稀有金属 2018,42(06),567-572 DOI:10.13373/j.cnki.cjrm.XY17050040
Ni, Si对Cu-Cr-Zr-Mg合金析出相及性能的影响
林国标 张茂奎 张鸿
北京科技大学材料科学与工程学院
摘 要:
在Cu-Cr-Zr-Mg合金中加入少量的Ni, Si, 应用扫描电镜 (SEM) 、场发射电镜 (FESEM) 、透射电镜 (TEM) 分析了合金固溶、时效后的显微组织及析出相成分, 没有发现Ni-Si化合物形成。Si除了溶解在Cu基体外, 优先与Cr, Zr反应, 形成了微米级Cr3Si, Cu-Zr-Si-Ni化合物, 且在固溶过程中难以溶解, 观察显示时效后的合金组织中Cr3Si集中区域鲜见纳米析出相, 其余区域存在纳米析出相, 经能谱成分及电子衍射分析确定为由Cr及Cu-Zr组成, Si的加入减少了纳米析出相的形成, 降低了析出强化效果。用少量的Si替代Cu-Cr-Zr-Mg合金中部分Zr, 合金抗拉强度没有增加, 且由于Si在Cu基体中比Cr, Zr有较大固溶度和溶质散射电阻, 合金的导电率显著下降;在此合金成分的基础上加入少量Ni元素, 形成的合金强度有所回升, 但导电率进一步降低。文中分析了析出相和性能演变的原因。
关键词:
Cu-Cr-Zr-Mg合金;合金元素;显微组织;强度;导电率;
中图分类号: TG146.11
作者简介:林国标 (1964-) , 男, 安徽桐城人, 博士, 副教授, 研究方向:金属材料与加工工程;电话:010-62332882;E-mail:lin571@163.com;
收稿日期:2017-05-19
基金:国家自然科学基金项目 (51274265) 资助;
Precipitation Phases and Properties of Cu-Cr-Zr-Mg Alloy with Addition of Ni, Si
Lin Guobiao Zhang Maokui Zhang Hong
School of Materials Science and Engineering, University of Science and Technology Beijing
Abstract:
The microstructure and precipitation compositions of Cu-Cr-Zr-Mg alloy with minor addition of Si, Ni were investigated by means of scanning electron microscope (SEM) , field emission electron microscope (FESEM) and transmission electron microscope (TEM) . No Ni-Si compound was found in the alloy specimens after solid-solution and aging. In addition to dissolving in Cu matrix, Si preferentially reacted with Cr and Zr to form micro-scale compounds of Cr3Si, Cu-Zr-Si-Ni, which were difficult to dissolve in the matrix during solid-solution process. Observations demonstrated that the regions gathered with Cr3Si particles had few nano-scale precipitates, which were found in the rest and identified as Cr and Cu-Zr compound by means of energy dispersive X-ray spectrum and electrical diffraction. Consequently, addition of Si decreased amount of the nano-scale precipitates and lowered precipitation strengthening effect. The substitution of Si for partial Zr in Cu-Cr-Zr-Mg alloy did not increase its ultimate tensile strength, and yet remarkably lowered its conductivity as Si had higher solubility in Cu matrix and solution scattering resistivity than Cr or Zr. By introducing a little Ni into this composition, the ultimate tensile strength for the formed alloy recovered to some extent, whereas its electrical conductivity further decreased. The causes for the change of precipitation phase constituent and the properties were discussed.
Keyword:
Cu-Cr-Zr-Mg alloy; alloying elements; microstructure; strength; electrical conductivity;
Received: 2017-05-19
纯铜仅次于银具有良好的导电、导热性能和可加工性能, 但强度较低, 为满足应用于集成电路和半导体器件的引线框架材料、电气化铁路接触线、触头材料、冶金连铸用结晶器以及高科技、军工领域的需求, 需要发展高强高导铜合金材料, 几乎所有提高铜合金强度的措施都会带来铜合金导电导热性能不同程度的降低, 如何显著提高强度而又较少降低导电导热性能显得尤为重要, 广泛采用的办法是通过微量合金化和过程工艺控制以期产生更多的纳米弥散相的析出强化, 减少或避免微米级析出相, 同时要求合金元素在基体中溶解度低以减少对导电率的不利影响。不同的合金元素的综合作用效果各不相同, 目前发展比较成功的合金系有:Cu-Fe-P[1,2], Cu-Cr-Zr[1,3,4,5,6,7,8,9,10,11], CuNi-Si[1,12,13], 在这些合金系的基础上替换或加入其他合金元素, 又产生了不同元素组成的多种合金。其中, Cu-Cr-Zr系合金以较高的强度、较高导电率的综合性能备受关注, 通过高温固溶处理使凝固合金中更多析出相溶解, 淬火形成过饱和的固溶体后经时效处理析出纳米强化相Cr, Cu-Zr粒子, Cu-Zr相目前报道有多种[6], 如Cu4Zr[7,9], Cu5Zr[3,8], 由于Cr, Zr在铜基体中溶解度低, 对导电率影响小, Zr与Cr相比, 提高强度的幅度要弱些但对导电率的影响更小。热处理过程中加上形变处理可促进纳米粒子的弥散析出, 同时可使得未能完全固溶的微米级颗粒细化, 合金强度和导电率均能大幅度提高[4]。在Cu-Cr-Zr合金中加入某些合金元素可以进一步提高综合性能, 如Ag[5], Mg[10,11]。与Cu-Cr-Zr系合金相比, Cu-Ni-Si系合金中的Ni-Si纳米析出相 (Ni, Si原子比在3∶1~2∶1之间) 的强化效果更为显著 (虽然导电率稍低) , 能否在Cu-Cr-Zr合金强化相的基础上近一步形成Ni-Si纳米强化相, 近年来成为人们关注的课题, Pang等[14]对Cu-0.39Cr-0.15Zr-0.12Ni-0.03Si (%, 质量分数) 合金的变形、时效工艺进行研究, 发现合金性能可以达到硬度HV 177, 导电率82.2%IACS。也有报道[15], 在Cu-Cr合金中加入Si, Si溶解在Cu相和Cr相中, 与Cr反应形成脆性相Cr3Si;而Si又是Cu-Cr-Zr合金系制备中容易带来的杂质元素。鉴于这些原因, 本文以Cu-Cr-ZrMg合金为基础, 借助Cu-Cr-Zr合金系制备的基本过程 (固溶、淬火、时效处理) , 探讨了Ni, Si的同时加入对原有合金析出相、合金的强度及导电率的影响, 为高性能Cu-Cr-Zr合金的研究与制备提供参考。
1 实验
选用电解铜, 纯Ni, Cu-Cr, Cu-Zr, Cu-Si, CuMg中间合金作为原料, 使用真空感应熔炼炉进行合金冶炼, 充氩气浇注砂型试样棒, 试样棒尺寸为Ф20 mm×120 mm, 用硅碳棒箱式炉对合金进行固溶、时效热处理, 参考以前的工作[6], 确定980℃×2 h固溶后水淬, 然后进行440℃×20 h时效处理。导电率试样尺寸为Ф3 mm×120 mm, 采用四端法测量电阻, 计算其导电率, 每个导电率数据点为5次测量结果的平均值, 所用四探针仪器型号为美国产CASCADE;选用规格为Ф5 mm的标准拉伸试样, 按照GB6397-86标准在CMT电子拉伸试验机上进行检测, 加载速度2 mm·min-1, 每个拉伸强度试样的数据点为3个拉伸试样的平均值。利用扫描电镜 (SEM) 、场发射电镜 (FESEM) 、电子能谱 (EDXS) 、透射电镜 (TEM) 对合金的显微组织、相成分结构进行分析, 其中透射电镜样品用双喷电解抛光法制备, 电解液配比 (体积比) 为HNO3∶CH2OH=1∶3, 电解时电压为50 m V。
2 结果与讨论
2.1 加入Ni, Si的Cu-Cr-Zr-Mg合金析出相分析
图1为经980℃保温2 h固溶处理的Cu-0.24Cr-0.12Zr-0.10Si-0.41Ni-0.08Mg (%, 质量分数) 凝固合金组织的SEM图片, 从图1 (a) 可见, 在α-铜相晶粒上面也有少量的黑色颗粒, 晶粒间有很多细小的黑色颗粒 (本文中称为麻点组织) , 图1 (b) 为其放大相, 对这些黑色颗粒相进行能谱分析, 主要含有Cr, Si, 其典型成分 (%, 原子分数) 为:Cr73.18-Si26.82, Cu6.53-Cr68.49-Si24.98, 有些颗粒太小, 以至小于电子束斑激发区的面积, 因此能谱分析成分里含有Cu, 根据原子比及相关文献[14], 黑色颗粒相应为Cr3Si。另外, 还有白色的相即含Zr的相, 图1 (c) 所示为其中一Zr相的放大像, 图1 (d) 为其能谱图, 由图1 (d) 可见, 主要含有Cu, Zr, Si, Ni, Zr相旁边的黑色相主要含Cr, Si。
而与图1相对应的, 没有加Ni, Si的合金组织如图2所示, 则没有图1中晶粒间那种麻点状的组织, 虽然有少量黑色颗粒存在, 但主要含有的Cr, 如其中之一能谱成分 (%, 原子分数) 为:Cr97.14-Cu2.99-Zr0.17;测得的多个不同白色相颗粒成分 (%, 原子分数) 为:Cu88.14-Cr0.38-Zr11.29-Mg0.19, Cu88.90-0.31-Zr9.77-Mg1.02, Cu84.53-Cr1.01-Zr14.45, Cu 88.49-Cr0.63-Zr10.88, 可见主要含有Cu, Zr及少量Mg, 综合相关文献报道, 应该为Cu-Zr (Mg) 相。
图3为经440℃×20 h时效后的Cu-0.27Cr-0.12Zr-0.10Si-0.40Ni-0.08Mg显微组织的SEM图片, 与时效前的扫描电镜显微组织类似, 仍然有白色相和α-铜相晶粒间黑色颗粒聚集的麻点组织, 其成分及组织形态与时效前类似, 如图3 (b) 中黑色颗粒为Cr3Si, 白色颗粒能谱成分 (%, 原子分数) 为:Cu23.12-Cr1.76-Zr25.77-Ni17.26-Si32.09。
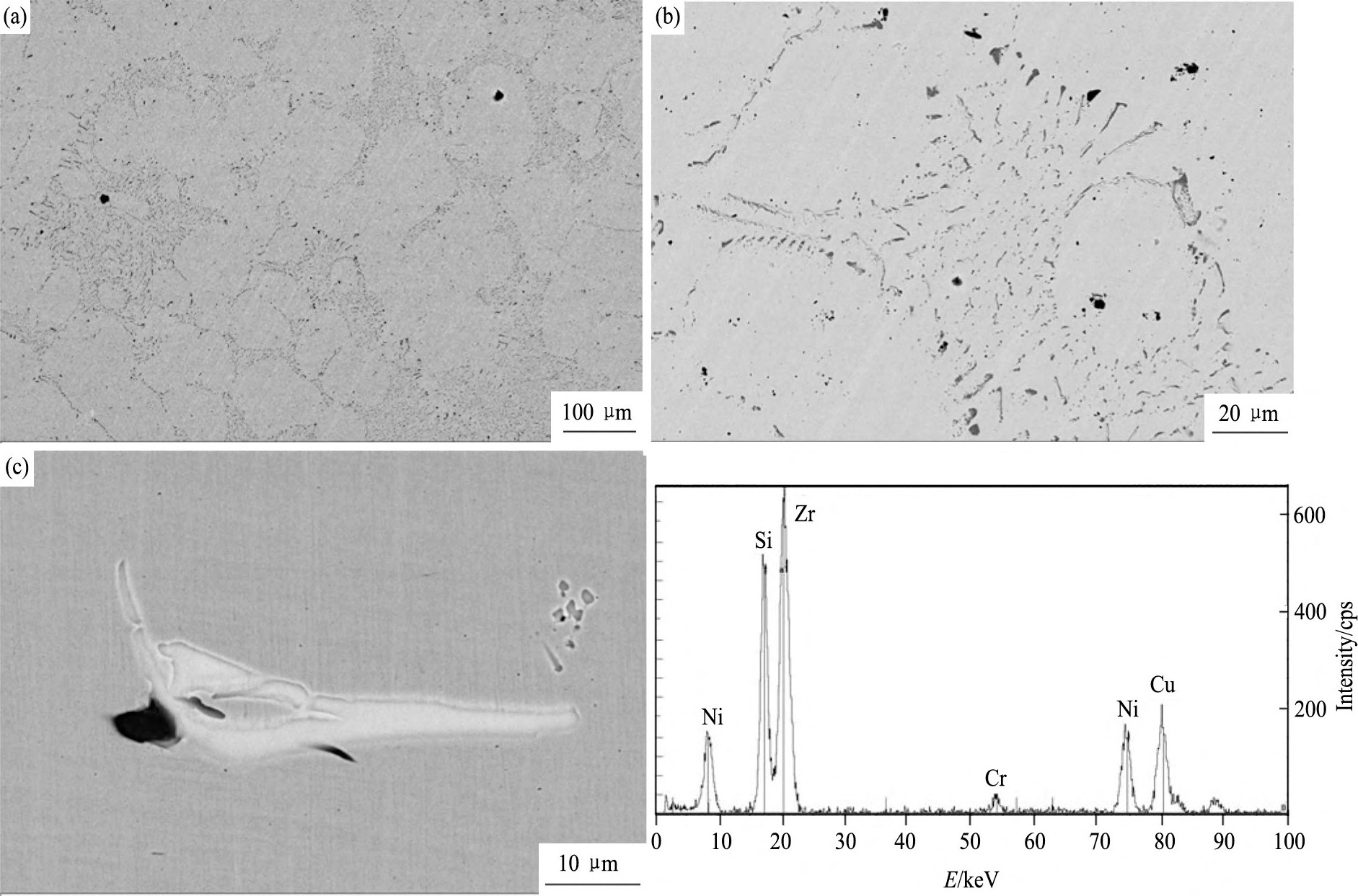
图1 固溶处理的Cu-0.24Cr-0.12Zr-0.10Si-0.41Ni-0.08Mg凝固合金组织的SEM图片Fig.1 SEM images for microstructure of solidified Cu-0.24Cr-0.12Zr-0.10Si-0.41Ni-0.08Mg alloy after solution heat treatment (a) Low magnification; (b) Amplification for inter-crystalline; (c) White phase in alloy; (d) EDXS analysis for white phase
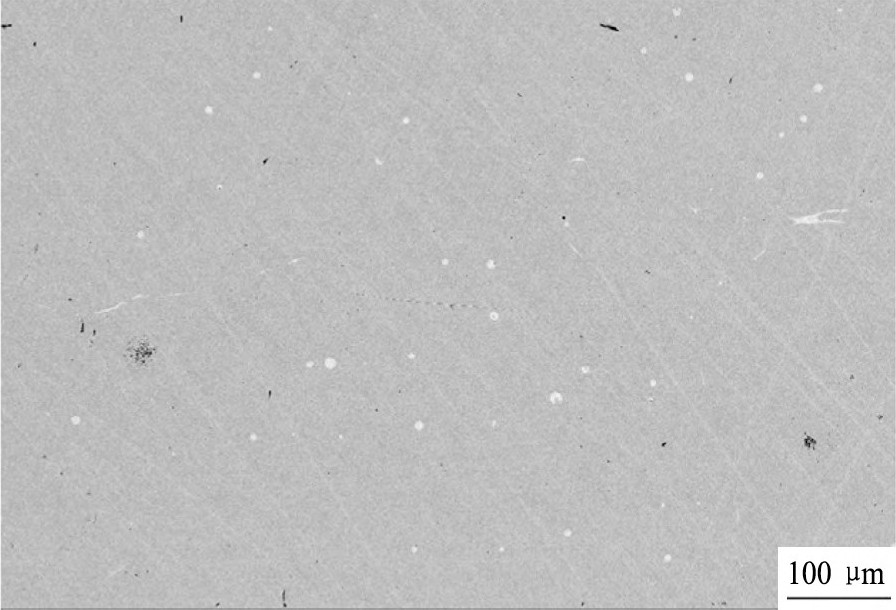
图2 Cu-0.24Cr-0.21Zr-0.08Mg合金低倍组织的SEM图片Fig.2 Low magnification SEM image of microstructure for Cu-0.24Cr-0.21Zr-0.08Mg alloy
为了分析是否有纳米级析出相, 应用场发射电镜进行了高放大倍数下的显微观察, 发现有纳米级粒子析出, 但分布不均匀, Cr3Si黑色颗粒聚集的麻点组织区域, 没有纳米粒子析出或极少, 而Cr3Si颗粒少的α-铜相晶粒内, 则有很多的纳米粒子, 典型情况如图4 (a) 所示;场发射电镜还发现Cr3Si颗粒也可形成于晶界上, 如图4 (b) 所示, 显然这对合金力学性能不利。应用场发射电镜能谱分析, 没有发现Ni-Si析出相。
为了进一步鉴别纳米析出相, 制备了透射电镜样品, 进行了透射电镜观察分析, 应用透射电镜能谱分析表明析出相主要含有Cr, Cu, Zr, 对纳米析出相进行了选区电子衍射分析, 结果如图5所示, 经标定确认为Cr相、Cu5Zr相, 这一结果与图2中微米级析出相能谱分析结果相接近, 也与相关的报道[3,8]相一致。这说明一部分Cr, Zr合金元素发生了固溶, 在时效时析出。
应用扫描电镜、场发射电镜及透射电镜的能谱进行分析, 均没有发现微米级或纳米级Ni-Si化合物相。加入的Ni, Si元素中, Si应为强化合物形成元素, 我们曾试验在合金中只加入Si没有加Ni, Si除了与Cr形成Cr3Si外, 与Zr也会形成化合物, 其中一能谱成分 (%) 为:Cu 24.50-Zr30.24-Si36.24-Cr9.02。根据合金相图Cr3Si熔点为1770℃, 远高于Ni-Si化合物的熔点[16,17], 前者应更为稳定, 在合金液凝固结晶时应优先形成;从电负性差来判断, Cr-Si化合物电负性差为:Si (1.9) -Cr (1.66) =0.24, Ni-Si化合物电负性差为:Ni (1.91) -Si (1.9) =0.01, 前者电负性差大, 应更容易化合。因此Si除了一部分溶解在基体外, 将优先与Cr反应形成Cr3Si, 而不与Ni反应形成Ni-Si化合物相, 另外Si还会形成微米级的Cu-Si-Zr-Ni化合物, 因而减少了纳米Cr, Cu-Zr析出相的形成。
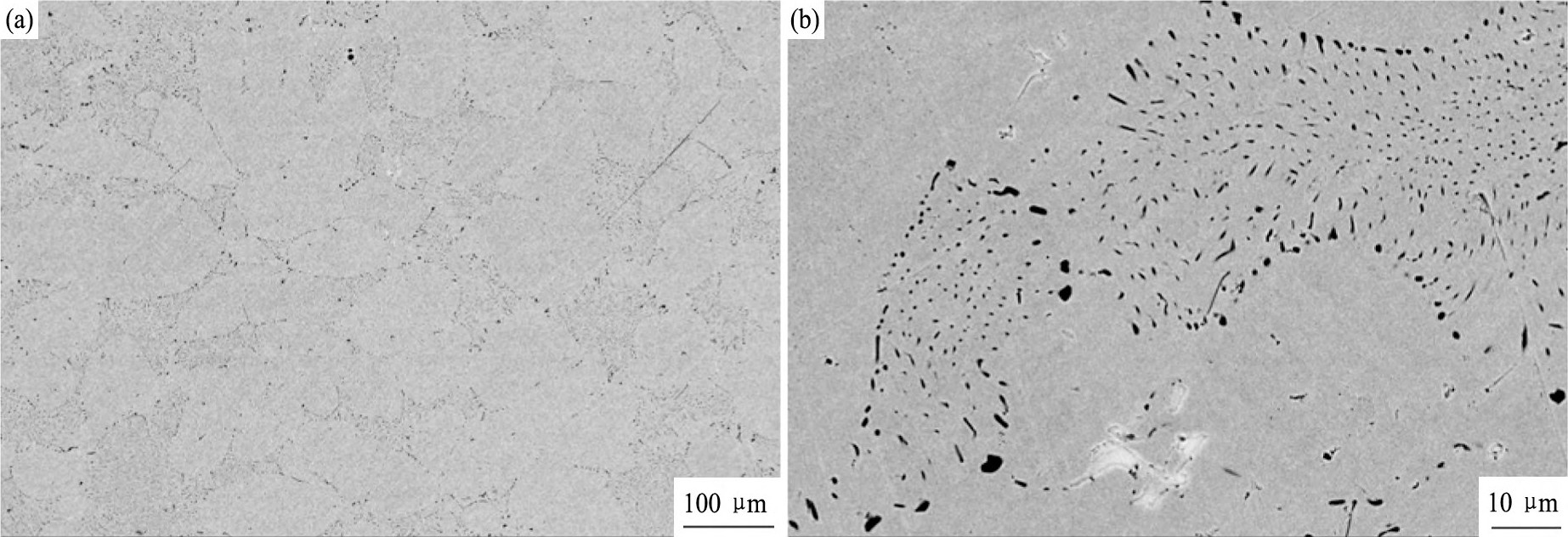
图3 Cu-0.24Cr-0.12Zr-0.10Si-0.41Ni-0.08Mg时效后的显微组织SEM图片Fig.3 SEM images for microstructure of Cu-0.24Cr-0.12Zr-0.10Si-0.41Ni-0.08Mg alloy after aging treatment (a) Low magnification; (b) Local amplification image
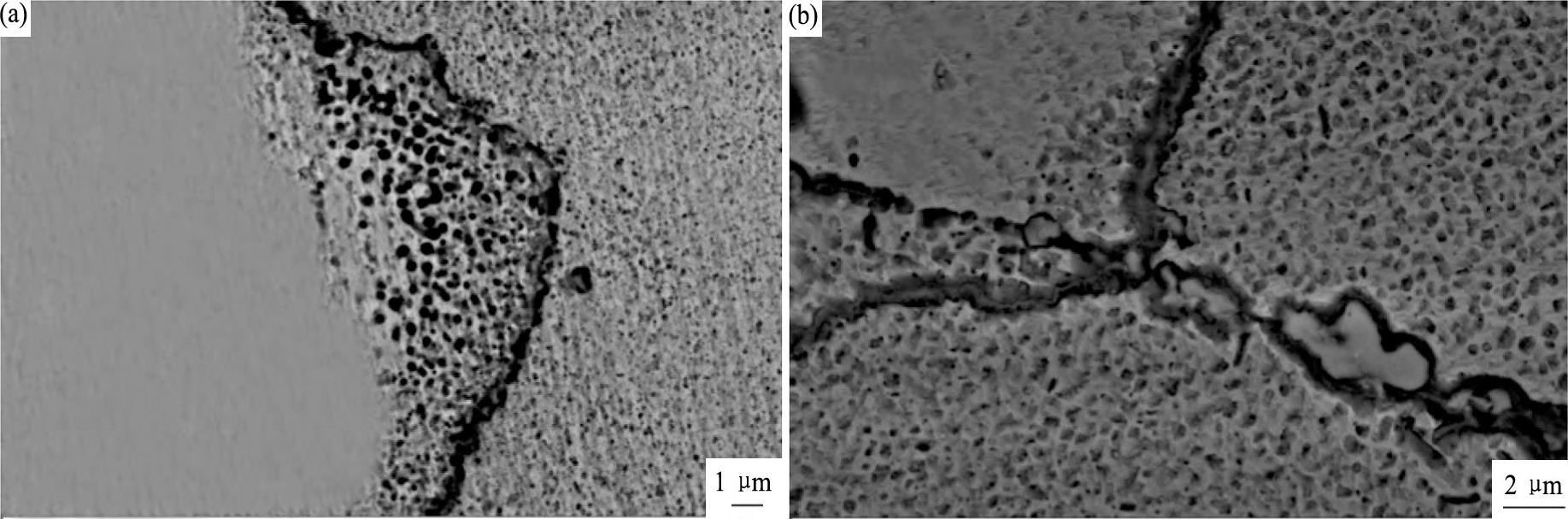
图4 场发射电镜对Cu-0.24Cr-0.12Zr-0.10Si-0.41Ni-0.08Mg时效组织的显微观察Fig.4 Microscopic examination of aged Cu-0.24Cr-0.12Zr-0.10Si-0.41Ni-0.08Mg alloy by field emission electron microscope (a) Uneven distribution of nano-sized precipitation phase; (b) Cr3Si precipitates on boundary
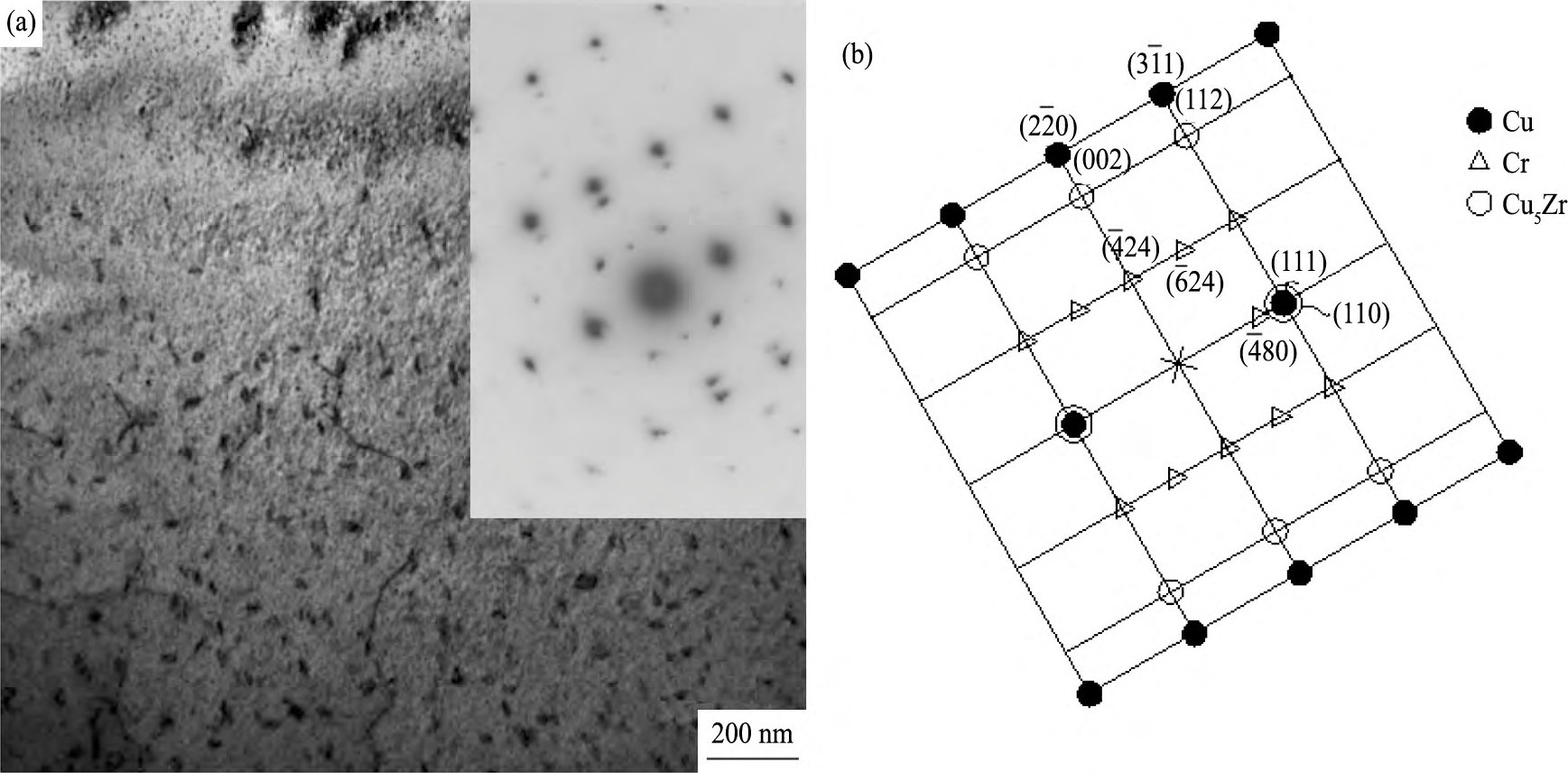
图5 Cu-0.24Cr-0.12Zr-0.10Si-0.41Ni-0.08Mg时效合金的透射电镜观察Fig.5 TEM observation of aged Cu-0.24Cr-0.12Zr-0.10Si-0.41Ni-0.08Mg alloy (a) Nano-sized precipitates and SAED pattern; (b) Schematic drawing for SAED pattern
2.2 Ni, Si的加入对合金性能的影响
为了对比分析不同合金元素对Cu-Cr-Zr合金性能的影响, 利用砂型浇注制备出了表1所示的合金成分试样, 试样均经980℃×2 h固溶处理、水淬、440℃×20 h时效处理。
由表1可见, 加入少量的Mg, 合金的导电率没有降低, 但强度有所增加。根据前面组织的分析, 除了在少数Zr相发现Mg外, 在析出相中并没有发现Mg, 文献[11]也曾报道Mg可存在于Zr相中。本实验试样残余0.08%Mg, 低于Mg在Cu的溶解度, Mg应主要以固溶的形式存在, 产生固溶强化, 增加了合金强度;另外, Mg熔点低, 冶炼过程中容易挥发, 考虑到烧损实际加入量均比较多, 控制熔炼工艺, 待液面平静后再浇注, 合金组织致密, 挥发的Mg对合金液产生了净化与除气, 这也有利于合金力学性能与导电性能的改善。
从表1可见, 用0.1%Si替代0.1%Zr, 合金的强度有所降低, 且导电率大幅度下降;在此基础上加入0.4%Ni, 合金强度有所回升, 但导电率进一步下降。根据上面析出相分析, Si的加入形成了微米级的Cr3Si和块状的Cu-Zr-Si-Ni多元复杂化合物, 这些化合物熔点高, 在固溶处理过程中难以消除, 势必减少纳米级Cr, Cu-Zr析出粒子的形成。据广泛的研究报道, 纳米级粒子的强化效果远优于微米级颗粒[3,18,19], 析出的纳米粒子的强化效果可以用Orowan机制来定性描述:

式中:T为位错线的线张力, R为粒子的半径, b为基体位错的Burgers矢量, f为粒子所占的体积分数。因此上述组织的改变势必带来强度的降低, 但由于Si, Ni的固溶强化及熔体中形成的Cr3Si对合金晶粒的细化[14], 总的效果强度损失不大。文献[14]也报道在Cu-15Cr另外加入0.5%Si, 并没有使硬度增加。
合金元素对金属室温导电率的影响主要有3方面:位错散射电阻, 即由位错对传导电子散射所产生的电阻, 本实验合金未经变形处理, 位错浓度应该不高;第二方面是界面散射电阻, 加入的Si是替代Zr, 加入的Ni与铜完全互溶, 界面变化应不大;第三方面是溶质散射电阻, 即铜基体中固溶合金元素产生的电阻, 这方面影响大, 查阅合金相图, 常温下Cr, Zr在Cu基体中饱和固溶度都很小, 而Si溶解度相对来说比较大, 可达4%, Ni完全溶解。溶质散射电阻可以用Mathiessen定律描述[1], 常温下低浓度固溶体的电阻率可表示为:

式中:ρ0为固溶体溶剂组元即纯铜的电阻率, C为溶质原子浓度, ξ为单位溶质浓度引起的附加电阻率, 不同合金元素的ξ不一样, 其影响顺序为Si>Cr>Ni>Zr, 由此可见Si替代Zr产生的固溶对导电率降低最大, Ni的加入也会降低导电率, 影响要小一些但也高于Zr, 因此可以理解表中合金成分的变化带来的导电率变化。
表1 Ni, Si, Mg元素的添加对Cu-Cr-Zr合金性能的影响Table 1 Effects of added Ni, Si, Mg on properties of Cu-Cr-Zr alloy 下载原图

表1 Ni, Si, Mg元素的添加对Cu-Cr-Zr合金性能的影响Table 1 Effects of added Ni, Si, Mg on properties of Cu-Cr-Zr alloy
3 结论
1.在Cu-Cr-Zr-Mg合金中加入Ni, Si, 没有发现形成Ni-Si化合物, Ni, Si除了固溶于基体外, 形成了微米级Cr3Si和Cu-Zr-Si-Ni化合物, 减少了纳米析出相的形成;合金中纳米析出相主要是Cr, Cu5Zr化合物。
2.Si替代部分Zr, 并没有增加合金强度, 反而使得合金导电率显著降低;在此合金成分的基础上加入部分Ni元素, 形成的合金强度有所回升, 导电率会进一步降低。因此在Cu-Cr-Zr合金中加入Ni, Si不是一种很好的选择。
3.从元素电负性与凝固析出顺序来看, Si优先与Cr起反应, 而不是与Ni化合;Si的加入增多了微米级析出颗粒, 减少了纳米析出粒子, 降低了析出强化效应;相比Cr和Zr, Si与Ni在合金基体中有较大溶解度和溶质散射电阻, 因而对合金导电率带来更多的不利影响。
参考文献
[1] Liu P, Zhao D M, Tian B H.Copper Alloys with High Properties and Their Processing Technology[M].Beijing:Metallurgical Industry Publisher, 2005.114. (刘平, 赵冬梅, 田保红.高性能铜合金及其加工技术[M].北京:冶金工业出版社, 2005.114.)
[2] Lu D P, Wang J, Zeng W J, Liu Y, Lu L, Sun B D.Study on high-strength and high-conductivity Cu-Fe-P alloys[J].Materials Science and Engineering A, 2006, 421:254.
[3] Holzwarth Uwe, Stamm Hermann.Precipitation behaviour of ITER-grade Cu-Cr-Zr alloy after simulating the thermal cycle of hot isostatic pressing[J].Journal of Nuclear Materials, 2000, 279:31.
[4] Liu Q, Zhang X, Ge Y, Wang J, Cui J Z.Effect of processing and heat treatment on behavior of Cu-Cr-Zr alloys to railway contact wire[J].Metallurgical And Materials Transactions A, 2006, 37A:3233.
[5] Zhang Y, Chai Z, Volinsky Alex A, Sun H L, Tian B H, Liu P, Liu Y.Hot deformation characteristics and processing maps of the Cu-Cr-Zr-Ag alloy[J].Journal of Materials Engineering and Performance, 2016, 25 (3) :1191.
[6] Zhao M, Lin G B, Wang Z D, Zhang M K.Analysis of precipitation in a Cu-Cr-Zr alloy[J].China Foundry, 2008, 11 (5) :268.
[7] Wang K, Liu K F, Zhang J B.Microstructure and properties of aging Cu-Cr-Zr alloy[J].Rare Metals, 2014, 33:134.
[8] Bi L M, Liu P, Chen X H, Liu X K, Li W, Ma F C.Analysis of phase in Cu-15%Cr-0.24%Zr alloy[J].Transactions of Nonferrous Metal Society of China, 2013, 23:1342.
[9] Zhang Y, Volinsky Alex A, Tran H T, Chai Z, Liu P, Tian B H, Liu Y.Aging behavior and precipitates analysis of the Cu-Cr-Zr-Ce alloy[J].Materials Science and Engineering A, 2016, 650:248.
[10] Cheng J Y, Yu F X, Shen B.Solute clusters and chemistry in a Cu-Cr-Zr-Mg alloy during the stage of aging[J].Materials Letters, 2014, 115:201.
[11] Su J H, Liu P, Li H J, Ren F Z, Dong Q M.Phase transformation in Cu-Cr-Zr-Mg alloy[J].Materials Letters, 2007, 61:4963.
[12] Lei Q, Li Z, Xiao T, Pang Y, Xiang Z Q, Qiu W T, Xiao Z.A new ultrahigh strength Cu-Ni-Si alloy[J].Intermetallics, 2013, 42:77.
[13] Srivastava V C, Schneider A, Uhlenwinkel V, Bauckhage K.Effect of thermomechanical treatment on spray formed Cu-Ni-Si alloy[J].Material Science and Technology, 2004, 20:839.
[14] Pang Y, Xia C D, Wang M P, Li Z, Xiao Z, Wei H G, Sheng X F, Jia Y L, Chen C.Effects of Zr and (Ni, Si) additions on properties and microstructure of Cu-Cr alloy[J].Journal of Alloys and Compounds, 2014, 582:786.
[15] Sun S J, Sakai Shigeki, Suzuki Hirowo G.Effect of Si on the microstructure and mechanical properties of as drawn Cu-15Cr in situ composites[J].Materials Science and Engineering A, 2001, 303:187.
[16] Wang C P, Zhu J J, Lu Y, Guo Y H, Liu X J.Thermodynamic description of the Cu-Ni-Si system[J].Journal of Phase Equilibria Diffusion, 2014, 35 (1) :93.
[17] Yu J Q, Yi W Z, Chen B D.Handbooks of Binary Alloy Phase Diagrams[M].Shanghai:Shanghai Scientific Press, 1984.494. (虞觉奇, 易文质, 陈邦迪.二元合金状态图集[M].上海:上海科学技术出版社, 1984.494.)
[18] Jiang S H, Wang H, Wu Y, Liu X J, Chen H H, Yao M J, Gault Baptiste, Ponge Dirk, Raabe Dierk, Hirata Akihiko, Chen M W, Wang Y D, Lu Z P.Ultrastrong steel via minimal lattice misfit and high-density nanoprecipitation[J].Nature, 2017, 1:22032.
[19] Li M M, Zhang X P, Chen H M, Wang H, Yang B.Microstructural evolution and mechanical property of CuCr-In alloy during thermo-mechanical treatment[J].Chinese Journal of Rare Metals, 2017, 41 (12) :1311. (李明茂, 张小平, 陈辉明, 汪航, 杨斌.CuCr-In合金形变热处理过程的组织与性能演变研究[J].稀有金属, 2017, 41 (12) :1311.)