density, macrostructure and hardness of LM13 alloy [J]. Mater Sci Eng A, 2006, A428(1/2): 135-140.
[8] CHEN Z W, THORPE W R. The Effects of squeeze casting pressure and iron content on the impact energy of Al-7Si-0.7Mg alloy [J]. Mater Sci Eng A, 1996, A221(1/2): 143-153.
[9] LYNCH R F, OLLEY R P and GALLAGHER P C J. Squeeze casting of aluminum [J]. AFS Transactions, 1975, 83: 569-576.
[10] HU Mao-liang, ZHAO Mi, JI Ze-sheng, SUN Guang-bin, PIAO Yong-ji. Effect of squeezing casting technology on structures and properties of air-conditioner swaying tray of automobile [J]. The Chinese Journal of Nonferrous Metals, 2006, 16(3): 400-405. (in Chinese)
[11] RAJAGOPAL S, ALTERGOTT W H. Quality control in squeeze casting of aluminum [J]. AFS Transactions, 1985, 93: 145-154.
[12] SHEHATA F. Squeeze casting of Al-Cu and Al-Si alloys [J]. Process Adv Mater, 1994, 4(3): 136-140.
[13] YUE T M. Squeeze casting of high-strength aluminum wrought alloy AA7010 [J]. Journal of Materials Processing Technology, 1997, 66(1/3): 179-185.
[14] KIM S W, DURRANT G, LEE J H, CANTOR B. The effect of die geometry on the microstructure of indirect squeeze cast and gravity die cast 7050 (Al-6.2Zn-2.3Cu-2.3Mg) wrought Al alloy [J]. Journal of Materials Science, 1999, 34(8): 1873-1883.
[15] BALAN P, PILLAI R M, SATYANARAYANA K G, PAI B C. The structure and properties of squeeze-cast eutectic Al - Si plates [J]. Int J Cast Metals Res, 1993, 6(3): 131-136.
Corresponding author: ZHANG Wei-wen; Tel: +86-20-87113832; E-mail: mewzhang@scut.edu.cn
(Edited by YANG Hua)