
Johnson-Cook dynamic constitutive relationship for TC16 titanium alloy
YANG Yang(杨扬), ZENG Yi(曾毅), WANG Bing-feng(汪冰峰)
School of Materials Science and Engineering, Central South University, Changsha 410083, China
Received 15 July 2007; accepted 10 September 2007
Abstract: The true stress—strain curves of TC16 alloy with a wide range of strain rates were investigated under uniaxial quasi-static tension and uniaxial dynamic compression with the Instron 8032 test machine and the split Hopkinson bar respectively. The results indicate that the true stress increases with increasing strain rate, while decreases with increasing temperature. Under the 105 s-1 high strain rate and temperature higher than 673 K, the true stress would even be less than that under quasi-static condition. A new method incorporating TC16’s stress—strain curve developing item was proposed to determine the coefficients in J-C model easily and to avoid the estimation of the adiabatic temperature rising. The Johnson-Cook dynamic constitutive relationship for TC16 was obtained for the first time. Good agreement was obtained between the model prediction and the experimental stress—strain curves for TC16 under both quasi-static and dynamic loadings.
Key words: TC16 titanium alloy; dynamic constitutive relationship; SHPB; strain rate; temperature
1 Introduction
TC16 titanium is a new type titanium alloy developed firstly by the Russia Institute of Aeronautical Materials. This high-strength titanium alloy has good mechanical and technological properties[1-2] and has been utilized extensively in aircraft structures[3-4].
Constitutive relationship is the change law of the flow stress variation with deformation temperature, strain and strain rate. Furthermore, it incarnates dynamic response of material due to thermomechanical parameters and is the important basis for numerical simulation in metal plastic deforming process[5-6]. Considerable amounts of work were carried out on the dynamic mechanical behaviors of several main Ti alloys[7-10] with the change of deformation temperature. However, up to now, there was little work concerning that of TC16 alloy. The plastic deformation under quasi-static loading condition can be treated as an isothermal process, the high strain rate deformation process is essentially adiabatic, where most of the heat generated due to the plastic deformation cannot conduct and radiate. Thus, the adiabatic temperature rise is produced within the specimen. This temperature rise has a significant effect on the constitutive behavior of metals at high stain rates, causing thermal softening phenomenon. Apparently the effects of strain rate, strain hardening, and adiabatic temperature rise on the plastic deformation of metals are coupled during the high strain rate process[11]. The coefficients of the temperature item need to be modified for several times for a good result in obtaining constitutive equation[12], because such phenomenon is very complicate.
WANG and ZHOU[11] performed the recovery tensile impact tests in a bar-bar tensile impact apparatus (BTIA, a kind of Split Hopkinson Tension Bar setups) to obtain the isothermal tensile stress—strain curves for brass under repeated loading and unloading process at high strain rates. The advantages of these recovery experimental techniques make it possible to uncouple the thermal softening effect from the strain rate effect and strain hardening effect on the plastic deformation with the increasing of the experiment complication.
The main objective of the present work was to obtain the constitutive relationship of TC16 under both quasi-static and dynamic loading based on the SHPB technique, and a new method was proposed to determine the coefficients in J-C model easily and to avoid the estimation of adiabatic temperature rising.
2 Experimental
The specimen material used in the present study was TC16 titanium alloy with the composition of 87.5%Ti, 3%Al, 5%Mo, and the rest of V.
The uniaxial dynamic compression tests were carried out using the split Hopkinson bar (SHPB)[13-14] at deformation temperature from 293 K to 773 K and in the strain rate range of 4 623 to 15 550 s-1. The shape of specimen was cylinder. The height and diameter of the specimen were 4 mm and 2 mm respectively at the order rate 103 s-1, and 2 mm and 2 mm respectively at the order rate 104 s-1. The small-size specimens were used in the higher rate tests, so strains and strain rates were raised without increasing the velocity of incident bar greatly. The strain and strain rate of the specimen could be controlled and the dynamic test could be carried out even at the temperature high up to 1 200 K with this compression SHPB device. Using this technique, the second compressive incident wave was eliminated which traveled after the tensile wave. Thus the specimen avoided to be impacted for multiple times. The specimen was heated far from incident bar and transmission bar during high temperature experiment. Because of the absence of the second compressive incident wave, the split Hopkinson Bar experimental technique could be used to measure the dynamic behavior of materials at high strain rates and high temperatures.
3 Results and discussion
3.1 Experiment results
Fig.1 shows the microstructure of the specimen before deformation. The structure is homogeneous and the average grain size is about 1 μm, so that TC16 has relative good plasticity and high strength. As can be seen from the true stress—strain curves of TC16 shown in Fig.2, the temperature and the strain rate obviously affect the true stress. The true stress decreases with the increase of temperature under approximate strain rate according to the curves 3 and 6. The true stresses increase with the increase of strain rate at the same temperature shown from the curves 1, 2 and 5, which indicates that TC16 is the strain rate sensitive material. The plasticity of TC16 is improved with the increase of temperature, which proves its good hot deformation ability.
3.2 Establishment of constitutive model and acquisition of its coefficients
3.2.1 Establishment of constitutive model
The main thermo-viscoplastic constitutive models were proposed[15], for example, Johnson-Cook model, Zerrilli-Armstrong model, Follansbee-Kocks model and Bodner-Paton model. Due to its simple multiplication form and its application for various crystal structures, the empirically based Johnson-Cook(J-C) model was selected to describe the mechanical behavior of material at high strain rates and various temperatures. The strain rate hardening, strain hardening, and thermal softening effects on the plastic deformation could be simply incorporated in the model as a multiplication form and expressed as follows[12]:
(1)
where A = 1 111 MPa was the initial yield stress,
= 0.001 s-1 is the reference strain rate, T0 = 293 K is the reference temperature; B, n, C, m, D and k are the undetermined coefficients.
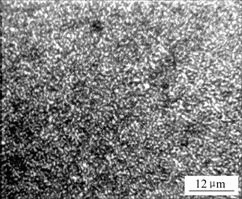
Fig.1 Microstructure of TC16
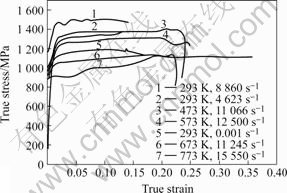
Fig.2 True stress—strain curves for TC16 under different conditions
It should be mentioned that T is not the environment temperature but the deformation temperature. The previous solutions were almost as follows[12]: firstly, deformation process was divided into many steps; and then adiabatic temperature rising of every step was estimated by Eqn.(2), which was added to preceding step deformation temperature as the current step deformation temperature. So the deformation temperature was unstably changed with the variation of stress and strain, which made it difficult to obtain the coefficients of the temperature item.
(2)
where η is a conversion factor of plastic work into heat, ρ is the density, cv is the specific heat capacity, εs is the initial strain and εe is the finished strain.
A new method was proposed to solve the difficulties through two steps. The first one was that the yield stresses under different deformation conditions were predicted using J-C model without considering the adiabatic temperature rising. The yield point in present work corresponded to 0.015 plastic strain, which could be found from the true stress—strain curves of TC16 shown in Fig.2. The second step was the acquisition of stress—strain curve developing item. The plastic loading proportion of the stress—strain curves could be approximately regarded as several lines with different slopes. The slope of line was set as s. Fig.3 shows the approximate lines and true stress—strain curves at 293 K and different rates, which illustrates that the different strain rates have a little effect on s at the same temperature. The temperature is the main factor affecting the variation of s from Fig.5.
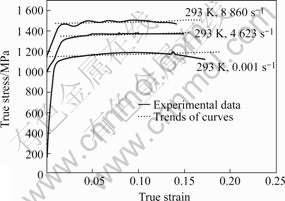
Fig.3 Approximate lines and true stress—strain curves at 293 K and different rates
In sum, the new method was proposed and the Johnson-Cook dynamic constitutive could be transformed as follows:
σ = σ0.015+s(ε-0.015) =

(3)
3.2.2 Acquisition of coefficients
To obtain the accurate coefficients, the least square method was used to determine the best-fit coefficients. The data of quasi-static curve 5 (strain rate 0.001 s-1, temperature 293 K) were substituted into Eqn.(1), and then B = 106.62 and n=0.29 were gained. The curve data of strain 0.015 at temperature 293 K and strain rates of 431, 4 623 and 8 860 s-1 were substituted into Eqn.(1) without changing B and n, and then C = 2.54×10-27 and m = 21.62 were gained. Similarly, the curve data of strain 0.015 under other deformation conditions were substituted into Eqn.(1) without changing other coefficients, and then D = 0.28, k = 0.99 were gained. The J-C equation for strain 0.015 was expressed as follows.
σ0.015=(1 111+106.62×0.0150.29)×
[1+2.54×10-27×
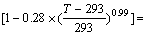

(4)
The values of σ0.015 under different deformation conditions were predicted by Eqn.(4) and shown in Table 1. The result indicated that the predicted data were in good agreement with the experimental data. The first step was finished.
Table 1 Comparison between experimental data and prediction for σ0.015 under different conditions
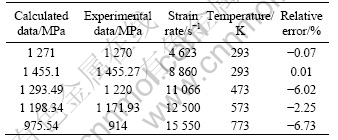
Fig.4 shows the approximate lines of plastic loading proportion of stress—strain cures. Fig.5 illustrates the
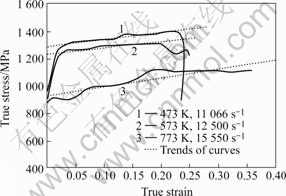
Fig.4 True stress—strain curves and their trends under different conditions
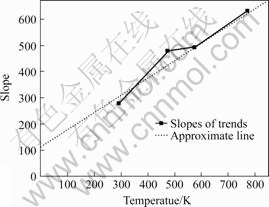
Fig.5 Slopes of approximate lines at different temperatures
relation of slop of line and temperature which is similar to be linear relation and may be expressed as:
s = 111.53+0.66 T (5)
The results of the first and second step were integrated to obtain the completed Johnson-Cook thermo-viscoplastic constitutive equation as follows:
σ = σ0.015+s(ε-0.015) =

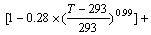
(3)
The prediction of the above J-C equation is quite in agreement with the experimental data from Fig.6 and Fig.7. The experiment data at temperature 673 K and strain rate 11 245 s-1, not used for equation fit, were used for comparing with the prediction of the J-C equation shown in Fig.8. It can be seen that the J-C constitutive equation gives a good agreement with the experimental response of TC16 at both quasi-static and high strain rates.

Fig.6 Comparison between predicted and measured true stress—strain curves at 293 K
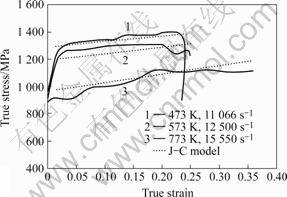
Fig.7 Comparison between predicted and measured true stress—strain curves under different conditions
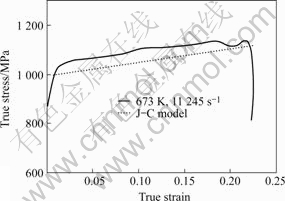
Fig.8 Comparison between predicted and measured true stress—strain curve at 673 K and strain rate 1 1245 s-1
4 Conclusions
1) The dynamic mechanical behaviors of TC16 alloy were investigated by means of the split Hopkinson bar. TC16 alloy was a kind of strain rate sensitive materials.
2) A new method incorporating TC16’s stress— strain curve developing item was proposed to obtain the J–C model easily and to avoid the complication in fitting of the coefficients of the temperature item.
3) The J-C dynamic constitutive equation could predict the flow stress of TC16 well under both quasi-static and dynamic loading.
References
[1] БОРИСОВА Е А. The metallography of titanium alloys[M]. Beijing: National Defense Industry Press, 1986: 326-344.
[2] WU Chong-zhou, LI Xing-wu. Study of deformation characters of TC16 titanium alloys under room temperature[J]. Titanium Industry Progress, 2006, 23(6): 17-19.
[3] ZHAO Yong-qing, XI Zheng-ping, QU Heng-lei. Current situation of titanium alloy materials used for national aviation[J]. Journal of Aeronautical Materials, 2003, 23: 215-219.
[4] TAN Zhen, LIU Dao-xin, ZHANG Guang-lai, ZHANG Xiao-hua, WANG Xiao-feng, LIU Jun. Fatigue behavior of TC16 titanium alloy bolts and 30CrMnSiA steel joint holes[J]. Mechanical Science and Technology, 2006, 25(7): 765-770.
[5] LIU Fang, SHAN De-bin, LU Yan. Influence of thermo-deformation parameters on the flow stress of LD7 aluminum alloy[J]. Mater Sci Technol, 2003, 11(1): 55-58.
[6] SHU Ying, ZENG Wei-dong, ZHOU Jun, ZHOU Yi-gang, ZHOU Lian. A study of hot deformation behavior for BT20 alloy[J]. Materials Science & Technology, 2005, 13(1): 66-69.
[7] SEO S W, MIN O K, YANG H M. Constitutive equation for Ti-6Al-4V at high temperatures measured using the SHPB technique[J]. International Journal of Impact Engineering, 2005, 31(6): 735-754.
[8] KIM J H, SEMIATIN S L, LEE C S. Constitutive analysis of the high-temperature deformation mechanisms of Ti-6Al-4V and Ti-6.85Al-1.6V alloys[J]. Mater Sci Eng A,2005, 394(1/2): 366-375.
[9] LI L X, LOU Y, YANG L B, PENG D S, RAO K P. Flow stress behavior and deformation characteristics of Ti-3Al-5V-5Mo compressed at elevated temperatures[J]. Materials & Design, 2002, 25(3): 451-457.
[10] KIM H Y, HONG S H. High temperature deformation behavior and microstructural evolution of Ti-47Al-2Cr-4Nb intermetallic alloys[J]. Scripta Materialia, 1998, 38(10): 1517-1523.
[11] WANG Yang, ZHOU Yuan-xin, XIA Yuan-ming. A constitutive description of tensile behavior for brass over a wide range of strain rates[J]. Mater Sci Eng A, 2004, 372: 186-190.
[12] GUO Wei-guo. Plastic flow behavior of a new austenitic stainless steel AL6-XN under different strain rates and temperatures[J]. Journal of Northwestern Polytechnical University, 2001, 19(3): 476-479.
[13] NEMAT-NASSER S, ISAACS J B, STARRETT J E. Hopkinson techniques for dynamic recovery experiments[J]. Proceedings of the Royal Society London, 1991, 435(A): 371-391.
[14] WANG Yang, XIA Yuan-ming. A modified constitutive equation for unidirectional composites under tensile impact and the dynamic tensile properties of KFRP[J]. Composites Science and Technology, 2000, 4(1): 591-596.
[15] YANG Yang, CHENG Xin-lin. Current status and trends in researches on adiabatic shearing[J]. The Chinese Journal of Nonferrous Metals, 2002, 12(3): 401-408. (in Chinese)
Foundation item: Projects(50471059, 50671121) supported by the National Natural Science Foundation of China
Corresponding author: YANG Yang; Tel: +86-731-8830770; E-mail: yangyang@mail.csu.edu.cn
(Edited by YUAN Sai-qian)