
Numerical simulation and its application of rheological forming of titanium alloy vane disk
YU Min(余 敏)1,2, LUO Ying-she(罗迎社)1, PENG Xiang-hua(彭相华)3, QIN Yin-hui(覃银辉) 1,2
1. Institute of Rheological Mechanics and Material Engineering, Central South University of Forestry and Technology, Changsha 410004, China;
2. Institute of Fundamental Mechanics and Material Engineering, Xiangtan University,
Xiangtan 411105, China;
3. College of Information Engineering, Xiangtan University, Xiangtan 411105, China
Received 10 April 2006; accepted 25 April 2006
Abstract: The hot rheological forming method was proposed to form the second titanium alloy vane disk. The hot rheological forming process of the TC11 titanium vane disk under a certain temperature and different strain rates was investigated by using the bulk forming software of DEFORM 3D. A series of results including temperature field, equivalent strain distribution, load-stroke curve and rheology procedure were obtained by this finite element method. The rheological forming characteristics were well realized and the forming parameters were determined. The results and analysis show that with decreasing strain rate, the metal flow more equably and the filling of the vane shape is also better. Moreover, the mechanical properties and microstructures of the products produced by this new technique are improved evidently compared with that produced by traditional method.
Key words: TC11 titanium alloy; vane disk; hot rheological forming; numerical simulation; stain rate
1 Introduction
Metal rheological forming is a new developing method of metal processing based on metal plastic forming and super-plastic forming. It focuses on considering the influence of rate-sensitivity, large deformation, temperature sensitivity and crystal boundary on metal forming. Actually, metal forming process is a procedure of flow and deformation under many factors, such as load, temperature, deformation history and time, which can also be called as rheological forming [1-5]. Deforming body, namely, the rheological forming material should be considered an elasto-visco- plastic material and furthermore it can be regarded as a visco-plastic material when elasticity can be ignored in large deformation. Considering the visco-plasticity of material, parts with complex shape and bad machining property can be produced by this rheological forming method while creating certain conditions, such as heating, adding press or changing strain rate for material [6]. There are many factors that can influence hot rheological forming, mainly including temperature, friction coefficients, forming velocity, and so on. In order to reveal the effect of these factors concretely, a recommending method to perform numerical simulation should be taken before actual manufacture. Titanium disks, like compressor disk, vane disk, etc used to be manufactured by impression die forging and hammer forging. However, the cutting property of titanium is bad, so the successful rate of finished products is extreme low and lots of valuable materials are wasted. LUO et al[7, 8] have proposed to manufacture aluminum alloy missile shell and TC11 titanium alloy compressor disk by using the rheological forming method and the manufacturing practice proved that the internal microstructure has been improved and the mechanical properties of the products have also been enhanced awfully.
In this paper, the hot rheological forming process analysis for TC11 titanium alloy vane disk under a certain temperature (920 ℃) and three different strain rates, is carried out by applying the numerical simulation with simplified dies based on DEFORM 3D. The influence of different velocity on the forming of vane disk is investigated and the influent law is also obtained, which provides us with the theoretical guidance and scientific basis for actual manufacture. Besides, the microstructure and the mechanical properties are inspected for the hot rheological forming parts.
2 Basic theories
2.1 Mechanics model
Metal billet is always considered an elasto-visco- plastic material. Elastic deformation is little and material is non-compressed in hot rheological forming, so the rheological forming of TC11 titanium alloy in mold can be described by visco-plastic flow. The yield function F is
(1)
where σij is the stress tensor; εij is the strain tensor;
is the strain rate tensor;
is temperature. When T is a constant, Eqn.(1) can be simplified as
(2)
where
is the second invariant of the deviator stress; K is a parameter concerned with material hardening. The primary distinction between Eqn.(2) and the static yield function of isotropic hardening material rests with the containing of strain rate tensor
.
For TC11 titanium alloy, the visco-plastic constitutive equation, which is educed from Perzyna’ research method, is imported. It neglects the elastic deformation and introduces the bulk non-compressed term:
(3)
where Sij is the deviator stress;
is the viscoplastic strain rate tensor component and
is its corresponding equivalent viscoplastic strain rate tensor component;
denotes the equivalent stress and η is the generalized viscosity[7].
2.2 Variation principle of rigid viscoplastic non-compressed material
The rigid viscoplastic finite element ignores the elastic deformation and imports the bulk non-compressed term. The penalty function method and Lagrange method are introduced to deal with the bulk non-compressed term. According to Markov variation principle, the total energy dissipating function Φ can obtain its minimal value by true solution, and here the velocity of which is regarded as the initial velocity field.
(4)
The variation principle designates an approach to solve metal forming problem, namely, the true solution can be obtained by finding the velocity field which satisfies the minimum value term [9].
3 Simulation setting
In order to perform the numerical simulation of hot rheological process conveniently, we simplify the models of billet and dies, and have the following hypotheses for simulation [10]:
1) Billet and dies are modeled based on UG NX3, and the whole process is simulated by DEFORM 3D;
2) The temperature in simulation is set as a constant with 920 ℃;
3) The heat transfer between billet and dies in simulation is not considered.
4) Dies are regarded as rigid bodies and will not be damaged in rheological forming.
5) Shear model with lubricant is adopted for friction, and the friction coefficient between billet and dies is specialized as 0.3, which approaches the true situation.
6) Regions where large deformation will occur are meshed by MESH WINDOW, and the rest is meshed using absolute meshing with the minimal element of 1 and mesh ratio of 2. The billet is divided to 102 822 tetrahedron elements. Then, the mesh ratio is changed to 3, which can be used for systematic remeshing while mesh aberrance occurs severely.
7) The stress and strain field is inherited during simulation.
The three–dimensional models of billet and dies are shown in Fig.1. The rheological forming under three strain rates (0.008 s-1, 0.005 s-1, 0.001 s-1) are simulated by importing the models to DEFORM 3D and according to the setting terms above.
4 Simulation results and discussion
4.1 Temperature field
Fig.2 shows the temperature distributing cloud under different strain rates (0.008, 0.005 and 0.001 s-1) and an initial temperature of 920 ℃ at the end of rheological forming process. We can see from the picture that the temperature of the whole billet rises to higher than 920 ℃ due to plastic deformation work and friction work during rheological forming progress. The ranges of temperature are separately 923-938, 922-931 and 920-924 ℃ and the corresponding differences in temperature are 15, 9 and 4℃ severally. The ascending magnitude of temperature is distinct owing to different strain rates, which is 18, 10 and 4℃, respectively. Moreover, rapid forming velocity leads to rapid defor-
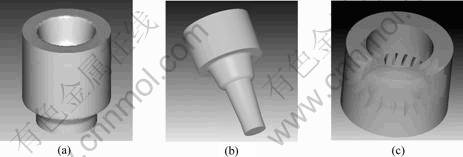
Fig.1 Three-dimensional geometry modeling of billet and dies: (a) Billet; (b) Punch; (c) Concave die
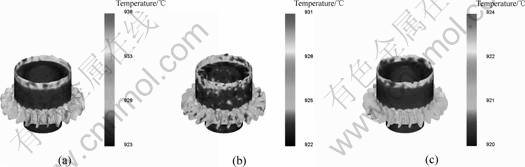
Fig.2 Temperature distribution of workpiece: (a)
; (b)
; (c) 
mation. Therefore, the quantity of heat cannot release in short time, which results in larger scope of temperature ascending. Meanwhile, the difference in inner temperature differs due to the distinct forming velocity, and as the forming velocity becomes slow, the difference in temperature becomes little. As the difference of inner temperature increases, the asymmetry of deformation and interior quality also increases, which should be reduced or avoided.
According to the temperature field in numerical simulation, we find that the temperature of billet increases obviously and the difference in temperature is large. Therefore, it is important to control temperature in actual manufacture. The interior quality of parts can be improved by doing so. Otherwise it will make workpiece rejected because of over-heating.
4.2 Equivalent strain field
Fig.3 gives the cloud and isoclines of equivalent strain distribution at the end of rheological forming process under the same temperature and different strain rates. We can easily see that the deformation of billet is nonreversible and asymmetrical. The equivalent strain value near the entrance of little-diameter of cavity die achieves the maximum and that of the other region is relative little. From Fig.3, it can be seen that the maximum of equivalent strain under three different strain rates is distinct. The maximum differences of equivalent strain in diverse regions are 2.586, 1.797, 1.127, respectively. It is obvious that the deformation under low
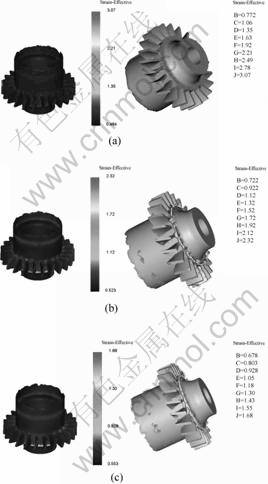
Fig.3 Equivalent strain distribution of workpiece: (a)
s-1; (b)
s-1; (c)
s-1
strain rate distributes equably and the symmetrical inner structure is also easy to acquire. Therefore, reducing strain rate is an effective way to ensure the accurate dimension of products.
4.3 Load-stroke curves
Fig.4 shows the load-stroke curves of rheological forming process under a certain temperature and three strain rates. Comparing Fig.4(a), (b) and (c), we can see that the deformation resistance forces of dies are sensitive with strain rates. The deformation resistance force becomes larger as the forming velocity increases. The rheological forming process of metal performs in a certain speed. The rheological process performs deficiently in a larger forming velocity. Forming under a lower strain rate can not only reduce the elastic deformation of the die and enhance the dimensional precision of product, which will benefit the well proportioned deformation of parts, but also improve the suffering of force for dies and increase the die security. Hence, the lower tonnage of press can be used to manufacture the secondary vane disk in practice with adopting a low strain rate.
The load-stroke curve can be used for estimating the formation load and choosing the tonnage of press. Here, the simulation result of deformation load is 3 732 043 N, which is reduced by near 28.2% compared with that of strain rate of 0.008 s-1. So we can use the tonnage of press of 400 t in actual manufacture.
4.4 Grid scheme of rheological forming process
From the above analysis, it can be seen that forming under a low strain rate can attain satisfying effect. Thereby, we choose the best simulation scheme with strain rate of 0.001 s-1 and initial temperature of 920 ℃. Its formation effect and flowing characteristic are analyzed by applying this simulation scheme. From Fig.5, we can clearly see the whole rheological forming process of TC11 titanium alloy billet in mold. The results show that the secondary vane disk can attain technology requirement by using hot rheological forming method. Metal fills it well and the workpiece is basically shaped.
5 Properties testing of hot rheological forming products
The physical-chemistry analysis and mechanical properties testing are carried out for rheological forming products, which are manufactured by adopting the above scheme. From Fig.6, it is obvious that the inner structures of hot rheological products are well proportioned and belong to isoaxes α+β transformation structure. The microstructure photos under high multiple accepting criterion, so the products satisfy the accord
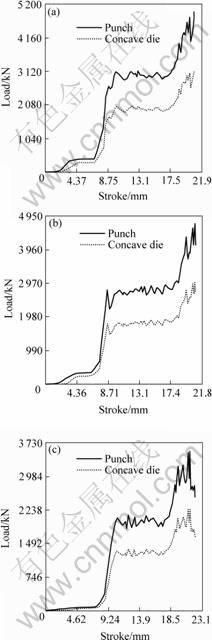
Fig.4 Curves of load vs stroke: (a)
s-1; (b)
s-1; (c)
s-1
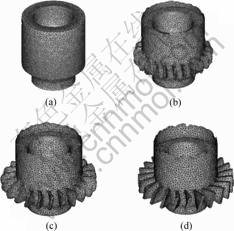
Fig.5 Deformed meshes of rheological forming process
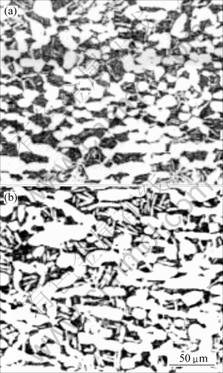
Fig.6 Microstructures of products under high multiple: (a) Sample 1#; (b) Sample 2#
with the eligible pictures in checking and requirement of technology qualification.
The testing data of mechanical properties under room temperature and high temperature are shown in Tables 1 and 2, respectively. It is easy to find that the
Table 1 Mechanical properties of secondary titanium alloy vane disk under room-temperature
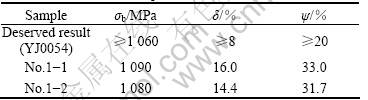
Table 2 Mechanical properties of secondary titanium alloy vane disk under high temperature (500 ℃)
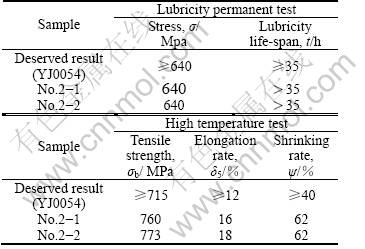
mechanical properties are improved and accord with the requirement of YJ0252 technology qualification.
6 Conclusions
1) The simulation of hot rheological forming process of the secondary vane disk and the analysis of temperature field, strain field and load–stroke curve provide the basis for practical manufacture. Consequently, the testing materials and costs are saved, and the technology circle is shortened.
2) TC11 titanium is sensitive with strain rate. Therefore, forming under a low strain rate makes formation equably, improving dimensional precision and reducing the deformation resistance and the tonnage of press.
References
[1] LUO Y S, LUO K W, HU Y G. Theory and practice on metal’s rheological forming [J]. Forging Technology, 1997, 22(4): 11-13.
[2] LUO Y S, LUO Z H. Mechanism inquiry and practice analysis on metal’s rheological forming [J]. Hot Working Technology, 1997, 126: 11-13.
[3] LUO Y S, GUO X G, MEI Y F, HU Y G. Dislocation evolution with rheological forming of metal [J]. Trans Nonferrous Met Soc China, 1999, 9(3): 623-628.
[4] LUO Ying-she. The survey in researching and prospect on metal processing rheology [A]. Proc of XШth international congress of rheology [C]. Cambridge, 2000. 406-408.
[5] LUO Ying-she, LIU Fei, YANG Liu, et al. The numerical simulation and mechanics analysis for deep-draw thermal-rheological forming of one Ti alloy rectification internal hood[J]. Key Engineering Material, 2004, 274-276: 721-726.
[6] LUO Y S. The thermal analyses of hover-plane Titanium alloy axial flow impeller thermal-rheological forming [J]. Nat Sci of Xiangtan Uni,1989, 11(1): 153-161.
[7] LI S Y, LUO Y S, XU X H, ZHOU J L. The numerical simulation and its application on the rheological forming of the TC11 titanium alloy disk [J]. Hot Working Technology, 2001, 1: 22-25.
[8] HU Y G, LUO Y S, LI S W, et al. Numerical simulation of rheological warm extrusion molding of missile shell [J]. Forging Technology, 2000, 1:10-12.
[9] LIU J S, CHEN H Q, GUO X X. Finite Simulation Technology of Metal Plastic Machining and Its Application [M]. Beijing: Metallurgical Industry Press. 2003. (in Chinese)
[10] WANG G C, ZHAO G Q, XIE S S, et al. Numerical and experimental study on new cole precision forging technique of spur gears [J]. Trans Nonferrous Met Soc China, 2003, 13(4): 798-802.
(Edited by YUAN Sai-qian)
Foundation item: Project(02103) support by the Education Ministry of China; Project(02A008) supported by the Education Department of Hunan Province and Central South University of Foresty & Technology
Corresponding author: LUO Ying-she; E-mail: lys0258@sina.com