
New extrusion process of Mg alloy automobile wheels
WANG Qiang(王 强)1, ZHANG Zhi-min(张治民)2 , ZHANG Xing(张 星)2, LI Guo-jun(李国俊)1
1. College of Materials Science and Engineering, North University of China, Taiyuan 030051, China
2. Engineering Research Center of Magnesium-base Material Processing Technology, Ministry of Education,North University of China, Taiyuan 030051, China
Received 23 September 2009; accepted 30 January 2010
Abstract: The recent research and development of forged magnesium road wheel were reviewed. Methods of flow-forming, spin forging of manufacturing a forged magnesium alloy wheel were introduced. A new extrusion method was investigated especially. Extrusion from hollow billet was proposed in order to enhance the strength of spoke portion and reduce the maximum forming load. By means of the developed technique, the one-piece Mg wheels were produced successfully by extrusion from AZ80+ alloy. At the same time, the existing problems on the research and development of forged magnesium road wheel were analyzed. The impact testing, radial fatigue testing and bending fatigue testing results show that AZ80+ wheel can meet application requirement in automobile industry.
Key words: magnesium alloy; road wheel; extrusion; flow-forming; spin forging
1 Introduction
Magnesium alloy is promising structural light metal because of its low densities, good recyclical potential and abundant resources, which is expected to become a next-generation material[1-4]. This material is received special attention due to the renewed interest in energy conservation. Its use is increasing in automobile industries as a replacement for aluminum and steel. Magnesium alloy road wheels have to be considered in particular due to their beneficial effect such as safety, comfort and energy saving. As a safety-related component, the essential factors in wheel applications are the fatigue strength and the impact strength. At the same time, we should also take account of other requirements such as corrosion resistance and cost.
In order to have a widespread use of magnesium alloy wheels, casting and forging processes have been adopted for wheel manufacturing. In the case of the magnesium alloys, the manufacture of the entire wheel only by the casting (low pressure die casting, squeeze casting, gravity casting)[5-8] results in insufficient strength of, for example, a rim portion which carries a tire, as well as casting quality(porosity, inclusions) often does not meet the requirements.
Forging is an alternative production technology for Mg alloy parts with high strength requirements[9]. The products manufactured by this process are characterized by fine-grained microstructure without pores and improved mechanical properties compared with casting Mg parts[10-12]. For magnesium road wheel forging, methods of flow-forming and spin forging had been investigated[13-14]. But heavy-duty press equipment is used and the fatigue strength cannot meet application requirement[13, 15]. To enhance the fatigue strength and reduce the forming load, a new extrusion process for magnesium alloy wheels was introduced and investigated especially in this work. The one-piece AZ80+ alloy wheel was extruded successfully by means of the developed technique.
2 Forging technique used for wheel manufacturing
2.1 Forging and flow-forming process
The technique of forged Mg alloy wheels requires the following two process steps: forging the wheel disc blank and flow-forming the rim[13]. The billets are made by continuous casting process, and are homogenized before the forming process. Prior to the forging and flow-forming process, the billets are heated up to suitable temperature to provide the required formability.
The forging consists of three steps using hydraulic press with different pressing powers. The first forging operation with a high degree of reduction provides a wheel blank. The final shape of the wheel disc is mainly achieved by the second forging. The forming process is completed by subsequent deburring operation as the last step. The flow-forming operation itself runs in three steps: splitting up the forged flange, flow-forming the rim and calibrating the rim contour, as shown in Fig.1. The flow-forming device consists of mandrel and tailstock plate to be used for locking the wheel disc. Three forming rollers are positioned approximately in 120? orientations: roller 1 splits up the flange, roller 2 and 3 flow-form the rim including calibration of the final rim contour.
The ZK30 alloy prototype wheel has been manufactured by using flow-forming technique. Its mass is 6.8 kg representing 35% mass saving than forged aluminum wheel. High strength can be achieved in the rim especially in flow direction due to the high deformation induced by flow forming process. However, the properties and influence of flow direction on the material properties are reduced due to lower degree of
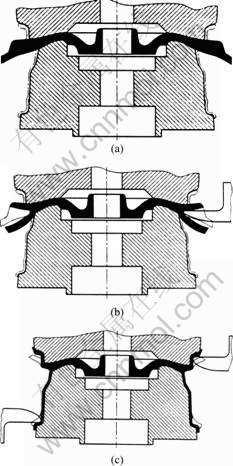
Fig.1 Schematic diagram of flow-forming process: (a) Process starting position; (b) Splitting up flange; (c) Flow-forming rim
reduction of the wheel disc section. Rotary fatigue test shows durability lifetime (84 000 cycles under 3 000 N?m test load) is 8.5% that of the series aluminum wheel. Hence, it is necessary to thicken the wheel sections for achieving the required lifetime. Thus the actual mass saving potential is reduced to 10%-15% in regard to aluminum wheel based on FEA analysis.
2.2 Forging and spin forging process
The technique of forged Mg alloy wheels consists of the three process steps[14]: forging wheel blank, spin forging rim and roll processing rim edge portion, as shown in Fig.2. AZ80 magnesium alloy casting was prepared by casting and was subsequently forged to provide a wheel blank of a shape substantially identical with that of the eventually manufactured wheel.
An automotive wheel is obtained by forging from the wheel blank using forging machine with an upper die and a lower die. The average crystalline particle size of the material is reduced. Then the wheel is subjected to a solution treatment and an artificial treatment. Upon completion of T6 treatment, spin forging is carried out. While the wheel is rotated together with the mandrel and the press member, a roll is pressed against a rim of the
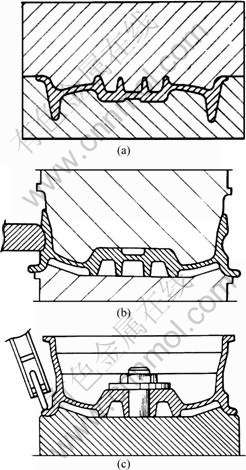
Fig.2 Schematic diagram of spin forging process: (a) Blank forging; (b) Spin forging; (c) Roll processing
wheel, so that the rim may be finished by a spinning treatment. Finally, the wheel is subjected to a roll processing. A roll is pressed against an edge portion of the rim while the rotary platform together with the wheel is rotated, micronizing crystalline particle to improve the resistance to corrosion of the edge portion.
The physical properties of the wheel using spin forging technique are considerably improved by the synergistic effect of the crystalline particles and the T6 treatment, especially the strength of a rim portion is enhanced. The technical parameters such as temperatures swaging rate and average crystalline particle size are optimized. But, the related reports on fatigue strength, mass and application instance have not been seen yet.
3 Extrusion technique used for wheel manufacturing
3.1 Extrusion from hollow billet
The maximum load was chosen as the extrusion load during extrusion process. A new concept of hollow billet was proposed and a method of extrusion from hollow billet was developed[16]. The schematic diagram of extrusion from hollow billet is shown in Fig.3.

Fig.3 Schematic diagram of extrusion from hollow billet
To investigate the press force during extrusion from hollow billet, the finite element simulation was conducted using an implicit FE code MSC/Autoforge. The data on AZ80 alloy flow stress as function of strain, strain rate and temperature established based on compression experiment have to be introduced into the FE package. Fig.4 shows the calculational force— displacement curves during extrusion from hollow billet at different r1=d3/d1, where d1 is outside diameter of hollow billet; d2 is inner diameter of hollow billet; and d3 is diameter of mandrel. The results show that forming force is decreased enormously during extrusion from hollow billet, because of the decrease of contact area and
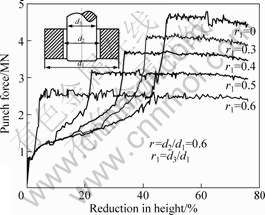
Fig.4 Calculational force—displacement curves
average positive stress on interface. At the same time, the hole is formed directly and cutting process is reduced for the parts with center hole such as wheel by extrusion from hollow billet.
3.2 Extrusion process of wheels
The extrusion technique of wheels[17] has been developed for magnesium alloy wheel manufacturing, as shown in Fig.5. A can is backward extruded from hollow

Fig.5 Schematic diagram of extrusion process: (a) Extruding can; (b) Forging front lip; (c) Expanding rim and back lip
billet made by upsetting and punching from as-cast alloy. Upon completion of extrusion, the front lip is forged from can extruded. The rim contour and back lip are finally achieved by expanding. The metal may flow inwards and outwards simultaneously during forging the front lip, which may make the billet deformation at relatively low forging force and the die cavity filled sufficiently. At the same time, the degree of reduction of the wheel disc section is enhanced. High strength can be achieved in the wheel disc section due to the high deformation.
3.3 Experimental results
The AZ80+ alloy was produced by continuous casting method for the wheel. The billets were machined in order to remove the effect of the surface layer of the ingot and homogenized (385 ℃, 12 h) before deformation. Extrusion was conducted under isothermal conditions in which the die temperatures were varied depending on the billet temperature. The billet was heated to a temperature within 320 to 380 ℃ during forming process. The oil-hydraulic press of capacity 12.5 MN was employed and the average forming speed of a ram was 10 mm/s. A graphite coating was used to lubricate billet and punch surface.
The one-piece magnesium alloy wheels are produced according to the present technique, as shown in Fig.6. The forming force was decreased by extrusion from hollow billet. The (13×10) J and (14×6) J wheels were extruded under 12.5 MN oil-hydraulic press. The technology and dies designed have many other advantages such as better filling for flange, high production precision, low surface roughness and convenient mould unloading for near-net shape forming. The manufacture costs are reduced due to using limited capacity of press equipment and less forming process.
The mechanical properties are remarkably improved for AZ80+ alloy wheel extruded in the both rim and disc section. The ultimate tensile strength is 300-320 MPa and the elongation is above 10%. For example, the mass of (14×6) J wheel is 5.2 kg representing 28% mass saving of aluminum wheel. The impact testing, radial fatigue testing and bending fatigue testing results in Table 1 show that the magnesium wheels can meet application requirement in automobile industry.
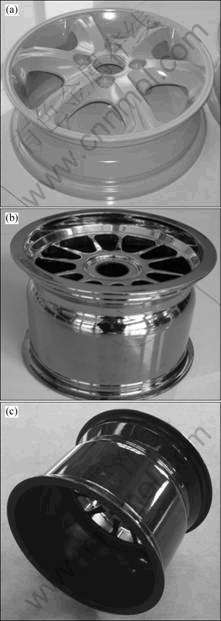
Fig.6 AZ80+ Mg alloy wheels extruded: (a) (14×6) J; (b) (13×10) J; (c) (13×8) J
4 Conclusions
1) Methods of flow-forming and spin forging of manufacturing a forged magnesium alloy wheel are introduced and the existing problems are analyzed. The
Table 1 Testing results of wheels

fatigue strength, impact strength, corrosion resistance and cost are main factors in the magnesium road wheel application.
2) Extrusion from hollow billet developed for Mg alloy wheel manufacturing can not only enhance strength in the wheel disc section due to the high deformation, but also reduce the maximum forming load because of decreasing of contact area and average stress on interface.
3) The one-piece AZ80+ alloy wheel is extruded successfully for near-net shape forming by means of the developed extrusion technique. The testing results show that it can meet application requirement in automobile industry.
References
[1] Asm International, Magnesium and magnesium alloy [M]. OH: Metal Park, 1999.
[2] GRAY J E, LUAN B. Protective coatings on magnesium and its alloys—A critical review [J]. Journal of Alloys and Compounds, 2002, 336: 88-113.
[3] MA Chun-jiang, LIU Man-ping, WU Guo-hua, DING Wen-jiang, ZHU Yan-ping. Tensile properties of extruded ZK60/RE alloys [J]. Materials Science and Engineering A, 2003, 349: 207-212.
[4] JARDIM P M, SOL?RZANO G, VANDER SANDE J B. Second phase formation in melt-spun Mg-Ca-Zn alloys [J]. Materials Science and Engineering A, 2004, 381: 196-205.
[5] WANG Jian-hong, LONG Si-yuan, CAO Han-xue. Casting technology for wheels of automobile and motor bike [J]. Special Casting & Nonferrous Alloys, 2004(5): 21-23. (in Chinese)
[6] PENG Ying-hong, WANG Ying-chun, LI Da-yong. Numerical simulation of low pressure die casting of magnesium alloy wheel [J]. China Mechanical Engineering, 2006, 17(19): 2034-2037. (in Chinese)
[7] WU Zeng-chen, LONG Si-yuan, XU Shao-yong. A new squeeze casting process for magnesium wheels production [J]. Foundry, 2005, 54(9): 878-880. (in Chinese)
[8] CAI Suo-qi, CUI Er-xin. Gravity casting of Mg alloy automobile wheels [J]. Foundry Technology, 2001(5): 8-10. (in Chinese)
[9] BEHRENS B A, SCHMIDT I. Improving the properties of forged magnesium parts by optimized process parameters [J]. Journal of Materials Processing Technology, 2007, 187/188: 761-765.
[10] CISAR L, YOSHIDA Y, KAMADO S, KOJIMA Y, WATANABE F. Microstructures and tensile properties of ECAE-processed and forged AZ31 magnesium alloy [J]. Materials Transactions, 2003, 44: 476-483.
[11] DOEGE E, DRO¨DER K. Sheet metal forming of magnesium wrought alloys—Formability and process technology [J]. Journal of Materials Processing Technology, 2001, 115: 14-19.
[12] LIM S C V, YONG M S. Plane-strain forging of wrought magnesium alloy AZ31 [J]. Journal of Materials Processing Technology, 2006, 171: 393-398.
[13] SCHEMME K, LOWAK H. Manufacturing of light-weight wheels by forging and flow-forming [C]//KUNZE H D. Competitive Advantages by Near-Net-Shape Manufacturing, DGM- Informationsgesellschaft mbH, Frankfurt/Main, 1997: 115-120.
[14] FUJITA M, YAMAMOTO Y, SAKATE N, HIRABARA S. Method of making an article of manufacture made of a magnesium alloy. US5902424 [P].1999-11-05.
[15] KIM Y H, RYOU T K, CHOI H J, HWANG B B. An analysis of the forging processes for 6061 aluminum-alloy wheels [J]. Journal of Materials Processing Technology, 2002, 123: 270-276.
[16] WANG Qiang, ZHANG Zhi-min, ZHANG Xing, YU Jian-min. Precision forging technologies for magnesium alloy bracket and wheel [J]. Trans Nonferrous Met Soc China, 2008, 18(s1): s205-s208.
[17] ZHANG Zhi-min, WANG Qiang. A method and device of forming with decreasing force for magnesium alloy wheel. ZL 200610012829.9[P]. 2009-04-08.
(Edited by ZHAO Jun)
Foundation item: Project(50735005) supported by the National Natural Science Foundation of China
Corresponding author: WANG Qiang; Tel: +86-351-3921398, +86-13834166948; Fax: +86-351-3921778; E-mail: ncustwangq@nuc.edu.cn