.
Structural macrokinetics of synthesizing ZnFe2O4 by mechanical ball milling
ZHAO Zhong-wei(赵中伟)1, OUYANG Kingsam(欧阳全胜)1, WANG Ming(王 明)1, 2
1. School of Metallurgical Science and Engineering, Central South University, Changsha 410083, China;
2. Changsha Engineering and Research Institute of Nonferrous Metallurgy, Changsha 410011, China
Received 16 April 2010; accepted 24 May 201
Abstract: Powder mixtures of Fe2O3 and ZnO were milled in a high-energy planetary ball mill to synthesize ZnFe2O4 and X-ray powder diffractometry was used to obtain the relative content of phases, crystallite size and microstrain of both Fe2O3 and ZnFe2O4. The lattice constants of Fe2O3 were obtained by cell refinement method. The macrokinetics and the structure evolution of matters were studied and the results show that the dynamics process of mechanochemical synthesis of ZnFe2O4 fits Avrami-Erofe’ev model and is controlled by a nucleation-growth mechanism, and the structural macrokinetics theory in combustion synthesis research area could be used to describe the kinetic process as well.
Key words: mechanochemistry; ball milling; combustion synthesis; structural macrokinetics; kinetics model; ZnFe2O4
1 Introduction
Mechanochemistry is the subject that deals with the chemical and physicochemical changes of substances induced by mechanical force. Since PETERS[1] clearly put forward that mechanochemical reaction was induced by mechanical force, mechanochemistry has been widely used in many fields, such as materials engineering, extractive metallurgy, crystal engineering, coal industry, building industry, agriculture, pharmacy and waste treatment[2-6]. The science base for mechanochemistry, however, appears to be limited[6-9], especially the study of kinetics. Hence, it lacks a set of systematic and applicable theory to describe the mechanochemical processing.
During the process of mechanochemical reaction, in a very short time and a tiny space, the reactants may emit electrons and ions to form plasma area and begin chemical reaction under the action of high-speed impacts. Once the action is over, the systematic energy decreases rapidly and then gradually slows down, where the rest energy is stored in solid in the form of plastic deformation[10-11] and the structure of resultant is further transformed. As mechanical treatment can produce nonequilibrium intermediate phase[6, 12], mechanochemical reaction is often accompanied with the formation of intermediate amorphous product, which will result in the fact that the structure formation of final crystal product lags behind the chemical transformation. Therefore, in order to better describe the kinetic process of mechanochemical reaction, besides considering the classical chemical reaction kinetics, the kinetics of structural changes should be employed as well.
Structural macrokinetics[13-15], put forward by scholars of the former Soviet Union, aims to describe the chemical reaction processes, particularly the essence of combustion synthesis that is one kind of physico- chemical processes far from equilibrium state. Structural macrokinetics can be used to explain the basic rules of chemical change and structure evolution of material in the combustion synthesis process.
Structural macrokinetics can be defined by the following two formulas[13]:
Classical macrokinetics=chemical kinetics+heat and mass transfer theory;
Structural macrokinetics=classical macrokinetics+ kinetics of structural transformations.
In fact, combustion synthesis maintains the reaction process by energy generated by its own exothermal reaction, while mechanochemical reaction through the energy continuously provided by mechanical milling. If we consider each collision as a micro-area combustion synthesis, the whole ball-milling process can be regarded as the numerous continuous “ignition” of reactants.
Mechanochemical synthesis and combustion synthesis belong to different research areas, but there are lots of similarities between them, especially the fact that the structure formation of resultant in both processes all falls behind the chemical transformation. So, it is feasible that the structural macrokinetics theory can be used to research the mechanochemical reaction process. The theory and research methods of structural macrokinetics were firstly put forward to apply in mechanochemical research areas by the authors, aiming to enrich the kinetic theory of mechanochemical reaction. Taking for example in this work, the mechanochemical synthesis of ZnFe2O4 by high-energy ball milling the mixture of Fe2O3 and ZnO powders, and the structural macrokinetics were studied.
2 Experimental
2.1 Experimental methods
The Fe2O3 (A.R.) and ZnO (A.R.) powders were used as the starting materials for mechanical milling in a planetary ball mill (QM-1SP2-CL, 0.75 kW, Nanjing University Instrument Plant). About 20 g of starting mixtures (molar ratio of Fe2O3 to ZnO=1:1) were loaded together with 400 g steel balls in a sealed steel container before ball milling. The ball-to-powder mass ratio of 20:1 was chosen and the milling speed was 500 r/min. The milling process was interrupted after selected time to take out small amounts of powders for analysis, till reaction finished.
2.2 Analysis methods
The milled samples were determined by a Rigaku X-ray diffractometer (Dmax/2550VB+, Japan) using Cu Kα radiation. The voltage was 40 kV and the tube current was 300 mA. MDI Jade 5.0 was used as analytical software for X-ray diffractometry (XRD). The relative fraction of materials was calculated by K value method (also known as RIR method)[16]. Considering that grain refinement and microstrain could simultaneously happen, the crystallite size and microstrain of milled powders were calculated by Williamson-Hall method, and the crystallite size of starting materials by Scherrer equation[17]. The lattice constants of substance were obtained by cell refinement method using MDI Jade 5.0 software.
3 Results and discussion
3.1 Macrokinetics analysis
Fig.1 shows the XRD patterns of the samples milled for different time. As shown in Fig.1, Fe2O3 and ZnO mixed powders were complete crystal respectively before ball milling. But after milling for 5 h, the main peaks of Fe2O3 and ZnO were obviously weakened and broadened. These suggest that mechanical force decreases the grain size and crystallinity of reactant. Furthermore, the decrease of ZnO peaks was more obvious, compared with that of Fe2O3 peaks. Two reasons related with the influence of high-energy ball milling might account for this phenomenon: one is the amorphization of ZnO and the other is the diffusion of ZnO into Fe2O3 phase. JIANG et al[18] reported that there was no amorphous ZnO after milling for 120 h. So, the latter reason seemed more likely. Furthermore, the diffraction peak at 29.84? (2θ) which was indexed by ZnFe2O4(220) crystal plane indicated that ZnFe2O4 formed by solid-state reaction of Fe2O3 and ZnO at low temperature with mechanical treatment. After milling for 10 h, ZnO peaks almost disappeared, but many peaks of Fe2O3 remained. Considering that the molar ratio of Fe2O3 to ZnO was 1:1, it further explained that ZnO diffused into Fe2O3 crystal lattice during ball-milling process. With the increase of ball-milling time, the peaks of ZnO and ZnFe2O4 continuously became weak and strong, respectively. When the reaction time reached 40 h, the diffraction peaks of two reactants completely disappeared, with only ZnFe2O4 left.
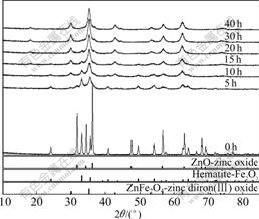
Fig.1 XRD patterns of samples milled for different time
The relative mole fraction of each phase as a function of milling time is shown in Fig.2. Taking into account of the diffusion of ZnO into Fe2O3 crystal lattice during ball-milling process, the relative mole fraction of ZnO was adjusted according to stoichiometric relationship.
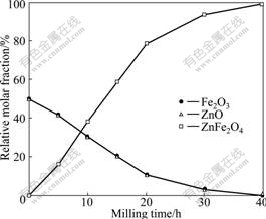
Fig.2 Relative mole fraction of phases as function of milling time
The conversion degree of the reaction as a function of milling time could be obtained from Fig.2, as presented in Fig.3.
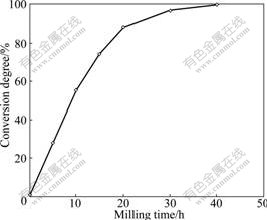
Fig.3 Conversion degree of reaction as function of milling time
Chemical reaction rate usually abides the following rate formula:
(1)
where
is the reaction rate; k is the rate constant; α is the conversion degree;and f(α) is the function of α.
The integral formula of Eq.(1) is given by
(2)
Supposing
the equation is
obtained as follows:
F(α)=kt+c (3)
Solid-state reaction models commonly include diffusion-control model, nucleation-growth model, boundary-reaction model and chemical reaction model. The kinetic model functions usually employed for the solid-state reactions are collected in Table 1, with different reaction mechanisms corresponding to different kinetic equations F(α).
The data in Fig.3 are fitted to those kinetic models. And the Avrami-Erofe’ev equation (m=1.5) which belongs to nucleation-growth model has the highest fitting accuracy, as represented by
m=1.5 (4)
The fitting result is shown in Fig.4, and the fitted kinetic equation is given as
(5)
The fact that the relative fraction of each phase changes in accordance with S-shaped curve (see Fig.2) could be interpreted as follows: crystal nucleus form in different positions and then grow up[20]. Under the action of the high-energy mechanical force, the reactant powder reaches a high degree of mixing, the grains are highly refined and then a large number of defects such as vacancies and dislocations are generated, which greatly reduces the diffusion distance and weakens the diffusion resistance among ions. Hence, the diffusion rate of this process could be considered to be very fast. In addition, the instantaneous high temperature and pressure caused by high-energy ball milling provide favorable conditions for chemical reaction, which significantly improves the reactivity of reactants and enhances the chemical reaction process. Thus, it is considered that chemical reaction is not the controlling step of the whole process. From Fig.4, it could be concluded that the reaction process of ZnFe2O4 synthesized by mechanical ball milling in Fe2O3 and ZnO mixed powder could well fit Avrami-Erofe’ev kinetic model. It is suggested that the solid conversion degree of this reaction process is controlled by the crystal nucleus formation and its growth rate.
Table 1 Kinetic model functions usually employed for solid-state reactions[19]
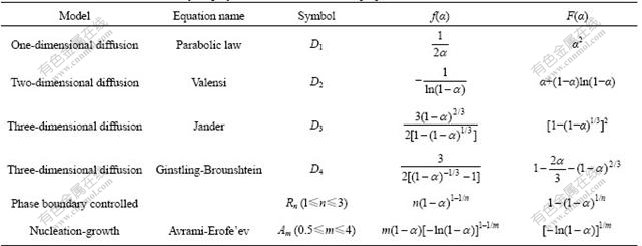
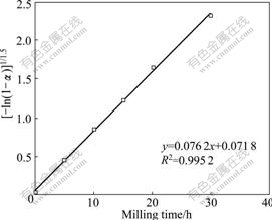
Fig.4 Fitting results of reaction process by Avrami-Erofe’ev equation (m=1.5)
3.2 Structure evolution of phases
3.2.1 Change of crystallite size, microstrain and lattice constants for Fe2O3
Fig.5 shows that the crystallite size, microstrain and lattice constants of Fe2O3 vary with ball-milling time. It can be seen that in the first 5 h, the crystallite size decreases rapidly, and then the decrease rate slows down. This indicates that the decrease of Fe2O3 crystallite size caused by milling mainly occurs in the initial period of ball milling.
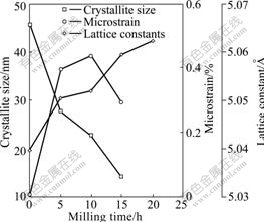
Fig.5 Change of crystallite size, microstrain and lattice constants for Fe2O3 as function of milling time
It is proved that with the increase of milling time, Fe2O3 lattice constants gradually increase, showing that under the action of mechanical force, ZnO enters Fe2O3 lattice and forms solid solution, which leads to Fe2O3 lattice expansion and lattice constants increase.
With the increase of milling time, the microstrain of Fe2O3 firstly increases gradually, and then decreases. In the early milling, the increase of the internal dislocation and other defects of Fe2O3 grain causes the increase of stress, but the starting powder has better toughness, so the stress could not be well released. Besides, along with ZnO entering into the lattice of Fe2O3, the lattice distortion occurs, which further increases the microstrain. After 10 h, the microstrain begins to decrease since the grain of remained Fe2O3 has become very small. With the ball-milling time extending and the dislocation and other defects density reducing, the stress stored in the interior of the powder particles releases continuously to cause microstrain dropping down.
3.2.2 Change of crystallite size and microstrain for ZnFe2O4
The changes of the crystallite size and microstrain for ZnFe2O4 with the milling time are shown in Fig.6. It can be seen that with the increase of milling time, the crystallite size and microstrain of resultant ZnFe2O4 constantly grow up. High-energy ball milling reduces the crystallite size of resultant, leading to producing dislocation and other defects and then forming the active site of reaction where ZnFe2O4 firstly nucleates, and then grows up continuously. Meanwhile, the microstrain caused by mechanical force also increases during the milling process.
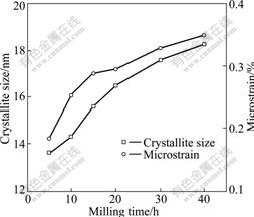
Fig.6 Changes of crystallite size and microstrain for ZnFe2O4 as function of milling time
4 Conclusions
1) The synthesizing process of ZnFe2O4 by high-energy ball milling the mixture of Fe2O3 and ZnO is controlled by the nucleation-growth mechanism, and the reaction process fits Avrami-Erofe’ev kinetic model. The kinetic equation is
.
2) The structure evolution of phases is presented regularly in different stages, and the reaction process of mechanochemistry can be better understood by analyzing the structure evolution of reactant and resultant.
3) The theory of structure macrokinetics could well describe the kinetics of ZnFe2O4 synthesis by mechanical milling, which has great significance to improving theoretical basis of mechanochemistry.
References
[1] PETERS K. Mechanochemische reaktionen [M]. Frankfurt: Legend Press, 1962: 78-79.
[2] BAL?? P, DUTKOV? E. Fine milling in applied mechanochemistry [J]. Minerals Engineering, 2009, 22: 681-694.
[3] ZYRYANOV V V. Mechanochemical synthesis of complex oxides [J]. Russian Chemical Reviews, 2008, 77(2): 105-135.
[4] WIECZOREK-CIUROWA K, GAMRAT K. Some aspects of mechanochemical reactions [J]. Materials Science-Poland, 2007, 25(1): 219-232.
[5] GUO Xiu-ying, XIANG Dong, DUAN Guang-hong, MOU Peng. A review of mechanochemistry applications in waste management [J]. Waste Management, 2010, 30: 4-10.
[6] IVANOV E, SURYANARAYANA C. Materials and process design through mechanochemical routes [J]. Journal of Materials Synthesis and Processing, 2000, 8: 235-244.
[7] KON?PKA M, TURANSK? R, REICHERT J, FUCHS H, MARX D, ?TICH I. Mechanochemistry and thermochemistry are different: Stress-induced strengthening of chemical bonds [J]. Physical Review Letters, 2008, 100: 115503.
[8] ROSEN B M, PERCEC V. Mechanochemistry: A reaction to stress [J]. Nature, 2007, 446: 381-382.
[9] BOLDYREV V V. Mechanochemistry and mechanical activation of solids [J]. Russian Chemical Reviews, 2006, 75(3): 177-189.
[10] CHEN Zhen-hua, CHEN Ding. Mechanical alloying and solid-liquid reaction milling [M]. Beijing: Chemical Industry Press, 2006: 439-440. (in Chinese)
[11] MILOSEVIC S, RISTIC M M. Thermodynamics and kinetics of the mechanical activation of materials [J]. Science of Sintering, 1998, 30: 29-38.
[12] BOLDYREV V V, TK??OV? K. Mechanochemistry of solids: Past, present, and prospects [J]. Journal of Materials Synthesis and Processing, 2000, 8: 121-132.
[13] MERZHANOV A G, ROGACHEV A S. Structural macrokinetics of SHS processes [J]. Pure & Appl Chem, 1992, 64(7): 941-953.
[14] WANG Han-li, HUANG Wei-xiu. Materials synthesis of SHS [J]. Journal of Hubei University of Education, 2008, 25(2): 74-77. (in Chinese)
[15] YIN Sheng. Combustion synthesis [M]. Beijing: Metallurgical Industry Press, 2004: 1-142. (in Chinese)
[16] LIAO Li-bing, LI Guo-wu. X-ray diffraction method and application [M]. Beijing: Geological Press, 2008: 72-79. (in Chinese)
[17] POURGHAHRAMANI P, FORSSBERG E. Microstructure characterization of mechanically activated hematite using XRD line broadening [J]. Int J Miner Process, 2006, 79: 106-119.
[18] JIANG Ji-sen, GAO Lian, GUO Jing-kun, YANG Xie-long. Preparation of nanocrystalline Zn ferrite by high energy ball milling [J]. Chinese Journal of Materials Research, 1999, 13(2): 142-146. (in Chinese)
[19] TANAKA H. Thermal analysis and kinetics of solid state reactions [J]. Thermochimica Acta, 1995, 267: 29-44.
[20] SOHN H Y, WADSWORTH M E. Rate processes of extractive metallurgy [M]. ZHENG Di-ji transl. Beijing: Metallurgical Industry Press, 1984: 262. (in Chinese)
Foundation item: Project(50434010) supported by the National Natural Science Foundation of China
Corresponding author: ZHAO Zhong-wei; Tel: +86-731-88830476, E-mail: zhaozw@mail.csu.edu.cn
DOI: 10.1016/S1003-6326(09)60267-3
(Edited by YUAN Sai-qian)