
Evaluation of sliding wear behavior of graphite particle-containing magnesium alloy composites
QI Qing-ju(祁庆琚)
Technology Center, Baoshan Iron and Steel Company Ltd, Shanghai 201900, China
Received 28 November 2005; accepted 1 April 2006
Abstract: The influence of graphite particle content on the friction and wear characteristics of AZ91 magnesium alloy matrix composite was studied. The results show that the wear resistances of graphite-containing composite are much better than those of the matrix under the test conditions. The anti-wear ability of magnesium alloy composite is improved substantially with the increase of the graphite content from 5% to 20%, and both wear mass loss and coefficient of friction are decreased to low level. Different wear mechanisms operate at different sliding stages. A continuous black lubricating film forms progressively on the worn surface along sliding, which effectively limits the direct interaction between the composite tribosurface and the counterpart, and also remarkably delays the transition from mild wear to severe wear for magnesium alloy composite.
Key words: magnesium alloy; composite; graphite particle; friction; wear
1 Introduction
More and more magnesium alloy products have been used in automobile and aerospace industries due to their low density, high specific strength and specific stiffness, good damping characteristic, excellent machineability and castability, etc[1-6]. At present, the most commonly used magnesium alloy is AZ91 alloy. Wear is a serious problem in many engineering applications such as bearing, moving parts, engine parts. Although it is only a surface phenomenon it can completely undermine the mechanical function of engineering parts. It can cause structural failure directly, so reduce the fine tolerances and destroy the surface finish.
Despite of the growing interest in magnesium alloys, very few data exist on their friction and wear behavior [7]. In recent years, considerable work has been done on graphite particle reinforced metal matrix composites which exhibit low friction, low wear rate, and excellent anti-seizing properties. In this viewpoint, an attempt is made to prepare AZ91 magnesium alloy matrix composites with various graphite particle (Grp) contents and their dry sliding wear behavior in a range of normal loads is evaluated. The matrix alloy AZ91 has also been subjected to identical test for comparison. The wear mechanism has been examined.
2 Experimental
AZ91 alloy having the chemical composition given in Table 1 was chosen as the base matrix alloy in the present study. Graphite particles with an average size of 76-88 μm were used. The addition amounts of Grp are 5%, 10%, 15%, 20%, respectively. 8% Al2O3 short fibers (8-12 μm in diameter, 300-700 μm in length) were added into composites in order to enhance the strength of the specimens. Composite samples were prepared using squeezing casting method. Graphite particles and Al2O3 short fibers were fabricated into a preform with a certain strength firstly. The preform and the die were preheated to 450 ℃ and 300 ℃ respectively, then the preform was put into the die. AZ91 magnesium alloy was melted at 680 ℃ before pouring into the die. After pouring, a pressure of 55 MPa was applied to the liquid alloy and held for 60 s[8]. The liquid alloy was thus infiltrated into the preform in the die and solidified under pressure before the casting was ejected.
Wear tests were carried out using a pin-on-disc configuration in a MM-2000 wear test machine. In this system, the test sample (d 6 mm×12 mm) was clamped in the holder and held vertically against the rotating disc (70 mm in diameter and 10 mm in thickness). The disc was made of 5CrNiMo steel with hardness HRC of 55. The whole experiments were conducted under dry friction conditions at 25 ℃. The speed of the disc employed was 0.628 m/s. The range of loads was 10-200 N. The surface of the wear test samples was polished with 1000# SiC papers until the surface roughness Ra reached 0.3 μm. The disc and specimens were cleaned with acetone to remove any possible traces of grease and other surface contaminants. The wear results were taken from mass losses measured before and after the sliding tests by using an analytical balance with the accuracy of ±0.1 mg. Friction coefficients(μ) were calculated by dividing the mean friction force recorded during each experiment by the applied normal force. Worn surfaces and debris were examined under a scanning electron microscope(SEM) equipped with an energy dispersive X-ray spectrometer (EDS).
Table 1 Chemical compositions of AZ91 alloy (%)

3 Results and discussion
3.1 Microstructure
Optical microstructures of Mg matrix composites are shown in Fig.1. Optical microscopy investigations show a uniform distribution of Grp and Al2O3 fibers in the white Mg alloy matrix. Graphite particles exhibit in black unregular flake or strip and Al2O3 fibers in gray round or needle-like shape. Reinforcements remain well bonded to the matrix and no obvious casting defects are found.
3.2 Hardness and tensile properties
Hardness and tensile properties of the composites are given in Figs.2 and 3, respectively. It can be seen form Fig.2 that hardness of the composite with low Grp content (5%) reaches the maximum owing to the existence of hard Al2O3 fiber phase whose hardness is much higher than that of the matrix, and it diminishes progressively with an increase in the number of soft Grp phase. On the other hand, graphite particles, as soft phase, may segment in the matrix, leading to stress concentration. Hence, cracks nucleate due to the stress propagation during tensile test and then fractures occur. More Grp content will generate more severe segmenting effect on the matrix and severe stress concentration can be formed[9]. Therefore, ultimate tensile strength and elongation of the composites tend to decrease with increase of Grp content, as illustrated in Fig.3.
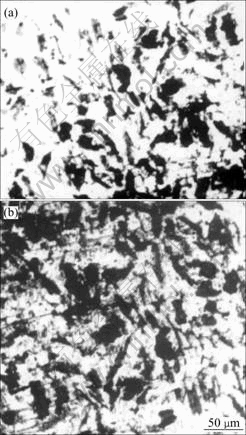
Fig.1 Microstructures of magnesium alloy matrix composites: (a) 5%Grp; (b) 15%Grp
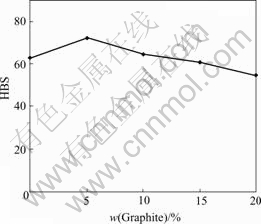
Fig.2 Hardness of composites
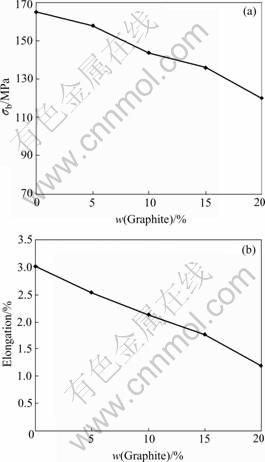
Fig.3 Tensile properties of composites: (a) Ultimate tensile strength; (b) Elongation
3.3 Wear characteristics
The wear behavior of composites containing different contents of graphite particles has been determined and compared with that observed in the base alloy. Fig.4 is the graph representing the wear mass loss of the composites as well as the base alloy specimens as a function of the applied load. It can be seen that the wear mass loss of both the unreinforced alloy and the composite specimen increases with the increase of the applied load. It may be noted that the composites possess significantly lower wear rates than the base alloy. The wear mass loss of each composite specimen reduces with the increase in graphite content. A feature common to the wear curves is that the mass loss of composites is very little under low loads (10-20 N), which may be attributed to the existence of Al2O3 fibers. Thereafter, apparent changes on curves take place with the rise in Grp content. The wear mass loss for the composites containing 5% and 10% Grp increases monotonically with increasing normal loads. However, the curves become steady in the load range of 80-160 N for 15% Grp composite and 60-160 N for 20%Grp composite, respectively, suggesting that loading capacity of the composites is increased greatly. Under higher normal load (>160 N), the wear mass loss increases remarkably. It is also clearly evident from Fig.4 that there exists a sudden increase in the wear mass loss of both composites and base alloy. However, the transition loads for the composites are much higher than that observed for the base alloy, and also the transition load increases with the increase in graphite particle content.
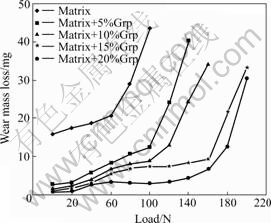
Fig.4 Relation between wear mass loss and load
Fig.5 shows the variation of the friction coefficient of the composites normalized with respect to that of the base alloy as a function of applied load against the hardened steel under stable wear process. It can be seen that the friction coefficients of composites are much lower than those of the matrix alloy. The graphite content presents significant effect on the friction coefficient of the specimens and the friction coefficients reduce with increasing Grp content. It is also observed from the curves that the friction coefficient gets a little increase under low loads, and it diminishes progressively with increasing applied load, appearing to approach a lower steady value after reaching a certain load.
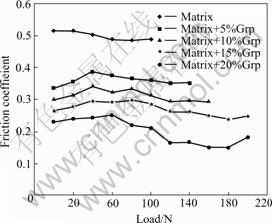
Fig.5 Relation between friction coefficient and load
It can be obtained that the wear rate of the specimens shows different wear behaviors, indicating that different wear mechanisms operate within sliding process under the investigation. The scanning electron microscopy(SEM) micrographs of a typical worn surface of the 15% Grp-containing composite are presented in Fig.6. Similar micrographs are also generated for the other compositions as well. For brevity and convenience, the micrographs of only 15% Grp composites at all the loads have been presented. However, the explanation holds good agreement for the other Grp content composites as well.
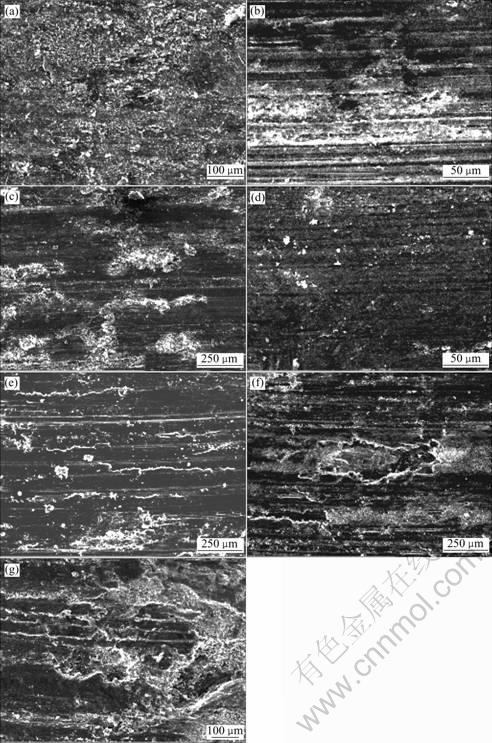
Fig.6 Worm surface morphologies of 15% graphite particle reinforced composite under different loads: (a) 10 N; (b) 40 N; (c) 60 N; (d) 100 N; (e) 160 N; (f) 160 N; (g) 200 N
It can be seen from the results acquired that at lower loads, comparatively low wear rates exist in the regime of mild wear. At the normal load of 10 N, the pin surface was subjected to light ploughing and no obvious grooves can be found. The wear debris are very fine and small in size as shown in Fig.7(a), which gives rise to a relatively low wear mass loss. In this sliding process under low load conditions, Al2O3 reinforcement phase has an excellent load-bearing capacity to withstand stress without plastic deformation or fracture, which may hinder the subsurface flow and improve the anti-adhesion ability. It is well established by investigators[10] that the wear rate and surface damage can be minimized if the plastic deformation of the material at the contact interface is prevented. Besides, the hardness and wear resistance of the reinforcement phase are markedly high, thus the reinforcement phase has grinding and micro- scoring effect on the counterpart disc, leading to the generation of iron debris. The iron debris are mechanically mixed with the pin material at the sliding interface and are oxidized abruptly at elevated temperatures during sliding. Most of them are deposited on the surface of the pin and tamped into a hard transferring layer, protecting the pin surface effectively in sliding process. Hence, the wear rate of the composites decreases on the whole, which can be proved from the investigation on the wear behavior of the composite. This kind of transferring layer will not form on the wear surface of magnesium base alloy because of the absence of hard reinforcing phase. It is evident that the transferring layer formed on the worn surface of composite pins is substantially harder than the bulk material[11-13]. The friction coefficient is a composite function of the extent, to which the energy is dissipated in the pin and the mating disc. The presence of the very hard surface layer should increase the average shear strength substantially, which needs higher friction force to deform, resulting in high friction coefficient as experimentally observed (Fig.5). The EDS analysis for Fig.6(a), as listed in Table 2 , exhibits the presence of the elements of O, Mg, Fe, etc., implying that the surface layer consists of the oxide mixture of these elements. The wear mechanisms operating within the mild wear regime are oxidational wear and micro-plowing wear.
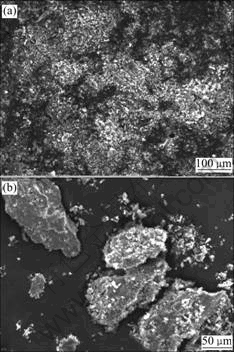
Fig.7 Debris morphologies of 15% graphite particle reinforced composite: (a) 10 N; (b) 160 N
Table 2 Energy dispersive X-ray analysis on worn surface
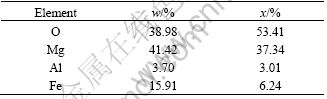
With the increase of applied loads, the subsurface of the specimens is subjected to more severe damage and the protective transferring layer can no longer remain stable under the ploughing action. Al2O3 fibers fracture in the sliding process and loss their ability to support normal loads. The surface transferring layer disappears; as a result, the counterface consequently comes in direct contact with the matrix alloy. Therefore, the high strains in the matrix alloy are developed, corresponding to the a little increased wear rate and friction coefficient (Fig.4). Fragmentation of the reinforcement induces abrasive wear, manifesting itself by distinct scratches and grooves on the worn surface (Fig.6(b)). Consequently, it can be concluded that the main wear mechanism in this process is abrasive wear. At the same time, the reinforcements’ fracture also generates micro-defects in the materials, offering the crack initiation for delamination wear mechanism along the process of the sliding.
The sliding is complex for composite materials containing solid lubricants like graphite. A black lubricating film forms progressively on the sliding surface under the normal loads of 60-160 N, as revealed in Figs.6(c)-(e). Graphite particles are apt to be covered by plastic flow of the matrix and the debris under lower loads, which inhibits graphite to spread sufficiently, as shown in Figs.6(a) and (b). It can be seen from Fig.6(c) that only part of the worn surface possess black lubricating film. In Figs.6(d) and (e), a continuous lubricating film almost covers the whole sliding surface. The formation of the film of graphite during sliding limits effectively the direct metal-to-metal interaction between the composite tribo-surface and the counterpart, and changes the relationship among friction coefficient, wear mass loss and load, corresponding to the lowest friction coefficient and the sluggish increase in wear rate. It is also clear that the wear rate of the composites does not correlate well with either tensile ductility or hardness. It is determined by the relative wear resistance of the matrix and particulates and also by the nature of the interface layer that forms between the sliding surfaces which could be entirely different from the bulk composite. The formation of the film of graphite during sliding plays an important role in improving the wear resistance of the composite. The film also reduces the level of normal pressure transmitted through it to the surface of the composite and thereby contributes to the increase of wear resistance. Lower energy dissipation apparently is resulted from the formation of a lubricating film on the tribo-deformed surface of the composite. It also can be found from Fig.6(e) that micro-cracks exist in the surface film, and some damage spots in the form of craters can be seen(Fig.6(f)). The material removal during the process is in the form of small pieces, resulting in the formation of multilayered flake-type debris, indicating that crack initiation and propagation take place in the subsurface mainly. When such subsurface cracks join the wear surface, delamination is the dominant wear mechanism. At higher loads up to 200 N, more severe wear proceeds, leading to the breakage of the surface film. The presence of many transverse cracks on the worn surface is clearly evident from the SEM micrograph shown in Fig.6(g). The wear process is characterized by sharper plastic deformation and a rapid removal rate of material.
As the magnesium alloy composites containing graphite particles are subjected to sliding friction conditions, graphite particles tend to be scaled off and transferred to the tribosurface due to their layer structure and very low hardness. Besides, graphite is squeezed from its embedded sate due to plastic flow of metal below the sliding surface caused by friction strain. That may be referred as one of the basic tribological characteristics, for ceramic-graphite composites also possess similar friction behavior[14]. Graphite coming to the tribosurface is then smeared onto the worn surface by shearing action of the mating disc, giving rise to the formation of a lubricating film. On the other hand, graphite has the tendency to be covered by plastic flow of matrix alloy because of consistent sliding, restricting supply of graphite to tribosurface. Hence, the formation process of surface lubricating film is determined by a dynamic balance between the amount of graphite being squeezed out and the amount of graphite covered by deformed matrix. The result obtained is in agreement with the one made by LIU[15], who has reported the smearing process of graphite in Al alloy composite under dry sliding conditions.
4 Conclusions
1) Wear resistance of AZ91 magnesium alloy matrix composite is improved substantially with the increase in graphite particle content form 5% to 20%, and wear mass loss and friction coefficient reduce to a lower level. Wear rate increases quite slowly under a certain range of load and friction coefficient reaches the minimum especially for the composite with graphite particle content exceeding 15%.
2) Al2O3 reinforcement has an excellent load- bearing capacity under low applied load in sliding process, enhancing the wear resistance of composite. With increasing applied load, Al2O3 fibers fracture and lose their ability to support normal loads, leading to the increase in wear rate and friction coefficient.
3) Formation of a continuous black lubricating film on the worn surface along sliding effectively limits the direct interaction between the composite tribo-surface and the counterpart, corresponding to the very low wear mass loss and friction coefficient in wear curves.
4) The wear rate increases abruptly above a critical load. The graphite particles help delay the transition from the mild wear to the severe wear.
References
[1] POLMEAR I J. Recent developments in light alloy [J]. Trans JIM, 1996, 37(1): 12-31.
[2] IDRIS M H. Precision casting of a magnesium-base alloy [J]. Br Foundryman, 1997, 90(4): 140-144.
[3] Qi Qing-ju, LIU Yong-bing, YANG Xiao-hong. Effects of rare earths on friction and wear characteristics of magnesium alloy AZ91D [J]. Trans Nonferrous Met Soc China, 2003, 13(1): 111-115.
[4] JOHN E, ALLISON, GERALD S. Metal matrix composites in the automotive industry: opportunities and challenges [J]. JOM, 1993(1): 19-26.
[5] ZHENG Rong-chang, KE Wei, XU Yong-bo, HAN En-hou. Recent development and application of Mg alloys [J]. Acta Metallurgica Sinica, 2001, 37(7): 673-685.
[6] LIU Chu-ming, JI Ren-feng, ZHOU Hai-tao, CHEN Ming-an. Research and development progress of damping capacity of magnesium and magnesium alloys [J]. The Chinese Journal of Nonferrous Metals, 2005, 15(9): 1319-1325. (in Chinese)
[7] CHEN H, ALPAS A T. Sliding wear map for the magnesium alloy Mg-9Al-0.9Zn(AZ91) [J]. Wear, 2000, 246: 106-116.
[8] QI Qing-ju, LIU Yong-bing, YANG Xiao-hong. Hybrid reinforced AZ91 magnesium alloy composites [J]. Special Casting & Nonferrous Alloys, 2005, 25(3): 170-171.
[9] HUANG Pei-yun. Theory on Powder Metallurgy [M]. Beijing: Metallurgical Industry Press, 1982.
[10] KOMVOPOULOS K, SAKA N, SUH N P. Role of hard layers in lubricated and dry sliding [J]. J Tribol, 1987, 109(2): 223-229.
[11] VENKATARAMAN B, SUNDARARAJAN G. The sliding wear behavior of Al-SiC particulate composites(Ⅰ): macrobehaviour [J]. Acta Mater, 1996, 44(2): 451-460.
[12] ZHANG I F, ZHANG L C, MAI Y W. Particle effects on friction and wear of aluminum matrix composites [J]. Journal of Materials Science, 1995, 30: 5939-6004.
[13] SARAVANAN R A, SURAPPA M K. Fabrication and characterization of pure magnesium-30vol%SiC particle composite [J]. Materials Science and Engineering, 2000, 276A: 108-116.
[14] DONG Li-min, ZHANG Bao-qing, TIAN Jie-mo, LI Zhao-xin. A study on the friction and wear behavior of ceramic-graphite composite [J]. Tribology, 1997, 17(4): 363-366.
[15] LIU Y B. Friction and wear of aluminum-graphite composites: the smearing process of graphite during sliding [J]. Wear, 1992, 159: 201-205.
Corresponding author: QI Qing-ju; Tel: +86-21-26649114; E-mail: qqj@baosteel.com
(Edited by YANG Bing)