Article ID: 1003-6326(2005)02-0238-05
Fabrication of TiB2 composite powders coated with BN by high speed airflow impact
FENG Cai-mei(冯彩梅), WANG Wei-min(王为民), FU Zheng-yi(傅正义)
(State Key Laboratory of Advanced Technology for Material Synthesis and Processing,
Wuhan University of Technology, Wuhan 430070, China)
Abstract: TiB2 powders coated with BN were prepared by Hybridization System making use of dry impact blending method to achieve powder surface modification. Parameters of coating were analyzed and the most appropriate condition was summarized. Scan electron microscope of JSM-5610LV and transmission electron microscope of H-600STEM/EDS were used to observe the microstructure of coated powders. Results show that treatment time, rotation speed, granularity ratio of TiB2 to BN, pretreatment of materials etc influence the coating results evidently. Mixing raw materials and coating with BN under the appropriate condition can get round TiB2/BN composite powder with smooth surface and compact coating layer.
Key words: high-speed airflow impaction; hybridization system; coating; TiB2/BN composite powder CLC number: TQ174
Document code: A
1 INTRODUCTION
TiB2 -based ceramics have been studied extensively because of their excellent properties such as high melting point, high rigidity, and stability to chemical etch. But further applications are restricted to a certain extent because of their great brittleness and difficulty to be processed. h-BN is a soft material after sintering because of its lubricant property. TiB2 and BN are consistent well in chemical properties, so TiB2-BN composite ceramic can be manufactured[1-3]. The preparation of BN-coated TiB2 composite powders can make foundation for making composite ceramics possessing their advantages as well as eliminating limitations.
Surface coating is one of the most useful technology to improve particles properties[4-7]. There are many ways such as sol-gel technique, homogeneous precipitation, and heterocoagulation[8-12] to realize powder surface coating. Luther et al and Wang succeeded in coating Si3N4 using aluminum alkoxide, and Shih et al coated the same material using boehmite by the sol-gel technique. Mitchell and Hu adapted homogeneous precipitation techniques to coat SiC particles and whiskers with alumina precursor[13]. However, in most cases, these techniques still need further development to take full advantage of them and these techniques often result in non-uniform coating and inhomogeneous microstructure owing to the growth of isolated nuclei.
Micro hybridization technology is a surface modification technique for producing finer particles, in which coating, encapsulating and high-energy mechano-chemical reaction are employed[14]. With respect to surface modification by the mechano-chemical reaction, Honda and Koishi have reported that adhesion and embedding of fine particles onto other large particle surfaces were often observed in the dry blending of a binary powder mixtures with two different sizes, and that the adhesion among particles was due to Van der Waals interaction. This phenomenon can be used in combination of many different powders, for example, the manufacture and preparation of cosmetics, foods, drugs and copy toners.
In this study, we introduced Micro Hybridization System to achieve TiB2/BN composite powders with excellent microstructure. At the same time, we studied the influence of some technical parameters and got the most feasible work condition.
2 EXPERIMENTAL
2.1 Technique and apparatus
A Nara Hybridization System (Model NHS-0; Nara Machinery Co Ltd, Tokyo, Japan) was used. Hybridization is a method for preparing complexes of materials by a mechanical shock process involving dry impact blending. Many studies were carried out by using this method and revealed the possibility to create high quality particle composites with uniform microstructure and excellent properties. The apparatus is composed of feed chute, exhaust chute, mainframe and operating system. The mainframe is made up of high-speed circumrotate rotor, stator and circulation route in which particles are dispersed rapidly by high-speed airflow impaction[15]. There are many forces such as compression, friction, shear and impaction, brought by particles interaction, which cause adhesion and embedding of fine particles onto larger particle surface.
2.2 Experimental project and process
On the basis of large numbers of experiments, we find out that treatment time, rotation speed, granularity ratio of TiB2 to BN, mass of materials, material disposal in advance etc are main factors affecting the modification outcome. Table 1 presents several typical experiment, which contains the main parameters.
Weighing TiB2 and BN respectively according to Table 1, mixing powders in a planet ball mill for 4h, then coating was realized in the Hybridization System. Scan electron microscope(SEM) of JSM-5610LV and transmission electron microscope(TEM) of H-600STEM/EDS were used to observe the microstructure of coated powder.
3 RESULTS AND DISCUSSION
3.1 Changes of temperature in process of coating
Kinetic energy produced by the fiction and collision among particles changes to heat energy when coating is carried out. Fig.1 shows the changes of temperature along with treatment time. In experiment 1 and experiment 2, the temperature increases quickly in the first 4min and keeps almost unchanged subsequently. It shows the same trend in experiment 3. In experiment 4, the time of change is shortened to just 2min. We can conclude from these results that the main coating process occurs in the first few minutes and too long treatment time is meaningless. Furthermore time is relevant to the mass of materials and rarely affected by the rotation speed.
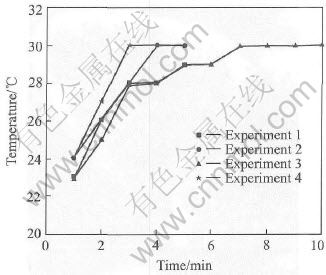
Fig.1 Change of temperature with treatment time
3.2 Effect of technical parameters on coating outcome
Fig.2 shows the surface morphologies of coated powders under conditions of different treatment time and different rotation speeds. The particles have got coated when treatment time is 5min in experiment 1 and have hardly any improvement in their coating effects while the treatment time is prolonged to 10min in experiment 2. This result accords well with foregoing analysis about the changes of temperature. So we think 5min is enough to realize coating in this system.
Experiment 3 is done on the basis of experiment 1 just by changing the rotation speed from 10000r/min to 15000r/min. Low rotation speed cannot make the circulation of airflow fluent and high rotation speed is helpful to making coated powders more round and smooth. But rotation speed of 15000r/min seems to be too high for this system because there appears crack as shown in Fig.2(c). So we take 13000r/min as suitable rotation speed.
Table 1 Several typical experiments which contains main parameters
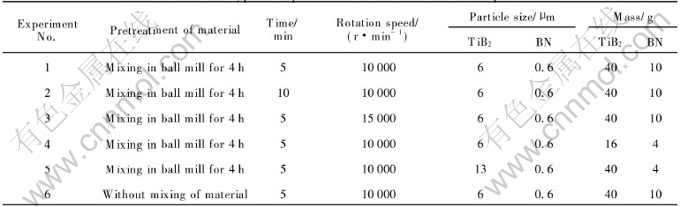
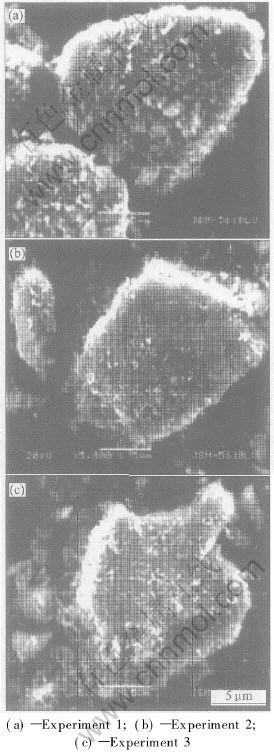
Fig.2 SEM photographs of coated powders
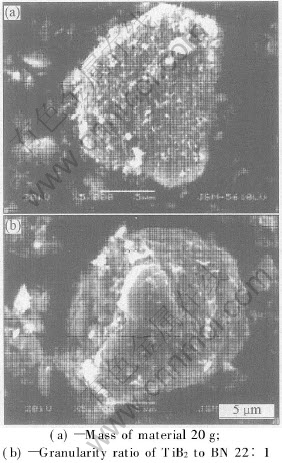
Fig.3 SEM photographs of coated powders in experiment 4(a) and experiment 5(b)
Mass of materials is another important factor affecting coating. Fig.3(a) clearly shows that particles coated in experiment 4 are less smooth and round than those coated in experiment 1, that is to say, appropriate mass is significant. This is probably because that the chance of impaction among particles will be reduced while quantity is too small. So we conclude that 50g is the most proper quantity just as the equipment demands as a limit. Fig.3(b) shows the difference of coated powders with different granularity ratio of TiB2 to BN. It is evident that big ratio of particle size is helpful for the process of coating and can make particles more round and smooth. It is clear that big granularity ratio can provide more surface area for particles to take contact and be impacted and collided.
Pretreatment of material will have apparent influence on coating. As Fig.4(a) shows, the coated powders without any pretreatment get scarcely any change to roundness and many fine particles dont gain attachment to larger core particles. Mixing of TiB2 and BN in a planet ball mill for 4h can facilitate coating(Fig.4(b)) and disposing of TiB2 solely beforehand can make well-coated powders(Fig.4(c)).
3.3 Best-coated powders got at most proper technical parameter
We can conclude from the experiments and analysis that the most suitable coating condition is disposing TiB2 powders and mixing raw materials beforehand, then coating with treatment of 5min, rotation speed of 13000r/min, mass of 50g at one time.
As Fig.5(a) shows, the TiB2 particles without coating are hexastyle crystal. After coating, as Figs.5(b) and (c) show, the composite powders are round with smooth surface and dense coating layer. Fine BN particles are attached to the surface of TiB2 particles and the TiB2 particles loss their edges and corners. We think the Hybridization System provides powerful airflow to disperse particles and finer BN particles adhered to the surface of bigger TiB2 particles mainly due to Van der Waals got from particles’ impact.
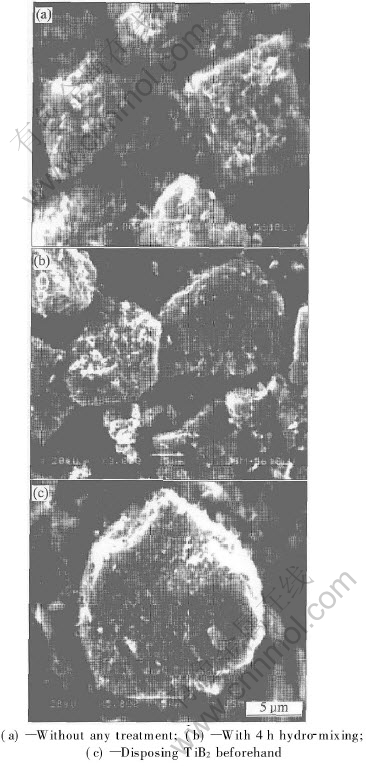
Fig.4 SEM photographs of coated powders with different pretreatments

Fig.5 Microstructures of TiB2 particles and best-coated powders
4 CONCLUSIONS
TiB2/BN composite particles that are modified to round-shape are prepared by Micro Hybridization technology. Treatment time, rotation speed, ratio of particle size, mass, pretreatment etc are main factors affecting the modification outcome. The most suitable parameters for the preparation is found to be 5min, 13000r/min, 50g and doing pretreatment to materials. Fine BN particles adhere to bigger TiB2 particles evenly. The surfaces of coated particles are round and smooth. The further study of TiB2/BN coated powders manufactured with the technology of Micro Hybridization System will be taken.
REFERENCES
[1]WANG Wei-min, FU Zheng-yi, WANG Hao. Influence of hot pressing sintering temperature and time on microstructure and mechanical properties of TiB2 ceramics [J]. Journal of the European Ceramic Society, 2002, 22 (7): 1045-1049.
[2]WANG Yu-cheng, FU Zheng-yi. Research progress of TiB2-BN compound conductible ceramics [J]. Journal of Wuhan University of Technology, 2000, 22(5): 35-37.
[3]ZHANG Guo-jun. Preparation of BN-AlN-TiB2 electrical ceramic composite (BAT ceramics) by reactive hot-pressing (RHP) method [J]. China Ceramics, 1994(3): 8-13.
[4]CHEN Long-wu, REN Yu, GAN Li-hua, et al. Surface modification technique for inorganic powders [J]. Research and Exploration in Laboratory, 2003, 22 (6): 45-46.
[5]XIE Gang, ZHU Hua-shan, ZHANG Hao-dong, et al. Study on the surface modification of nanosized titanium dioxide [J]. Journal of Kunming University of Science and Technology(Science and Technology), 2004, 29(4): 38-42.
[6]LI Min, LI Hui-dong, LI Hui-qi, et al. Development of plasma surface modification technology [J]. Metal Heat Treatment, 2004, 29(7): 5-9.
[7]LIU Li-jun, GUO Fen, CHEN Jian-feng. Surface modification of nanosized aluminium trihydrate [J]. Journal of Beijing University of Chemical Technology, 2004, 31(3): 22-26.
[8]Hayes J D, Malik A. Sol-gel chemistry-based upon-coated columns for capillary electrophoesis [J]. Journal of Chromatograph B, 1997, 695(1): 3-13.
[9]Jorand Y, Taha M, Missiaen J M, et al. Compaction and sintering behavior of sol-gel powders [J]. Journal of the European Ceramic Society, 1995, 15(5): 469-477.
[10]Sohn S, Kwon Y, Kim Y, et al. Synthesis and characterization of near-monodisperse yttria particles by homogeneous precipitation method [J]. Powder Technology, 2004, 142(2-3):136-153.
[11]Ko T, Hwang D K. Preparation of nanocrystalline lead zirconate powder by homogeneous precipitation using hydrogen peroxide and urea [J]. Materials Letters, 2003, 57(16-17): 2472-2479.
[12]Maroto J A, de las Nieves F J. Optimization of the heterocoagulation process of polymer colloids with different particle size [J]. Colloids and Surfaces A: Physicochemical and Engineering Aspects, 1995, 96(1-2): 121-133.
[13]ZHANG Ju-xian, GAO Long-qiao. Nanocomposite powders from coating with heterogeneous nucleation processing [J]. Ceramics International, 2001, 27(2): 143-147.
[14]GU Yuan. The technology and application of powder surface modification [J]. Chemical Industry and Engineering Progress, 1994(1): 33-41.
[15]LIU Guang-wen. Powder modification system with air-flow impact [J]. Chemical Industry Equipment Technology, 1995, 16(4): 47-49.
Foundation item: Project(50372047) supported by the National Natural Science Foundation of China
Received date: 2004-12-15; Accepted date: 2005-01-18
Correspondence: FENG Cai-mei; Tel: +86-27-87867824; E-mail: fljcm2002@sohu.com
(Edited by YANG Bing)