
Formation process of composite plasma electrolytic oxidation coating containing zirconium oxides on AM50 magnesium alloy
LIU Feng, SHAN Da-yong, SONG Ying-wei, HAN En-hou
State Key Laboratory for Corrosion and Protection, Institute of Metal Research,
Chinese Academy of Sciences, Shenyang 110016, China
Received 25 September 2010; accepted 20 December 2010
Abstract: The formation processes of a composite ceramic coating on AM50 magnesium alloy prepared by plasma electrolytic oxidation (PEO) in a K2ZrF6 electrolyte solution were studied by scanning electron microscope (SEM) and energy dispersive X-ray spectroscope (EDX). Electrochemical impedance spectroscopy (EIS) tests were used to study the variation of the corrosion resistance of the coating during the PEO treatment. The results show that the coating formed on Mg alloy is mainly composed of MgO and MgF2 when the applied voltage is lower than the sparking voltage, and zirconium oxides start to be deposited on Mg substrate after the potential exceeding the sparking voltage. The corrosion resistance of the coating increases with increasing the applied voltage.
Key words: plasma electrolytic oxidation coating; zirconium oxide; MgO; corrosion resistance
1 Introduction
Magnesium alloys have been widely used in the aircraft and automobile industries[1-2]. However, the corrosion resistance of magnesium alloys is poor[3]. Surface treatments, such as chemical conversion coating and anodic oxidation, have been introduced to protect magnesium alloys from being corroded[4]. However, these treatments cannot provide sufficient protection for magnesium alloys in aggressive environments.
Based on the theory of anodic oxidation, plasma electrolytic oxidation (PEO) technique has already been introduced to protect magnesium alloys. Conventional PEO coatings on magnesium alloy are mainly composed of MgO with some other compounds, like SiO2 and MgO·Al2O3[5-7]. However, the stability of MgO in acid or neutral solution is low and it restricts the corrosion resistance of coatings. Recently, it was reported that ZrO2 could be deposited on magnesium alloys by PEO in the electrolyte solutions containing K2ZrF6[8-11]. These PEO coatings are mainly composed of ZrO2, MgF2 and a little of MgO. As a result, these PEO coatings have superior corrosion resistance because ZrO2 and MgF2 have higher stability than MgO in neutral or acid solution.
Usually, PEO coatings can be prepared by the methods of constant current and constant voltage, and the current electrolytic solutions for obtaining PEO coatings containing zirconium oxides are only workable by constant voltage method. However, there are some problems when a PEO coating is prepared by the constant voltage method. One problem is that a large power supply is necessary because the peak current is much higher when the sample has a greater dimension. Another problem is that much heat is produced during the treatment, and it increases the solution temperature. As a result, the stability of the solution would decrease, and some K2ZrF6 would even be deposited and the solution would become ineffective. In addition, local corrosion of the magnesium alloy at the initial stage of PEO treatment is another problem. In this work, a novel K2ZrF6 electrolytic solution was employed and a PEO coating containing zirconium oxides was prepared on a magnesium alloy in this solution by the constant current method.
The formation processes of this kind of coating are different from those of conventional PEO coating on magnesium alloy. It includes the decomposition of K2ZrF6 and the deposition of zirconium oxides. The formation processes have a great influence on the properties of the coating. Thus, the formation processes of PEO coating in this electrolyte were studied here. Moreover, the variation of coating morphologies and corrosion resistance during the PEO treatment was studied.
2 Experimental
The substrate material used for this investigation was die-cast AM50 magnesium alloy with dimensions of 50 mm×25 mm×4 mm. Samples were ground using 1000 grit silicon carbide papers, then cleaned using distilled water and acetone, and dried in the cold air.
AM50 Mg alloy sample was used as anode, and a stainless steel cylinder container with size of d 140 mm×300 mm was used as cathode. K2ZrF6, KF, NH4H2PO4, C6H5O7K3 and methenamine were dissolved using distilled water, and then put in the cylinder container as electrolyte. The concentrations of these compositions in electrolyte solution are listed in Table 1. The stainless container with electrolytic was put in a water-cooled bath to keep the temperature of the electrolyte solution lower than 45 °C during the PEO treatment. A 20 kW-DC power supply was employed. The PEO coating was prepared in this solution at a current density of 2 A/dm2, and the plus frequency and duty ratio were 500 Hz and 50%, respectively. In order to study the formation processes of the coating, the samples were oxidized to the given potentials, and then the samples were washed using distilled water, and dried in the cold air.
Table 1 Concentration of compositions in electrolyte solution (g/L)

A camera was used to record the states of sample during PEO treatment. SEM was used to observe the surface and cross-sectional morphologies of the coating. Electrochemical tests conducted in 3.5% NaCl (mass fraction) solution were used to study the variation of corrosion resistance of the coating during PEO treatment. Samples were mounted by ceresin wax with surface of 1 cm2 exposed. An initial retard of 600 s was set to obtain a stable testing system after each sample was immerged in 3.5% NaCl solution, and then the electrochemical impendence spectroscopy (EIS) test was measured. A conventional three-electrode cell system (reference electrode: SCE) was used in the electrochemical tests. The EIS tests were measured at open circuit potential using a model 5210 lock-in amplifier coupled with potentiostat model 273. The scan frequency range was from 100 kHz to 10 mHz with an amplitude of 5 mV.
3 Results and discussion
3.1 Formation processes of PEO coating
Figure 1 shows the voltage—time response for the PEO treatment in the electrolyte solution. Applied voltage increased rapidly before sparking (about 130 V), and it did not oscillate in this region. This indicated that a thin dielectric film formed on magnesium alloy, and this dielectric film was compact and it could inhibit the local corrosion of magnesium alloy. When the applied voltage reached sparking voltage, numerous flickered sparks covered the surface of sample, as shown in Fig.2. Number of sparks decreased with the increase of applied voltage, but the dimension and lifetime of sparks increased. The dimension of the sparks did not change greatly when the applied voltage was higher than 410 V. Then, sparks with brighter color and bigger dimension appeared on the sample when the applied voltage reached 435V, which was termed as “arcing”. Thus, the applied voltage should be lower than 435 V since these sparks had broken effects on the structure of the coating[12].
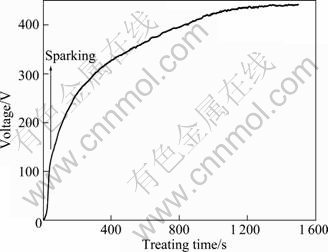
Fig.1 Variation of voltage with time during PEO treatment
3.2 Surface morphology
Figure 3 shows the surface morphologies of samples after being oxidized to various voltages. A thin film with network structure formed on the surface of the sample when the voltage reached 95 V, as shown in Fig.3(a). Local corrosion spots could not be found on the sample surface. Figure 4(a) shows that this thin film is composed of elements Mg, O, Al and F analyzed by EDX. Thus, the film formed on Mg alloy before sparking was mainly composed of MgO and MgF2. Surface of the sample presented typical PEO structure when the voltage reached 150 V (Fig.3(b)). The film on the sample was composed of elements Mg, Al, F, O, Zr and P, as shown in Fig.4(b). It can be concluded from the variation of the composition of the film that the sparks promote the deposition of zirconium oxides on the sample surface, and zirconium oxides start to be deposited on Mg substrate after the potential exceeding sparking voltage. The dimension of the pores in the coating increased with increasing the voltage when it was lower than 420 V. It is well known that pores in the coating are the traces of the sparks, and the dimension of the pores in coating related to the state of the sparks during PEO treatment.
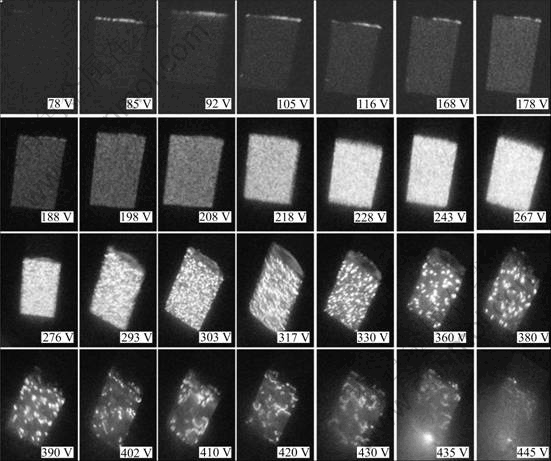
Fig.2 States of sparks on sample during PEO treatment
Figure 5 shows the backscattered scanning electron (BSEM) morphologies of the cross-sectioned PEO coating after being oxidized at different voltages. The coating had typical PEO coating structural characteristics, defects like pores and cracks existed in the coating. Thickness of the coating was not uniform and the average thickness of the coating was about 5 μm when the voltage reached 250 V. There was crack even running though the coating and reached the interface of coating and substrate, as marked by arrow in Fig.5(a). Thickness of the coating increased with increasing the applied voltage, and the average thickness of the coating was about 10 μm when the applied potential reached 360 V (Fig.5(b)). There still were some cracks running though the coating as marked by arrows. Thickness of the coating did not change greatly when potential reached 420 V and it was about 13 μm, as shown in Fig.5(c), and there were no cracks running though the coating. The coating was uniform and about 20 μm in thickness when the applied potential reached 430 V, as shown in Fig.5(d).
3.3 Variation of corrosion resistance of coating during PEO treatment
Figure 6 shows the EIS plots of the coated samples after being oxidized at different applied voltages. It could be seen that the Nyquist plots (Fig.6(a)) contained two capacitive loops and one inductive loop when the voltages were lower than 420 V. The inductive loop in low frequency disappeared when the applied voltage reached 430 V. The appearance of the inductive loop indicated that the corrosive medium had already induced the corrosion of substrate. From the observation of micrographs of cross-sectioned PEO coating (Fig.5), the coating was not thick enough to prevent the penetration of the corrosive medium through the coating defects when the potentials were lower than 430 V.
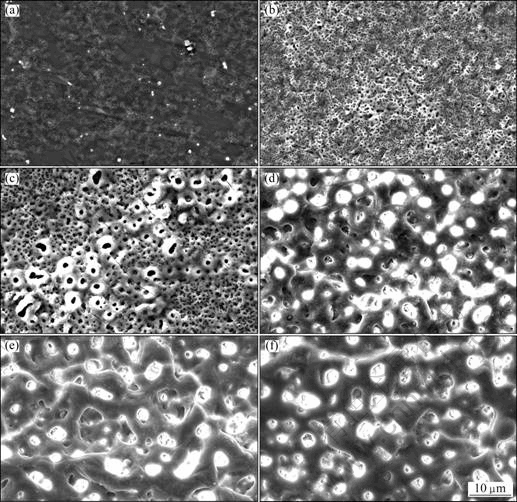
Fig.3 Morphologies of samples after being oxidized at different voltages during PEO treatment: (a) 95 V; (b) 150 V; (c) 190 V; (d) 360 V; (e) 420 V; (f) 430 V
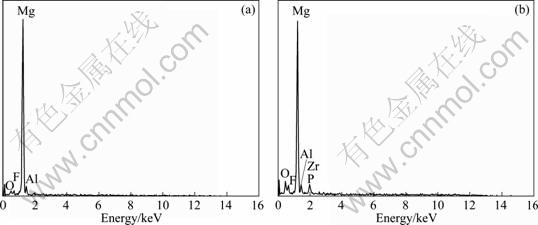
Fig.4 EDX spectra of samples after being oxidized at different voltages during PEO treatment: (a) 95 V; (b) 150 V
The value of the impedance magnitude (|Z|) in high frequency (HF) range (102–105 Hz) and medium frequency (MF) range (100–102 Hz) represented the characteristics of outer porous layer and inner dense layer of the PEO coating, respectively[7]. In Bobe plots (Fig.6(b)), the value of |Z| for the coated sample in high frequency (HF) range (102–105 Hz) increased about one order of magnitude when the applied voltage increased from 250 V to 360 V. This indicated that the corrosion resistance of outer porous layer increased greatly in this voltage range. The value of |Z| in HF slowly increased with the increase of applied voltage after the applied voltage exceeding 360 V. The impedance magnitude (|Z|) of the coated sample in low frequency range (100-10-2 Hz) dramatically increased in the voltage range from 360 to 430 V. This indicated that the corrosion resistance of the inner dense layer increased greatly in this voltage range. The impedance |Z| was higher than 106 Ω·cm2 when the applied voltage reached 430 V.
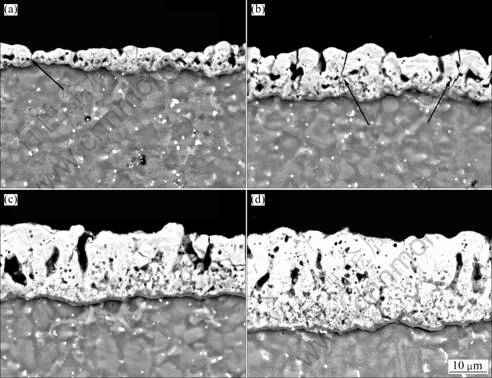
Fig.5 Backscattered scanning electron (BSEM) micrographs of cross-sectioned PEO coating after being oxidized at different voltages: (a) 250 V; (b) 360 V; (c) 420 V; (d) 430 V
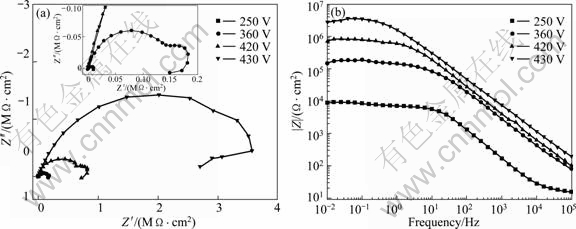
Fig.6 EIS plots of coated samples after being oxidized to different applied voltages measured in 3.5% NaCl solution: (a) Nyquist plots; (b) Bobe plots
4 Conclusions
1) A novel K2ZrF6 electrolytic solution was employed and the PEO coating containing zirconium oxides could be prepared in this solution by constant current.
2) The film formed on Mg alloy before sparking is composed of elements Mg, O, Al and F, mainly in the form of MgO and MgF2. Sparks promote the deposition of zirconium oxides on the sample surface, and zirconium oxides start to be deposited on Mg substrate after the voltage potential exceeding sparking voltage (about 130 V).
3) Thickness of the coating increases with increasing the applied voltage, and it is about 20 μm in thickness when the applied potential reaches 430 V. The corrosion resistance of the outer porous layer increases greatly when the applied voltage increases from 250 to 360 V, and the corrosion resistance of the inner dense layer increases greatly when the voltage exceeds 360 V. The impedance |Z| is higher than 106 Ω·cm2 when the applied voltage reaches 430 V.
References
[1] COLE G S, SHERMAN A M. Lightweight materials for automotive applications [J]. Materials Characterization, 1995, 35 (1): 3-9.
[2] IMMARIGEON J P, HOLT R T, KOUL A K, ZHAO L, WALLACE W, BEDDOES J C. Lightweight materials for aircraft applications [J]. Materials Characterization, 1995, 35 (1): 41-67.
[3] SONG G, ATRENS A, STJOHN D, NAIRN J. The electrochemical corrosion of pure magnesium in 1N NaCl [J]. Corrosion Science, 1997, 39(5): 855-875.
[4] GRAY J E, LUAN B. Protective coatings on magnesium and its alloys-A critical review [J]. Journal of Alloys and Compounds, 2002, 336(1-2): 88-113.
[5] CAI Q Z, WANG L S, WEI B K, LIU Q X. Electrochemical performance of microarc oxidation films formed on AZ91D magnesium alloy in silicate and phosphate electrolytes [J]. SurfaceandCoatings Technology, 2006, 200(12-13): 3727-3733.
[6] ARRABAL R, MATYKINA E, HASHIMOTO T, SKELDON P, THOMPSON G E. Characterization of AC PEO coatings on magnesium alloys [J]. SurfaceandCoatings Technology, 2009, 203(16): 2207-2220.
[7] DUAN H P, YAN C W, WANG F H. Effect of electrolyte additives on performance of plasma electrolytic oxidation films formed on magnesium alloy AZ91D [J]. Electrochimica Acta, 2007, 52: 3785-3793.
[8] YAO Z P, GAO H H, JIANG Z H, WANG F P. Structure and properties of ZrO2 ceramic coatings on AZ91D Mg alloy by plasma electrolytic oxidation [J]. Journal of the American Ceramic Society, 2008, 91(2): 555-558.
[9] LIANG J, BALA SRINIVASAN P, BLAWERT C, DIETZEL W. Comparison of electrochemical corrosion behaviour of MgO and ZrO2coatings on AM50 magnesium alloy formed by plasma electrolytic oxidation [J]. Corrosion Science, 2009, 51(10): 2483-2492.
[10] MU W Y, HAN Y. Characterization and properties of the MgF2/ZrO2 composite coatings on magnesium prepared by micro-arc oxidation [J]. Surface and Coatings Technology, 2008, 202(17): 4278-4284.
[11] HAN Y, SONG J F. Novel Mg2Zr5O12/Mg2Zr5O12–ZrO2–MgF2 gradient layer coating on magnesium formed by microarc oxidation [J]. Journal of the American Ceramic Society, 2009, 92(8): 1813-1816.
[12] VERDIER S, BOINET M, MAXIMOVITCH S, DALARD F. Formation, structure and composition of anodic films on AM60 magnesium alloy obtained by DC plasma anodizing [J]. Corrosion Science, 2005, 47: 1429-1444.
AM50镁合金表面含氧化锆的
微弧氧化复合涂层的形成过程
刘 锋, 单大勇, 宋影伟, 韩恩厚
中国科学院 金属研究所 金属腐蚀与防护国家重点实验室,沈阳 110016
摘 要:采用扫描电镜(SEM)和电子衍射能谱(EDX)研究在含K2ZrF6 的溶液中AM50镁合金表面复合微弧体氧化涂层的形成过程。采用电化学阻抗谱(EIS)研究在微弧体氧化制备膜层过程中膜层耐腐蚀性能的变化。结果表明:当电压小于起弧电压时,合金表面膜层的主要成分为MgO和MgF2;当施加电压超过起弧电压时,锆氧化物开始在合金表面沉积,且膜层的耐腐蚀性随着电压的升高而提高。
关键词:微弧氧化膜;锆氧化物;MgO;耐腐蚀性
(Edited by LI Xiang-qun)
Foundation item: Project (2007CB613705) supported by the National Basic Research Program of China; Project (50901082) supported by the National Natural Science Foundation of China
Corresponding author: SHAN Da-yong; Tel: +86-24-23893115; Fax: +86-24-23894149; E-mail: dyshan@imr.ac.cn
DOI: 10.1016/S1003-6326(11)60805-4