
Electrodeposition of Ni-SiC nanocomposite film
NIU Zhao-xia(牛朝霞)1, CAO Fa-he(曹发和)1, WANG Wei(王 玮)1,
ZHANG Zhao(张 昭)1, ZHANG Jian-qing(张鉴清)1, 2, CAO Chu-nan(曹楚南)1,2
1. Department of Chemistry, Zhejiang University, Hangzhou 310027, China;
2. State Key Laboratory for Corrosion and Protection, Metal Research Institute, The Chinese Academy of Science, Shenyang 110015, China
Received 20 April 2006; accepted 12 July 2006
Abstract: The point of zero charge(PZC) of SiC nanoparticles was determined by means of standard potentiometric titration method, while the influences of the main technological parameters on the microstructure of electrodeposited Ni-SiC composite film were studied and optimized. The results show that high bath pH value favors SiC nanoparticles negatively charged and high bath temperature promotes them positively charged. Under the experimental conditions, sodium dodecyl-glycol is proven to be an effective surface modification anionic surfactant for SiC nanoparticles. The results also show that the optimized Ni-SiC composite film is composed of the nanoparticles with the average grain size in the nanometer range (100 nm), and SiC nanoparticles disperse into the nickel matrix uniformly.
Key words: Ni-SiC nanocomposite film; point of zero charge; potentiometric titration; electroplating
1 Introduction
Metal matrix nanocomposite thin films, over the past years, exhibit many excellent performances, such as unique magnetic and optical properties[1-3]. Consequently, extensive research efforts with regard to nanocomposites have been done[4-7]. It is well known that deposition of electrochemical composite coatings (ECC) is not a newly developed technique and has been in continuous development since 1970s[8]. Meanwhile, compared with other techniques for nanocomposite synthesis, electroplating possesses many advantages including[9]: low cost and industrial applicability, simple operation, versatility, high production rates, few size and shape limitations, and high probability of transferring this technology to existing electroplating and electroforming industries.
Nowadays, the most investigated ECC are nickel-base nanocomposite films in spite of that the as-prepared films are defective and not integrated. In addition,a problem in conventional method is that a strong conglobation trend occurs easily among the nanoparticles due to their high surface activity[1-3].
The purpose of this paper is to solve the conglobation problem of SiC nanoparticles in the electroplating solutions. The holistic Ni-SiC nano- composite film was prepared using traditional DC (direct current) electroplating technique, and the influences of principal technological parameters on the microstructure of electrodeposited Ni-SiC nanocomposite film were ascertained.
2 Experimental
2.1 Determination of PZC based on potentiometric titration method
Potentiometric titrations[10-11] of SiC nano- particles were performed in a thermostatic beaker, the temperature of which was kept constant. 40 mL NaNO3 solution of different concentrations (0.1, 0.01 or 0.001 mol/L) containing 0.1 g SiC nanoparticles was added into the beaker and equilibrated for 1 h with continuous magnetic stirring. Following the equilibration at the desired temperature (293, 303, and (313±1) K respectively), 2 mL HNO3 was added and the suspension was further agitated for 30 min. Then, the pH value of the suspension was recorded using an Orion pH meter (model 710A) with a glass electrode. At the same time, the suspension was further titrated by the addition of standardized 0.05 mol/L NaOH solutions using a micro-burette of very fine capillary tip in increments of 0.2 mL. The suspension must equilibrate for 2 min with constant stirring after each titration, at the end of which the pH changes were less than 0.01 per minute, and the pH value of the suspension was recorded after each titration. The potentiometric titrations were performed at 293, 303, and (313±1) K respectively in 0.1, 0.01, 0.001 mol/L NaNO3 solutions. The average error between the duplicates was less than 2. The blank titrations were also carried out with similar solutions in the absence of SiC nanoparticles. During the potentiometric titrations, the N2 gas was constantly passed through the suspensions to bubble out the CO2.
The surface charge densities of SiC nanoparticles in aqueous solutions were calculated according to the following potentiometric titration relationship[10-11]:
(1)
where δ0 is the surface charge (?C?cm-2), F is the Faraday constant (C?mol-1); ca and cb are the concentrations (mol?L-3) of HNO3 and NaOH added into the suspension, respectively; m is the mass of SiC sample (g); [H+] and [OH-] are the concentrations of H+ and OH- determined from the pH of the solution after each titration, and S is the specific surface area of SiC powder [10-11].
2.2 Preparation of Ni -SiC nanocomposite film
The experimental electrolyte was prepared with AR grade reagents and twice-distilled water according to the basic composition shown in Table 1. In this study, the mean diameter of SiC nanoparticles is 50 nm, the surface-to-volume ratio is 90 m2/g, and the density is 0.05 g/cm3.
Table 1 Electroplating conditions for fabricating Ni-SiC composite film
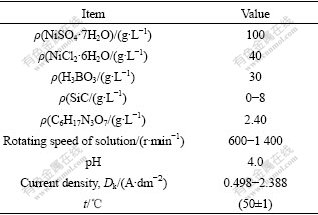
A double-electrode system consisting of a large bright platinum foil as counter electrode was employed and disc copper/zinc alloy with an area of 0.502 4 cm2 exposed used as working electrode (WE). Before the electroplating experiments, the working electrode was polished with silicon carbide papers from 400# to 800# and velvet, rinsed with twice-distilled water, washed with acetone, rinsed with twice-distilled water again and then dried in air. The temperature was controlled by thermostat water tank at (50±1) ℃. After each experi- ment, scanning electron microscope(SEM), atomic force microscope(AFM) and transmission electron microscope(TEM) were used to observe the morphologies respectively.
3 Results and discussion
3.1 Determination of surface charge density by potentiometric titration
From Figs.1-3, it can be seen that high pH value favors SiC nanoparticles negatively charged, while high bath temperature promotes them to positively charge. For the reason that the operation bath temperature and bath pH for electroplating Ni-SiC composite film in this study is (50±1)℃ and 4.0 respectively (Table 1), SiC nanoparticles under such conditions should be positively charged (Fig.3). Therefore, in order to effectively disperse SiC nanoparticles into electroplating solutions without agglomeration/conglobation, the surfaces of SiC nanoparticles should be chemically modified using anionic surfactants prior to their addition (into bath solutions).
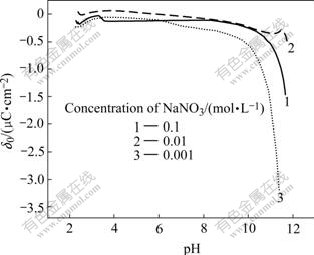
Fig.1 Variation of surface charge density (δ0) of SiC vs pH in aqueous solution containing different concentrations of NaNO3 at 20 ℃
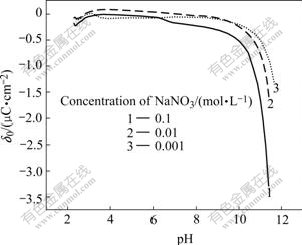
Fig.2 Variation of surface charge density (δ0) of SiC vs pH in aqueous solution containing different concentrations of NaNO3 at 30 ℃
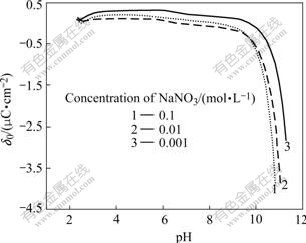
Fig.3 Variation of surface charge density (δ0) of SiC vs pH in aqueous solution containing different concentrations of NaNO3 at 40 ℃
3.2 Influences of experimental parameters on Ni-SiC composite film
Based on the above potentiometric titration experimental results, SiC nanoparticles are chemically modified using 0.1 g/L sodium dodecyl-glycol prior to their addition into basic Ni electroplating solutions (Table 1). The reason for choosing sodium dodecyl- glycol for surface modification of SiC nanoparticles is that it is a kind of anionic surfactants and is usually used as a leveling additive in solutions for metals or alloys electroplating[12-13].
According to the studies of NWOKO et al[14] and GUGLIELMI et al[15], the microstructures of traditional composite film were mainly influenced by current density and the inert particle concentration in
the bath. Meanwhile, prior to the work in this paper, a number of preliminary electroplating experiments have been carried out in our lab to determine the principal technological parameters that influence the microstructures of Ni-SiC composite films remarkably. It is found that, under the experimental conditions, the agitation speed of solutions also influences the microstructures of Ni-SiC composite films prominently. The preliminary results also clearly indicate that high bath pH value and low bath temperature are detrimental for the stabilization of electroplating system, while low pH value and high temperature are respectively responsible for low current efficiency and high energy loss and therefore are also disadvantageous. Consequently, the influences of solution agitation speed, SiC nanoparticles concentration and current density were investigated in details in the following section, as shown in Figs.4-6.
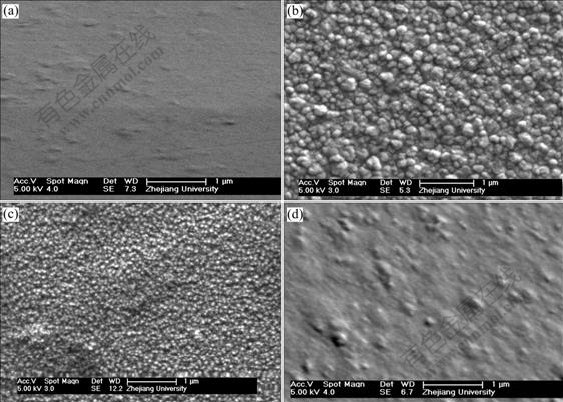
Fig.4 Influence of solution agitation speed on microstructure of Ni-SiC composite film (current: 7.5 mA, concentration of SiC: 6 g/L, bath temperature: (50±1) ℃): (a) 600 r/min; (b) 900 r/min; (c) 1 200 r/min; (d) 1 400 r/min
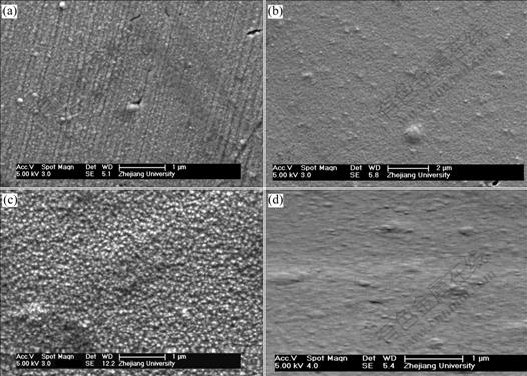
Fig.5 Influence of concentration of SiC nanoparticles on microstructure of Ni-SiC composite film(current: 7.5 mA, solution agitation speed: 1 200 r/min, bath temperature: (50±1) ℃): (a) 0 g/L; (b) 4 g/L; (c) 6 g/L; (d) 8 g/L
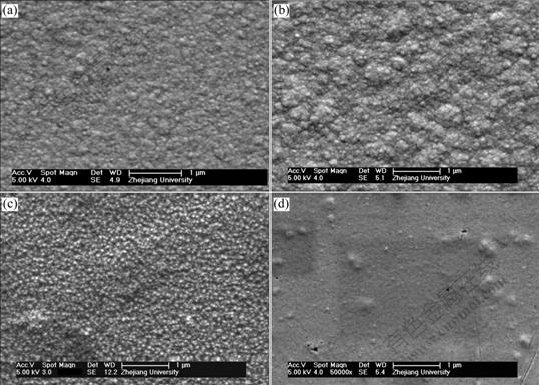
Fig.6 Influence of current on microstructure of Ni-SiC composite film (concentration of SiC: 6 g/L, solution agitation speed: 1 200 r/min, bath temperature: (50±1) ℃): (a) 2.5 mA; (b) 5 mA; (c) 7.5 mA; (d) 12 mA
Fig.4 clearly shows that too much low or too much high solution agitation speed is not better for fabricating nanocomposite film because in the traditional composite electroplating processes, there are three possible controlling factors for inert particles to be entrapped by metal matrix, i.e., exoteric agitation, electrophoresis and adsorption[14]. Accordingly, too much low agitation speed certainly decreases the adsorbed amount of SiC nanoparticles caused by mechanical effect. Meanwhile the gravitation effect will also subside the suspended SiC nanoparticles and weaken their adsorption amount onto cathode surface synchronously. The decrease of SiC inclusion into Ni matrix will certainly reduce the cathodical polarization, while makes the spatial resistance to small nickel crystallites to grow up, resulting in crystal structure of electrodeposits. The above results tally tightly with those obtained by NOWAK et al[16] who found that the addition of SiC nanoparticles into nickel bath remarkably increased the charge-transfer resistance of electroplating processes.
On the other hand, according to the theoretical model proposed by GUGLIELMI[15] for the traditional composite electroplating, the inert particles suspended in bath solutions come into metal matrix by two successive adsorption steps. In the first step the particles are loosely adsorbed on the cathode surface and are in equilibrium with the particles in suspension, while in the second step the particles are irreversibly adsorbed. Consequently, in the case of too much high agitation speed, the intensive force convection of solutions will bring away the loosely adsorbed SiC nanoparticles from the cathode surface, and results in the similar crystal films as those obtained at too much low solution agitation speed.
It is well known that the presence of SiC nanoparticle in electroplating solutions can increase the cathodical polarization and inhibit the growth of metal crystallites simultaneously[16]. Consequently, it is rational to deduce that much high concentration of SiC nanoparticles in solutions should refine the structures of electrodeposits. However, from Fig.5, it can be seen that too much high concentration of SiC nanoparticles in solutions is not better. The reason may be that much high SiC concentration will accelerate the agglomeration effect among SiC nanoparticles and their subsequent gravitational sedimentation, which will result in the decrease of the amount of the loosely adsorbed SiC nanoparticles onto cathode and of their consequent content in electrodeposits[15].
Fig.6 shows the influence of electroplating current on the microstructure of Ni-SiC composite film. It can be seen that too much high current is disadvantageous for fabricating nanocomposite. The results tally tightly with those obtained by WALTER et al[17]. The reason may be that, the first loose adsorption step is to be substantially physical but electrochemical in nature[15] and it is less sensitive to current than metal ions. Consequently high current accelerates the reduction processes of nickel metal and results in crystal structure of electrodeposits.
3.3 Characterization of optimized Ni-SiC nano- composite film
After numerous experiments, the optimized electroplating conditions for holistic Ni-SiC nanocomposite film are obtained as follows: NiSO4? 7H2O 100 g/L, NiCl2?6H2O 40 g/L, H3BO3 30 g/L, SiC 6 g/L, C6H17N3O7 2.4 g/L, sodium dodecyl-glycol 0.1 g/L, pH=4.0, Dk= 1.493 A?dm-2, t=(50±1) ℃ and rotating speed of solution 1 200 r/min.
The microstructure of the optimized Ni-SiC composite film was characterized by scanning electron microscope(SEM), atomic force microscope(AFM) and transmission electron microscope (TEM), as shown in Fig.7. It can be clearly seen that the optimized Ni-SiC composite film is composed of the nanoparticles with the average grain sizes in the nanometer range, which proves that the as-obtained Ni-SiC composite film is substantially characterized by nanostructure.
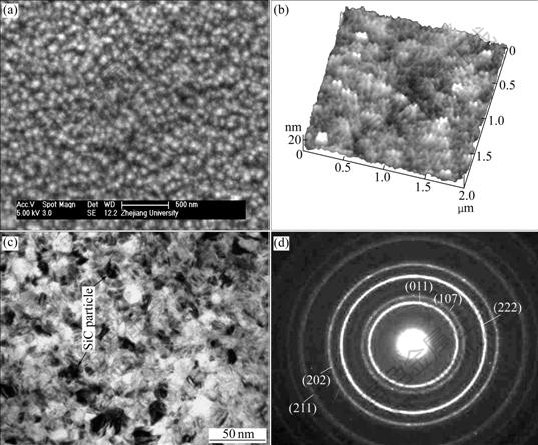
Fig.7 Microstructures of optimized Ni-SiC nanocomposite film: (a) SEM image; (b) AFM image; (c) Bright-field TEM image; (d) Electron diffraction pattern
Fig.7(c) clearly indicates that SiC nanoparticle predecessors (pointed by arrows in Fig.7(c)) are dispersed into the nickel matrix uniformly, which also proves that sodium dodecyl-glycol is an effective surface modification anionic surfactant to chemically modify SiC nanoparticles prior to their addition into solutions for fabricating Ni-SiC nanocomposite film. Meanwhile, the incorporation of the nanometric sized SiC particles into the nickel matrix can also be proved by the selected-area electron diffraction(SAED) pattern of the same sample (Fig.7(d)), where the arrow-pointed (011), (202) and (211) rings correspond to the crystal parameter of Ni, and the (107) and (222) rings correspond to the crystal parameter of SiC.
The formation of nanostructured Ni-SiC composite film can be explained based on the fact that the formation of an electrodeposited film is a competition between nucleation and crystal growth steps. The nano- SiC particles adsorbed on the cathode inhibit the growth processes of nickel crystallites due to their spatial resistance effect and increase the cathodical polarization, which consequently activates more points for nucleation, damages the preferential/sequential growth of bulk nickel (which is characterized by linear ravines or trenches[13] in Fig.5(a)) and finally results in the fine nano-structured composite film.
4 Conclusions
1) High bath pH value favors SiC nanoparticles negatively charged, while high bath temperature promotes them positively charged.
2) Sodium dodecyl- glycol is proven to be an effective surface modification anionic surfactant for SiC nanoparticles prior to their addition into solutions.
3) Ni-SiC composite film is obtained using DC electroplating technique, and the influences of principal technological parameters including solution agitation speed, concentration of SiC nanoparticles and current density on the microstructure of Ni-SiC composite film are investigated and optimized. The optimized Ni-SiC composite film is composed of the nanoparticles with the average grain sizes in the nanometer range, and SiC nanopaticles disperse into the nickel matrix uniformly.
References
[1] PODLAHA E J. Selective electrodeposition of nanoparticulates into metal matrices [J]. Nano Letters, 2001, 1(8): 413-416.
[2] STAN V, MARITZA G J V H, PAVLA K, JAN P. Different approaches to superhard coatings and nanocomposites [J]. Thin Solid Films, 2005, 476: 1-29.
[3] XU B S, WANG H D, DONG S Y, JIANG B, TU W Y. Electrodeposition nickel silica (SiO2) nano-composites coatings [J]. Electrochemistry Communications, 2005, 7: 572-575.
[4] BENEA B, BONORA P L, BORELLO A, MARTELLI S, WENGER F, PONTHOAUX P, GALLAND J. Composite electrodeposition to obtain nanostructured coatings [J]. J Electrochem Soc, 2001, 148(7): C461-C465.
[5] BENEA L, BONORA P L, BRELLO A, MARTELLI S, WENGER F, PONTHIAUX P, GALLAND J. Preparation and investigation of nanostructured SiC-nickel layers by electro- deposition [J]. Solid State Ionics, 2002, 151: 89-95.
[6] LI J, SUN Y, SUN X, QIAO J. Mechanical and corrosion-resistance performance of electrodeposited titania-nickel nanocomposite coatings [J]. Surf Coat Technol, 2005, 192: 331-335.
[7] LIN C S, HUANG K C. Codeposition and microstructure of nickel-SiC composite coating electrodeposited from sulphamate bath [J]. J Appl Electrochem, 2004, 34: 1013-1019.
[8] BENEA L, BONORA P L, BORELLO A, MARTELLI S. Wear corrosion properties of nano-structured SiC-nickel composite coatings obtained by electroplating [J]. Wear, 2002, 249: 995-1003.
[9] TJONG S C, CHEN H. Nanocrystalline materials and coatings [J]. Mater Sci Eng R, 2004, R45: 1-88.
[10] MUSTAFA S, DILARA B, NARGIS K, NAEEM A, SHAHIDA P. Surface properties of the mixed oxides of iron and silica [J]. Coll Surf A, 2002, 205: 273-282.
[11] OLSSON M, JAKOBSSON A M, ALBINSSON Y. Surface charge densities of two actinide (IV) oxides: UO2 and ThO2 [J]. J Colloid and Interface Sci, 2002, 256: 256-261.
[12] YANG Zhong-nian, ZHANG Zhao, LENG Wen-hua, LING Ke, ZHANG Jian-qing. In-situ monitoring of nickel electrodeposit structure using electrochemical noise technique [J]. Trans Nonferrous Met Soc China, 2006, 16(1): 209-216.
[13] ZHANG Z, DENG S W, ZHANG J Q. Preparation of thin solid CoNiFe films by pulse-reverse electroplating technique [J]. Bull Electrochem, 2005, 21(5): 233-239.
[14] NWOKO V O, SHREIR L L. Electron micrographic examination of electrodeposited dispersion-hardened nickel [J]. J Appl Electrochem, 1973, 3: 137-141.
[15] GUGLIELMI N. Kinetics of deposition of inert particles from electrolytic baths [J]. J Electrochem Soc, 1972, 119(8): 1009-1012.
[16] NOWAK P, SOCHA R P, KAISHEVA M, FRANSAER J, CELIS J P, STOINOV Z. Electrochemical investigation of the codeposition of SiC and SiO2 particles with nickel [J]. J Appl Electrochem, 2000, 30: 429-437.
[17] WALTER E C, ZACH M P, FAVIER F, MURRAY B J, INAZU K, HEMMINGER J C, PENNER R M. Metal nanowire arrays by electrodeposition [J]. Chem Phys Chem, 2003, 4: 131-138.
Foundation item: Project(20203015) supported by the National Natural Science Foundation of China; Project supported by the State Key Laboratory for Corrosion and Protection of China
Corresponding author: ZHANG Zhao; Tel: +86-571-87952318; E-mail: eagelzzy@zjuem.zju.edu.cn
(Edited by LI Xiang-qun)